



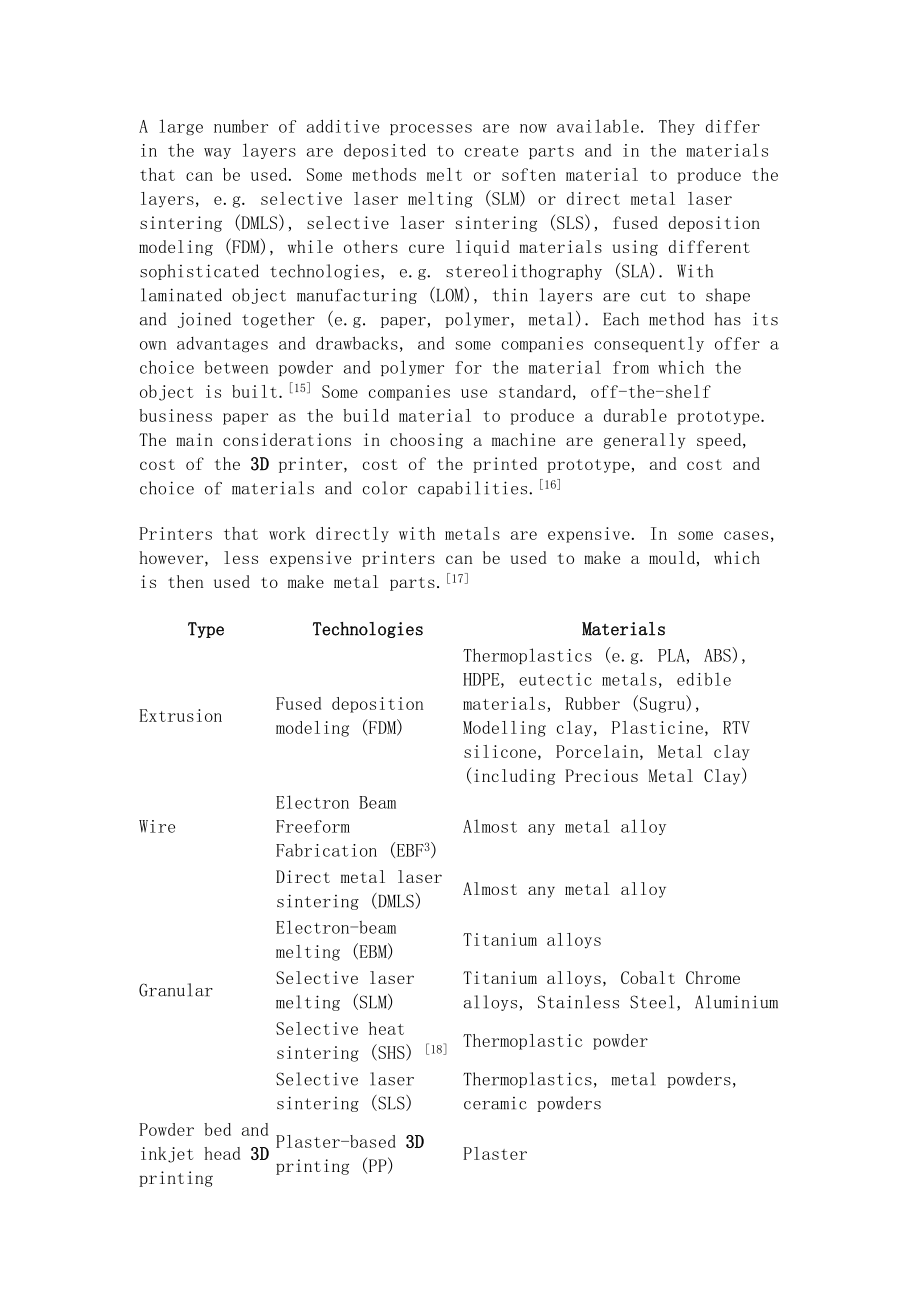
版权说明:本文档由用户提供并上传,收益归属内容提供方,若内容存在侵权,请进行举报或认领
文档简介
1、3D printingFor methods of applying a 2D image on a 3D surface, see pad printing. For methods of printing 2D parallax stereograms that seem 3D to the eye, see lenticular printing and holography.An ORDbot Quantum 3D printer. Timelapse video of a hyperboloid object (designed by George W. Hart) mad
2、e of PLA using a RepRap "Prusa Mendel" 3D printer for molten polymer deposition.3D printing or Additive manufacturing1 is a process of making a three-dimensional solid object of virtually any shape from a digital model. 3D printing is achieved using an additive process, where successive la
3、yers of material are laid down in different shapes.23D printing is also considered distinct from traditional machining techniques, which mostly rely on the removal of material by methods such as cutting or drilling (subtractive processes).A 3D printer is a limited type of industrial robot that is ca
4、pable of carrying out an additive process under computer control.While 3D printing technology has been around since the 1980s, it was not until the early 2010s that the printers became widely available commercially.3 The first working 3D printer was created in 1984 by Chuck Hull of 3D Systems Corp.4
5、 Since the start of the 21st century there has been a large growth in the sales of these machines, and their price has dropped substantially.5 According to Wohlers Associates, a consultancy, the market for 3D printers and services was worth $2.2 billion worldwide in 2012, up 29% from 2011.6The
6、3D printing technology is used for both prototyping and distributed manufacturing with applications in architecture, construction (AEC), industrial design, automotive, aerospace, military, engineering, civil engineering, dental and medical industries, biotech (human tissue replacement), fashion, foo
7、twear, jewelry, eyewear, education, geographic information systems, food, and many other fields. One study has found7 that open source3D printing could become a mass market item because domestic 3D printers can offset their capital costs by enabling consumers to avoid costs associated with purchasin
8、g common household objects.8TerminologyThe term additive manufacturing refers to technologies that create objects through sequential layering. Objects that are manufactured additively can be used anywhere throughout the product life cycle, from pre-production (i.e. rapid prototyping) to full-scale p
9、roduction (i.e. rapid manufacturing), in addition to tooling applications and post-production customization.9In manufacturing, and machining in particular, subtractive methods refers to more traditional methods. The term subtractive manufacturing is a retronym developed in recent years to distinguis
10、h it from newer additive manufacturing techniques. Although fabrication has included methods that are essentially "additive" for centuries (such as joining plates, sheets, forgings, and rolled work via riveting, screwing, forge welding, or newer kinds of welding), it did not include the in
11、formation technology component of model-based definition. Machining (generating exact shapes with high precision) has typically been subtractive, from filing and turning to milling, drilling and grinding.9The term stereolithography was defined by Charles W. Hull as a "system for generating thre
12、e-dimensional objects by creating a cross-sectional pattern of the object to be formed"in a 1984 patent.1011General principles3D model slicing.PrintingTo perform a print, the machine reads the design from an STL file and lays down successive layers of liquid, powder, paper or sheet material to
13、build the model from a series of cross sections. These layers, which correspond to the virtual cross sections from the CAD model, are joined or automatically fused to create the final shape. The primary advantage of this technique is its ability to create almost any shape or geometric feature.Printe
14、r resolution describes layer thickness and X-Y resolution in dpi (dots per inch),citation needed or micrometers. Typical layer thickness is around 100 ?m (250 DPI), although some machines such as the Objet Connex series and 3D Systems' ProJet series can print layers as thin as 16 ?m (1,600&
15、#160;DPI).12 X-Y resolution is comparable to that of laser printers. The particles (3D dots) are around 50 to 100 ?m (510 to 250 DPI) in diameter.Construction of a model with contemporary methods can take anywhere from several hours to several days, depending on the method used and the size and
16、 complexity of the model. Additive systems can typically reduce this time to a few hours, although it varies widely depending on the type of machine used and the size and number of models being produced simultaneously.Traditional techniques like injection molding can be less expensive for manufactur
17、ing polymer products in high quantities, but additive manufacturing can be faster, more flexible and less expensive when producing relatively small quantities of parts. 3D printers give designers and concept development teams the ability to produce parts and concept models using a desktop size print
18、er.FinishingThough the printer-produced resolution is sufficient for many applications, printing a slightly oversized version of the desired object in standard resolution and then removing material with a higher-resolution subtractive process can achieve greater precision.citation neededSome additiv
19、e manufacturing techniques are capable of using multiple materials in the course of constructing parts. Some are able to print in multiple colors and color combinations simultaneously. Some also utilize supports when building. Supports are removable or dissolvable upon completion of the print, and a
20、re used to support overhanging features during construction.Additive processesRapid prototyping worldwide 200113The Audi RSQ was made with rapid prototyping industrial KUKA robots.Several different 3D printing processes have been invented since the late 1970s. The printers were originally large, exp
21、ensive, and highly limited in what they could produce.14A large number of additive processes are now available. They differ in the way layers are deposited to create parts and in the materials that can be used. Some methods melt or soften material to produce the layers, e.g. selective laser melting
22、(SLM) or direct metal laser sintering (DMLS), selective laser sintering (SLS), fused deposition modeling (FDM), while others cure liquid materials using different sophisticated technologies, e.g. stereolithography (SLA). With laminated object manufacturing (LOM), thin layers are cut to shape and joi
23、ned together (e.g. paper, polymer, metal). Each method has its own advantages and drawbacks, and some companies consequently offer a choice between powder and polymer for the material from which the object is built.15 Some companies use standard, off-the-shelf business paper as the build material to
24、 produce a durable prototype. The main considerations in choosing a machine are generally speed, cost of the 3D printer, cost of the printed prototype, and cost and choice of materials and color capabilities.16Printers that work directly with metals are expensive. In some cases, however, less expens
25、ive printers can be used to make a mould, which is then used to make metal parts.17TypeTechnologiesMaterialsExtrusionFused deposition modeling (FDM)Thermoplastics (e.g. PLA, ABS), HDPE, eutectic metals, edible materials, Rubber (Sugru), Modelling clay, Plasticine, RTV silicone, Porcelain, Metal clay
26、 (including Precious Metal Clay)WireElectron Beam Freeform Fabrication (EBF3)Almost any metal alloyGranularDirect metal laser sintering (DMLS)Almost any metal alloyElectron-beam melting (EBM)Titanium alloysSelective laser melting (SLM)Titanium alloys, Cobalt Chrome alloys, Stainless Steel, Aluminium
27、Selective heat sintering (SHS) 18Thermoplastic powderSelective laser sintering (SLS)Thermoplastics, metal powders, ceramic powdersPowder bed and inkjet head 3D printingPlaster-based 3D printing (PP)PlasterLaminatedLaminated object manufacturing (LOM)Paper, metal foil, plastic filmLight polymerisedSt
28、ereolithography (SLA)photopolymerDigital Light Processing (DLP)photopolymerExtrusion depositionFused deposition modeling: 1 nozzle ejecting molten plastic, 2 deposited material (modeled part), 3 controlled movable table.Main article: Fused deposition modelingFused deposition modeling (FDM) was devel
29、oped by S. Scott Crump in the late 1980s and was commercialized in 1990 by Stratasys.19 With the expiration of the patent on this technology there is now a large open-source development community, as well as commercial and DIY variants, which utilize this type of 3D printer. This has led to a two or
30、ders of magnitude price drop since this technology's creation.In fused deposition modeling the model or part is produced by extruding small beads of material which harden immediately to form layers. A thermoplastic filament or metal wire that is wound on a coil is unreeled to supply material to
31、an extrusion nozzle head. The nozzle head heats the material and turns the flow on and off. Typically stepper motors or servo motors are employed to move the extrusion head and adjust the flow and the head can be moved in both horizontal and vertical directions. Control of this mechanism is typicall
32、y done by a computer-aided manufacturing (CAM) software package running on a microcontroller.Various polymers are used, including acrylonitrile butadiene styrene (ABS), polycarbonate (PC), polylactic acid (PLA), high density polyethylene (HDPE), PC/ABS, and polyphenylsulfone (PPSU). In general the p
33、olymer is in the form of a filament, fabricated from virgin resins. Multiple projects in the open-source community exist that are aimed at processing post-consumer plastic waste into filament. These involve machines to shred and extrude the plastic material into filament.FDM has some restrictions on
34、 the shapes that may be fabricated. For example, FDM usually cannot produce stalactite-like structures, since they would be unsupported during the build. These have to be avoided or a thin support may be designed into the structure which can be broken away during finishing.Granular materials binding
35、The CandyFab granular printing system uses heated air and granulated sugar to produce food-grade art objects.Another 3D printing approach is the selective fusing of materials in a granular bed. The technique fuses parts of the layer, and then moves the working area downwards, adding another layer of
36、 granules and repeating the process until the piece has built up. This process uses the unfused media to support overhangs and thin walls in the part being produced, which reduces the need for temporary auxiliary supports for the piece. A laser is typically used to sinter the media into a solid. Exa
37、mples include selective laser sintering (SLS), with both metals and polymers (e.g. PA, PA-GF, Rigid GF, PEEK, PS, Alumide, Carbonmide, elastomers), and direct metal laser sintering (DMLS).Selective Laser Sintering (SLS) was developed and patented by Dr. Carl Deckard and Dr. Joseph Beaman at the Univ
38、ersity of Texas at Austin in the mid-1980s, under sponsorship of DARPA.20 A similar process was patented without being commercialized by R. F. Housholder in 1979.21Selective Laser Melting (SLM) does not use sintering for the fusion of powder granules but will completely melt the powder using a high-
39、energy laser to create fully dense materials in a layerwise method with similar mechanical properties to conventional manufactured metals.Electron beam melting (EBM) is a similar type of additive manufacturing technology for metal parts (e.g. titanium alloys). EBM manufactures parts by melting metal
40、 powder layer by layer with an electron beam in a high vacuum. Unlike metal sintering techniques that operate below melting point, EBM parts are fully dense, void-free, and very strong.2223Another method consists of an inkjet 3D printing system. The printer creates the model one layer at a time by s
41、preading a layer of powder (plaster, or resins) and printing a binder in the cross-section of the part using an inkjet-like process. This is repeated until every layer has been printed. This technology allows the printing of full color prototypes, overhangs, and elastomer parts. The strength of bond
42、ed powder prints can be enhanced with wax or thermoset polymer impregnation.LaminationMain article: Laminated object manufacturingIn some printers, paper can be used as the build material, resulting in a lower cost to print. During the 1990s some companies marketed printers that cut cross sections o
43、ut of special adhesive coated paper using a carbon dioxide laser, and then laminated them together.In 2005, Mcor Technologies Ltd developed a different process using ordinary sheets of office paper, a Tungsten carbide blade to cut the shape, and selective deposition of adhesive and pressure to bond
44、the prototype.24There are also a number of companies selling printers that print laminated objects using thin plastic and metal sheets.PhotopolymerizationStereolithography apparatus.Main article: StereolithographyStereolithography was patented in 1986 by Chuck Hull.25 Photopolymerization is primaril
45、y used in stereolithography (SLA) to produce a solid part from a liquid. This process dramatically redefined previous efforts, from the Photosculpture method of Fran?ois Willème (18301905) in 186026 through the photopolymerization of Mitsubishis Matsubara in 1974.27In Digital Light Processing (
46、DLP), a vat of liquid polymer is exposed to light from a DLP projector under safelight conditions. The exposed liquid polymer hardens. The build plate then moves down in small increments and the liquid polymer is again exposed to light. The process repeats until the model has been built. The liquid
47、polymer is then drained from the vat, leaving the solid model. The EnvisionTECPerfactory28 is an example of a DLP rapid prototyping system.Inkjet printer systems like the Objet PolyJet system spray photopolymer materials onto a build tray in ultra-thin layers (between 16 and 30 ?m) until the pa
48、rt is completed. Each photopolymer layer is cured with UV light after it is jetted, producing fully cured models that can be handled and used immediately, without post-curing. The gel-like support material, which is designed to support complicated geometries, is removed by hand and water jetting. It
49、 is also suitable for elastomers.Ultra-small features can be made with the 3D microfabrication technique used in multiphoton photopolymerization. This approach traces the desired 3D object in a block of gel using a focused laser. Due to the nonlinear nature of photoexcitation, the gel is cured to a
50、solid only in the places where the laser was focused and the remaining gel is then washed away. Feature sizes of under 100 nm are easily produced, as well as complex structures with moving and interlocked parts.29Yet another approach uses a synthetic resin that is solidified using LEDs.30Mask-i
51、mage-projection-based stereolithographyIn this technique a 3D digital model is sliced by a set of horizontal planes. Each slice is converted into a two-dimensional mask image. The mask image is then projected onto a photocurable liquid resin surface and light is projected onto the resin to cure it i
52、n the shape of the layer.31In research systems, the light is projected from below, allowing the resin to be quickly spread into uniform thin layers, reducing production time from hours to minutes.31The technique has been used to create objects composed of multiple materials that cure at different ra
53、tes.31Commercially available devices such as Objet Connex apply the resin via small nozzles.31PrintersIndustry useAs of October 2012, Stratasys, the result of a merger of an American and an Israeli company, now sells additive manufacturing systems that range from $2,000 to $500,000; General Electric
54、 uses the high-end model to build parts for turbines, one example of GE's commitment of in-house investment of more than $1 billion on the technology.32Consumer useRepRap version 2.0 (Mendel).MakerBot Cupcake CNC. Printing in progress in a MakerBot 3D printer during Mozilla Maker party
55、, BangaloreAirwolf 3D AW3D v.4 (Prusa).Several projects and companies are making efforts to develop affordable 3D printers for home desktop use. Much of this work has been driven by and targeted at DIY/enthusiast/early adopter communities, with additional ties to the academic and hacker communities.
56、33RepRap is one of the longest running projects in the desktop category. The RepRap project aims to produce a free and open source software (FOSS) 3D printer, whose full specifications are released under the GNU General Public License, and which is capable of replicating itself by printing many of i
57、ts own (plastic) parts to create more machines.34 Research is under way to enable the device to printcircuit boards and metal parts.Because of the FOSS aims of RepRap, many related projects have used their design for inspiration, creating an ecosystem of related or derivative 3D printers, most of wh
58、ich are also open source designs. The availability of these open source designs means that variants of 3D printers are easy to invent. The quality and complexity of printer designs, however, as well as the quality of kit or finished products, varies greatly from project to project. This rapid develo
59、pment of open source 3D printers is gaining interest in many spheres as it enables hyper-customization and the use of public domain designs to fabricate open source appropriate technology through conduits such as Thingiverse and Cubify. This technology can also assist initiatives in sustainable development since technologies are easily and eco
温馨提示
- 1. 本站所有资源如无特殊说明,都需要本地电脑安装OFFICE2007和PDF阅读器。图纸软件为CAD,CAXA,PROE,UG,SolidWorks等.压缩文件请下载最新的WinRAR软件解压。
- 2. 本站的文档不包含任何第三方提供的附件图纸等,如果需要附件,请联系上传者。文件的所有权益归上传用户所有。
- 3. 本站RAR压缩包中若带图纸,网页内容里面会有图纸预览,若没有图纸预览就没有图纸。
- 4. 未经权益所有人同意不得将文件中的内容挪作商业或盈利用途。
- 5. 人人文库网仅提供信息存储空间,仅对用户上传内容的表现方式做保护处理,对用户上传分享的文档内容本身不做任何修改或编辑,并不能对任何下载内容负责。
- 6. 下载文件中如有侵权或不适当内容,请与我们联系,我们立即纠正。
- 7. 本站不保证下载资源的准确性、安全性和完整性, 同时也不承担用户因使用这些下载资源对自己和他人造成任何形式的伤害或损失。
最新文档
- 河北工艺美术职业学院《传感器与自动检测技术》2023-2024学年第二学期期末试卷
- 上海欧华职业技术学院《木材识别与鉴定》2023-2024学年第二学期期末试卷
- 宜宾职业技术学院《飞行器气动特性分析与设计》2023-2024学年第二学期期末试卷
- 保山学院《化学学科课程与教学论》2023-2024学年第二学期期末试卷
- 浙大宁波理工学院《针织成形技术》2023-2024学年第二学期期末试卷
- 温州医科大学仁济学院《现代秘书学》2023-2024学年第二学期期末试卷
- 泉州信息工程学院《移动电商实务》2023-2024学年第二学期期末试卷
- 石家庄铁道大学《英语听说(3)》2023-2024学年第二学期期末试卷
- 宁夏职业技术学院《中国传统文化书法》2023-2024学年第二学期期末试卷
- 西南财经大学《识图实训II》2023-2024学年第二学期期末试卷
- 上海嘉定区2025年公开招聘农村(村务)工作者笔试题带答案分析
- 皮肤科临床诊疗规范2020版
- 保密警示教育典型泄密案例教育学习
- 2025年注册会计师《会计》所得税会计模拟试题解析与答题技巧
- 封隔器加工合同协议
- 《大学生职业生涯规划与就业指导(实践版)》全套教学课件
- 建筑企业财务管理的风险控制与应对策略
- 抗生素合理使用研究试题及答案
- 批评不可怕课件
- 智能建造基础考试题及答案
- 通信工程项目管理流程
评论
0/150
提交评论