
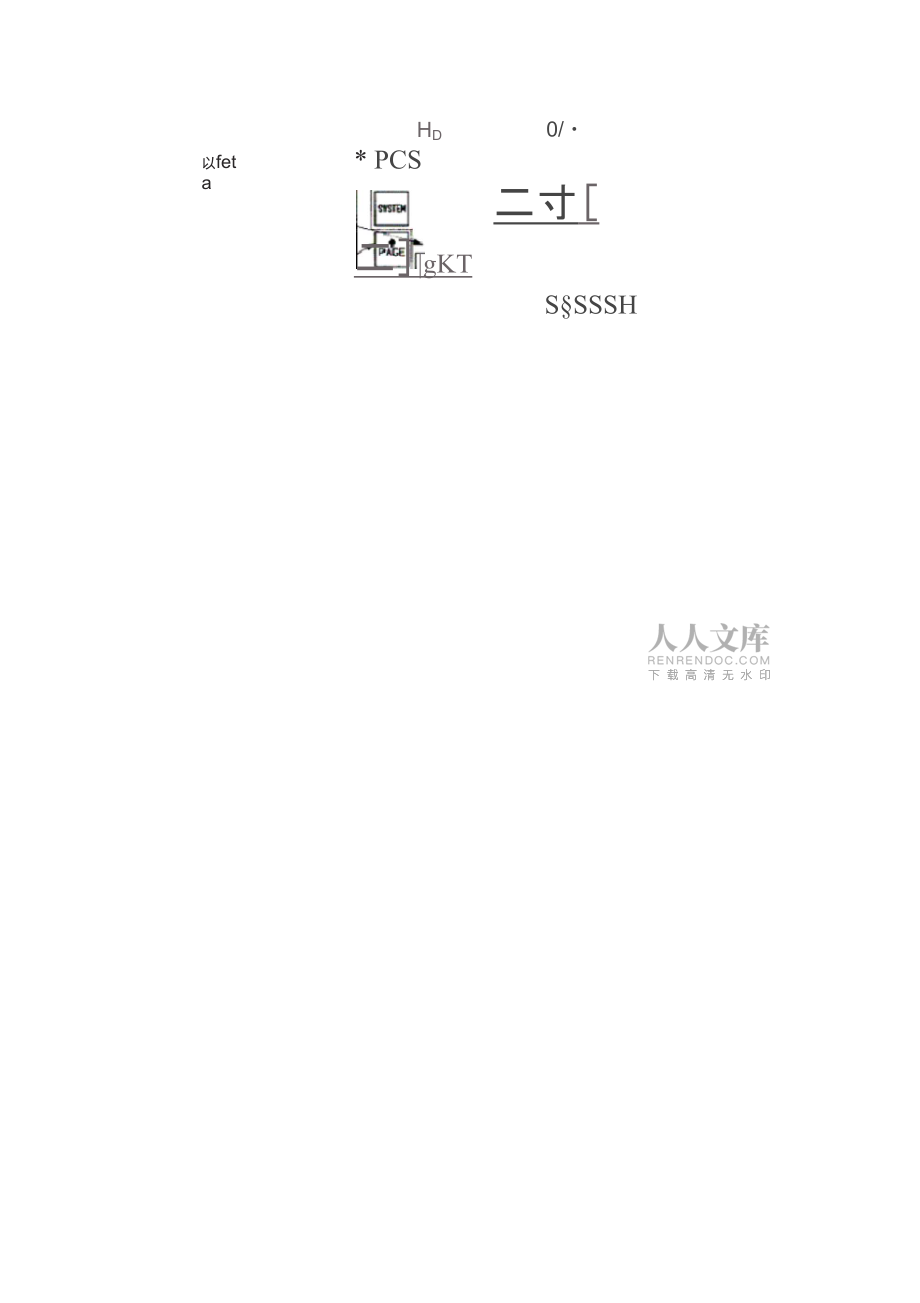

版权说明:本文档由用户提供并上传,收益归属内容提供方,若内容存在侵权,请进行举报或认领
文档简介
1、第一课加工中心FANUC系统操作面板功能键及 开关的使用方法一、FANUC系统操作面板功能键的含义N¥2*DLitF5鼻XzF AMUC Series Oi-UM0&dvrHLTt理狂汇t弋兀供;)oou'jjj odo an-400.000-200.0000.000血丁尸誌 aBumas £ 一 T 囁令IE运打訂返ACTJ UL'J!. j【們】 i|l ' 1 " g n 口 s Z.<£|2£迪址KJI 丫sJItJ i£125£一取洎fit输入壌HD0/以feta* PCS二寸
2、二|gKTS§SSSH犍盘的洋细说明*2.2、n)i面檢上的详鋼從列号详细说列1A按F这些谜町以便CNC建位或音取消报警瓠2E3当对MDI犍的操作不明白时,抜下这个可以获得帝助 (MfihWh3软业根据不岡的厕面.轶键有不同的功9L软仲功能昱示在屏 暮的底端4地址和救字键按卜这些键町以綸入字阳,数字或者其它字符.15换档健 打ft在谀键盘上,有些梶具有两个功怡 按下yhiftHt可以在 这阿个功能之间进行切换.当一个鼻右下彝的字毋可枝输 入时.炊会在屛暮上显示一个特殊的字符世61DA/?当按下 緩存区到値置个7冈键或&敷7储时,再按该fit数据骏禺入到 ,并且显示&屏
3、<上:耍彎6入馥存区的数据拷贝1NRJ1脊存嚣中等.谄按卜«L这个tif与轶8!上的1番是等效的。71収浦键S按尸这个確删除Jft后一个进入输入缱存区的宁符或诉号. 勺健输入级存区布显示为:>N001X2002_11当按卜_储时,Z Wifi并且显示如下:>NOOiX1008卜1£1(1啊1卜花彳誓下如丁犍战行程序编舅:ALTER11:替換WSSU1一 !插入|(El£1E:掰除9功譬|二。5 |按T这空8L切换不同功廃的显示WW. 详ffliff见m23的功tti«o一般的馬“I作匕K )1 JC血网) TJLJLJLZJP表22 M
4、DI面板上键的详细说明編号名称详 ttiftsfl10光标移动键有四种不同的光标移动键;H :这个健用于将咒标向右威舀向和移动.光标以小的 单位向前移动。FH :这个铳用于将比标向左诚皆往回甘厉.光标以水的 单位往回移动。EU :这个键用于将光标向下或者向和移动.光标以大的 敢位向前移动.ED :这个促闪于将光标向上戚&往回移就1.光标以大的 单位往回移动。11換页催SS矜两匸换更键to该憶用于将隔幕显示的页面向舗翻矶 E3 :该變用于梅辟样显示的页面往回1M1K.23功瞬和软键功腿畏是用来选卅将豪昱示的瞬移(功旎)的.兰一个软键(直节 选择软徒)在功能琏之后立即枝技尸広,乞町以选择与
5、所选功就相 关的屏尊(分MI0F )2J.11. 按HMDI面板上的功能健。JKF所选功能的一型软犍"显示出2. ttTK中一个章节iXffffe則所选章节的層暮覆显示出来.如 果有关一个目标章节的屏松S有显示岀笊菜草继续!(下 一粟单键人有些情况.可以选择一章中的附加章节.3 当II标章节解址禾斤按下探作选H0L以驶禾裂进斤操作 的数駄4.为了里新显示章节雄择耿糙按下菜单返回雜,粛节选荐软 tt虑作堆择软簾单电冋傅上itn解權了通常的屏幕旻示过視。然喇,实际的显示过程,每 « 豪那不一倂.耍了解详细情况.请见相关的操作叙逑.的历帯.惟下馬龍tt后帧諛観.itt(也用于实际
6、 車节的射f按下一令功隐厲石蚊遂显那揀餡娈此is;w劭下阳中符号的含叉如下祈示: II ;呈乔的時:丨我彌过擅下功mt而瞬的厨幕*r).;卷示一平默馄*2()t去祈舸MDI面板班饰入*一«衷示一平晁示为關色的找谴.叵:密示賣甲处媒nt (壷右边的软魅(*3)tT按下珀陡蛇皆常用併科之时的牌横. '2很昭配背用尸阿 有竝血臓徒护予詁询、开关的使用方法S-K 些*BPBJ*设定自动运行方式 设定程序编辑方式 设定MDI方式设定DNC运行方式.单程序段运行方式可选程序段跳过运行方式,跳过程序段开头带有 /的程序程序停止 手动示教(手轮示教)方式程序重启机床机械锁住循环停止(自动操作
7、停止) 循环启动(自动操作开始) 程序停(进给保持)返回参考点方式手动进给方式: 手轮进给方式 .: 手轮进给倍率: 手动进给轴选择 .: 快速进给 .: 移动方向选择 .: 主轴 , 正转 , 停止 , 反转 .: 进给倍率 .:主轴转速倍率: 紧急停止: 程序保护开关六、小结: 加工中心 慨况及面板操作 七、作业:操作面板,熟练面板各个功能键第二课 加工中心加工工件的安装、对刀与换刀加工中心加工定位基准的选择:1选择基准的三个基本要求: ( 1)所选基准应能保证工件定位准确装卸方便方便可靠。( 2)所选基准与各加工部位的的尺寸计算简单。( 3)保证加工精度。2选择定位基准 6原则:( 1)
8、尽量选择设计基准作为定位基准; (2)定位基准与设计基准 不能统一时,应严格控制定位误差保证加工精度;( 3)工件需两次以上装夹加工时,所选基准在一次装夹定位能完成全部关键精度部位的加工;( 4)所选基准要保证完成尽可能多的加工容; ( 5)批量加工时,零件定位基准应尽可能与建立工件坐标系的对刀基准重合; (6)需要多次装夹时,基准应该前后统一。加工中心夹具的确定:1对夹具的基本要求: ( 1)夹紧机构不得影响进给,加工部位要敞开;(2)夹具在机床上能实现定向安装; ( 3)夹具的刚性与稳定性要好。2常用夹具种类: (1)通用夹具:如虎钳、分度头、卡盘等; ( 2)组合夹具:组合夹具 由一套结
9、构已经标准化、尺寸已经规格化的通用元件组合元件所构成;( 3)专用夹具:专为某一项或类似的几项加工设计制造的夹具; ( 4)可调整夹具:组合夹具与专用夹具的结 合,既能保证加工的精度,装夹更具灵活性; ( 5)多工位夹具:可同时装夹多个工件的夹 具;( 6)成组夹具:专门用于形状相似、尺寸相近且定位、夹紧、加工方法相同或相似的 工件的装夹。3加工中心夹具的选用原则:(1)在保证加工精度和生产效率的前提下,优先选用通用夹具;(2)批量加工可考虑采用简单专用夹具;(3)大批量加工可考虑采用多工位夹具和高效的气压、液压等专用夹具;(4)采用成组工艺时应使用成组夹具;4工件在机床工作台上的最佳装夹位置
10、:工件装夹位置应保证工件在机床各轴的加工行 程围,并且使得刀具的长度尽可能缩短,提高刀具的加工刚性。加工中心加工的对刀与换刀对刀:对刀也就是工件在机床上找正加紧后,确定工件坐标(编程坐标)原点的机床坐标(确定G54 的 X、Y、Z 的值)。换刀:根据工艺需要,要用不同参数的刀具加工工件。在加工中按需要更换刀具的过程叫 换刀。对刀点与换刀点的确定:对刀点: 对刀点是工件在机床上找正夹紧后, 用于确定工件坐标系在机床坐标系中位置的 基准点。对刀点可选在工件上或装夹定位元件上,但对刀点与工件坐标点必须有准确、合理、简单 的位置对应关系,方便计算工件坐标点在机床上的位置(工件坐标点的机床坐标)。对刀点
11、最好能与工件坐标点重合。换刀点:加工中心有刀库和自动换刀装置,根据程序的需要可以自动换刀。换刀点应在换 刀时工件、夹具、刀具、机床相互之间没有任何的碰撞和干涉的位置上,加工中心的换刀 点往往是固定的。对刀方法:水平方向对刀( x 、 y 坐标):(1)杠杆百分表对刀:对刀点为圆柱孔中心;(2)采用寻边器对刀:圆孔或基准边(3)采用碰刀或试切方式对刀。Z 向对刀( z 坐标):(1)机上对刀:采用 z 向坐标对刀。( 2)机外刀具预调 +机上对刀。 机外对刀仪对刀:测量刀具的直径、长度、刀刃形状和刀角。(4)卧式加工中心多工位加工中的对刀问题 第三课加工中心加工工艺二:选择走刀路线与确定工艺参数
12、加工工序的划分( 5 分钟) 在数控机床上特别是在加工中心上加工零件,工序十分集中,许多零件只需在一次装卡中 就能完成全部工序。但是零件的粗加工,特别是铸、锻毛坯零件的基准平面、定位面等的加工 应在普通机床上完成之后,再装卡到数控机床上进行加工。这样可以发挥数控机床的特点,保 持数控机床的精度,延长数控机床的使用寿命,降低数控机床的使用成本。在数控机床上加工 零件其工序划分的方法有:1、刀具集中分序法 即按所用刀具划分工序,用同一把刀加工完零件上所有可以完成的部位,在用第二把刀、 第三把刀完成它们可以完成的其它部位。这种分序法可以减少换刀次数,压缩空程时间,减少 不必要的定位误差。2、粗、精加
13、工分序法 这种分序法是根据零件的形状、尺寸精度等因素,按照粗、精加工分开的原则进行分序。 对单个零件或一批零件先进行粗加工、半精加工,而后精加工。粗精加工之间,最好隔一段时 间,以使粗加工后零件的变形得到充分恢复,再进行精加工,以提高零件的加工精度。3、按加工部位分序法 即先加工平面、定位面,再加工孔;先加工简单的几何形状,再加工复杂的几何形状;先 加工精度比较低的部位,再加工精度要求较高的部位。总之,在数控机床上加工零件,其加工工序的划分要视加工零件的具体情况具体分析。许 多工序的安排是综合了上述各分序方法的。选择走刀路线( 5分钟) 走刀路线是数控加工过程中刀具相对于被加工件的的运动轨迹和
14、方向。 走刀路线的确定非(1)保证零件的加工精度和表面粗糙度;(2)方便数值计算,减少编程工作量;(3)缩短走刀路线,减少进退刀时间和其他辅助时间;(4)尽量减少程序段数。另外,在选择走刀路线时还要充分注意以下所讲解的几个方面的容。避免引入反向间隙误差(5分钟)数控机床在反向运动时会岀现反向间隙,如果在走刀路线中将反向间隙带入,就会影响刀具的定位精度,增加工件的定位误差。例如精镗图16-1中所示的四个孔,由于孔的位置精度要求较高,因此安排镗孔路线的问题就显得比较重要,安排不当就有可能把坐标轴的反向间隙带 入,直接影响孔的位置精度。这里给岀两个方案,方案a如图16-1a)所示,方案b如图16-1
15、b)所示。从图中不难看岀,方案 a中由于W孔与I、n、皿孔的定位方向相反,X向的反向间隙会使定位误差增加,而影响w孔的位置精度。在方案b中,当加工完皿孔后并没有直接在w孔处定位,而是多运动了一段距离,然后折回来在w孔处定位。这样I、n、皿孔与w孔的定位方向是一 致的,就可以避免弓I入反向间隙的误差,从而提高了w孔与各孔之间的孔距精度。图16-1镗铣加工路线图切入切岀路径(5分钟)在铣削轮廓表面时一般采用立铣刀侧面刃口进行切削,由于主轴系统和刀具的刚度变化, 当沿法向切入工件时,会在切入处产生刀痕,所以应尽量避免沿法向切入工件。当铣切外表面 轮廓形状时,应安排刀具沿零件轮廓曲线的切向切入工件,并
16、且在其延长线上加入一段外延距 离,以保证零件轮廓的光滑过渡。同样,在切出零件轮廓时也应从工件曲线的切向延长线上切 岀。如图16-2a)所示。当铣切表面轮廓形状时,也应该尽量遵循从切向切入的方法,但此时切入无法外延,最好 安排从圆弧过渡到圆弧的加工路线。切岀时也应多安排一段过渡圆弧再退刀,如图16-2b)所示。当实在无法沿零件曲线的切向切入、切岀时,铣刀只有沿法线方向切入和切岀,在这种情况下, 切入切出点应选在零件轮廓两几何要素的交点上,而且进给过程中要避免停顿。底)怫削外團加工跑衣Cb)規削内圆加H册梗图16-2铳削圆的加工路线为了消除由于系统刚度变化引起进退刀时的痕迹,可采用多次走刀的方法,
17、减小最后精铣时的余量,以减小切削力。在切入工件前应该已经完成刀具半径补偿,而不能在切入工件时同时进行刀具补偿,如图16-2a)所示,这样会产生过切现象。为此,应在切入工件前的切向延长线上另找一点,作为完 成刀具半径补偿点,如图 16-2b )所示。图16-3切入切出路径例如,16-3所示零件的切入切出路线应当考虑注意切入点及延长线方向。顺、逆铳及切削方向和方式的确定(5分钟)在铳削加工中,若铳刀的走刀方向与在切削点的切削分力方向相反,称为顺铳;反之 则称为逆铳。由于采用顺铳方式时,零件的表面精度和加工精度较高,并且可以减少机床 的颤振”所以在铳削加工零件轮廓时应尽量采用顺铳加工方式。若要铳削沟
18、槽的两侧面,就应来回走刀两次,保证两侧面都是顺铳加工方式,以使两侧面 具有相同的表面加工精度。加工中心铳削加工工艺参数的确定(5分钟)确定工艺参数是工艺制定中重要的容,采用自动编程时更是程序成功与否的关键。(一)用球铳刀加工曲面时与切削精度有关的工艺参数的确定1、步长I (步距)的确定步长I (步距)一一每两个刀位点之间距离的长度,决定刀位点数据的多少。曲线轨迹步长I的确定方法:直接定义步长法:在编程时直接给出步长值,根据零件加工精度确定 间接定义步长法:通过定义逼近误差来间接定义步长2、行距S (切削间距)的确定行距S (切削间距)一一加工轨迹中相邻两行刀具轨迹之间的距离。影响:行距小:加工
19、精度高,但加工时间长,费用高行距大:加工精度低,零件型面失真性较大,但加工时间短。两种方法定义行距:(1)直接定义行距算法简单、计算速度快,适于粗加工、半精加工和形状比较平坦零件的精加工的刀具运动 轨迹的生成。(2)用残留高度h来定义行距残留高度h被加工表面的法矢量方向上两相邻切削行之间残留沟纹的高度。h大:表面粗糙度值大h小:可以提高加工精度,但程序长,占机时间成倍增加,效率降低选取考虑:粗加工时,行距可选大些,精加工时选小一些。有时为减小刀峰高度,可在原两行之间加 密行切一次,即进行曲刀峰处理,这相当于将S减小一半,实际效果更好些。(二)与切削用量有关的工艺参数确定1背吃刀量ap与侧吃刀量
20、ae背吃刀量ap平行于铳刀轴线测量的切削层尺寸。侧吃刀量ae垂直于铳刀轴线测量的切削层尺寸。从刀具耐用度的角度出发,切削用量的选择方法是:先选取背吃刀量 ap或侧吃刀量ae,其次确定进给速度,最后确定切削速度。如果零件精度要求不高,在工艺系统刚度允许的情况下,最好一次切净加工余量,以提高加工效率;如果零件精度要求高,为保证精度和表面粗糙度,只好采用多次走刀。2、与进给有关参数的确定在加工复杂表面的自动编程中,有五种进给速度须设定,它们是:(1)快速走刀速度(空刀进给速度)为节省非切削加工时间,一般选为机床允许的最大进给速度,即G00速度。(2)下刀速度(接近工件表面进给速度)为使刀具安全可靠的
21、接近工件,而不损坏机床、刀具和工件,下刀速度不能太高,要小于 或等于切削进给速度。对软材料一般为200mm/min ;对钢类或铸铁类一般为 50mm/min。(3)切削进给速度F切削进给速度应根据所采用机床的性能、刀具材料和尺寸、被加工材料的切削加工性能和加工余量的大小来综合的确定。一般原则是:工件表面的加工余量大,切削进给速度低;反之相反。切削进给速度可由机床操作者根据被加工工件表面的具体情况进行手工调整,以获得最佳切削状态。切削进给速度不能超过按逼近误差和插补周期计算所允许的进给速度。建议值:加工塑料类制件:1500 mm/min加工大余量钢类零件:250 mm/mi n小余量钢类零件精加
22、工:500 mm/mi n铸件精加工:600 mm/min(4)行间连接速度(跨越进给速度)行间连接速度刀具从一切削行运动到下一切削行的运动速度。该速度一般小于或等于切削进给速度。(5)退刀进给速度(退刀速度)为节省非切削加工时间,一般选为机床允许的最大进给速度,即G00速度。3、与切削速度有关的参数确定(1)切削速度uc切削速度uc的高低主要取决于被加工零件的精度和材料、刀具的材料和耐用度等因素。(2)主轴转速n主轴转速n根据允许的切削速度uc来确定:n=1000 u c/ nd理论上,u越大越好,这样可以提高生产率,而且可以避开生成积屑瘤的临界速度,获得较低的表面粗糙度值。但实际上由于机床
23、、刀具等的限制,使用国机床、刀具时允许的切 削速度常常只能在100200m/min围选取。、小结:1、在数控机床上特别是在加工中心上加工零件,工序十分集中,许多零件只需在一次装卡 中就能完成全部工序。2、走刀路线的确定非常重要,因为它与零件的加工精度和表面质量密切相关。确定走刀 路线首先要保证零件的加工精度和表面粗糙度,其次要方便数值计算,减少编程工作量。3、选择走刀路线时还要特别注意不要引入反向间隙误差、切入切出路径不要发生过切、 尽量采用顺铣加工方机床操作面板主要由操作模式开关、 主轴转速倍率调整旋钮、 进给速度调节旋钮、 各种辅助 功能选择开关、手轮、各种指示灯等组成。各按钮、旋钮、开关
24、的位置结构由机床厂家自行 设计制作, 因此各机床厂家生产的机床操作面板各不相同。 下面介绍 Fanuc 系统标准的操 作按钮的功能和操作方法。自动运行方式 MEM:FANUC 标准 MTB 面板自动运行操作按钮为图 2-1 。自动执行加 工程序;在 “MEM ”自动运行状态下,按下操作面板上各种机床功能开关(搬动功能开关的 同时,其对应的功能灯将点亮) ,可使该功能起作用。这些功能开关包括:1)单程序段( Single Block ):在自动运行方式( MEM )下,启动 “单程序段 ”功 能,则按下程序循环启动按钮, 执行完一段指令后程序暂停, 机床处于进给保持状态; 继续 按下程序循环启动
25、按钮,执行下一段程序后又停止。用这种功能可以检查程序。2 )选择跳段( Block Delete ):在自动运行方式( MEM )下,当 “选择跳段 ”功能起 作用时,当程序执行中到带有 “/ ”语句时,则跳过这个语句不执行。3)选择停止( Option Stop ):在自动运行方式( MEM )下,当 “选择停止 ”功能起作 用时,当程序执行到 “M01 ”指令,程序暂停,机床处于进给保持状态。4 )试运行( Dry Run ):不装夹工件只检查刀具的运动。通过操作面板上的旋钮,控 制刀具运动的速度。用于检验程序。5)机床闭锁状态:即机床坐标轴处于停止状态,而只有轴的位置显示在变。可以将机
26、床闭锁功能与试运行功能同时使用,用于快速检测程序。6)辅助功能闭锁:在机床锁住状态中,当自动运行被置于辅助功能锁住方式时,所有 的辅助功能(主轴旋转、刀具更换、冷却液开 / 关等)均不执行。编辑方式 Edit:FANUC 标准 MTB 面板自动运行操作按钮为图 2-2 。选择编程功 能 图 2-3 和编辑方式 图 2-4 ,可以输入及编辑加工程序。手动数据输入方式 MDI :FANUC 标准 MTB 面板自动运行操作按钮为 图 2-5 。在 MDI 方式下,通过 MDI 面板,可以编制最多 10 行的程序并被执行,程序格式和通常程序一 样。 MDI 方式适用于简单的测试操作。 DNC 方式 :FANUC 标准 MTB 面板 DNC 运行操作按钮为 图 2-6 现在的数控系统功能已非常完善 ,一般都支持 RS -232C 通信功能, 即通过 RS-232 口接 收或发送加工程序,有很多 CNC 系统可实现一边接收 NC 程序一边进行切削加工,
温馨提示
- 1. 本站所有资源如无特殊说明,都需要本地电脑安装OFFICE2007和PDF阅读器。图纸软件为CAD,CAXA,PROE,UG,SolidWorks等.压缩文件请下载最新的WinRAR软件解压。
- 2. 本站的文档不包含任何第三方提供的附件图纸等,如果需要附件,请联系上传者。文件的所有权益归上传用户所有。
- 3. 本站RAR压缩包中若带图纸,网页内容里面会有图纸预览,若没有图纸预览就没有图纸。
- 4. 未经权益所有人同意不得将文件中的内容挪作商业或盈利用途。
- 5. 人人文库网仅提供信息存储空间,仅对用户上传内容的表现方式做保护处理,对用户上传分享的文档内容本身不做任何修改或编辑,并不能对任何下载内容负责。
- 6. 下载文件中如有侵权或不适当内容,请与我们联系,我们立即纠正。
- 7. 本站不保证下载资源的准确性、安全性和完整性, 同时也不承担用户因使用这些下载资源对自己和他人造成任何形式的伤害或损失。
最新文档
- 火烧云作业设计
- 2025届邢台市南宫市数学三年级第一学期期末教学质量检测试题含解析
- 水利水电工程未来挑战与机遇试题及答案
- 市政工程考试模拟题库试题及答案
- 冷饮小商店课件
- 2025年工程项目管理的重要试题与答案
- 禁烟与安全教育主题班会
- 简述行政协议的概念与特征
- 2025年经济师考题分析中级经济师试题及答案
- 外派工作经历与能力鉴定证明(5篇)
- 安全生产事故调查培训
- 环境社会学考试必考点
- 多模态医学影像融合
- 2023发电企业运行管理办法
- 蓝藻打捞及资源化利用投标方案(技术方案)
- 清理坡面危石施工方案
- 中医外科学周围血管及淋巴管疾病课件
- 企业网络安全咨询服务项目
- 基于苦味产生机制的掩味策略与评价
- 防火卷帘施工方案
- 2023年广东深圳市福田街道办事处招聘高频考点题库(共500题含答案解析)模拟练习试卷
评论
0/150
提交评论