
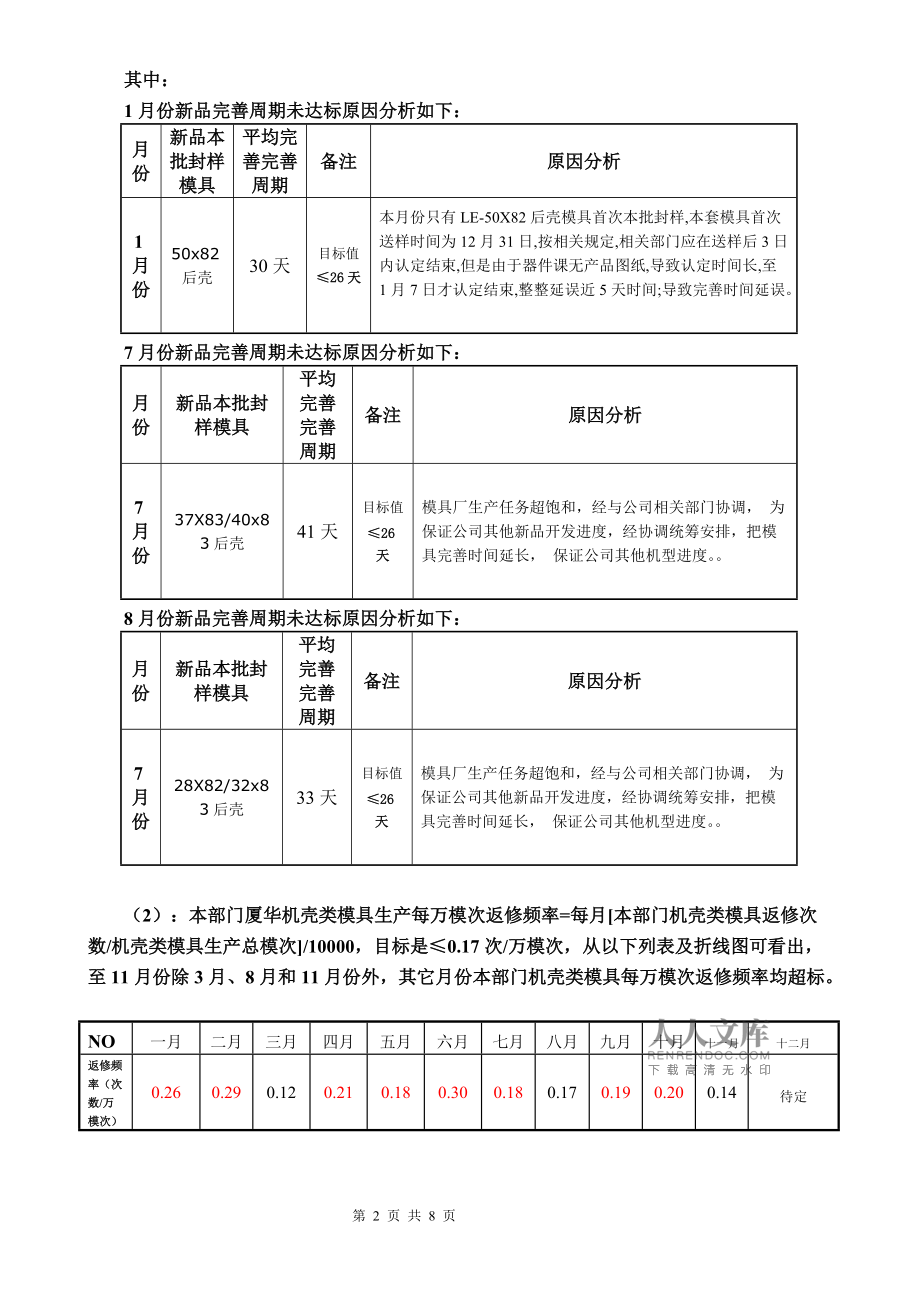



版权说明:本文档由用户提供并上传,收益归属内容提供方,若内容存在侵权,请进行举报或认领
文档简介
1、制一课2013年管理评审总结报告一:质量目标完成情况及建议调整说明1. 质量目标完成情况:(1):新模完善周期(天)= 本批封样时间-首次试模时间(仅针对机壳类模具),从以下列表及折线图可看出,本部门2013年每月新模完善周期除1/7/8月份外其余均达到目标要求,达到了预期的效果。NO一月二月三月四月五月六月七月八月九月十月十一月十二月目标26 26 26 26 26 26 26 26 26 26 26 26 新模完善周期(天)302626无考核模具无考核模具无考核模具4133无考核模具无考核模具16无考核模具 其中:1月份新品完善周期未达标原因分析如下:月份新品本批封样模具平均完善完善周期备
2、注原因分析1月份50x82后壳30天目标值26天本月份只有LE-50X82后壳模具首次本批封样,本套模具首次送样时间为12月31日,按相关规定,相关部门应在送样后3日内认定结束,但是由于器件课无产品图纸,导致认定时间长,至1月7日才认定结束,整整延误近5天时间;导致完善时间延误。7月份新品完善周期未达标原因分析如下:月份新品本批封样模具平均完善完善周期备注原因分析7月份37X83/40x83后壳41天目标值26天模具厂生产任务超饱和,经与公司相关部门协调, 为保证公司其他新品开发进度,经协调统筹安排,把模具完善时间延长, 保证公司其他机型进度。8月份新品完善周期未达标原因分析如下:月份新品本批
3、封样模具平均完善完善周期备注原因分析7月份28X82/32x83后壳33天目标值26天模具厂生产任务超饱和,经与公司相关部门协调, 为保证公司其他新品开发进度,经协调统筹安排,把模具完善时间延长, 保证公司其他机型进度。(2):本部门厦华机壳类模具生产每万模次返修频率=每月本部门机壳类模具返修次数/机壳类模具生产总模次/10000,目标是0.17次/万模次,从以下列表及折线图可看出,至11月份除3月、8月和11月份外,其它月份本部门机壳类模具每万模次返修频率均超标。NO一月二月三月四月五月六月七月八月九月十月十一月十二月返修频率(次数/万模次)0.26 0.29 0.12 0.21 0.18
4、0.30 0.18 0.17 0.19 0.20 0.14 待定 其中:1月、2月、4月、5月、6月、7月、9月和10月份返修频率未达标原因分析如下:月份修模次数注塑机壳数量返修频率备注原因分析1月份3次116744个0.26次目标值0.17次超标原因:注塑厂订单量少, 为提高注塑厂生产效率,我司配合注塑厂部分模具进行保养完善, 保证后续大生产顺利进行。2月份2次68017个0.29次目标值0.17次超标原因:注塑厂订单量少, 为提高注塑厂生产效率,我司配合注塑厂部分模具进行保养完善, 保证后续大生产顺利进行。3月份1次86005个0.12次目标值0.17次达标。4月份2次97230个0.21
5、次目标值0.17次超标原因:注塑厂订单量少, 为提高注塑厂生产效率,我司配合注塑厂部分模具进行保养完善, 保证后续大生产顺利进行。5月份2次109724个0.18次目标值0.17次超标原因:注塑厂订单量少, 为提高注塑厂生产效率,我司配合注塑厂部分模具进行保养完善, 保证后续大生产顺利进行。6月份2次67209个0.30次目标值0.17次超标原因:注塑厂订单量少, 为提高注塑厂生产效率,我司配合注塑厂部分模具进行保养完善, 保证后续大生产顺利进行。7月份2次111356个0.18次目标值0.17次超标原因:注塑厂订单量少, 为提高注塑厂生产效率,我司配合注塑厂部分模具进行保养完善, 保证后续大
6、生产顺8月份3次181453个0.17次目标值0.17次达标。9月份4次209703个0.19次目标值0.17次超标原因:注塑厂订单量少, 为提高注塑厂生产效率,我司配合注塑厂部分模具进行保养完善, 保证后续大生产顺10月份4次203320个0.20次目标值0.17次超标原因:注塑厂订单量少, 为提高注塑厂生产效率,我司配合注塑厂部分模具进行保养完善, 保证后续大生产顺11月份2次141809个0.14次目标值0.17次达标。12月份目标值0.17次待定。2. 质量目标调整说明:根椐以上面两幅折线可以看出,1).2013年部门新模完善周期除1月份/7月份/8月份超标外,其余基本达成目标值,考虑
7、今年三个月超标原因:系多数新品模具完善阶段改模次数多/认定滞后等综合因素,势必会对后续完善周期产生影响,故建议暂不调整该项目标;2).厦华模具生产每万模次返修率平均0.20次/万模次(目标值0.18次/万模次),但除3月份/8月份/11月份外,其余均超标,考虑影响指标原因系公司订单量持续下降等因素,故建议进行适当调整即可;二:纠正和预防措施执行情况:1.部门2012年异常事故次数汇总 2012年品质异常次数汇总表NO一月二月三月四月五月六月七月八月九月十月十一月十二月品质异常次数000000001次00待定2. 9月份部门出现异常事故原因分析、对策及措施(1):9月份主要问题分析及对策、措施:
8、序号问题点原因分析与解决对策后续需改善方向1LCM-23X82胶框浇口镶件电火花加工后发现16插穿封胶面过切,出胶口不圆,工件无法直接使用1:电极设计未按规范采用粗精电极;2:可能加工过程中机台出现接触不良或模具方面是否是密封圈原因导致接触不良,后续继续跟踪验证。 3:激光焊厚重新加工1:严格按规范设计电极;2:加工过程不定时检查加工是否异常;3:继续跟踪机台是否存在异常情况 三:公司于2013年内外审所提出的整改建议及执行情况。2013年公司内外审过程部门均未出现不符合项。四:根据公司经营方针、6S管理思想,及ISO内外审时对我部提出的整改建议,2012年我部对本部门的一些不尽完善之处采取了
9、必要措施,继续加强了多项6s改进及技术创新项目,具体如下:一:6S改进项目:(1). 自制8件畚斗,a.原部门各组配置一个外购畚斗,因质量较差无法满足现行清理铁屑,现已基本损坏。b.部门采用外购铁皮自制成型使用(8件),至今未出现质量问题!(2). 自制大摇壁钻工作站台(2个)a.制一大摇壁钻机床原未配置专用工作站台,造成钳工在钻大尺寸模板时需用现有站台(500mm)加垫木材才足以操作钻孔,不仅影响生产效率且极易产生安全事故。b. 部门用外购三角铁及木材设计制作高度为1m的两专用站台,至今使用效果良好。.(3). 自制摇壁钻床钻夹头拆装工具a.现行制一摇壁钻机床辅助拆装钻夹头的三角铁均已丢失,
10、大部分员工均采用废螺钉进行拆装作业,该方式不仅影响效率、影响机床夹头、钻夹头寿命,且员工在拆装过程容易碰伤手指。b. 部门用场内废铁进行制作(需调质处理)15件(4). 一层洗手间门口拖车放置区域改进a. 原一层洗手间门口拖车放置区域摆放不齐(现有区域不够摆放且部分已出现故障),造成了该区域通道的堵塞。b. 建议后续根据生产任务情况适当封存部分拖车(暂存样品临时放置处),同时要求做好相关保养工作,对于有异常的需及时上报检修(5). 整改皂化液桶装结构及放置区域原制一皂化液(冷却液)放置处不符合6s管理要求,现行放置使用不仅使得员工效率低下(未稀释且很难装),且使得地板被严重污染,要求对该处进行
11、整改(要求统一用带水龙头的桶装并稀释好)。(6). 制一工作区域应急通道照明系统改进制一生产现场(安全通道)原规划安装照明线路时,未考虑配置一安全照明(远程开关控制)供应急等情况时使用,造成下午及晚上下班的员工均在黑暗中行走,极易导致各种安全隐患发生,故规划配置一定时控制开关(晚上下班时间上下10分钟定期开启)的照明灯(两处)。等等各项工作的改进,过程中均有责任人主导且均能按指定目标完成,使得部门6S工作在本年度均能有续进行。二:技术改进项目1. 标准件及加工工艺更改:1).模具日期章箭头指示极易转动(注塑过程自行转动)及箭头旋转槽极易变形导致无法旋转:原因1:日期章直径6/8/10/12mm
12、与镶件配合部分未止转造成注塑过程自行转动;改进1:要求设计更改结构(日期章外径底部增加定位结构),后续导入所有新品模具制造;原因2:箭头旋转槽型芯硬度偏软(HRC30)使得注塑厂人员在旋转时极易变形,甚至出现无法旋转需回厂更换;改进2:要求设计更新此标准件技术要求(由HRC30改为HRC60),后续导入所有新品模具制造!2).高光前壳模具斜顶连接杆易烧伤卡死:原因1:斜顶连接杆两侧平面部分未开储油槽,影响润滑效果;改进1:重新修订标准件连接杆图纸(两侧平面部分未开储油槽),并要求外购供应商按要求加工到位,后续导入所有新品模具制造(先行导入50x70前壳模具并跟踪效果);原因2:与连接杆配合的导
13、向套硬度偏硬,影响配合效果;改进2:原导向套材料738改为S55C,先行导入50x70前壳模具并跟踪效果;原因3:连接杆孔歪及连接杆间底部台阶干涉(密集连接杆部分),导致连接杆与导向套配合部分出现卡死;改进4:责任钳工在装配高光前壳模具至顶针板部分时需严格把关连接杆在复位及顶出状态是否顺畅,需保证配合顺畅的情况下方可进一步装模。2.外购模架加工及技术要求改进1).技术要求需明确模架吊环孔深度及配置全新吊环,确保现场起吊安全原因1:吊环孔深度无法安装到位;改进1:重新修订外购模架吊环孔加工的技术要求,即需保证吊环孔加工后能锁到底并保证配置吊环系全新,同时后续要求将此项列入必检项目;原因2:吊环因
14、频繁使用后已达使用寿命;改进2:定期清理并封存现场存在安全隐患的吊环(钳工徐安定、陈清彬/生产陈怀森主导);原因3:吊环或孔部分螺纹有碰伤,造成吊环无法安装到位;改进3:组织现场员工培训模具起吊前需确保吊环锁到底。2).模架止口、方型辅助器等结构改动a.后壳模具模架周圈凸台止口原留于动模,未能有效保护后壳定模型腔分型面及滑块,建议将周圈凸台止口留于定模,确保定模止口高度高于模具分型面;b.前后壳模具模架方型辅助器厚度太薄(18-25mm),其强度未能有效保证模具大批量生产(模具于注塑机上装模错位等引起烧伤),建议加大方型辅助器厚度(增加标准);c.原订购模架图纸顶针板中托司部分未要求需同步装配
15、于模架上,极易导致中托司丢失及装配不良,建议增加该项要求务必将中托司安装到位后方能与模架同时回厂。3).修改模架推杆加工技术要求鉴于新品外购模架回厂时出现推杆螺孔(M10*22mm)深度不足问题,导致推杆螺孔频繁出现返工后方能装配,经与设计组沟通确认并修正如下技术说明: a.设计订购模架时推杆长度按大于实际使用长度5-10mm订做,确保推杆头部螺孔被切掉部分不大于10mm! b.设计订购模架时推杆螺牙深度按30mm订做(经检测之前回厂模架推杆螺牙深度均为22mm左右),确保推杆头部被切掉10mm后螺牙深度需大于18mm.3. 修改大型模具支撑柱固定螺钉过孔加工尺寸a.改进前频繁出现因支撑柱过孔
16、让位不够使得模具无法顺利装模,大大影响钳工装模效率;原因系支撑柱理论单边配合间隙2.5mm,但支撑柱外形(毛坯)比理论大0.1-0.8mm左右、支撑柱端面未能与外圆垂直及钳工在钻固定支撑柱的螺钉过孔时按单边间隙0.5-1mm左右进行作业(主要原因),等等综合误差导致支撑柱无法装配!b.改进后要求设计于图纸标注具体尺寸(单边间隙0.1-0.15mm)(原标注:螺钉过孔),同时后续要求钳工务必按设计要求作业,此方式应可大大提升钳工装模效率!4. 修改增加内部模具更改通知单事宜鉴于今年模具更改事宜日趋增多且趋于老龄化,为今后更能详细体现需更改模具的模况,以便厂部及时判断模具能否实施更改(模具是否超过
17、保修等),经与设计组沟通拟在现行设计组通报的模具更改通知表格上增加模具开模日期及模具注塑产量,具体信息可由生产保障课协助填报。5. 热流道结构改进1)改进自制热流道本体内孔直径15mm加工工艺针对现行我厂自制热流道本体内孔(¢15mm)存在的缺陷(表面粗糙),导致钳工清胶困难、注塑生产时胶口容易冷胶等现象,大大的影响了模具整体品质,故做以下几点加工工艺改进说明:原因: 原自制热流道本体¢15mm孔由车床上钻孔加工,故表面粗糙!对策: 本体¢15mm孔改成深孔钻加工,表面粗糙度应可满足要求,但需配合制作工装夹具方可装夹钻孔,相关工装结构(需热处理)已加工完成并导入制
18、作加工!2)改进自制热流道本体加工工艺及加热圈功率针对新品39x70后壳BF1模具T1过程胶口易碳化问题(自制热流道),做如下改进: a.本体胶口(¢8.77mm)侧面直段太长(约10mm),极易引起胶口堵塞、碳化并导致型腔皮纹面腐蚀生锈,胶口直段太长原因系主钳工在本体车成型后未继续送火花清角(本体主流道¢16mm与胶口¢8.77mm过渡处需由单边斜角15度过渡),现行因残胶较多无法继续用电火花清角,故采用钳工磨成型刀直接钻铰成型!-此工艺经改进由钳共钻铰可行,故后续统一由钳工徐安定主导钻铰成型! b.2本体加热圈由功率850W改成700W,具体加热效果待T2调试
19、验证!6. 新品模具动模小镶件固定台阶结构改进针对新品前后壳模具动模小镶件挂台厚度(固定台阶)大部分均设计成5mm(含有排布顶针的镶件),此结构尺寸对于含有排布顶针的镶件存在极大的安全隐患,在顶针烧伤的情况下极易使小镶件被带出(挂台被剪切掉),故做如下改进:a.对于未排布顶出件的镶件台阶可继续按 5mm 厚度设计加工;b.对于有排布顶出件的镶件台阶厚度需按大于 8mm 设计加工;7. 新品模具推杆油槽结构改进针对近半年来屡次出现新品模具推杆烧伤咬死现象(如39x70后壳/50x80前壳模具等推杆烧伤咬死事故),已严重影响了公司的排产计划,为降低类似事故的发生几率,做如下改进: a.原推杆油槽间
20、距40mm系模架厂家按标准尺寸加工,但已不能满足现有生产润滑要求,故要求设计订购模架时需提供推杆相关尺寸(油槽间距改成20mm)给采购协商订购(备注说明); b.钳工装配模具过程需保证所有推杆装配良好(推杆不与让位部分干涉),且需润滑到位; c.为确保模具顶出配件不被冷凝水腐蚀生锈引起烧伤卡死,已要求注塑厂林和志通知车间定期做好喷防锈剂工作,另要求钳工注意跟踪回厂修改模的模具顶出配件是否生锈,如生锈需及时反馈杨海明处备案并做处理。8. 热电偶正负极统一标识针对近期新品模具自制热流道出现多次温控异常无法出胶事故,经分析主要原因系热电偶正负极接反造成,造成钳工接反原因系外订热电偶正负极标识未与我厂
21、达成共识(需确保红线为负极),故经与外协热流道配件厂家研讨并形成共识需确保红线为负极,后续由品管把关对于不符合要求的需退货更换。9. 修改模架检验单针对32x83后壳模具加工过程发现M48吊环无法锁到底事宜(部门自行返工),该模架系2/5到厂且检验时未能及时发现M48吊环无法锁到底,经落实原模架质量检验单未体现该检验项,即原模架质量检验单已未能满足现行高光模具需求,经协商后做以下几点必检项的表单修改:a.吊环螺牙是否能按要求旋到底、方型辅助器能否安装到位、双托铜导套是否配齐等;b.复位杆孔中心是否与模具基角一致;推杆螺牙深度及油槽是否按要求加工到位;c.动定模板上的螺钉装配情况,重点系需保证垂直度。10. 新品斜顶热处理工艺改进针对新品39X83机型内审时达成的共识,后续拟对窄边框模具斜顶(较薄)热处理工艺进行调整,同时需提前做好相关实验验证,具体如下:1).热处理实验验证跟踪: 因现行3983系列模具斜顶比较薄,原先热处理加工工艺已经不能适应,经过试验用吊炉方式热处理(工件钻工艺孔,用铁丝吊着处理),工件几乎没有变形(测试件工件为180MM×20MM×7.2MM,其中一件平面度为0.07MM,另外一件为0.03MM,热处理后检测,工件平面度和原先一样),2).新品较薄斜顶热处理加工工艺建议调整为: a
温馨提示
- 1. 本站所有资源如无特殊说明,都需要本地电脑安装OFFICE2007和PDF阅读器。图纸软件为CAD,CAXA,PROE,UG,SolidWorks等.压缩文件请下载最新的WinRAR软件解压。
- 2. 本站的文档不包含任何第三方提供的附件图纸等,如果需要附件,请联系上传者。文件的所有权益归上传用户所有。
- 3. 本站RAR压缩包中若带图纸,网页内容里面会有图纸预览,若没有图纸预览就没有图纸。
- 4. 未经权益所有人同意不得将文件中的内容挪作商业或盈利用途。
- 5. 人人文库网仅提供信息存储空间,仅对用户上传内容的表现方式做保护处理,对用户上传分享的文档内容本身不做任何修改或编辑,并不能对任何下载内容负责。
- 6. 下载文件中如有侵权或不适当内容,请与我们联系,我们立即纠正。
- 7. 本站不保证下载资源的准确性、安全性和完整性, 同时也不承担用户因使用这些下载资源对自己和他人造成任何形式的伤害或损失。
最新文档
- 2024年纺织品设计师证书考试知识树构建试题及答案
- 加拿大中文试题及答案
- 广告设计师如何提升2024年考试综合素质试题及答案
- 天一试题及答案物理
- 深入研究2024年国际商业设计师的职业选择试题及答案
- 2024年助理广告师考试管理能力试题及答案
- 德语课堂考试题及答案
- 2024年助理广告师考试疑难重点试题及答案
- 弱电运行考试试题及答案
- 探索国际商业美术设计师考试试题及答案
- 应急疏散的标识与规范
- 光伏项目服务承诺书
- 人教版三年级下册数学口算题题卡1000道带答案可打印
- 《儿科护理》 课件 22.3.1婴儿沐浴法
- 竣工结算审计服务投标方案(2024修订版)(技术方案)
- 《健康成年人身体活动能量消耗参考值》
- 热力学统计物理-第四版-汪志诚-课后答案
- 《铁路工务维修现场实战技巧》课件 任务2.9轨道检查仪作业
- 中国常规肺功能检查基层指南(2024年)解读
- 【MOOC】广告创意学-湖南大学 中国大学慕课MOOC答案
- 水域景观课件用
评论
0/150
提交评论