摘 要
塑料注射模具是工业生产的基础工艺设备,在电子、汽车、电机、电器、仪表、家电和通讯等产品中,60%~80%的零部件,都要依靠模具成形。它不仅直接影响工业产品的水平,也是一个国家工业化程度和机械制造工业技术水平的综合体现。
照相机外壳是一类体积适中,形状、结构较为简单的塑料零件。根据照相机外壳的结构确定模具的结构方案,利用塑件的三维零件图,确定模具的主要结构方式,进而画出其模具的CAD装配图和零件图。
通过对塑件的结构分析,本次设计采用一模四腔设计,滑块侧抽芯机构,实现照相机外壳侧孔的生成;采用侧浇口形式;塑件的体积适中,采用推杆推出实现脱料。采用此模具结构不仅可以保证塑件的表面要求和尺寸精度,而且生产率高、成本低、结构简单,可行性强,是一副实用性很强的模具。
关键词:注塑模具;照相机外壳;塑件;斜滑块
The camera shell injection mold design
Abstract
Plastic injection mould is the basis of process equipment in industrial production, in the electronic, automobile, motor, electrical appliance, instrument, home appliances and communication products, 60%-80% of the parts, must rely on forming die. It not only directly affect the level of industrial products, is a comprehensive reflection of a country industrialization and machinery manufacturing industry technical level.
Camera housing is a kind of medium in size, shape, simple structure of plastic parts. According to the camera shell structure determine the structure scheme of the mould, plastic parts of the 3D part drawings, the main structure of dies, and then draw the production of plastic parts CAD parts and assembly plans.
Through the structural analysis of plastic parts, the design adopts the design of a mold four cavity, slanted slide block core-pulling mechanism, realization of generating camera housing side hole; the side gate; moderate volume of plastic parts, the push rod is introduced to achieve stripping. The die structure can not only ensure the surface requirements of plastic parts and precision, and high productivity, low cost, simple structure, strong feasibility, is a very practical mould.
Key words: injection mold; camera housing; plastic parts; Oblique slippery
主要符号表
G——注塑机的实际最大注射量,或g;
T——注塑机的额定锁模力,t;
q——熔融塑料在模腔内的压力,;
S——注射机开模行程,mm;
——塑料的平均收缩率;
——制品的设计公差;
——模具制造公差;
——型芯或成型孔中心距;
——制品孔或凸台中心距;
——动模板受的总压力,MPa;
F——塑件浇注系统在动模上的投影面积,;
P——型腔压力,一般取25~45MPa,取32MPa;
E——塑料的弹性模量,;
——塑料的成型收缩率,查表取;
——型芯的脱模斜度,为1°
——塑料的泊松比,查表得
——与及有关的系数,
——塑料与型芯间的静摩擦因数;
——推杆最大应力,
c——型芯成型部分的平均周长,mm;
h——型芯被塑料包紧部分的长度,mm;
p——单位面积的包紧力,MPa
——推杆最大应力,
——抽芯力,N
——冷却介质的体积流量,;
——单位时间(每分钟)内注入模具中的塑料质量,
——单位重量的塑件在凝固时所放出的热量,
——冷却介质的密度,
——冷却介质的比热容,
——冷却介质的体积流量,
——冷却管道孔壁与冷却介质之间的传热膜系数,
——模温与冷却介质温度之间的平均温差,℃
目 录
1 绪论 1
1.1概述 1
1.2模具发展现状及发展方向 1
1.2.1塑料模具工业的发展现状及方向 1
1.3本课题的内容和具体要求 3
1.3.1本课题的内容 3
1.3.2具体要求 3
2 模具方案的论证和选择 4
2.1 ABS注射成型的原理及工艺过程 4
2.1.1注射成型的原理 4
2.1.2注塑成型工艺过程 4
2.1.3注射成形工艺参数 4
2.2 注塑模具的基本组成 4
2.2.1基本组成 5
2.2.2注塑模具装配图的技术要求 5
3 注射机的选择和型腔数目的确定及分布 6
3.1塑件材料的选择 6
3.2塑件的基本资料 6
3.2.1产品资料 6
3.3ABS注射工艺性 6
3.4型腔数目的确定及分布 7
3.5注射机的选择 8
3.5.1注射量的校核 8
3.5.2锁模力的校核 8
3.5.3最大注射容量校核 9
3.5.4注射压力校核 9
3.5.5模具厚度的校核 9
3.5.6开模行程的校核 9
3.6分型面的选择原则 10
3.6.1分型面的选择原则 10
3.6.2分型面的分类 10
3.6.3分型面的确定 10
4 排气系统的设计 12
5 浇注系统的设计 13
5.1浇注系统设计的原则 13
5.1.1了解塑料的成型特性 13
5.1.2布局合理 13
5.1.3防止型芯和塑件的变形 13
5.1.4减小流程及塑料耗量 13
5.1.5排气良好 13
5.1.6修整方便,保证塑件外观质量 13
5.2主流道设计 13
5.3冷料穴设计 14
5.4分流道设计 14
5.5浇口设计 14
5.5.1浇口的主要作用 15
5.5.2浇口位置的选择原则 15
5.6浇口套的选择 15
6 拉料杆的设计 16
7 成型零件的设计 17
7.1凹模、凸模的结构设计 17
7.1.1凹模的结构设计 17
7.1.2凸模的结构设计 17
7.2成形零件钢材选用 17
7.2.1成形零件对钢材的要求 17
7.3成型零件工作尺寸 17
7.3.1工作尺寸分类和确定 17
7.3.2影响塑件尺寸精度的因素如下。 18
7.4成型零件工作尺寸的计算 19
7.4.1凹模尺寸计算 19
7.4.2凸模和型芯的尺寸计算 19
7.4.3型芯中心距或成型孔中心距尺寸计算 20
7.5动模板强度校核 20
8 脱模机构的设计 22
8.1脱模机构的基本要求 22
8.2脱模机构的设计原则 22
8.3推出机构的确定 22
8.4脱模力的计算 22
8.5推杆强度的校核 23
8.6复位杆的设计 24
9 导向机构的设计 26
9.1导向机构的作用和设计原则 26
9.1.1导向机构的作用 26
9.1.2设计原则 26
9.2导柱导套的设计 26
9.2.1导柱的设计 27
9.2.2导套的设计 27
9.3导向孔的布局 27
10 抽芯机构的设计 29
10.1抽芯机构概述 29
10.2抽芯机构的确定 29
10.3斜导柱抽芯机构的结构设计 29
10.3.1斜导柱分型与抽芯机构 29
10.3.2斜导侧向分型与抽芯机构应具备以下基本功能 29
10.4斜导柱抽芯机构的有关参数计算 29
10.4.1抽芯距S 30
10.4.2斜导柱倾斜角的确定 30
10.4.3抽芯力的计算 30
10.4.4斜导柱直径的计算 30
10.4.5斜导柱长度的计算 31
10.5斜导柱的结构 31
10.6滑块的设计 32
10.7楔紧块的设计 32
10.8导滑槽的设计 33
10.8.1设计要点 33
10.8.2导滑槽和滑块的配合关系 33
10.8.3导滑槽的结构 33
11 温度调节系统的设计 34
11.1温度调节对塑件质量的影响 34
11.2温度调节系统的要求 34
11.3模具温度对制品质量的影响 34
11.3.1变形 34
11.3.2尺寸精度 34
11.3.3力学性能 34
11.4模具冷却装置的设计 34
11.4.1冷却装置的设计要点 34
11.4.2确定冷却系统的参数 35
11.4.3水嘴的结构形式 37
11.4.4冷却水道的结构 37
12 其它结构零部件设计 38
13 模具的材料 39
13.1塑料模具对模具材料的要求 39
13.2塑料模具常用材料 39
13.3模具的淬火硬度 39
13.4模具的表面粗糙度 39
13.5热处理的选择 39
13.6模具材料性能分析 40
14 模具的可行性分析 41
14.1模具的特点 41
14.2经济效率与市场前景分析 41
15 结论 42
参考文献 43
致 谢 44
毕业设计(论文)知识产权声明 45
毕业设计(论文)独创性声明 46
1 绪论
1.1概述
塑料注射模具是工业生产的基础工艺设备。振兴和发展我国的模具工业,日益受到人们的重视和关注。在电子、汽车、电机、电器、仪表、家电和通讯等产品中,60%~80%零部件,都要依靠模具成形。用模具生产制作所表现出来的高精度、高复杂程度、高一致性、高生产率和低消耗,是其他加工制造方法所不能比拟的。模具又是“效率放大器”,用模具生产的最终产品的价值,往往是模具自身价值的几十倍、上百倍。因此,塑料模具技术,特别是制造精密、复杂、大型模具的技术,已成为衡量一个国家机械制造水平的重要标志之一。




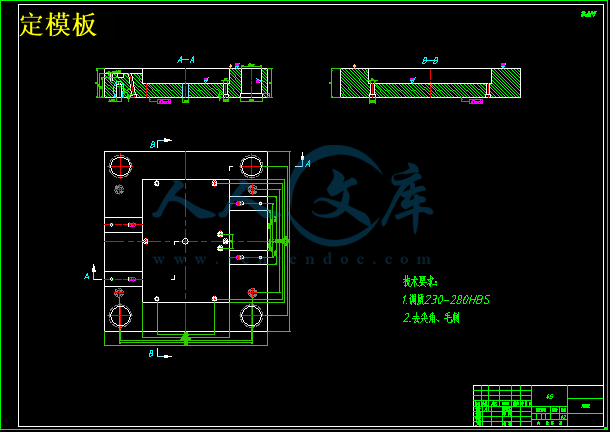
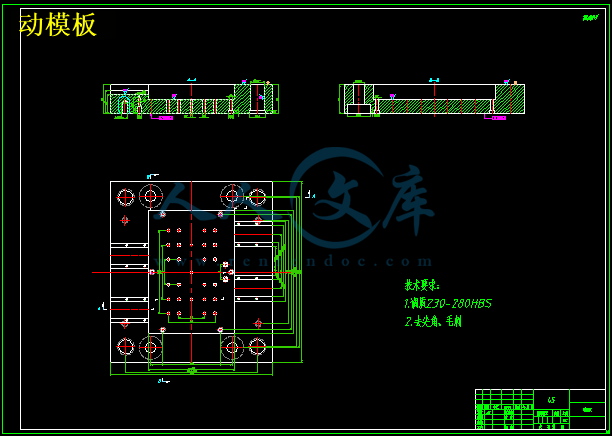







