PE400X600复摆颚式破碎机的设计【新版本、含CAD图纸、说明书文档】
收藏
资源目录
压缩包内文档预览:(预览前20页/共33页)
编号:17972723
类型:共享资源
大小:5.12MB
格式:ZIP
上传时间:2019-04-20
上传人:机****料
认证信息
个人认证
高**(实名认证)
河南
IP属地:河南
50
积分
- 关 键 词:
-
新版本、含CAD图纸、说明书文档
复摆颚式破碎机设计【
含CAD图纸
400复摆颚式破碎机的设计【
复摆颚式破碎机的设计【
600复摆颚式破碎机
600
复摆颚式破碎机
600复摆颚式破碎机设计
- 资源描述:
-





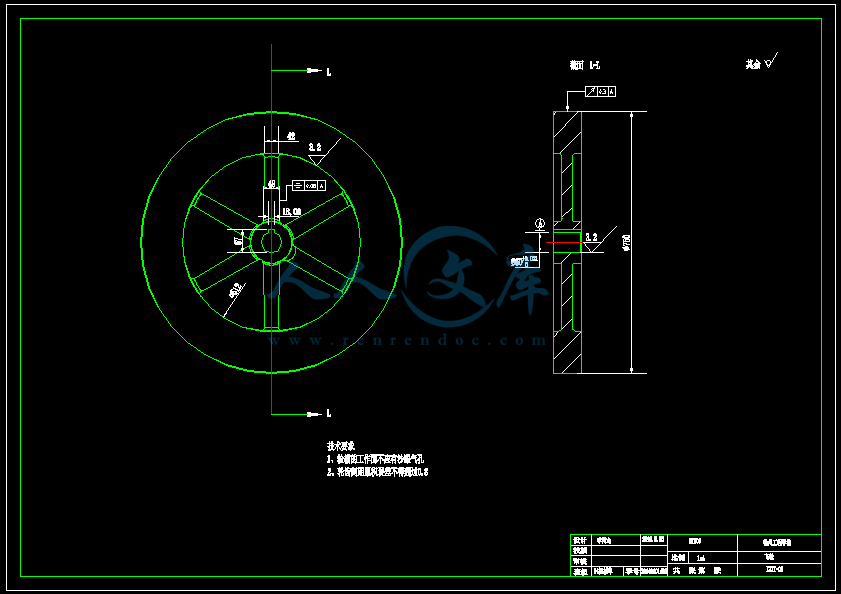







- 内容简介:
-
毕 业 设 计(论 文) 任 务 书 学院(系):机电工程学院专 业:机械设计制造及其自动化学生姓名:学 号:设计(论文)题目:PE400600复摆颚式破碎机的设计 起 迄 日 期:2018年 2月 26日 2018年 5月 26日指 导 教 师:教研室主任: 发任务书日期: 2018年 2月 28日 毕 业 设 计(论 文)任 务 书 1毕业设计的背景:国外从上世纪中后期开始利用计算机仿真技术对颚式破碎机机构、腔型、产量和磨损等进行优化,研制开发出无塞点、高度低、重量轻、产品粒型好、产量高的高性能、低能耗的新型颚式破碎机,从而大大提高了破碎机的性能,缩短了产品开发周期,提高了产品的市场竞争力。然而国内对颚式破碎机的仿真优化设计的研究主要限于对特定型号的颚式破碎机编写相应程序进行优化设计,这些程序大多重用性差,只能解决特定型号中的特定问题。然而破碎机的优化内容是根据不同客户要求需要经常变化的,因而仿真优化设计工作经常要重复大量而繁锁的编写程序工作,费时费力,而且还延长了产品开发周期。2毕业设计(论文)的内容和要求:了解PE400600复摆颚式破碎机的工作原理并确定其设计方案;进行PE400600复摆颚式破碎机动颚部分设计;主要零件的结构设计与强度计算;用AutoCAD软件绘制PE400600复摆颚式破碎机零件图以及装配总图,要求视图完整,其中装配图一张,零件图若干,满足本科毕业设计要求。参考文献至少15篇以上,另外有2篇以上外文文献。完成至少1万5千字的论文,以及至少4000汉字的英文翻译3主要参考文献:1 孙康,陈峰,王军锋. PE250400型复摆颚式破碎机的参数设计. 矿山机械,2012(10):73762 机械设计手册.第五版.北京;机械工业出版社.20083 罗中华. 复摆颚式破碎机运动机构的优化设计.矿山机械,2012(01):58614 张敬孜. PE600900破碎机运动尺寸参数优化设计. 西华大学硕士论文.20145 成大先.机械设计手册M.第5卷.北京:化学工业民出版社,2008,3.6 金波,戴素江. PE7501060复摆颚式破碎机的设计计算.矿山机械.2007(01):46484毕业设计(论文)进度计划(以周为单位):18年第1、2周 毕业实习,学生提交实习报告、开题报告18年第3、4周 与指导老师进行讨论,确定最终设计方案18年第5、6周 进行PE400600复摆颚式破碎机动颚部分设计18年第7、8周 主要零件的结构设计与强度计算18年第911周 绘制装配图和主要零件图,完成毕业设计论文。18年第12周 提交毕业设计材料18年第13周 答辩教研室审查意见: 教研室主任签名: 年 月 日学院审查意见: 教学院长签名: 年 月 日5 毕业设计外文翻译学生姓名学院名称专业名称指导教师2012年5月26日 高速机床的高精密加工摘要目的:现代机床加工精密产品的三维加工的磨削速度超过20000转每分钟。硬加工和柔性加工的差异对机床的概念有影响。刚度和硬度的特性和变量是影响加工零件的精度和质量的原因。设计/方法/途径:本文介绍了一些有趣的具有不同概念的现代机床如:DCG (Drive in Centre of Gravity - Mori Seiki), LAF (Look Ahead Function on machine - Sodick),高速为20000-60000转每分钟,线性驱动等。从想法到加工零件的转变方式将会被演示。结果:为了达到高精度,满足机床上许多需要的功能是必须的。结果表明加工零件也取决于加工材料(硬度、结构、晶体尺寸)。研究局限性/含义:工程师的工作是准备与CAD-CAM软件相关的最优的数控程序。在提到的所有因素后加工和测量工件。创意/价值:对比预测的测量结果,让我们知道事实和对高精度产品的决定。关键词:制造与加工;加工;高速机床;精密加工;精密产品;柔性加工;硬加工1 简介现代机床的一些细节包括超模块,如旋转工作台、精密高转速主轴、棒料库、刀具库、工件库、激光零点测量系统、诊断过程的切削力测力机、频率传感器、声响传感器等1。加工时为了连接所有的模块,机床的计算机必须是最优秀的。计算机中的软件如神经网络、遗传算法、遗传编程、预测功能,这些都是用来保证加工过程中的最优切削参数2、3。世界各地的许多切削机床的制造商提供了机床空载时的精度水平。为了获得高精密产品,我们需要高水平性能的车床。性能越好,车床的价格也越高。顶级机床的价格是500000到1000000欧元,它的价格超过了三轴机床。带有驱动工具的三轴铣床和车床价格低于400000欧元。小型旧机床的传统加工没有现代化的高速,在个体制造业或刀具制造业也是非常有用。上面提到的机床价格低于200000欧元。它们大部分不能达到高速区,高速区是由更多的元素定义的,这将在这篇文章的下面章节给出。3D凹印抛光对获得较低的表面粗糙度是一项非常特殊的工作。这一工作耗时的主要方面是操作。那是因为它的自动化与驱动抛光的刀具和减少特殊切削技术的选择有关。所以确保选择球头铣刀、低切削深度、小进给量和很高的速度是必要的。因为技术是重要的软件和控制器,所以在自学控制器的基础上,它包括了复杂的优化的切削条件的大量知识4,5。自动进给最小化在使用3D磨具靠近表面加工和抛光时是很有用的。2 现代切削机床的内容我们所提到的模块也是有适应性。旋转工作台在工件自动夹紧装置的情况下是更有效的。我们已经实现设计和工艺6。图1给出了夹紧装置上相关液压控制的概念原理图。下图给出了机床电源,动力装置和空气和液压介质的控制系统。图1铣床上介质流从信号源到工作板的原理展示切削机床拥有高生产率,那是因为它享有现代传统系统的60支座床身等级作为卧式和立式切削机床的新概念,如图2。配有驱动刀具和双侧主轴切削机床的生产率也高。由于增加轴Z1、Z2和轴C1、C2,生产率比常规车床的生产率提高5-7倍。立式车床也是集成化加工的新概念,与卧式车床相比,它的原理晶片有更好的运转。图2是工件在主轴的下面。这也有可能是相对的,主轴在上面,切削刀具在旋转器和串联刀具夹紧系统上移动。想这样的机床会更精确、更精密、更高效。图2有两个旋转台、辅助轴承和Y轴的卧式车床和立式车床图3稳健的水平加工中心稳健的水平加工中心,如图3所示的多轴机床的模块和结构的粗糙概念。B轴称为水平调节控制轴4。它能够加工三维工件的复杂形状。因为急需要机床,所以我们有必要为机械加工准备有效的编程工程师。来自低等教育的普通管理工人不但不能提供最优的加工时间,而且还会提高生产成本。最新车床的床身低于60度。如图4,图5这样的角度给切削力组件的假设提供了最优解。振动是有限的,芯片流同样也是有规定的。下面的原理图介绍了两个主轴、两个旋转台和驱动刀具。在相反面加工的同时切削力会得到补偿。图4拥有两个旋转台和辅助轴承的卧式车床的基本结构图5拥有两个旋转台和相对主轴的卧式车床的基本结构最后的模型是多轴机床。该车床基本上包含了所有可能的模块和轴。由于主轴的左右两面,我们可以在没有后勤保证体系、双向定位和夹紧的条件下在同一台机床上完成产品的加工。铣床主轴生产的形状复杂的产品与7台不同机床的传统生产不一样。图6多轴加工中心现代机床的工作原理和控制器的收集模块如图7所示,传统的控制是数控,然后是计算机数控,最新的是中央处理器单元。所有的片段都与高速互联网总线连接相连。高功率的电机是交流的数字伺服电机。 图7带有CPU技术的CNC控制的现代机床的控制原理3 精密加工;理论和原理精加工可以通过更多的方法完成,如传统精细切削、光滑加工、滚动和后处理。传统的方法是由锋利的切削刃和小的进给率加工的。光滑加工是在切割刃切割较大半径R的现代加工方法,进给率大,去除率8倍大。如图8所示,通过观察加工的时间来获得所需的表面粗糙度是非常重要的。图8表面粗糙度和加工时间的对应图刀具材料对工件表面粗糙度有很重要的影响。特别是镀膜的类型如TiN,TiCN,TiALN将较少刀具的磨损,如图9。为了使刀具磨损最小,刀具的寿命要达到切削刃的标准。柔性切削加工会引起较好的滑动现象、更好的摩擦学接触和更好的表面粗糙度。如用所提到的硬质合金刀具,表面粗糙度会显著降低。图9不同镀膜的硬质合金材料的铣刀的刀具寿命球头铣刀是精加工中最理想的切削刀具。那种尖头铣刀可以使切削工件的硬度达到62HRc。刀具生产商们可以生产直径为0.5毫米带有两个出屑槽的刀具。这些刀具的每个切削刃都很锋利,而且还有非常精确的切削角。如图10所示,当超过加工时间后切削刃将会磨损。正常的理论磨损是在刀具的出屑槽,但是在刀具的中间部分,也就是刀具的中心部分也会有一些破损9。原因是切削速度越小,积削瘤对磨损也有影响10。刀具磨损和刀具的使用寿命取决于使用刀具的材料和刀具在加工表面上运行的次数。镀膜为TiALN或TiN的W或VB处的刀具磨损是最好的,如图11。图10球头铣刀上的不同磨损形状图11基于中间磨损的刀具磨损图表我们进行较多的实验后,得到精密加工的最优解是:多层镀膜后的最后一层镀膜是TiN12,这样刀具就会有较低的摩擦系数。如图12所示,刀具磨损是最小的。通常情况切削参数定义为a=0.1mm,f=0.05mm切削速度v=150-200m/min。只有20000到40000转每分钟的高速机床才有可能获得较小刀具直径。图12切削刃的刀具磨损图13告诉我们铣刀的圆头尖端上自由表面的刀具磨损是较大的。切削刃损坏在铣刀圆头尖端是可以看见的。出现这样的情况就是机床参数的错误决定。在这种情况下,原因是进给率太高。为获得更大的材料去除量只考虑增大进给率是不正确的。进给率必须保持很小。只有在更高的切削速度下我们才能获得更大的材料去除量。图13切削刃上的磨损4 抛光加工表面的最后一步是抛光。它只有在几何形状要求的公差不超过2微米时有用。抛光不但费时,而且需要手工驱动抛光刀具。使用这种方法抛光时,抛光的时间会缩短,因为抛光段上的振动能量会帮助抛光。如图14用模具进行闭合表面的最后精加工。结合精密研磨,抛光的时间从16小时缩短到3小时。图14用驱动刀具对工件手动抛光使用不同的人造钻石抛光凝胶也会缩短抛光时间。不同的凝胶用于不同的材料。抛光表面的硬度和粗糙度要求不同的人造钻石尺寸。凝胶的流动性和粘性同样影响抛光的时间,如图15。图15人造钻石抛光凝胶如上所述,抛光刀具的振动能量是有用的。图16是拥有超声波频率的抛光装置。这意味着从14到21赫兹,当工人不集中于他的工作时,这样的运动对表面是有危害的。在另一种情况下装置上的力较小时,表面会由于预热过高而损坏,这也是引起表面层再结晶的原因。图16超生波设备下的工件的手动/驱动/抛光5 机床Sodick的精密性和性能的案例研究机床的案例的研究是在模具工件产品上进行的。图17是原理运动图,这对产品获得所需的形状是必需的。作为第一次设计CAD的程序之一,输入设计是新的或者旧的部分会有所改变。如果那样,逆向工程将是数控编程快速编写的正确方法。计算机辅助设计是建立在CAM软件上的数控编程。故障是喷流的后置处理,这样每台机床的控制器就小多了。图18是许多现代模块集成的现代化车床的案例。工件库在加工中心的左边,较强的控制系统在加工中心的右边,最右边是刀具库。图17CAD-CAM测略模式的流程图图18高速加工中心Sodick MC430L正如我们前面所提到的许多现代模块包括SODICK机械加工中心。其中的一个很有趣的解释是因为高的进给速度对柔性加工很重要。这些特征保证了线性驱动电机。异步电动机的原理是基础,它是从线性形状的旋转发展来的。永久磁铁位于磁铁板中的线性转子处。电动机的外壳部分与电力和控制系统相连。这样的话我们可以对移动区域的每一点精确而快速的定位。所有的三轴都有各自的线性驱动系统。转台由Y,X轴驱动,Z轴是主轴的进给系统。 下一个试验是对所需部分的加工。一些重要的形状、尺寸和公差是在计算机辅助设计上的设计图上设计的。图19是有趣的表面光栅,作为产品的特殊表面设计它越来越现代化。三维设计展现了药片的不同形状。加工产品需要许多相似的形状,所以我们必须优化切削技术。机床上的程序可以使刀具快速换刀,这种情况我们可以描述为切削操作。刀具换刀系统为药片的小孔设计选择球片刀具。主轴在刀具库、零点检测系统和加工工件之间以快速的进给速度移动。为实现刀具直径的最佳切削速度所需的主轴上的切削工艺参数是28转每分钟。加工的进给速度是800-2300毫米每分钟,进给速度大小取决于精密加工的要求。一些加工表面的细节如图20和21。图21所示的麻点形状是很好的精密加工,在这种情况下,就不再需要手动抛光了,因为粗糙度值Ra=0.2微米。最后必须应用加工抛光来获得较好的表面粗糙度质量。用不同的切削参数和没有磨损的刀具可以使表面粗糙度值为0.5微米。通常在这之后就不需要手工抛光了。图20加工表面的细节用光栅制药是有趣的。铝模型的设计用于药片包装。图21加工表面的细节生产机床的各厂家将机床特性作为机床的质量证书。尺寸的精密性很有可能控制机床所有的轴。我们会测量铣床主轴相对于转台间的垂直度。因为是微米测量,所以我们用最好最精确的测量设备。机床生产商保证X和Y轴的值为0.007毫米。通过测量SODICK,X轴的值为0.004毫米。在实验室LABOD-卢布尔雅那大学的机械工程学院,我们得到了更好的结果:X,Y两轴都是0.002毫米。图22是提到的所有值的表格。图19测试产品案例研究的设计图22铣床主轴和转台间的垂直度6 总结现代的各类生产都基于切削技术参数的自我系统优化。首先是在策略金字塔上最顶层的精密高速机床。加工时间的减少对模具是必须的,模具加工是由拥有精密加工和抛光的现代高速铣床得到的。与传统加工方法相比,闭模表面的调整时间大约减少15%。软件测量的正确值0.05毫米比刀具的正确值大。这样的话最好用五轴机床。闭模和快速产品(短周期的铝合金铸模)的较小公差要求额外的模具功能,如真空封闭雕刻。通过试验和测量的偏差,我们将会额外的扩大技术数据库。随着越来越多和越好数据,我们可能使用CAM编程更加简短的手工加工来适应闭模表面加工。在汽车业中,部分材料的选择和发展能够在特定的力学性能和维修中遇到热量的条件下继续操作,与此同时维持它们的切削加工性能的特点能够保证使用材料的经济性。在切削刃处测试材料的加工会产生高温,这将损害刀具材料的性能。市面上能买到的刀具材料只能用在速度小的条件下。更高级的刀具材料如CBN能够在较高的切削速度的条件下生产高质量的零件。就像所有的刀具材料都一样,在切削表面产生的极限温度和压力的条件下,它们的刀具寿命是有限的。因为所有的刀具材料在高速切削的条件下都会失去它们的硬度,所以为最小化刀具-工件和刀具-晶片接口产生的温度制定特定的技术是必需的。在机械加工工艺的优化中,必须考虑加工零件的客户的需求。在汽车零件的加工中,表面质量、公差和生产率是客户制定的要求,其中加工零件的表面质量的主要体现是表面粗糙度和毛刺外观。提高使用刀具的性能不但非常困难、昂贵,而且CBN刀具的图层所含有的TiALN和TiN对有效的切削技术有很大的影响。未来,在高速条件下通过适当刀具材料、加工技术和刀具几何形状的合理选择,对软、硬材料的加工可以得到提高。图书分类号:密级:毕业设计说明书PE400600 复摆颚式破碎机的设计THE DESIGN OF PE400 X 600 COMPOUND JAW CRUSHER学生姓名 学号 班级 指导教师 专业名称机械设计制造及其自动化学院名称机电工程学院年 5 月 26 日毕业设计原创性声明本人郑重声明: 所呈交的毕业设计,是本人在导师的指导下,独立进行研究工作所取得的成果。除文中已经注明引用或参考的内容外,本设计说明书不含任何其他个人或集体已经发表或撰写过的作品或成果。对本文的研究做出重要贡献的个人和集体,均已在文中以明确方式标注。本人完全意识到本声明的法律结果由本人承担。论文作者签名: 日期: 年 5月 26日毕业设计版权协议书本人完全了解关于收集、保存、使用毕业设计的规定,即:本校学生在学习期间所完成的毕业设计的知识产权归所拥有。有权保留并向国家有关部门或机构送交设计说明书的纸本复印件和电子文档拷贝,允许说明书被查阅和借阅。可以公布说明书的全部或部分内容,可以将说明书的全部或部分内容提交至各类数据库进行发布和检索,可以采用影印、缩印或扫描等复制手段保存和汇编本说明书。论文作者签名:导师签名:日期年 5月 26日日期: 年 5月26 日 毕业设计(论文)开题报告 课题名称:PE400600复摆颚式破碎机的设计学生姓名:学号:指导教师:职称:讲师所在学院:机电工程学院专业名称:机械设计制造及其自动化 日期: 2018年 3月 16日 说 明1根据毕业设计(论文)管理规定,学生必须撰写毕业设计(论文)开题报告,由指导教师签署意见、教研室审查,学院教学院长批准后实施。2开题报告是毕业设计(论文)答辩委员会对学生答辩资格审查的依据材料之一。学生应当在毕业设计(论文)工作前期内完成,开题报告不合格者不得参加答辩。3毕业设计开题报告各项内容要实事求是,逐条认真填写。其中的文字表达要明确、严谨,语言通顺,外来语要同时用原文和中文表达。第一次出现缩写词,须注出全称。4本报告中,由学生本人撰写的对课题和研究工作的分析及描述,没有经过整理归纳,缺乏个人见解仅仅从网上下载材料拼凑而成的开题报告按不合格论。 5课题类型填:工程设计类;理论研究类;应用(实验)研究类;软件设计类;其它。6课题来源填:教师科研;社会生产实践;教学;其它 毕业设计(论文)开题报告课题名称PE400600复摆颚式破碎机的设计课题来源社会生产实践课题类型工程设计类1选题的背景及意义:我国自50年代生产 颚式破碎机以来,在破碎机设计方面经历了模拟,仿制、图解法设计阶段,目前正向计算机辅助设计阶段过渡。生产制造的颚式破碎机越来越大、性能越来越好,品种越来越多,并在国际上占有一定的市场。我国曾以前苏联颚式破碎标准TOCT7084-80为依据,制定了颚式破碎机国标送审稿,对颚式破碎机的设计、制造和使用提出了更高的要求。因此全面总结颚式破碎机在设计、使用和测试方面的经验,积累合适我国破碎机结构特点的实验数据和数据,建立破碎机最优化设计的理论与方法并使之推广普及是提高我国颚式破碎机技术性能,赶超国际先进水平的关键2研究内容拟解决的主要问题:1.鄂式破碎机总体设计方案:(1)研究颚式破碎机的构造。(2)研究颚式破碎机动颚部分。(3)研究颚式破碎机的受力情况。2.确定主要参数:(1).破碎腔的高度 (2).钳角(3).偏心距3.电动机的选择: (1).电动机的容量 (2).电动机的型号3研究方法技术路线:1 鄂式破碎机的总体设计方案的拟定;(1)研究颚式破碎机的构造:确定鄂式破碎机由动颚板、定颚板、偏心轴、机架和肋板以及一些辅助零件组成。(2)研究颚式破碎机动颚部分:为减轻重量,采用焊接结构,按结构特点可分为箱型结构和非箱型加筋结构,本次设计可采用箱型结构。(3)研究颚式破碎机的受力情况:根据设计要求对其主要零件(如偏向轴、肘板等)进行设计计算及强度计算。2.确定主要参数:粉碎腔的高度取决与粉碎比H=(2.25-2.5)B;根据破碎机活动颚板与固定颚板的夹角可确定钳角的大小;偏心距大小是由动颚行程通过画机构图来初步确定。3.电动机的选择:应用维雅德公式Na=0.0114LDmax可求得电动机容量;首先确定采用三相异步电动机,具体型号可由额定功率确定。4研究的总体安排和进度计划:18年第1、2周 毕业实习,学生提交实习报告、开题报告18年第3、4周 与指导老师进行讨论,确定最终设计方案18年第5、6周 进行PE400600复摆颚式破碎机动颚部分设计18年第7、8周 主要零件的结构设计与强度计算18年第911周 绘制装配图和主要零件图,完成毕业设计论文。18年第12周 提交毕业设计材料18年第13周 答辩5主要参考文献:1 孙康,陈峰,王军锋. PE250400型复摆颚式破碎机的参数设计. 矿山机械,2012(10):73762 机械设计手册.第五版.北京;机械工业出版社.20083 罗中华. 复摆颚式破碎机运动机构的优化设计. 矿山机械,2012(01):58614 张敬孜. PE600900破碎机运动尺寸参数优化设计. 西华大学硕士论文.20145 成大先.机械设计手册M.第5卷.北京:化学工业民出版社,2008,3.6 金波,戴素江. PE7501060复摆颚式破碎机的设计计算.矿山机械.2007(01):4648指导教师意见:该生拟进行PE400600复摆颚式破碎机的设计,前期对该领域的研究进展进行了较为详尽的了解。在此基础上,提出了该研究的主要问题,研究的技术路线可行。预期可按计划完成毕业设计的研究工作,同意选题。 指导教师签名: 年 月 日教研室意见:同意 教研室主任签名: 年 月 日学院意见: 教学院长签名: 年 月 日7PE400600复摆鄂式破碎机,姓名,选题背景,因为我国今年来GDP发展迅猛,矿产资源的合理开发,使得各种类型的破碎机大量涌入市场,而我们的复摆鄂式破碎机依靠破碎比大,产量高,结构简单,工作可靠,维护方便等优点,快速的在各类的破碎机中脱颖而出,主要研究内容,1动力源:整个机器主要由电机带动 2传动部分:整个机器的传动机构可以看作是一个曲柄摇杆机构,原理相似 3破碎部分: 整个机器的破碎工作主要是由破碎机的动颚来完成,主要组成部分,破碎机主要由机架、偏心轴、动颚板,定颚板、肘板这五个部分组成,工作原理,电动机产生的驱动转矩,通过带轮传递给偏心轴,然后偏心轴驱使动颚板进行复杂的平面运动,对石料进行破碎,动态图,主要根据公式,电机的选择,-主电动机最大功率,-进料口尺寸,-最大的给料尺寸,总结,主要是对颚板,齿板等部件进行了设计,对V带进行了参数计算,对电动机的型号进行了选择。,请各位老师批评指导, Copyright by International OCSCO World Press. All rights reserved. 2007 VOLUME 24 ISSUE 1 September 2007 Occasional paper405 of Achievements in Materials and Manufacturing Engineering of Achievements in Materials and Manufacturing Engineering High precision machining on high speed machines J. Kopa* Faculty of Mechanical Engineering, University of Ljubljana, Askerceva 6, SI-1000 Ljubljana, Slovenia * Corresponding author: E-mail address: janez.kopacfs.uni-lj.si Received 15.04.2007; published in revised form 01.09.2007 Manufacturing and processing AbstrAct Purpose: Modern Machines for precision products for three dimensional machining have by milling over 20.000 rpm. Differences between hard and soft machining have influences on concept of machines. Stiffness and rigidity are characteristics and variables which caused the precision and quality of machined part. Design/methodology/approach: This paper introduce some of interesting modern machine tools with different concept as DCG (Drive in Centre of Gravity - Mori Seiki), LAF (Look Ahead Function on machine - Sodick), high speed 20.000 60.000 rpm, linear drive, etc. The way from idea to machined part will be shown. Findings: To achieve high precision it is necessary to fill out many request function on machine. Results on machined part depend also from machined material (hardness, structure, size of crystals). Research limitations/implications: Engineers job is to prepare the optimal CNC (PNC) program on connection of CAD CAM softwares. After all mentioned factor test work piece is machined and measured. Originality/value: Comparison between results data on plan and measurement shows us the reality and give us decision around high precision product. Keywords: Manufacturing and processing; Machining; High speed machine tools; Precision machining; Precise products; Soft machining; Hard machining 1. Introduction Some specifics of modern machine tool are included over modules, as rotation table, precise high RPM spindle, bar magazine, tools magazine, work pieces magazine, laser zero point measurement system, cutting forces dynamometer for diagnostic of process, frequencies sensor, acoustic sensors, etc., 1. To connect all modules in working action, the machine computer must be excellent. Softwares in computer as NN (Neural Network), GA (Genetic Algorithm), GP (Genetic Programming), LAF (Look Ahead Function), are assuring all time in machining process optimal cutting parameters 2, 3. Many of producers of cutting machine tools all over of the world provide machines in idle level of precision. To achieve precision production we need high level of machine quality. The highest quality caused also high price of machine. Top level ob machine price are 500.000 to 1.000.000 euros for more then three axis machine. 3axis milling machines and turn machines with driven tools are under 400.000 euros. Classical machining on little older machines - no modern high speed, is also very useful in individual production or in tool making industries. The prices of mentioned machines are under 200.000 euros. They are also mostly not able to achieve HS region. HS region is defined with more of elements, which will be shown in some of next chapter of this paper. 3D gravures polishing is very special job for achieving low surface roughness. Its time consumption technology, mostly handy made. That for it has to be automated with driven polishing tool and minimize with choice of special cutting technology. To ensure it is necessary to choice ball nose cutter, low depth of cut, small feed rate and very high speed. After technology are important maters software and controllers, where is include huge knowledge around complex optimization of cutting condition on base of self-learning controller 4,5. Automaticaly federate minimization is very usefull before finishing and polishing closing surfaces by 3D dies and moulds. 1. Introduction Occasional paper406 Journal of Achievements in Materials and Manufacturing Engineering J. Kopa Volume 24 Issue 1 September 2007 2. Specifics of modern cutting machine tools Mentioned modules are also adaptable. Rotation table is more effective in the case of automated clamping device for work piece. Design and workmanship was realized 6. Figure 1 shows schematically concept to connect hydraulically control on clamping device - above. Below part of figure shows machine cell, powered and control over air and hydraulic medium. Fig.1. Schematically present of medium flow from source to palette on milling machine High productive are turn machines, which are shared in modern classical system on 60 support bed degree as horizontal and new concept of vertical turn machine, Figure 2. With driven tools equipped and both side spindle turn machine is high productive. With added axis as Z1, Z2 and C1, C2 is production 5-7x higher as on conventional lathe 7. Vertical turn machine is also new concept of intensive machining, where the chips have better flow away versus horizontal principle. On Figure 2 is concept with below the spindle with work piece. It is possible also opposite; to be spindle above and the cutting tools are moving over revolver and cascade tool clamping system. Machine like this is more rigid, more precise and high productive. Fig. 2. Horizontal turn machine tool with two revolvers, auxiliary spindle and Y axis and vertical turn machine tool Fig. 3. Robust horizontal machining centre Robust horizontal machining centre, Figure 3 shows rough concept of modules and structure more axis machine. B axis is so called axis nr.4. It gives possibility of complex shapes of 3D work piece. Machine is also more exacting and it is necessary to prepare effective programming engineer of machining. Simple managing from low educated worker gives not optimal machining time and also higher production costs. The latest turn machine bed is under angle 60 degrees. Angle like this on Figure 4, Figure 5 gives optimal solution for assumption of cutting force components 8. The vibrations are limited and chips flow is regulated as well. Schematically introduce below shows two spindles, two revolvers and driven cutters. With opposite side machining in same time make forces compensations. Fig. 4. Basic structure of horizontal lathe with two revolvers and auxiliary spindle revolver operation panel spindle revolver 2 opposite spindle chip transporter Fig. 5. Basic structure of horizontal lathe with two revolvers and opposite spindle Step more and the last model is multi axes machine. It is basically turn machine with all possible modules and axis. With right and left side of spindle is possible to finish the product on the same machine without logistics, double positioning and clamping. Milling spindle produce the shapes in complexity versus classical production on 7 different machines. milling spindle oposite spindle spindle revolver milling spindle Fig. 6. Multi axis turn- machining centre Working principles and controller of modern machine collect modules as shows Figure 7. Classical control was NC, after then CNC, but new one is CPU unit. All segments are connected with fast internet bus connection. High power electro motors are AC concept, digital servo motors. PLC fast internet bus conecton spindle drive digital AC servo motors axes drive X, Y, Z, B digital AC servo motors CAD/CAM ethernet RS-232 memory card CNC CPU unit information machine server Fig. 7. Working principle of modern machine tool with CNC control with CPU technology 3. Precision machining; theory and principles Fine machining can be done on more ways, as classical fine cutting, smooth machining, rolling and finishing. Classical way was cutting with sharp cutting edge and small feed rate. Smooth 2. specifics of modern cutting machine tools 407 Manufacturing and processing High precision machining on high speed machines 2. Specifics of modern cutting machine tools Mentioned modules are also adaptable. Rotation table is more effective in the case of automated clamping device for work piece. Design and workmanship was realized 6. Figure 1 shows schematically concept to connect hydraulically control on clamping device - above. Below part of figure shows machine cell, powered and control over air and hydraulic medium. Fig.1. Schematically present of medium flow from source to palette on milling machine High productive are turn machines, which are shared in modern classical system on 60 support bed degree as horizontal and new concept of vertical turn machine, Figure 2. With driven tools equipped and both side spindle turn machine is high productive. With added axis as Z1, Z2 and C1, C2 is production 5-7x higher as on conventional lathe 7. Vertical turn machine is also new concept of intensive machining, where the chips have better flow away versus horizontal principle. On Figure 2 is concept with below the spindle with work piece. It is possible also opposite; to be spindle above and the cutting tools are moving over revolver and cascade tool clamping system. Machine like this is more rigid, more precise and high productive. Fig. 2. Horizontal turn machine tool with two revolvers, auxiliary spindle and Y axis and vertical turn machine tool Fig. 3. Robust horizontal machining centre Robust horizontal machining centre, Figure 3 shows rough concept of modules and structure more axis machine. B axis is so called axis nr.4. It gives possibility of complex shapes of 3D work piece. Machine is also more exacting and it is necessary to prepare effective programming engineer of machining. Simple managing from low educated worker gives not optimal machining time and also higher production costs. The latest turn machine bed is under angle 60 degrees. Angle like this on Figure 4, Figure 5 gives optimal solution for assumption of cutting force components 8. The vibrations are limited and chips flow is regulated as well. Schematically introduce below shows two spindles, two revolvers and driven cutters. With opposite side machining in same time make forces compensations. Fig. 4. Basic structure of horizontal lathe with two revolvers and auxiliary spindle revolver operation panel spindle revolver 2 opposite spindle chip transporter Fig. 5. Basic structure of horizontal lathe with two revolvers and opposite spindle Step more and the last model is multi axes machine. It is basically turn machine with all possible modules and axis. With right and left side of spindle is possible to finish the product on the same machine without logistics, double positioning and clamping. Milling spindle produce the shapes in complexity versus classical production on 7 different machines. milling spindle oposite spindle spindle revolver milling spindle Fig. 6. Multi axis turn- machining centre Working principles and controller of modern machine collect modules as shows Figure 7. Classical control was NC, after then CNC, but new one is CPU unit. All segments are connected with fast internet bus connection. High power electro motors are AC concept, digital servo motors. PLC fast internet bus conecton spindle drive digital AC servo motors axes drive X, Y, Z, B digital AC servo motors CAD/CAM ethernet RS-232 memory card CNC CPU unit information machine server Fig. 7. Working principle of modern machine tool with CNC control with CPU technology 3. Precision machining; theory and principles Fine machining can be done on more ways, as classical fine cutting, smooth machining, rolling and finishing. Classical way was cutting with sharp cutting edge and small feed rate. Smooth 3. Precision machining; theory and principles Occasional paper408 Journal of Achievements in Materials and Manufacturing Engineering J. Kopa Volume 24 Issue 1 September 2007 machining is modern way of cutting with big radius R on cutting edge. Fed rate is huge and remove rate is 8 x bigger. It is very important from view of machining time for achieve required surface roughness, Figure 8. required roughness Rth machining time t Fig. 8. Surface roughness quality versus machining time Cutting tool material has important influence on work piece surface roughness. Especially type of coating as TiN, TiCN, TiAlN caused lower toll wear, Figure 9. As result of minimal toll wear is toll life to achieve criteria of cutting edge changing. Movic as soft cutting caused good sliding phenomena, better tribology contact and better surface roughness. Ra achieved with mentioned tolls is significant lower as by inserts of tungsten carbides. Cutting speed m/min Tool life of cutter m no coating Fig. 9. Tool life of milling cutter carbide cutting tool material with different coatings Ball nose milling cutter is ideal cutting tool for fine machining. Phenomena of that pencil milling tools is possibility to cut work piece hardness to 62 HRc. Producers of cutting tools are able to produce diameter of cuter 0.5 mm with two flutes. Every cutting edge is very sharp and has very precise cutting angles. After machining time the cutting edges are weared, Figure 10. Normal, theoretical wear is on flutes, but middle part of cutter, it means central part can has also some breakages 9. The reason is in smaller cutting speed, where BUE is assist able 10. Tool wear and tool life depends of used cutting tool materials and Nr. of passes of tool over the machined surface. Tool wear W or VB is the best by coating TiAlN/TiN 11, Figure 11. Central wearTool flank wear Fig. 10. Different wear shapes on the pencil milling ball end nose Number of crossings Medium wear W mm Fig. 11. Toll wear diagram based on middle of cutter After more experiments we carried out optimal solution for precise machining: It is multilayer coatings with last layer of TiN 12, which has very low tribological coefficient. Toll wear is minimal, as shows Figure 12. Normally the parameters of cutting must be defined as a= 0.1mm, f=0.05mm and cutting speed v = 150 - 200 m/ min. By small cutter diameter it is possible to achieve only on HS machine, which has 20.000 to 40.000rpm 13. Fig. 12. Tool wears on cutting edge Figure 13 shows toll wear of the free surface on the rounded tip of the milling tool which is quite big. The break down of the cutting edge is visible on the rounded tip of the milling tool. It is the case of wrong decision of machining parameters. Feed rate in this case was too high. To achieve bigger material remove is not feed rate right solution. It must stay small. Only with higher cutting speed we achieve bigger removal chip volume. Fig. 13.Toll wear on cutting edge by pencil cutter bed case 5. Polishing Last step by finishing of machined surface is polishing. It is useful only in the case, when geometry shape is not request to be in tolerances over 2 m. Polishing is very time consumption and using driven hand polishing tools is request. On this way polishing time is shorter, because vibrant power on polishing segment helped as well. Figure 14 shows last fine machining on closing surface by mould tool. With combination of precise milling, the polishing time was shorted from 16 hours to 3 hours. Fig. 14. Hand polishing of work piece with driving tool Using different diamante polishing gel help also to shorter the polishing time. Different gels are using for different materials. Hardness of polished surface and Ra request different size of diamante cons. Gel fluid and his viscosity is influencing on intensively/time of polishing, Figure 15. Fig. 15. Diamante polishing gel As mentioned above, vibrations powered polishing tools are very effective. Figure 16 shows polishing device with ultrasound powering frequency. It means from 14 to 21 KHz. Movements as this one can be danger for surface in case, when worker is not really concentrated on his obligation. Force on device has to be very gently in another case the surface can be damage over preheating, what caused recrystalization of surface layer. Fig. 16. Hand/driven/polishing of work piece with ultrasound device 6. Case study of precise and ability of machine Sodick Machining case study was carried out over the mould work piece product. Figure 17 shows schematically actions, which are necessary to achieve requested shape of product. As first was done design over one of CAD program. Input of design is new or old part with some changes. In that case RE Reverse Engineering is right way for quick preparing of CNC program. After CAD is CNC program created over CAM software. Missing is still jet post processing, where is for every machine tool controller a little bit another. Case of modern turn machine with integration of many modern modules shows Figure 18. Work pieces magazine is on left and strong control system is on right side of machine centre. Very right is toll magazine. 409 Manufacturing and processing High precision machining on high speed machines machining is modern way of cutting with big radius R on cutting edge. Fed rate is huge and remove rate is 8 x bigger. It is very important from view of machining time for achieve required surface roughness, Figure 8. required roughness R
- 温馨提示:
1: 本站所有资源如无特殊说明,都需要本地电脑安装OFFICE2007和PDF阅读器。图纸软件为CAD,CAXA,PROE,UG,SolidWorks等.压缩文件请下载最新的WinRAR软件解压。
2: 本站的文档不包含任何第三方提供的附件图纸等,如果需要附件,请联系上传者。文件的所有权益归上传用户所有。
3.本站RAR压缩包中若带图纸,网页内容里面会有图纸预览,若没有图纸预览就没有图纸。
4. 未经权益所有人同意不得将文件中的内容挪作商业或盈利用途。
5. 人人文库网仅提供信息存储空间,仅对用户上传内容的表现方式做保护处理,对用户上传分享的文档内容本身不做任何修改或编辑,并不能对任何下载内容负责。
6. 下载文件中如有侵权或不适当内容,请与我们联系,我们立即纠正。
7. 本站不保证下载资源的准确性、安全性和完整性, 同时也不承担用户因使用这些下载资源对自己和他人造成任何形式的伤害或损失。

人人文库网所有资源均是用户自行上传分享,仅供网友学习交流,未经上传用户书面授权,请勿作他用。