三星手机充电器外壳注塑模设计
30页 9000字数+说明书+UG三维图+9张CAD图纸【详情如下】
UG三维图.rar
三星手机充电器-模具CAD图纸9张.dwg
三星手机充电器外壳-说明书目录.doc
三星手机充电器外壳注塑模设计说明书.doc
目录
第一章 产品技术要求和工艺分析……………………………… 2
产品技术要求…………………………………………… 3
1.1.1产品设计图 ………………………………………… 3
1.1.2 产品技术要求 …………………………………… 3
2.2 塑件的工艺分析………………………………………… 3
2.2.1 尺寸和精度 …………………………………… 3
2.2.2常用热塑性塑料成型特点 ………………………… 4
2.3 塑件材料性能…………………………………………… 4
2.4 制件成型工艺性能………………………………………4
3.3成型零件的工作尺寸计算…………………………………5
第二章 拟定成型方案及动作原理 …………………………………7
2.1 分型面位置的确定 ………………………………………8
2.2 导柱、导套的设计 …………………………………… 9
2.3 浇注系统的设计 ……………………………………… 9
2.3.1 主流道设计 …………………………………… 10
2.3.2 分流道设计 …………………………………… 11
2.3.3分流道的布置形式…………………………………12
2.3.4 浇口设计 ……………………………………… 15
第三章 模架及注塑机的选择及成型零件设计 ……………………18
3.1 注塑机的选择 …………………………………………15
3.1.1外壳体积的计算 ………………………………15
3.1.2外壳质量的计算 ……………………………… 15
3.1.3 塑料注射机参数 ……………………………… 16
3.1.4 选标准模架 …………………………………… 17
3.2 注塑机相关参数的校核……………………………… 18
3.2.1 注塑压力的校核 ……………………………… 18
3.2.2 锁模力的校核 ………………………………… 18
3.2.2模具与注塑机装模部位相关尺寸的校核 …… 19
第四章 推出机构设计 ……………………………………… 19
4.1 推出机构的设计原理 ………………………………… 19
4.2 推出机构 ……………………………………………… 19
4.3 推出机构的结构设计要求 …………………………… 20
4.4 推出力的计算 ………………………………………… 22
4.5 推出机构的结构特点 ………………………………… 24
4.6 冷却系统的设计 ………………………………………25
4.7 装配图…………………………………………………… 27
参文献…………………………………………………………… 30
设 计 过 程
此毕业设计工件名称为充电器外壳件,材料为ABS,收缩率为0.4%---0.6%。
一、产品技术要求和工艺分析
1.1 产品技术要求
1.1.1 产品设计图
1.产品图 1.1.2 产品技术要求 塑料零件的材料为ABS,其工件要求无气泡、残缺,表面有较高的光洁度, 无杂质,性能可靠。2.2 塑件的工艺分析
2.2.1尺寸和精度
尺寸:塑件尺寸的大小受到塑料材料流动性好坏的制约,塑件尺寸越大,要求材料的流动性越好,流动性差的材料在模具型腔未充满前就已经固化或熔接不牢,导致制品缺陷和强度下降。
尺寸精度:影响塑件制品尺寸精度的因素是比较复杂的,如模具各部分的制造精度,塑料收缩率,成型工艺及模具加工表面质量等等。本次设计是外壳的模具设计,精度采用的是IT12。
2.2.2 常用热塑性塑料成型特点
虽然吸水性好,但高温时对水分比较敏感,会出现银丝、气泡及强度下降现象,所以加工前必须进行干燥处理,而且最好采用真空干燥法;熔融温度高,熔体黏度大,流动性差,所以成型时要求有较高的温度和压力;熔体黏度对温度十分敏感,一般采用提高温度的方法来增加熔融塑料的流动性。
2.3 塑件材料性能 此外壳是采用ABS注塑成的。查相关手册可知其特性。
2.4工艺性分析
2.4.1该工件尺寸适中,一般精度要求为一模四腔,并要求不对其进行后加工。
2.4.2为满足制品表面质量及嵌件的定位精度,采用二板模侧口进胶。
2.4.3为了加工方便和模具装配方便,采用整体结构。 2.4.5按工件图纸经三维造型得
Vs=7.02L
查表6-1塑料ABS密度为1.02---1.08g/cm
单件塑料重量m=ρv =1.06×7.02≈7.44g
3.成型零件的工作尺寸计算
影响塑件尺寸精度的因素较为复杂,主要存在以下几方面(1)、零件的制造公差;(2)、设计时所估计的收缩率和实际收缩率之间的差异和生产制品时收缩率波动;(3)、模具使用过程中的磨损。以上三方面的影响表述如下:1、制造误差:△z=ai=a(0.45 +0.001D)其中,D — 被加工零件的尺寸,可被视为被加工模具零件的成型尺寸;△z — 成型零件的制造公差值;i — 公差单位;a — 精度系数,对模具制造最常用的精度等级。2 成型收缩率波动影响 其中, — 塑件成型收缩率;LM — 模具成型尺寸;LS — 塑件对应尺寸。3 型腔磨损对尺寸的影响为简便计算,凡与脱模方向垂直的面不考虑磨损量,与脱模方向平行的面才考虑磨损。考虑磨损主要从模具的使用寿命来选定,磨损值随产量的增加而增大;此外,还应考虑塑料对钢材的磨损情况;同时还应考虑模具材料的耐模性及热处理情况,型腔表面是否镀铬、氮化等。有资料介绍,中小型模具的最大磨损量可取塑件总误差的1/6(常取0.02~0.05mm),而对于大的模具则应取1/6以下。但实际上对于聚烯烃(如像PP)、尼龙等塑料来说对模具的磨损是很小的,对小型塑件来说,成型零件磨损量对塑件的总误差有一定的影响,而对于大的塑件来说影响很小。
2.4.4由于工件要求采用一模四腔如图所示:

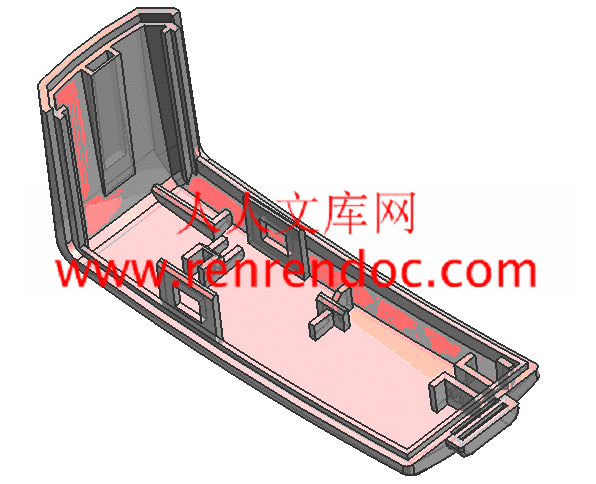
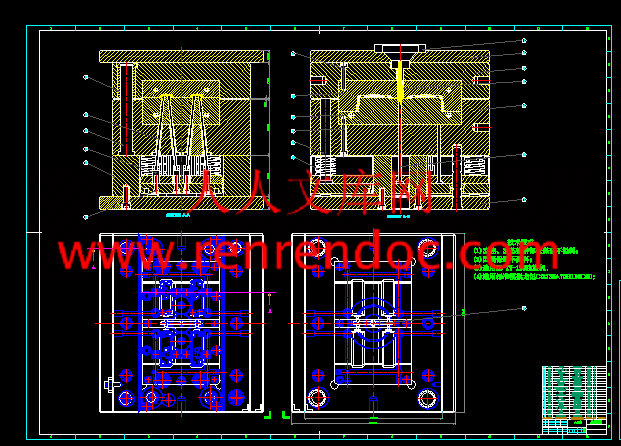