【温馨提示】 购买原稿文件请充值后自助下载。
[全部文件] 那张截图中的文件为本资料所有内容,下载后即可获得。
预览截图请勿抄袭,原稿文件完整清晰,无水印,可编辑。
有疑问可以咨询QQ:414951605或1304139763
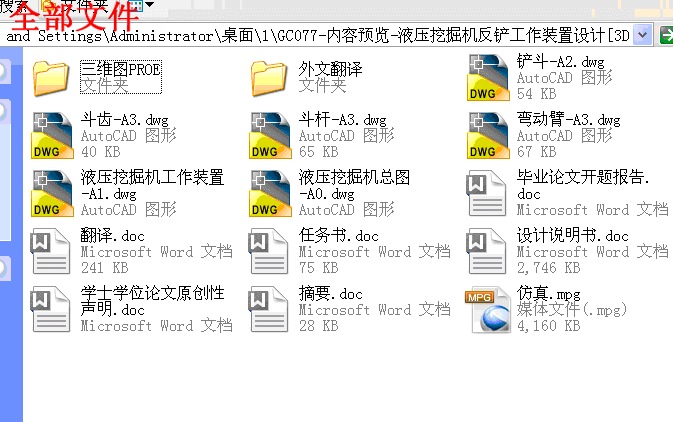
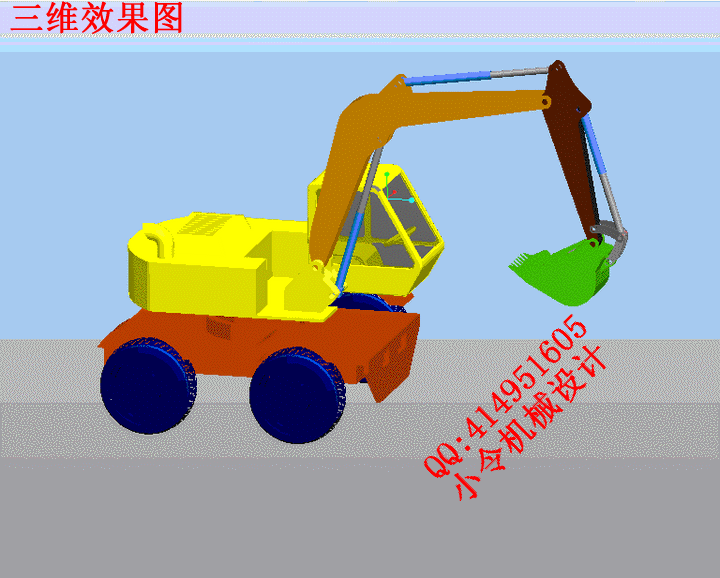
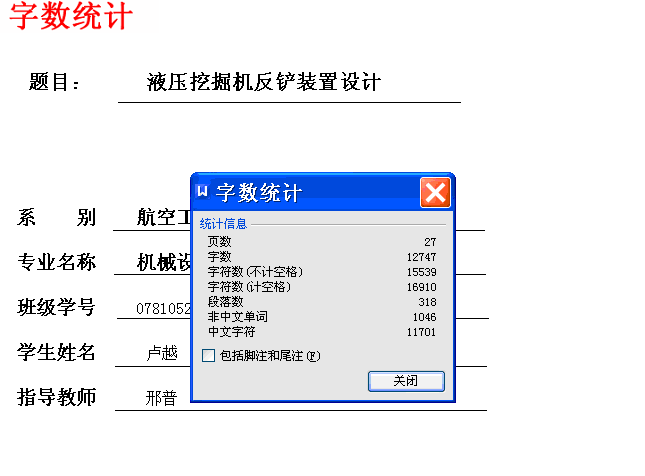
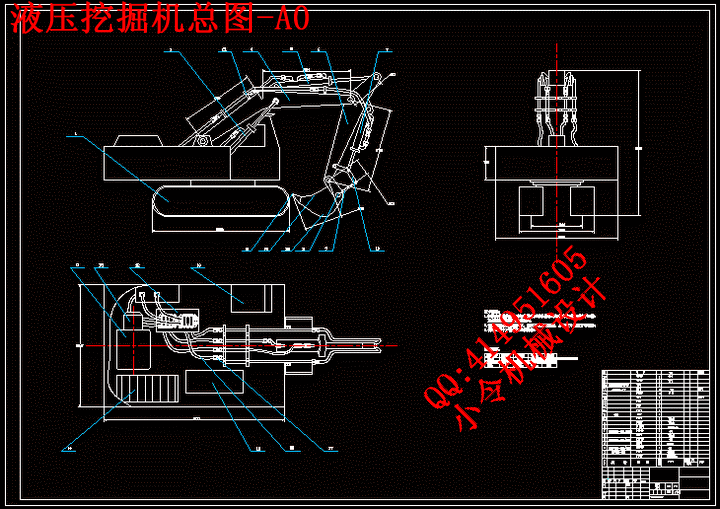



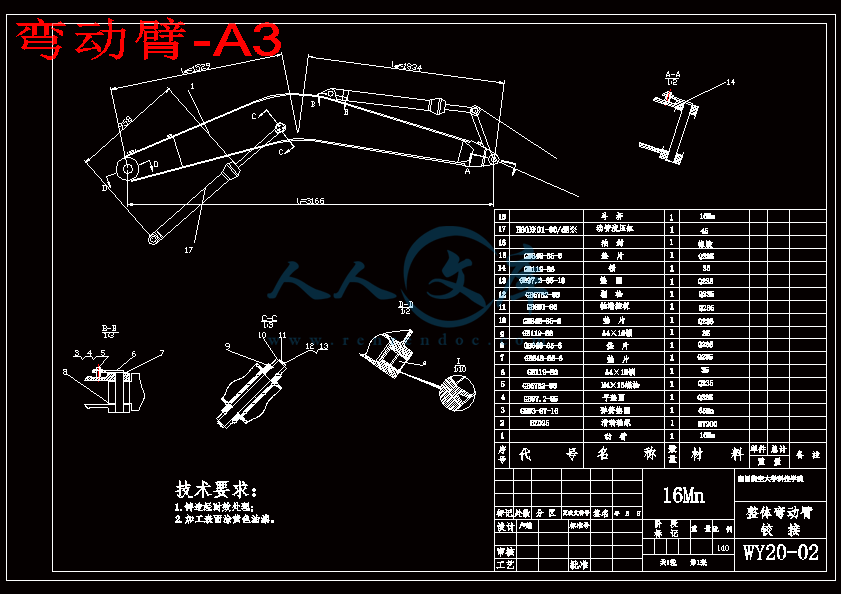

摘 要
本次设计的题目是液压挖掘机反铲装置机构。与其它类型的挖掘机相比,这种类型的挖掘机因有良好通过性能应用最广,对松软地面或沼泽地带还可采用加宽、加长以及浮式履带来降低接地比压。
液压挖掘机反铲装置的主要特点为:反铲是中小型液压挖掘机的主要工作装置。液压挖掘机的反铲装置由动臂,斗杆铲斗,以及动臂油缸,斗杆油缸,铲斗油缸和连杆机构组成。其构造特点是各部件之间的连接全部采用铰接,通过油缸的伸缩来实现挖掘工作中的各种动作。动臂的小铰点与回转平台铰接,并以动臂油缸来支撑和改变动臂的倾角,通过动臂油缸的伸缩可使动臂绕小铰点转动而升降。斗杆铰接于动臂的上端,斗杆与动臂的相对位置由斗杆油缸来控制,当斗杆油缸伸缩时,斗杆便可绕动臂上焦铰点转动。本次设计的主要参数是斗容量0.2m3,它属于中小型液压挖掘机,主要设计挖掘机的工作装置。
在设计中,采用了轮胎式行走装置,来满足要求。上部转台是全回转式,因此它可在一个更大的范围内工作。又因采用液压传动控制而使整机性能得以改善。与机械式挖掘机相比,其挖掘力提高到2~3倍,整机质量约为5吨,挖掘力约为30kN,最大卸载高度约为2.65m,最大挖掘深度4.2m,最大挖掘半径约为5.728m,从中可以看出整机作业能力有了很大的改进,不仅挖掘力大,且机器重量轻,传动平稳,作业效率高,结构紧凑。另外,还对挖掘机的工作装置提出基于结构推理的机构方案创新设计方法。
关键词:液压挖掘机 ;反铲机构;设计
ABSTRACT
This designed topic is the marchinghydraulic excavatorexcavational organization. Compared with other types excavators, thiskind of type excavator used very universal that because has good through theperformance, also may use tolengthenswidens as well as the floating type caterpillar bandto reduce pressure for the soft ground or the bogregion.
The hydraulic excavator main characteristic is: The small and medium-sized hydraulic excavator shovel is the main work device. Hydraulic excavator shovel device by the arm, dou stem bucket, and arm oil cylinder, dou rod oil cylinders, the bucket of cylinder and linkage mechanism. Its structure feature is between components All adopt the connection by oil cylinder hinged adjustable to realize the various movements excavation. Moving arm little hinge point and rotary platform, and with hinged arm oil cylinder to support and change the dip Angle, through arm arm Oil cylinder telescopic can make moving arm around small hinge point lifting rotation. Dou lever arm hinged on the upper arm, dou rod and the relative By dou pole position to control oil cylinder, when dou rod oil cylinder telescopic, dou lever arm can be around the upper energizer hinge point rotation. This designed main parameter is scoop capacity 0.2m3, it is long to themiddle and small scale hydraulic excavator, mainly design the excavator,s the work installment and the hydraulic transmissionprinciple.
In the design, used marching walked the installment to satisfied request. Upside the turnplate is the entire rotation , thereof it may work in a greater scope. And further because uses the hydraulicsteering to enable the entire machine performance to improve. Compared with the mechanical type excavator, its excavation strength enhance to 2 ~ 3 times, the entire machine weight approximately is 5 tons,the excavation strength approximately is 30kN, the biggest unloadinghigh approximately is 2.65m, biggest digging depth is 4.2m, the biggestexcavation radius approximately is 5.728m, thus can see theentire machine work ability to have the very big improvement, not onlyexcavation strength big, but also machine weight light, transmissionsteadyly, work efficiency is high, the structure is compact. Moreover, butalso proposes to the excavator work installment based on the structureinference organization plan innovation design method.
Key word:Hydraulic pressure excavator;Excavation organization ;Hydraulic system ;Innovation design
目 录
1 绪论1
1.1液压挖掘机的工作特点和基本类型1
1.1.1液压挖掘机的主要优点1
1.1.2液压挖掘机的基本类型及主要特点2
1.2反铲装置的工作原理2
2 总体设计方案4
2.1工作装置设计方案原则4
2.2液压系统设计方案原则(总体)4
2.2.1对液压系统作业动作要求4
2.2.2对液压系统基本的要求5
3挖掘机工作装置设计.............................6
3.1确定动臂的结构形式………………………………………………………………………..6
3.2动臂、铲斗机构参数的选择…………………………………………………………...6
3.2.1反铲装置总体方案的选择………………………………………………………….6
3.2.2铲斗参数的选择7
3.2.3动臂机构参数的选择8
4液压挖掘机工作装置运动仿真13
4.1模型建立………………………………………………………………………………..13
4.2构件运动配装……………………………………………………………………..……15
4.3构件运动仿真………………………………………………………………………17
结论………………………………………………………………………………………………21
致谢………………………………………………………………………………………………22
参考文献…………………………………………………………………………………………23
1 绪论
液压挖掘机是在机械传动挖掘机的基础上发展起来的。它的工作过程是以铲斗的切削刃切削土壤,铲斗装满后提升、回转至卸土位置,卸空后的铲斗再回到挖掘位置并开始下一次的作业。因此,液压挖掘机是一种周期作业的土方机械。
液压挖掘机与机械传动挖掘机一样,在工业与民用建筑、交通运输、水利施工、露天采矿及现代化军事工程中都有着广泛的应用,是各种土石方施工中不可缺少的一种重要机械设备。
在建筑工程中,可用来挖掘苦坑、排水沟,拆除旧有建筑物,平整场地等。更换工作装置后,可进行装卸、安装、打桩和拔除树根等作业。
在水利施工中,可用来开挖水库、运河、水电站堤坝的基坑、排水或灌溉的沟渠,疏浚和挖深原有河道等。
在铁路、公路建设中,用来挖掘土方、建筑路基、平整地面和开挖路旁排水沟等。
在石油、电力、通信业的基础建设及市政建设中,用来挖掘电缆沟和管道等。
在露天采矿场上,可用来剥离矿石或煤,也可用来进行堆弃、装载和钻孔等作业。
所以,液压挖掘机作为工程机械的一个重要品种,对于减轻工人繁重的体力劳动,提高施工机械化水平,加快施工进度,促进各项建设事业的发展,都 起着很大的作用。据建筑施工部门统计,一台斗容量1.0m3的液压挖掘机挖掘Ⅰ~Ⅳ级土壤埋,每班生产率大约相当于300~400个工人一天的工作量。因此,大力发展液压挖掘机,对于提高劳动生产率和加速国民经济的发展具有重要意义。
1.1液压挖掘机的工作特点和基本类型
1.1.1液压挖掘机的主要优点
液压挖掘机在动力装置之间采用容积式液压静压传动,即靠液体的压力能进行工作。液压传动与机械传动相比有许多优点。
①能无级调速且调速范围大,例如液压马达的最高转速与最低转速之比可达1000∶1。
②能得到较低的稳定转速,例如柱塞式液压马达的稳定转速可低达1r/min.
③快速作用时,液压元件产生的运动惯性小,加速性能好,并可作调整反转。例如电动机在启动时的惯性力矩比其平稳盍时的驱动力矩大50%,而液压马达则不大于5%,加速中等功率电动机需1s到数秒,而加速液压马达只需0.1s。
④传动平稳,结构简单,可吸收冲击和振动,操纵省力,易实现自动化控制。
⑤易于实现标准化、系列化、通用化。
基于液压传动的上述优点,液压挖掘机与机械传动挖掘机相比,具有下列主要特点。
①大大改善了挖掘机的技术性能,挖掘力大、牵引力大,机器重量,传动平稳,作用效率高,结构紧凑。液压挖掘机与同级机械传动挖掘机相比,挖掘力约高30%,例如1.0m液压挖掘机铲斗挖掘力120~150KN,而同级机械传动挖掘机只有100KN左右。
挖掘机在工作时的主要动作包括行走、转台回转和工作装置的作业动作,其中动作最频繁的是回转和工作装置的循环往复运动。这种入选运动一般速度不高,而所需作用力却很大,要求在短时间内通过变速或换向来完成各种复杂动作。机械传动挖掘机完成上述运动需通过磨擦离合器、减速器、制动器、逆转机构、提升和推压机构等配合来完成。因此,机械传动挖掘力不仅结构复杂,而且还要产生很大的惯性力和冲击载荷。而液压挖掘机则不需要庞大和复杂的蹭传动,大大简化了结构,也减少了易损件。由于结构简化,液压挖掘机的质量大约比相同斗容量的机械传动挖掘机轻30%,不仅节省了钢材,而且降低了接地比压。液压挖掘机上的各种液压元件可相对独立布置,使整机结构紧凑、外形美观,同时也易于改进或变型。
②液压挖掘机的液压系统有防止过载的能力,所以使用安全可靠,操纵简便。由于可采用液压先导控制,无论驱动功率多大,操纵均很灵活、省力,司机的工作条件得到改善。更换工作装置时,由于不牵连转台上部的其他机构,因此更换工作装置容易,而机械式挖掘机则受到提升机构和推压机构的牵连和限制。