GD1146-90型对辊成型机设计
84页 16000字数+说明书+任务书+8张CAD图纸【详情如下】
GD1146-90型对辊成型机设计说明书.doc
减速器A1.dwg
型板A2.dwg
型辊组件A1.dwg
大带轮A2.dwg
总装图A0.dwg
扉页-任务书-目录格式.doc
摘要.doc
辊心A2.dwg
辊轮轴A3.dwg
齿轮A3.dwg
目 录
绪论1
1.电机选型及传动比计算2
1.1选择电动机2
1.1.1选择电动机的类型和结构形式2
1.1.2选择电动机的容量2
1.2计算传动装置的总传动比并分配各级传动比3
1.2.1传动装置的总传动比3
1.2.2分配各级传动比3
2.V带设计计算4
2.1确定计算功率4
2.2选择带型4
2.3确定带轮基准直径4
2.4验算带的速度5
2.5初定中心距5
2.6确定基准长度5
2.7确定实际轴间距6
2.8验算小带轮包角6
2.9单根V带的基本额定功率6
2.10单根V带的功率增量6
2.11V带的根数6
2.12单根V带的预紧力7
2.13带轮的结构7
2.13.1小带轮的结构7
3.基本参数计算8
各轴的转速、传递功率、转矩8
4.同步齿轮减速箱齿轮的设计计算9
4.1I轴齿轮设计计算9
4.1.1选择齿轮材料9
4.1.2初定齿轮主要参数9
4.1.3校核齿面接触疲劳强度12
4.2Ⅱ轴齿轮设计计算14
4.2.1选择齿轮材料14
4.2.2初定齿轮主要参数14
4.2.3校核齿面接触疲劳强度17
4.3Ⅲ轴齿轮设计计算19
4.3.1选择齿轮材料19
4.3.2初定齿轮主要参数19
4.3.3校核齿面接触疲劳强度22
4.4Ⅳ轴齿轮设计计算24
4.4.1选择齿轮材料24
5.同步齿轮减速箱轴的设计计算29
5.1Ⅰ轴的设计计算29
5.1.1选择轴的材料29
5.1.2初步估算轴的的直径29
5.1.3轴上零部件的选择和轴的结构设计29
5.1.4轴的受力分析30
5.1.5轴的强度计算32
5.2Ⅱ轴的设计计算33
5.2.1选择轴的材料33
5.2.2初步估算轴的的直径33
5.2.3轴上零部件的选择和轴的结构设计33
5.2.4轴的受力分析34
5.2.5轴的强度计算37
5.3Ⅲ轴的设计计算38
5.3.1选择轴的材料38
5.3.2初步估算轴的的直径38
5.3.3轴上零部件的选择和轴的结构设计39
5.3.4轴的受力分析39
5.3.5轴的强度计算44
5.4Ⅳ轴的设计计算44
5.4.1选择轴的材料44
5.4.2初步估算轴的的直径44
5.4.3轴上零部件的选择和轴的结构设计45
5.4.4轴的受力分析45
5.5.5轴的强度计算53
6.同步齿轮减速箱轴承的校核54
6.1I轴轴承的校核54
6.1.1计算轴承支反力54
6.1.2轴承的派生轴向力54
6.1.3轴承所受的轴向载荷54
6.1.4轴承的当量动载荷55
6.1.5轴承寿命55
6.2II轴轴承的校核55
6.2.1计算轴承支反力56
6.2.2轴承的派生轴向力56
6.2.3轴承所受的轴向载荷56
6.2.4轴承的当量动载荷56
6.2.5轴承寿命57
6.3III轴轴承的校核57
6.3.1计算轴承支反力57
6.3.2轴承的派生轴向力57
6.3.3轴承所受的轴向载荷57
6.3.4轴承的当量动载荷58
6.3.5轴承寿命58
6.4IV轴轴承的校核58
6.4.1计算轴承支反力59
6.4.2轴承的派生轴向力59
6.4.3轴承所受的轴向载荷59
6.4.4轴承的当量动载荷59
6.4.5轴承寿命60
6.5V轴轴承的校核60
6.5.1计算轴承支反力60
6.5.2轴承的派生轴向力60
6.5.3轴承所受的轴向载荷60
6.5.4轴承的当量动载荷61
6.5.5轴承寿命61
7.同步齿轮减速箱键的校核61
7.1I轴键的校核61
7.2II轴健的校核62
7.3III轴健的校核62
7.4IV轴健的校核62
7.5V轴键的校核63
8.同步齿轮减速箱箱体及附件设计计算63
8.1箱体设计63
8.1.1箱体结构设计63
8.2减速器附件63
8.2.1检查孔及其盖板63
8.2.2通气器63
8.2.3轴承盖和密封装置63
8.2.4定位销64
8.2.5油面指示器64
8.2.6放油开关64
8.2.7起吊装置64
9机架及成型装置的设计计算64
9.1型辊轴的设计64
9.1.1选择轴的材料64
9.1.2初步估算轴的的直径64
9.1.3轴上零部件的选择和轴的结构设计64
9.2辊心的设计65
9.2.1选择辊心的材料65
9.2.2辊心结构设计65
9.3型板的设计66
10 液压加载装置的选型66
结论67
参考文献68
致谢79
摘要
本设计是对现有的蜂窝煤成型机结构的设计,用冲头机构完成蜂窝煤的成型脱模,槽轮机构结构简单,工作可靠等特性,因此定位分度准确本机结构简单,使用维修方便,生产的煤品质量好,成本低,能一机多用。目前国内生产蜂窝煤成型机的厂家不少,但是现有的蜂窝煤成型机的冲压成型,均有连杆机构带动在横梁的弹簧式冲头冲压成型,由于冲孔后抜冲针的需要在冲头上装有圆柱弹簧,弹簧在间歇往复应力作用下高速工作,极易产生疲劳,弹簧较弱,影响拔针,出现夹煤重冲故障,同时由于弹簧配件制造质量很不稳定,常常断裂,从而增加生产成本。此外还有往的许多制造煤块的机构存在着许多避之不及的缺陷,即有些机构制造出的煤块不够敦实,放干后有一些裂纹;有些机构造出的煤块经常出现孔内坍塌现象;有些机构在工作是会出现许多不能及时清理的煤屑,造成工作环境的相对恶劣,很大程度上造成了环境污染及能源的浪费。
关键词 机构;成型机;蜂窝煤
Abstract
The design of the existing honeycomb molding machine structure design, with punch mechanism completes the honeycomb molding and demolding, grooved pulley mechanism has the advantages of simple structure, reliable work and other characteristics, thus positioning accurate indexing with the machine has the advantages of simple structure, convenient repair and use, production of coal products of good quality, low cost, can use a machine.The current domestic production of briquette machine manufacturers a lot, but existing briquette machine stamping molding, with connecting rod mechanism to drive the crossbar of the spring-loaded punch stamping molding, because after piercing for punching needle needs in the punch is provided with cylindrical spring, a spring in the intermittent reciprocating stress under the action of high speed, easy to produce fatigue, spring is weaker, effects of needle, appeared with coal heavy punching failure, at the same time as the spring accessories manufacturing quality is not stable, often breaking, thereby increasing the production cost. In addition to the many manufacturing coal institutions exist many avoid defects, i.e. some institutions produce coal is stocky, placed after doing some crack; some institutions to build coal hole collapse phenomenon often appears in some institutions; there will be a lot of work is not cleared up the slack, resulting in the work environment the relatively poor, largely caused by the environmental pollution and energy waste.
Keywords Mechanism; Molding Machine ; Honeycomb
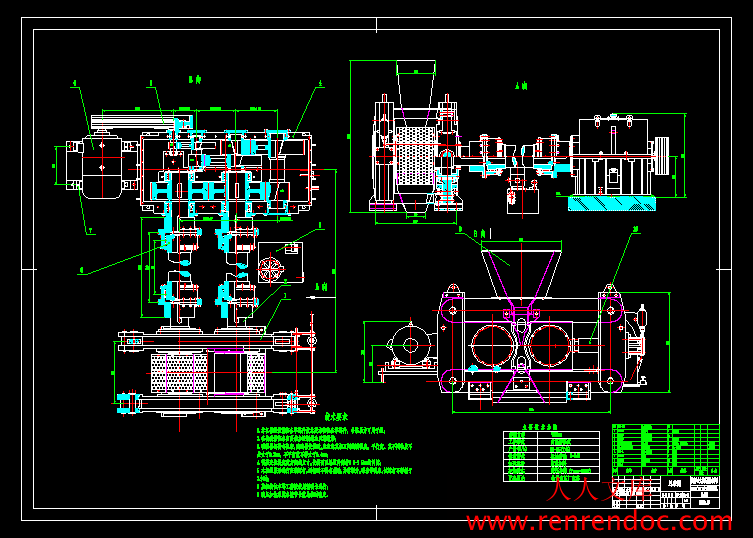
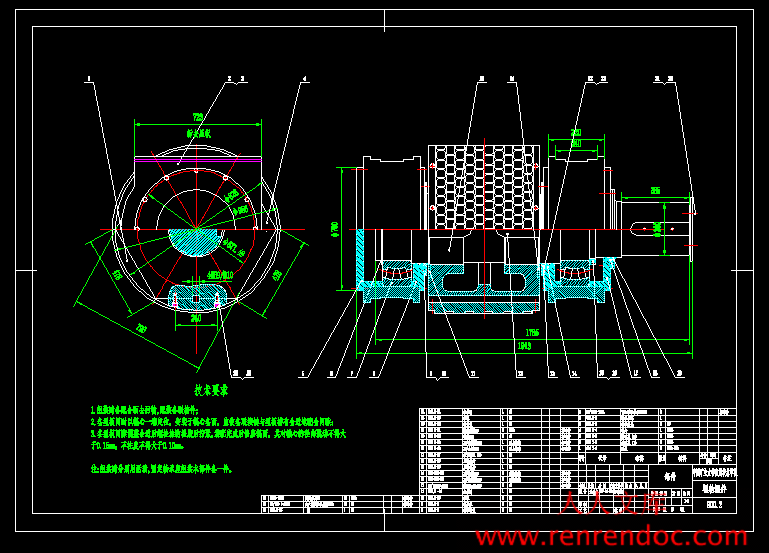
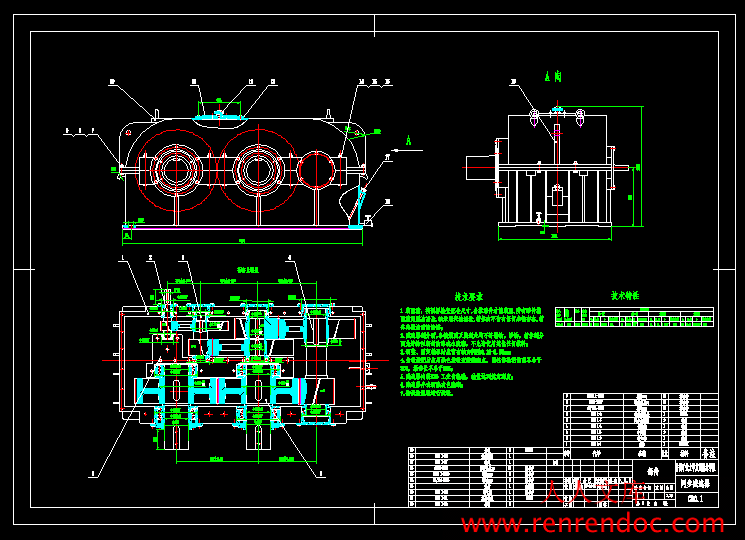