JS2000型混凝土搅拌主机设计
38页 15000字数+说明书+5张CAD图纸【详情如下】
JS2000型混凝土搅拌主机设计说明书.DOC
卸料门.dwg
封面.doc
总装配图.dwg
搅拌桶体.dwg
轴系图.dwg
轴零件图.dwg
第一章 概述
本设计说明书详细叙述了有关强制式混凝土搅拌主机的工作原理和结构以及相关设计内容,我的设计思路是根据拟订的传动路线,从电机的选择、电机带轮和减速器带轮的设计、联轴节和减速器以及联轴器的选择、搅拌轴的设计与计算并伴有轴承的选择与校核计算、卸料门的设计以及润滑系统的设计,最后还有主机的装配工艺等内容。本次设计我在老师和公司的综合指导下和详细查阅有关机械方面书籍来完成毕业设计的。以下从工作原理逐步展开:
工作原理:主要由水平安置的两个相连水平安置的圆槽形拌筒,两根按相反方向转动的搅拌轴和转动机构等组成,在两根轴上安装了几组搅拌叶片,其前后上下都错开一定的空间,从而使混合料在两个搅拌桶内轮番地得到搅拌,一方面将搅拌筒底部和中间的混合料向上翻转,另一方面又将混合料沿轴线分别向前后推压,从而使混合料得到快速而均匀的搅拌,因此,该类搅拌机具有自落式和强制式两种搅拌功能,搅拌效果好,耐磨性好,能耗低,宜制成大容量搅拌机。
1.1分类
混凝土搅拌机是制备混凝土的专用机械,其种类很多。按混凝土搅拌机的工作性质分有:周期性搅拌机和连续作用搅拌机两大类;按混凝土的搅拌原理分有:自落式搅拌机和强制式搅拌机两大类;按搅拌筒形状分为:鼓筒式,锥式(含锥形及梨形)和圆周盘式等搅拌机,常用的是周期性搅拌机,其具体分类如下:1.3 搅拌主机结构详细说明
混凝土搅拌机由搅拌机盖、搅拌筒体、搅拌装置、轴端密封、传动装置、衬板、卸料门润滑系统。
1.3.1.搅拌机盖
搅拌机盖是为搅拌主机工作时防尘和进料连接而设计的,盖与桶体间采用螺栓联结,中间有密封胶条,各进料口形状和位置可接不同机型或用户要求制作,检视门有安全开关。
搅拌机盖设计的喷雾系统有效地压住投料时扬起的粉尘并与吸尘装置连在一起,确保环保要求。
1.3.2.搅拌筒体
搅拌筒体由优质钢板整体弯成“奥米加Ω”形状,而且由特别管状框架承托,有足够的刚度和强度,保证主机的正常运作。
1.3.3.搅拌装置
两根搅拌轴上的多组搅拌臂和叶片组成搅拌装置,保证桶体内混合料℃能在最短时间内作充分的纵向和横向掺和,达到充分拌和的目的。搅拌臂分为进给臂、搅拌臂、返回臂,同时为了便于磨损后的调整和更换,每组搅拌叶片均能方便地在受力磨损的方向调整,直至搅拌叶片正常磨损后的更换。
为适应不同工况和骨料粒径的要求,搅拌臂可在轴上做60o、120o和180o的排列,以达到搅拌最大骨料粒径。
叶片为高强度抗冲击耐磨铸铁,正常生产时能达到3700罐/次,其性能指标符合JG/T5045.1—93规定(HRC≥58,冲击值≥5.0N.M/mm2,抗弯强度600N/mm2)。
1.3.4.轴端密封
对卧轴式混凝土搅拌机,因工作时主轴浸没在摩擦力很强的砂石水泥材料中,如果没有行之有效的轴端密封措施,主轴颈会很快被磨损,毁坏,产生严重的漏浆,影响级配。
采用三道密封及骨料架油封和液压系统供油旁泵,其工作原理用压盖1,耐磨橡胶圈2和转毂3为第一道密封,为防止砂浆浸入缝隙,由注油孔向内腔注入压力油脂,至主缝中有少量油脂挤出为止,用油脂外溢来阻挡砂浆入侵,第二道密封由转毂3转毂6和O型密封圈组成即浮动环密封,浮动环组借助O型圈的弹性保持一定的压紧力和磨损后的间隙补助,由注油孔注入润滑油脂,转毂为粉末冶金专用件,密封面经研磨加工,最后由安装的J型骨架密封组成第三道。
搅拌轴的支承由独立的轴承座和带锥套调心滚子轴承共同承担,同时通过两个骨架油封的作用能有效的保证轴承的良好工作环境,以保证机的正常运作。
1.3.5.传动装置
JS 型搅拌主机采用进口和国产两种螺旋锥齿行星减速机传动,减速机与搅拌主轴间采用鼓型齿联轴器联结,搅拌主轴采用高速端十字轴万向联轴器同步,使两轴作反向同步运转,达到强制搅拌效果,与传统的大小的链轮传动,大齿轮同步的结构相比,具有结构紧凑,传动平稳,遇非正常过载时能通过皮带打滑保护等特点。
为保证减速机的正常工作,传动装置中可以选配冷却装置散热器的功率为0.055KW,由本机所附加的自动感温器控制,在减速机油温达到60度时自动启动,油泵的动力由主电机通过皮带传动提供。
1.3.6.衬板
弧衬板为高硌耐磨合金铸铁,其性能指标符合JG/T5045.2—93规定(HRC≥54,冲击值≥7.0N.M/mm2,抗弯强度≥600N/mm2)特殊设计的菱形结构能提高衬板的使用寿命,端衬板为优质高Mn耐磨钢板制成.
1.3.7.卸料门
卸料门的结构形式独特可靠,整体弧面与桶内衬板面持平,能有效地减少强烈冲击,磨损真正做到优质耐久,另外,卸料门两端的支承轴承座可上下调节,接触面磨损后可以调节间隙,确保卸料门的密封.卸料门采用进口液压系统驱动,与传统的气动形式相比具有结构紧凑,动作平稳,开门定位准确,能手动开关门等特点,油泵系统产生的高压油通过控制系统,经高压油管作用到油缸,驱动卸料门的开关,通过调节卸料门轴端接近开关的位置和电控系统共同使用,可以实现卸料门的开门到位的任意调整,以实现不同的卸料速度.
1.4 搅拌主机类型选择
由于强制式混凝土搅拌机有立轴式和卧轴式两大类。立轴式有分为涡浆式和行星式。混凝土搅拌机是将石子(粗骨料)、沙子(细骨料)、水泥、水和某种添加剂搅拌成匀质混合料的机械。广泛应用于工业和民用建筑、道路
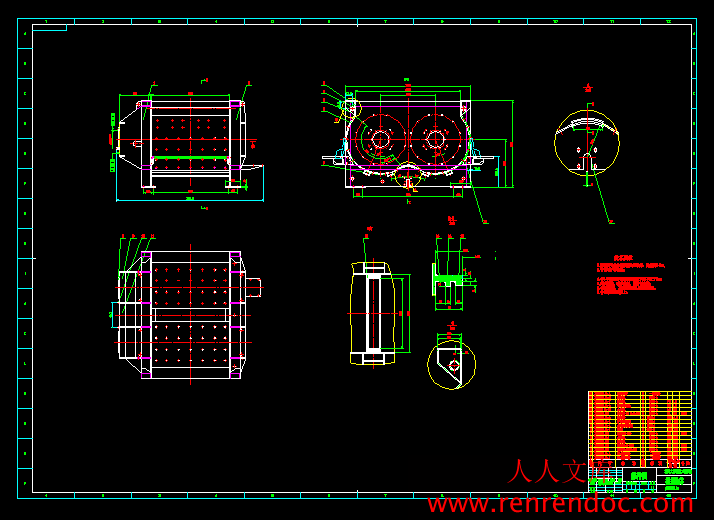
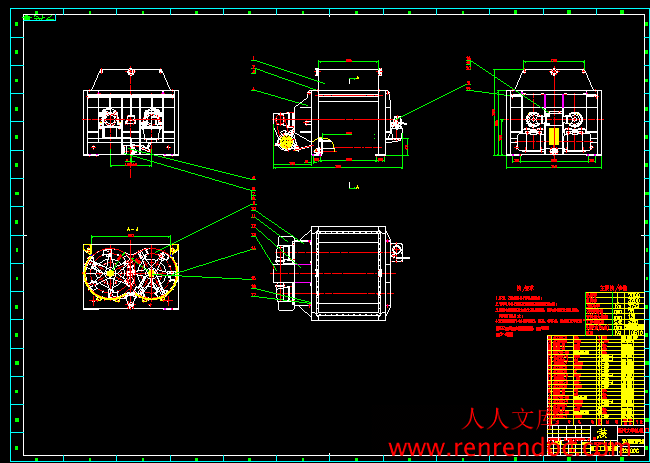
