皮带轮注射模设计
28页 17000字数+说明书+9张CAD图纸【详情如下】
【客户资料】--皮带轮注射模设计
皮带轮注射模9张图纸.dwg
皮带轮注射模设计说明书.doc
摘 要:基于塑料皮带轮的几何形状,材料性能、技术要求,完成塑料皮带轮模具的设计工作,该模具是一套塑料注射模具。在设计过程中,我选择斜导柱侧分型机构,而且把型腔设置在跟滑块固定的侧型芯上。其分型方式选择多个分型面同时分形,来完成型腔与塑件的分型。这样不仅使得该模具的结构得到了一定的简化,而且降低了这个模具的加工成本。为了提高模具在实际生产中的生产效率,采用了一模两腔的形式。在注射成型过程中,为了避免合模时滑块可能产生滑移,导致无法保证制品精度以及减少斜导柱在生产过程中的受力情况以及受力后的变形,我设置了楔紧块装置。为了保证斜导柱伸出端能够准确可靠地插入滑块端的斜孔中,要求滑块在完成抽芯以后仍然停留在刚刚脱离斜导柱的位置,不能发生任何的偏移,否则合模时斜导柱不能准确地进入滑块斜孔,因此设置了限位板对滑块进行定位。另外,合模完成后,为了避免两个滑块的位置发生左右偏移,导致型腔结构尺寸受到影响,必须在滑块合模终端位置设置定位机构,以保障两个滑块的位置不会发生不必要的偏移。此外还完成了该模具一些主要零件的加工工艺规程的编制工作。
关键词:皮带轮;模具;一模两腔;抽芯;注射模;
目 录
1 引言- 1 -
1.1塑料及塑料工业发展- 1 -
1.2塑料工业在国民经济中的作用- 1 -
1.3模具工业在国民经济中的重要性- 1 -
1.4本模具的总体说明- 2 -
2 塑料材料及塑件几何形状- 2 -
2.1塑料材料的简介- 2 -
2.2分析塑件的结构、尺寸精度及表面质量- 3 -
3 注射机的选用- 4 -
3.1 计算制品的体积和质量- 4 -
3.2 初步选定注射机- 4 -
4 确定型腔数及位置布局方案- 6 -
4.1型腔数的确定- 6 -
4.2型腔布局方案- 6 -
5 确定模具结构方案- 7 -
5.1确定分型面- 7 -
5.2确定模架组合形式- 7 -
5.3.1主流道设计- 9 -
5.3.2主流道衬套的设计- 9 -
5.3.3分流道设计- 10 -
5.3.4.浇口的设计- 11 -
5.3.5.冷料穴的设计- 12 -
5.4成形零部件的设计- 12 -
5.4.1.确定成形零部件工作尺寸- 12 -
5.4.2.侧向分型与抽芯机构设计- 13 -
5.4.3.排气系统的设计- 16 -
5.5注射模结构零部件设计- 17 -
5.5.1.合模导向机构- 17 -
5.5.2.设计推出脱模机构- 17 -
5.6推出零件的设计- 18 -
5.7复位机构的设计- 18 -
5.8脱模力的计算- 18 -
5.9 推出零件尺寸的确定- 19 -
6 模具各部分的校核- 20 -
6.1注射量的校核- 20 -
6.2注射压力校核- 20 -
6.3锁模力校核- 20 -
6.4模具高度与注射机闭合高度的关系校核- 20 -
6.5开模行程的校核- 21 -
7 结论和模具结构图- 21 -
参考文献- 21 -
致谢- 23 -
PVC是白色粉状的颗粒,密度为1.35~1.45g/cm3,由于在结构中具有含有较高的氯,所以具有耐燃自熄的特性;PVC的大分子链含有极性的氯原子,分子间的作用力比PE大,所以它的强度和硬度都比PE稍大;PVC的相对分子量为3~10万,呈现线性无定形结构。它的分子量对加工和塑件性能都有很大影响,分子量越大,加工时就要用更高的压力和温度,这样才能使熔料的流动性达到加工要求,使得加工难度变得大,但制品的机械强度得以提高。
PVC的热稳定性和耐热性比较差,软化的温度接近于分解的温度,因此在加工时要加入各种稳定剂和增塑剂才行。PVC在70~80℃时软化,150~170℃时呈熔融状态,190℃以上会分解并放出有毒的氯化氢。由于增塑剂加入量不同,可制得硬质PVC(H-PVC)和软质PVC(S-PVC)。PVC的电绝缘性能良好,有较好的消振性,成本较低。但是,PVC的热稳定性较差,受热会引起不同程度的分解,而软质PVC制品中的增剂还有外迁之弊,它对应变较敏感,变形后不能完全的复原,且在低温时会变硬[10]。与S-PVC相比,H-PVC的强度及硬度要更大一点,更适合做成结构性零件,故此皮带轮应选用H-PVC成形。
2.2分析塑件的结构、尺寸精度及表面质量
此次设计的模具需要成形的塑料零件是皮带轮,材质是聚氯乙烯(PVC),所以注射模是其最适合成形的塑料模。
(1)结构分析 从塑料制品图2-1可见,该制品几何结构比较复杂,有侧向凹槽和孔,因此,模具设计时必须考虑侧向分型和抽芯机构;零件形状总体为圆柱形,轮廓尺寸大小为88×22.5mm,属于机构比较复杂的小型件。
(2)尺寸精度分析 该制品尺寸较小,一般的精度等级对应的模具相关零件的尺寸加工可以保证。从制品厚度上来看,制品平均厚度约为22~23mm,对零件的成型不是很有利。
(3)表面质量分析 该零件表面的质量要求较高,外表面不得有气痕飞边等缺陷,综合分析可以看出,注射时在工艺参数控制得较好的情况下,该制品的成型要求可以得到保证。
由于模具是与注射机配套使用的,设计模具时,大部分结构都是根据注射机的技术规格来设计模具的,因此设计过程中,注射机的选用就显得尤为重要,而且应该先选用注射机。
3 注射机的选用
根据制品的生产批量及尺寸精度的要求,采用多型腔模,初步确定型腔数为两个,既一模两腔。
3.1 计算制品的体积和质量
按照图1塑料制品所示尺寸近似计算为:


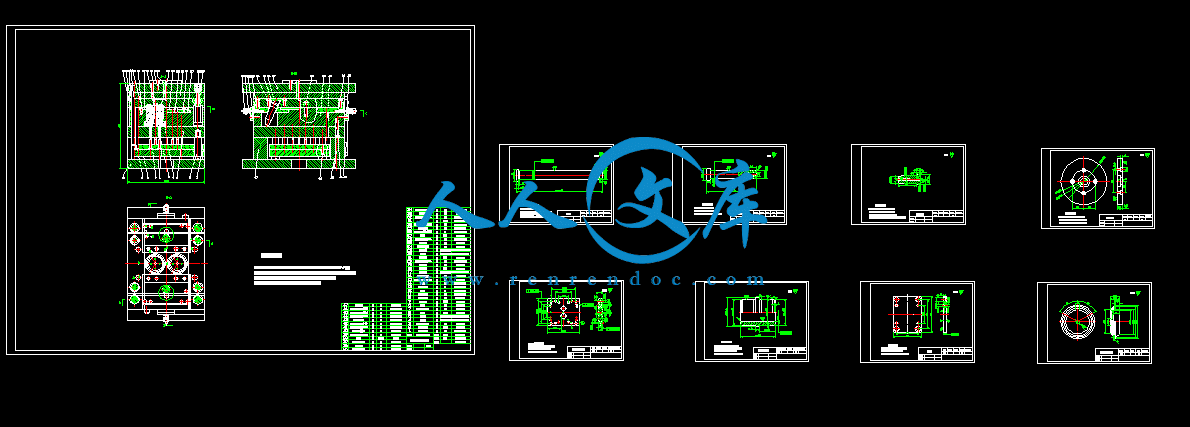