数控车床主轴参数化建模及频域分析
39页 14000字数+说明书+外文翻译+3张CAD图纸
外文翻译--齿轮和轴的介绍.doc
套筒.dwg
数控车床主轴参数化建模及频域分析.doc
装配图.dwg
齿轮.dwg
数控车床主轴参数化建模及频域分析
摘要:
本毕业设计是对CKA6140数控车床主轴进行参数化建模及频域分析,将现代化的设计方法应用于机床的设计,以数控系统设计方案的拟定为主线,通过对数控车床主轴伺服系统机械部分进行参数化设计,理论强度基础计算及其关键零件的校核,对车床进给伺服系统进行数学建模,然后使用ANSYS软件进行频域仿真,简要论述了频域方法和动力学分析的基本求解过程,建立机床主轴频域模型,合理的确定了载荷、轴承支承刚度和约束条件,选定了单元类型。采用Lanczos法对其进行自由模的具体研究内容,总结了机床、动态设计方法研究和机床主轴动静态研究的发展状况和发展趋势,在总结前人研究成果的基础上,结合当前的技术发展趋势,采用频域方法来进行研究,简要论述了模态分析,得到主轴的固有频率和振型,找出工作时容易发生共振的频率域,为进一步提高精度和转速提供理论依据。通过毕业设计进行了机电结合的全方面训练,从而培养设计计算的能力以及分析和处理生产过程中所遇到的问题的综合能力。
关键词:频域分析;模态分析;机床主轴;振动
目 录
1 绪 论1
1.1 课题研究的背景及意义1
1.2 数控机床主轴国内外研究现状1
1.3 本课题的研究内容2
2 总体设计方案4
2.1 设计要求4
2.2 设计参数5
2.3 总体设计方案图5
3 数控系统选择6
3.1 简介西门子802S数控系统6
3.2 802S数控系统的组成6
3.3数控机床伺服系统的选择7
4 主轴计算及校核8
4.1 主轴设计8
4.1.1 电动机的选择8
4.1.2 带传动设计8
4.2 主轴的校核10
4.2.1 传动组齿轮模数的确定和校核10
4.2.2 齿轮强度校核11
4.2.3 主轴挠度的校核12
4.2.4 主轴弯曲变形的校核13
4.2.5主轴扭转变形校核13
4.3 主轴最佳跨距的确定14
4.3.1选择轴颈直径,轴承型号和最佳跨距14
4.3.2求轴承刚度14
4.4 主轴支承处轴承的选择15
4.5 主轴图16
5 参数化建模17
5.1理论基础17
5.1.1 主轴的动力学模型17
5.2 建立目标函数18
5.3约束条件19
5.3.1 刚度约束19
5.3.2 强度约束19
5.3.3 转角的限制20
5.3.4 扭转变形的限制20
5.3.5 切削力的限制20
6 数控车床主轴的频域分析21
6.1 频域简介及ANSYS软件应用21
6.1.1 频域概述21
6.1.2 ANSYS软件应用22
6.2 机床主轴频域分析模型22
6.2.1 构建几何模型22
6.2.2 频域模型建立22
6.2.3 单元类型选择和网格划分23
6.3 机床主轴振动模态分析25
6.3.1 ANSYS动力分析25
6.3.2 模态分析25
结论30
致谢31
参考文献32
附录33
1.1 课题研究的背景及意义
制造业是体现一个国家综合实力的重要方面,是国家财富的主要创造者世界上凡是发达国家都拥有高水平的制造业。而装备制造业作为整个国家工业部门的装备提供者,其水平的高低决定了我国制造业的国际竞争力,特别是我国加入到WTO以后,行业竞争更加激烈,已经关系到我们国家现代化的进程和民族的复兴,因此提高我国装备制造业的整体技术水平具有重大的理论和现实意义。在当前的振兴过程中,我们应该清醒的认识到我国装备制造业和发达国家的差距,不能只看到眼前的一时繁荣。特别是机床行业,在设计水平上与发达国家有着比较大的差距,缺少创新和突破,掌握核心技术较少,特别在高端的产品领域,竞争力还不够强大。
动态设计的原则:目标是保证机械满足其功能前提要求的条件下具有较高的动刚度,使其经济合理、运转平稳、可靠。要从总体上把握机械结构的固有频率、振型和阻尼比。具体为:避开共振,避开率应在15%-20%;降低机器运行过程中的振动幅度;结构各阶模态刚度最大且尽量相等;结构的各阶模态阻尼比要尽量高;避免结构疲劳破坏;提高振动稳定性。
设计步骤:
(1)建立机械结构或机械系统的动力学模型,根据设计图纸建立力学模型,也可以应用试验模态分析技术建立结构的试验模型;
(2)利用数学模型求解自由振动方程得到结构振动的固有特性,引入外部激励可以进行动力响应分析;
(3)动态性能评定;
(4)结构修改和优化设计[1]。 机床主轴的动静态特性主要就是固有频率、受力变形、临界转速、动态响应等,在60年代以前,一般采用经验模拟法设计,方法繁琐,精度低。60年代以后由于计算机技术和计算方法的进步,出现了有限差分法、结构分析法、频域法、结构修正法,模态法等大量方法。本课题就是要研究机床主轴的动静态特性,其主要任务是计算轴承的刚度、建立合理有效的模型,特别是轴承部分的简化,再对模型进行静变形、模态及响应等各方面的分析,得到固有频率、振型等参数。其中轴承刚度的计算较复杂,静刚度可用经验公式计算得出[12];而动刚度的计算部分则要考虑主轴高速运转条件下对轴承的影响。
2.1 设计要求
1)数控车床应具有性能:
(1)数控代码制:ISO
(2)输入方式:增量值、绝对值通用
(3)同时控制坐标轴数:2坐标轴(纵向Z,横向X)
(4)纵向脉冲当量值:0.01mm/puls
(5)刀具补偿量:0~99.99mm
(6)自动升降速性能:有
(7)数控系统选连续控制系统。
(8)进给伺服系统采用步进电机开环控制系统。
(9)一般采用8位微机。在8位微机中,MCS—51系列单片机具有集成度高、可靠性好、功能强、速度快、抗干扰能力强、具有很高的性价比,因此,可选 MCS—51系列单片机扩展系统。
(10)设计自动回转刀架及其控制电路。
(11)为了保证进给伺服系统的传动精度和平稳性,选用摩擦小、传动效率高的滚珠丝杠螺母副,并应有预紧机构,以提高传动刚度和消除间隙,齿轮副也应有消除齿侧间隙的机构。
(12)采用贴塑导轨,以减小导轨的摩擦力。
2)数控车床的工艺范围:具有快速定位,直线插补,顺、逆圆插补,暂停,循环加工。
3)对微机数控系统的要求:
微机控制系统要有可靠性好、功能强、速度快、抗干扰能力强,具有很高的性能价格比等特点。控制系统的加工程序和控制命令通过键盘操作实现,显示器采用数码管显示加工数据及机床状态等信息。2.2 设计参数
表2.1 机床基本参数
项目单位 参数
型号 CKA6140
床身回转直径mm 400mm
刀架上回转直径mm 210mm
主轴最高转速r/min 1920r/min
主电机功率KW 7.5KW
数控系统 西门子802S
尾座主轴直径行程及主轴孔锥度mmmm75mm150mm;莫氏圆锥5号
丝杠螺距mm12mm
系统环境工作条件℃ %温度-10~+40℃;湿度为40% ~80%
输入电网电压V交流(220±22)V;频率为50Hz;电流为1.5A
2.3 总体设计方案图
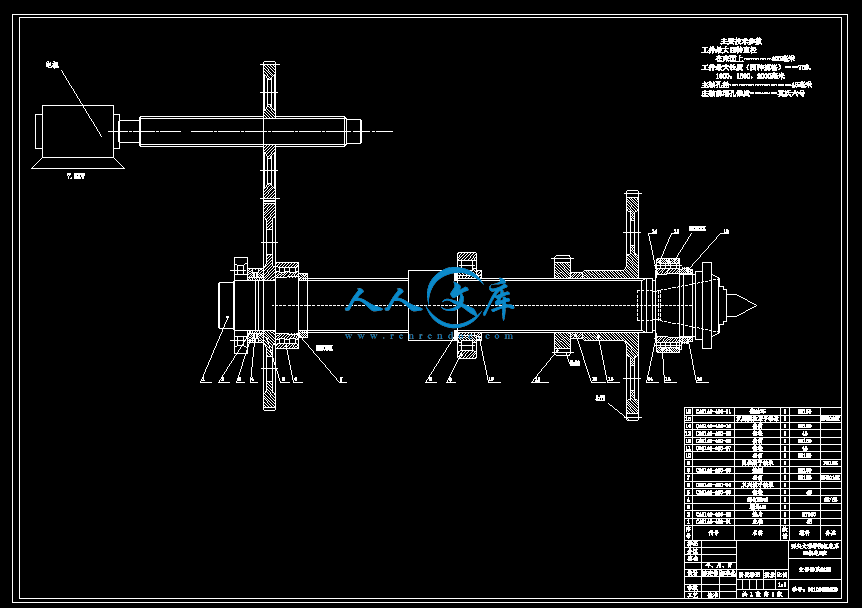