轮辐专用六轴钻床设计
59页 19000字数+说明书+开题报告+8张CAD图纸
A0装配图.dwg
A1底座.dwg
A2压料板.dwg
A2小齿轮轴.dwg
A2工作台.dwg
A2液压缸.dwg
A2隔板.dwg
A3立柱.dwg
轮辐专用六轴钻床设计开题报告.doc
轮辐专用六轴钻床设计说明书.doc
摘要
众所周知,在现代机械制造业中,企业对专用机床有着广泛的需求。一般钻床劳动强度大,专用性能低,生产率不高且不能保证精度;而多轴专用钻床操纵方便、省力、容易掌握,不易发生操作错误和故障,不仅能减少工人的疲劳,保证工人和钻床的安全,还能提高钻床的生产率。因此,专用机床的使用,对企业的竞争力有着十分重要的作用。本文针对一般钻床上述种种缺点及加工对象的具体情况设计一台轮辐专用多轴钻床,力求达到满足性能要求,经济效益和人机关系等技术经济指标。
Abstract
As it is known, the special-purpose lathe is extensively demanded by enterprises in the modern mechanical manugfacturing industry. The ordinary lathe not only need a large number of man-power. But has a low performance. In addition, its productivity is low and the accuracy can't be ensured. However, the special-purpose lathe can not merely help enterprises to boost productivity greatly, saving a large number of manpower, the material resources, still can improve the quality of the products. Meanwhile, it is easily maneuvered and guarantees workers' safty. Hence, the use of the special-purpose lathe plays an important part in the competitiveness of enterprises. Owing to the variety disadvantages of the ordinary lathe, this article presents a new design of mutil-axles drilling machine. It is designed based on the specific information of the object. We try our bests to make it satisfies the performance demands as well as other index such as economic efficiences and relation between humen and machines.
Key words: muti-axles drilling machine.
目录
第一章 多轴钻床总体设计8
第一节 概论8
一.性能要求9
二.经济效益10
三.人机关系11
第二节 多轴钻床总体布局分析11
一.操作、观察与调整对总体布局的影响11
二.零件的加工工艺方法对总体布局的影响12
三.机床的运动分配对总体布局的影响12
四.精度等级对总体布局的影响13
五.生产效率对总体布局的影响13
六.机床的造型对总体布局的影响14
第三节 多轴钻床工艺方案的制定14
一.影响机床工艺方案制定的主要因素15
二.加工工件的工艺分析15
第二章 多轴钻床部件设计16
第一节 动力部件的选择16
一.切削用量的选择16
二.刀具的选择17
三.动力部件的选择17
第二节 减速器的选取20
第三节 上台板的设计21
一.材料的选取22
二.尺寸的确定22
三.结构设计23
第四节 主轴箱体的设计24
第五节 主轴箱零件的设计26
一.齿轮的设计26
二.齿轮的计算及校核28
三.轴的设计34
第六节 夹紧机构的设计40
一.概述40
二.夹紧机构的设计42
第三章 支承件的设计43
第一节 概述43
一.支承件的功能43
二.支承件的静刚度和形状选择原则44
三.支撑件的动态特性44
第二节 导轨(立柱)的设计45
一.概述45
二.导轨的设计46
第三节 底座的设计48
一.材料选择48
二.结构设计49
三.尺寸确定49
第四章 液压系统的设计49
一.工况分析50
二.确定液压缸的参数52
三.绘制工作原理图54
第五章 电器控制系统的设计55
一.方案分析55
二.工作过程56
后记58
致谢59
参考文献60
第一章 多轴钻床总体设计
第一节 概论
多轴钻床的总体设计是机床设计的关键环节,它对机床所达到的技术性能和经济性能往往起着决定性的作用。
机床总体设计,目前基本上有两种情况:其一,是根据具体加工对象的具体情况进行专门设计;其二,因机床在组成部件方面有共性,可设计成通用部件,可以利用通用部件来进行机床设计。本设计属于第一种情况,这也是当前最普遍的做法。
一般来说,机床总体设计时应考虑下列几点:
用合适的加工工艺,制定最佳方案;
合理的确定机床工序集中程度;
合适的选择机床通用部件;
选择当前机床的配置形式;
合理的选择切削用量;
设计高效率的夹具,刀具及主轴箱;
要保证给定的工艺过程;
保证机床的刚度、精度、抗振性和稳定性,力求减轻机床重量;
保证机床结构简单,尽量用较短的传动链,以提高传动精度和效率;
保证良好的加工工艺性,以便于机床的加工和装配;
保证安全生产,便于操作调整和维修;
尽可能保证占地面积小;
机床外形美观大方,符合人机工程学原理。
评价机床性能的优劣,主要是根据技术经济指标来判断的。机床设计的技术经济指标可从满足性能要求,经济效益和人机关系等方面进行分析讨论。
一.性能要求
工艺范围
机床的工艺范围是指机床适应不同生产要求的能力。大致包括下列内容:在机床上可完成的工序种类;加工零件的类型,材料和尺寸范围;毛坯的种类等。
加工精度和表面粗糙度
机床的加工精度是被加工零件在尺寸,形状和相互位置等方面所能达到的准确程度。机床精度分三级:普通精度级,精密级和高精密级。机床的精度,包括几何精度,传动精度,运动精度和定位精度等。几何精度是指机床在不运动或运动速度较低时的精度,它是由机床各主要部件的几何形状和它们之间的相对位置与运动轨迹的精度决定的。传动精度是指内传动链两末端件之间的相对运动精度,它取决于传动系统中机件的制造精度和装配精度以及传动系统设计的合理性。运动精度是指机床的主要部件以工作状态的速度运动时的精度。定位精度是指机床主要部件在运动终点所达到的实际位置的精度。只有机床精度达到一定要求后,才能满足机床加工精度的要求。
机床加工的工件表面粗糙度也是机床主要性能之一。它与工件和刀具的材料,进给量,刀具的几何形状和切削时的振动有关。对表面质量要求越高,也就是要求表面粗糙度越小,则对抗振性的要求越高。机床的抗振性包括两个方面:抵抗受迫振动的能力和抵抗自激振动的能力。如果振源的频率与机床某主要部件振动的固有频率重合时,就将发生共振。振幅大增,加工表面粗糙度将会大大增加。切削自激振动,产生于切削工程中。如果切削不稳定,则切过的表面,其波纹度将越来越大,振动越来越剧烈,将严重影响加工表面的质量。
生产率
机床的生产率通常是指在单位时间内机床所能加工的工件数量。要提高机床的生产率,必须缩短加工一个工件的平均总时间,其中包括缩短切削加工时间,辅助时间以及分摊到每个工件上的准备和结束时间。
自动化
机床自动化可减少人对加工的干预,从而保证加工的一致性,即被加工零件的精度稳定性。还具有提高生产率和减轻工人劳动强度的优点。
可靠性
机床的工作可靠性也是一项重要的技术经济指标。随着机床安全化的发展,可靠性在机床设计中的地位逐步提高。
机床寿命
机床寿命就是机床保持它应具有的加工精度的时间。随着技术设备更新的加速,对机床寿命所要求的时间也在减短。对于本次设计的多轴专用钻床来说,寿命要求短,因为它将随加工产品的更新而废弃。这就要求机床在最高生产率的条件下工作,在使用期内充分发挥机床的效能,取得最大的经济效益。
确保和提高机床的寿命,主要是提高关键性零件的耐磨性,并使主要传动件的疲劳寿命与之相适应。
二.经济效益
在保证实现机床性能要求的同时,还必须使机床具有很高的经济效益。不仅要考虑机床设计和生产的经济效益,更重要的是要从用户出发,提高机床使用厂的经济效益。对于机床生产厂的经济效益,主要反映在机床成本上。机床的成本包括材料,加工制造费用,而且还包括研制和管理费用。
对于机床使用厂的经济效益,首先是提高机床的加工效率和可靠性。要使机床能够充分发挥其效能,减少能源消耗,提高机床的机械效率,也是十分重要的。机床的机械效率是有效功率对输入功率之比。两者的差值就是损失,主要是摩擦损失。而且,摩擦功转化为热量,将引起机床的热变形,又对机床的工作带来不良的后果。因此,设计时必须重视提高机床的机械效率。
三.人机关系
在设计中,还应该重视人机关系问题。
机床应操纵方便,省力,容易掌握,不易发生操作错误和故障。这样不仅能减少工人的疲劳,保证工人和机床的安全,还能提高机床的生产率。
防止机床对周围环境的污染,也是对机床设计和制造提出的一项主要要求。噪声要低,不仅噪声声级要达到规定值以下,而且不能对人耳有强烈的不适感。。
对于上述的各项技术经济指标,在机床设计时我们将综合考虑,并应根据不同的需求,有所侧重。
第二节 多轴钻床总体布局分析
机床布局的设计是一个重要的全局性问题,它对机床的部件设计,制造和使用都有较大的影响。机床总布局的任务,是解决机床各部件的相对运动和相对位置的关系,并使机床具有一个协调完美的造型。工艺分析和工件的形状,尺寸和重量,在很大程度上左右着机床的布局形式。
一.操作、观察与调整对总体布局的影响
机床的布局必须充分考虑到操作机床的人,处理好人机关系。充分发挥人与机床各自的特点,使人机的综合效能达到最佳。
机床各部件的相对位置的安排,应考虑到便于操作和观察及测量。安装工件部位的高度,应正好处于操作者手臂平伸的位置(较重件除外)。为适应一般操作者的身材高度,对安装工件位置较低的机床,应将床腿或床座垫高。
根据手臂所能到达指定位置的难易程度,有最大工作区,正常工作区和最佳工作区之分。为了便于检修,要考虑人体蹲下是较适于工作的区域。还应考虑到操作者可能达到的最大视野和反应敏锐的视野区等。
二.零件的加工工艺方法对总体布局的影响
专用机床加工工件的工艺方法是多种多样的。在设计多轴钻床时,往往由于工艺方法的改变,导致机床的传动部件配置以及结构等产生一系列的改变。因此在确定专用多轴钻床的总体布局时应首先分析和选择合理的加工工艺。
三.机床的运动分配对总体布局的影响
钻床的工艺方案确定后,刀具与工件在加工时的相对运动也随之被确定了。但此相对运动可以完全分配给刀具,也可以完全分配给工件,或由刀具和工件共同完成。下面我们拟定几种分配方案,分析比较不同方案的优缺点,选择最佳运动方案。
钻削加工的相对运动由刀具实现
在轮辐专用多轴钻床上钻孔时,主运动和进给运动都有刀具完成,钻头的轴向移动为进给运动,钻头的回转运动为主运动。主运动和进给运动形成了切削加工时的全部相对运动。
钻削加工时的相对运动由刀具和工件共同完成
在多轴钻床设计中,扩铰轮辐孔时主运动分配给钻头,进给运动由工件完成,即钻头的向下运动和工件的向上移动,该方案用于工件重量不大的设计中。
方案比较:把运动完全分配给刀具的方案,一般用于重型工件的加工。由于多轴钻床所加工的轮辐重量不是很大,故本设计采用第二种方案。具体方案如下图:
四.精度等级对总体布局的影响
由于多轴钻床的加工精度和光洁度与机床的刚度和抗震性有关,为了获得所要求的加工精度和光洁度,在机床总体布局上应保证有足够的刚度和抗震性。通常情况下,支承形式为封闭的框架时,其刚度较好。机床在加工过程中产生震动传递给工件和刀具,会使被加工表面产生震动,降低表面光洁度;震动也会使刀具寿命缩短,使机床零件磨损加快;震动所造成的噪音,使工人疲劳。因此,设计中应采取一定的措施来消除和减少震动。
五.生产效率对总体布局的影响
机床的生产批量不同,其结构可能完全不同。强力轮辐股份有限公司加工轮辐属于大批量生产,因此制造轮辐扩铰专用机床,一次完成多孔加工,效率高,劳动强度低,从而节约人力和时间。
六.机床的造型对总体布局的影响
机床的外观,应寻求整体统一,均衡稳定,比例协调机床总布局的任务,是解决机床各部件的相对运动和相对位置的关系,并使机床具有一个协调完美的造型。
钻床一般型式是单臂式和框架式。单臂式的特点是能方便的更换点位进行加工。但这类布局型式与框架式相比刚度较差,所以本设计采用框架式结构,这种型式的机床具有占地面积小,工人所处的操作位置比较灵活的特点,且刚度高,加工精度高。本设计框架式结构见下图:
第三节 多轴钻床工艺方案的制定
工艺方案制定的正确与否,将决定机床能否达到“质量轻,体积小,结构简单,使用方便,效率高,质量好”的要求。故在确定专用机床的总体布局方案时,应重点分析和选择合理的工艺方案。
一.影响机床工艺方案制定的主要因素
被加工零件需要在机床上完成的工序及加工精度,是制定机床工艺方案的主要依据。制定工艺方案时,首先需要全面的分析工件的加工精度及技术要求,了解现场加工工艺及保证精度的有效措施。
被加工零件的特点
工件材料及硬度、加工部件的结构形式、工件的刚性、工艺基面等,对于机床工艺方案的制定都有重要的影响。
工件的刚性不足,加工时工序就不能太集中。有时为了减少机床台数,必须采用高度集中工序时,从安排上,也必须把一些工序从时间上错开加工,以避免同时加工时因工件受力变形、发热变形以及振动而影响加工精度。
工件的生产方式
被加工零件生产批量的大小,对机床方案的制定也有影响。对大批量生产的箱体零件,工序安排上,一般趋于分散。例如加工轮辐螺栓孔,其粗加工,精加工分别在不同的机床上进行。机床虽多一些,但由于生产批量很大,从提高生产率,稳定的保证加工精度的角度来讲仍然是合理的。在小批量生产情况下,完成同样工艺内容,则力求减少机床台数,此时应当将工序尽量集中在一台或少数几台机床上进行加工,以提高机床的利用率。
二.加工工件的工艺分析
本次设计的机床是轮辐螺栓孔专用扩铰多轴钻床。以下对所加工工件外形及加工面的位置作详细的分析。
由零件图可以看出,此步工序是对轮辐面上六个直径为32的孔进行扩铰加工。如果采用一般钻床,也可以完成此步工序,但是一次只能加工一个孔,一个轮辐需要加工六次,劳动强度大,生产率低且不能保证精度。为了保证配合质量,提高生产效率和减轻劳动强度,可以使用多轴钻床一次完成六个孔的扩铰工作,从而节省人力和时间。所加工工件在扩孔后的零件图如下图所示:
第二章 多轴钻床部件设计
第一节 动力部件的选择
动力部件的选择在整个多轴钻床的设计中是至关重要的。动力部件的功率如果选取过大,电动机经常处于低负荷情况,功率因素小,造成电力浪费,同时使转动件及相关尺寸选取过大,浪费材料,且机床笨重。如果选取过小,则机床达不到设计提出的使用性能要求。本设计主运动采用电动机带动,进给运动采用电动机带动液压系统运动。
一.切削用量的选择
多轴钻床正常工作与合理地选用切削用量,即确定合理的切削速度和工作进给量,有很大的关系。切削用量选用的恰当,能使多轴机床以最少的停车损失,最高的生产效率,最长的刀具寿命和最好的加工质量,也就是“多快好省”的进行生产。
工作时,六轴钻床的六把刀具同时运转,为了使钻床能正常工作,不经常停车换刀,而达到较高的生产率,所选的切削用量比一般钻床单刀加工要低一些。概括地说,在多轴钻床上不宜采用较大的切削速度和进给量。
对于扩铰孔,要想达到较理想的状态,除刀具须保证合理的几何形状及冷却充分,很重要的一点是合理选择切削用量。一般是速度低一点好,进给量不宜太大。
查《组合机床设计》第一册“机械部分”表2—13“扩孔切削用量”,得V=12~20m/min,f=0.3~0.4mm/r,本设计选取v=20m/min,f=0.3mm/r。
二.刀具的选择



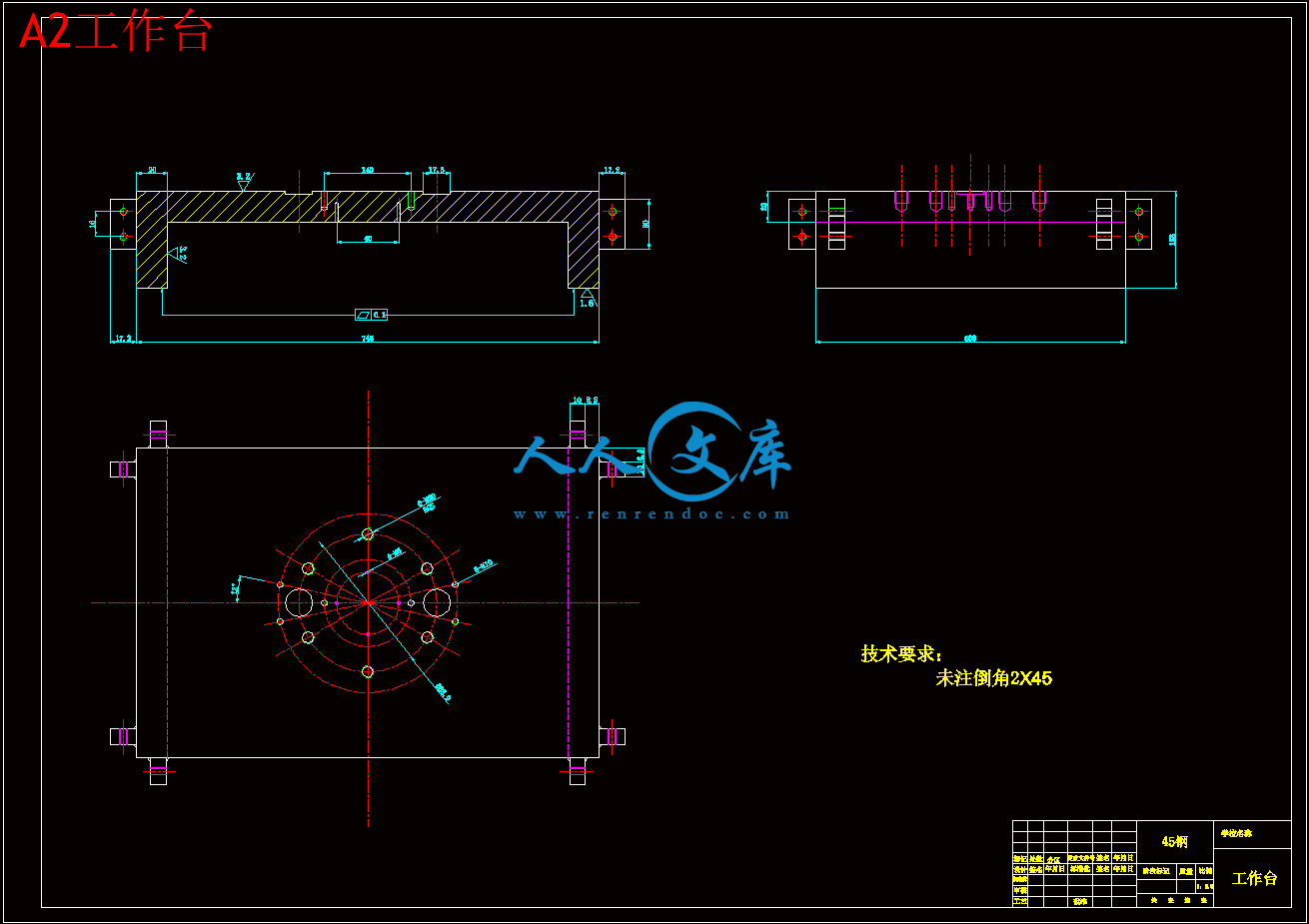

