WH212减速机壳体加工工艺及夹具设计
51页 18000字数+说明书+任务书+工序卡+17张CAD图纸
WH212减速机壳体加工工艺及夹具设计说明书.DOC
任务书.doc
减速器机座.dwg
减速器机盖.dwg
封面.doc
工序卡11张.dwg
摘要.doc
目录.doc
钻底孔Φ19夹具体图.dwg
钻底孔Φ19夹具装配图.dwg
镗夹具零件图.dwg
镗床夹具装配图.dwg


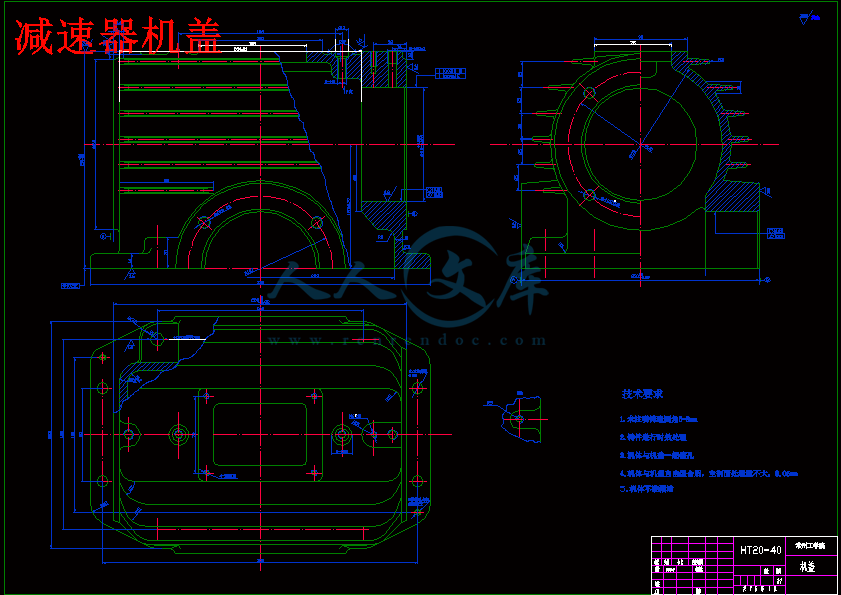




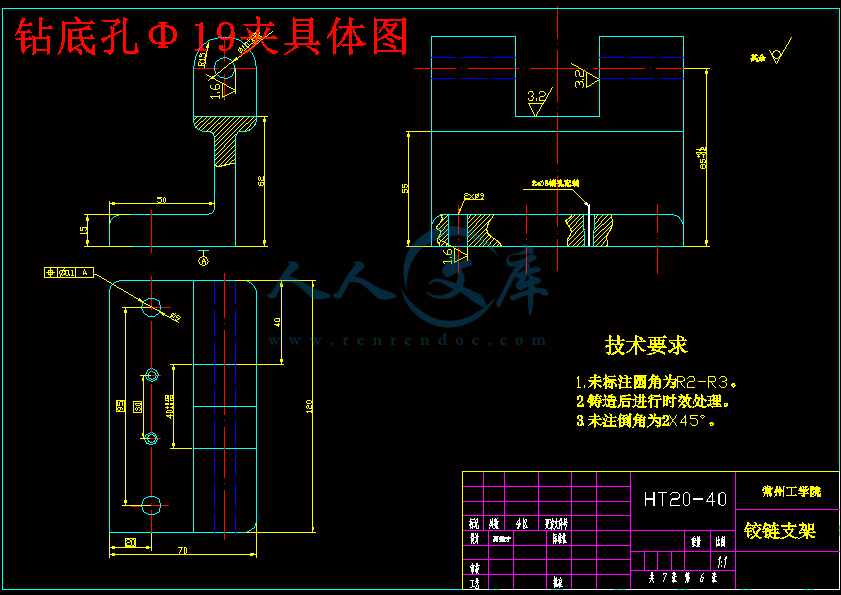

目 录
第1章 简介1
第2章 WH212减速机机壳加工工艺-2
2.1 箱体的结构-2
2.1.1尺寸较大 -2
2.1.2形状复杂 -2
2.1.3精度要求 -2
2.1.4有许多紧固螺钉定位箱孔-2
2.2 箱体的材料、毛坯及热处理-2
2.2.1?毛坯种类的确定 -2
2.2.2毛坯的形状及尺寸的确定-3
2.2.3毛坯的材料热处理3
第3章 减速机箱体加工工艺过程及分析5
3.1 速器箱体的主要技术要求5
3.2 减速器箱体的机械加工工艺过程-6
3.3 零件图分析6
3.4 减速器加工的工艺路线-7
3.4.1 加工方法的选择 -7
3.4.2 加工阶段的划分 -8
3.4.3 工序的集中与分散 -9
3.4.4 加工顺序的安排 9
第4章 减速器WH212机盖的工艺过程-13
第5章 主要表面的加工-17
5.1 箱体的平面加工17
5.2 主轴孔的加工-17
5.3 孔系加工 17
5.3.1 从箱体一端进行加工 -18
5.3.2 从箱体两端进行镗孔-18
第6章 定位基准的选择-19
6.1 粗基准的选择19
6.2 精基准的选择20
第7章 工艺尺寸的计算-22
7.1 加工余量的确定22
7.1.1 顶面与结合面的加工余量 22
7.1.2 下箱体结合面与底面的加工余量-22
7.1.3 箱体左右端面的加工余量-22
7.1.4 箱体前后端面的加工余量 -22
7.1.5 两轴承孔的加工余量22
7.2寸链的计算 -22
7.2.1 两中心面与底面的尺寸链计算-22
7.2.2 观油孔的尺寸链的计算-23
7.3 切削用量的选择24
7.4 切削的工时定额具的动作过程-27
第8章夹具设计34
8.1 设计任务分析34
8.2 设计方案论证34
8.3 切削力及夹紧力的计算-34
8.4 计及操作的简要说明 35
8.5 结构分析 35
8.6 夹具的公差 36
8.7 工序精度分析37
第9章 镗床夹具设计39
9.1 结构分析-39
9.2 夹具的结构类型39
9.3 夹紧力大小的确定原则-40
9.4 定位销尺寸确定与高度计算-42
9.4.1 定位销尺寸的确定42
9.4.2 定位销高度的计算44
总结 46
致谢 47
参考文献- 48
摘 要
本设计要求“以质量求发展,以效益求生存”,在保证零件加工质量的前提下,提高了生产率,降低了生产成本,是国内外现代机械加工工艺的主要发展方面方向之一。通过对WH212减速器箱体零件图的分析及结构形式的了解,从而对减速器进行工艺分析、工艺说明及加工过程的技术要求和精度分析。然后再对减速器箱体的底孔、轴承孔的加工进行夹具设计与精度和误差分析,该工艺与夹具设计结果能应用于生产要求。
关键词: 减速器 加工工艺 定位 夹具设计
第1章 简 介
WH212减速机是一种动力传达机构,利用齿轮的速度转换器,将马达的回转数减速到所要的回转数,并得到较大转矩的机构。
WH212减速机有很多种,各种的工作原理和结构都不相同, 它主要通过改变传动比来进行减速的,常见的有齿轮、蜗轮减速。常用的减速机有皮带,齿轮、蜗轮和行星摆线减速.齿轮减速机体积大,造价高,结构复杂,加工复杂,维修不方便,可以用于重负荷设备,蜗轮减速机结构简单,维修不便,体积大,可改变方向,有制动的作用,可用于重负荷设备.行星摆线减速机结构简单,维修方便,体积小造价低,加工复杂,可用于轻负荷设备.皮带减速,结构简单,造价低,加工简单,维修量低,减速范围低,允许丢转,用于轻负荷设备,可配合以上三种加速机一起使用,可扩大减速范围和增加启动力矩
WH212减速机的工作原理:减速机一般用于低转速大扭矩的传动设备,把电动机.内燃机或其它高速运转的动力通过减速机的输入轴上的齿数少的齿轮啮合输出轴上的大齿轮来达到减速的目的,普通的减速机也会有几对相同原理齿轮达到理想的减速效果,大小齿轮的齿数之比,就是传动比。
WH212减速机的作用
1)降速同时提高输出扭矩,扭矩输出比例按电机输出乘减速比,但要注意不能超出减速机额定扭矩。
2)速同时降低了负载的惯量,惯量的减少为减速比的平方。大家可以看一下一般电机都有一个惯量数值。
第2章WH212减速机机壳加工工艺
2.1 箱体的结构特点
箱体是机器和部件的基础零件,由它将机器和部件中许多零件连接成一个整体,并使之保持正确的相互位置,彼此能协调地运动.常见的箱体零件有:各种形式的机床主轴箱.减速箱和变速箱等.
各种箱体类零件由于功用不同,形状结构差别较大,但结构上也存在着相同的特点 :
2.1.1尺寸较大
箱体通常是机器中最大的零件之一,它是其他零件的母体,如大型减速箱体长达5~6m,宽3~4m,重50~60吨,正因为它是一个母体,所以它是机器整体的最大零件.
2.1.2形状复杂
其复杂程度取决于安装在箱体上的零件的数量及在空间的相互位置,为确保零件的载荷与作用力,尽量缩小体积.有时为了减少机械加工量或减轻零件的重量,而又要保证足够的刚度,常在铸造时减小壁的厚度,再在必要的地方加筋板.凸台.凸边等结构来满足工艺与力的要求.
2.1.3精度要求
有若干个尺寸精度和相互位置精度要求很高的平面和孔,这些第9章 镗床夹具设计
镗床夹具又称镗模它主要用于加工相体,支架等工件上的单孔或孔系。镗模不仅广泛用于一般镗床和镗孔组合机床上也可以用在一般车床、铣床和摇臂钻床上,加工有较高精度要求的孔或孔系。镗床夹具,除具有定位元件、加紧机构和夹具体等基本部分外,还有引导刀具的镗套。而且还像钻套布置在钻模板上一样,镗套也按照被加工孔或孔系的坐标位置,布置在一个或几个专用的镗孔的位置精度和孔的几何形状精度。因此,镗套、镗模支架和镗杆是镗床夹具的特有元件。
9.1 结构分析
加工工件为减速器箱体工件,要求加工两直径均为φ110mm的同轴孔。
工件的装配基准为底面和两工艺孔,本工序所加工的孔为7级精度,各孔均有一定的平行度、同轴度要求,装配基面及定位孔已精加工过。使用专用机床、粗、半精、精镗φ110H7mm孔。由于采用专用机床同时加工出各孔,所以中心与底面的距离要求为280mm,因此,底面和工艺孔是φ110 H7mm孔的工序基准。
根据基准面重合的原则,选定底面定位基准,限制三个自由度,工序孔限制三个自由度,实现定位。由于定位基准是经过加工过的光平面,故定位元件等用夹具体把两个定位元件做成一体,工件放在上面,使重力与加紧方向一致。第8章 夹具设计
设计任务:设计在成批生产条件下,在专用立式钻床上减速器底孔φ19的钻床夹具
8.1 设计任务分析
1 φ19为自由尺寸,可一次钻削保证.该孔在轴线方向的设计基准是以钻套的中心线.径线的设计基准是以轴承孔与另一端面.
2 面铣结合面是前一工序已完成的尺寸,本工序的后续工序是以孔φ19为底孔钻结合面孔,4-φ11,4-φ13.
3、专用钻床的最大钻孔直径为φ25mm.主轴端面到工作台面的最大距离H=700mm,工作台面尺寸为375x500mm2, 其空间尺寸完全满足夹具的布置和加工范围的要求。
4、本工序是对四个孔进行加工,采取移动的夹具,钻模板选用旋
式;使用快换钻套。
8.2 设计方案论证
1、定位基准的选择
工序结合面是已加工过的平面,且又是本工序要加工的孔φ19mm的设计基准,按照基准重合原则选择它作为定位基准是比较恰当的。若定位元件采用φ110的轴承孔,则基准不重合。因此,选择结合面与轴承端面作为定位比较合理。
2、夹紧结构的确定
参 考 文 献
[1]梁炳文主编,《机械加工工艺与窍门精选》,机械工业出版社。
[2]周增文 张亮蜂等编著,《机械加工工艺基础》,中南大学出版社。
[3]郑文虎编 ,《机械加工实用经验》,国防工业出版社。
[4]李喜桥编 ,《加工工艺学》,北京航空航天大学出版社。
[5]杨方主编 ,《机械加工工艺基础》,西北工业大学出版社。
[6]陈宏均主编,《实用机械加工工艺手册》,机械工业出版社。
[7]王绍俊主编,《机械制造工艺设计手册》,哈尔滨工业大学出版社。
[8]王生力主编,《重型机械制造工艺学》,冶金工业出版社1986年。
[9]谢明才等主编,《机床夹具设计》,机械工业出版社1980。
[10]李庆寿主编,《机床夹具设计》,机械工业出版社1984。
[11]李家宝主编,《夹具设计》,机械工业出版社1961。
[12]贵州工学院机制工艺研究室编,《机床夹具结构图》,机械工业出版社1983。
[13]龚定安 蔡建国编著,《机床夹具设计原理》,陕西科技出版社,1981年。
[14]潘晓弘,《机械制造工程》,浙江大学出版社2001年。
[15]刘文剑 曹天河编著,《夹具工程师手册》,黑龙江科学技术出版社1987年。
[16]于骏一主编,《典型零件制造工艺》,机械工业出版社1989年。
[17]成大先,王德夫,姜勇,等.机械设计手册[M].北京:化学工业出版社,1993。
[18]乐兑谦主编.《金属切削刀具》机械工业出版社,1985。