



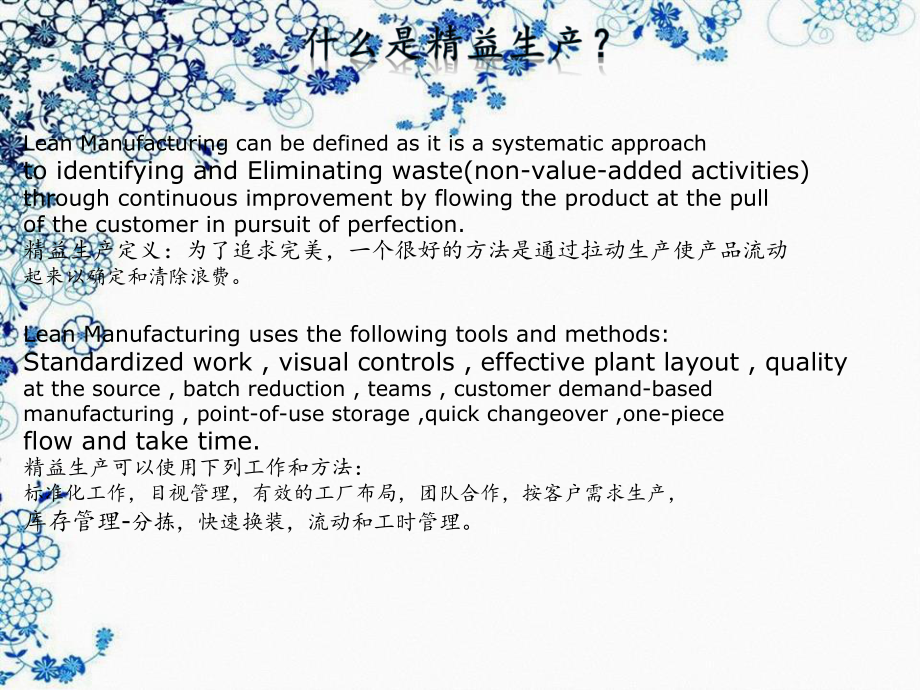
版权说明:本文档由用户提供并上传,收益归属内容提供方,若内容存在侵权,请进行举报或认领
文档简介
1、精益生产精益生产-拉动系统,拉动系统,KANBAN精益生产精益生产-TPM,OEE精益生产精益生产-5s,目视化管理,目视化管理精益生产精益生产-价值流管理价值流管理精益生产概论精益生产概论-核心理念:消除浪费核心理念:消除浪费精益思考精益思考-精益原则,精益模型,精益原则,精益模型,KAIZEN,PDCA精益生产精益生产-问题解决问题解决In 1913,Henry Ford invented the assembly line.In the1950s EijiToyoda visited Ford Plant and Taiichi Ohno spent over 20years to de
2、velop the system which became known as The Toyota Production System (TPS) to compete with the US automakers.Lean Manufacuring is well introduced with James WomacksBook,”The Machine That Changed The World”in 1990.1913年,亨利福特发明了装配流水线。上世纪50年代丰田参观了福特工厂,然后大野耐一花了20多年的时间发明了著名的丰田生产体系用来和美国汽车厂家竞争。精益生产被James Wo
3、mack 在上世纪90年代推广,并著书 The Machine That Changed The World.约定最好的质量、成本、交货期时间,重量轻可持续的改进完美交付 标准化和稳定过程工作场所组织(5 s)和可视化管理管理通过事实使用适当的工具清晰的战略基础团队合作资源的质量Lean Manufacturing can be defined as it is a systematic approach to identifying and Eliminating waste(non-value-added activities) through continuous improvement
4、 by flowing the product at the pull of the customer in pursuit of perfection.精益生产定义:为了追求完美,一个很好的方法是通过拉动生产使产品流动起来以确定和清除浪费。Lean Manufacturing uses the following tools and methods:Standardized work , visual controls , effective plant layout , quality at the source , batch reduction , teams , customer d
5、emand-based manufacturing , point-of-use storage ,quick changeover ,one-piece flow and take time.精益生产可以使用下列工作和方法:标准化工作,目视管理,有效的工厂布局,团队合作,按客户需求生产,库存管理-分拣,快速换装,流动和工时管理。Lean Manufacturing will improve:1.On-Time delivery 按时交付2.Improved response 提高反应(VSM)3.Reduced inventory减少库存(JIT)4.Improved quality 提高质
6、量(ZERO DEFECT)5.Improved material and information workflow 提高无聊和信息流6.Achievement of flexibility灵活换装(JIDOKA)7.Culure change 文化改变8.Better use of plant and skilled labour 提高工厂和技术工人使用(PRODUCTIVITY)Overproduction :increases inventory levels and associated costs , long throughput times and delays in ident
7、ifying problems. Overproduction has a negative impact on the smooth flow of materials, thus on productivity, flexibility Quality and cost. Withinthe company , overproduction means making more/faster than is required by the next process.过多生产:增加库存和相关的成本,投产的时间太长导致对确认的问题的延迟。过多的生产会对于材料生产的流程产生负面影响,也会影响生产力
8、,质量和成本的灵活性。在公司内部,生产过剩的意思是生产的速度或者生产量比下一个过程快,或者比下一个过程多。Countermeasures 方法:Balance the work load 平衡工作量Order-based scheduling根据订单生产Improve setup/changeover capacities 提高设置/换装能力Waiting is mostly due to long runs , poor production flow and machine downtime , Including waiting for the next process step or
9、for parts or for tools . Waiting is a major cause of production and sales bottlenecks and high inventory levels of raw material, parts , sub-assembly and finished goods storage.等待是由于长期不完善的生产流程和机器停顿的时间,包括等待下一个处理步骤,或是处理部分,或者是需要的工具和零件。等待是导致生产和销售瓶颈的主要原因,也是导致原材料,零部件,半成品和成品的高库存水平的主要原因。Countermeasures 方法:I
10、mprove production flow 提高生产流动Shorten production cycles减少生产时间Kanban Scheduling 看板生产Teamwork and clear responsibility团队合作和清晰责任Standardized 标准化工作Unnecessary transportation is about Material handling either to production area or within production areas .Is will impact onproduct quality and costs negativ
11、ely . It is a waste of time and can cause Waiting of the next station.不必要运输是关于在产品环节或者在生产过程中的原材料的处理。 它会对生产质量和成本产生负面的影响,是对时间的浪费,也会导致在等待下一环节时间上的损耗。Countermeasures方法:Process Mapping工艺流程图Production Line Layout Improvement产线布局调整Inappropriate Processing:means doing more or less processing to the parts or p
12、roducts than the customer really requires . It will cost more time or money or influence products quality.不合适的流程:生产比客户需求量过剩或过少的零件和产品。不合适的流程会浪费时间跟金钱,以及影响产品质量。Countermeasures 方法:根据产品变化而变化流程合适的机器和工具与客户和同事有良好的沟通 Unnecessary Motion means :the movements unnecessary to perform an operation . Such as lookin
13、g for tools and walking long way to get parts or place parts. 不必要的动作(操作):在进行操作过程中存在着不必要的动作,比如说在寻找工具或者零部件和存放场所时进行不必要的动作。Countermeasures 方法:工具就近原则(分拣)5S目视管理流程布局Unnecessary Inventory means :excess material storage or Work In Process(WIP).It is the most expensive wastes because it influencethe cash flow
14、 of the company . Excess inventory utilises shop floor space and obstructs production flows.High WIP inventory levels will cause overproduction and waiting.浪费(不必要的库存): 库存材料和工作在制品过剩,它是成本最高的的浪费,因为他们会影响公司的现金流。库存过剩还会增加建筑面积,影响生产流程,高的库存量跟在制品还会导致生产过剩及等待等问题。Countermeasures 方法:市场预测系统计划供应链管理Defects : result i
15、n rework and scrap . It requires additional resources and time to correct defects before shipping or flowing to next station.Defects cause additional material cost , production capacity losses and work rescheduling.缺陷:会导致返工和废品,还会浪费额外的资源和时间,在运输或者到下一个工作流程之前需要额外的时间跟资源去修正那些缺陷,缺陷会导致额外的材料成本,影响生产力,会影响工作时间的
16、分配。Countermeasures 方法:工作指导书和标准化工作流程控制和质量计划员工培训和基准化分析流程提高 浪费浪费: 浪费是指那些导致成本增加的因素浪费是指那些导致成本增加的因素 虽然增加价值但是耗用资源过高虽然增加价值但是耗用资源过高 一种浪费通常能够导致另外一种浪费一种浪费通常能够导致另外一种浪费 发现浪费和认识浪费的能力很重要发现浪费和认识浪费的能力很重要区分人和物的浪费区分人和物的浪费 (人的)等待时间长 (物的)紧缺材料到达不及时 (人的)擅自离开座位 (物的)材料取集困难 (物的)设计变更过多 (人的) 作业Error多 (人的)作业者能力与工作不均衡 (物的)设计图面过于
17、复杂 (物的)作业Balance不佳 (人的)不遵守计划日程 (人的)没有图纸的情况下进行加工 (物的)不检查材料 (人的)不合理的事强行 (物的)作业没有进行改善 (人的)设备点检不彻底 (人的)检查作业不充分 (人的)不合理的工作硬要执行 (人的)作业Error发现不及时 (人的)作业训练不充分 (物的)作业没有标准化 (物的)作业方法不知道 (物的)动力系统故障过多 (物的)作业标准改正过慢 (物的)设备故障过多 (人的)不清楚工厂的纪律 (人的)监督者不严厉 (人的)作业环境恶劣 (物的)修理设备不够精细 (人的)作业间信息传达不通畅 (物的)没有具备手工具 (物的)缺少测量仪器 (物
18、的)测量仪器精度不达标 (人的)参加没有效果的会议 (物的)搬运方法没有计划性 (人的)慢性加班过多 (人的)作业指示不明确 (物的)同样的事故反复出现 (人的)缺少熟练工 (人的)没有工作欲望 (物的)受伤者过多 (物的)事故不及时时向工厂反映 (物的)没有安全装置 显性浪费:显性浪费: 定义为可见浪费 这些浪费容易鉴别 如:等待时间浪费,原材料浪费 隐形浪费:隐形浪费: 定义为看不见的浪费 这些浪费不容易被鉴别 工作中看起来非常有价值直到使用才发现其中很大的浪费 如:开会,工作分配不均衡,高耗能增值工作。库存库存1.为什么出现库存的浪费?为什么出现库存的浪费? 视库存为当然 设备配置不当或
19、设备能力差 大批量生产,重视稼动 物流混乱,呆滞物品未及时处理 提早生产 无计划生产 客户需求信息未了解清楚2.出现什么样的问题?出现什么样的问题? 产生不必要的搬运、堆积、放置、找寻、防护处理等浪费动作 使先进先出的作业困难 损失利息及管理费用 物品之价值会减低、变成呆滞品 占用厂房、造成多余的工作场所、仓库建设 投资的浪费 造成无形的浪费产生后果:掩盖问题,占用资金,变质,库存准确性。解决方案:准时化生产、产线平衡、VSM、均衡生产。物料搬运(或移动)物料搬运(或移动)定义:不必要的搬运、工作的移动、预置、改装以及长距离的搬运流程和活性度差等。搬运时作业时有必要,但是搬运本身不产生附加价值
20、所以是浪费。表现形式表现形式 搬运距离很远的地方,小批量的运输 主副线中的搬运 出入库次数多的搬运 破损、刮痕的发生原因原因 生产配置不当 未均衡化生产 坐姿作业 设立了固定的半成品放置区 生产计划安排不当产生后果:增加不必要的运输设备或人员。产品或材料搬运中的损坏,库存准确性。解决方案:生产线U型配置,标准作业、自动化输送线。动作动作定义:不必要的动作、无附加价值的动作,及较慢的动作表现表现 工作时的换手作业 未倒角之产品造成不易装配的浪费 小零件组合时,握持压住的浪费 动作顺序不当造成动作重复的浪费 寻找的浪费起因起因 没有标准作业 落后的小规模作业 工程布局不好 没有教育和训练 产生后果
21、:生产过程中出现最多的浪费,具有隐蔽性。解决方案:挑战流水线生产,U字型设备布局,标准作业合作改善原则。等待等待定义:人员及设备等资源未同步所造成的空闲。表现表现 自动机器操作中,人员的“闲视”等待 作业充实度不够的等待 设备故障、材料不良的等待 生产安排不当的人员等待 上下工程间未衔接好造成的工程间的等待起因起因 生产线布置不当,物流混乱 设备配置、保养不当 生产计划安排不当 工序生产能力不平衡 材料未及时到位 管理控制点数过多 品质不良 产生后果:产能、设备及人力资源的浪费。 解决方案:采用均衡化生产,防错措施,自动化及设备保养加强(TPM),实施 目视管理加工上的浪费加工上的浪费定义:因
22、技术(设计、加工)不足造成加工上的浪费表现表现 在加工时查过必要以上的距离所造成的浪费 冲床作业上重复的试模,不必要的动作 成型后去毛头,加工的浪费 钻孔后的倒角,纹孔作业的浪费 最终工序的修正动作起因起因 工程顺序检讨不足 作业内容与工艺检讨不足 模夹治具不良 标准化不彻底 材料未检讨 产生后果:产能及设备、人力资源的浪费。解决方案:设计FMEA的确实推进,标准作业的贯彻。质量缺陷质量缺陷定义:制造不良品所损失的浪费,越做损失越大表现表现 因作业不熟练所造成的不良 因不良而修整时所造成的浪费 因不良造成人员及工程增多的浪费 材料费增加起因起因 标准作业欠缺 过分要求品质 人员技能欠缺 品质控
23、制点设定错误 认为可整修而做出不良 检查方法、基准等不完备 设备、模夹治具造成的不准确 解决方案:标准作业,防误装置,品保制度的确立及运行 定期的设备、模治具保养TPM,持续开展5S活动(1)双手应同时开始并同时完成其动作。(2)除规定时间外,双手不应同时空闲。(3)双臂的动作应对称,同一方向并同时作业。(4)手的动作幅度最小并且能得到满意结果最为妥当。(5)物体的动量应尽可能利用,但如需用手制止时,应尽可能 用最小的力。(6)连续的曲线运动,比含有方向突变的直线运动要好。(7)抛物线式的运动,较受限制的运动轻快确定。(8)动作应尽可能使用轻松自然之节奏,因节奏能使动作流利 及自发。1、关于人
24、机工程学应用:、关于人机工程学应用:(9)工具物料应放于固定处。(10)工具物料及装置应布置于工作者之前近处。(11)零件物料之供给,应利用其数量堕至工作者。(12)【堕送】方法应尽可能利用之。(13)工具物料应依照最佳之工作顺序排列。(14)应有适当之照明设备,使视觉满意舒适。(15)工作台及椅之高度,应使工作者坐立适宜。(16)工作椅式样及高度,应可使工作者保持良好的姿势。2、关于操作场所布置:、关于操作场所布置:(17)尽量解除手的工作,而以夹具或足踏工具代替。(18)可能时,应将两种工具合并为之。(19)工具物料应尽可能预放在工作位置。(20)手指分别工作时,其各个负荷按照其本能,予以
25、分配。(21)手柄的设计,应尽可能使比手的接触面积增大。(22)机器上杠杆,十字杠及手轮之位置,应能使工作者极少 变动其姿势,且能利用机械的最大能力。3、关于工具设备:、关于工具设备: 无止境的改善无止境的改善不满足一时的成功,树立起更高的目标,实践无止境不间断不满足一时的成功,树立起更高的目标,实践无止境不间断的改善。据此革新势在必行。的改善。据此革新势在必行。我们为了创造出更好的东西,一天天的进行着改良。我们为了创造出更好的东西,一天天的进行着改良。 -丰田喜一郎丰田喜一郎改善内容:动作改善、作业流程改善、物流改善、设备模夹改善内容:动作改善、作业流程改善、物流改善、设备模夹治具改善、品质
26、改善、管理改善等。治具改善、品质改善、管理改善等。 改变以达到更好持续改进思考使变好使更好为了打破为了修改为了改变改改善善改善改善+=什么是什么是KAIZEN?改善的定义:改善的定义:所谓改善,就是持续不断地改进和优化工作,通过激发作业所谓改善,就是持续不断地改进和优化工作,通过激发作业人员自身的新思维,不断寻求更佳,更适合经济效益的作业人员自身的新思维,不断寻求更佳,更适合经济效益的作业方法的一种管理理念。方法的一种管理理念。 企业最大财富:全体员工企业最大财富:全体员工 以人为本是改善出发点以人为本是改善出发点 改善是全体员工的事,一线员工是真正的专家改善是全体员工的事,一线员工是真正的专
27、家 改善不是突然的大的改变,而是细小之处的改善累积改善不是突然的大的改变,而是细小之处的改善累积 改善不是新技术的投资,是人的观念和对现状的改善改善不是新技术的投资,是人的观念和对现状的改善改善企业文化的特点改善企业文化的特点 摒弃做法的固定观念摒弃做法的固定观念 与其说明不能做的理由,不如考虑做的方法与其说明不能做的理由,不如考虑做的方法 不要找理由,首先要否定现状不要找理由,首先要否定现状 好事马上做,坏事马上停好事马上做,坏事马上停 不要追求太完美,不要追求太完美,60分就可以了,暂且先推进下去分就可以了,暂且先推进下去 对待错误,要当时当地的改正对待错误,要当时当地的改正 不感到为难就
28、运用不出不感到为难就运用不出“智慧智慧” 真正原因的追求真正原因的追求-5次反复问次反复问“为什么为什么” 一个人的一个人的“才华才华”赶不上十个人的赶不上十个人的“智慧智慧” 改善无止境改善无止境改善的基本精神改善的基本精神持续改善的步骤持续改善的步骤 选择工作任务选择工作任务 弄清当前的情况弄清当前的情况 对搜集的数据进行分析,以便弄清事情的真正背景及原因对搜集的数据进行分析,以便弄清事情的真正背景及原因 在分析的基础上研究对策在分析的基础上研究对策 导入执行对策导入执行对策 观察并记录采用对策后的影响观察并记录采用对策后的影响 修改或重新制定标准,以免类似问题再次发生修改或重新制定标准,
29、以免类似问题再次发生 检查从步骤检查从步骤1到到7的整个过程,据以引入下一步的行动的整个过程,据以引入下一步的行动 PDCA CyclePlan,Do,Check and Act :持续改善基础工作方法一持续改善基础工作方法一持续改善持续改善5MIEMAN(人)(人)METHOD(方法)(方法)MEASUREMENT(测量)(测量)MATERILA(物)(物)MACHINE(机器)(机器)ENVIRONMENTS(环境)(环境)持续改善基础工作方法二持续改善基础工作方法二持续改善持续改善5W2HHOW(怎么做?如何实施)(怎么做?如何实施)METHOD(方法)(方法)HOW MUCH(多少?(
30、多少?数量如何?什么程度?)数量如何?什么程度?)WHAT(是什么目的?(是什么目的?做什么工作)做什么工作)WHERE(何处?在哪里做?(何处?在哪里做?何处入手?)何处入手?)WHEN(什么时间完成?(什么时间完成?何时?)何时?)WHY(为什么这样做?理由(为什么这样做?理由何在?)何在?)WHO(由谁完成?)(由谁完成?)持续改善基础工作方法三持续改善基础工作方法三持续改善持续改善5P 团队团队Purpose(目标)(目标)METHOD(方法)(方法)People(人)(人)Position(团队定位)(团队定位)Power(权限)(权限)Plan & control(计划和控
31、制)(计划和控制)WHY(为什么这样做?理由何(为什么这样做?理由何在?)在?)WHO(由谁完成?)(由谁完成?)WHO(由谁完成?)(由谁完成?)改善常用工具和技巧改善常用工具和技巧 “顾客想要付钱的部分顾客想要付钱的部分”只有顾客才能定义价值只有顾客才能定义价值对整个产品定义价值对整个产品定义价值再次挑战和重新思考价值再次挑战和重新思考价值确定目标成本(去除目前所有的浪费)确定目标成本(去除目前所有的浪费)价值吸引更多的顾客价值吸引更多的顾客价值的定义价值的定义“去除所有的不创造价值的行为去除所有的不创造价值的行为”顾客要求的产品或服务形成的所有步骤的集合顾客要求的产品或服务形成的所有步骤
32、的集合(增值(增值+非增值)非增值)识别和管理每个主要产品族整个价值流识别和管理每个主要产品族整个价值流(内部价值流(内部价值流+供应链价值流)供应链价值流)价值流包含的是特定产品从进公司到发货至客户的价值流包含的是特定产品从进公司到发货至客户的所有要素(包括增值的和非增值的)。所有要素(包括增值的和非增值的)。价值流的定义价值流的定义需求需求设计设计订单处理订单处理零件生产零件生产生产装配生产装配发货发货客户客户Your Text装配装配过程过程 3原材料原材料成品成品加工加工过程过程 2加工加工过程过程 1价值流价值流 传统思维中,我们总是从原材料开始一直追逐到产品的完成来检查价值流。传统
33、思维中,我们总是从原材料开始一直追逐到产品的完成来检查价值流。Your Text价值流绘制目标价值流绘制目标为观察到物流,信息流和过程流提供了方法。为观察到物流,信息流和过程流提供了方法。支持价值流层面和工厂层面不断改进行动的优先次序支持价值流层面和工厂层面不断改进行动的优先次序化。化。为布局规划的发展提供基础。为布局规划的发展提供基础。还有:清除浪费。还有:清除浪费。6-weekForecastsIN5PRODUCTION1OXOX过程框共享的过程框信息框看板(可视信号)取货注明信息技术的过程框多名操作员操作员库存框(信息队列)库存超市卡车发货均衡(组合或数量)库存(物料队列) 现在状态的绘
34、制现在状态的绘制定义价值流(产品族)定义价值流(产品族)-从客户端开始确定价值流从客户端开始确定价值流-产品必须经过相似的工艺流程并且以相同的要求结束产品必须经过相似的工艺流程并且以相同的要求结束-门到门的范围(在厂内的价值流)门到门的范围(在厂内的价值流)步骤步骤1:选择一个价值流(产品族):选择一个价值流(产品族)列出零件数列出零件数现在状态的绘制现在状态的绘制选择组织一个综合职能的小组选择组织一个综合职能的小组选择熟悉产品的小组成员选择熟悉产品的小组成员确保小组成员已接受过使用价值确保小组成员已接受过使用价值流图的培训流图的培训任命负责人(通常是业务线经理)任命负责人(通常是业务线经理)
35、步骤步骤2:组成一个小组:组成一个小组综合职能小组维修维护维修维护产品工程产品工程物料部物料部领导支持领导支持精益顾问精益顾问工艺工程工艺工程现在状态的绘制现在状态的绘制每一个零件的计划每一个零件的计划工艺工程预算产能工艺工程预算产能生产的控制(每月生产的控制(每月/每周的预测)每周的预测)生产的历史(分析每天的差异,月度间的差异)生产的历史(分析每天的差异,月度间的差异)销售(产品更改,新业务等)销售(产品更改,新业务等)步骤步骤3:理解客户需求:理解客户需求步骤步骤4:绘制过程流:绘制过程流客户Demand/monthPart A=Part B=Part C=冲压Takt=CT=DT=ET
36、Q=C/O Time=4hrsLot Size=#Of ShiflsWIP=焊接Takt=CT=DT=20%ETQ=C/O Time=4hrsLot Size=#Of ShiflsWIP=总装Takt=CT=DT=ETQ=90%C/O Time=4hrsLot Size=#Of ShiflsWIP=发运InventoryPart A=Part B=Part C=#Of Shifls换型停机时间一次质量#Of Shifls步骤步骤5:绘制物料流:绘制物料流发运InventoryPart A=750pcxPart B=600pcxPart C=1650pcx#Of Shifls冲压Takt=CT=DT=ETQ=C/O Time=4hrsLot Size=#Of ShiflsWIP=25pcx换型焊接Takt=CT=DT=20%ETQ=C/O Time=4hrsLot Size=#Of ShiflsWIP=60pc
温馨提示
- 1. 本站所有资源如无特殊说明,都需要本地电脑安装OFFICE2007和PDF阅读器。图纸软件为CAD,CAXA,PROE,UG,SolidWorks等.压缩文件请下载最新的WinRAR软件解压。
- 2. 本站的文档不包含任何第三方提供的附件图纸等,如果需要附件,请联系上传者。文件的所有权益归上传用户所有。
- 3. 本站RAR压缩包中若带图纸,网页内容里面会有图纸预览,若没有图纸预览就没有图纸。
- 4. 未经权益所有人同意不得将文件中的内容挪作商业或盈利用途。
- 5. 人人文库网仅提供信息存储空间,仅对用户上传内容的表现方式做保护处理,对用户上传分享的文档内容本身不做任何修改或编辑,并不能对任何下载内容负责。
- 6. 下载文件中如有侵权或不适当内容,请与我们联系,我们立即纠正。
- 7. 本站不保证下载资源的准确性、安全性和完整性, 同时也不承担用户因使用这些下载资源对自己和他人造成任何形式的伤害或损失。
最新文档
- 2025年江西丰城宁能生物质发电有限公司招聘笔试参考题库附带答案详解
- 2025年山东青岛中集集装箱制造有限公司招聘笔试参考题库附带答案详解
- 2025年上海崇明县江龙建设工程有限公司招聘笔试参考题库附带答案详解
- 安全培训课件收尾
- 法制大课堂教育模板
- 小书虫作文指导课件
- 孩子梦想的课件
- 主管护师考点聚焦与试题及答案
- 行政管理专科教学改革试题及答案总结
- 行政管理专科考点及试题与答案解析
- 承包经营食堂日控管周排查月调度记录和管理表
- 陪诊可行性报告
- 专题07-对比手法(解析版)初中现代文阅读考点+答题技巧模板之记叙文
- 跨国公司的外汇风险管理分析-以TCL科技为例
- 企业防范用工风险知识讲座
- 心理健康教育课件《如何面对考试焦虑》
- 污水源热泵方案
- 完整版江苏省政府采购专家库入库考试题库(1-4套卷)
- 《唐诗中的春夏秋冬》五年级下册诗词鉴赏一等奖课件
- 围挡维修施工方案
- 智能水务一体化管理系统项目售后服务与培训方案
评论
0/150
提交评论