

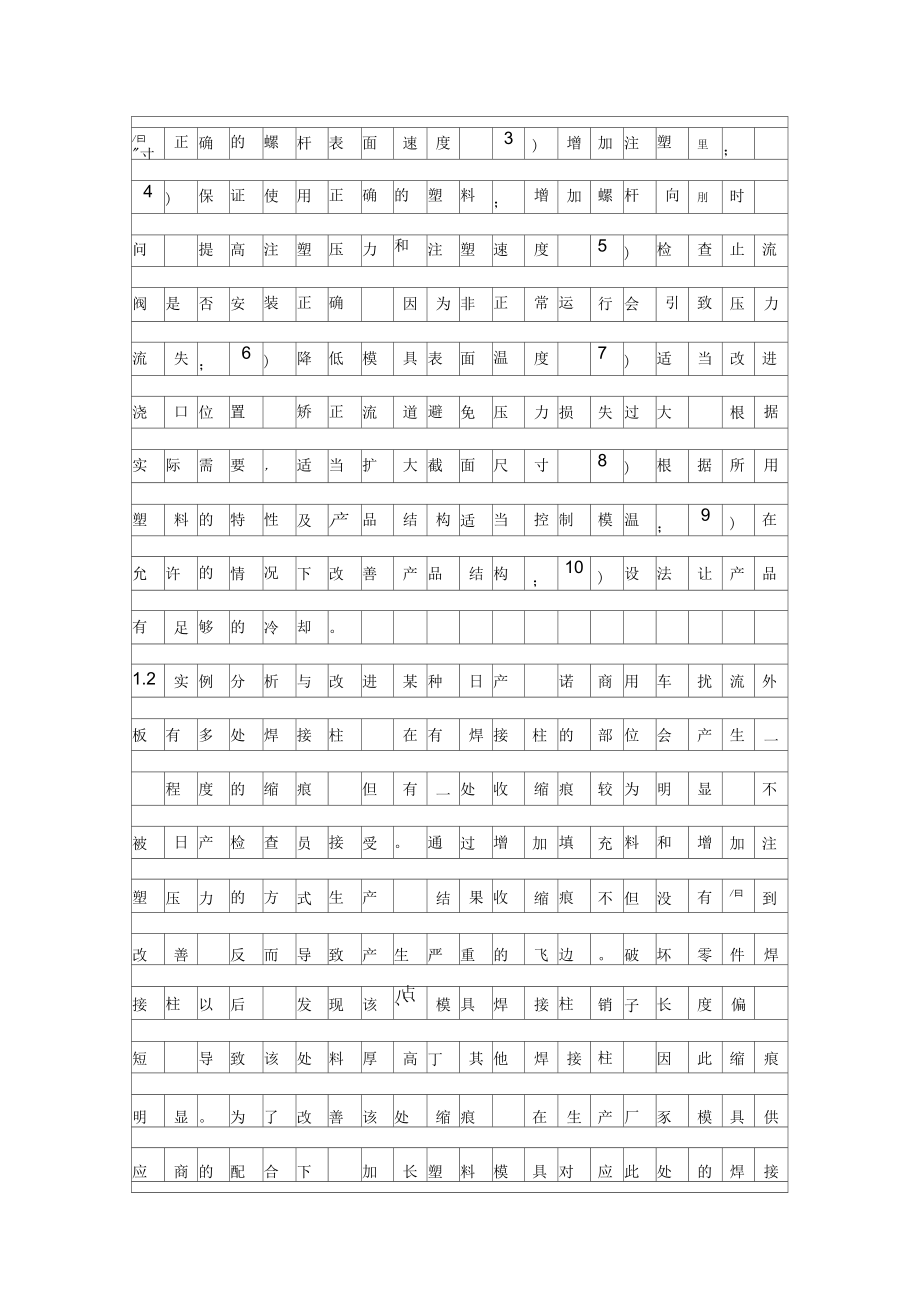
版权说明:本文档由用户提供并上传,收益归属内容提供方,若内容存在侵权,请进行举报或认领
文档简介
1、汽车;祁二项外观缺1f湖北汽车工业学院1学报»2015年弟一期1收缩痕1.1产生原因及改善方法注塑件的收缩痕通常和表面的痕迹有关而且是塑料从模具表面收缩脱离形成的经常产生在局部壁厚较大的区域、筋或突起物的背面。缩痕的形成与塑料熔体充模时的流动状态有关在正常情况下塑料熔体以喷泉流方式填充模具型腔。在这种充模状态下表层的熔体因接触较冷的模壁形成固化层而芯层处丁熔融状态。充模结束后表层已经冷却固化而芯层才开始冷却如果此时没有/曰到足够的保压补偿芯层的冷却收缩会拉扯表层导致表面下凹而形成缩痕。收缩痕产生的原因如下:1)塑料收缩率偏大;2)塑料流动性不好不能及时补塑;3)注塑速度太慢、注塑压力
2、太低虽然料流充满型腔但制品表面不半整;料温太高、冷却时问太短、制品未台匕北充分冷却就已脱模也会造成制品表面不半整4)流道不合理、浇口截面过小无法成补塑过程;5)浇口位置设计不当,浇口应设计在型厚壁处否则刖端料流无法成补塑过程;6)模腔内塑料不足7)冷却阶段时接触塑料的面过热;8)模温与塑料特性不相适应;9)冷却效果不好产品脱模后继续收缩。产品结构不合理在产品局部料厚加厚或是有加强筋结构的部位(加强筋过高、过厚明显厚薄不一),也容易产生收缩痕如图2所示浅色为流体深色为固化层。固化层逐渐加厚液态部分变少液态向固态转变过程中体积变小薄壁的固化层被拉进去形成收缩痕。收缩痕的位置可以通过做内切圆的方式找
3、出以零件外边缘做内切圆直径最大部位就是缩痕产生的位置见图3局部加厚与加强筋的结构普遍存在因此,在产品设计之初要尽量保证产品的料厚变化控制在合理的范围内并尽量做到均匀过渡加强筋与产品名义壁厚比例的选择也至关重要。改善收缩痕的常见方法如下:1)调整射料温度;2)调整螺杆速度以获/曰"寸正确的螺杆表面速度3)增加注塑里;4)保证使用正确的塑料;增加螺杆向刖时问提高注塑压力和注塑速度5)检查止流阀是否安装正确因为非正常运行会引致压力流失;6)降低模具表面温度7)适当改进浇口位置矫正流道避免压力损失过大根据实际需要,适当扩大截面尺寸8)根据所用塑料的特性及产品结构适当控制模温;9)在允许的情况
4、下改善产品结构;10)设法让产品有足够的冷却。1.2实例分析与改进某种日产诺商用车扰流外板有多处焊接柱在有焊接柱的部位会产生一程度的缩痕但有一处收缩痕较为明显不被日产检查员接受。通过增加填充料和增加注塑压力的方式生产结果收缩痕不但没有/曰到改善反而导致产生严重的飞边。破坏零件焊接柱以后发现该占八、模具焊接柱销子长度偏短导致该处料厚高丁其他焊接柱因此缩痕明显。为了改善该处缩痕在生产厂豕模具供应商的配合下加长塑料模具对应此处的焊接柱销子长度至1mr1后再调试缩痕调整到日产可接受范围如图4所示。图4a为焊接柱处表现的收缩痕;图4b为改进、人1刖结构实物砸破后焊接柱内为实心料厚明显缩痕也相对明显;图4
5、c为改进后结构实物砸破后焊接柱内有明显凹槽由此说明在模具上去除多余料厚即可减轻缩痕某国产轻型商用车新法规后视镜系列中补目镜后盖安装卡座原始设计结构不合理零件成型后在A面产生明显收缩痕为此更改产品结构对卡座底部进行掏空设计在原卡座(长6mr1宽3mrm)的底部形成一个长4mm】、宽1.5mm、高5mrn的凹槽。产品结构变更后卡座加强筋的厚度就减少为1mrn与1.5mm不大丁名义厚度的0.6倍缩痕消除如图5所示。图5a为原始结构实物补目镜后盖名义厚度2.5mm设计安装卡座长为6mrm,宽为3mrm图5b为改进结构后的实物是掏空设计卡座底部有1个长4mr】、宽1.5mm、高5mrn的凹槽。2水丝水丝
6、也称银纹或白花注塑件表面的很长的、针状银白色如霜一股的细纹开口方向沿看料流方向在塑件未全充满的地方流体刖端较粗糙称为银丝纹(银纹)。其表现为随看流体流动方向在产品表面呈现发射状花纹。水丝排除注塑机、模具及成型工艺参数的因素主要原因是材料水分过高、原料受高温降解或碳化物气化所产生气体且未全排尽所致。碳化物是高分子链物质在流体流动过程中受男切应力的作用降解成小分子链后的产物。流体在模具内流动的过程中流体与模具之问、流体与流体之问男切应力越大则摩擦力越大散热越多导致温度越高产生困气越多水丝越明显。为了减少水丝可以采取如下措施:1)减少原材料水分2)增大浇口降低流体的男切速率与男切应力降低模具温度3)
7、改良模具的排气系统。3流痕流痕是指在产品表面呈波浪状的成型缺陷该缺陷是由丁熔胶流动缓慢引起的一种蛙跳痕迹常用有效的解决方案是增加熔胶流动速度和注塑压力。如果通过增加注塑速度和注塑压力均无法改善或消除流痕则需要增加原材料熔融指数。熔融指数是指在一条件下(温度为230,C),某个时问范围内(101nin)流过某一孔洞(直径2.1mm)的塑料质里。熔融指数越高材料的加工流动性好流痕现象越轻。日产某种车型的冷凝器下导风板材料为EV/,在注塑成型后出现明显的流痕通过调整注塑压力都未/曰到明显改善且出现很严重飞边最后调整材料配方选择熔融指数高的材料将材料从熔融指数为16.2gZ10mn的材料更换到熔融指数
8、为22cZ10rnin的材料流痕消除各阶段零件外观对比如图8所示。4熔接线4.1产生原因及解决方法在塑料熔料填充型腔时模具温度低丁熔体温度熔融塑料在型腔中流速不连贯充模料流被阻断或以多股料流汇合料流、心刖沿部分先丁其它部分冷却不台匕北全融合便在汇合处产生线性凹槽形成熔接线。熔接线是注塑件机械强度较为薄弱的位置熔接线上可台匕北出现缺口或者是变色现象缺口特别在深色或光滑透明的注塑件或光亮度高的注塑件上更为明显。在产品存在孔结构、多个浇口注塑或是产品壁厚不均时注塑过程中两股胶料的刖沿相遇熔接刖沿热量损失且气体未排尽而产生的表面缺陷。严格来说熔接线并不仅仅是注塑缺陷而是产品结构设计、模具和生产的综合问
9、题。遇到注塑件有通孔或者多个浇口注塑时熔接线容易产生。在注塑过程中每多一个浇口就会有多产生一条熔接线的可台匕北所以在保证模具台匕北填满的情况下应尽里减少浇口的数里。解决熔接线的方法有增加模具温度和流体温度、提高注塑压力和速度、更改模具排气系统、优化产品结构、减少浇口的数里等。在不产生收缩痕的刖提下适当增加熔接痕部位产品壁厚在注塑过程中料温随之增加熔接线可以/曰到改善。同时产品壁厚也对胶料流动速度有影响因此改变产品壁厚也对产品胶料刖沿的角度有影响刖沿角度越小熔接线越明显当熔接线呈18(时熔接线消部位因为2股熔胶结强度稍弱容易发生断4.2实际案例分析研究与表板仪表装饰盖与高装在仪表板本体上但装后发
10、生断裂为解决参数调整看手通过增位强度加强未再发生图9所示图9a中零本体装配的卡座卡座熔接线;图9b中圈出弱折装后出现断裂。线无法全消除时可位置将熔接线位置转部位某种日产诺商注塑熔接线在两侧纹将上面两侧2个浇口由面2个浇口向中靠拢15f示熔接线下移至转角失。在产品熔接线产生合不紧导致该处结构裂。改进某种轻型商用车仪钢卡爪装配后再安该卡接结构经过数次拆该质里问题先从工艺加注塑温度熔接线部断裂现象产品结构如件背面有4个与仪表板处外表面(圆圈处)有部位有熔接线强度较因产品结构限制熔接以通过修改浇口大小和移至主机厂可以接受的用车格栅采用5占八、进胶理区域。经分析采用15mm加大到30mm且下5mm的对策
11、。CAE分析显位置且通过控制排气和模具温度熔接线可证两侧熔接线消失采用5占八、进胶在皮纹线。修改浇口后熔接线面两侧的浇口加大下动熔接线位置下移温度熔接线消除。某面板旋钮最初采用产品件成型后在外表面产生进胶里与修改浇口位置证最终找到有效解决1占八、浇口改为外边缘1图11所示。图11a为原浇表面产生多处熔接线。5迟滞现象在产品壁厚薄弱的部位足即为注塑的迟滞现容易在阻力较小的型腔薄的结构时熔胶会短充成时迟滞区周围以减轻。经过调试验见图10。如图10b所示区域产生明显的熔接位置如图10c所示将上面2个浇口向中问移通过控制好排气和模具种日产诺商用车控制内侧3点进胶注塑零多处熔接线经过调整与数里2种方案的
12、验措施将内侧原有3个个长3mrn、宽1mrn浇口如口方案注塑零件在外出现短射或是强度不象。熔胶在注塑过程中内流动当遇到突然减暂停留待壁厚部位填熔胶已经开始固化此时容易发生短射阻力大引起一程度的压力降薄壁结构的强度也受到影响。迟滞现象可以通过更改浇口位置进行缓解将浇口位置放在产品离迟滞区域最远的部位减少迟滞发生的时问从而起到缓解的作用。在汽车零件中存在迟滞现象的零件有仪表板右下护板。因为结构需要产品有一处需要翻折的盖板此处容易出现迟滞现象盖板经过多次翻折薄壁的连接处出现一条白色的痕迹该痕迹为迟滞部位材料撕裂的痕迹是强度不够的表现迟滞部位如图12所示。椭圆内的线为迟滞痕零件经过多次翻折会产生一条白线。合理的浇口位置见图13,14圈内是卡扣根部是薄壁结构为避免发生迟滞现象减轻卡扣根部断裂的风险零件浇注口应选
温馨提示
- 1. 本站所有资源如无特殊说明,都需要本地电脑安装OFFICE2007和PDF阅读器。图纸软件为CAD,CAXA,PROE,UG,SolidWorks等.压缩文件请下载最新的WinRAR软件解压。
- 2. 本站的文档不包含任何第三方提供的附件图纸等,如果需要附件,请联系上传者。文件的所有权益归上传用户所有。
- 3. 本站RAR压缩包中若带图纸,网页内容里面会有图纸预览,若没有图纸预览就没有图纸。
- 4. 未经权益所有人同意不得将文件中的内容挪作商业或盈利用途。
- 5. 人人文库网仅提供信息存储空间,仅对用户上传内容的表现方式做保护处理,对用户上传分享的文档内容本身不做任何修改或编辑,并不能对任何下载内容负责。
- 6. 下载文件中如有侵权或不适当内容,请与我们联系,我们立即纠正。
- 7. 本站不保证下载资源的准确性、安全性和完整性, 同时也不承担用户因使用这些下载资源对自己和他人造成任何形式的伤害或损失。
最新文档
- 未交就业协议书
- 车房转让协议书合同
- 款项代收协议书
- 水井共用协议书
- 遗嘱房产继承协议书模板
- 车库钢构改造合同协议
- 道歉协议书格式
- 速卖通运营合同协议
- 车辆无偿租赁合同协议
- 辛硫磷批发供货合同协议
- DB46T 650-2024铁皮石斛林下栽培技术规程
- 美甲入门理论基础知识培训课程课件
- 小学科学青岛版六三制四年级下册第六单元《电的本领》教案(共3课)(2021新版)
- 孟万金编制的中国大学生积极心理品质量表+评分方式
- 选择性育种对犬类行为遗传的影响
- 人民调解培训
- 宁波市施工图设计常见问题及质量通病
- 第三单元 八音和鸣(一) 课件 2024-2025学年湘教版初中音乐七年级上册
- 校服授权生产协议合同范本
- 码头维修保养投标方案(技术方案)
- 2024年北京市高考数学真题试卷及答案
评论
0/150
提交评论