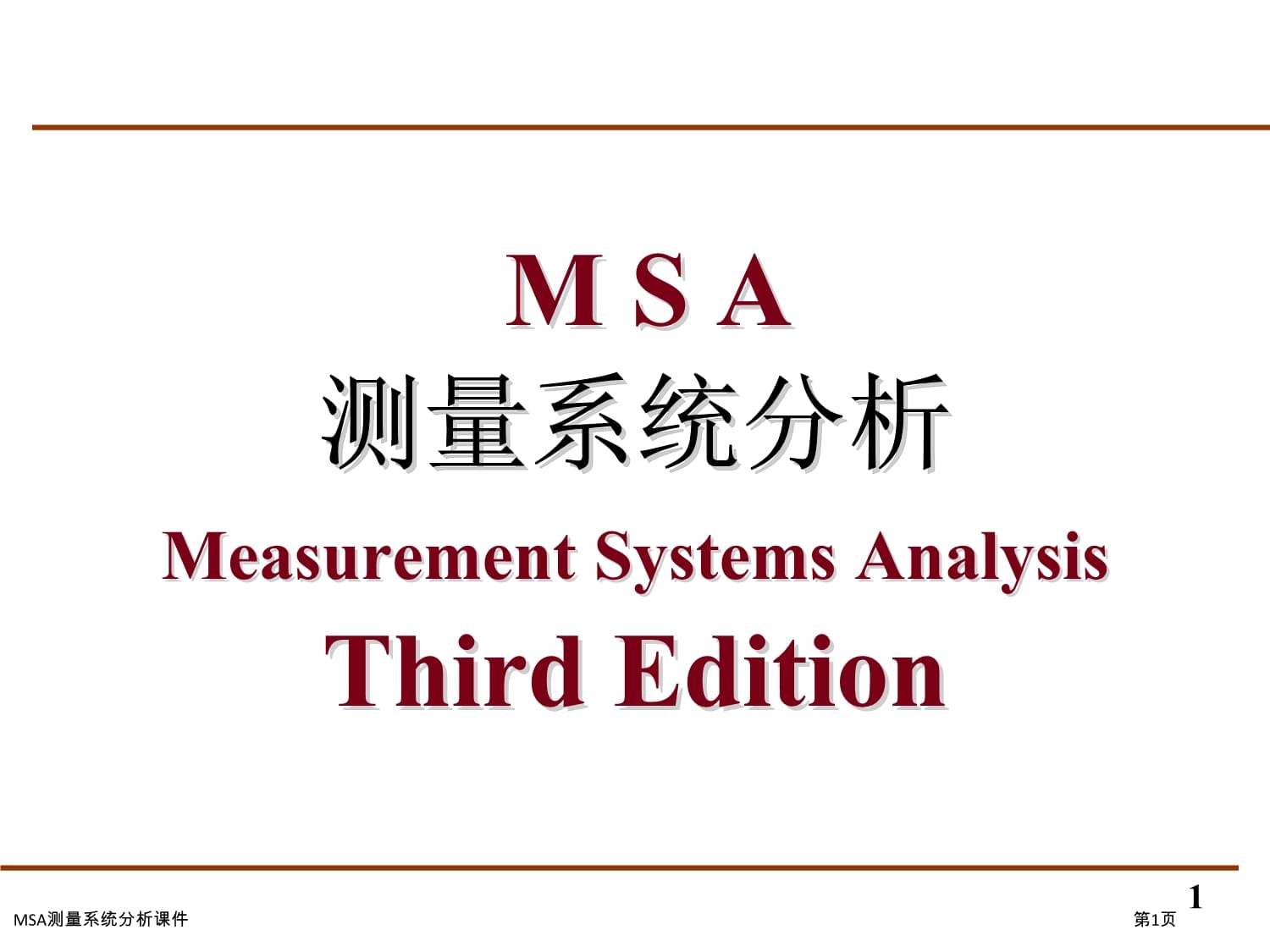




版权说明:本文档由用户提供并上传,收益归属内容提供方,若内容存在侵权,请进行举报或认领
文档简介
MSA
测量系统分析
MeasurementSystemsAnalysis
ThirdEdition1MSA测量系统分析课件第1页MSA培训课程目录差异分析(了解学员或企业现实状况提出改进提议)MSA目标及应用时机MSA术语介绍测量误差类型及影响测量问题分析方法及程序计量型测量系统分析及案例-稳定性(控制图法)-偏倚(独立样件法和控制图法)-线性(t检定)-重复性和再现性(极差法\均值极差法\方差分析法)计数型测量系统研究及案例-风险分析方法(假设性试验分析\信号探测理论)-分析法计数型测量系统研究及案例其它测量系统介绍并提供EXCEL程序2MSA测量系统分析课件第2页差异分析
了解学员或企业现实状况提出改进提议3MSA测量系统分析课件第3页MSA第三版改进
为符合QS9000:1998要求使用了新格式更多范例和说明讨论了测量不确定度概念包含测量系统寿命周期概念促使MSA成为常规过程分析…4MSA测量系统分析课件第4页MSA目标及应用时机
1.1测量数据作用:决定产品和过程符合性回归分析5MSA测量系统分析课件第5页1.2表征数据质量统计指标
--测量定义:对某详细事物赋予数字(或数值),以表示它们对于特定特征之间关系.
--量具(Gage)是指任何用来取得测量装置。经常是尤其用在工厂现场装置,包含通/止规(go/nogodevice)。
--测量系统(Measurementsystem)是对测量单元进行量化或对被测特征进行评定,其所使用仪器或量具、标准、操作、方法、夹具、软件、人员、环境及假设集合;也就是说,用来取得测量结果整个过程。MSA目标及应用时机
6MSA测量系统分析课件第6页1.2表征数据质量统计指标
在你企业中,需要测量什么过程和/或产品特征?
一个好或高质量测量具备哪些特点?
一个差或低质量测量具备哪些特点?
假如某一特征测量值靠近它参考值,则称该数据质量高.
假如某一特征测量值远离它参考值,则称该数据质量低.
偏倚(bias)和变差(variance)MSA目标及应用时机
7MSA测量系统分析课件第7页1.3MSA应用时机:
ISO/TS16949:
7.6.1
测量系统分析
为分析出现在各种测量和试验设备系统测量结果
中变差,必须开展统计研究.本要求必须适合用于在控制计划提及测量系统.全部分析方法和接收标准必须符合客户相关测量系统分析参考手册.假如得到客户同意,也可使用其它分析方法和接收标准.MSA目标及应用时机
8MSA测量系统分析课件第8页1.3MSA应用时机:
APQP:
第三章过程设计和开发
3.9测量系统分析计划
产品质量策划小组应确保依据要求制订一个测量系统分析计划。这个计划最少应包含确保量具线性、准确度、重复性、再现性和与备用量具相关性职责。参见MSA手册。
第四章产品和过程确认
4.2测量系统评价
在试生产当中或之前,应使用要求测量装置和方法按工程规范,检验控制计划标识特征并进行测量系统评价。参见MSA手册。MSA目标及应用时机
9MSA测量系统分析课件第9页1.3MSA应用时机:
PPAP:
I.2.2.9初始过程研究
I.2.2.9.1总则
为了了解测量误差是怎样影响被研究测量值,供方必须进行测量系统分析。(见I.2.2.10和MSA手册)
I.2.2.10测量系统分析研究
供方必须对全部新或改进后量具、测量和试验设备进行适当测量系统分析研究,如:量具重复性和在现性、偏差、线性和稳定性研究。(见I.2.2.9.1和MSA手册)
MSA目标及应用时机
10MSA测量系统分析课件第10页2.1可操作定义
可相互交流含有相同含义如:特定试验判断用准则决定:是或者不是,符合或不符合术语
11MSA测量系统分析课件第11页2.2标准用于比较可接收偏倚接收准则被接收而为一真值参考值术语
传递标准传递标准校准标准参考标准工作标准基准基准检验标准测量和试验设备12MSA测量系统分析课件第12页2.3参考值用高一级测量设备(如:度量衡试验室或全尺寸检验设备)屡次测量平均值法定值理论值常被用来替换真值(零件实际值)术语
13MSA测量系统分析课件第13页2.4分辨力术语
分辨力是指一测量仪器能够检测并忠实地显示相对于参考值改变量。通常也被称为可读程度或分辨率。这种测量能力通常是某测量仪器上最小刻度值。假如仪器刻度较“粗略”,则能够使用刻度值二分之一作为解析度。一个通用百分比规则是,测量设备分辨力要最少等于被测量距离十分之一,传统上把该距离看成是产品规范;最近这10:1规则意义被解释为:测量设备要能分辨出过程变差最少十分之一以上。这与连续改进构想是一致。(比如:过程关注焦点是一用户指定目标。)14MSA测量系统分析课件第14页2.4分辨力术语
分辨力15MSA测量系统分析课件第15页2.4分辨力术语
控制只有在以下条件下才可用于控制:与规范相比,过程变差较小在预期过程变差上,损失函数很平缓过程变差主要起源造成了平均值偏移分析用于过程参数及指数预计是不可接收只能指出过程是否正在产生合格或不合格零件依据过程分布,可被用为准计量型控制技术可产生不敏感计量型控制图用于过程参数及指数预计普通是不可接收,因为它仅提供粗劣预计可用于计量型控制图提议使用图5:过程分布区分分类数(NumberofDiStinctCategories,ndc)对控制与分析活动影响16MSA测量系统分析课件第16页2.4分辨力术语
过程控制图17MSA测量系统分析课件第17页2.5测量过程变差术语
图7:测量过程变差特征18MSA测量系统分析课件第18页2.6偏倚对相同零件上同一特征观察平均值与真值(参考值)差异术语-位置变差
19MSA测量系统分析课件第19页偏倚过大原因
术语-位置变差
仪器需要校准仪器、设备或夹具磨损基准磨损或损坏,基准偏差不适当校准或使用基准设定仪器质量不良——设计或符合性线性误差使用了错误量具不一样测量方法——作业准备、载入、夹紧、技巧测量特征不对变形(量具或零件)环境——温度、湿度、振动、清洁错误假设,应用常数不对应用——零件数量、位置、操作者技能、疲劳、观察误差(易读性、视差)20MSA测量系统分析课件第20页2.7稳定性稳定性(或漂移)是指经一段长久时间下,用相同测量系统对同一基准或零件同一特征进行测量所取得总变差.也就是说,稳定性是整个时间偏倚改变.术语-位置变差
21MSA测量系统分析课件第21页造成不稳定可能原因
术语-位置变差
仪器需要校准,缩短校准周期仪器、设备或夹具磨损正常老化或损坏维护保养不好——空气、动力、液体、过滤器、腐蚀、尘土、清洁基准磨损或损坏,基准误差不适当校准或使用基准设定仪器质量不好——设计或符合性仪器缺乏稳健设计或方法不一样测量方法——作业准备、载入、夹紧、技巧变形(量具或零件)环境改变——温度、湿度、振动、清洁错误假设,应用常数不对应用——零件数量、位置、操作者技能、疲劳、观察误差(易读性、视差)22MSA测量系统分析课件第22页①测量系统稳定外部条件是什么?如有些测量系统在使用前需要预热5分钟才能使用②受控测量系统是否σ较大?
受控测量系统不一定能够接收,σ越大,PV越大,即过程变差大,此时要分析原因。有些测量系统对周围环境交互作用太敏感,则要改进测量系统对环境敏感性。③测量系统稳定性能够保持多长时间?
用更高一级测量系统定时对其进行校准。保持稳定性主要问题23MSA测量系统分析课件第23页2.8线性线性是在测量设备预期工作(测量)量程内,偏倚值差异.线性可被视为偏倚对于量程大小不一样所发生改变.术语-位置变差
24MSA测量系统分析课件第24页造成线性误差可能原因术语-位置变差
仪器需要校准,缩短校准周期仪器、设备或夹具磨损维护保养不好——空气、动力、液体、过滤器、腐蚀、尘土、清洁基准磨损或损坏,基准误差——最小/最大不适当校准(没有涵盖操作范围)或使用基准设定仪器质量不好——设计或符合性缺乏稳健仪器设计或方法应用了错误量具不一样测量方法——作业准备、载入、夹紧、技巧伴随测量尺寸不一样,(量具或零件)变形量不一样环境——温度、湿度、振动、清洁错误假设,应用常数不对应用——零件数量、位置、操作者技能、疲劳、观察误差(易读性、视差)25MSA测量系统分析课件第25页2.9重复性传统上称为评价人内部变差用一个评价人使用相同测量仪器对同一零件上同一特征进行屡次测量所得到测量变差.通常称为设备变差(EquipmentVariation,EV)术语-宽度变差
26MSA测量系统分析课件第26页造成重复性误差可能原因术语
术语-宽度变差
零件内部(抽样样本):形状、位置、表面光度、锥度、样本一致性仪器内部维修、磨损、设备或夹具失效、质量或保养不好标准内部质量、等级、磨损方法内部作业准备、技巧、归零、固定、夹持、点密度变差。评价人内部:技巧、位置、缺乏经验、操作技能或培训、意识、疲劳环境内部对温度、湿度、振动、清洁小幅度波动错误假设——稳定,适当操作缺乏稳健仪器设计或方法,一致性不好量具误用失真(量具或零件)、缺乏坚固性应用——零件数量、位置、观察误差(易读性、视差)27MSA测量系统分析课件第27页2.10再现性传统上称为评价人之间变差不一样评价人使用相同测量仪器对同一零件上同一特征进行测量所得到平均值变差.通常称为评价人变差(AppraiserVariation,EV)术语
术语-宽度变差
28MSA测量系统分析课件第28页造成再现性误差可能原因术语
术语-宽度变差
零件之间(抽样样本):使用相同仪器、操作者和方法测量A、B、C零件类型时平均差异。仪器之间:在相同零件、操作者和环境下使用A、B、C仪器测量平均值差异。注意:在这种情况下,再现性误差通常还混有方法和/或操作者误差。标准之间:在测量过程中,不一样设定标准平均影响。方法之间:因为改变测量点密度、手动或自动系统、归零、固定或夹紧方法等所造成平均值差异。评价人(操作者)之间:评价人A、B、C之间因为培训、技巧、技能和经验所造成平均值差异。推荐在为产品和过程判定和使用手动测量仪器时使用这种研究方法。环境之间:在经过1、2、3等时段所进行测量,因为环境周期所造成平均值差异。这种研究惯用在使用高度自动化测量系统对产品和过程判定。研究中假设有误。缺乏稳健仪器设计或方法。操作者培训有效性。应用——零件数量、位置、观察误差(易读性、视差)。29MSA测量系统分析课件第29页2.11量具R&R或GRR量具R&R是结合了重复性和在现性变差预计值.换句话说,GRR值等于系统内部变差和系统之间变差和.σ2GRR=σ2再现性+σ2重复性术语
术语-宽度变差
30MSA测量系统分析课件第30页2.12测量系统能力是基于在短期评定中测量系统误差(随机和系统)组合变差预计值.包含:不准确偏倚或线性重复性或再现性(GRR),包含短期一致性σ2能力=σ2偏倚或线性+σ2GRR术语
31MSA测量系统分析课件第31页2.12测量系统性能是全部重大和决定性变差起源长久总影响,组合了测量误差(随机和系统)长久预计值.包含:能力(短期误差)稳定性和一致性σ2性能=σ2能力+σ2稳定性+σ2一致性术语
32MSA测量系统分析课件第32页2.13不确定度是一个与测量结果相关参数,其特征是因为被测物特征所可能合理造成数值离散.测量实际值=测量观察值(结果)±UU=Kuc(组合标准差uc包含测量过程中全部重大变差要素)uc2=σ2能力+σ2稳定性
与MSA主要不一样点:MSA专注于了解某测量过程,确定这过程中误差大小,并评定这测量系统是否适合用于产品和过程控制.MSA提升了解和改进(降低变差).不确定度是测量值范围,经过一个置信度区间定义,与测量结果相关,并预期包含测量真值.术语
33MSA测量系统分析课件第33页2.14可追溯性经过一条比较链追溯到NMI。不过在工业界许多情况下,测量可追溯性可能追溯到用户和供方双方同意参考值或“一致标准”术语
图1:长度测量可追溯性链举例34MSA测量系统分析课件第34页2.14评论偏倚和重复性是相互独立控制了一些误差起源中一个原因,不能确保控制了其它误差原因.一个理想测量系统是每次使用时均能产生“正确”测量结果;能够产生这么测量结果测量系统被称为含有以下统计特征:零变差零偏倚对其所测量产品被错误分析可能性为零。
术语
35MSA测量系统分析课件第35页3.1测量过程
测量误差类型及影响
36MSA测量系统分析课件第36页3.2“好”测量系统基本特征:
1.含有足够分辨力和敏感度.
2.测量系统应处于统计受控状态.
3.为了产品控制,测量系统变差必须小于规范
限值.
4.为了过程控制,测量系统变差应该能证实具
有有效精密度,而且小于制造过程变差.测量误差类型及影响
37MSA测量系统分析课件第37页3.3测量系统误差起源
测量误差类型及影响
38MSA测量系统分析课件第38页3.4测量系统误差影响
测量误差类型及影响
原理关注点产品控制零件是否在指定范围内?过程控制过程变差是否稳定并可接收?表1:控制理论和驱使关注点39MSA测量系统分析课件第39页对产品决议影响
测量误差类型及影响
图中,第Ⅰ类区 坏零件永远被称为坏零件第Ⅱ类区 可能做出潜在错误决定第Ⅲ类区 好零件永远被称为好零件两个选择:改进生产过程:降低过程变差,不会生产出落在区域Ⅱ产品。改进测量系统:降低测量系统误差以减低区域Ⅱ大小,这么,生产出全部产品将全部落在区域Ⅲ内,且就能降低做犯错误决定风险。40MSA测量系统分析课件第40页对过程决议影响
测量误差类型及影响
..将普通原因识别为特殊原因..将特殊原因识别为普通原因实际与观察到过程变差之间基本相互关系为:σ2观=σ2实+σ2测σ2观——观察到过程变差值σ2实——实际过程变差σ2测——测量系统变差能力指数9Cp由下式计算:(Cp)-2观=(Cp)-2实+(Cp)-2测举例说明,假如测量系统Cp值为2,实际过程Cp必须大或等于1.79,才能得到1.33计算值(观察值)。假如测量系统Cp值本身只有1.33,则该过程需要没有任何变差才能使观察到过程能力到达1.33—显而易见,这是个不可能存在情况。41MSA测量系统分析课件第41页漏斗试验
测量误差类型及影响
漏斗试验有以下四个规则:规则1:除非过程不稳定,不然不要进行调整或采取办法。规则2:从过程上一次被测量偏向相反方向,对过程调整一个相等量。规则3:将过程重新设置到目标值,然后从目标值往相反方向调整一个相等量。规则4:将过程调整到上一次测量位置。42MSA测量系统分析课件第42页3.5测量系统误差分为五类:
偏倚
重复性
再现性
稳定性
线性测量误差类型及影响
43MSA测量系统分析课件第43页测量误差类型及影响
接收一新测量设备准则。一个测量装置与另一个测量装置比较。评价一个疑似不充分量具依据。测量设备维修前后比较。为计算过程变差以及生产过程可接收程度必要组成描绘量具性能曲线(GPC)必要信息。量具性能曲线是指接收某一零件真值概率。44MSA测量系统分析课件第44页3.1测量问题分析
1识别问题
2识别小组
3测量系统和过程流程图
4因果图
5计划——实施——研究行动(PDSA)
6可能处理方法及纠正证实
7将变更制度化测量问题分析方法及程序45MSA测量系统分析课件第45页3.2第1&2阶段
第1阶段
了解测量过程,确定它是否满足要求?
第2阶段
伴随时间推移,测量系统是否能连续满足要求?测量问题分析方法及程序46MSA测量系统分析课件第46页3.3选择/开发试验程序:
1.试验中是否应该使用诸如那些可追溯至NIST标准?对
于在第二阶段连续试验,应考虑使用盲测
2.试验成本。
3.试验所需要时间。
4.任何没有被普遍接收术语应该被可操作定义。
5.由这个测量系统取得测量结果是否要与另外一个测量系
统得到测量结果比对?
6.第2阶段试验应该每隔多久进行一次?
测量问题分析方法及程序47MSA测量系统分析课件第47页3.4测量系统研究准备
1.应该计划所使用方法。
2.应该事先确定评价人人数、抽样零件数量,及重复读数数量等。
3.因为目标是评价全部测量系统,评价人应该从那些正常操作该仪器
人员中选择。
4.样件选择对适当分析是很关键:
5.仪器应该有足够分辨力,特征直接被读出值最少是预期过程变差
十分之一。
6.确保测量方法(如评价人和仪器)是测量特征尺寸,并遵照已定义测
量程序。
7.测量应该以一随机次序进行,从而确保可能发生漂移或改变将随机地
分布在整个研究中。
8.对设备读值,应该按测量仪器解析度实际极限纪录这测量值。
9.这研究工作应该由了解实施一个可靠研究主要性人员负责管理和监
督测量问题分析方法及程序48MSA测量系统分析课件第48页3.5结果分析
接收性准则——位置误差
位置误差通常被定义为偏倚和线性分析。
通常,假如—测量系统偏倚或线性误差显著异于零、或超出该量具校准程序中所建立最大允许误差,则该测量系统为不可接收。在这种情况下,应该对这测量系统进行重新校准或进行一个赔偿修下来降低这误差。
测量问题分析方法及程序49MSA测量系统分析课件第49页3.5结果分析
接收性准则—宽度误差
一测量系统变差是否为满意准则,取决于测量系统变差对制造过程误差或零件公差所占百分比。对特定测量系统最终接收准则取决于测量系统环境和目标,而且应该经用户同意。
对于目标是用来分析—过程测量系统,对测量系统可接收性通用百分比标准以下:
低于10%误差——通常被认为是一个可接收测量系统。
10%到30%误差——依据应用主要性、测量装置成本、维修费用等,可能是可接收。
大于30%误差——考虑为不可接收一应该尽各种力量以改进这测量系统。
另外,由测量系统对过程进行划分区分分类数(ndc)要能大于或等于5。
一测量系统最终可接收性应该不但仅取决于一些简单指数,应该同时使用随时间改变图表来分析测量系统长久性能。测量问题分析方法及程序50MSA测量系统分析课件第50页4.1稳定性简单测量系统-计量型1)取得一样件并建立其可追溯到相关标准参考值。
2)以一定周期基础(天天、每七天)测量基准件三到五次。
3)将数据按时间次序画在&R或&s控制图上。
结果分析——图示法
建立控制限,使用控制图分析法来评价是否有不受控或不稳定情况。
结果分析——数值法
除了通常控制图分析法外,没有用于稳定性分析特定数值分析或指数。
假如该测量系统为稳定,这些数值可用来确定测量系统偏倚。51MSA测量系统分析课件第51页4.1范例—稳定性简单测量系统-计量型选取了生产过程输出范围中靠近中间值一个零件。该零件被送到了测量试验室,经测量其参考值确定为6.01。小组每班测量该零件5次,共测了四面(20个子组);搜集到全部数据后,画出了X&R图
(用于稳定性分析控制图)
控制图分析表明该测量过程处于稳定状态,因为没有显著可见特殊原因结果发生。52MSA测量系统分析课件第52页4.2偏倚-独立样件法简单测量系统-计量型取得一个样件,而且建立其与可追溯到相关标准参考值。假如不能得到这参考值,选择一件落在生产测量范围中间生产件,并将它指定为偏倚分析基准件。在工具室里测量该零件n>10次,并计算这n个读值平均值。将该平均值视为“参考值”。
可能会希望拥有位于期望测量结果下限、中间及上限位置基准样件,假如可做到这么,能够使用线性研究来分析这些数据。
让一个评价者以正常方式测量样件n>10次。
结果分析——图示法
画出这些数据相对于参考值直方图。使用专业知识评审这直方图,从而确定是否存在任何特殊原因或异常点。假如不存在,继续分析。当n<30时,对任何解释或分析时,要能尤其注意。53MSA测量系统分析课件第53页4.2偏倚-独立样件法简单测量系统-计量型结果分析——数值法
1.计算n个读值平均值
2.计算重复性标准差(参见下面量具研究,极差法)
公式中d2*可从附录C查到取,g=1,且m=n。
假如已取得GRR研究(且为有效),重复性标准差计算应该取决于该研究结果。
3.确定偏倚t统计值(t-statistic)
偏倚=观察到平均测量值-参考值
4.假如0落在偏倚值附近1-α自信度界限内,则
偏倚在α水准上是可接收。
公式中,v能够在附录C中查到,能够利用标准t分布表中查到。
假如α自信度水准不是使用预设值0.05(95%自信度),则应该得到用户同意。54MSA测量系统分析课件第54页4.2范例—偏倚-独立样件法简单测量系统-计量型偏倚研究用数据参考值偏倚=6.0015.8-0.225.7-0.335.9-0.145.9-0.156.00.0测66.10.1量76.00.0次86.10.1数96.40.4106.30.3116.00.0126.10.1136.20.2145.6-0.4156.00.055MSA测量系统分析课件第55页4.2范例—偏倚-独立样件法简单测量系统-计量型测量数值图10:偏倚研究——偏倚研究直方图56MSA测量系统分析课件第56页4.2范例—偏倚-独立样件法简单测量系统-计量型,n(m)平均值标准差,σr标准误差平均值,σb测量值156.0067.22514.05813参考值=6.00,α=.05,g=1,
d2*
=3.55统计t值df显著t值(2-有尾数)偏倚偏倚95%自信度区间上限下限测量值.115310.82.206.0067-.1215.1319表3:偏倚研究——偏倚研究分析57MSA测量系统分析课件第57页4.2偏倚-控制图法简单测量系统-计量型假如用一&R图或用&s图来衡量稳定性,其数据也能够用来进行偏倚评价。在偏倚被评价之前,控制图分析应该表明这测量系统处于稳定状态。
1)取得一个样件,而且建立可追溯到一相关标准参考值。假如不能取得参考值,选择一件落在生产测量值范围中间生产零件,将它指定为偏倚分析基准样件。在工具室里测量该零件n>10次,并计算n个读值平均值。使用该平均值作为“参考值”。
结果分析——图示法
2)画出这些数据相对于参考值直方图。对直方图进行评审,以专业知识确定是否存在特殊原因变差或出现异常。假如没有,继续这项分析。58MSA测量系统分析课件第58页4.2偏倚-控制图法简单测量系统-计量型结果分析——数值法
3)从控制图上获取平均值
4)用平均值减去参考值,计算得到偏倚
偏倚=-参考值
5)用极差平均值来计算重复性标准差。
公式中,d2*取决于子组多少(m)和在控制图中子组中数量(g)。(见附录C)
6)确定对偏倚统计t值:
7)若0落在偏倚值附近1-α自信区间内,则偏倚在这α水准上是可接收。
公式中,v可从附录C中查到,能够利用标准t分布表中查到。
所使用α水准取决于敏感度水准,敏感度水准对评价/控制一过程是必要,而且与产品/过程损失函数(敏感度曲线)相关。假如α自信度水准不是使用预设值0.05(95%自信度),则应该得到用户同意。59MSA测量系统分析课件第59页4.2范例—偏倚-控制图法简单测量系统-计量型对一个参考值为6.01零件进行了稳定性研究,全部样本(20个子组)整体平均值为6.021;所以偏倚计算值为0.011。
使用散布图和统计软件,检验员得到了数值分析结果。
因为0落在这偏倚自信度区间内(-0.0299,0.0519),该过程小组能够假设这测量系统偏倚是可接收,即在实际使用中将不会带来额外变差起源。参考值=6.01,α=.05,m
=5,g
=20,
d2*
=2.334,d2=2.326统计t值df显著t值(2-有尾数)偏倚偏倚95%自信度区间上限下限测量值.537172.71.993.011-.0299.0519n平均值,标准差,σr平均值标准误差,σb测量值1006.021.2048.045860MSA测量系统分析课件第60页4.2偏倚简单测量系统-计量型
假如偏倚在统计上不等于0,检验是否存在以下原因:
1)基准件或参考值有误,检验确定标准件程序。
2)仪器磨损。这问题会在稳定性分析中展现出来,提议进行维修或重新整修计划。
3)仪器产生错误尺寸。
4)仪器所测量特征有误。
5)仪器没有经过适当校准。对校准规程进行评审。
6)评价者使用仪器方法不正确。对测量指导书进行评审。
7)仪器纠正指令错误
假如测量系统偏倚不等于零。若有可能,应该采取硬体修正法、软件修正法或同时使用这两种方法来对量具进行重新校准以到达零偏倚。假如偏倚不能调整到零,经过变更程序(如:对每个读值依据偏倚进行修正)还能够继续使用该测量系统。因为存在评价人误差这一高度风险,所以这种方法只能在取得用户同意后方能使用。61MSA测量系统分析课件第61页4.3线性简单测量系统-计量型可使用以下指南进行线性评价:
1.因为存在过程变差,选择g>5个零件,使这测量涵盖这量具整个工作量程.
2.对每个零件进行全尺寸测量,从而确定其参考值,并确定涵盖了这量具工作量程。
3.让经常使用该量具操作者测量每个零件m>10次。
要随机选择零件,从而降低评价人对测量中偏倚“记忆”。
结果分析——图示法
4.计算零件每次测量偏倚,以及每个零件偏倚平均值。
偏倚i,j=Xi,j-(参考值)i
5.在线性图上画出相对于参考值每个偏倚及偏倚平均值。(参见图11)
62MSA测量系统分析课件第62页4.3线性简单测量系统-计量型6.应用以下公式,计算并画出最适合线及该线自信度区间。
对最适合线,用公式:式中
xi=参考值,,=偏倚平均值
以及
对于一个已知xO,α自信度区间为:
63MSA测量系统分析课件第63页4.3线性简单测量系统-计量型7.画出“偏倚=0”线,并对图进行评审,以观察是否存在特殊原因,以及线性是否可接收。(见图11)
假如“偏倚=0”整个直线都位于自信度区间以内,则称该测量系统线性是可接收。
结果分析——数值法
假如图示法分析表示该测量系统线性是可接收,则以下假设应该为真:
Ho:a=0,斜率=0
假如下式成立,则不能被否定
假如以上假设为真,则测量系统对全部参考值含有相同偏倚。这个偏倚必须为0,该线性才可被接收。
Ho:b=0,中心(偏倚)=0
假如下式成立,则不能被否定:64MSA测量系统分析课件第64页4.3范例--线性简单测量系统-计量型
某工厂检验员对某过程引进了一套新测量系统。作为PPAP41一部分,需要对测量系统线性进行评价。依据已文件化过程变差描述,在测量系统全部工作量程范围内选取了五个零件。经过对每个零件进行全尺寸检验从而确定它们参考值,然后由主要操作者对每个零件测量12次。在分析中,这些零件是随机抽取。65MSA测量系统分析课件第65页4.3范例--线性简单测量系统-计量型零件参考值123452.004.006.008.0010.0012.705.105.807.609.1022.503.905.707.709.3032.404.205.907.809.5042.505.005.907.709.30测52.703.806.007.809.40量62.303.906.107.809.50次72.503.906.007.809.50数82.503.906.107.709.5092.403.906.407.809.60102.404.006.307.509.20112.604.106.007.609.30122.403.806.107.709.40表5:线性研究数据66MSA测量系统分析课件第66页4.3范例--线性简单测量系统-计量型12345零件参考值2.004.006.008.0010.0010.71.1-0.2-0.4-0.920.5-0.1-0.3-0.3-0.730.40.2-0.1-0.2-0.540.51-0.1-0.3-0.750.7-0.20.0-0.2-0.6偏60.3-0.10.1-0.2-0.5倚70.5-0.10.0-0.2-0.580.5-0.10.1-0.3-0.590.4-0.10.4-0.2-0.4100.40.00.3-0.5-0.8110.60.10.0-0.4-0.7120.4-0.20.1-0.3-0.6偏倚平均值0.4916670.1250.025-0.29167-0.61667表6:线性研究——中途结果67MSA测量系统分析课件第67页4.3范例--线性简单测量系统-计量型线性范例Y=0.736667–0.131667xR-Sq=71.4%68MSA测量系统分析课件第68页4.4重复性和再现性简单测量系统-计量型确定重复性和再现性指南
能够使用不一样方法进行计量型量具研究。本节将详细讨论三种可接收方法。它们是:
.极差法(Rangemethod)
.均值——极差法(AverageandRangemethod)
.方差分析法(ANOVAmethod)
除极差法之外,其它方法所用研究数据设计都很相同。如所展现,全部方法在它们分析时均忽略了零件内部变差(如:在第四章,第A节所讨论圆度、锥度直径、平面度等。)69MSA测量系统分析课件第69页4.4.1极差法简单测量系统-计量型极差法是一个经修正计量型量具研究方法,它能对测量变差提供一个快速地近似值。这方法只能对测量系统提供变差整体情况,不能将变差分解成重复性和再现性。它通惯用来快速地检验以验证GRR是否有改变。
使用这方法能够潜在检测出测量系统为不可接收概率是:对于抽样次数是5情况下,机率为80%;对于抽样次数为10情况下,机率为90%。
用极差法进行研究时通常选取两个评价人与五个零件。在这种研究中,两个评价人测量每个零件一次。由评价人A测量每个零件极差与由评价人B测量每个零件极差是决然不一样。计算极差之和以及极差平均值();总测量变差即为极差平均值乘以可在附录C中查到,取m=2,且g=零件数量。70MSA测量系统分析课件第70页4.4.1极差法简单测量系统-计量型(过程标准差=0.0777从之前研究中取得)零件评价人A评价人B极差(A,B)10.850.800.0520.750.700.0531.000.950.0540.450.550.1050.500.600.1071MSA测量系统分析课件第71页4.4.2平均值和极差法简单测量系统-计量型平均值和极差法(&R)是一个可同时对测量系统提供重复性和再现性预计值研究方法。与极差法不一样,这方法允许将测量系统变差分解成两个独立部分:重复性和再现性,但不能确定它们二者相互作用。
进行研究
尽管评价人人数、测量次数及零件数量均可会不一样,但下面讨论展现进行研究最正确情况。参见图12中GRR数据表,详细程序以下:
1)取得一个能代表过程变差实际或预期范围样本,为n>5个零件样本。
2)给评价人编号为A、B、C等,并将零件从1到n进行编号,但零件编号不要让评价人看到。72MSA测量系统分析课件第72页4.4.2平均值和极差法简单测量系统-计量型3)对量具进行校准,假如这是正常测量系统程序中一部分话。让评价人A以随机次序测量n个零件,并将结果统计在第1行。
4)让评价人B和C依次测量这些一样n个零件,不要让他们知道他人读值:然后将结果分别统计在第6行和第11行。
5)用不一样随机测量次序重复以上循环,并将数据统计在第2、7和12行;注意将数据统计在适当栏位中,比如:假如首先被测量是零件7,然后将数据统计在标有零件7栏位中。假如需要进行三次测量,则重复以上循环,并将数据统计在第3、8和13行中。
6)当测量大型零件或不可能同时取得数个零件时,第3步到第5步将变更成以下次序:
让评价人A测量第一个零件并将读值统计在第1行:让评价人B测量第一个零件并将读值统计在第6行;让评价人C测量第一个零件并将读值统计在第11行。73MSA测量系统分析课件第73页4.4.2平均值和极差法简单测量系统-计量型
让评价人A重新测量第一个零件并将读值统计在第2行:评价人B重新测量第一个零件并将读值统计在第7行;评价人C重复测量第一个零件并将读值统计住第12行。假如需要进行三次测量,则重复以上循环,并将数值统计在第3、8和13行中。
7)假如评价人处于不一样班次,能够使用一个替换方法。让评价人A测量全部10个零件,并将读值统计在第1行;然后让评价人A按照不一样次序重新测量,并把读值统计在第2行和第3行。评价人B和评价人C也一样做。74MSA测量系统分析课件第74页4.4.2平均值和极差法简单测量系统-计量型结果分析——图示法
平均值图(AverageChart)
用来确认评价人之间一致性75MSA测量系统分析课件第75页4.4.2平均值和极差法简单测量系统-计量型结果分析——图示法
极差图(RangeChart)
评审以上图表显示评价人变差之间存在差异。76MSA测量系统分析课件第76页4.4.2平均值和极差法简单测量系统-计量型结果分析——图示法
链图(RunChart):
1)个别零件在变差一致性上影响
2)奇异读值展现(即不正常读值)77MSA测量系统分析课件第77页4.4.2平均值和极差法简单测量系统-计量型结果分析——图示法
振荡图(WhiskersChart):
1)评价人之间一致性
2)分离展现
3)零件——评价人之间相互作用78MSA测量系统分析课件第78页4.4.2平均值和极差法简单测量系统-计量型结果分析——图示法
振荡图(WhiskersChart):
1)评价人之间一致性
2)分离展现
3)零件——评价人之间相互作用79MSA测量系统分析课件第79页4.4.2平均值和极差法简单测量系统-计量型结果分析——数值计算
1)用1、2、3行中最大值减去它们中最小值,把结果记入第5行。在第6、7、8行和第11、12、13行重复以上步骤,并将结果分别统计在第10行和第15行。
2)填入第5、10及15行数据是极差,所以它们都总是正值。
3)将第5行数据相加,然后除以零件抽样数量即得到了第一个评价人测量极差平均值;对第10行和第15行进行一样计算以得到和。
4)将第5、10和第15行平均值(,和)转到第17行。用它们和除以评价人数,结果记入栏(全部极差平均值)。
80MSA测量系统分析课件第80页4.4.2平均值和极差法简单测量系统-计量型结果分析——数值计算
5)将输入第19和20行,并乘以D4以得到控制限上限和下限。注意假如进行两次测量,则D4为3.27。将该单独极差上控制限(UCLR)填入19行,对于测量次数少于7次情况下,极差下控制限(LCLR)为零。
6)对于极差结果大于UCLR计算结果任何读值,让原来计价人对原来零件进行重新测量,或剔除那些读值,然后依据修改后抽样数量重新平均并计算极差平均值和控制限UCLR。假如已使用了前面所讨论控制图来绘制并分析数据,这种情况将已经得到了纠正,所以不会在这发生。81MSA测量系统分析课件第81页4.4.2平均值和极差法简单测量系统-计量型结果分析——数值计算
7)加总第1、2、3、6、7、8、11、12和13行读值,然后将每行总和除以抽样数量,并将结果埴入该行最右边标有“平均值”栏位中。
8)将1、2、3行平均值相加,用该总和除以测量次数,将所得结果填入第4行中栏为中。对第6、7、8行和第11、12、13行重复以上步骤,并将结果分别统计在第9行和第14行中和栏位中。
9)找出第4、9及14行平均值(、和)中最大值和最小值,并将它们填入第18行适当位置并求出它们差;将这差值填入第18行中标示空白处。
82MSA测量系统分析课件第82页4.4.2平均值和极差法简单测量系统-计量型结果分析——数值计算
10)计算每次测量每个零件读值之和,然后除以总测量次数(测量次数乘以评价人人数);将结果填在第16行为每个零件平均值提供空白处。
11)用零件平均值最大值减去零件平均值最小值,并将结果填入第16行中标示RP栏位。RP是零件平均值极差。
12)将计算所得、、RP填入汇报表格所提供空白处。
13)进行汇报表格左侧标题为“测量单元分析”栏之下计算。
14)进行汇报表格右侧标题为“总变差%”栏之下计算。
15)检验计算结果以确定没有错误。83MSA测量系统分析课件第83页4.4.2平均值和极差法简单测量系统-计量型结果分析——数值计算
1)重复性或设备变差(EV或σE)是由极差平均值()乘以一个常数(K1)来决定。K1取决于量具研究中测量次数,其值为从附录C查到d2*倒数。d2*取决于测量次数(m)和零件数量乘以评价人人数(g)。
2)再现性或评价人变差(AV或σA)是由评价人平均值最大差值()乘以一个常数(K2)来决定。K2取决于量具研究中评价人人数,其值为从附录C查到d2*倒数。d2*取决于评价人人数(m),且g=1,因为只有一个极差计算。因为评价人变差被包含在设备变差中,所以必须经过减去设备变差一个分数来对其进行调整。所以,评价人变差(AV)可由下式计算得到:84MSA测量系统分析课件第84页4.4.2平均值和极差法简单测量系统-计量型结果分析——数值计算
式中:n=零件数量,以及r=测量次数
假如根号下所得数值为负数,则评价人变差(AV)为零。
3)测量系统变差重复性和再现性(GRR或σM)计算为设备变差平方加上评价人变差平方,然后再开根号,以下式:
85MSA测量系统分析课件第85页4.4.2平均值和极差法简单测量系统-计量型结果分析——数值计算
4)
零件与零件之间变差(PV或σp)是由零件平均值极差(Rp)乘以一个常数(K3)所决定。K3取决于量具研究中零件数量,其值为从附录C查到d2*倒数。d2*取决于零件数量(m)与(g),在这情况g=1,因为只有一个极差计算。
5)这研究总变差(TV或σT)是加总了重复性和再现性变差平方与零件之间变差(PV)平方,再开根号计算而得。即:86MSA测量系统分析课件第86页4.4.2平均值和极差法简单测量系统-计量型结果分析——数值计算
6)
设备变差(%EV)占总变差(TV)百分比,被计算为100[EV/TV],其它原因占总变差百分比计算方法相同,以下式;
%AV=100[AV/TV]
%GRR=100[GRR/TV]
%PV=100[PV/TV]
每个原因所占百分比之和将不等于100%。87MSA测量系统分析课件第87页4.4.2平均值和极差法简单测量系统-计量型结果分析——数值计算
7)在这数值分析最终一步是确定区分分类数(thenumberofdistinctcategories),这能由该测量系统可靠地分辨,这是能够覆盖预期产品变差非重迭97%自信度区间。
另外,ndc应该四舍五入到整数,且要能大于或等于5。88MSA测量系统分析课件第88页4.4.3方差分析法(ANOVA)简单测量系统-计量型方差分析法(anlysisofvariance,ANOVA)是一个标准统计技术,可用它来分析测量误差和一测量系统研究中其它变差起源。在变差分析中,变差可分解成四类:
零件、评价人、零件与评价人之间相互作用,以及因为量具造成重复误差。
与平均值和极差法相比,ANOVA方法有以下优点:
1)有能力处理任何试验作业准备;
2)能更准确地预计变差;
3)可从试验数据中得到更多信息(如:零件与评价人之间相互作用影响)。
其缺点是:其数值计算愈加复杂,而且要求一定程度统计学知识以解释它结果。以下章节所介绍ANOVA方法是一提议方法,尤其是能够使用电脑时。89MSA测量系统分析课件第89页简单测量系统-计数型计数型测量系统是一个测量数值为一有限分类数量测量系统。它与能取得一连串数值结果计量型测量系统截然不一样。通/止规(go/nogogage)是最惯用量具,它只有两种可能结果;其它计数型测量系统,比如目视标准,可能产生五到七个分类,如非常好、好、普通、差、非常差。在前面章节中所介绍分析方法不能被用来评价这么系统。
风险分析方法
1)假设性试验分析
2)信号探测理论5.1风险分析方法
90MSA测量系统分析课件第90页简单测量系统-计数型假设性试验分析——交叉表法
从过程中随机选取50个零件,以取得涵盖了整个过程范围零件。
使用3名评价人,每位评价人对每个零件测量3次。
设定用1表示可接收决定,0为不可接收决定。表中所表示参考决定和计量参考值在一开始还没有被确定。表还显示了“代码”列,分别用“-”、“x”、“+”代表零件是否位于Ⅰ区,Ⅱ区及Ⅲ区。5.1风险分析方法
91MSA测量系统分析课件第91页零件A-1A-2A-3B-1B-2B-3C-1C-2C-3参考参考值代码111111111110.476901+211111111110.509015+300000000000.576459-400000000000.566152-500000000000.570360-611011010010.544951x711111110110.465454x811111111110.502295+900000000000.437817-1011111111110.515573+1111111111110.488905+1200000001000.559918x1311111111110.542704+1411011110010.454518x1511111111110.517377+1611111111110.531939+1711111111110.519694+1811111111110.484167+1911111111110.520496+2011111111110.477236+2111010101010.452310x2200101011000.545604x2311111111110.529065+2411111111110.514192+2500000000000.599581-92MSA测量系统分析课件第92页2601000000100.547204x2711111111110.502436+2811111111110.521642+2911111111110.523754+3000000100000.561457x3111111111110.503091+3211111111110.505850+3311111111110.487613+3400100101100.449696x3511111111110.498698+3611011110110.543077x3700000000000.409238-3811111111110.488184+3900000000000.427687-4011111111110.501132+4111111111110.513779+4200000000000.566575-4310111111010.462410x4411111111110.470832+4500000000000.412453-4611111111110.493441+4711111111110.486379+4800000000000.587893-4911111111110.483803+5000000000000.446697-93MSA测量系统分析课件第93页A*B参考交叉表B总计.001.00A.00数量期望数量4415.7634.35050.01.00数量期望数量331.39768.7100100.0总计数量期望数量4747.0103103.0150150.0B*C参考交叉表C总计.001.00B.00数量期望数量4216.0531.04747.01.00数量期望数量935.09468.0103103.0总计数量期望数量5151.09999.0150150.0A*C参考交叉表C总计.001.00A.00数量期望数量4317.0733.05050.01.00数量期望数量834.09266.0100100.0总计数量期望数量5151.09999.0150150.094MSA测量系统分析课件第94页简单测量系统-计数型假设性试验分析——交叉表法
表格目标在于确定评价人之间一致性程度。为确定这一致性程度,小组使用了(cohen)Kappa,这是用来衡量两个评价人对同一物体进行评价时,其评定结论一致性。Kappa为1时,表示有完全一致性,为0时,表示一致性不比可能性来得好。
Kappa一个对评价人内部一致性衡量,它测试在诊疗区(取得相同评定零件)中数量与那些基于可能性期望数量是否有差异。
让 Po=在诊疗区中观察部分总和
Pe=在诊疗区中期望部分总和5.1风险分析方法
95MSA测量系统分析课件第95页简单测量系统-计数型假设性试验分析——交叉表法
Kappa是一个程度而不是一个试验。通用百分比法则是kappa值大于0.75则表示有很好一致性(最大kappa=1);kappa值小于0.40则表示一致性不好。
Kappa不考虑评价人之间不一致量有多大,只考虑他们之间是不是一致。
全部评价人与其它评价人之间有良好一致性
5.1风险分析方法
kappaABCA-.86.78B.86-.79C.78.79-96MSA测量系统分析课件第96页A*参考交叉表参考总计.001.00A.00数量期望数量4516.0534.05050.01.00数量期望数量332.09768.0100100.0总计数量期望数量4848.0102102.0150150.0B*参考交叉表参考总计.001.00B.00数量期望数量4515.0232.04747.01.00数量期望数量333.010070.0103103.0总计数量期望数量4848.0102101.0150150.0C*参考交叉表参考总计.001.00C.00数量期望数量4216.3934.75151.01.00数量期望数量631.79367.39999.0总计数量期望数量4848.0102102.0150150.097MSA测量系统分析课件第97页简单测量系统-计数型假设性试验分析——交叉表法
小组也计算出了kappa值以确定每个评价人与参考决定之间一致性。
以上数据可被解释为每个评价人与标准之间有很好一致性。5.1风险分析方法
ABCkappa
.88.92.7798MSA测量系统分析课件第98页简单测量系统-计数型假设性试验分析——交叉表法
然后这过程小组计算这测量系统有效性。5.1风险分析方法
99MSA测量系统分析课件第99页变差起源计价人%1计价人A评价人B评价人C结果%与归因比较2计价人A评价人B评价人C总检验数505050505050相配数424540424540错误拒收(因为评价人偏倚造成拒收)000错误接收(因为评价人偏倚造成接收)000不相配851095%UCI93%97%90%93%97%90%计算所得结果84%90%80%84%90%80%95%LCI71%78%66%71%78%66%系统有效结果%3系统有效结果%与参考比较4检验总数5050一致数量393995%UCI89%89%计算所得结果78%78%95%LCl64%64%注(1)在全部测量中,评价人本身是一致。(2)评价人对全部测量与已知标准一致。(3)全部评价人本身与其它人之间是一致。(4)全部评价人本身与其它人之间一致,并与参考值一致。(5)UCI和LCI分别为自信区间边界上限和下限。100MSA测量系统分析课件第100页简单测量系统-计数型假设性试验分析——交叉表法
小组也计算出了kappa值以确定每个评价人与参考决定之间一致性。
以上数据可被解释为每个评价人与标准之间有很好一致性。5.1风险分析方法
ABCkappa
.88.92.77101MSA测量系统分析课件第101页简单测量系统-计数型假设性试验分析——交叉表法
然后这过程小组计算这测量系统有效性
5.1风险分析方法
决定测量系统有效性错误率错误警报率评价人可接收条件>90%<2%<5%评价人可接收条件-可能需要改进>80%<5%<10%评价人不可接收条件-需要改进<80%>5%>10%对他们所已经得到全部信息进行汇总,小组得到以下结论:有效性错误率错误警报率A84%6.3%4.9%B90%6.3%2.0%C80%12.5%8.8%102MSA测量系统分析课件第102页简单测量系统-计数型假设性试验分析——信号检验方法
另一个替换方法—信号检验理论来确定区域Ⅱ近似宽度,从而确定测量系统GRR。
让=被全部评价人接收最终一个零件与被全部评价人拒收第一个零件之间距离(对于每个规范)。
然后,
d=平均值
这是区域Ⅱ预计值,且GRR预计值为
在本例中:
=0.470832-0.446697=0.024135
=0.566152-0.542104=0.023448
d=0.0237915
或者,%GRR预计值为:
%GRR=29%
实际%GRR=25%,所以这预计值将导引至测量系统相同评价。
5.1风险分析方法
103MSA测量系统分析课件第103页参考值代码参考值代码0.599581-0.503091+0.587893-0.502436+0.76459-0.502295+0.570360-0.501132+0.566575-0.498698+0.566152-0.493441+0.561457x0.488905+0.559918x0.488184+0.547204x0.487613+0.545604x0.486379+0.544951x0.484167+0.543077x0.483803+0.542704+0.477236+0.531939+0.476901+0.529065+0.470832+0.523754+0.465454x0.521642+0.462410x0.520496+0.454518x0.519694+0.452310x0.517377+0.449696x0.515573+0.446697-0.514192+0.437817-0.513779+0.427686-0.509015+0.412453-0.505850+0.409238-104MSA测量系统分析课件第104页实施复杂或不可重复测量系统不可重复测量系统情景——非破坏性测量系统范例在测量过程中零件不会被改变:即测量系统是非破坏性,并可使用含有以下属性零件(样本)静态属性,或已经稳定动态(改变)属性用于不是新车辆/动力系统进行测功试验有计量型数据泄漏试验己知特征(属性)定性期限,并能延续至超出期望研究期间——即经过一段预期使用后,被测特征不会改变。从单一材料批次中
温馨提示
- 1. 本站所有资源如无特殊说明,都需要本地电脑安装OFFICE2007和PDF阅读器。图纸软件为CAD,CAXA,PROE,UG,SolidWorks等.压缩文件请下载最新的WinRAR软件解压。
- 2. 本站的文档不包含任何第三方提供的附件图纸等,如果需要附件,请联系上传者。文件的所有权益归上传用户所有。
- 3. 本站RAR压缩包中若带图纸,网页内容里面会有图纸预览,若没有图纸预览就没有图纸。
- 4. 未经权益所有人同意不得将文件中的内容挪作商业或盈利用途。
- 5. 人人文库网仅提供信息存储空间,仅对用户上传内容的表现方式做保护处理,对用户上传分享的文档内容本身不做任何修改或编辑,并不能对任何下载内容负责。
- 6. 下载文件中如有侵权或不适当内容,请与我们联系,我们立即纠正。
- 7. 本站不保证下载资源的准确性、安全性和完整性, 同时也不承担用户因使用这些下载资源对自己和他人造成任何形式的伤害或损失。
最新文档
- 行政管理学中的代表性人物考查试题及答案
- 了解专家建议2025年建筑试题及答案
- 2025农产品供货合同农产品供货合同协议
- 2025赠与车辆买卖合同模板
- 重要概念市政学试题及答案
- 2025超市货架租赁合同
- 公文写作的实际应用场景分析试题及答案
- 管理心理学与创造性思维发展的考察试题及答案
- 现代管理思维培养试题及答案
- 行政管理学核心理念试题及答案
- 政协专项调研方案
- 编制气候可行性论证报告
- 年产500吨IMD高端环保油墨研发生产项目环境信息公示
- 地下水监测系统方案
- 为什么你的学生不思考
- 全喉切除护理查房
- 美国次贷危机对中国经济的影响
- 养老院项目组织结构方案
- 基于单片机的光照度自动调节系统设计
- 电烤箱温度控制系统设计
- 2021年数学中考复习课件第四章三角形微专题 五大常考相似模型
评论
0/150
提交评论