摘 要
模具设计是工业生产中的重要工艺,是我国经济发展体系里的重要因素,好的模具能节省材料节省人力,节省时间,因此受到广泛的关注。注塑模是模具设计里的一种重要成型工艺,它主要用于热变形塑料的成形,也可以成形热固性塑料。它的生产效率极高,并且非常容易实现自动化,最重要的是生产出来的塑件质量都很好。注塑模形式多样,内容多样,结构复杂,对于它的发展也不会就此止步。
本次毕业设计的主要任务是对外螺纹液压管接头四通管模具的设计,也就是设计一副注塑模具来生产外螺纹液压管接头四通管的塑件产品,以实现自动化提高产量。主要内容包括绪论、塑件的结构及成型工艺分析、材料的选择及成型工艺、注射机的选择及校核、模具的工作及结构原理、浇注系统的设计、成型零部件的设计、侧向分型机构的设计、合模导向机构的设计、温度调节系统的设计、排气系统的设计、顶出机构的设计、支撑零部件的设计等。在设计过程种运用到了Proe3.0软件对塑件进行三维造型,通过使用AutoCAD来设计整套模具,并运用CAXA/CAD对其装配图与零件图等进行表述,设计过程中也借鉴到很多学者的著作,设计相对充实。
本文是探究四通管的注塑模具设计,详细描述了整套模具的设计过程。通过对整个模具设计的过程,进一步加深对注塑成型工艺的了解,同时也巩固了对成型工艺的类型、结构、工作原理等的理论知识,以及在实践中总结并掌握模具设计的关键要点和设计方法。
关键词: 外螺纹四通管;注塑模具;注射机;侧型芯滑块;
Abstract
This graduation design is the main task of the inclined tee mould design, namely a pair of injection mold is designed to produce the plastic parts of inclined tee products, in order to realize the automation to increase production. The main contents include design options and checking , mold and structural work principle , the introduction of gating system , structure and plastic parts molding process analysis , choice of materials and molding process , injection machine , designed molded parts , lateral sub- design mechanism design guide clamping mechanism , temperature control system design, the design of the exhaust system , the ejection mechanism designed to support the design of parts .
This article is to explore the plastic injection mold design four line , a detailed description of the entire mold design process.Through the entire mold design process , and further deepen their understanding of the injection molding process , but also to consolidate the process of forming the type, structure and operating principles of the theory of knowledge, as well as summary and master mold design practice and design a key point methods.
Key words: oblique tee; Injection mould; Injection machine; Core side slide block;
目 录
引言 1
2 塑件成型工艺的可行性分析 3
2.1 塑件分析 3
2.2 塑件的原材料分析 3
2.2.1主要技术指标 4
2.2.2 ABS的注射工艺参数 4
2.3 塑件的成型工艺分析 4
2.3.1精度等级 4
2.3.2脱模斜度 5
2.3.3塑件壁厚 5
3 注射成型机的选择与成型腔数的确定 5
3.1 注射成型机的选择 5
3.1.1估算零件体积和投影面积 5
3.1.2注射量的计算 6
3.1.3锁模力 6
3.1.4选择注射机及注射机的主要参数 6
3.2 注塑机的校核 6
3.2.1最大注塑量校核 6
3.2.2注射压力的校核 7
3.2.3锁模力校核 7
3.3 成型腔数的确定 7
4 浇注系统的设计 8
4.1 浇注系统的作用 8
4.2 浇注系统的组成 8
4.3 主流道设计 8
4.3.1 主流道设计要点 8
4.3.2浇口套的尺寸设计要求 9
4.4 浇口设计 10
4.6 主流道剪切速率校核 11
4.6.1估算主流道凝料体积 11
4.6.2主流道剪切速率校核 11
5 成型零件结构设计 12
5.1 分型面的设计 12
5.1.1分型面的分类 12
5.1.2分型面的选择原则 12
5.1.3分型面的确定 12
5.2 型腔的分布 13
5.3 凹模的结构设计 13
5.4 模具型零成件的工作尺寸计算 14
5.4.1塑件的收缩率波动误差s 14
5.4.3模具成型零件的磨损c 15
5.4.4模具安装配合误差j 15
5.5 型腔和型芯径向尺寸的计算 16
5.5.1型腔径向尺寸的计算 16
5.5.2型芯径向尺寸的计算 16
5.5.3型腔深度和型芯高度尺寸的计算 16
6 排气系统的设计 17
6.1 排气不良的危害 17
6.2排气系统的设计方法 17
7 导向与脱模机构的设计 18
7.1导向机构的作用和设计原则 18
7.1.1导向机构的作用 18
7.1.2导向机构的设计原则 18
7.2导柱、导套的设计 18
7.2.1导柱的设计 18
7.2.2导套的设计 19
7.2.3导向孔的总体布局 19
7.3 推出机构设计 19
7.4 脱模力的计算 20
7.5 推杆的设计 21
7.5.1推杆长度及强度计算 21
7.5.2推杆的形状及固定形式 22
7.2.3推杆位置的选择 23
8侧向分型与抽芯机构的设计 24
8.1 抽芯机构设计原则 24
8.2 抽芯机构的确定 24
8.3 抽芯距S 24
8.4 滑块的设计 24
8.5 导滑槽的设计 25
8.6 锁紧块 25
8.7 锁紧块的结构形式 26
9冷却系统设计 26
9.1 冷却系统的设计原则 26
9.2 温度调节对塑件质量的影响 27
9.3 对温度调节系统的要求 27
9.4 冷却装置的设计要点 27
9.5 冷却系统设计计算 27
9.5.1冷却水的体积流量 27
9.5.2冷却水管直径 28
9.5.3冷却水道的结构 28
10 其它结构零部件的设计 29
10.1 模具安装尺寸校核 29
10.2 开模行程的效核 29
11小结 30
参考文献 31
致 谢 32
引言
注塑成型是一项越来越成熟的加工技术,它目前是在塑性成型的各个领域加工中最常见也最常用的加工方法,其中注塑模具已经被广泛的采用,在很多方面的应用都得到相当高的重视[12]。我国模具研究单位因此也投入了很大的科研精力,目的在于使注塑模具的发展得到最大的提高。它的生产零件的质量、模具的结构、温度调控系统、制造精度、生产周期以及生产效率的高低,直接影响到产品的质量、产量和成本。当今社会,我们追求的正是质量与成本,统称为性价比,模具的应用正是性价比的最高体现,有的时候我们用一个模具可以同时制造出很多个质量精良,结构复杂的高精度塑件,这在以前来说几乎是不可能实现的[2]。注塑成型现已被广泛的应用于机械、计算机、高科技材料、电子、航空、航天、军工、学习用品、交通、汽车、建材、医疗器械、生物、能源和日用品等领域[1]。虽然在很多人看来一个小小的模具制造工艺能有多大的影响对于一个国家的发展,我觉得这种想法是错误的,因为从小方面来说这一门技术的成熟意味着对塑件成型的深入研究取得了长足进步,也就是说我们生产塑件就会更加便捷也会更加快速,这对于塑料工业来说是一个很大的贡献,因此不容小视;大方面来说正是这种对于先进技术的渴望推动我们整个民族在进步,我们知道我们在清政府以后闭关锁国导致在科技方面落后西方一大截,但我们中华民族从来没有服输过,一直都是在迎头赶上,只为了争这一口气,而注塑模的研究进步正是对我们的一种肯定,因此我们应当不遗余力的继续在这条路上走下去。我国近年来一直致力于模具的研究,现在也已经逐步跟上了欧美先进的步伐。在一些发达国家,模具产业早已形成产业链,成为这些国家的基础经济工业之一。很多国家在发展高科技产业的同时也兼顾发展轻工业,在美国,模具工业被成为“美国工业的基石”,在日本被称为“促进社会富裕的动力、源泉”[3]。因此在轻工业行业有这么一句话:工业要发展,模具要先行。没有高水平的模具制造工艺就没有质量非常优良的科技产品。现在,模具工业水平是衡量一个国家制造工业制造水平高低的重要标志。可以这么大胆的预测,模具工业在国民经济中的地位将与日俱增,并且扮演越来越重要的角色。因此我们必须毫无疑虑的发展模具工业,对于我们国家的生产力的进步有很大的推动作用。




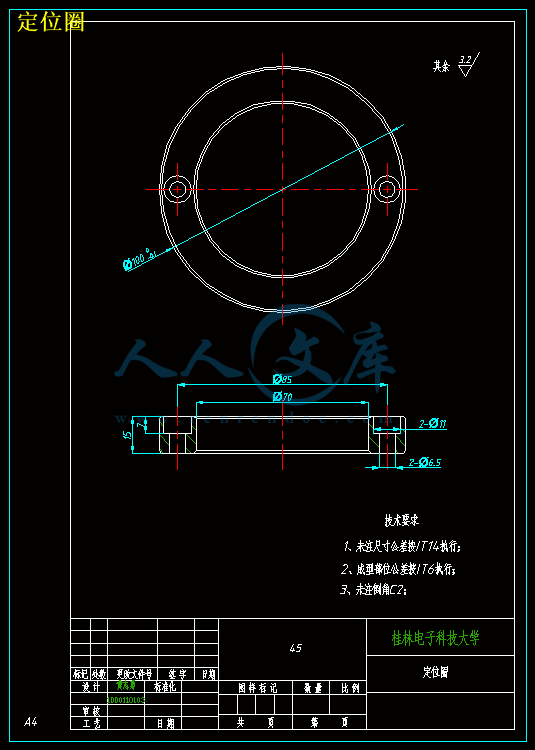



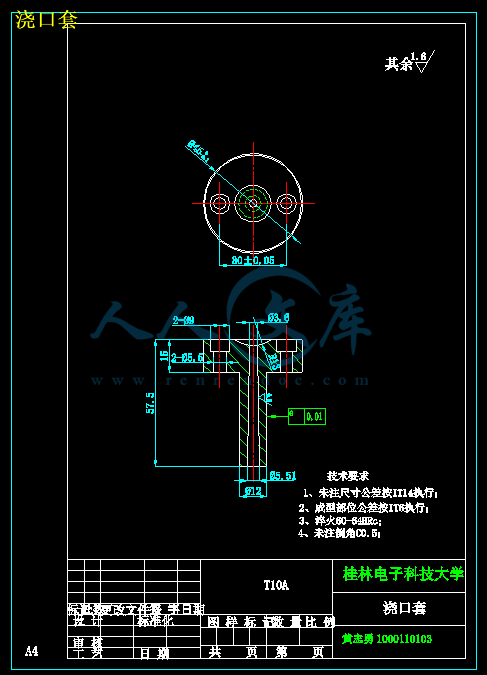

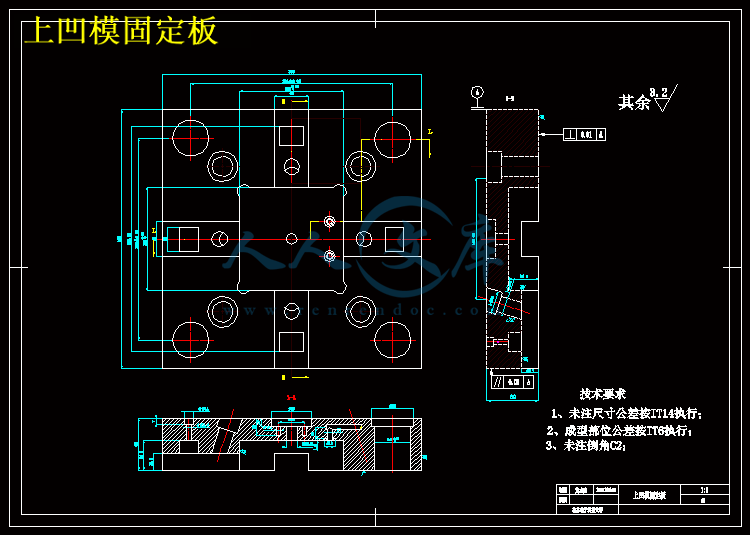
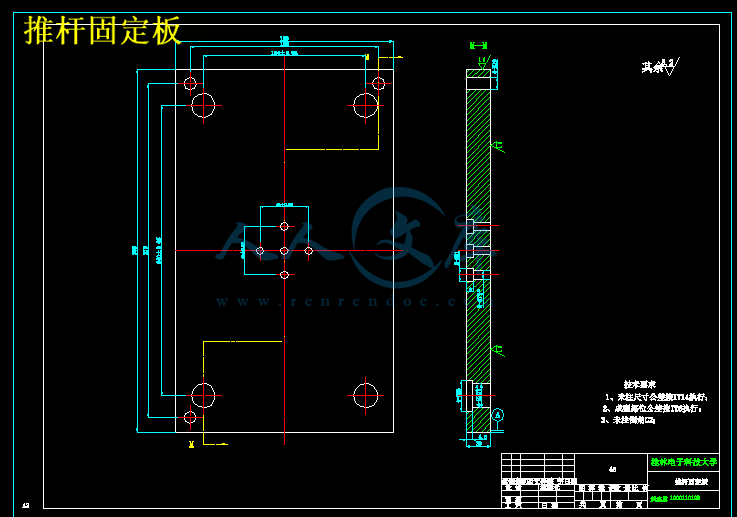

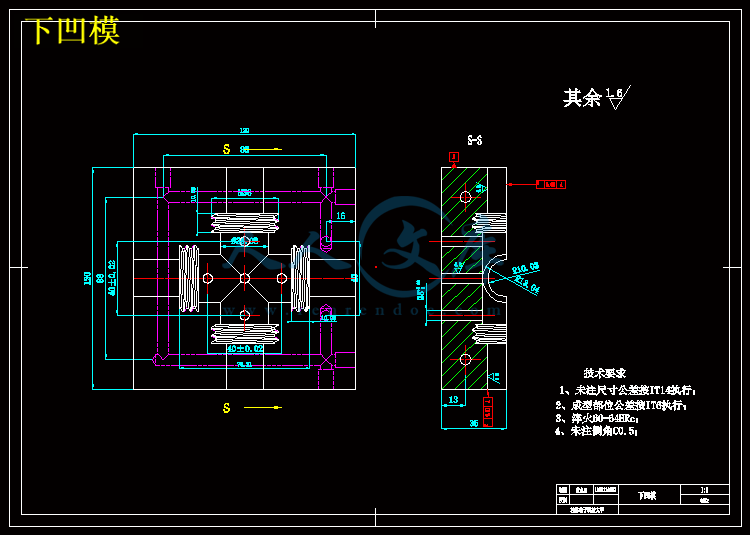
