变压器油枕前盖冲压成形级进模设计【5张图纸】【优秀】
收藏
资源目录
压缩包内文档预览:
编号:271424
类型:共享资源
大小:1.07MB
格式:RAR
上传时间:2014-04-05
上传人:上***
认证信息
个人认证
高**(实名认证)
江苏
IP属地:江苏
50
积分
- 关 键 词:
-
变压器
油枕前盖
冲压
成形
级进模
设计
图纸
优秀
优良
- 资源描述:
-
变压器油枕前盖冲压成形级进模设计
说明书 48页20000字数+开题报告+任务书+5张CAD图纸+5张CAXA图纸
凸凹模.dwg
凸凹模.exb
凹模.dwg
凹模.exb
前盖产品图.dwg
前盖产品图.exb
压力机.dwg
压力机.exb
变压器油枕前盖冲压成形级进模设计说明书.doc
封皮.doc
开题报告.doc
摘要.doc
模具装配图.dwg
模具装配图.exb
目录.doc
目录
前言1
1 设计初始资料3
2 分析冲压工件的工艺性4
2.1 冲压件的工艺性分析4
2.2 冲压件的尺寸精度及标注4
2.3 工艺方案的确定及模具形式4
3 拟定冲压件工艺方案5
3.1 排样5
3.2 工序的确定5
3.3 搭边类型的确定5
3.4 卸料板的选择6
4 工艺计算7
4.1 毛坯料尺寸计算7
4.1.1 确定是否加修边余量7
4.1.2 毛坯直径7
4.1.3 确定是否需要压边圈8
4.1.4 确定拉伸次数8
4.2 搭边8
4.2.1 搭边的作用8
4.2.2 搭边的数值9
4.3 送料步距10
4.4 条料宽度10
4.5 材料利用率11
4.6 计算冲压力12
4.6.1 对毛坯冲孔、落料的冲裁力计算12
4.6.2 对于毛坯用压边圈拉深的计算13
4.6.3 辅助工艺力计算14
4.7 压力中心的确定16
4.7.1 压力中心16
4.7.2 压力中心的计算16
5 凸、凹模刃口尺寸计算18
5.1 刃口尺寸确定的原则18
5.2 冲裁间隙的选择18
5.3 尺寸计算19
5.3.1 对于φ286毛坯进行落料时的刃口尺寸计算19
5.3.2 对于φ11㎜和φ4㎜ 孔冲裁时的尺寸计算20
5.3.3 对拉深模的尺寸计算20
6 模具强度的校核22
6.1 模具失效形式22
6.2 对冲裁部分的模具零件进行校核计算22
6.2.1 压应力校核22
6.2.2 弯曲应力的校核23
7 模具主要零部件设计24
7.1 模架的选用24
7.2 导向装置的确定24
7.3 模柄的选择24
7.4 定位装置的设计24
7.5 卸料形式的确定25
7.6 导料装置的确定25
8 模具材料的选用26
8.1 选择材料的原则26
8.2 工作零件材料的选择方法及步骤26
9 压力机的选用28
10 模具工作过程29
11 经济性分析30
12 总结32
致谢33
参考文献34
附录A35
附录B39
摘要
一副级进模内可以包含冲裁,弯曲,成型,拉深等多道工序,一台冲床可完成从板料到成品的各种冲压过程。它免去了用单工序模的周转和每次冲压的定位过程,提高了劳动生产率和设备利用率。
本文进行了变压器油枕前盖冲压成形级进模的设计,通过对待冲压成形的工件——变压器油枕前盖的分析,确立了冲压的工艺过程以及冲压级进模的结构。而后对级进模的各个主要零部件进行了尺寸的计算和强度校核,通过压力机的确定,设计出了整个冲压级进模。所设计的级进模,使目前生产变压器油枕前盖的效率大大提高,并且有效降低了生产成本,获得收益的增加。
关键词:级进模;变压器油枕前盖;模具设计
变压器是一种把电压和电流转变成另一种(或几种)同频率的不同电压电流的电气设备。发电机发出的电功率,需要升高电压才能送至远方用户,而用户则需把电压再降成低压才能使用,这个任务是变压器才能完成的。因此变压器是电力工业中非常重要的组成部分,在发电、输电、配电、电能转换和电能消耗等各个环节都起着至关重要的作用,也是电工行业的主要组成部分之一,在国民经济中占有非常重要的地位[1]。 作为电力工业的重要的装备行业之一,变压器制造业其发展受电力工业的影响非常大,其中电网基础建设的投资和发展对变压器产品需求的影响更为直接。油枕作为变压器油箱的主要附件需求量也在增大。
油枕也称储油柜,油枕装在油箱的顶盖上。油枕的体积是油箱提及的10%左右。在油枕和油箱之间有管子连通。当变压器的体积随着油的温度变化而膨胀或缩小时,油枕起着储油和补油的作用,保证铁芯和绕组浸在油内;同时由于装了油枕,缩小了油和空气的接触面,减少了油的劣化速度。油枕侧面有油标,在玻璃管的旁边有油温在-30℃、+20℃和+40℃时的油面高度标准线,表示未投入运行的变压器应该达到的油面;标准线主要可以反映变压器在不同温度下运行时,油量是否充足。油枕上装着呼吸孔,使油枕上部空间和大气相通。变压器油热胀冷缩时,油枕上部的空气可以通过呼吸孔出入,油面可以上升或下降,防止油箱变形甚至损坏。
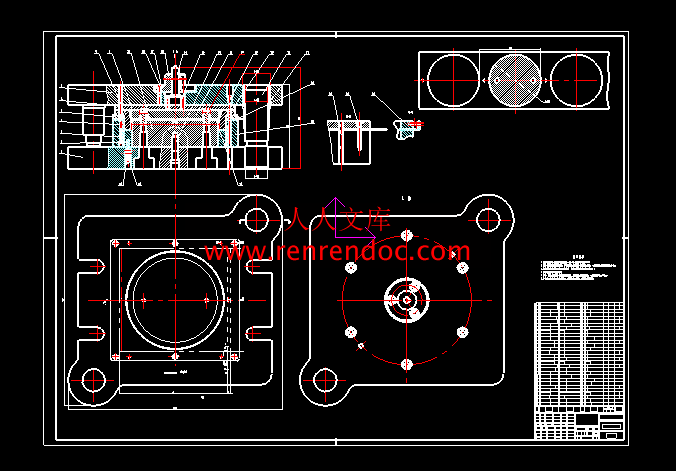
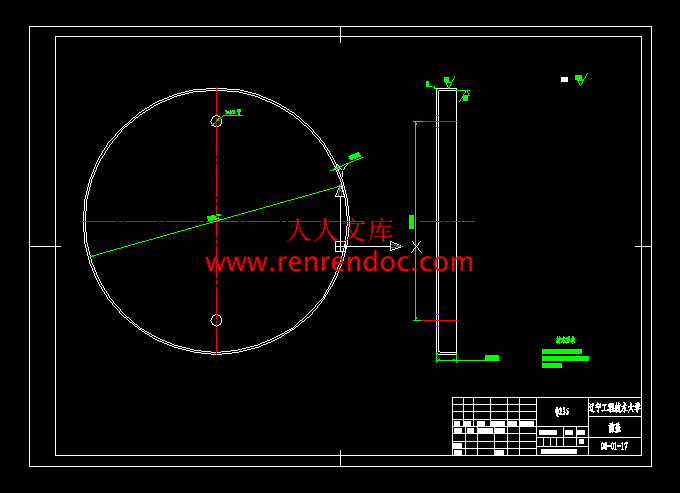
- 内容简介:
-
变压器油枕前盖冲压成形级进模设计目录前言11 设计初始资料32 分析冲压工件的工艺性42.1 冲压件的工艺性分析42.2 冲压件的尺寸精度及标注42.3 工艺方案的确定及模具形式43 拟定冲压件工艺方案53.1 排样53.2 工序的确定53.3 搭边类型的确定53.4 卸料板的选择64 工艺计算74.1 毛坯料尺寸计算74.1.1 确定是否加修边余量74.1.2 毛坯直径74.1.3 确定是否需要压边圈84.1.4 确定拉伸次数84.2 搭边84.2.1 搭边的作用84.2.2 搭边的数值94.3 送料步距104.4 条料宽度104.5 材料利用率114.6 计算冲压力124.6.1 对毛坯冲孔、落料的冲裁力计算124.6.2 对于毛坯用压边圈拉深的计算134.6.3 辅助工艺力计算144.7 压力中心的确定164.7.1 压力中心164.7.2 压力中心的计算165 凸、凹模刃口尺寸计算185.1 刃口尺寸确定的原则185.2 冲裁间隙的选择185.3 尺寸计算195.3.1 对于286毛坯进行落料时的刃口尺寸计算195.3.2 对于11和4 孔冲裁时的尺寸计算205.3.3 对拉深模的尺寸计算206 模具强度的校核226.1 模具失效形式226.2 对冲裁部分的模具零件进行校核计算226.2.1 压应力校核226.2.2 弯曲应力的校核237 模具主要零部件设计247.1 模架的选用247.2 导向装置的确定247.3 模柄的选择247.4 定位装置的设计247.5 卸料形式的确定257.6 导料装置的确定258 模具材料的选用268.1 选择材料的原则268.2 工作零件材料的选择方法及步骤269 压力机的选用2810 模具工作过程2911 经济性分析3012 总结32致谢33参考文献34附录A35附录B39 摘要一副级进模内可以包含冲裁,弯曲,成型,拉深等多道工序,一台冲床可完成从板料到成品的各种冲压过程。它免去了用单工序模的周转和每次冲压的定位过程,提高了劳动生产率和设备利用率。本文进行了变压器油枕前盖冲压成形级进模的设计,通过对待冲压成形的工件变压器油枕前盖的分析,确立了冲压的工艺过程以及冲压级进模的结构。而后对级进模的各个主要零部件进行了尺寸的计算和强度校核,通过压力机的确定,设计出了整个冲压级进模。所设计的级进模,使目前生产变压器油枕前盖的效率大大提高,并且有效降低了生产成本,获得收益的增加。关键词:级进模;变压器油枕前盖;模具设计ABSTRACTThere are many working procedure in a progressive die, and only one piercing lath can finish the process from material to finished product. It exempted from locating process which appeared in the plain die, and increased the working productivity and using rate of equipment. This article has designed the progressive die which is in use of punching the front cover of transformer. By analyzing the front cover of transformer, it designed the technical process and the structure of progressive die. Then it calculated the size of important components, checked them, and designed the whole progressive die by the way of choosing pressure motor finally. the progressive die designed improved the productivity of the oil tank front cover of transformer, decreased the cost of producing and increased the income.Key words: progressive die; the oil tank front cover of transformer; die design前言变压器是一种把电压和电流转变成另一种(或几种)同频率的不同电压电流的电气设备。发电机发出的电功率,需要升高电压才能送至远方用户,而用户则需把电压再降成低压才能使用,这个任务是变压器才能完成的。因此变压器是电力工业中非常重要的组成部分,在发电、输电、配电、电能转换和电能消耗等各个环节都起着至关重要的作用,也是电工行业的主要组成部分之一,在国民经济中占有非常重要的地位1。 作为电力工业的重要的装备行业之一,变压器制造业其发展受电力工业的影响非常大,其中电网基础建设的投资和发展对变压器产品需求的影响更为直接。油枕作为变压器油箱的主要附件需求量也在增大。 油枕也称储油柜,油枕装在油箱的顶盖上。油枕的体积是油箱提及的10%左右。在油枕和油箱之间有管子连通。当变压器的体积随着油的温度变化而膨胀或缩小时,油枕起着储油和补油的作用,保证铁芯和绕组浸在油内;同时由于装了油枕,缩小了油和空气的接触面,减少了油的劣化速度。油枕侧面有油标,在玻璃管的旁边有油温在-30、+20和+40时的油面高度标准线,表示未投入运行的变压器应该达到的油面;标准线主要可以反映变压器在不同温度下运行时,油量是否充足。油枕上装着呼吸孔,使油枕上部空间和大气相通。变压器油热胀冷缩时,油枕上部的空气可以通过呼吸孔出入,油面可以上升或下降,防止油箱变形甚至损坏。油枕的作用是:调节油量,保证变压器油箱内经常充满油;减小油和空气的接触面,防止油受潮或氧化速度过快2。油枕前盖是油枕的主要部分,前盖上面留有油标安装位置。而现在的油枕前盖制作仍处在小批量生产,生产率低。为适应现在市场上的需求量,应采用生产率高的能实现大批量生产的级进模加工。目前,我国的模具技术有了很大发展,模具的精密度、复杂程度和寿命都有很大提高。如,主要的汽车模具企业已能生产大型、精密的轿车覆盖件模具;体现高水平制造技术的多工位级进模的覆盖面增加;塑料模热流道技术日渐成熟,气体辅助注射技术开始采用;压铸工艺得到发展。此外,CAD/CAM/CAE技术得到广泛应用,高速加工、复合加工等先进的加工技术也得到进一步推广;快速原型进展很快;模具的标准化程度也有一定提高。但是,由于我国的模具行业起步较晚,与国外相比,仍存在不小的差距,主要体现在: 产需矛盾:随着工业发展水平的不断提高,工业产品更新速度的加快,对模具的需求越来越大。无论是数量还是质量都无法满足国内市场的需要,只达到70左右。造成矛盾突出的原因是模具企业的专业化、标准化程度低,生产周期长。另外,设计和制造工艺水平还不能完全适应发展的需要。企业结构不合理:我国很多模具生产能力集中在各主机厂的模具分厂或车间内,模具的商品化程度低,而国外70以上都是专业模具厂,且走的是“小而精”的道路,因此生产效率和经济效益俱佳。产品水平:衡量模具的产品水平,主要有模具加工的制造精度和表面粗糙度,加工模具的复杂程度,以及模具的制造周期和使用寿命。而这几项指标与国外相比的差距都十分明显。此外,模具工业的整体装备水平也存在相对落后,利用率低的现象。高素质的模具技术人才缺乏,产品的综合开发能力还急需加强。经过了几年的大学学习之后,在此毕业设计中,我选择了模具设计的这个题目,在各位老师的指导及帮助下完成了本次设计。因本人无任何实际生产经验及设计经验,仅从理论和书本上出发,进行了本次设计,难免有不少疏漏和错误之处,恳请各位指导老师予以指正,提出批评。另外,对设计中对我进行指导的所有老师表示感谢!491 设计初始资料注有技术要求的产品零件图,如下:图1-1 待加工工件-变压器油枕前盖Fig 1-1 the workpiece waiting to machining1) 工件生产批量此零件的生产批量为大批量生产。2) 原材料规格冲压零件使用材料为Q235, 3) 未注公差这次所设计工件,未注尺寸公差取自由精度IT14。4) 模具制造技术能力和设备条件及可采用模具标准状况因为本设计是在理论基础上进行设计,故模具制造技术能力及设备条件从理论上满足即可。在设计中,尽可能地利用模具标准件。我国的模具零部件有不少已经形成国家标准,且有系列化标准。比如:凸模、凹模、挡料销、定位销、上下模板、模柄、凸凹模固定板等。设计中,对于模架及连接、定位件,都采用了国家标准。对于凸模、凹模等不易采用国家标准的零件,进行了单独设计,以满足加工产品零件的加工要求以及使用要求。2 分析冲压工件的工艺性分析冲压零件的工艺性主要包括以下两个方面:即经济和技术两方面。由于该工件为大批量生产,故可采用冲模冲压加工生产,采用普通的冲压的模具生产较率低,且费用较高,经估算占冲压件总成本的30%40%,甚至更高一些。因此,在选择生产方法时,根据工件特点选择采用级进模冲压生产以提高生产效率、降低生产成本。另外,在设计时尽量简化加工工序、采用简单的冲模结构也可降低模具的生产成本,以取得更大的经济效益。2.1 冲压件的工艺性分析由产品零件简图中可以得到以下信息:在前盖这个零件中,没有不规则的曲线及棱角,且在各曲线相接之处均有圆角过渡,没有一处为尖角,所以从这一点来看,前盖这个零件可以用冲压工艺生产。而且,这些圆滑过渡还有利于模具制造及提高模具的使用寿命。2.2 冲压件的尺寸精度及标注表2-1 冲模制造精度与冲裁件精度之间的关系Tab.2-1 the connection between precision of punching die and cuttered parts冲模制造精度板料厚度()1.52.03.04.05.06.08.0IT6IT7IT8IT8IT9IT10IT10IT7IT8IT9IT10IT12IT12IT12IT12IT9IT12IT12IT12IT12IT12IT14IT142.3 工艺方案的确定及模具形式1) 根据以上对该工件的分析,该工件尺寸精度要求不高,形状简单,无尖锐清角等问题存在,但产量较大,根据尺寸较大,材料较厚的特点,同时为保证孔位精度,冲模有较高的生产率,采用工序集中的方案。2) 同时根据工件特点,采用导正销进行定位、刚性卸料装置、自然漏料方式的级进模冲压模结构形式。3 拟定冲压件工艺方案3.1 排样排样是冲裁件在条料上的布置方法。合理的排样可以提高材料的利用率,从而降低生产成本。因此,合理的排样是冲裁模设计的重要内容。排样主要依据工件的外形特征,主要分为直排、斜排、直对排、混合排、多行排等形式。考虑到压力机的使用以及模具的设计成本,本次设计的工件采用直排可使生产成本最少3。根据该冲压件的形状特征,采用单排排样。3.2 工序的确定在级进模设计中,应根据产品零件的技术要求和形状特点选择合适的冲压工序,确定各工位所完成的工序,这一工作成为工序排样。根据零件图的特点初步确定工序性质、工序数目、工序顺序。由于此工件采用级进模具加工,考虑到模具的制造难易成度以及材料的利用率,加工步骤确定如下:1) 冲工艺孔2) 落料、拉深、冲工件孔3.3 搭边类型的确定在条料上冲裁时,工件之间以及工件和条料侧边之间的余料称为搭边。搭边分为三种:有搭边、少搭边和无搭边。搭边的作用是补偿送料误差,以保证冲出合格工件;保持条料刚度利利于送料避免废料丝进入模具间隙导致模具损坏。搭边值要合理确定,从节省材料出发搭边值越小越好,但搭边值小于一定数值后,对模具寿命和剪切表面质量不利。搭边值的大小与下列因素有关:1) 材料的力学性能 硬材料的搭边值可小一些,软材料、脆材料的搭边值要大一些。2) 零件的形状与尺寸 零件尺寸大或有尖角和突出等复杂开头时,搭边值应大一些。3) 材料厚度 厚度大的材料搭边值取大一些。4) 送料及挡料方式 手工送料时,有侧压板导向的搭边值可以小些。3.4 卸料板的选择卸料板的主要作用是把材料从凸模上卸下,有时也可作压料板用以防止材料变形,并能帮助送料导向和保护凸模等。卸料板有固定卸料板(又称钢性卸料板)和弹性卸料板两种。固定卸料板用于厚料或硬材,特点是卸料力大,使用安全,但送料操作受约束;弹性卸料板具有卸料和压料的双重作用,多用于冲制薄料,使工件的平面主提高,借助弹簧、橡胶或气垫等弹性装置卸料,常兼作压边、压料装置或凸模导向。本次设计选择使用刚性卸料装置。4 工艺计算4.1 毛坯料尺寸计算4.1.1 确定是否加修边余量 根据冲压件相对高度: (4-1) 可不考虑加修边余量。4.1.2 毛坯直径根据下图和下公式,可计算毛坯直径 (4-2)式中 毛坯直径(); 中径(); 中径高(); 圆角半径()图4-1 毛坯料展开尺寸计算5Fig.4-1 dimension calculating on material unfolded4.1.3 确定是否需要压边圈根据坯料相对厚度 (4-3) 式中 坯料厚度()所以需要压边圈。表4-1 采用或不采用压边圈的条件Tab.4-1 conditions on adopt or not press circle拉深方法第一次拉深以后各次拉深 (%)(%)用压边圈1.50.610.8可用不可用1.52.00.611.50.8不用压边圈2.04.1.4 确定拉伸次数根据相对厚度查设计资料确定出圆筒形件(带压边圈)极限拉深系数m1=0.600.631.02=0.6120.6426,而工件的拉深系数为,大于m1,则可一次拉成。4.2 搭边排样时冲裁件与冲裁件之间(a)以及冲裁件与条料侧边之间(a1)留下的工艺余料称为搭边。4.2.1 搭边的作用起补偿条料的剪裁误差、送料步距误差以及补偿由于条料与导料板之间有间隙所造成的送料歪斜误差的作用。若没有搭边则可能发生工件缺角、缺边或尺寸超差等废品。使凸、凹模刃口双边受力。由于搭边的存在,使凸、凹模刃口沿整个封闭轮廓线冲裁,受力平衡,合理间隙不易破坏,模具寿命与工作断面质量都能提高。对于利用搭边拉条料的自动送料模具,搭边使条料有一定的刚度,以保证条料的连续送进。4.2.2 搭边的数值搭边过大,浪费材料。搭边太小,起不到上述应有的作用。过小的搭边还可能被拉入凸模和凹模的间隙,使模具容易磨损,甚至损坏模具刃口。搭边的合理数值就是保证冲裁件质量、保证模具较长寿命、保证自动送料时不被拉弯拉断条件下允许的最小值。搭边的合理数值主要决定于材料厚度、材料种类、冲裁件的大小以及冲裁件的轮廓形状等。一般来说,板料愈厚,材料愈软以及冲裁件尺寸愈大,形状愈复杂,则搭边值a与a1也应愈大。下表是对应图的搭边宽度的经验值。表4-2 搭边尺寸Tab.4-2 the dimension of side料宽搭边a和a1a和a1的最小值251.0t0.825751.25t1.2751501.5t2.51503002t5.5图4-2 搭边尺寸3Fig.4-2 the dimension of side3在本设计中,根据上表中a值最小值为5.5,由实际情况决定取a=34。4.3 送料步距条料在模具上每次送进的距离称为送料步距(简称步距或进距)。每个步距可以冲出一个零件,也可以冲出几个零件。送料步距的大小应为条料上两个对应冲裁件的对应点之间的距离。本次设计为每次只冲一个零件,步距A计算公式为: (4-4)式中 冲裁步距(); 沿条料送进方向,毛坯外形轮廓的最大宽度值(); 沿送进方向的搭边值()在本次设计中,工件沿条料送进方向上最大宽度为286,工艺孔沿条料送进方向上最大宽度为4,所以冲裁步距A=L+a=286+34=3204.4 条料宽度条料是由板料剪裁下料而得,为保证送料顺利,剪裁时的公差带分布规定上偏差为零,下偏差为负值(-)。条料在模具上送进时一般都有导向,当使用导料板导向而又无侧压装置时,在宽度方向也会产生送料误差。条料宽度B的计算应保证在这二种误差的影响下,仍能保证在冲裁件与条料侧边之间有一定的搭边值a1。本设计采用无侧压装置,条料宽度按下式计算4: (4-5)式中 条料与导料板之间的间隙(表4-3)() 剪板机剪料的下偏差(表4-4)()表4-3 条料与导料板之间的间隙 ()Tab.4-3 the gap between strip and leading board条料厚度无侧压装置有侧压装置条料宽度10010020020030010010010.50.5158150.81158表4-4 剪板机剪料的下偏差()Tab.4-4 the Lower deviation of cutted materical by cutting machine条料厚度条料宽度50501001002002004001.0130.51.01.01.0341.01.01.01.5461.01.01.52.04.5 材料利用率图3-1 排样图5Fig 3-1 pilot5选用9002000的钢板根据条料宽度裁成3条。 =900/300=3条每条裁板上的冲压件数(个)每张钢板的冲压件总数(个)板料的利用率: (4-6)式中 板料利用率; 每张板料的冲压件总数(个) 整个板料长度(); 整个板料宽度()4.6 计算冲压力4.6.1 对毛坯冲孔、落料的冲裁力计算冲裁力是指冲裁时,材料对凸模的最大抵抗力,它是选择冲压设备和校核模具强度的重要依据6。其冲裁力按以下公式计算: (4-7)式中 冲裁力(N); 冲裁件周长(); 板料厚度(); 料抗剪强度(N/2); 系数公式是对冲裁区的变形进行简化,认为是纯剪变形区得到的,而变形区的实际情况比较复杂,因此采用系数加以修正,一般取=1.3,在本设计中冲裁部分均为圆形,所以冲裁件周长为圆周长在进行毛坯落料时,冲裁力为 式中 毛坯直径,286 材料抗剪强度,Q235钢=310380MPa,取330MPa在进行毛坯冲孔时,冲裁力为F冲,同时冲2个的孔和的孔,则 式中 工件孔直径, 11 工艺孔直径, 44.6.2 对于毛坯用压边圈拉深的计算在实用上,拉深力F(N)可按下式计算: (4-8)式中 拉深件直径(); 料厚(); 材料抗拉极限(MPa); 修正系数,与拉深系数有关。m愈小,愈大。式中 修正系数,=0.4,由表4-5查得; 材料抗拉强度,Q235钢=380470MPa,取440MPa表4-5 修正系数K的数值Tab.4-5 the value of modifying coefficientm10.550.570.600.620.650.670.070.720.750.770.80K11.000.930.860.790.720.660.600.550.500.450.40mn0.700.720.750.770.800.850.900.95K21.000.950.900.850.800.700.600.504.6.3 辅助工艺力计算1) 压边力在拉深过程中,为防止凸缘部分材料起皱,可以采用压边圈的方法。此时,压边力应适当。当压边力不足时,材料会起皱;压边力过大时,拉深件壁部易拉裂破坏。压边力通常可以调节。本设计中采用了压边圈,另外由于加工需要,压力圈还兼起顶出工件的作用。压边力计算公式: (4-9)式中 压边面积(2); 单位面积上的压边力(MPa) ,其值可有表4-6查取。表4-6 单位压边力值Tab.4-6 the value of unit pressure on side材料单位压边力p/MPa铝0.81.2紫铜、杜拉铝(退火的或淬好火的)1.21.8黄铜1.52.0软钢 t0.52.02.5软钢 t20钢、08钢、镀锡钢板2.53.0软化状态的耐热钢2.83.5高合金钢、高锰钢、不锈钢3.04.5对于筒形件,则第一次拉深时的压边力:式中 凹模圆角半径,取=6; 单位压边力,=2.5MPa 查表可知。 2) 卸料力在冲裁后,多余的材料会由于弹性变形而卡在凸模上,这时就需要把废料卸下来,卸料的作用力就是卸料力。 (4-10)式中 系数,由表4-2查得3) 顶料力在拉深之后,工件会有一定的弹性形变,所以要将其顶出来。计算公式: (4-11)式中 系数,由表4-2查得,取0.055 拉深件个数表4-7 卸料力,推件力和顶件力系数Tab.4-7 the coefficient of pressure that unloading material, pushing part and peaking part料厚/mm钢0.10.0650.070.050.0450.0550.0630.040.050.0550.030.040.0450.056.50.020.030.0250.03铝,铝合金0.0250.080.030.07紫铜,黄铜0.020.060.030.094) 推料力 在冲压加工完成后,由工件变形和模具结构上来看,工件可能卡在上模中,此时由推料机构将其从上模中推出,其推料力计算公式为: (4-12)式中 系数,由表4-2查得,取0.06 为使压力机能安全工作,压力机标称压力应大于所需总压力所以选取。初选压力机为J21A-160型。其主要参数如下:标称压力:1600kN滑块行程:20160工作台尺寸:1000710最大装模高度:350最小装模高度:230工作台孔直径:4254.7 压力中心的确定4.7.1 压力中心冲压力合力的作用点称为冲模压力中心。为保证冲模能够正确和平衡地工作,冲模压力中心必须与通过模柄轴线和压力机滑块的中心线相重合。以免滑块受偏心载荷,从而减少冲模及压力机导轨的非正常磨损,提高模具寿命,避免冲压事故9。模具压力中心可按静力平衡原理计算,即压力中心等于各冲压力构成的平行力系构成的合力作用点7。4.7.2 压力中心的计算根据下图计算图4-3 压力中心计算Fig.4-3 the calculate on press center由于所冲两个孔关于中心线对称的,所以冲孔力的作用点就在中心线上。在(x1,0)处的作用力为P1,在(x2,0)处作用力为P2,且=155,令x1=100,则x2=255公式: (4-13) 及x1=100,x2=255代入式中得从上式结果中可以看出,压力中心几乎与工件几何中心重合,而且二者相差极小。加上在实际生产中难免存在的加工误差影响,所以可将工艺冲压力忽略,即取工件的几何中心为压力中心。5 凸、凹模刃口尺寸计算5.1 刃口尺寸确定的原则凸、凹模刃口尺寸和公差的确定,直接影响冲裁生产的技术经济效果,是冲裁模设计的重要环节,必须根据冲裁的变形规律、冲模的磨损规律和经济的合理性综合考虑,遵循以下原则8:1) 设计落料模时,应以凹模尺寸为基准,间隙取在凸模上,靠减小其尺寸获得;设计冲孔模时,应以凸模尺寸为基准,间隙取在凹模上,靠增大其尺寸获得。2) 根据冲模的磨损规律,凹模的磨损使落料件轮廓尺寸增大,因此设计落料模时,凹模的刃口尺寸应等于或接近工件的下极限尺寸;凸模的磨损使冲孔件的孔径尺寸减小,因此设计冲孔模时,凸模的刃口尺寸应等于或接近工件的上极限尺寸。3) 冲裁模在使用中,由于磨损间隙值将不断增大,因此设计时无论是落料模还是冲孔模,新模具都必须选取最小合理间隙Zmin,使模具具有较长的寿命。4) 根据工件尺寸公差的要求,确定模具刃口尺寸的公差等级,如表所示。表5-1 模具公差和工件公差的关系8Tab.5-1 the connection of tolerance between mold and workpiece8模具公差板料厚度()1.52.03.04.05.06.08.0工件公差IT6IT7IT8IT8IT9IT10IT10IT7IT8IT9IT10IT12IT12IT12IT12IT9IT12IT12IT12IT12IT12IT14IT145.2 冲裁间隙的选择间隙在冲裁模中指凸、凹模刃口间缝隙的距离,通常称为单边间隙。考虑使用习惯,仍采用双边间隙作为间隙的定义。对普通冲裁,间隙对冲裁力和卸料力有明显影响。特别对卸料力影响显著。与此同时,间隙还影响冲裁件的尺寸和模具寿命。试验表明,当间隙过小时,落料件尺寸大于凹模尺寸,冲孔件尺寸小于凸模尺寸;间隙过大时,落料件尺寸小于凹模尺寸,冲孔件大于凸模尺寸。在正常使用情况下,间隙增大,模具寿命会明显提高。选用冲裁间隙的主要依据是在保证冲件断面质量的前提下使模具寿命提高。在通常情况下,可根据冲件剪切表面质量及尺寸精度、模具寿命等因素,将冲裁间隙分为两大类。其中小间隙主要适用于电子、电工、仪表等行业,冲裁厚度较薄(t0.5);大间隙适用于冲裁厚件(t0.5)的冲模以及一般技术要求的模具。5.3 尺寸计算凸、凹模的刃口尺寸计算按加工方法不同,可分为两种情况:凸模和凹模分开加工;凸模和凹模配合加工。在本设计中,因主要冲裁的工件形状均为圆形,故采用前一种方法,即凸模与凹模分开加工。采用此方法时,要分别标注凹模及凸模的刃口尺寸及制造公差。5.3.1 对于286毛坯进行落料时的刃口尺寸计算设落料尺寸为,根据以上各原则,此时先确定凹模刃口尺寸,其基本尺寸接近好等于工件轮廓最小极限尺寸,再减小凸模刃口尺寸以保证最小合理间隙。计算公式如下: (5-1) (5-2)式中 , 分别为落料凸、凹模刃口尺寸(); 工件制造公差(); 落料件外径的基本尺寸(); 最小合理间隙(双边)(); , 分别为凸凹模制造偏差(); 磨损系数,工件精度为IT14时,=0.5已知落料时工件尺寸为查表取=0.246,=+0.050 =-0.035所以凹模尺寸:凸模尺寸: 5.3.2 对于11和4 孔冲裁时的尺寸计算设工件孔的尺寸为,根据上述原则,冲孔应先确定凸模刃口尺寸,凸模刃口的基本尺寸接近或等于工件孔的最大尺寸,再增大凹模刃口尺寸以保证最小合理间隙。凸模制造偏差取负偏差,凹模制造偏差取正偏差。计算公式如下: (5-3) (5-4)式中 , 分别为冲孔凸模和凹模尺寸(); 孔基本尺寸; 工件制造公差 磨损系数,工件精度为IT14时,=0.5已知冲孔时,孔基本尺寸为查表得 =0.246,=-0.020,=+0.020所以凸模尺寸:凹模尺寸: 对于冲的工艺孔也如上计算其基本尺寸为查表得=0.246,=-0.020,=+0.020所以凸模尺寸:凹模尺寸:5.3.3 对拉深模的尺寸计算1)拉深模间隙的确定拉深模的间隙是指单边间隙,即。间隙过小增加摩擦阻力,使拉深件容易破裂,且易擦伤零件表面,降低模具寿命;间隙过大,则拉深时对毛坯的校直作用小,影响零件尺寸精度。因此,确定间隙的原则是既要考虑板料厚度的公差,又要考虑筒形件口部的增厚现象,根据拉深时是否采用压边圈和零件的尺寸精度要求合理确定。本设计中采用了压边圈拉深一次拉深成形,可查表选取拉深间隙Z=1t=12=2。2)拉深凹模和凸模的尺寸及其公差:本设计对工件要求内形尺寸,以凸模尺寸为基准进行计算。即凸模尺寸: (5-5)凹模尺寸: (5-6)加工工件尺寸为,查表 =0.06 , =0.10凸模尺寸:凹模尺寸:6 模具强度的校核6.1 模具失效形式模具的失效是指模具丧失了正常工作能力,其生产出的产品已成为废品。模具的基本失效形式是断裂及开裂、磨损、疲劳及冷热疲劳、变形腐蚀。模具在工作过程中可能出现多种损坏形式,各种损伤之间又互相渗透,相互促进,各自发展,而当某种损坏的发展,导致模具失去正常功能时,则模具失效9。而影响模具失效的因素主要有以下几方面:1) 模具结构影响。模具结构包括模具几何形状、模具间隙、冲头模具的长径比、端面倾角、端面倾角、过渡角大小、装配结构等。不合理的机构可能会引起严重的应力集中或高的工作温度,从而恶化模具的工作条件。2) 模具材料的影响。模具材料必须满足对塑性变形抗力、断裂抗力、疲劳抗力、硬度耐磨性、冷热疲劳抗力,以及韧性等性能要求。如不能满足,则会发生模具早期失效。如在循环载荷下,如果材料的疲劳抗力差,在经过一定的应力循环后,可能萌发疲劳裂纹,并逐渐发展至模具断裂失效。3) 热处理及加工制造工艺的影响。模具进行热处理的目的是为了使模具获得理想组织,从而获得所需性能。但若热处理工艺不当,或工艺不合理,则可导致模具韧性下降,产生热处理缺陷,或性能降低,从而引发模具早期失效。模具加工制造工艺,特别是锻造工艺,对模具的失效影响就越大。合理地锻造工艺使大块碳化物破碎,使之细小分布均匀,但若锻造工艺不合理,则达不到打碎晶粒,改善方向性,提高钢的致密等目的,甚至引发锻造缺陷。6.2 对冲裁部分的模具零件进行校核计算在本次模具设计中,容易发生失效的零件主要是加工孔和孔的凸模,针对此零件进行校核。6.2.1 压应力校核 (6-1)式中 凸模最小直径(); 材料厚度(); 材料的抗剪强度(MPa);Q235为310380MPa,取330MPa; 凸模材料许用压力(MPa);本设计凸模材料选用T10A,取1600MPa。则 ,远远小于11和4,故满足使用要求。6.2.2 弯曲应力的校核冲孔是有导向装置的,其公式为: (6-2)式中 凸模允许的最大自由长度(); 凸模的最小直径(); 冲裁力(N)在设计中,凸模长度取4041.6满足。对于的孔,为无导向的,其公式为: (6-3)式中 凸模最大允许长度() 凸模最小直径() 冲裁力(N) 在设计中,凸模长度为5066.8,故满足。 7 模具主要零部件设计7.1 模架的选用模架是由上、下模座、模柄及导向装置(最常用的是导柱、导套)组成。模架是整副模具的骨架,模具的全部零件都固定在它上面,并且承受冲压过程中的全部载荷。模架的上模座通过模柄与压力机滑块相连,下模座用螺钉压板固定在压力机工作台面上。上、下模之间靠模架的导向装置来保持其精确位置,来引导凸模的运动,保证冲裁过程中间隙均匀。一般模架均以列入标准,设计模具时,正确选择即可10。标准模架中,应用最广的是用导柱、导套作为导向装置的模架。根据导柱、导套配置不同分4种形式:后侧导柱模架;中间导柱模架;对角导柱模架;四导柱模架。模架大小的规格可直接由凹模的周界尺寸从标准中选取。根据加工工件的最大高度为20,下模最大尺寸值为360,选出模架规格为 ,导程其国标号为:GB/T2851.1-907.2 导向装置的确定由于模架已确定,故导柱的直径就已经确定,再根据模具需要的闭合高度H应大于零件加工最大高度的22.5倍即可确定导柱长度。在设计中,选用了国标号为GB/T2861.2-90B型滑动型导柱。其直径d=50,长度为240导柱确定后,导套直径就确定了,导套外径为D=65。因为工件的最大高度为20,所以与导柱的滑动配合处长度应大于2.520=50。再根据国家标准GB/T2861.7-90,确定导套长度为140。7.3 模柄的选择 由压力机参数中的模柄孔直径就可以确定模柄尺寸。选用模柄C型凸缘模柄,其基本参数为,模柄凸缘直径D=115,模柄高度为90,使用三个M8的沉头内六角圆柱螺钉与上模座连接。7.4 定位装置的设计定位装置:为限定被冲材料的进给步距和正确地将工件安装在冲模上完成下一步的冲压工序,必须采用各种形式的定位装置。定位装置应可靠并具有一定的强度,以保证工作精度,质量的稳定;定位装置应可以调整并设置在操作者容易观察和便于操作的地方;定位装置应避开油污,碎屑的干扰并且不与运动机构干涉。本设计中在条料进入导料时,在进行第一次冲压前,设有初始挡料削,用与定位,保证条料有正确的送料距。另外在凸模上安装导正销,在落料工位进行导正,其以尖圆头一端先进入零件在第一工位冲孔时预先冲出的定位孔中,以辅正送料中的误差,起到精确定位的作用,然后再进行落料冲压,提高产品精度。7.5 卸料形式的确定卸料板的主要作用是把材料从凸模上卸下,有时也可作压料板用以防止材料变形,并能帮助送料导向和保护凸模等。卸料板有固定卸料板(又称钢性卸料板)和弹性卸料板两种。固定卸料板用于厚料或硬材,特点是卸料力大,使用安全,但送料操作受约束;弹性卸料板具有卸料和压料的双重作用,多用于冲制薄料,使工件的平面主提高,借助弹簧、橡胶或气垫等弹性装置卸料,常兼作压边、压料装置或凸模导向。由于本次设计中卸料力较大,因此本次设计选择使用刚性卸料装置。7.6 导料装置的确定在设计中,采用2条320的导料尺进行导料。 采用自动送料装置,为防止增大摩擦力,使条料不能送进,所以不采用侧压装置。8 模具材料的选用8.1 选择材料的原则选择模具材料应遵守以下几条原则11:1) 使用性原则使用性原则是保证模具完成预定功能的必要条件,也就是说,用选择的材料制成的模具零件,从材料的机械性能及能理性能方面,能够满足该零件的使用功能要求。2) 加工工艺性原则加工工艺性原则是指所选材料加工零件时,应具有较好的加工工艺性。与使用原则相比,它处于次要地位。选择材料时,在满足了使用性原则基础上,应力求所选材料具有较好的加工性能。比如:切削加工性能、特种加工性能、锻造性能以及热处理加工性能。3) 经济效果原则经济效果原则要求选用便宜的材料,将模具的费用降低到最低程度,求得最好的选材经济效果。合理选用材料,在满足使用性能原则基础上尽可能利用成本低、供应充分的钢材。例如:模具钢垫板,当作用的单位压力特别大时,应选用材料T8A或9Mn2V;当作用的单位压力较小时,应选用45中碳钢。再如工作零件,能选用低合金就不选用单价较高的高铬钢。采用先进的加工方法,以提高模具的使用寿命。推广新型模具材料和表面处理方法,节约贵重钢材。8.2 工作零件材料的选择方法及步骤工作零件选材料最重要的是要做好“一个对比”和“一个结合”。一个对比是将现有模具材料进行对比,从中初选出满足性能要求的材料。一个结合是指将使用性能、加工工艺性和经济效果三原则相结合,从中选出一个合适的材料。一般常用方法与步骤:1) 分析模具工作条件、应力状态,明确技术要求。2) 根据所要求的机械性能,正确选择钢种。3) 审核选用钢种是否满足工艺性能要求以及实现新工艺、采用新技术的可能性。4) 考虑所选钢种的生产经济性。另外还需要考虑两个因素: 被加工对象的特点,不同加工材料其变形能力不同;加工零件数量,加工零件总数越多,磨损越严重,要求模具材料愈好。以下为各主要零件材料选用状况:落料凹模T10A淬硬HRC5862凸凹模Cr12MoV淬硬HRC5862拉深凸模T10A淬硬HRC5660拉深凹模 T10A淬硬HRC5862冲孔凸模Cr12MoV淬硬HRC5862压边圈T10A淬硬HRC5458卸料板45压板(推块) Q235淬硬HRC4348顶杆、推杆45淬硬HRC4348模柄Q235淬硬HRC4348导柱、导套20渗碳淬火HRC5862上下模座HT200上模固定板45淬火HRC43489 压力机的选用在冷冲压生产中,为了适应不同的冲压工作需要,采用了不同类型的压力机。压力机的类型很多,按传动方式的不同,主要可分为曲柄压力机和液压压力机两大类。其中机械压力机在冷冲压生产中应用最广泛。随着现代冲压技术的发展,高速压力机、数控回转头压力机等也日益得到广泛地应用12。1) 模具闭合高度曲柄压力机,模具的闭合高度与压力机闭合高度之间要符合以下公式。 (9-1)式中 模具的闭合高度(); 压力机的最大闭合高度(); 压力机的最小闭合高度(); 压力机的垫板厚度()由压力机参数中 345248240所以符合要求。工作台尺寸一般应大于模具下模座5070,以便于安装;垫板孔径应大于制件或废料的投影尺寸,以便于漏料;模柄尺寸应与模柄尺寸相符。2) 滑块行程在模具冲压之后,工件加工成形后,要将工件取出,所以开模后上、下模之间距离必须大于工件高度的22.5倍。压力机滑块最大行程为而工件的最大高度为20202.5=50小于160,故满足。另外,模具最大轮廓为595595,而压力机工作台为1000710也满足。从上述计算中,可知J21A-160型,满足设计需要。10 模具工作过程 参照模具总装图叙述模具工作过程。将剪裁好的板料用自动送料机构送进模具中,由右往左送进,条料第一次送入时用初始挡料销24,进行定位,凸模20冲工艺孔,一次冲压后,自动送料机构将板料送进一个步距,活动挡料销3 卡入冲好的工艺孔对落料拉深进行定位。压力机带动上模向下运动,进行落料拉深,拉伸弹簧28被拉长,落料凹模8比拉深凸模10的相对位置高出一个材料厚度。完成拉深后,凸模冲孔,完成整个加工成形过程,上模随模柄13上升,推料螺钉在拉伸弹簧作用下收缩,将压边圈29向上推出,从而把工件推出,工件可能卡在上模中,当上模上升到一定高度时,打料杆14推动推块15,推块15推动推料杆11,推动凹模17将工件推出。待工件由专门装置取出或人工取出后,继续下一个工件的加工,如此循环下去。11 经济性分析模具的技术经济指标概括起来可以归纳为:模具的精度和刚度、模具的生产周期、模具的生产成本和模具的寿命个基本方面。模具生产过程的各个环节都应该根据生产对模具在这个方面的要求考虑问题。同时模具的技术经济指标也是衡量一个国家、地区和企业模具生产技术水平的重要标志。模具的精度和刚度:模具的精度机械产品的精度包括尺寸精度、形状精度、位置精度和表面粗糙度。机械产品在工作状态和非工作状态的精度不同,分别称为动态精度和静态精度。模具的精度主要体现在模具工作零件的精度和相关部位的配合精度。模具工作部位的精度高于产品制件的精度,例如冲裁模刃口尺寸的精度要高于产品制件的精度。冲裁凸模和凹模间冲裁间隙的数值大小和均匀一致性也是主要精度参数之一。平时测量出的精度都是非工作状态下的精度(如冲裁间隙),即静态精度。而在工作状态时,受到工作条件的影响,静态精度发生了变化,变为动态精度,动态精度才是真正有实际意义的。一般模具的精度也应与产品件的精度相协调,同时受模具加工技术手段的制约。随着制造技术的发展,模具加工技术手段的提高,模具精度也会相应地提高,模具工作零件的互换性生产将成为现实。模具的刚度对于高速冲压模、大型件冲压成型模、精密塑料模和大型塑料模,不仅要求其精度高,同时还要求其具有良好的刚度。这类模具的工作负荷较大,当出现较大的弹性变形时,不仅要影响模具的动态精度,而且关系到模具能否正常工作。因此在模具设计中,在满足强度要求的同时,还应保证模具的刚度,同时在制造中也要避免由于加工不当造成的附加变形。模具的生产周期:模具的生产周期是指从接受模具订货任务开始到模具试模鉴定后交付合格模具所用的时间。当前,模具使用单位要求模具的生产周期越来越短,以满足市场竞争和更新换代的需要。因此,模具生产周期的长短是衡量模具企业生产能力和技术水平的综合标志之一,也关系到模具企业在激烈的市场竞争中有无立足之地。同时模具的生产周期长短也是衡量一个国家模具技术管理水平高低的标志。影响模具生产周期的主要因素有: 模具技术和生产的标准化程度; 模具企业的专门化程度;模具生产技术手段的先进程度;模具生产的经营和管理水平。模具的生产成本:模具的生产成本是指企业为生产和销售模具支付费用的总和。模具的生产成本包括原材料费、外购件费、外协件费、设备折旧费、经营开支等等。从性质上又分为生产成本、非生产成本和生产外成本,通常讲的模具生产成本是指与模具生产过程有直接关系的生产成本。影响模具生产成本的主要因素有:模具结构的复杂程度和模具功能的高低;模具精度的高低;模具材料的选择; 模具的加工设备;模具的标准化程度和企业生产的专门化程度。模具的寿命:模具的寿命是指模具在保证产品零件质量的前提下,所能加工的制件的总数量,它包括工作面的多次修磨及易损件更换前后所加工制件的数量之和。一般在模具设计阶段就应明确该模具所适用的生产批量类型或模具生产制件的总次数,即模具的设计寿命。不同类型模具的正常损坏形式也不一样,但总的来说工作表面损坏的形式有摩擦损坏、塑性变形、开裂、疲劳损坏、啃伤等等。影响模具寿命的主要因素有:模具的结构合理的模具结构有助于提高模具的承载能力,减轻模具承受的热-机械负荷水平。模具的材料应根据产品零件生产批量的大小,选择模具材料。模具的加工质量模具零件在机械加工、电火花加工、锻造、预处理、淬硬和表面处理时的缺陷,都会对模具的耐磨性、抗咬合能力、抗断裂能力产生显著的影响。模具的工作状态模具工作时,所使用设备的精度与刚度、润滑条件、被加工材料的预处理状态、模具的预热和冷却条件等都对模具的寿命产生影响。产品零件的状况被加工零件材料的表面质量状态,材料的硬度、延展率等力学性能,被加工零件的尺寸精度等都与模具的寿命有直接的关系。模具的精度和刚度、生产周期、模具的生产成本以及模具的寿命,它们之间是互相影响和互相制约的。在实际生产过程中要根据产品零件和客观需要综合平衡这些因素,抓住主要矛盾,求得最佳的经济效益,满足生产的需要。12 总结1) 通过对变压器油枕前盖的初始资料的分析,我们得知用级进模具生产变压器油枕前盖是可行的。2) 通过对冲压件的工艺性分析,我们得知冲压零件的工艺性主要包括经济和技术两方面。由于该零件为大批量生产,采用级进模生产要比普通生产更高效,成本更低。3) 通过确定工艺方案,我们确制定了先冲工艺孔再落料拉深冲孔的生产工序。并计算了合理的搭边值。4) 通过对压力的计算,我们初步确定了压力机型号,并且确定了压力中心。根据生产工序,对凸、凹模工作部分尺寸进行了计算。确定个主要零件结构尺寸。通过对凸、凹模标准化分析,选择的合理的凸、凹模结构。5) 由于模具的磨损会引起模具工作失效,所以对模具强度的校核非常重要,经分析,凸,凹模均满足生产要求。6) 冲压设备的正确选择及合理使用将决定冲压生产能否顺利进行,并与产品质量,模具寿命,生产效率,产品成本等密切相关。在这里我们选择J21A-160开式固定台压力机。7) 选择模具标准件时要根据工件的受力变形特点,坯件定位,出位方式,材料送进方向,导柱受力状态,操作是否方便等方面进行综合考虑。然后选择最合理的标准配件。分析冲压过程,确定各部件的材料。8) 模具装配都有一定的装配顺序。级进模先装配下模,再以下模为准装配上模,冲裁模装配的主要技术要求是保证凸、凹模的均匀配合间隙。9) 经过广泛的搜集资料,对工件以及级进模的经济性分析,简化了模具的设计及生产成本,提高了模具的使用寿命。10) 通过对变压器油枕前盖级进模的设计,我们学习了模具从设计到生产的整个过程,并且通过与实际生产相结合,与计算机辅助设计相结合。为以后的工作打好了坚实的基础。致谢大学生活即将结束了,在这几年的生活和学习中掌握了一定的专业知识。而毕业设计就是对我们学习知识,掌握情况的检验,锻炼自己动手设计的能力。毕业设计是大学几年中最重要的设计,通过对冲压模具的分析,然后查阅了大量的设计资料,在各位老师及同学的帮助下,逐步完善了设计方案。通过这次毕业设计,把自己以前所学的知识有机的结合起来,并从理论和实际生产两个方面统一考虑,是毕业设计尽量完美。由于本人水平有限,在设计总不可避免出现很多不足之处,希望各位老师给予批评,指正。在设计中,得到了很多老师的帮助,特别是我的指导老师于英华老师给予我很多的帮助,在此表示衷心的感谢!参考文献1 20042005年中国变压器产业研究报告,2005 /news/scfx/20064101716596221919.htm2 尹克宁.变压器设计原理M.第1版.北京:中国电力出版社,20043 许发樾.模具设计与制造简明手册M.第1版.北京:机械工业出版社,20004 陈万林,姜彤,陈集,陈涛等.实用模具技术M.第1版.北京:机械工业出版社,20015 洪慎章.模具工业的发展趋势及塑性成形技术的研究方向J.模具制造.2002,20(12):136 许发樾.模具常用机构设计M.第1版.北京:机械工业出版社,2003 7 郝滨海.冲压模具简明设计手册M.第1版.北京:化学工业出版社,20058 薛啟翔.冲压模具设计结构图册M.第1版.北京:化学工业出版社,20059 窦智.级进模设计中的要点及生产中的故障排除J.模具制造.2005,47(03):313310 屈振生.机械图学M.沈阳:东北大学出版社,2000 11 李学锋.模具设计与制造实训教程M.第1版.北京:化学工业出版社,200512 许发樾.冲模设计应用实例M.第1版.北京:机械工业出版社,200013 Michael Korneli, Contributing Writer. Designing progressive dies.2001 /ToolandDie/ToolandDie_Article.cfm?ID=229附录A级进模的设计当设计级进模加工工件时,必须有构思折中。首先了解一下程序细节会对你有所帮助。是否用连续生产一种零件取决于两个因素:产品的尺寸值和零件的复杂程度。这两个因素是设计的仪器性和加工的难度。记录所有影响零件质量预期水平、工具维护和使用寿命的因素是非常重要的。送料移动也是达到要求所必须的,并且会影响加工花费。工件定位第一步骤是决定工件怎样通过模具。这个由工件的性质和定位公差值决定。然后,开始送料移位。让材料得到最佳利用也许需要在加工过程中旋转工件,这会改变工件钢材的纹理方向也会因此改变工件任意形式的强度。纹理的形成可能引起金属疲劳和断裂,还会使拐角形成更加困难。因此,结构形式也会深受分子化学组成问题的影响。一个即将加工成计算机工业零件的条料被旋转,达到形成由两不同纹理挤压成的角。依据形式决定工件的尺寸以及公差值0.025mm。旋转条料用来使组织形式更坚固,而不是最有效的利用材料。如此一来,保证工件公差优于有效利用材质。工件的结构提供了工件旋转的第二个动力。如果需要凸轮形成或者穿孔连续加工,旋转工件是最好的,有时也是唯一的选择,因为凸轮和驱动可能会占用大半个房间。典型工件需要旋转以达到和圈料垂直的性质。这也提供了最简单并且最容易达到的形成凸轮的条件。通常,旋转工件以最好的利用材料和挤压凸轮以保证他们在盘绕卷之外这两种方法的折中是最终的结果。这样可能增加单个工件和加工花费。为了能连续制造工件,这种折中是必须的。第三种看法是之所以需要在条料中旋转工件是由于让条料通过模具是必要的。推力有时可能被适当的工件旋转同步消除。在同一方向上任何形式的零件,应力都可能通过向上成型消除。这样通常会增加模具的成本。当工件在反方向上成型时,多余的推力,材料的浪费,加工的复杂性和成本都会增加加工时的花费。工件被阶梯形运输带运输,运输带在圈料周围运输材料,因为只有两个小地方可以运输工件。也由于成品的形状和长度,一定程度的推力是必须的。外部提料件运输阶梯条料在高位安然工作。最后一个考虑是工件在条料上的定位是,工件应该旋转来让用料尽可能短。这个尤其适用于比较重的材料和窄的圈料。裂缝过程可能引起圈料弯曲,而使运输困难。较短的运输工序进行较快,并且少有机会引起运输问题。当工件长度和宽度本质上的不同存在时,通常采用短程导料加工是更物有所值。运输工件工件在条料上的运输方法影响模具的运输,条料提升的能力,和生产高质量工件的能力。尽管许多方法都可用,但只有三个基本运输工件的选择是可行的。在最接近垂直的地方,工件被周围废料围绕。多余的许清理的材料每边等于一个或两个材料厚度。某些工件结构需要用这种方法。当工件旋转时,工件必须在级进导料中有足够的可用空间。当选择这种运输时,在模具中提升条料可能变的困难。条料边缘的导料板不充足维持平衡或者运输平衡的导料板是所需的,或者在模具中运输条料可能也会成问题。如果大量凸缘需要形成,要达到适合的提升是很难的。这种运输形式可能引起另外一种运输问题。卷料边缘的大量清理可能引起条料的弯曲就像在钢材上撤消压力一样。模具中有越多的工序,就会有更多的运输和提升问题由弯曲引起。工件结构,材料厚度和运输所需窄度是决定弯曲是否是成为问题的因素。为了防止弯曲,卷料宽度应该增加,以至于卷料的运输边可以被清理。在卷料相反边缘额外的清理会释放压力,条料一方的工件运输可能最大限度影响材料利用率。第三种运输方案是阶梯运输。阶梯式运输的优势在前面已经讨论过了。这些运输工具把复杂工件以及所许的大幅度提升工作做的很好。因为这种方法允许调料简易运输,他也经常被用于需要高运输效率的地方。阶梯运输对每个工件用料更多。尽管这样,工件一般来说是不能被连续生产的。如果产品值是连续监工的开端,更复杂工序模具和额外的材料浪费所增加的花费或许会使多项操作加工工件成为一个更好的选择。排样工件旋转和运输方式的确定必须用第三个考虑因素同时进行考虑,排样。形式,定位,和排样次数都会影响到工序,卷料和运输方式。由检查工件结构和公差需求来开始排样。在工件内冲孔排样是否可能和被人接受呢?如果一个工件包含孔,如果需要用工件做标准件,工件必须足够大。孔应该空留尽可能大的长度帮助提高精确度,而且如果他们是用来固定条料的话他们必须在合适的位置并且帮助在模具内成型。所要冲的工件孔公差应该考虑。如果孔直径公差非常小,甚至在成型过程中有轻微延长也会产生费件。延长可能由一些如旧送料板或者调节轻微脱离这样简单的事引起。如果一个工件定位在费料或者运输器上,轻微的延长是可以接受的,只要单个工件尺寸仍然在公差范围内。有时,工件或许需要定位在两个不同的位置。在这些应用中,这工件的两个定位应该同时被冲出以提供从第一个定位到第二个的精确转换。当大量条料行程在具内,问题就会出现。导料板想连接条料一样连接材料。如果考虑条料行程在内,销钉会摩擦销钉孔,也会因此引起定位的困难。最好的解决方式是导出条料并且安置销钉在条料上。导出模具决定工件如何从模具中导出通常要看设计的最后。尽管如此,有时这也是决定模具设计的关键因素。从模具中移动工件需要旋转工件,用不同形式的运输器,或者改变模具内的操作次序。工件成型的定位被直接运输依赖于工件怎样从模具中移出或是否从模具中移出。阶梯形条料提供了从模具中移出的最简单的方法。通常,工件可以切削并且切割模具。当模具被设计出来以至于工件被切并且允许落料,有几个因素必须考虑。例如,工件重量必须足够保持平衡以允许模块落料。圆锥销钉能被加在条料上以确保工件在模内位置。如果成品内部或边缘已经过成型加工,清除必须要做。如果不可能,重新设计模具以保证工件的完成。如果边缘向上形成,条料的前进有时会把工件挤出模具。确定工序数一旦基本设计决定了,工序的位置就能被估计到。让模具结构形成脑中是非常重要的。经常,空位应该被包含来防止模具受损,如果有必要进行更多的修正。除此之外,保养工具的方法应该记住。随着工具复杂性的增加,设计中自信的程度也在决定工序数过程中起很重要的作用。如果问题出现在工件是否被合理绘制或者成品按要求出现,一个或多个空位应该加上未定因素越多,应该加的空位就越多。如果模具在没有空位情况下建立并且额外的操作需要加入,选择就几乎没有了。在几乎所有这样的离子中,模具的整体必须拆除来容纳修改。经常,非常不希望保持的条件一定会建入模具中。每种形式可能导致生产会破坏的模具是值得保持的。结论 获得原理正确是生产品质,经济影响模和单件的重点。模具越复杂,基础就越重要。通过合适的评估,最佳方案才能一直选择。传动模具很容易被保养。模具会生产一直的,高质量零件来印。合适的决定应该给公司刀具提供最好的参数值。附录BDesigning progressive diesDecisions and compromises must be made when designing progressive dies to produce a part. Knowing ahead of time what this process entails just might help you.The decision to produce a part progressively is usually determined by two factors: the volume of production and the complexity of the part. These two factors are instrumental in the design and construction of the tooling. It is important to address all factors that will contribute to the desired level of part quality, tool maintenance, and tooling life. Trade-offs will be necessary to reach most decisions, and all will affect tooling costs.Part OrientationThe process begins with determining how the part will be run through the die. This is governed by the features of the part and the locations of the datums and critical tolerances. Then, the trade-offs begin.Optimizing material usage may require rotating the part in the strip, which changes the grain direction of the steel in the part and thus can affect the strength of any forms in the part. Forming with the grain can cause cracking and fatiguing of the metal and make holding consistent form angles more difficult. Therefore, the form will be far more susceptible to problems associated with the chemical makeup of each coil that is run.For example, a part for the computer industry that was rotated in the strip to guard against inconsistent form angles that could be caused by differences between coils. The part contained critical dimensions with 0.025-millimeter tolerances dependent on the forms. Rotating the strip to ensure more consistent forms was not the most efficient use of material. In this case, however, part tolerances won out over optimizing material usage.Part configuration could provide a second motivation for rotating a part in the strip. If cam forming or piercing is required to make the part progressively, rotating the part may be the best, and sometimes only, option because the cam and driver can take up a significant amount of room. The part typically is rotated so that the cams functions are perpendicular to the coil. This provides the easiest and most accessible condition for the cams.Often, a compromise between rotating a part to optimize material usage and angling the cams to keep them outside of the coil is the final result. This could increase piece part and tooling costs. To produce the part progressively, however, such a compromise may be necessary.A third consideration that may require rotating the part in the strip is the amount of lift that is needed to carry the strip through the die. Lift can sometimes be reduced significantly or eliminated by properly rotating a part.If all forms in a part are in the same direction, lift can be eliminated by forming upward. This usually adds to the cost of the die. When the part has forms in opposite directions, compromises must be made among excessive lift, poor material use, and the complexity and cost of the tooling. The part is carried through with a ladder-style carrier, which adds material to the coil width because only two small areas are available for carrying the part. Also, because of the shape and length of the forms, a significant amount of lift is needed. External stock lifters carrying the ladder strip work well in high-lift situations.One final consideration for part orientation within the strip is that a part should be rotated so that the feed is as short as possible. This is especially true for heavier materials and narrow coils. The slitting process can cause camber in coils that can make feeding difficult. A shorter progression feed runs faster and has less chance to cause feed problems. When a substantial difference between the length and width of the part exists, it is usually more cost-effective to build the tooling with the shorter lead. Carrying the PartHow parts are carried in the strip affects how well the die feeds, the ability to lift the strip for feeding, and the ability to produce consistent-quality parts.Three basic options are available for carrying a part, although many variations of each also can be used. In the most straightforward approach, parts are carried by the scrap between them. Excess material equal to one to two material thicknesses per side is required for trimming. This method typically produces minimal scrap.Certain part configurations are needed to use this method. When rotated and laid out end to end, the parts must have enough usable area on both the leading and trailing edges of the progression The second basic strip option, in which a part is carried on one side of the strip.This style is suitable for parts that require a great deal of forming on as many as three sides. It also improves accessibility if cam piercing or forming is required.Lifting the strip through the die can become more difficult when this carrier option is used. A stock lifter on the edge of the strip is not sufficientlifters are needed in the center of the strip for balancing, or feeding the strip through the die can become a problem. If large or numerous flanges are to be formed down, achieving the proper lift can be difficult.This type of carrier can cause another feeding problem. Trimming a large quantity of material from one side of the coil can cause camber in the strip as stresses are released from the steel. The more progressions in a die, the greater is the risk of feed and pilot alignment problems caused by camber.Part configuration, stock material thickness, and how narrow the carrier must be are all factors that influence whether camber becomes a problem. To prevent camber, the coil width should be increased so that the carrier side of the coil also can be trimmed. The additional trim releases stresses from the opposite side of the coil and balances the strip. Even with the additional trim, carrying the part on one side of the strip can be the most effective method to run a part from a material usage standpoint.The third carrier option is the ladder style. Some of the advantages of the ladder carrier were discussed earlier. These carriers work well with complex parts and with those requiring significant amounts of lift. Because this method allows a strip to feed easily, it also is often used in applications in which higher feed rates are needed.The ladder carrier uses more material per part. Often, however, a part cannot be produced progressively any other way. If production volumes are borderline to begin with in terms of justifying progressive tooling, the added costs of the more complex progressive die and additional material waste may make producing the part through multiple operations a better option.Piloting Decisions on part rotation and carrier type must be made concurrently with a third consideration, piloting. The type, locations, and number of pilots all affect the progression, coil, and carrier type.Choosing pilots begins with examining the part configuration and tolerance requirements. Is piloting off of holes within the part possible or even acceptable? If a part contains holes, they must be large enough if they are to be used as pilots. Holes should be spaced as far apart as possible to help increase accuracy, and they must be in the proper locations if they are used to stabilize a strip and help with the forming taking place in the die.The tolerances of the proposed pilot holes in the part should be considered. If the hole diameter tolerance is very tight, even slight elongations caused during forming may produce scrap parts. Elongation could be caused by something as simple as an old feeder or one that is slightly out of adjustment. If a pilot is located in the scrap or the carrier, slight elongation is acceptable, as long as the piece part dimensions remain within tolerance.At times, two different sets of pilots may be required. In these applications, both sets of pilots should be pierced at the same time to provide an accurate transition from the first set of
- 温馨提示:
1: 本站所有资源如无特殊说明,都需要本地电脑安装OFFICE2007和PDF阅读器。图纸软件为CAD,CAXA,PROE,UG,SolidWorks等.压缩文件请下载最新的WinRAR软件解压。
2: 本站的文档不包含任何第三方提供的附件图纸等,如果需要附件,请联系上传者。文件的所有权益归上传用户所有。
3.本站RAR压缩包中若带图纸,网页内容里面会有图纸预览,若没有图纸预览就没有图纸。
4. 未经权益所有人同意不得将文件中的内容挪作商业或盈利用途。
5. 人人文库网仅提供信息存储空间,仅对用户上传内容的表现方式做保护处理,对用户上传分享的文档内容本身不做任何修改或编辑,并不能对任何下载内容负责。
6. 下载文件中如有侵权或不适当内容,请与我们联系,我们立即纠正。
7. 本站不保证下载资源的准确性、安全性和完整性, 同时也不承担用户因使用这些下载资源对自己和他人造成任何形式的伤害或损失。

人人文库网所有资源均是用户自行上传分享,仅供网友学习交流,未经上传用户书面授权,请勿作他用。