拨叉831008零件工艺及钻Φ20孔夹具设计【14张图纸】【优秀】
收藏
资源目录
压缩包内文档预览:
编号:271425
类型:共享资源
大小:695.05KB
格式:RAR
上传时间:2014-04-05
上传人:上***
认证信息
个人认证
高**(实名认证)
江苏
IP属地:江苏
40
积分
- 关 键 词:
-
拨叉831008
零件
工艺
20
夹具
设计
- 资源描述:
-
拨叉831008零件工艺及钻Φ20孔夹具设计
27页 11000字数+说明书+工艺过程卡+工序+任务书+14张CAD图纸
任务书.doc
夹具1.dwg
夹具2.dwg
夹具3.dwg
工序1.dwg
工序2.dwg
工序3.dwg
工序4.dwg
工序5.dwg
工序6.dwg
工序7.dwg
工艺过程卡.dwg
拨叉831008零件工艺及钻Φ20孔夹具设计说明书.doc
钻Φ20孔夹具装配图.dwg
零件图831008.dwg
零件毛坯图.dwg
目 录
1 绪论1
2 数控加工工艺概述1
2.1 数控加工工艺分析的一般步骤与方法1
2.2 机床的合理选用1
2.3 数控加工零件工艺性分析2
2.3.1 零件图样上尺寸数据的给出应符合编程方便的原则2
2.3.2 零件各加工部位的结构工艺性应符合数控加工的特点2
2.4 加工方法的选择与加工方案的确定2
2.4.1 加工方法的选择2
2.4.2 加工方案确定的原则3
2.5 工序与工步的划分及加工顺序安排3
2.5.1?工序的划分3
2.5.2 工步的划分3
2.5.3 加工顺序安排4
2.6 零件的安装与夹具的选择4
2.6.1 定位安装的基本原则4
2.6.2 选择夹具的基本原则4
2.7 刀具的选择与切削用量的确定4
2.7.1 刀具的选择4
2.7.2 切削用量的确定5
2.8 对刀点与换刀点的确定5
2.9 加工路线的确定5
3 拨叉零件数控加工工艺分析6
3.1 拨叉零件的作用6
3.2 拨叉零件的工艺分析7
3.3 确定拨叉零件生产类型7
3.4 确定拨叉零件毛坯类型7
3.4.1 确定毛坯种类7
3.4.2 确定铸件加工余量及形状7
3.4.3 绘制铸件零件图8
3.5 拨叉零件数控加工工艺规程设计8
3.5.1 选择定位基准8
3.5.2 制定数控加工工艺路线8
3.6 机械加工余量、工序尺寸及公差的确定9
3.6.1 圆柱表面工序尺寸9
3.6.2 平面工序尺寸10
3.6.3 确定切削用量及时间定额10
4 夹具设计19
4.1 问题的提出19
4.2 夹具设计19
4.2.1 定位基准选择19
4.2.2切削力及夹紧力计算20
4.3定位误差分析20
4.3.1定位元件尺寸及公差的确定20
4.3.2计算钻套中心线与工作台的垂直度误差20
4.3.3计算定位销轴与工作台的平行度误差21
4.4夹具设计及操作的简要说明21
5结束语23
致谢24
参考文献25
拨叉零件的工艺分析
零件的材料HT200其生产工艺简单,铸造性能优良,但塑性较差、脆性高,不适合磨削。以下是拨叉需要加工的表面及加工表面之间的位置要求:
(1)小头孔Φ20以及与此孔相通的Φ8的锥孔、M6螺纹孔。
(2)大头半圆孔Φ50。
(3)拨叉底面、小头孔端面、大头半圆孔端面,大头半圆孔两端面与小头孔中心线的垂直度误差为0.07mm,小头孔上端面与其中心线的垂直度误差为0.05mm。
分析可知,可以粗加工拨叉下端面,然后以此作为基准采用专用夹具进行加工,并且保证位置精度要求。由于拨叉零件的加工工序较多,形状较复杂,考虑到工序集中所以采用数控机床来进行加工。
3.3 确定拨叉零件生产类型
已知此拨叉零件的生产纲领为5000件/年,零件的质量是1.0Kg/个,查《机械制造工艺设计简明手册》第2页表1.1-2,可确定该拨叉生产类型为中批生产,所以初步确定工艺安排为:加工过程划分阶段;工序适当集中;加工设备以数控机床为主,大量采用专用工装。
3.4 确定拨叉零件毛坯类型
3.4.1 确定毛坯种类
零件材料为HT200。考虑零件在机床运行过程中所受冲击不大,零件结构又比较简单,生产类型为中批生产,故选择木摸手工砂型铸件毛坯。查《机械制造工艺设计简明手册》第41页表2.2-5,选用铸件尺寸公差等级为CT-12。
3.4.2 确定铸件加工余量及形状
查《机械制造工艺设计简明手册》第41页表2.2-5,选用加工余量为MA-H级,并查表2.2-4确定各个加工面的铸件机械加工余量,铸件的分型面的选用及加工余量,如下表所示:
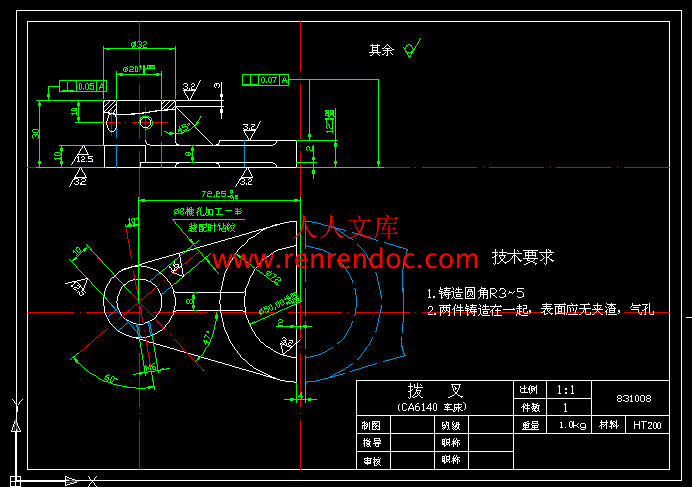
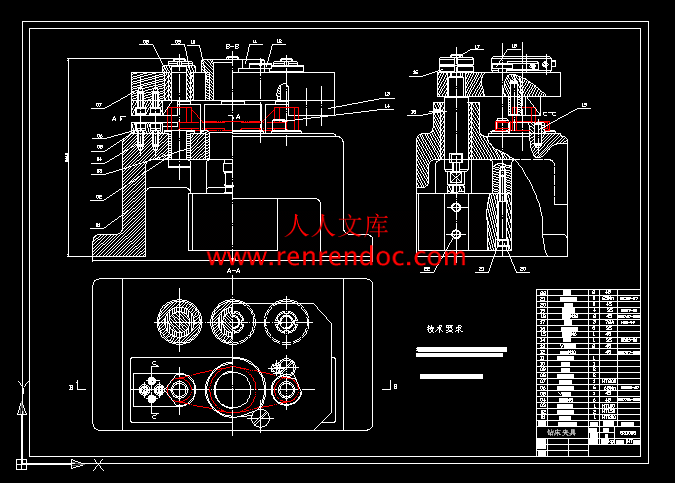
- 内容简介:
-
机械设计制造及其自动化专业机械制造技术课程设计任务书班级_09机自5班 姓名 丁杭杭 学号 091280507 指导教师_常秋香 朱火美 课题名称设计时间起始时间 2012 年11 月2 日完成时间2012 年11 月23日原始技术条件1、 拔叉零件图样,每台产品 拔叉 零件的数量为 5000件。2、产品的生产纲领 10000件 /年, 拔叉 零件备品率为 ,废品率为 5 。3、毛坯为外协件,生产条件根据需要确定。4、由机加车间负责生产。设计工作量1、绘制零件图1张。2、绘制毛坯图1张。3、编制机械加工工艺规程卡片(工艺过程卡片和工序卡片)1套。4、绘制指导教师指定的具体工序的夹具装配总图1张和本套夹具中的主要零件图2张。5、撰写设计说明书1份。参考资料1.机械制造技术基础教材 2机械制造技术基础课程设计教材3机械制造工艺手册手册 4.其他相关书籍工作进度1、零件图的工艺分析及绘制、毛坯的选择及毛坯图的绘制。 1.5天2、选择定位基准、选择各表面的加工方法和加工方案、安排 1.5天加工顺序,划分加工阶段、制订工艺路线、选择机床及工艺装备。 3、加工余量及工序间尺寸与公差的确定、切削用量和时间 2天定额的确定、填写机械加工工艺过程卡和工序卡。 4、确定夹具设计方案,绘制结构原理示意图; 4天 5、计算夹紧力;绘制夹具装配图和零件图。 4天6、编写整理设计说明书 2天教研室意见1目目 录录1 绪论.12 数控加工工艺概述.12.1 数控加工工艺分析的一般步骤与方法.12.2 机床的合理选用.12.3 数控加工零件工艺性分析.22.3.1 零件图样上尺寸数据的给出应符合编程方便的原则.22.3.2 零件各加工部位的结构工艺性应符合数控加工的特点.22.4 加工方法的选择与加工方案的确定.22.4.1 加工方法的选择.22.4.2 加工方案确定的原则.32.5 工序与工步的划分及加工顺序安排.32.5.1 工序的划分.32.5.2 工步的划分.32.5.3 加工顺序安排.42.6 零件的安装与夹具的选择.42.6.1 定位安装的基本原则.42.6.2 选择夹具的基本原则.42.7 刀具的选择与切削用量的确定.42.7.1 刀具的选择.42.7.2 切削用量的确定.52.8 对刀点与换刀点的确定.52.9 加工路线的确定.53 拨叉零件数控加工工艺分析.63.1 拨叉零件的作用.63.2 拨叉零件的工艺分析.73.3 确定拨叉零件生产类型.73.4 确定拨叉零件毛坯类型.73.4.1 确定毛坯种类.73.4.2 确定铸件加工余量及形状.73.4.3 绘制铸件零件图.83.5 拨叉零件数控加工工艺规程设计.83.5.1 选择定位基准.83.5.2 制定数控加工工艺路线.83.6 机械加工余量、工序尺寸及公差的确定.93.6.1 圆柱表面工序尺寸.93.6.2 平面工序尺寸.103.6.3 确定切削用量及时间定额.104 夹具设计.194.1 问题的提出.194.2 夹具设计.1924.2.1 定位基准选择.194.2.2 切削力及夹紧力计算.204.3 定位误差分析.204.3.1 定位元件尺寸及公差的确定.204.3.2 计算钻套中心线与工作台的垂直度误差.204.3.3 计算定位销轴与工作台的平行度误差.214.4 夹具设计及操作的简要说明.215 结束语.23致谢.24参考文献.251 绪论绪论随着我国现代制造技术的发展,数控机床的普及和从事数控加工人员的增多,数控加工越来越受到人们的重视。拨叉零件广泛应用于我们的日常生活及生产当中,拨叉零件的制造精度能不能够满足技术要求,如何更大限度的降低机加工的基本劳动时间及提高单位时间内的生产率,都成为机械行业势待解决的技术性问题。随着数控技术的不断发展及数控技术应用的不断广泛化、深入化,我们意识到,采用数控机床来加工拨叉零件既能够提高零件的精度又能够完成采用普通机床加工应运受限的瓶颈,对提高加工效率、以及降低劳动强度都有不可估量之好处。随着计算机科学、信息技术的迅速发展,传统的制造业已发生了十分显著的变化,发达国家正进行由传统的制造技术向现代制造技术的转变,并提出了全新的制造模式。数控加工技术将逐步引航现代机械制造业的发展。数控机床的应用范围日益扩大,其产生的经济效益与社会效益十分明显。对传统零件的数控加工技术也得到越来越广泛的应用。面对新技术、新工艺的不断出现,提高数控加工技术在传统拨叉类零件的应用也受到越来越多的重视。如何使数控技术在加工这一类零件中表现出其高质量、高精度、高效率,都成为各国争先要解决的问题。因此研究它对我国的制造行业很有借鉴作用。2 数控加工工艺概述数控加工工艺概述2.1 数控加工工艺分析的一般步骤与方法数控加工工艺分析的一般步骤与方法 工作人员在进行工艺分析时,要有机床说明书、编程手册、切削用量表、标准工具、夹具手册等资料,根据被加工工件的材料、轮廓形状、加工精度等3选用合适的机床,制定加工方案,确定零件的加工顺序,各工序所用刀具,夹具和切削用量等。 2.2 机床的合理选用机床的合理选用在数控机床上加工零件时,一般有两种情况。第一种情况:有零件图样和毛坯,要选择适合加工该零件的数控机床。第二种情况:已经有了数控机床,要选择适合在该机床上加工的零件。无论哪种情况,考虑的因素主要有,毛坯的材料和类、零件轮廓形状复杂程度、尺寸大小、加工精度、零件数量、热处理要求等。概括起来有三点:(1)要保证加工零件的技术要求,加工出合格的产品;(2)有利于提高生产率;(3)尽可能降低生产成本(加工费用)。2.3 数控加工零件工艺性分析数控加工零件工艺性分析数控加工工艺性分析涉及面很广,在此仅从数控加工的可能性和方便性两方面加以分析。2.3.1 零件图样上尺寸数据的给出应符合编程方便的原则零件图样上尺寸数据的给出应符合编程方便的原则(1)零件图上尺寸标注方法应适应数控加工的特点在数控加工零件图上,应以同一基准引注尺寸或直接给出坐标尺寸。在保持设计基准、工艺基准、检测基准与编程原点设置的一致性方面带来很大方便。由于零件设计人员一般在尺寸标注中较多地考虑装配等使用特性方面,而不得不采用局部分散的标注方法,这样就会给工序安排与数控加工带来许多不便。由于数控加工精度和重复定位精度都很高,不会因产生较大的积累误差而破坏使用特性,因此可将局部的分散标注法改为同一基准引注尺寸或直接给出坐标尺寸的标注法。(2)构成零件轮廓的几何元素的条件应充分。在分析零件图时,要分析几何元素的给定条件是否充分。如圆弧与直线,圆弧与圆弧在图样上相切,但根据图上给出的尺寸,在计算相切条件时,变成了相交或相离状态。由于构成零件几何元素条件的不充分,使编程时无法下手。遇到这种情况时,应与零件设计者协商解决。2.3.2 零件各加工部位的结构工艺性应符合数控加工的特点零件各加工部位的结构工艺性应符合数控加工的特点(1)零件的内腔和外形最好采用统一的几何类型和尺寸。这样可以减少刀具规格和换刀次数,使编程方便,生产效益提高。4(2)内槽圆角的大小决定着刀具直径的大小,因而内槽圆角半径不应过小。零件工艺性的好坏与被加工轮廓的高低、转接圆弧半径的大小等有关。(3)零件铣削底平面时,槽底圆角半径 r 不应过大。(4)应采用统一的基准定位。在数控加工中,若没有统一基准定位,会因工件的重新安装而导致加工后的两个面上轮廓位置及尺寸不协调现象。因此要避免上述问题的产生,保证两次装夹加工后其相对位置的准确性,应采用统一的基准定位。零件上最好有合适的孔作为定位基准孔,若没有,要设置工艺孔作为定位基准孔。若无法制出工艺孔时,最起码也要用经过精加工的表面作为统一基准,以减少两次装夹产生的误差。此外,还应分析零件所要求的加工精度、尺寸公差等是否可以得到保证、有无引起矛盾的多余尺寸或影响工序安排的封闭尺寸等。2.4 加工方法的选择与加工方案的确定加工方法的选择与加工方案的确定2.4.1 加工方法的选择加工方法的选择加工方法的选择原则是保证加工表面的加工精度和表面粗糙度的要求。由于获得同一级精度及表面粗糙度的加工方法一般有许多,因而在实际选择时,要结合零件的形状、尺寸大小和热处理要求等全面考虑。例如,对于 IT7 级精度的孔采用镗削、铰削、磨削等加工方法均可达到精度要求,但箱体上的孔一般采用镗削或铰削,而不宜采用磨削。一般小尺寸的箱体孔选择铰孔,当孔径较大时则应选择镗孔。此外,还应考虑生产率和经济性的要求,以及工厂的生产设备等实际情况。常用加工方法的经济加工精度及表面粗糙度可查阅有关工艺手册。2.4.2 加工方案确定的原则加工方案确定的原则零件上比较精密表面的加工,常常是通过粗加工、半精加工和精加工逐步达到的。对这些表面仅仅根据质量要求选择相应的最终加工方法是不够的,还应正确地确定从毛坯到最终成形的加工方案。确定加工方案时,首先应根据主要表面的精度和表面粗糙度的要求,初步确定为达到这些要求所需要的加工方法。例如,对于孔径不大的 IT7 级精度的孔,最终加工方法取精铰时,则在精铰孔前通常要经过钻孔、扩孔和粗铰孔等加工。2.5 工序与工步的划分及加工顺序安排工序与工步的划分及加工顺序安排2.5.1 工序的划分工序的划分5在数控机床上加工零件,工序可以比较集中,在一次装夹中尽可能完成大部分或全部工序。首先应根据零件图样,考虑被加工零件是否可以在一台数控机床上完成整个零件的加工工作,若不能则应决定其中哪一部分在数控机床上加工,哪一部分在其他机床上加工,即对零件的加工工序进行划分。一般工序划分有以下几种方式:(1)以一次安装、加工作为一道工序。(2)以同一把刀具加工的内容划分工序。(3)以加工部位划分工序。(4)以粗、精加工划分工序。2.5.2 工步的划分工步的划分工步的划分主要从加工精度和效率两方面考虑。在一个工序内往往需要采用不同的刀具和切削用量,对不同的表面进行加工。为了便于分析和描述较复杂的工序,在工序内又细分为工步。下面以加工中心为例来说明工步划分的原则:(1)同一表面按粗加工、半精加工、精加工依次完成,或全部加工表面按先粗后精加工分开进行。(2)对于既有铣面又有镗孔的零件,可先铣面后镗孔。(3)按刀具划分工步。 总之,工序与工步的划分要根据具体零件的结构特点、技术要求等情况综合考虑。2.5.3 加工加工顺序安排顺序安排顺序的安排应根据零件的结构和毛坯状况,以及定位、安装与夹紧的需要来考虑。顺序安排一般应按以下原则进行: (1)上道工序的加工不能影响下道工序的定位与夹紧,中间穿插有通用机床加工工序的也应综合考虑; (2)先进行内腔加工,后进行外形加工; (3)以相同定位、夹紧方式加工或用同一把刀具加工的工序,最好连续加工,以减少重复定位次数、换刀次数与挪动压板次数;2.6 零件的安装与夹具的选择零件的安装与夹具的选择2.6.1 定位安装的基本原则定位安装的基本原则(1)力求设计、工艺与编程计算的基准统一。6(2)尽量减少装夹次数,尽可能在一次定位装夹后,加工出全部待加工表面。(3)避免采用占机人工调整式加工方案,以充分发挥数控机床的效能。2.6.2 选择夹具的基本原则选择夹具的基本原则数控加工的特点对夹具提出了两个基本要求:一是要保证夹具的坐标方向与机床的坐标方向相对固定;二是要协调零件和机床坐标系的尺寸关系。除此之外,还要考虑以下四点:(1)当零件加工批量不大时,应尽量采用组合夹具、可调式夹具及其他通用夹具,以缩短生产准备时间、节省生产费用。(2)在成批生产时才考虑采用专用夹具,并力求结构简单。(3)零件的装卸要快速、方便、可靠,以缩短机床的停顿时间。(4)夹具上各零部件应不妨碍机床对零件各表面的加工,即夹具要开敞其定位、夹紧机构元件不能影响加工中的走刀(如产生碰撞等)。2.7 刀具的选择与切削用量的确定刀具的选择与切削用量的确定2.7.1 刀具的选择刀具的选择刀具的选择是数控加工工艺中重要内容之一,它不仅影响机床的加工效率,而且直接影响加工质量。编程时,选择刀具通常要考虑机床的加工能力、工序内容、工件材料等因素。与传统的加工方法相比,数控加工对刀具的要求更高。不仅要求精度高、刚度好、耐用度高,而且要求尺寸稳定、安装调整方便。这就要求采用新型优质材料制造数控加工刀具,并优选刀具参数。 2.7.2 切削用量的确定切削用量的确定切削用量包括主轴转速(切削速度)、背吃刀量、进给量。对于不同的加工方法,需要选择不同的切削用量,并应编入程序单内。合理选择切削用量的原则是,粗加工时,一般以提高生产率为主,但也应考虑经济性和加工成本;半精加工和精加工时,应在保证加工质量的前提下,兼顾切削效率、经济性和加工成本。具体数值应根据机床说明书、切削用量手册,并结合经验而定。2.8 对刀点与换刀点的确定对刀点与换刀点的确定7在编程时,应正确地选择“对刀点”和“换刀点”的位置。“对刀点”就是在数控机床上加工零件时,刀具相对于工件运动的起点。由于程序段从该点开始执行,所以对刀点又称为“程序起点”或“起刀点”。对刀点的选择原则是:(1)所选的对刀点应使程序编制简单;(2)对刀点应选择在容易找正、便于确定零件加工原点的位置;(3)对刀点应选在加工时检验方便、可靠的位置;(4)对刀点的选择应有利于提高加工精度。加工过程中需要换刀时,应规定换刀点。所谓“换刀点”是刀架转位换刀时的位置。该点可以是某一固定点(如加工中心机床,其换刀机械手的位置是固定的),也可以是任意的一点(如车床)。换刀点应设在工件或夹具的外部,以刀架转位时不碰工件及其它部件为准。其设定值可用实际测量方法或计算确定。、 2.9 加工路线的确定加工路线的确定在数控加工中,刀具刀位点相对于工件运动的轨迹称为加工路线。编程时,加工路线的确定原则主要有以下几点:(1)加工路线应保证被加工零件的精度和表面粗糙度,且效率较高。(2)使数值计算简单,以减少编程工作量。(3)应使加工路线最短,这样既可减少程序段,又可减少空刀时间。 如加工图 a 所示零件上的孔系。b 图的走刀路线为先加工完外圈孔后,再加工内圈孔。若改用 c 图的走刀路线,减少空刀时间,则可节省定位时间近一倍,提高了加工效率。 a)零件图样 b)路线 1 c)路线 2图 1 最短走刀路线的设计3 拨叉零件数控加工工艺分析拨叉零件数控加工工艺分析3.1 拨叉零件的作用拨叉零件的作用8图 2 拨叉零件图图 2 是 CA6140 车床上的拨叉零件,它位于车床变速机构中,主要起换档,使主轴回转运动按照工作者的要求工作,获得所需的速度和扭矩的作用。零件上方的 20 孔与操纵机构相连,二下方的 50 半孔则是用于与所控制齿轮所在的轴接触。通过上方的力拨动下方的齿轮变速。两件零件铸为一体,加工时分开。3.2 拨叉零件的工艺分析拨叉零件的工艺分析零件的材料 HT200 其生产工艺简单,铸造性能优良,但塑性较差、脆性高,不适合磨削。以下是拨叉需要加工的表面及加工表面之间的位置要求:(1)小头孔 20 以及与此孔相通的 8 的锥孔、M6 螺纹孔。(2)大头半圆孔 50。(3)拨叉底面、小头孔端面、大头半圆孔端面,大头半圆孔两端面与小头孔中心线的垂直度误差为 0.07mm,小头孔上端面与其中心线的垂直度误差为0.05mm。9分析可知,可以粗加工拨叉下端面,然后以此作为基准采用专用夹具进行加工,并且保证位置精度要求。由于拨叉零件的加工工序较多,形状较复杂,考虑到工序集中所以采用数控机床来进行加工。3.3 确定拨叉零件生产类型确定拨叉零件生产类型已知此拨叉零件的生产纲领为 5000 件/年,零件的质量是 1.0Kg/个,查机械制造工艺设计简明手册第 2 页表 1.1-2,可确定该拨叉生产类型为中批生产,所以初步确定工艺安排为:加工过程划分阶段;工序适当集中;加工设备以数控机床为主,大量采用专用工装。3.4 确定拨叉零件毛坯类型确定拨叉零件毛坯类型3.4.1 确定毛坯种类确定毛坯种类零件材料为 HT200。考虑零件在机床运行过程中所受冲击不大,零件结构又比较简单,生产类型为中批生产,故选择木摸手工砂型铸件毛坯。查机械制造工艺设计简明手册第 41 页表 2.2-5,选用铸件尺寸公差等级为 CT-12。3.4.2 确定铸件加工余量及形状确定铸件加工余量及形状查机械制造工艺设计简明手册第 41 页表 2.2-5,选用加工余量为 MA-H 级,并查表 2.2-4 确定各个加工面的铸件机械加工余量,铸件的分型面的选用及加工余量,如下表所示:表 1 各加工表面的加工余量简 图加工面代号基本尺寸加工余量等级加工余量说 明D120H1.02 孔降一级双侧加工D250H3.52孔降一级双侧加工T230H5单侧加工T312H5单侧加工T412H5单侧加工3.4.3 绘制铸件零件图绘制铸件零件图10图 3 拨叉毛坯图3.5 拨叉零件数控加工工艺规程设计拨叉零件数控加工工艺规程设计3.5.1 选择定位基准选择定位基准(1)粗基准的选择:以零件的小头上端面为主要的定位粗基准,以两个小头孔外圆表面为辅助粗基准。(2)精基准的选择:考虑要保证零件的加工精度和装夹准确方便,依据“基准重合”原则和“基准统一”原则,以粗加工后的底面为主要的定位精基准,以两个小头孔外圆柱表面为辅助的定位精基准。3.5.2 制定数控加工工艺路线制定数控加工工艺路线根据零件的几何形状、尺寸精度及位置精度等技术要求,以及加工方法所能达到的经济精度,在生产纲领已确定的情况下,可以考虑采用数控机床配以专用工卡具,并尽量使工序集中来提高生产率。除此之外,还应当考虑经济效果,以便使生产成本尽量下降。查机械制造工艺设计简明手册第 20 页表 1.4-7、1.4-8、1.4-11,选择零件的加工方法及工艺路线方案如下:工序 01 粗铣、精铣 20、50 下端面,以 T2 为粗基准,采用立式数控铣床加专用夹具;工序 02 粗铣、精铣 20 上端面,以 T4 为定位基准,采用立式数控铣床加专用夹具;粗铣、精铣 50 上端面,以 T4 为定位基准,采用立式数控铣床加专用夹具;工序 03 钻、扩 20 孔,粗铰、精铰 20 孔;以 32 外圆和 T2 为基准,采用立式数控钻床加专用夹具;粗镗、半精镗 50 孔,以 D1 为定位基准,采用卧式数控镗床加专用夹具;11工序 04 铣斜肩,以 D1 和 T2 为定位基准,采用立式数控铣床加专用夹具;工序 05 精铣 50 端面,以 D1 为基准,采用立式数控铣床加专用夹具;工序 06 钻、铰 8 锥孔,以 T1 和零件中线为基准,采用立式数控钻床加专用夹具;工序 07 钻 M6 底孔,攻螺纹,以 T1 和零件中线为基准,采用立式数控钻床并采用专用夹具;工序 08 铣断,以 D1 为基准,采用卧式数控铣床加专用夹具;工序 09 去毛刺;工序 10 终检。3.6 机械加工余量、工序尺寸及公差的确定机械加工余量、工序尺寸及公差的确定3.6.1 圆柱表面工序尺寸圆柱表面工序尺寸前面已初步确定工件各面的总加工余量,现在确定各工序的加工余量如下:表 2 圆柱表面加工余量工序余量加工表面加工内容加工余量精度等级工序尺寸表面粗糙度最小最大铸 件7.0CT128 . 243粗 镗4.0IT12250. 00476.30.956.850IT12(D2)半精镗3.0IT10100. 00503.22.93.25钻18IT11110. 001817.8918扩1.8IT10084. 008 .196.31.7161.910粗 铰0.14IT8033. 0094.193.20.1070.22420IT7(D1)精 铰0.06IT7021. 00201.60.0390.0933.6.2 平面工序尺寸平面工序尺寸表 3 平面加工余量工序余量工序号工序内容加工余量基本尺寸经济精度工序尺寸偏差最小最大铸 件5.0CT125 . 201粗铣 20 孔下端面4.036.01200.251.57.751202粗铣 20 孔上端面4.032.01200.251.57.7503粗铣 50 孔上端面4.014.0120180. 01.86.3807精铣 20 孔下端面1.031.080033. 00.751.28308精铣 20 孔上端面1.030.080033. 00.751.28310精铣 50 孔端面1.0212.08016. 0016. 00.9511.0163.6.3 确定切削用量及时间定额确定切削用量及时间定额工序 01 粗铣、精铣 20、50 下端面,以 T2 为粗基准,采用立式数控铣床加专用夹具(1) 粗铣 20、50 下端面,以 T2 为粗基准。1) 加工条件工件材料:HT200, b =170240MPa,铸造;工件尺寸:H=40mm,L=176mm;加工要求:粗铣 20 孔下端面,加工余量 4mm;机床:X51 立式数控铣床;刀具:YG6 硬质合金端铣刀。铣削宽度 ae90,深度 ap6,齿数 z=12,故根据机械制造工艺设计简明手册(后简称简明手册)表 3.1,取刀具直径 d0=125mm。根据切削用量手册(后简称切削手册)表 3.16,选择刀具前角 00后角 08,副后角 0=10,刃倾角:s=10,主偏角 Kr=60,过渡刃 Kr=30,副偏角 Kr=5。(2) 切削用量1) 确定切削深度 ap 因为余量较小,故选择 ap=4mm,一次走刀即可完成。2) 确定每齿进给量 fz 由于本工序为粗加工,尺寸精度和表面质量可不考虑,从而可采用不对称端铣,以提高进给量提高加工效率。根据切削手册表 3.5,使用 YG6 硬质13合金端铣刀加工,机床功率为 4.5kw(据简明手册表 4.2-35,X51 立式铣床)时:fz=0.090.18mm/z故选择:fz=0.18mm/z。3) 确定刀具寿命及磨钝标准 根据切削手册表 3.7,铣刀刀齿后刀面最大磨损量为 1.5mm;由于铣刀直径 d0=125mm,故刀具使用寿命 T=180min(据简明手册表 3.8)。4) 计算切削速度 vc 和每分钟进给量 vf根据切削手册表 3.16,当 d0=125mm,Z=12,ap7.5,fz0.18mm/z时,vt=98m/min,nt=250r/min,vft=471mm/min。各修正系数为:kMV= 1.0,kSV= 0.8。切削速度计算公式为:vpvevzvpTvvckzuayfxaqdcvvm0其中 ,mmae72mmap4245vC2 . 0qv15. 0xv35. 0yv,8 . 08 . 00 . 1kkkSvMvv2 . 0uv0pv32. 0mmin180T,将以上数据代入公式:zmmfz/18. 012Zmin/1428 . 0122 . 07235. 008. 015. 041802 . 012524532. 0mvc确定机床主轴转速: 。min/3611000rdvnwcs根据简明手册表 4.2-36,选择 nc=300r/min,vfc=390mm/min,因此实际进给量和每分钟进给量为:vc=m/min=118m/min10000nd100030012514. 3f zc=v fc/ncz=390/30012 mm/z=0.1mm/z5)校验机床功率 根据切削手册表 3.24,近似为 Pcc=3.3kw,根据机床使用说明书,主轴允许功率 Pcm=4.50.75kw=3.375kwPcc。故校验合格最终确定:ap=4.0mm,nc=300r/min,vf=390mm/s,vc=118m/min,fz=0.1mm/z。146)计算基本工时tmL/ vf,L=l+ y+,l=176mm.查切削手册表 3. 26,入切量及超切量为:y+=40mm,则:tmL/ Vf=(176+40)/390=0.81min.(2)精铣 20、50 下端面,以 T2 为粗基准。刀具:YG6 硬质合金端铣刀;机床:X51 立式数控铣床;查切削手册表 3.5,进给量为:,取为 0.5mm/rmin/0 . 15 . 0mmfz参考有关手册,确定,采用 YG6 硬质合金端铣刀,min/124mv ,则:12,125zmmdwmin/31612512410001000rdvnws现采用 X51 立式数控铣床,根据简明手册表 4.2-36,取,min/300rnw故实际切削速度:min/75.11710003001251000mndvww当时,工作台每分钟进给量:min/300rnw,取为 980mm/minmin/1800300125 . 0mmnzffwzm本工序切削时间为:min62. 0980125176222flttmm工序 02 粗铣、精铣 20 上端面,以 T4 为定位基准,采用 X51 立式数控铣床加专用夹具;粗铣、精铣 50 上端面,以 T4 为定位基准,采用 X51 立式数控铣床加专用夹具(1) 粗铣 20、50 上端面,以 T4 为定位基准。 切削用量和时间定额及其计算过程同工序 01。(2) 精铣 20 上端面,以 T1 为定位基准。切削用量同工序 01;精铣时;mmdy1250基本工时:。31. 0980125176fltmm(3)粗铣 50 上端面,以 T4 为定位基准。刀具:YG6 硬质合金端铣刀,10,400Zmmd15机床:X51 立式铣床根据切削手册查得,。根据简明手册mmazmmfpz4,/13. 0表 4.2-36 查得,取:,故实际切削速度: min/300rnwmin/7 .371000300401000mndvww当时,工作台每分钟进给量应为:min/300rnwmin/3903001013. 0mmnZffwzm查说明书,取min/400mmfm计算切削基本工时:mmyL82107272因此,min205. 039082fLtmm工序 03 钻、扩 20 孔;粗铰、精铰 20 孔;以 32 外圆和 T2 为基准;采用 Z525 立式数控钻床加专用夹具;粗镗、半精镗 50 孔,以 D1 为定位基准,采用 T616 卧式数控镗床加专用夹具(1) 钻、扩 20 孔,以 32 外圆和 T2 为基准。1) 选择钻头 根据切削手册表 2.1.2.2,选择高速钢麻花钻钻头,粗钻时 do=18mm,钻头采用双锥后磨横刀,后角 o12,二重刃长度 b=3.5mm,横刀长b=2mm,宽 l=4mm,棱带长度, mml5 . 111002302) 选择切削用量 确定进给量按加工要求确定进给量:查切削手册,rmmf/53. 043. 0,由切削手册表 2.7,系数为 0.5,则: 367. 11830dlrmmf/)265. 0215. 0(5 . 0)53. 043. 0(按钻头强度选择:查切削手册表 2.8,钻头允许进给量为:;rmmf/0 . 2按机床进给机构强度选择:查切削手册表 2.9,机床进给机构允许轴向力为8330N 时,进给量为。以上三个进给量比较得出,受限制的进给rmmf/93. 016量是工艺要求,其值为:0.2150.265mm/r。根据简明手册表 4.2-16,最终选择进给量。rmmf/22. 0根据切削手册表 2.19 查出,钻孔时轴向力 Ff=2500N,轴向力修正系数为 1.0,故 Ff=2500N。根据 Z525 立式钻床使用说明书,机床进给机构允许的最大轴向力为 8830NFf,故所选进给量可用。 确定钻头磨钝标准及寿命后刀面最大磨损限度(查简明手册)为 0.6mm,寿命min45T 切削速度查切削手册表 2.30,切削速度计算公式为: (m/min)vyxpmvckfaTdcvvvvz0其中,5 . 9Cvmmd18025. 0vz125. 0m9pa0vx,查得修正系数:,故实际55. 0vy22. 0f0 . 1vTk85. 0lvk0 . 1tvk的切削速度:min/5 . 985. 022. 0160185 . 955. 0125. 025. 0mvc 检验机床扭矩及功率查切削手册表 2.20,当 f0.26, do19mm 时,Mt=31.78Nm,修正系数均为 1.0,故 MC=31.78 Nm。查机床使用说明书:Mm =144.2 Nm。查切削手册表 2.23,钻头消耗功率:Pc=1.3kw。查机床使用说明书,。kwPE26. 281. 08 . 2由于,故切削用量可用,即:mcMM ECPP ,rmmf/22. 0min/272rnncmin/4 .15 mvc3) 计算工时min64. 022. 0272830nfLtm4) 扩孔至 19.8查切削手册表 2.10,扩孔进给量为:,并由机床使rmmf/8 . 07 . 0用说明书最终选定进给量为:。rmmf/81. 017根据资料,切削速度 ,其中为用钻头钻同样尺寸实心孔时的钻vv4 . 0钻v切削速度,故:,根据机min/8 . 35 . 94 . 0mvmin/1 .618 .198 . 31000rns床使用说明书选取: 。min/97rnw基本工时: min48. 081. 09783081. 097yLt(3)粗铰、精铰 20 孔;以 32 外圆和 T2 为基准。1) 粗铰至mm94.19刀具:专用铰刀机床:Z525 立式钻床根据有关手册的规定,铰刀的进给量为0.81.2mm/z,进给量取fz0.81mm/r,机床主轴转速取为=140r/min,则其切削速度为:fznw。min/77. 8mdnv机动时切削工时,=38mm,830lmin34. 081. 01403838fntwm2) 精铰至mm20刀具:mmdw20机床:Z525 立式数控钻床根据有关手册的规定,铰刀的进给量取0.48mm/r,机床主轴转速取为:f=140r/min,则其切削速度为:nwmin/8 . 8 mdnv机动时切削工时,=38mm830lmin57. 048. 01403838fntwm机床:X51 立式数控铣床刀具:硬质合金立铣刀(镶齿螺旋形刀片),由切削手册表 3.6 查得:,,即 27m/min,因此,smv/45. 0min/08. 0, 6,40mmfzdzmin/214402710001000rdvnws现采用 X51 立式铣床,取 ,工作台每分钟进给量应为:min/210rnwfm,min/8 .100210608. 0mmnzffwzm18查机床使用说明书,取 。min/100mmfm铣削基本工时:min84. 01001272tmmin68. 1284. 02tm(3) 粗镗、半精镗 50 孔,以 D1 为定位基准1) 粗镗 50 孔,以 D1 为定位基准。机床:T60 卧式数控镗床单边余量 可一次切除,则 。根据简明手册,5 . 2 mmZ mmap5 . 24.2-20 查得,取 。根据简明手册4.2-21 查得,取:rmmf/52. 0。min/200rn 计算切削基本工时:min13. 052. 02001212fLtmm2) 半精镗 50 孔,以 D1 做定位基准。单边余量,可一次切除,则 。mmz0 . 1mmap0 . 1由切削手册表 1.6 查得,进给量取为,/40. 025. 0rmmfz0.27mm/r。由切削手册表 1.1 查得,则:min/100mv min/6375010010001000rdvnww查简明手册表 4.2-20,取为 630r/min。nw加工基本工时:min038. 05 . 063012fnltw工序 04 铣斜肩,以 D1 和 T2 为定位基准刀具:硬质合金三面刃铣刀机床:X51 立式铣床根据简明手册查得:。根据切削手册查得:1663Zmmdw,因此:,/10. 0zmmfzmin/136632710001000rdvnws现采用 X51 立式铣床,取:,故实际切削速度为:min/100rnwmin/8 .191000100631000mndvww19当时,工作台每分钟进给量应为:min/300rnwmin/1601001610. 0mmnZffwzm根据切削手册表 4.2-37 查得,取:。min/165mmfm计算切削基本工时:mmylL5 .37255 .12因此:min227. 01655 .37fLtmm工序 05 精铣 50 端面,以 D1 为基准,采用 X51 立式数控铣床加专用夹具机床:X51 立式数控铣床刀具:硬质合金立铣刀(镶齿螺旋形刀片),由切削手册表 3.6 查得:,,即 27m/min,因此,smv/45. 0min/08. 0, 6,40mmfzdzmin/214402710001000rdvnws现采用 X51 立式铣床,取 ,工作台每分钟进给量应为:min/210rnwfm,min/8 .100210608. 0mmnzffwzm查机床使用说明书,取 。min/100mmfm铣削基本工时:min84. 01001272tmmin68. 1284. 02tm工序 06 钻、铰 8 锥孔,以 T1 和零件中线为基准刀具:专用刀具机床:Z525 立式钻床确定进给量:根据切削手册表 2.7 查得,查frmmf/26. 022. 0Z525 机床使用说明书,现取。查切削手册表 2.15,rmmf/22. 0,计算机床主轴转速:min/17mv min/6948 . 71710001000rdvnws按机床选取,所以实际切削速度为:min/680nw20min/66.1610006808 . 71000mndvww计算切削基本工时:min066. 022. 068046fyltmm工序 07 钻 M6 底孔,攻螺纹,以 T1 和零件中线为基准(1) 钻螺纹底孔mm8 . 4机床:Z525 立式钻床刀具:高速钢麻花钻根据切削手册查得,进给量为0.180.22mm/z,现取ff=0.22mm/z,v=17m/min,则:min/11288 . 41710001000rdvnws查简明手册表 4.2-15,取。所以实际切削速度为:min/960rnwmin/48.1410009608 . 41000mndvww计算切削基本工时:min047. 022. 096046fyltmm(2) 攻螺纹 M6机床:Z525 立式钻床刀具:丝锥 M6,P=1mm切削用量选为:,机床主轴转速为:min/6/1 . 0msmv,按机床使用说明书选取:,则 min/318rnsmin/272rnw;机动时,计算切削基本工时:min/1 . 5 mv mml1046min04. 0272110nfltm工序 08 铣断,以 D1 为基准选择锯片铣刀,d=160mm,l=4mm,中齿,Z=40采用 X61 卧式铣床21查切削手册,选择进给量为:,切削速度为:zmmf/10. 0,则:min/27mv min/541602710001000rdvnws根据简明手册表 4.2-39,取,故实际切削速度为:min/100rnwmin/2 .501000100801000mndvww此时工作台每分钟进给量应为:fmmin/400100401 . 0mmnZffwzm查切削手册表 4.2-40,刚好有。min/400mmfm计算切削基本工时:min255. 04003072fyltmm4 夹具设计夹具设计为了提高劳动生产率,保证加工质量,降低劳动强度,需要设计专用夹具。并设计工序 03钻、扩 20 孔,粗铰、精铰 20 孔;粗镗、半精镗 50 孔;刀具为高速钢麻花钻。4.1 问题的提出问题的提出本夹具主要用来钻 20、50 底孔,该孔为通孔,跟拨叉的上下底面有垂直度的技术要求要求,在加工时应保证孔的垂直度要求分别为 0.05、0.07。此外在本工序加工时还应考虑如何提高劳动生产率,降低劳动强度,所以为了满足该要求,在进行夹紧拨叉工件时采用了气缸自动装置来进行装夹工件,并采用快换钻套提高钻孔的速度,能够提高加工效率。4.2 夹具设计夹具设计4.2.1 定位基准选择定位基准选择由零件图可知,孔 20、50 为通孔,跟拨叉的上下底面有垂直度的技术要求,为使定位误差为零,应该选择拨叉下底面为定位基准保证该垂直度要求。此外,还应以 20 孔外圆柱面为基准,从而保证孔在精度要求。22为了提高加工效率,现决定采用自动夹紧装置,并采用快换钻套以利于在钻底孔后进行精铰或精镗。4.2.2 切削力及夹紧力计算切削力及夹紧力计算刀具:硬质合金麻花钻,(1)钻 20 时的夹紧力由实际加工的经验可知,钻削时的主要切削力为钻头的切削方向,即垂直于工作台,查切削手册表 2.3,切削力计算公式为:FFFkfdCFyZFf0其中:,410CF2 . 1ZF75. 0yFmmd8 .19022. 0f,与加工材料有关,取 0.94;与刀具刃磨形状有关,取kkkkhFxFMFFkMFkxF1.33;与刀具磨钝标准有关,取 1.0,则:khFNF6 .592225. 122. 08 .1941075. 02 . 1在 20 孔两个端面只需要采用开口垫圈和六角螺母适当夹紧后本夹具即可安全工作. (2)钻 50 孔时的夹紧力取钻头直径mmd8 .490有上述公式可得:NF7 .1791325. 122. 08 .4941075. 02 . 14.3 定位误差分析定位误差分析4.3.1 定位元件尺寸及公差的确定定位元件尺寸及公差的确定夹具的主要定位元件为两个定位销,这两个定位销的尺寸与公差规定为与本零件在工作时与其相匹配轴的尺寸与公差相同,即。此外,这两10620k定位销共同保证加工孔的垂直度。4.3.2 计算钻套中心线与工作台的垂直度误差计算钻套中心线与工作台的垂直度误差钻套外径与衬套孔的最大间隙为:520g726H026. 0)011. 0(015. 0max23衬套外径与钻模板孔的最大间隙为:650r756H005. 0023. 0018. 0max则钻套中心与工作台平面的垂直度误差为:0.026-0.005=0.021。4.3.3 计算定位销轴与工作台的平行度误差计算定位销轴与工作台的平行度误差定位销轴与夹具体孔的最大间隙为:034. 0001. 0035. 0max4.4 夹具设计及操作的简要说明夹具设计及操作的简要说明如前所述,在设计夹具时,应该考虑提高劳动生产率。为此,设计采用了快换装置。拆卸时,松开夹紧螺母 12 扣,拔下开口垫圈,实现工件
- 温馨提示:
1: 本站所有资源如无特殊说明,都需要本地电脑安装OFFICE2007和PDF阅读器。图纸软件为CAD,CAXA,PROE,UG,SolidWorks等.压缩文件请下载最新的WinRAR软件解压。
2: 本站的文档不包含任何第三方提供的附件图纸等,如果需要附件,请联系上传者。文件的所有权益归上传用户所有。
3.本站RAR压缩包中若带图纸,网页内容里面会有图纸预览,若没有图纸预览就没有图纸。
4. 未经权益所有人同意不得将文件中的内容挪作商业或盈利用途。
5. 人人文库网仅提供信息存储空间,仅对用户上传内容的表现方式做保护处理,对用户上传分享的文档内容本身不做任何修改或编辑,并不能对任何下载内容负责。
6. 下载文件中如有侵权或不适当内容,请与我们联系,我们立即纠正。
7. 本站不保证下载资源的准确性、安全性和完整性, 同时也不承担用户因使用这些下载资源对自己和他人造成任何形式的伤害或损失。

人人文库网所有资源均是用户自行上传分享,仅供网友学习交流,未经上传用户书面授权,请勿作他用。