止转垫板冷冲压工艺及其连续模设计【14张图纸】【优秀】
收藏
资源目录
压缩包内文档预览:
编号:271540
类型:共享资源
大小:1.42MB
格式:RAR
上传时间:2014-04-07
上传人:上***
认证信息
个人认证
高**(实名认证)
江苏
IP属地:江苏
50
积分
- 关 键 词:
-
止转垫板
冲压
工艺
及其
连续
设计
图纸
优秀
- 资源描述:
-
止转垫板冷冲压工艺及其连续模设计
37页 16000字数+说明书+任务书+开题报告+外文翻译+14张CAD图纸【详情如下】
3凹模-A2.dwg
3凹模-A2.exb
4卸料板-A2.dwg
4卸料板-A2.exb
5上模座-A1.exb
6凸模垫板-A3.exb
7落料凸模-A4.dwg
7落料凸模-A4.exb
8大孔凸模-A4.exb
9小凸模2-A4.exb
任务书.doc
冷冲压工艺卡片-A4.doc
外文翻译--切削技术与加工工序.doc
止转垫板冷冲压工艺及其连续模设计开题报告.doc
止转垫板冷冲压工艺及其连续模设计论文.doc
相关资料.doc
计划周记进度检查表.xls
10小凸模1-A4.exb
11凸模固定板-A2.dwg
11凸模固定板-A2.exb
12后导料板-A3.exb
13前导料板-A3.exb
14侧刃-A4.exb
1装配图-A0.dwg
1装配图-A0.exb
2下模座-A1.dwg
2下模座-A1.exb
摘 要
本设计为一止转垫板的冷冲压连续模具设计,根据设计零件的尺寸、材料、批量生产等要求,首先分析零件的工艺性,确定冲裁工艺方案及模具结构方案,然后通过工艺设计计算,确定排样和裁板,计算冲压力和压力中心,冲孔、落料压力,初选压力机,计算凸、凹模刃口尺寸和公差,最后设计选用零、部件,对压力机进行校核,绘制模具总装草图,以及对模具主要零件的加工工艺规程进行编制。其中在结构设计中,主要对落料凸模、凹模、凸凹模、定位零件、卸料与出件装置、模架、冲压设备、紧固件等进行了设计,对于部分零部件选用的是标准件,并且在结构设计的同时,对部分零部件进行了加工工艺分析,最终才完成这篇毕业设计。本次对止转垫板进行的连续模设计,利用CAXA软件对制件进行设计绘图。明确了设计思路,确定了冲压成型工艺过程并对各个具体部分进行了详细的计算和校核。如此设计出的结构可确保模具工作运用可靠,保证了与其他部件的配合。并绘制了模具的装配图和零件图。
关键词:止转垫板;冲压工艺;排样;连续模
目 录
摘 要III
AbstractIV
目 录V
1 绪论1
1.1本课题的研究内容和意义1
1.2国内外的发展概况1
1.2.1 国外模具发展概况1
1.2.2国内模具发展概况2
1.3本课题应达到的要求3
2 冲压工艺设计4
2.1 冲压件简介4
2.2 冲压的工艺性分析4
2.3 冲压工序5
2.4冲裁间隙5
2.5 冲压工艺方案的确定6
3 止转垫板连续模设计7
3.1 模具结构7
3.2 确定其搭边值8
3.3 确定排样图8
3.4 材料利用率计算9
3.5 凸、凹模刃口尺寸的确定9
3.5.1 落料部份凸、凹模刃口尺寸的确定9
3.5.2 冲4个小孔凸、凹模刃口尺寸的确定10
3.5.3 中间大孔凸、凹模刃口尺寸的确定12
3.6 冲压力计算12
3.6.1 落料部分冲压力13
3.6.2 冲孔部分冲压力13
3.6.3 侧刃部分冲压力14
3.6.4 总冲压力14
3.7压力机选用14
3.8 压力中心计算15
3.9 模具主要零部件的结构设计15
3.9.1 凹模结构及设计16
3.9.2 小凸模1设计17
3.9.3 小孔凸模2设计18
3.9.4 落料凸模设计18
3.9.5 中间大孔凸模设计19
3.9.6 卸料板设计20
3.9.7 凸模固定板设计21
3.9.8 凸模垫板设计21
3.9.9 侧刃设计22
3.9.10 侧刃挡块设计23
3.9.11 前侧导板设计23
3.9.12 后侧导板设计24
3.10 标准件确定24
3.10.1 模架确定24
3.10.2 上模螺钉确定24
3.10.3 上模销确定25
3.10.4 下模螺钉确定25
3.10.5 下模销确定25
3.10.6 卸料螺钉确定25
3.10.7 弹性元件设计25
3.10.8 模柄确定26
3.10.9 模柄上止转销的确定26
3.11 模具闭合高度、校验压力机26
4 结论与展望27
4.1 结论27
4.2 不足之处及未来展望27
致 谢28
参考文献29
1 绪论
1.1本课题的研究内容和意义
现代模具行业是技术、资金密集型的行业;现代模具是高技术背景下的工艺密集型工业。它作为重要的生产装备行业在为各行各业服务的同时,也直接为高新技术产业服务。
由于现在模具生产要采用一系列高新技术,如CAD/CAE/CAM/CAPP等技术、计算机网络技术、激光技术、逆向工程和并行工程、快速成形技术及敏捷制造技术、高速加工及超精加工、微细加工、复合加工、表面处理技术等等。因此,模具工业已成为高新技术产业的一个重要组成部分。模具技术水平在很大程度上决定于人才的整体水平,而模具技术水平的高低,又决定着产品的质量、效益和新产品的开发能力,因此模具技术已成为衡量一个国家产品制造水平高低的重要标志!
如今汽车、电子、电器、航空、仪表、轻工、塑料、日用品等工业部门极其依赖模具。没有模具,就没有高质量的产品。模具不是一般的工艺装备,而是技术密集型的产品,工业发达国家把模具作为机械制造方面的高科技产品来对待他们认为:“模具是发展工业的一把钥匙”;“模具是一个企业的心脏”;“模具是富裕社会的一种动力”。
冲压模具在实际工业生产中应用广泛。在传统的工业生产中,工人生产的劳动强度大、劳动量大,严重影响生产效率的提高。随着当今科技的发展,?工业生产中模具的使用已经越来越引起人们的重视,而被大量应用到工业生产中来。冲压模具的自动送料技术也投入到实际的生产中,冲压模具可以大大的提高劳动生产效率,减轻工人负担,具有重要的技术进步意义和经济价值。
冲压模具作为模具行业里不可或缺的一部分,已成为制造业的重要基础工艺装备。用模具生产制件所达到的高精度、高复杂程度、高一致性、高生产率和低耗能、低耗材,使模具工业在制造业中的地位越来越重要。
工业发展水平的不断提高,工业产品更新速度加快,对模具的要求越来越高,尽管改革开放以来,模具工业有了较大发展,但无论是数量还是质量仍满足不了国内市场的需要,因此,要使国民经济各个部门获得高速发展,加速实现社会主义四个现代化,就必须尽快将模具工业搞上去,从而充分发挥模具工业在国民经济中的关键作用。1.3本课题应达到的要求
冲压模具的设计在其生产、加工以及使用过程中尤为重要。特别是它的结构设计,对加工、装配、工期、成本乃至冲压产品的质量及生产效率产生极大的影响。本课题要求对给定零件止板垫片进行落料、冲孔、成形连续模设计,通过对零件进行详细的冲压工艺、排样方案、模具结构分析确定零件的冲压工艺方案并制定部分零件的制造工艺,如:凸模、凹模、凸凹模、凸模固定板、垫板、凹模固定板、卸料板、导尺、挡料销、导正销等。从应用性方面来说,模具是生产效率极高的工具之一,能有效保证产品一致性和可更换性,具有很好的发展前途和应用前景。通过该课题能够让学生掌握中等复杂程度零件冲压连续模设计与制造的一般方法,对零件冲压连续模工艺方案的制定、工艺计算及连续模具设计有了更深层次的认识,并学会对模具设计资料的检索与整合以及对已有资料的充分合理的使用,连续模在模具中技术含量高,制造、装配难度大,该课题将会是对学生理论学习水平的实践和检验,可对以后从事类似的工作有一定的指导性与实践性意义

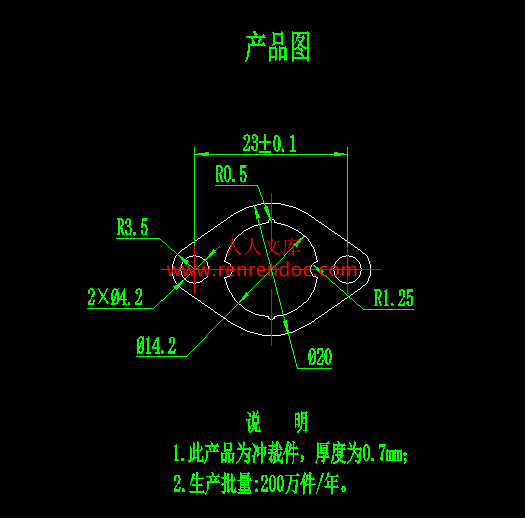
- 内容简介:
-
无锡太湖学院信 机系 机械工程及自动化 专业毕 业 设 计论 文 任 务 书一、题目及专题:1、题目止转垫板冷冲压工艺及连续模设计 2、专题 二、课题来源及选题依据 来源于无锡海诺有限公司,是电器产品上的一个零件。 模具是机械工程及其自动化专业的一个专业方向,选择模具方向的毕业设计题目完全符合本专业的要求,从应用性方面来说,模具又是生产效率极高的工具之一,能有效保证产品一致性和可更换性,具有很好的发展前途和应用前景。连续模在模具中技术含量高,制造、装配难度大,因此本课题研究连续模的冲压工艺、排样方案、模具结构分析等方面,同时要求学生要有良好的心理素质和仔细认真的作风,对学生也是一次很好的练习机会。 三、本设计(论文或其他)应达到的要求:综合应用各种所学的专业知识,在规定的时间内对产品进行冷冲压工艺分析,制订完整的冲压工艺方案,并完成整副模具设计、数据计算和图纸(所有图纸折合A0不少于2.5张)绘制,具体内容如下:1完成模具装配图:1张(A0或A1); 2零件图:主要是非标准件零件图(不少于5张); 3冷冲压工艺卡片:1张 ; 4设计说明书:1份(15000字以上,其中参考文献不少于10篇,外文不少于5篇); 5翻译8000以上外文印刷字符,折合中文字数约5000字的有关技术资料或专业文献,内容要尽量结合课题。 四、接受任务学生: 机械96 班 姓名 刘 奎 五、开始及完成日期:自2012年11月12日 至2013年5月25日六、设计(论文)指导(或顾问):指导教师签名 签名 签名教研室主任学科组组长研究所所长签名 系主任 签名2012年11月12日无锡太湖学院冷冲压工艺卡片零件名称止转垫板零件图号115010材料牌号及规格10钢0.725.4L毛坯种类带料毛坯尺寸25.4L每毛坯可制件数1件/每22.52工序号工序名称工序内容冲压设备工艺装备一次加工数工 序 附 图10冲裁冲2个孔、侧刃J23-10模具和自动送料机构120冲裁冲内孔J23-10模具和自动送料机构130冲裁落料J23-10模具和自动送料机构140冲裁侧刃J23-10模具和自动送料机构150检验检验班级机械96姓名刘奎学号0923278日期2013.5.16批改日期英文原文 Cutting Technology and Machining OperationsBasically, in metal cutting, a sharpened wedge-shaped tool removes a rather narrow strip of metal from the surface of a ductile workpiece in the form of a severely deformed chip. The chip is a waste product that is considerably shorter than the workpiece from which it came but with a corresponding increase in thickness of the uncut chip. The geometrical shape of workpiece depends on the shape of the tool and its path during the machining operation. Most machining operations produce parts of differing geometry. If a rough cylindrical workpiece revolves about a central axis and the tool penetrates beneath its surface and travels parallel to the center of rotation, a surface of revolution is produced, and the operation is called turning. If a hollow tube is machined on the inside in a similar manner, the operation is called boring. Producing an external conical surface uniformly varying diameter is called taper turning, if the tool point travels in a path of varying radius, a contoured surface like that of a bowling pin can be produced; or, if the piece is short enough and the support is sufficiently rigid, a contoured surface could be produced by feeding a shaped tool normal to the axis of rotation. Short tapered or cylindrical surfaces could also be contour formed. Multiple-edged tools can also be used. Drilling uses a twin-edged fluted tool for holes with depths up to 5 to 10 times the drill diameter. Whether the drill turns or the workpiece rotates, relative motion between the cutting edge and the workpiece is the important factor. In milling operations a rotary cutter with a number of cutting edges engages the workpiece. Which moves slowly with respect to the cutter. Plane or contoured surfaces may be produced, depending on the geometry of the cutter and the type of feed. Horizontal or vertical axes of rotation may be used, and the feed of the workpiece may be in any of the three coordinate directions. Speeds, feeds, and depth of cut are the three major variables for economical machining. Other variables are the work and tool materials, coolant and geometry of the cutting tool. The rate of metal removal and power required for machining depend upon these variables. The depth of cut, feed, and cutting speed are machine settings that must be established in any metal-cutting operation. They all affect the forces, the power, and the rate of metal removal. They can be defined by comparing them to the needle and record of a phonograph. The cutting speed (V) is represented by the velocity of- the record surface relative to the needle in the tone arm at any instant. Feed is represented by the advance of the needle radially inward per revolution, or is the difference in position between two adjacent grooves. The depth of cut is the penetration of the needle into the record or the depth of the grooves. The basic operations performed on an engine lathe are illustrated. Those operations performed on external surfaces with a single point cutting tool are called turning. Except for drilling, reaming, and lapping, the operations on internal surfaces are also performed by a single point cutting tool. All machining operations, including turning and boring, can be classified as roughing, finishing, or semi-finishing. The objective of a roughing operation is to remove the bulk of the material as rapidly and as efficiently as possible, while leaving a small amount of material on the work-piece for the finishing operation. Finishing operations are performed to obtain the final size, shape, and surface finish on the workpiece. Sometimes a semi-finishing operation will precede the finishing operation to leave a small predetermined and uniform amount of stock on the work-piece to be removed by the finishing operation. Generally, longer workpieces are turned while supported on one or two lathe centers. Cone shaped holes, called center holes, which fit the lathe centers are drilled in the ends of the workpiece-usually along the axis of the cylindrical part. The end of the workpiece adjacent to the tailstock is always supported by a tailstock center, while the end near the headstock may be supported by a headstock center or held in a chuck. The headstock end of the workpiece may be held in a four-jaw chuck, or in a type chuck. This method holds the workpiece firmly and transfers the power to the workpiece smoothly; the additional support to the workpiece provided by the chuck lessens the tendency for chatter to occur when cutting. Precise results can be obtained with this method if care is taken to hold the workpiece accurately in the chuck. Very precise results can be obtained by supporting the workpiece between two centers. A lathe dog is clamped to the workpiece; together they are driven by a driver plate mounted on the spindle nose. One end of the Workpiece is mecained;then the workpiece can be turned around in the lathe to machine the other end. The center holes in the workpiece serve as precise locating surfaces as well as bearing surfaces to carry the weight of the workpiece and to resist the cutting forces. After the workpiece has been removed from the lathe for any reason, the center holes will accurately align the workpiece back in the lathe or in another lathe, or in a cylindrical grinding machine. The workpiece must never be held at the headstock end by both a chuck and a lathe center. While at first thought this seems like a quick method of aligning the workpiece in the chuck, this must not be done because it is not possible to press evenly with the jaws against the workpiece while it is also supported by the center. The alignment provided by the center will not be maintained and the pressure of the jaws may damage the center hole, the lathe center, and perhaps even the lathe spindle. Compensating or floating jaw chucks used almost exclusively on high production work provide an exception to the statements made above. These chucks are really work drivers and cannot be used for the same purpose as ordinary three or four-jaw chucks. While very large diameter workpieces are sometimes mounted on two centers, they are preferably held at the headstock end by faceplate jaws to obtain the smooth power transmission; moreover, large lathe dogs that are adequate to transmit the power not generally available, although they can be made as a special. Faceplate jaws are like chuck jaws except that they are mounted on a faceplate, which has less overhang from the spindle bearings than a large chuck would have. Machining as a shape-producing method is the most universally used and the most important of all manufacturing processes. Machining is a shape-producing process in which a power-driven device causes material to be removed in chip form. Most machining is done with equipment that supports both the work piece and cutting tool although in some cases portable equipment is used with unsupported workpiece. Close accuracies, good finishes. The second application for machining is based on the high accuracies and surface finishes possible. Many of the parts machined in low quantities would be produced with lower but acceptable tolerances if produced in high quantities by some other process. On the other hand, many parts are given their general shapes by some high quantity deformation process and machined only on selected surfaces where high accuracies are needed. Internal threads, for example, are seldom produced by any means other than machining and small holes in press worked parts may be machined following the press working operations.The basic tool-work relationship in cutting is adequately described by means of four factors: tool geometry, cutting speed, feed, and depth of cut. The cutting tool must be made of an appropriate material; it must be strong, tough, hard, and wear resistant. The tool s geometry characterized by planes and angles, must be correct for each cutting operation. Cutting speed is the rate at which the work surface passes by the cutting edge. It may be expressed in feet per minute. For efficient machining the cutting speed must be of a magnitude appropriate to the particular work-tool combination. In general, the harder the work material, the slower the speed. Feed is the rate at which the cutting tool advances into the workpiece. Where the workpiece or the tool rotates, feed is measured in inches per revolution. When the tool or the work reciprocates, feed is measured in inches per stroke, Generally, feed varies inversely with cutting speed for otherwise similar conditions. The depth of cut, measured inches is the distance the tool is set into the work. It is the width of the chip in turning or the thickness of the chip in a rectilinear cut. In roughing operations, the depth of cut can be larger than for finishing operations. In metal cutting operations heat is generated in the primary and secondary deformation zones and these results in a complex temperature distribution throughout the tool, workpiece and chip. A typical set of isotherms is shown in figure where it can be seen that, as could be expected, there is a very large temperature gradient throughout the width of the chip as the workpiece material is sheared in primary deformation and there is a further large temperature in the chip adjacent to the face as the chip is sheared in secondary deformation. This leads to a maximum cutting temperature a short distance up the face from the cutting edge and a small distance into the chip. Since virtually all the work done in metal cutting is converted into heat, it could be expected that factors which increase the power consumed per unit volume of metal removed will increase the cutting temperature. Thus an increase in the rake angle, all other parameters remaining constant, will reduce the power per unit volume of metal removed and the cutting temperatures will reduce. When considering increase in unreformed chip thickness and cutting speed the situation is more complex. An increase in undeformed chip thickness tends to be a scale effect where the amounts of heat which pass to the workpiece, the tool and chip remain in fixed proportions and the changes in cutting temperature tend to be small. Increase in cutting speed; however, reduce the amount of heat which passes into the workpiece and this increase the temperature rise of the chip m primary deformation. Further, the secondary deformation zone tends to be smaller and this has the effect of increasing the temperatures in this zone. Other changes in cutting parameters have virtually no effect on the power consumed per unit volume of metal removed and consequently have virtually no effect on the cutting temperatures. Since it has been shown that even small changes in cutting temperature have a significant effect on tool wear rate it is appropriate to indicate how cutting temperatures can be assessed from cutting data. The most direct and accurate method for measuring temperatures in high -speed-steel cutting tools is that of Wright &. Trent which also yields detailed information on temperature distributions in high-speed-steel cutting tools. The technique is based on the metallographic examination of sectioned high-speed-steel tools which relates microstructure changes to thermal history. Trent has described measurements of cutting temperatures and temperature distributions for high-speed-steel tools when machining a wide range of workpiece materials. This technique has been further developed by using scanning electron microscopy to study fine-scale microstructure changes arising from over tempering of the tempered martens tic matrix of various high-speed-steels. This technique has also been used to study temperature distributions in both high-speed -steel single point turning tools and twist drills. Discounting brittle fracture and edge chipping, which have already been dealt with, tool wear is basically of three types. Flank wear, crater wear, and notch wear. Flank wear occurs on both the major and the minor cutting edges. On the major cutting edge, which is responsible for bulk metal removal, these results in increased cutting forces and higher temperatures which if left unchecked can lead to vibration of the tool and workpiece and a condition where efficient cutting can no longer take place. On the minor cutting edge, which determines workpiece size and surface finish, flank wear can result in an oversized product which has poor surface finish. Under most practical cutting conditions, the tool will fail due to major flank wear before the minor flank wear is sufficiently large to result in the manufacture of an unacceptable component. Because of the stress distribution on the tool face, the frictional stress in the region of sliding contact between the chip and the face is at a maximum at the start of the sliding contact region and is zero at the end. Thus abrasive wear takes place in this region with more wear taking place adjacent to the seizure region than adjacent to the point at which the chip loses contact with the face. This result in localized pitting of the tool face some distance up the face which is usually referred to as catering and which normally has a section in the form of a circular arc. In many respects and for practical cutting conditions, crater wear is a less severe form of wear than flank wear and consequently flank wear is a more common tool failure criterion. However, since various authors have shown that the temperature on the face increases more rapidly with increasing cutting speed than the temperature on the flank, and since the rate of wear of any type is significantly affected by changes in temperature, crater wear usually occurs at high cutting speeds. At the end of the major flank wear land where the tool is in contact with the uncut workpiece surface it is common for the flank wear to be more pronounced than along the rest of the wear land. This is because of localised effects such as a hardened layer on the uncut surface caused by work hardening introduced by a previous cut, an oxide scale, and localised high temperatures resulting from the edge effect. This localised wear is usually referred to as notch wear and occasionally is very severe. Although the presence of the notch will not significantly affect the cutting properties of the tool, the notch is often relatively deep and if cutting were to continue there would be a good chance that the tool would fracture. If any form of progressive wear allowed to continue, dramatically and the tool would fail catastrophically, i. e. the tool would be no longer capable of cutting and, at best, the workpiece would be scrapped whilst, at worst, damage could be caused to the machine tool. For carbide cutting tools and for all types of wear, the tool is said to have reached the end of its useful life long before the onset of catastrophic failure. For high-speed-steel cutting tools, however, where the wear tends to be non-uniform it has been found that the most meaningful and reproducible results can be obtained when the wear is allowed to continue to the onset of catastrophic failure even though, of course, in practice a cutting time far less than that to failure would be used. The onset of catastrophic failure is characterized by one of several phenomena, the most common being a sudden increase in cutting force, the presence of burnished rings on the workpiece, and a significant increase in the noise level.There are basically five mechanisms which contribute to the production of a surface which have been machined. These are:(l) The basic geometry of the cutting process. (2) The efficiency of the cutting operation. (3) The stability of the machine tool. (4)The effectiveness of removing swarf. (5)The effective clearance angle on the cutting tool. Machine parts are manufactured so they are interchangeable. In other words, each part of a machine or mechanism is made to a certain size and shape so will fit into any other machine or mechanism of the same type. To make the part interchangeable, each individual part must be made to a size that will fit the mating part in the correct way. It is not only impossible, but also impractical to make many parts to an exact size. This is because machines are not perfect, and the tools become worn. A slight variation from the exact size is always allowed. The amount of this variation depends on the kind of part being manufactured. For examples part might be made 6 in. long with a variation allowed of 0.003 (three-thousandths) in. above and below this size. Therefore, the part could be 5.997 to 6.003 in. and still be the correct size. These are known as the limits. The difference between upper and lower limits is called the tolerance. A tolerance is the total permissible variation in the size of a part. The basic size is that size from which limits of size arc derived by the application of allowances and tolerances. Sometimes the limit is allowed in only one direction. This is known as unilateral tolerance.Unilateral tolerancing is a system of dimensioning where the tolerance (that is variation) is shown in only one direction from the nominal size. Unilateral tolerancing allow the changing of tolerance on a hole or shaft without seriously affecting the fit.When the tolerance is in both directions from the basic size it is known as a bilateral tolerance (plus and minus). Bilateral tolerancing is a system of dimensioning where the tolerance (that is variation) is split and is shown on either side of the nominal size. Limit dimensioning is a system of dimensioning where only the maximum and minimum dimensions arc shown. Thus, the tolerance is the difference between these two dimensions. Products that have been completed to their proper shape and size frequently require some type of surface finishing to enable them to satisfactorily fulfill their function. In some cases, it is necessary to improve the physical properties of the surface material for resistance to penetration or abrasion. In many manufacturing processes, the product surface is left with dirt .chips, grease, or other harmful material upon it. Assemblies that are made of different materials, or from the same materials processed in different manners, may require some special surface treatment to provide uniformity of appearance. Surface finishing may sometimes become an intermediate step processing. For instance, cleaning and polishing are usually essential before any kind of plating process. Some of the cleaning procedures are also used for improving surface smoothness on mating parts and for removing burrs and sharp corners, which might be harmful in later use. Another important need for surface finishing is for corrosion protection in a variety of: environments. The type of protection procedure will depend largely upon the anticipated exposure, with due consideration to the material being protected and the economic factors involved. Satisfying the above objectives necessitates the use of main surface-finishing methods that involve chemical change of the surface mechanical work affecting surface properties, cleaning by a variety of methods, and the application of protective coatings, organic and metallic. In the early days of engineering, the mating of parts was achieved by machining one part as nearly as possible to the required size, machining the mating part nearly to size, and then completing its machining, continually offering the other part to it, until the desired relationship was obtained. If it was inconvenient to offer one part to the other part during machining, the final work was done at the bench by a fitter, who scraped the mating parts until the desired fit was obtained, the fitter therefore being a fitter in the literal sense. J It is obvious that the two parts would have to remain together, and m the event of one having to be replaced, the fitting would have to be done all over again. In these days, we expect to be able to purchase a replacement for a broken part, and for it to function correctly without the need for scraping and other fitting operations.When one part can be used off the shelf to replace another of the same dimension and material specification, the parts are said to be interchangeable. A system of interchangeability usually lowers the production costs as there is no need for an expensive, fiddling operation, and it benefits the customer in the event of the need to replace worn parts. Traditional synchronous grippers for assembly equipment move parts to the gripper centre-line, assuring that the parts will be in a known position after they arc picked from a conveyor or nest. However, in some applications, forcing the part to the centre-line may damage cither the part or equipment. When the part is delicate and a small collision can result in scrap, when its location is fixed by a machine spindle or mould, or when tolerances are tight, it is preferable to make a gripper comply with the position of the part, rather than the other way around. For these tasks, Zaytran Inc. Of Elyria, Ohio, has created the GPN series of non- synchronous, compliant grippers. Because the force and synchronizations systems of the grippers are independent, the synchron、ization system can be replaced by a precision slide system without affecting gripper force. Gripper sizes range from 51b gripping force and 0.2 in. stroke to 40Glb gripping force and 6in stroke. Grippers Production is characterized by batch-size becoming smaller and smaller and greater variety of products. Assembly, being the last production step, is particularly vulnerable to changes in schedules, batch-sizes, and product design. This situation is forcing many companies to put more effort into extensive rationalization and automation of assembly that was previouslyextensive rationalization and automation of assembly that was previously the case. Although the development of flexible fixtures fell quickly behind the development of flexible handling systems such as industrial robots, there are, nonetheless promising attempts to increase the flexibility of fixtures. The fact that fixtures are the essential product - specific investment of a production system intensifies the economic necessity to make the fixture system more flexible. Fixtures can be divided according to their flexibility into special fixtures, group fixtures, modular fixtures and highly flexible fixtures. Flexible fixtures are characterized by their high adaptability to different workpieces, and by low change-over time and expenditure. There are several steps required to generate a fixture, in which a workpiece is fixed for a production task. The first step is to define the necessary position of the workpiece in the fixture, based on the unmachined or base pan, and the working features. Following this, a combination of stability planes must be selected. These stability planes constitute the fixture configuration in which the workpiece is fixed in the defined position, all the forces or torques are compensated, and the necessary access to the working features is ensured. Finally, the necessary positions of moveable or modular fixture elements must be calculated- adjusted, or assembled, so that the workpiece is firmly fixed in the fixture. Through such a procedure the planning and documentation of the configuration and assembly of fixture can be automated.The configuration task is to generate a combination of stability planes, such that fixture forces in these planes will result in workpiece and fixture stability. This task can be accomplished conventionally, interactively or in a nearly fully automated manner. The advantages of an interactive or automated configuration determination are a systematic fixture design process, a reduction of necessary designers, a shortening of lead time and better match to the working conditions. In short, a significant enhancement of fixture productivity and economy can be achieved.中文译文切削技术与加工工序基本上讲,金属切削是指一个磨尖的锲形工具从有韧性的工件表面上去除一条很窄的金属。切屑是被废弃的产品,与其它工件相比切屑较短,但对于未切削部分的厚度有一定的增加。工件表面的几何形状取决于刀具的形状以及加工操作过程中刀具的路径。大多数加工工序产生不同几何形状的零件。如果一个粗糙的工件在中心轴上转动并且刀具平行于旋转中心切入工件表面,一个旋转表面就产生了,这种操作称为车削。如果一个空心的管子以同样的方式在内表面加工,这种操作称为镗孔。当均匀地改变直径时便产生了一个圆锥形的外表面,这称为锥度车削。如果刀具接触点以改变半径的方式运动,那么一个外轮廓像球的工件便产生了;或者如果工件足够的短并且支撑是十分刚硬的,那么成型刀具相对于旋转轴正常进给的一个外表面便可产生,短锥形或圆柱形的表面也可形成。速度,进给量和切削深度是经济加工的三大变量。其他的量数是攻丝和刀具材料,冷却剂和刀具的几何形状,去除金属的速度和所需要的功率依赖于这些变量。切削深度,进给量和切削速度是任何一个金属加工工序中必须建立的机械参量。它们都影响去除金属的力,功率和速度。切削速度可以定义为在旋转一周时速度记录面相对任何瞬间呈辐射状扩散的针,或是两个相邻沟槽的距离。切削深度是进入的深度和沟槽的深度。在机动车床上完成的基本操作已被介绍了。那些用单点刀具在外表面的操作称为车削。除了钻孔,铰孔,研磨内部表面的操作也是由单点刀具完成的。所有的加工工序包括车削,镗孔可以被归类为粗加工,精加工或半精加工。精加工是尽可能快而有效的去除大量材料,而工件上留下的一小部分材料用于精加工。精加工为工件获得最后尺寸,形状和表面精度。有时,半精加工为精加工留下预定的一定量的材料,它是先于精加工的。一般来说,较长的工件同时被一个或两个车床中心支撑。锥形孔,所谓的中心孔,两端被钻的工件适于车床中心-通常沿着圆柱形工件的轴线。工件接近为架的那端通常由尾架中心支撑,在靠近主轴承的那端由主轴承中心支撑或由爪盘夹紧。这种方法可以牢固的加紧工件并且能顺利地将力传给工件;由卡盘对工件提供的辅助支撑减少切削时发生的颤振趋势,如果能小心准确地采用卡盘支撑工件的方法,则可以得到精确的结果。在两个中心之间支撑工件可以得到非常精确的结果。工件的一端已被加工,那么工件便可车削了。在车床上加工另一端,中心孔充当精确定位面和承载工件重量和抵制切削力的支撑面。当工件由于任何一原因从车床上移除后,中心孔将准确地使工件回到这个车床上或另一个车床上或一个圆柱磨床上。工件不允许被卡盘和车床中心夹在主轴承上。然而首先想到的是一个快速调整卡盘上工件的方法,但这是不允许的因为在由卡盘夹持的同时也由车床中心支撑是不可能的。由车床中心提供的调整将不能持续并且爪盘的压力会损坏中心孔和车床中心,甚至是车床主轴。浮动的爪盘为上述陈述提供了一个例外,它几乎完全使用在高生产工作上,这些卡盘是真正的工作驱动者并且不为同样的目的如普通的三爪,四爪卡盘使用。而大直径的工件有时装在两个中心,它们最好有由面板夹持在主轴承尾部来顺利得到能量转换;许多车床夹头并不能足量的转换能量,虽然可以作为特殊的能量转换。作为产生形状的一种方法,机械加工是所有制造过程中最普遍使用的而且是最重要的方法。机械加工过程是一个产生形状的过程,在这过程中,驱动装置使工件上的一些材料以切屑的形式被去除。尽管在某些场合,工件无支承情况下,使用移动式装备来实现加工,但大多数的机械加工是通过既支承工件又支承刀具的装备来完成。在切削时基本工具工作的关系充分描述的方法有4个因素:刀具几何形状,切削速度和切削深度。刀具必须由适当的材料做成;它必须有一定的强度,粗糙度,硬度和抗疲劳度。刀具几何形状由面和角度描述,对每一种切削操作都是正确的。切削速度是指切削刃通过工作面的速度,它已每分钟通过的英尺数表示。对于加工效率,切削速度相对于特殊工作组合必须具有适当规模。一般来讲,工件越硬,速度越小。进给是刀具进入工件的速率。当工件或刀具旋转时,进给量的单位是英寸每转。当刀具或工件往复移动时,进给量的单位是英寸没次,总的来说,在其他相似情况下进给量与切削速度成反比。切削速度用英寸表示,是刀具进入工件的距离表示的,它是指车削时屑片的宽度或是直线切削时屑片的厚度。粗加工时切削深度比精加工的切削深度大。在金属切削作业中热量产生于主要和第二变形区而这些结果导致了复杂温度遍布于刀具,工件和屑片。一个典型的等温先如图所示,它可以看出正如预测的,当工件材料经历主要变形,被减切时,有一个非常大温度梯度遍布于屑片的整个宽度。当第二变形区的屑片还有一小段距离就达到了最大温度。因为几乎所有的工作都以金属切削转化为热量而完成,可以预测去除每一单位体积的金属所增加的能量消耗将会提高切削温度。因此在所有其他参数不变,前角变大时,将减少去除每单位体积金属的能量和切削温度。当考虑到增加未形成屑片的厚度和速度,情况就更复杂了。增加切削厚度往往会大大影响热量传给工件,刀具的多少,而且会使屑片停留在一个固定数额,同时切削温度的变化也会很小,可是增加切削速度会减少传递给工件的热量,同时这将增大屑片主要变形的温升。此外,第二变形区是比较小的,在这个变形区会提高温度。切削参数的其他变化几乎不影响去除每单位体积的能量消耗和切削温度。因此已经表明,即使是切削温度的小规模变化对刀具磨损率也有重大影响,从切削数据来估计切削温度是恰当的。检测高速钢工具最直接最准确的方法,特伦特给出了高
- 温馨提示:
1: 本站所有资源如无特殊说明,都需要本地电脑安装OFFICE2007和PDF阅读器。图纸软件为CAD,CAXA,PROE,UG,SolidWorks等.压缩文件请下载最新的WinRAR软件解压。
2: 本站的文档不包含任何第三方提供的附件图纸等,如果需要附件,请联系上传者。文件的所有权益归上传用户所有。
3.本站RAR压缩包中若带图纸,网页内容里面会有图纸预览,若没有图纸预览就没有图纸。
4. 未经权益所有人同意不得将文件中的内容挪作商业或盈利用途。
5. 人人文库网仅提供信息存储空间,仅对用户上传内容的表现方式做保护处理,对用户上传分享的文档内容本身不做任何修改或编辑,并不能对任何下载内容负责。
6. 下载文件中如有侵权或不适当内容,请与我们联系,我们立即纠正。
7. 本站不保证下载资源的准确性、安全性和完整性, 同时也不承担用户因使用这些下载资源对自己和他人造成任何形式的伤害或损失。

人人文库网所有资源均是用户自行上传分享,仅供网友学习交流,未经上传用户书面授权,请勿作他用。