Santana3000轿车制动系统的设计【5张图纸】【优秀】
收藏
资源目录
压缩包内文档预览:
编号:271910
类型:共享资源
大小:1.07MB
格式:RAR
上传时间:2014-04-10
上传人:上***
认证信息
个人认证
高**(实名认证)
江苏
IP属地:江苏
80
积分
- 关 键 词:
-
santana3000
轿车
制动
系统
设计
图纸
优秀
优良
- 资源描述:
-
Santana3000轿车制动系统的设计
47页 21000字数+说明书+开题报告+任务书+5张CAD图纸
Santana3000轿车制动系统的设计开题报告.doc
Santana3000轿车制动系统的设计论文.doc
任务书.doc
内封评语及任务书.doc
制动钳体装配图.dwg
支架.dwg
管路总成图.dwg
钳体.dwg
鼓式制动器装配总成.dwg
目录
摘要I
AbstractII
第1章 绪 论1
1.1 汽车制动系统研究的目的和意义1
1.2 汽车制动系统的研究现状和发展趋势2
1.3 对汽车制动系的研究主要内容和设计要求6
第2章 制动系统总体方案的确定8
2.1 制动系统的分类及作用8
2.2 制动系统的主要参数的确定及计算9
2.2.1 制动力与制动力分配系数10
2.2.2 同步附着系数11
2.2.3 制动器最大制动力矩12
2.2.4 制动器因数12
2.3 本章小结14
第3章 制动驱动机构的设计15
3.1 制动驱动机构的结构型式选择15
3.2 液压制动驱动机构的设计计算16
3.2.1 制动轮缸直径与工作容积16
3.2.2 制动主缸直径与工作容积17
3.2.3制动踏板力与踏板的行程18
3.3 本章小结19
第4章 制动器设计和计算20
4.1 制动器方案确定20
4.1.1鼓式制动器20
4.1.2 盘式制动器22
4.2 鼓、盘式制动器的主要参数的确定23
4.2.1 鼓式制动器的结构参数和摩擦系数23
4.2.2 盘式制动器主要参数的确定25
4.3 制动器的设计与计算26
4.3.1 制动蹄摩擦面的压力分布规律及径向变形规律26
4.3.2制动蹄片上的制动力矩28
4.3.3 摩擦衬块的磨损特性计算28
4.3.4 制动器热容量和温升的核算31
4.3.5 盘式制动器制动力矩的计算32
4.3.6 驻车制动计算33
4.4 制动器主要零部件的结构设计35
4.4.1 制动鼓35
4.4.2 制动蹄36
4.4.3 制动底板37
4.4.4 制动蹄的支承37
4.4.5 制动轮缸37
4.4.6 制动盘38
4.4.7 制动钳38
4.4.8 制动块38
4.4.9 摩擦材料39
4.4.10 制动器间隙的调整方法及响应机构39
4.5 本章小结40
结 论41
致 谢42
参考文献43
附录A44
附录B55
摘 要
国内汽车市场迅速发展,而轿车是汽车发展的方向。然而随着汽车保有量的增加,带来的安全问题也越来越引起人们的注意,而制动系统则是汽车主动安全的重要系统之一。因此,如何开发出高性能的制动系统,为安全行驶提供保障是我们要解决的主要问题。另外,随着汽车市场竞争的加剧,如何缩短产品开发周期、提高设计效率,降低成本等,提高产品的市场竞争力,已经成为企业成功的关键。
本说明书主要设计了santana3000轿车制动系统。首先介绍了汽车制动系统的发展、结构、分类,并通过对鼓式制动器和盘式制动器的结构及优缺点进行分析。最终确定方案采用液压双回路前盘后鼓式制动器。除此之外,它还对前后制动器、制动主缸进行设计计算,主要部件的参数选择及制动管路布置形式等的设计过程。
关键词 制动;鼓式制动器;盘式制动器;液压;制动主缸

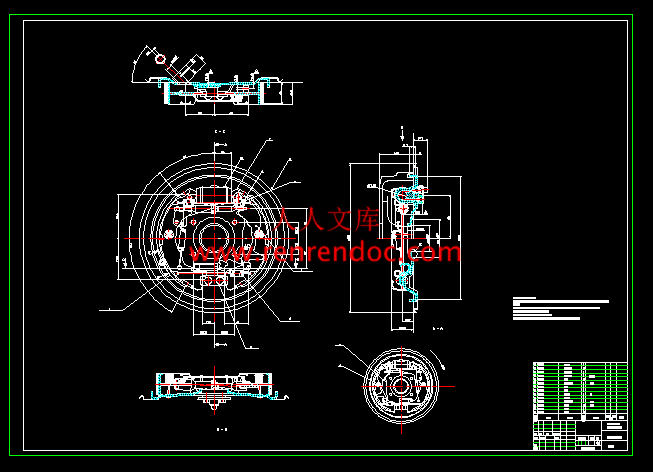

- 内容简介:
-
哈尔滨工业大学华德应用技术学院毕业设计(论文)开题报告题 目:Santana3000 轿车制动系统的设计系 (部) 机电工程系 专 业 机械设计制造及其自动化学 生 侯文强 学 号 1099512211 班 号 0995122 指导教师 王振波 开题报告日期 哈工大华德学院说 明一、开题报告应包括下列主要内容:1通过学生对文献论述和方案论证,判断是否已充分理解毕业设计(论文)的内容和要求。2进度计划是否切实可行。3是否具备毕业设计所要求的基础条件。4预计研究过程中可能遇到的困难和问题,以及解决的措施。5主要参考文献。二、如学生首次开题报告未通过,需在一周内再进行一次。三、开题报告由指导教师填写意见、签字后,统一交所在系(部)保存,以备检查。指导教师评语: 1. 指导教师签字: 检查日期: 一、课题研究现状,选题的目的和意义现在制动系统早已经是汽车必备的重要装置之一,制动系统的好坏直接影响到驾驶员的生命安全。制动系统的稳定性和工作可靠性十分重要。此外防水性,散热性和操作性都对车辆的制动有着多种的影响。ABS出现后提高了汽车在制动过程中的方向稳定性和转向操纵能力,缩短了制动距离的,防止车轮完全抱死,减少了事故的发生率。我设计的制动系统的目的就是为了更好的保护驾驶员的生命安全,减少汽车在制动时发生事故,更快更好的达到有效制动。2、 国内外在该方向的研究现状及分析目前,国内汽车的主流发展方向为低成本控制,所以在制动方面的应用多是传统的制动控制系统,即均匀分配油液压力制动方式。ABS也是只是基本的按照每个制动器的需要时对油液压力进行调节。而随着电子技术和一些智能控制技术的发展,在ABS的基础上也相继的出现了驱动防滑系统(ASR),电子控制制动系统(EBS)和全电路制动(BBW)。随着技术的进步,预计不久全电制动控制系统会真正代替传统的以液压为主的制动控制系统。三、设计(论文)的基本内容Santana 3000作为轿车,要求制动系统制动平顺,制动距离更短,制动过程中避免因制动效能过高而导致的车轮抱死的情况,满足汽车的安全性和乘员舒适性,因此制动系统的良好设计有利于提高汽车的整体性能。所以主要基本内容是设计完成汽车制动系统,包括制动系统的类型选择、总体布置形式,制动系统各零部件的结构设计和性能分析。四、研究方案及预期达到的目标1、确定总体方案2、确定制动系统主要参数3、确定驱动机构的形式及其制动器的设计和计算4、绘制设计图及其撰写说明书5、进行审查发现问题并完善设计6、设计完成汽车制动系统,提交设计五、为完成课题已具备和所需的条件 具备机械专业的相关理论知识,查询翻阅了大量有关汽车制动以及Santana3000轿车制动系统的相关资料对所要设计的制动系统有了深入的了解。六、预计研究过程中可能遇到的困难和问题,以及解决的措施1、制动系统确保具有足够的制动效能,工作可靠,保证汽车在制动的时候不丧失操纵性和方向性,并且操纵轻便,具有良好的随动性。2、通过对比分析国内、外制动系统的技术原理、设计准则和应用状况,力争保证设计的制动系统符合国内市场的应用以及未来发展的趋势。七、进度安排1 调研、资料收集、完成开题报告 (第1-2周)2 轿车制动系统的设计的现有技术查询(第3-4周)3 Santana3000制动系统的设计的原理及理论分析(第5-6周)4 Santana3000制动系统的设计的计算与校核(第7-9周)5 撰写论文撰写及绘图(第10-11周)6 毕业设计审核、修改(第12周)7 毕业设计答辩准备及答辩 (第13周)八、参考文献1 李鹏,李洪涛.汽车制动系统分析.商情,2008年35期:23282 齐志鹏.汽车制动系统的结构与原理.第5版,人民邮电出版社,2008,6:21373 魏春源.汽车工程手册.北理工出版社.2009: 35424 郭列炎.智能盘式制动器的研制.西安科技大学硕士学位论文,2006: 32495 刘惟信.汽车制动系统的结构分析与设计计算.清华大出版社,2009,68896 王望予.汽车设计.第7版,北京机械工业出版社,2007:12257 Rudolf Limpert.BRAKE DESIGN.WarrendalePA.15096,USA:SAE,Inc.2008:3258 John Fenton.Hand Book of Vehicle Design Analysis.Warrendale PA.USA:Society of Autmotuve Engineers,Inc.2009:25429 程龙.制动器设计说明.内蒙古大学硕士学位论文,2008: 355210 张欢.制动系统设计说明.北京科技大学硕士学位论文,2009: 123511 田夏.桑塔纳3000轿车使用与维护手册.北京:机械工业出版社,2008.2::32 6512 张洪欣.汽车设计.北京:机械工业出版社.2005:2 23九、备注哈尔滨工业大学华德应用技术学院毕业设计(论文)摘 要国内汽车市场迅速发展,而轿车是汽车发展的方向。然而随着汽车保有量的增加,带来的安全问题也越来越引起人们的注意,而制动系统则是汽车主动安全的重要系统之一。因此,如何开发出高性能的制动系统,为安全行驶提供保障是我们要解决的主要问题。另外,随着汽车市场竞争的加剧,如何缩短产品开发周期、提高设计效率,降低成本等,提高产品的市场竞争力,已经成为企业成功的关键。本说明书主要设计了santana3000轿车制动系统。首先介绍了汽车制动系统的发展、结构、分类,并通过对鼓式制动器和盘式制动器的结构及优缺点进行分析。最终确定方案采用液压双回路前盘后鼓式制动器。除此之外,它还对前后制动器、制动主缸进行设计计算,主要部件的参数选择及制动管路布置形式等的设计过程。关键词制动;鼓式制动器;盘式制动器;液压;制动主缸AbstractThe rapid development of the domestic vehicle market, saloon car is an important tendency of vehicle. However, with increasing of vehicle, security issues are arising from increasingly attracting attention, the braking system is one of important system of active safety. Therefore, how to design a high-performance braking system, to provide protection for safe driving is the main problem we must solve. In addition, with increasing competition of vehicle market, how to shorten the product development cycle, to improve design efficiency and to lower costs, to improve the market competitiveness of products, and has become a key to success of enterprises.This paper mainly introduces the design of braking system of the santana2000 type of car. Fist of all, braking systems development, structure and category are shown, and according to the structures, virtues and weakness of drum brake and disc brake, analysis is done. At last, the plan adopting hydroid two-backway brake with front disc and rear drum. Besides, this paper also introduces the designing process of front brake and rear brake, braking cylinder, parameters choice of main components braking and channel settings.Keywords braking; brake drum; brake disc; hydroid pressure;braking cylinder目录摘要IAbstractII第1章 绪 论11.1 汽车制动系统研究的目的和意义11.2 汽车制动系统的研究现状和发展趋势21.3 对汽车制动系的研究主要内容和设计要求6第2章 制动系统总体方案的确定82.1 制动系统的分类及作用82.2 制动系统的主要参数的确定及计算92.2.1 制动力与制动力分配系数102.2.2 同步附着系数112.2.3 制动器最大制动力矩122.2.4 制动器因数122.3 本章小结14第3章 制动驱动机构的设计153.1 制动驱动机构的结构型式选择153.2 液压制动驱动机构的设计计算163.2.1 制动轮缸直径与工作容积163.2.2 制动主缸直径与工作容积173.2.3制动踏板力与踏板的行程183.3 本章小结19第4章 制动器设计和计算204.1 制动器方案确定204.1.1鼓式制动器204.1.2 盘式制动器224.2 鼓、盘式制动器的主要参数的确定234.2.1 鼓式制动器的结构参数和摩擦系数234.2.2 盘式制动器主要参数的确定254.3 制动器的设计与计算264.3.1 制动蹄摩擦面的压力分布规律及径向变形规律264.3.2制动蹄片上的制动力矩284.3.3 摩擦衬块的磨损特性计算284.3.4 制动器热容量和温升的核算314.3.5 盘式制动器制动力矩的计算324.3.6 驻车制动计算334.4 制动器主要零部件的结构设计354.4.1 制动鼓354.4.2 制动蹄364.4.3 制动底板374.4.4 制动蹄的支承374.4.5 制动轮缸374.4.6 制动盘384.4.7 制动钳384.4.8 制动块384.4.9 摩擦材料394.4.10 制动器间隙的调整方法及响应机构394.5 本章小结40结 论41致 谢42参考文献43附录A44附录B55-40-第1章 绪 论 1.1 汽车制动系统研究的目的和意义汽车制动系是用于使行驶中的汽车减速或停车,使下坡行驶的汽车车速保持稳定以及使已停止的汽车停在原地(包括在斜坡上)驻留不动的机构,汽车制动系直接影响着汽车行驶的安全性和停车的可靠性。随着高速公路的迅速发展和车速的提高以及车流密度的日益增大,为了保证行车安全,停车可靠,汽车制动系的工作可靠性显得日益重要。也只有制动性能良好,制动系工作可靠的汽车才能充分发挥其性能。汽车制动系至少应有两套独立的制动装置,即行车制动装置和驻车制动装置,重型汽车或经常在山区行驶的汽车要增设应急制动装置及辅助制动装置,牵引汽车还应有自动制动装置。行车制动装置用于使行驶中的汽车强制减速或停车,并使汽车在下断坡时保持适当的稳定的车速。其驱动机构常采用双回路或多回路机构,以保证其工作可靠。驻车制动装置用于使汽车可靠而无时间限制地停驻在一定位置甚至在斜坡上,它也有助于汽车在坡路上起步。驻车制动装置应采用机械式驱动机构而不用液压或气压驱动,以免其发生故障。应急制动装置用于当行车制动装置意外发生故障而失效时,则可利用其机械力源(如强力压缩弹簧)实现汽车制动。应急制动装置不必是独立的制动系统,它可利用行车制动装置或驻车制动装置的某些制动器件。应急制动装置也不是每车必备的,因为普通的手力驻车制动器也可以起到应计制动的作用。辅助制动装置用在山区行驶的汽车上,利用发动机排气制动或电涡流制动等的辅助制动装置,可使汽车下长坡时长时间而持续地减低或保持稳定车速,并减轻或解除行车制动器的负荷。1.2 汽车制动系统的研究现状和发展趋势1)制动控制系统的历史 最原始的制动控制只是驾驶员操纵一组简单的机械装置向制动器施加作用力,这时的车辆的质量比较小,速度比较低,机械制动虽已满足车辆制动的需要,但随着汽车自质量的增加,助力装置对机械制动器来说已显得十分必要。这时,开始出现真空助力装置。1932年生产的质量为2860kg的凯迪拉克V16车四轮采用直径419.1mm的鼓式制动器,并有制动踏板控制的真空助力装置。林肯公司也于1932年推出V12轿车,该车采用通过四根软索控制真空加力器的鼓式制动器。随着科学技术的发展及汽车工业的发展,尤其是军用车辆及军用技术的发展,车辆制动有了新的突破,液压制动是继机械制动后的又一重大革新。Duesenberg Eight车率先使用了轿车液压制动器。克莱斯勒的四轮液压制动器于1924年问世。通用和福特分别于1934年和1939年采用了液压制动技术。到20世纪50年代,液压助力制动器才成为现实。20世纪80年代后期,随着电子技术的发展,世界汽车技术领域最显著的成就就是防抱制动系统(ABS)的实用和推广。ABS集微电子技术、精密加工技术、液压控制技术为一体,是机电一体化的高技术产品。它的安装大大提高了汽车的主动安全性和操纵性。防抱装置一般包括三部分:传感器、控制器(电子计算机)与压力调节器。传感器接受运动参数,如车轮角速度、角加速度、车速等传送给控制装置,控制装置进行计算并与规定的数值进行比较后,给压力调节器发出指令。2)制动控制系统的现状当考虑基本的制动功能量,液压操纵仍然是最可靠、最经济的方法。即使增加了防抱制动(ABS)功能后,传统的“油液制动系统”仍然占有优势地位。但是就复杂性和经济性而言,增加的牵引力控制、车辆稳定性控制和一些正在考虑用于“智能汽车”的新技术使基本的制动器显得微不足道。传统的制动控制系统只做一样事情,即均匀分配油液压力。当制动踏板踏下时,主缸就将等量的油液送到通往每个制动器的管路,并通过一个比例阀使前后平衡。而ABS或其他一种制动干预系统则按照每个制动器的需要时对油液压力进行调节。目前,车辆防抱制动控制系统(ABS)已发展成为成熟的产品,并在各种车辆上得到了广泛的应用,但是这些产品基本都是基于车轮加、减速门限及参考滑移率方法设计的。方法虽然简单实用,但是其调试比较困难,不同的车辆需要不同的匹配技术,在许多不同的道路上加以验证;从理论上来说,整个控制过程车轮滑移率不是保持在最佳滑移率上,并未达到最佳的制动效果。滑移率控制的难点在于确定各种路况下的最佳滑移率,另一个难点是车辆速度的测量问题,它应是低成本可靠的技术,并最终能发展成为使用的产品。对以滑移率为目标的ABS而言,控制精度并不是十分突出的问题,并且达到高精度的控制也比较困难;因为路面及车辆运动状态的变化很大,多种干扰影响较大,所以重要的问题在于控制的稳定性,即系统鲁棒性,应保持在各种条件下不失控。防抱系统要求高可靠性,否则会导致人身伤亡及车辆损坏。因此,发展鲁棒性的ABS控制系统成为关键。现在,多种鲁棒控制系统应用到ABS的控制逻辑中来。除传统的逻辑门限方法是以比较为目的外,增益调度PID控制、变结构控制和模糊控制是常用的鲁棒控制系统,是目前所采用的以滑移率为目标的连续控制系统。模糊控制法是基于经验规则的控制,与系统的模型无关,具有很好的鲁棒性和控制规则的灵活性,但调整控制参数比较困难,无理论而言,基本上是靠试凑的方法。然而对大多数基于目标值的控制而言,控制规律有一定的规律。车轮的驱动打滑与制动抱死是很类似的问题。在汽车起动或加速时,因驱动力过大而使驱动轮高速旋转、超过摩擦极限而引起打滑。此时,车轮同样不具有足够的侧向力来保持车辆的稳定,车轮切向力也减少,影响加速性能。由此看出,防止车轮打滑与抱死都是要控制汽车的滑移率,所以在ABS的基础上发展了驱动防滑系统(ASR)。ABS只有在极端情况下(车轮完全抱死)才会控制制动,在部分制动时,电子制动使可控制单个制动缸压力,因此反应时间缩短,确保在任一瞬间得到正确的制动压力。近几年电子技术及计算机控制技术的飞速发展为EBS的发展带来了机遇。德国自20世纪80年代以来率先发展了ABS/ASR系统并投入市场,在EBS的研究与发展过程中走到了世界的前列。3)制动控制系统的发展今天,ABS/ASR已经成为欧美和日本等发达国家汽车的标准设备。车辆制动控制系统的发展主要是控制技术的发展。一方面是扩大控制范围、增加控制功能;另一方面是采用优化控制理论,实施伺服控制和高精度控制。经过了一百多年的发展,汽车制动系统的形式已经基本固定下来。随着电子,特别是大规模、超大规模集成电路的发展,汽车制动系统的形式也将发生变化。如凯西-海斯(K-H)公司在一辆实验车上安装了一种电-液(EH)制动系统,该系统彻底改变了制动器的操作机理。通过采用4个比例阀和电力电子控制装置,K-H公司的EBM就能考虑到基本制动、ABS、牵引力控制、巡航控制制动干预等情况,而不需另外增加任何一种附加装置。EBM系统潜在的优点是比标准制动器能更加有效地分配基本制动力,从而使制动距离缩短5%。一种完全无油液、完全的电路制动BBW(Brake-By-Wire)的开发使传统的液压制动装置成为历史1。 4) 全电路制动(BBW)BBW是未来制动控制系统的L发展方向。全电制动不同于传统的制动系统,因为其传递的是电,而不是液压油或压缩空气,可以省略许多管路和传感器,缩短制动反应时间。全电制动的结构比较简单。其主要包含以下部分:(a)电制动器。其结构和液压制动器基本类似,有盘式和鼓式两种,制动力供给装置是电动机;(b)电制动控制单元(ECU)。接收制动踏板发出的信号,控制制动器制动;接收驻车制动信号,控制驻车制动;接收车轮传感器信号,识别车轮是否抱死、打滑等,控制车轮制动力,实现防抱死和驱动防滑。由于各种控制系统如卫星定位、导航系统,自动变速系统,无级转向系统,悬架系统等的控制系统与制动控制系统高度集成,所以ECU还得兼顾这些系统的控制;(c)轮速传感器。准确、可靠、及时地获得车轮的速度;(d)线束。给系统传递能源和电控制信号;(e)电源。为整个电制动系统提供能源。与其他系统共用。可以是各种电源,也包括再生能源。从结构上可以看出这种全电路制动系统具有其他传统制动控制系统无法比拟的优点:(a)整个制动系统结构简单,省去了传统制动系统中的制动油箱、制动主缸、助力装置。液压阀、复杂的管路系统等部件,使整车质量降低;(b)制动响应时间短,提高制动性能;(c)无制动液,维护简单;(d)系统总成制造、装配、测试简单快捷,制动分总成为模块化结构;(e)采用电线连接,系统耐久性能良好;(f)易于改进,稍加改进就可以增加各种电控制功能。全电制动控制系统是一个全新的系统,给制动控制系统带来了巨大的变革,为将来的车辆智能控制提供条件。但是,要想全面推广,还有不少问题需要解决:电制动控制系统首先用在混合动力制动系统车辆上,采用液压制动和电制动两种制动系统。这种混合制动系统是全电制动系统的过渡方案。由于两套制动系统共存,使结构复杂,成本偏高。随着技术的进步,上述的各种问题会逐步得到解决,全电制动控制系统会真正代替传统的以液压为主的制动控制系统。5) 结论综上所述:现代汽车制动控制技术正朝着电子制动控制方向发展。全电制动控制因其巨大的优越性,将取代传统的以液压为主的传统制动控制系统。同时,随着其他汽车电子技术特别是超大规模集成电路的发展,电子元件的成本及尺寸不断下降。汽车电子制动控制系统将与其他汽车电子系统如汽车电子悬架系统、汽车主动式方向摆动稳定系统、电子导航系统、无人驾驶系统等融合在一起成为综合的汽车电子控制系统,未来的汽车中就不存在孤立的制动控制系统,各种控制单元集中在一个ECU中,并将逐渐代替常规的控制系统,实现车辆控制的智能化。但是,汽车制动控制技术的发展受整个汽车工业发展的制约。有一个巨大的汽车现有及潜在的市场的吸引,各种先进的电子技术、生物技术、信息技术以及各种智能技术才不断应用到汽车制动控制系统中来。同时需要各种国际及国内的相关法规的健全,这样装备新的制动技术的汽车就会真正应用到汽车的批量生产中。1.3 对汽车制动系的研究主要内容和设计要求本设计研究的主要内容:设计完成汽车制动系统,包括制动系统的类型选择、总体布置形式,制动系统各零部件的结构设计和性能分析。设计要求:(1)各项性能指标除应满足设计任务书的规定和国家要求、法规制定的有关要求外,也要考虑到我的制动系统应符合现在国内汽车市场的低成本和高性能的要求。(2)具有足够的制动效能,包括行车制动效能和驻车制动效能。行车制动效能是由在一定的制动初速度下及最大踏板力下的制动减速器和制动距离两项指标来评定的。制动距离直接影响着汽车的行驶安全性。(3)工作可靠。为此,设计两套系统:行车制动系统和驻车制动系统,且它们的驱动机构是独立的,而行车制动装置的制动驱动机构至少应有两套独立的管路,当其中一套失效时,另一套应保证汽车制动效能不低于正常值的30%;驻车制动装置应采用工作可靠的机械式制动驱动机构。(4)制动效能热稳定性好。汽车的高速制动、短时间的频繁重复制动,尤其使下长坡时的连续制动,均会引起制动器的温升过快,温度过高。提高摩擦材料的高温摩擦稳定性,增大制动鼓、盘的热容量,改善其散热性或采用强制冷却装置,都是提高抗热衰退的措施。(5)制动效能的水稳定性好。制动器摩擦表面浸水后,会因水的润滑作用而使摩擦副的摩擦系数急剧减小而发生所谓的“水衰退”现象。一般规定在出水后反复制动515次,即应恢复其制动效能。良好的摩擦材料的吸水率低,其摩擦性能恢复迅速。另外也应防止泥沙等进入制动器摩擦副工作表面,否则会使制动效能降低并加速磨损。(6)制动时的汽车操纵稳定性好。即以任何速度制动,汽车均不应失去操纵性和方向稳定性。通过ABS来调节前后轮的制动油压来实现。为此,汽车前、后轮制动器的制动力矩应有适当的比例,最好能随各轴间载荷转移情况而变化;同一车轴上的左、右车轮制动器的制动力矩应相同。否则当前轮抱死而侧滑时,将失去操纵性;当后轮抱死而侧滑甩尾时,会失去方向稳定性;当左、右轮的制动力矩差值超过15%时,会在制动时发生汽车跑偏。(7)制动踏板和手柄的位置和行程符合人机工程学要求,即操作仪方便性好,操纵轻便、舒适,减少疲劳。(8)制动系的机件应使用寿命长,制造成本低;对摩擦材料的选择也应考虑到环保要求,应力求减小制动时飞散到大气中的有害于人体的石棉纤维。(9)制动时不应产生振动和噪声。(10)与悬架、转向装置不产生运动干涉,在车轮跳动或汽车转向时不会引起自行制动。(11)制动系中应有音响或光信号等警报装置,以便能及时发现制动驱动机件的故障和功能失效;制动系中应有必要的安全装置,在行驶中挂车一旦脱挂,亦应有安全装置驱使驻车制动将其停驻。(12)能全天候使用。气温高时液压制动管路不应有气阻现象;气温低时,气制动管路不应出现结冰现象。(13)作用滞后的时间要尽可能短,包括从制动踏板开始动作至达到给定制动效能水平所需的时间和从放开踏板至完全解除制动的时间。第2章 制动系统总体方案的确定2.1 制动系统的分类及作用制动系统按功用分为行车制动系统、驻车制动系统、应急制动系统和辅助制动系统。汽车制动系至少应有前两套制动系统,而重型汽车或者经常在山区行驶的汽车要增设应急制动系统及辅助制动系统。行车制动系统用于使行驶中的汽车强制减速或停车,并使汽车在下短坡时保持适当的稳定车速。其驱动机构常采用双回路或多回路结构,以保证其工作可靠。驻车制动系统使已停驶的汽车驻留在原地不动的一套装置。应采用机械式驱动机构而不用液压或气压驱动,以免其产生故障。现代汽车对于机械控制电子化的运用已经越来越广泛,从基本电子方向助力到复杂主动转向比例控制这些以往都是采用液压以及机械控制为主的部分,也逐渐向电子化控制靠拢,驾驶者能通过直接机械连接来自主控制的部分已经越来越少了。应急制动系统也叫第二制动系统,是在用于行车制动系统发生意外故障而失效时,保证汽车仍能实现减速或停车的一套装置。应急系统也不是每车必备的,因为普通的手力驻车装置也可起到应急制动的作用。辅助制动系统通常安装在常行驶于山区的汽车上,利用发动机排气或者电涡流制动等的辅助制动装置,可使汽车下长坡时长时间而持续地减低或保持车速,并减轻或解除行车制动器的负荷。 按制动系统的制动能源分类(1) 人力制动系统以驾驶员的肌体作为惟一制动能源的制动系统。(2) 动力制动系统完全靠由发动机的动力转化而成的气压或液压形式的势能进行制动的制动系统。(3) 伺服制动系统兼用人力和发动机进行制动的制动系统。 人力目前仍是国内中低档车最为适合的制动能源,它符合了降低成本同时又有可靠的性能保证。所以我选择人力为我的制动系统的能源。按照能量的传输方式,制动系统又可分为机械式、液压式、气压式和电磁式。在行车制动系统上我选用液压式,反应迅速,性能好。而在驻车制动系统上我选用机械式,性能稳定,故障少。通过以上的分析,本次设计围绕行车制动系统和驻车制动系统设计,而应急系统为了节省成本就利用现有的驻车系统来代替。本次设计的汽车使用范围是在城市内行驶,对于城市外范围不予考虑,所以不设计辅助制动系统(如图2-1所示)。如图2-1可见,制动系统包括供能装置;控制装置;传动装置;制动器。制动系统一般由制动操纵机构和制动器两个主要的部分组成。2.2 制动系统的主要参数的确定及计算制动系统设计中必须严格按照车辆整车参数进行计算设计,在制动器设计中需预先给定的整车参数有(见表2-1)。而对汽车制动性能有重要影响的制动系参数有:制动力及其分配系数、同步附着系数、制动器最大制动力矩与制动器因数等。表2-1 制动系统整车参数:整车质量空载满载1550kg2000kg质心位置ab1.35m1.25m质心高度空载满载轴 距0.95m0.85m2.6m其 他最高车速车轮工作半径轮 胎同步附着系数160km/h370mm195/60R14 85H=0.6图2-1 总体布置图2.2.1 制动力与制动力分配系数根据公式: (2-1)得:2.2.2 同步附着系数同步附着系数是汽车制动性能的一个重要参数,由汽车结构参数所决定的。它是制动器动力分配系数为b的汽车的实际前、后制动器制动力分配线,简称b线,与汽车理想的前、后制动器动力分配曲线I线的交点。对于前、后制动器制动力为固定比值的汽车,只有在附着系数等于同步附着系数的路面上,汽车前、后车轮才会同时抱死,当汽车在不同w植的路面上制动时,可能出现以下3种情况。(1)当时:制动时总是前轮先抱死,这是一种稳定工况,单失去转向能力。(2)当时:制动时总是后轮先抱死,这时容易发生后轴侧滑而使汽车失去方向稳定性。(3)当时:制动时前、后轮同时抱死,是一种稳定工况,但也失去转向能力。现代的道路条件大为改善,汽车行驶速度也大为提高,因此汽车因制动时后轮先抱死的后果十分严重。由于车速高,它不仅会引起侧滑甩尾甚至会发生调头而丧失操纵稳定性,因此后轮先抱死的情况十分严重,所以现在各类汽车的值都均有增大趋势。轿车0.6;货车0.5。 (2-2)故取=0.62.2.3 制动器最大制动力矩由轮胎与路面附着系数所决定的前后轴最大附着力矩: (2-3)式中 该车所能遇到的最大附着系数;q制动强度;车轮有效半径;后轴最大制动力矩;G汽车满载质量;L汽车轴距。q=0.66故后轴=1.57Nmm后轮的制动力矩为=0.785Nmm前轴= T=0.67/(10.67)1.57=3.2Nmm前轮的制动力矩为3.2/2=1.6Nmm2.2.4 制动器因数制动器因数定义为在制动鼓或制动盘的作用半径上所产生的摩擦力与输入力之比,即 (2-4) 式中 制动器的摩擦力矩; 制动盘或制动鼓的作用半径; 输入力,一般取加于两制动蹄张开力的平均值输入力。对于钳盘式制动器,设两侧制动块对制动盘的压紧力均为P,即制动盘在其两侧的作用半径上所受的摩擦力为2,此处为盘与制动衬块饿摩擦系数,于钳盘式制动器的制动器因数为 (2-5)f取0.5得BF=20.5=1对于鼓式制动器,当时,则有 如图2-2 ,假设在张力P的作用下,制动蹄的摩擦衬片与鼓之间作用力的合力N的B点上。这一法向力引起作用于制动蹄衬片上的摩擦力为,为摩擦系数。a,b,c,h,R及a为结构尺寸。对领题绕支点A的力矩平衡方程,即 (2-6)由上式得到领蹄的制动蹄因数为图2-2 受力图 (2-7)代入参数得:=0.79当制动鼓逆转时,上述制动蹄则又成为从蹄,这时摩擦力的方向相反,用上述分析方法,同样可得出从蹄绕支点A的力矩平衡方程,即 (2-8)由上式得从蹄的制动蹄因数为 (2-9)代入参数得:=0.48 2.3 本章小结本章先选定了要设计的制动系统的类型。然后确定了本设计的汽车的技术参数,通过这些参数,计算出了要设计的制动系统的制动力、制动力分配系数、同步附着系数、制动器最大制动力矩、制动器因数等重要参数。这些参数是保证该制动系统正常工作的前提。第3章 制动驱动机构的设计3.1 制动驱动机构的结构型式选择简单制动系即人力制动系,是靠司机作用于制动踏板上或手柄上的力作为制动力源而力的传递方式,又有机械式和液压式,一般的驻车制动系统为机械式,行车制动系统为液压式。驻车制动系统的机械式为杆系传力,其机构简单,造价低廉,而且性能稳定。由驾驶员拉动手柄,通过钢丝绳传递力到后驻车制动器,产生驻车效果。行车制动系统为液压式,作用滞后时间0.2s,工作压力10MPa。工作原理可用如图3-1所示的一种简单的液压制动系统工作原理示意图来说明。 1制动踏板;2推杆;3制动活塞;4制动主缸;5油管;6制动轮缸;7轮缸活塞;8制动鼓;9摩擦片;10制动蹄;11制动底板;12支承销;13制动蹄回位弹簧图3-1制动装置原理图一个以内圆柱面为工作表面的金属制动鼓8固定在车轮轮毂上,随车轮一同旋转。在固定不动的制动底板11上有两个支承销12,支承着两个弧形制动蹄10的下端。制动蹄的外圆柱面上装有摩擦片9。制动底板上还还装有液压制动轮缸6,用油管5与装在车驾上的液压制动主缸4相连通。主缸活塞3可由驾驶员通过制动踏板机构来操纵。 工作原理为:驾驶员踩下踏板时,作用力由活塞推杆2传给活塞3,活塞就移动,克服主缸内部的作用力,油液由主缸流出经油管5到达制动器的轮缸,使制动轮缸活塞推动制动蹄产生制动。钳盘式制动器原理一样。为防止空气进入制动系油液系统,当放松制动踏板时,制动系的油液系统应保持一定的剩余压力(0.5kg/cm)。3.2 液压制动驱动机构的设计计算3.2.1 制动轮缸直径与工作容积前轮制动轮缸直径与工作容积的设计计算 (3-1)式中 p考虑到制动力调节装置作用下的轮缸或灌录液压,p=8Mp12Mp.取p=10Mp查Santana3000轿车使用与维护手册得:P=19625N得: =50mm根据GB7524-87标准规定的尺寸中选取,因此轮缸直径为50mm。一个轮缸的工作容积 (3-2)式中 dw一个轮缸活塞的直径;n 轮缸活塞的数目;一个轮缸完全制动时的行程: (3-3)取=2mm消除制动蹄与制动鼓间的间隙所需的轮缸活塞行程。由于摩擦衬片变形而引起的轮缸活塞。,分别为鼓式制动器的变形与制动鼓的变形而引起的轮缸活塞行程。得:一个轮缸的工作容积=3925mm全部轮缸的工作容积: (3-4)式中 m轮缸的数目。V=2V+2V=22826+23925=13502mm3.2.2 制动主缸直径与工作容积制动主缸应有的工作容积 (3-5)式中 V 全部轮缸的总的工作容积;V制动软管在掖压下变形而引起的容积增量;V=13502mm轿车的制动主缸的工作容积可取为=1.1V=1.113502=14852.2 mm主缸直径和活塞行程S (3-6)一般S=(0.8-1.2)d取: S= d得: =26.65mm根据GB7524-87标准规定的尺寸中选取,因此主缸直径为28mm。=28mm3.2.3制动踏板力与踏板的行程制动踏板力可用下式验算: (3-7)式中 dm制动主缸活塞直径; p制动管路的液压; 制动踏板机构传动比,=4; h制动踏板机构及制动主缸的机械效率,可取h=0.9。求得:=1710N500N-700N所以需要加装真空助力器。 (3-8)式中 :真空助力比,取4。=1710/4=427.5N500N-700N所以符合要求 (3-9)式中 m1主缸中推杆与活塞的间隙,取2mm ; m2主缸活塞空行程,即主缸活塞由不工作的极限位置到使其皮碗完全封堵主缸上的旁通孔的行程,取2mm 。求得:=128mm150mm,符合设计要求。3.3 本章小结 这一章进行了液压驱动机构的设计,通过对不同的制动能源的利弊分析,选用了液压式作为这套制动系统的行车制动的能源,又选用了机械式作为驻车制动的能源。然后开始了对液压制动驱动结构的计算包括制动轮缸、制动主缸、真空助力器、踏板的行程与制动踏板力、油管和油管接头等一些重要元件。第4章 制动器设计和计算 汽车制动器几乎均为机械摩擦式,通过其中的固定元件对旋转元件施加制动力矩,使后者的旋转角速度降低,同时依靠车轮与路面的附着作用,产生路面对车轮的制动力,以使汽车减速或停车。汽车制动器按其在汽车上的位置分为车轮制动器和中央制动器。前者安装在车轮处,并用脚踩制动踏板进行操纵,故又称为脚制动;后者安装在传动系的某轴上,并用手拉操纵杆进行操纵,故又成为手制动。车轮制动器一般应用于行车制动,也有兼用第二制动和驻车制动。中央制动器一般只用于驻车制动和缓速制动。4.1 制动器方案确定4.1.1鼓式制动器鼓式制动器是最早形式的汽车制动器,当盘式制动器还没有出现前,它已经广泛用干各类汽车上。鼓式制动器又分为内张型鼓式制动器和外束型鼓式制动器两种结构型式。内张型鼓式制动器的摩擦元件是一对带有圆弧形摩擦蹄片的制动蹄,后者则安装在制动底板上,而制动底板则紧固在前桥的前梁或后桥桥壳半袖套管的凸缘上,其旋转的摩擦元件为制动鼓。车轮制动器的制动鼓均固定在轮鼓上。制动时,利用制动鼓的圆柱内表面与制动蹄摩擦路片的外表面作为一对摩擦表面在制动鼓上产生摩擦力矩,故又称为蹄式制动器。外束型鼓式制动器的固定摩擦元件是带有摩擦片且刚度较小的制动带,其旋转摩擦元件为制动鼓,并利用制动鼓的外因柱表面与制动带摩擦片的内圆弧面作为一对摩擦表面,产生摩擦力矩作用于制动鼓,故又称为带式制动器。在汽车制动系中,带式制动器曾仅用作一些汽车的中央制动器,但现代汽车已很少采用。所以内张型鼓式制动器通常简称为鼓式制动器,通常所说的鼓式制动器就是指这种内张型鼓式结构。鼓式制动器按蹄的类型分为:(1)领从蹄式制动器汽车倒车时制动鼓的旋转方向变为反向旋转,则相应地使领蹄与从蹄也就相互对调了。这种当制动鼓正、反方向旋转时总具有一个领蹄和一个从蹄的内张型鼓式制动器称为领从蹄式制动器。领蹄所受的摩擦力使蹄压得更紧,即摩擦力矩具有“增势”作用,故又称为增势蹄;而从蹄所受的摩擦力使蹄有离开制动鼓的趋势,即摩擦力矩具有“减势”作用,故又称为减势蹄。“增势”作用使领蹄所受的法向反力增大,而“减势”作用使从蹄所受的法向反力减小。领从蹄式制动器的效能及稳定性均处于中等水平,但由于其在汽车前进与倒车时的制动性能不变,且结构简单,造价较低,也便于附装驻车制动机构,故这种结构仍广泛用于中、重型载货汽车的前、后轮制动器及轿车的后轮制动器。(2)双领蹄式制动器若在汽车前进时两制动蹄均为领蹄的制动器,则称为双领蹄式制动器。显然,当汽车倒车时这种制动器的两制动蹄又都变为从蹄故它又可称为单向双领蹄式制动器。两制动蹄各用一个单活塞制动轮缸推动,两套制动蹄、制动轮缸等机件在制动底板上是以制动底板中心作对称布置的,因此,两蹄对制动鼓作用的合力恰好相互平衡,故属于平衡式制动器。双领蹄式制动器有高的正向制动效能,但倒车时则变为双从蹄式,使制动效能大降。这种结构常用于中级轿车的前轮制动器,这是因为这类汽车前进制动时,前轴的动轴荷及 附着力大于后轴,而倒车时则相反。(3)双向双领蹄式制动器当制动鼓正向和反向旋转时,两制动助均为领蹄的制动器则称为双向双领蹄式制动器。它也属于平衡式制动器。由于双向双领蹄式制动器在汽车前进及倒车时的制动性能不变,因此广泛用于中、轻型载货汽车和部分轿车的前、后车轮,但用作后轮制动器时,则需另设中央制动器用于驻车制动。(4)单向增力式制动器单向增力式制动器如图所示两蹄下端以顶杆相连接,第二制动蹄支承在其上端制动底板上的支承销上。由于制动时两蹄的法向反力不能相互平衡,因此它居于一种非平衡式制动器。单向增力式制动器在汽车前进制动时的制动效能很高,且高于前述的各种制动器,但在倒车制动时,其制动效能却是最低的。因此,它仅用于少数轻、中型货车和轿车上作为前轮制动器。(5)双向增力式制动器将单向增力式制动器的单活塞式制动轮缸换用双活塞式制动轮缸,其上端的支承销也作为两蹄共用的,则成为双向增力式制动器。对双向增力式制动器来说,不论汽车前进制动或倒退制动,该制动器均为增力式制动器。双向增力式制动器在大型高速轿车上用的较多,而且常常将其作为行车制动与驻车制动共用的制动器,但行车制动是由液压经制动轮缸产生制动蹄的张开力进行制动,而驻车制动则是用制动操纵手柄通过钢索拉绳及杠杆等机械操纵系统进行操纵。双向增力式制动器也广泛用作汽车的中央制动器,因为驻车制动要求制动器正向、反向的制动效能都很高,而且驻车制动若不用于应急制动时也不会产生高温,故其热衰退问题并不突出。但由于结构问题使它在制动过程中散热和排水性能差,容易导致制动效率下降。因此,在轿车领域上己经逐步退出让位给盘式制动器。但由于成本比较低,仍然在一些经济型车中使用,主要用于制动负荷比较小的后轮和驻车制动。本次设计最终采用的是领从蹄式制动器4.1.2 盘式制动器盘式制动器按摩擦副中定位原件结构的不同可分为钳盘式和全盘式两大类。(1)钳盘式钳盘式制动器按制动钳的结构型式又可分为定钳盘式制动器、浮钳盘式制动器等。定钳盘式制动器:这种制动器中的制动钳固定不动,制动盘与车轮相联并在制动钳体开口槽中旋转。具有下列优点:除活塞和制动块外无其他滑动件,易于保证制动钳的刚度;结构及制造工艺与一般鼓式制动器相差不多,容易实现从鼓式制动器到盘式制动器的改革;并且还能很好地适应多回路制动系的要求。浮动盘式制动器:这种制动器具有以下优点:仅在盘的内侧有液压缸,故轴向尺寸小,制动器能进一步靠近轮毂;没有跨越制动盘的油道或油管加之液压缸冷却条件好,所以制动液汽化的可能性小;成本低;浮动钳的制动块可兼用于驻车制动。(2)全盘式在全盘式制动器中,摩擦副的旋转元件及固定元件均为圆形盘,制动时各盘摩擦表面全部接触,其作用原理与摩擦式离合器相同。由于这种制动器散热条件较差,其应用远远没有浮钳盘式制动器广泛。通过对盘式、鼓式制动器的分析比较可以得出盘式制动器与鼓式制动器比较有如下均一些突出优点:(1)制动稳定性好,它的效能因素与摩擦系数关系的K-p曲线变化平衡,所以对摩擦系数的要求可以放宽,因而对制动时摩擦面间为温度、水的影响敏感度就低。所以在汽车高速行驶时均能保证制动的稳定性和可靠性,以满足人们需求。(2)盘式制动器制动时,汽车减速度与制动管路压力是线性关系,而鼓式制动器却是非线性关系。(3)输出力矩平衡.而鼓式则平衡性差。(4)制动盘的通风冷却较好,带通风孔的制动盘的散热效果尤佳,故热稳定性好,制动时所需踏板力也较小。(5)车速对踏板力的影响较小。综合以上优缺点最终确定本次设计采用前盘后鼓式。前盘选用浮动盘式制动器,后鼓采用领从蹄式制动器。4.2 鼓、盘式制动器的主要参数的确定4.2.1 鼓式制动器的结构参数和摩擦系数1结构参数(1)制动鼓直径D或半径R当输入力P一定时,制动鼓的直径越大,则制动力矩就越大,且使制动器的散热性能越好。但直径D的尺寸受到轮辋直径的限制,而且D的增大也使制动鼓的质量增加,使汽车的非悬挂质量增加,不利于汽车的平顺性。制动鼓与轮辋之间应有一定的间隙,此间隙一般不应小于20mm30mm,以利于散热通风,也可避免由于轮辋过热而损坏轮胎。由此间隙要求及轮辋的尺寸即可求得制动鼓D的尺寸。另外,制动鼓直径D与轮辋直径Dr之比的一般范围为;轿车 =0.640.74货车 =0.700.83轿车制动鼓内径一般比轮辋外径小125mm150mm 。综上取得制动鼓内径D=240mm ,轮辋直径=356mm 。制动鼓外径249mm。(2)制动蹄摩擦衬片的包角b及宽度b如图4-1所示包角b通常在b=9001200范围内选取,试验表明,摩擦衬片包角b=9001000时磨损最小,制动鼓的温度也最低,而制动效能则最高。再减小b虽有利于散热,但由于单位压力过高将加速磨损。包角b也不宜大于1200,因为过大不仅不利于散热,而且易使制动作用不平顺,甚至可能发生自锁。选取b=。摩擦衬片宽度b较大可以降低单位压力、减少磨损,但b的尺寸过大则不易保证与制动鼓全面接触。通常是根据在紧急制动时使其单位压力不超2.5MPa的条件来选择衬片宽度b的。选取b=45mm 。(3)摩擦衬片起始角b0摩擦衬片起始角b0通常为了适应单位压力的分布情况,将衬片相对于最大压力点对称布置,以改善制动效能和磨损的均匀性。根据=-(/2)=(4)张开力的作用线至制动器中线的距离a在满足制动轮缸或凸轮能布置在制动鼓内的条件下,应使距离a尽可能地大,以提高其制动效能。a=0.8R左右,求得a=99.6mm 。图4-1 制动蹄摩擦衬片参数(5)制动蹄支削中心的坐标位置k与c制动蹄支销中心的坐标尺寸k应尽可能地小,以使尺寸c尽可能地大,初步设计可取c=0.8R左右,取c=99.6mm 。2摩擦片摩擦系数在选择摩擦片时,不仅要希望其摩擦系数要高些,而且还得要求其稳定性好。受温度和压力的影响小。不宜单纯地追求摩擦材料的高摩擦系数,应提高对摩擦系数的稳定性和降低制动器对摩擦系数偏离正常值的敏感性的要求。后者对蹄式制动器是非常重要的。各种制动器用摩擦材料的摩擦系数的稳定值约为0.30.5,少数可达到0.7。一般来说,摩擦系数愈高的材料,起耐磨性愈差。所以在制动器设计时,并非一定要追求高摩擦系数的材料。选取f=0.3。4.2.2 盘式制动器主要参数的确定1.制动盘直径D制动盘直径D希望尽量大些,这时制动盘的有效半径得以增大,就可以降低制动钳的夹紧力,降低摩擦衬快的单位压力和工作温度。但制动盘直径D受轮辋直径的限制。通常,制动盘的直径D选择为轮辋直径的70%79%。所以求得制动盘直径D=256mm 。2.制动盘厚度h制动盘厚度直接影响制动盘质量和工作时的温升。为使质量不致太大,制动盘厚度应取小些;为了降低制动时的温升,制动盘厚度不宜过小。通常,实心制动盘厚度可取为10 mm20 mm;只有通风孔道的制动盘的两工作面之间的尺寸,即制动盘的厚度取为20 mm50 mm,但多采用20 mm30 mm。 取h=20mm 。3.摩擦衬块内半径R1与外半径R2推荐摩擦衬块的外半径R2与内半径R1的比值不大于1.5。若此比值偏大,工作时摩擦衬块外缘与内缘的圆周速度相差较大,则其磨损就会不均匀,接触面积将减小,最终会导致制动力矩变化大。4.摩擦衬块厚度与摩擦面积摩擦衬块厚度取14mm,推荐根据制动摩擦衬块单位面积占有的汽车质量在1.6kg/3.5 kg/内选取。摩擦面积取76cm。4.3 制动器的设计与计算4.3.1 制动蹄摩擦面的压力分布规律及径向变形规律由前面的分析可知,制动器摩擦材料的摩擦系数及所产生的摩擦力对制动蹄因数BF有很大影响。掌握制动蹄摩擦面上的压力分布规律,有助于正确分析制动器因数。但用分析方法精确计算沿蹄片长度方向上的压力分布规律比较困难,因为除了摩擦衬片有弹性变形外,制动蹄、制动鼓以及支承也会有弹性变形,但与摩擦衬片的变形量相比,则相对很小。故在通常的近似计算中只考虑衬片径向变形的影响,其他零件变形的影响较小,可忽略不计。即通常作以下一些假定。1.制动鼓、制动蹄为绝对刚性体;2.在外力作用下,变形仅发生在摩擦衬片上;3.压力与变形符合虎克定律。可根据图4-2来分析计算具有一个自由度的增势蹄摩擦衬片的径向变形规律和压力分布规律。此时摩擦衬片在张开力和摩擦力的作用下,绕支承销中心A1转动dg角。摩擦衬片表面任意点B1沿制动蹄转动的切线方向饿变形即为线段B1B1,其径向变形分量是线段B1B1在半径OB1延长线上的投影,即线段B1C1。由于dg角非常的小,可以认为=90则所求的摩擦衬片的径向变形为:图4-2摩擦衬片的径向变形规律和压力分布 (4-1)考虑到,则由等腰三角形可知” (4-2)代入上式,得摩擦衬片的径向变形和压力分别为: (4-3) 通过上式可看出摩擦片的径向变形和压力都是关于张开角a的正弦函数。4.3.2制动蹄片上的制动力矩在计算鼓式制动器时,必须建立制动蹄对制动鼓的压紧力与所产生的制动力矩之间的关系。增势蹄产生的制动力矩可表达如下: (4-4)式中 摩擦系数(前面以选择0.3); N1单元法向力的合力;P1摩擦力N1的作用半径。如图4-3求得力N1与张开力P1的关系式,写出制动蹄上力的平衡力方程式: (4-5)式中 S1x支承反力在x1轴上的投影; x1轴与力N1的作用线之间的夹角。对式(4-5)求解,得 (4-6)4.3.3 摩擦衬块的磨损特性计算摩擦衬片的磨损与摩擦副的材质,表面加工情况、温度、压力以及相对滑磨速度等多种因素有关,因此在理论上要精确计算磨损性能是困难的。但试验表明,摩擦表面的温度、压力、摩擦系数和表面状态等是影响磨损的重要因素。汽车的制动过程,是将其机械能(动能、势能)的一部分转变为热量而耗散的过程。在制动强度很大的紧急制动过程中,制动器几乎承担了耗散汽车全部动力的任务。此时由于在短时间内制动摩擦产生的热量来不及逸散到大气中,致使制动器温度升高。此即所谓制动器的能量负荷。能量负荷愈大,则摩擦衬片(衬块)的磨损亦愈严重。1)比能量耗散率双轴汽车的单个前轮制动器和单个后轮制动器的比能量耗散率分别为: (4-8) (4-9)式中 汽车回转质量换算系数,紧急制动时,=1; ma汽车总质量; ,汽车制动初速度与终速度,/;计算时轿车取27.8/; 制动时间,;按下式计算 t=27.8/6=4.6 制动减速度, 0.6106; ,:前、后制动器衬片的摩擦面积;=7600mm,质量在1.52.5/t的轿车摩擦衬片面积在200-300cm,图4-3 制动蹄对制动鼓的压紧力关系 t=27.8/6=4.6 故取A2=30000mm 制动力分配系数。则 =5.7轿车盘式制动器的比能量耗散率应不大于6.0,故符合要求。=0.7轿车鼓式制动器的比能量耗散率应不大于1.8,故符合要求。2)比滑磨功磨损和热的性能指标可用衬片在制动过程中由最高制动初速度至停车所完成的单位衬片面积的滑磨功,即比滑磨功来衡量: (4-10)式中 ma汽车总质量 A车轮制动器各制动衬片的总摩擦面积,=752cm; :; L许用比滑磨功,轿车取1000J/1500J/。 L =1497J/1000J/1500J/故符合要求。4.3.4 制动器热容量和温升的核算制动器热容量和温升是否满足下列条件: (4-11)式中 各制动鼓(盘)的总质量; mk与各制动鼓(盘)相连的受热金属件(如轮毂、轮辐、轮辋、制动钳体等)的总质量;cd制动鼓(盘)材料的比热容,对铸铁c=482J/(kg*K),对铝合金c=880 J/(kg*K);ck与制动鼓(盘)相连的受热金属件的比热容; 制动鼓(盘)的温升(一次=30km/h到完全停车的强烈制动,温升不应超过15); L满载汽车制动时由动能转变的热能,由于制动过程迅速,可以认为制动产生的热能全部为前、后制动器所吸收,并按前、后制动力 的分配比率给前、后制动器,即 (4-12)式中 ma满载汽车总质量; va汽车制动时的初速度,可取va=vamax; b汽车制动器制动力分配系数。式中的md=5kg, mk=20kg.将其他已知的参数代入式(4-8)得:前轮钳盘式制动器和后鼓式制动器的热容量和温升都满足。通过计算得出,前轮盘式制动器和后轮鼓式制动器的热容量和温升都在合理范围内,满足要求。4.3.5 盘式制动器制动力矩的计算盘式制动器的计算用简图4-4若衬块表面与制动盘接触良好,且各处的单位压力分布均匀,则盘式制动器的制动力矩为: 式中 摩擦系数;单侧制动块对制动盘的压紧力; 作用半径。对于常见的扇形摩擦衬块,其径向尺寸不大了,R为平均半径Rm或有效半径Re已足够精确。平均半径为: (4-13)式中 R1,R2扇形摩擦衬块的内半径和外半径。所以盘式制动器的力矩方程为:,是关于活塞给予制动块对制动盘的压紧力的一个直线函数。根据图4-4在任一单元面积上的摩擦力对盘中心的力矩为,式中q为衬块与制动盘之间的单位面积上的压力,则单侧制动块作用于制动盘上的制动力矩为: (4-14)单侧衬块给予制动盘的总摩擦力为: (4-15)得有效半径为: (4-16)令,则有: (4-17)因,故当。但当m过小即扇形的径向宽度过大时,衬块摩擦表面在不同半径处的滑磨速度相差太大,磨损将不均匀,因而单位压力分布将不均匀,则上述计算方法失效。图4-4 盘式制动器的计算用简图4.3.6 驻车制动计算驻车制动,一般叫做手刹,(个别也有用脚操作,如别克GL8),它的作用就是在停车时,给汽车一个阻力,使汽车不溜车。驻车制动,也就是手刹或者自动档中的停车档,锁住传动轴或者后轮。 驻车制动比行车制动的力小很多很多,仅仅是在坡路停车不溜车,就可以了。驻车制动有不同的类型,如上述用手或用脚操作的机械机构。另外,高级车也逐渐采用电子控制的驻车系统,俗称电子手刹。汽车在上坡路上停驻时的受力简图如图4-5由该图得出汽车上坡停驻时的后轴附着力为 (4-18)同样求出汽车下颇停驻的后轴车轮的附着力为 (4-19)根据后轴车轮附着力与后轮驻车制动的制动力相等的条件可求得汽车在上坡路和下坡路上停驻的坡度极限倾角,即由 (4-20)求得汽车在上坡时可能停驻的极限上坡路倾角为: (4-21)代入汽车参数,求得:23.22汽车在下坡时可能停驻的极限下坡路倾角为: (4-22)代入汽车参数,求得16.83 一般要求各类汽车的最大停驻坡度不应小于16%20%。汽车后轴的单个后轮驻车制动器的制动力矩的最大上限为: T= (4-23)代入汽车参数求得T=760.68图4-5 驻车制动计算模型4.4 制动器主要零部件的结构设计4.4.1 制动鼓制动鼓应当有足够的强度,刚度和热容量,与摩擦衬片材料相配合,又应当有较高的摩擦因数。所谓制动鼓就是鼓式刹车系统的一部份,刹车时,活塞对两对半月型的刹车蹄片施加压力,使其贴紧鼓室内壁,从而产生摩擦来停止车轮的旋转。制动鼓的材质一般为HT200-300(即灰铸铁),基体组织主要为珠光体以及少量的铁素体、渗碳体,石墨的主要为A级,形态为长片状,长度等级为4-6级,起到散热、增加摩擦性能、减低刹车噪音的作用。制动鼓毛坯的生产工艺为铸造,所需主要原材料一般为生铁、废钢以及回炉铁,同时加入一些合金,如Cu、Cr等,改善铸件性能。中型,重型载货汽车和中型,大型客车多采用灰铸铁HT200或合金铸铁制造的制动鼓(见图4-6(a));轻型货车和一些轿车则采用由钢板冲压成型的的辐板与铸铁鼓筒部分铸成一体的组合式制动鼓(见图4-6(b);带有灰铸铁内鼓筒的铸铝合金制动鼓(见图4-6(c)在轿车上得到了日益广泛的应用。铸铁内鼓筒与铝合金制动鼓也是铸到一起的,这种内镶一层珠光体组织的灰铸铁作为工作表现,其耐磨性和散热性都很好,而且减小了质量,所以非常适合于制造制动鼓。制动鼓相对于轮毂的中如图4-6所示,是以直径为dc的圆柱表面的配合来定位,并在两者装配紧固后精加工制动鼓内工作表面,以保证两者的轴线重合。两者装配后还需进行动平衡。其许用不平衡度对轿车为1520Ncm;对货车为3040Ncm。微型轿车要求其制动鼓工作表面的圆度和同轴度公差。制动鼓鼓壁厚的选取主要是从其刚度和强度方面考虑。壁厚取大些也有利于增大其热容量,但实验表明,壁厚由增至时,摩擦表面的平均最高温度变化并不大。一般铸造制动鼓的壁厚:轿车为;中,重型载货汽车为。制动鼓在闭合一侧外缘可开小孔,用于检查制动器间隙。本次设计采用的材料是HT20-40。4.4.2 制动蹄轿车和微型,轻型载货汽车的制动蹄广泛采用T形型钢碾压或钢板冲压焊接制成;大吨位载货汽车的制动蹄则多用铸铁,铸钢或铸铝合金制成。制动蹄的结构尺寸和断面形状应保证其刚度好,但小型车用钢板制的制动蹄腹板上有时开有一,两条径向槽,使蹄的弯曲刚度小些,以便使制动蹄摩擦衬片与制动鼓之间的解除压力均匀,因而使衬片的磨损较为均匀,并可减少制动时的尖叫声。本设计中制动蹄采用T形型钢辗压焊接制成。制动蹄腹板和翼缘的厚度,轿车的约为;货车的约为。摩擦衬片的厚度,轿车多为;货车多为以上。衬片可铆接或粘贴在制动蹄上,粘贴的允许其磨损厚度较大,使用寿命增长,但不易更换衬片,铆接的噪声小。这一次我的设计的制动蹄所采用的材料为HT200。制动蹄是很重要的零件,是外圆柱面可与制动衬片或摩擦材料制成一体的零件。(a)铸造制动鼓;(b),(c)组合式制动鼓1- 冲压成型幅板;2- 铸造鼓筒;3- 灰铸铁内鼓筒;4- 铸铝合金制动鼓图 4-6制动鼓4.4.3 制动底板制动底板是除制动鼓外制动器各零件的安装基体,应保证各安装零件相互间的正确位置。制功底板承受着制动器工作时的制动反力矩,因此它应有足够的刚度。为此,由钢板冲压成形的制动底板均只有凹凸起伏的形状。重型汽车则采用可联铸铁KTH37012的制动底板。刚度不足会使制动力矩减小,踏板行程加大,衬片磨损也不均匀。本次设计采用45号钢。4.4.4 制动蹄的支承二自由度制动蹄的支承,结构简单,并能使制动蹄相对制动鼓自行定位。为了使具有支承销的一个自由度的制动蹄的工作表面与制动鼓的工作表面同轴心,应使支承位置可调。例如采用偏心支承销或偏心轮。支承销由45号钢制造并高频淬火。其支座为可锻铸铁或球墨铸铁件。青铜偏心轮可保持制动蹄腹板上的支承孔的完好性并防止这些零件的腐蚀磨损。具有长支承销的支承能可靠地保持制动蹄的正确安装位置,避免侧向偏摆。有时在制动底板上附加一压紧装置,使制动蹄中部靠向制动底板,而在轮缸活塞顶块上或在张开机构调整推杆端部开槽供制动蹄腹板张开端插入,以保持制动蹄的正确位置。4.4.5 制动轮缸制动轮缸为液压制动系采用的活塞式制动蹄张开机构,其结构简单,在车轮制动器中布置方便。轮缸的缸体由灰铸铁HT250制成。其缸筒为通孔,需镗磨。活塞由铝合金制造。活塞外端压有钢制的开槽顶块,以支承插入槽中的制动蹄腹板端部或端部接头。轮缸的工作腔由装在活塞上的橡胶密封圈或靠在活塞内端面处的橡胶皮碗密封。多数制动轮缸有两个等直径活塞;少数有四个等直径活塞;双领蹄式制动器的两蹄则各用一个单活塞制动轮缸推动。本次设计采用的是HT250。4.4.6 制动盘制动盘一般用珠光体灰铸铁制成。其结构形状有平板形和礼帽形两种。后一种的圆柱部分长度取决于布置尺寸。制动盘在工作时不仅承受着制动块作用的法向力和切向力,而且承受着热负荷。为了改善冷却效果,钳盘式制动器的制动盘有的铸成中间有径向通风槽的双层盘,这样可大大地增加散热面积,降低温升约20%30%,但盘的整体厚度较厚。国产引进车型奥迪、桑塔纳2000、富康轿车和切诺基吉普车均采用带有通风槽的制动盘,其厚度在2022.5之间。而一般不带通风槽的轿车制动盘,其厚度约在1013之间。4.4.7 制动钳制动钳由可锻铸铁KTH370-12或球墨铸铁QT400-18制造,也有用轻合金制造的,例如用铝合金呀铸。可做成整体的,也可做成两半由螺栓连接,其外缘留有开口,以便不必拆下制动迁便可检查或更换制动块。制动钳体应有高的强度和刚度。一般多在钳体中加工出制动油缸,钳盘式制动器油缸直径比鼓式制动器的轮缸大的多。为了减少传给制动液的热量,多将杯形活塞的开口端顶靠制动块的背板。活塞又铸铝合金制造或由刚制造。为了提高其耐磨损性能,活塞的工作面进行镀铬处理。制动钳在汽车上的安装位置可在车轴的前方或后方。制动钳位于车轴前可避免胎甩出来的泥、水进入制动钳,位于车轴后则可减小制动时轮毂轴承的合成载荷。4.4.8 制动块制动块由背板和摩擦衬块构成,两者直接牢固地压嵌或铆接或粘接在一起。材料多为扇形,也有矩形、正方形或长圆形的。活塞应能压住尽量多的制动块面积,以免衬块发生卷角而引起尖叫声。制动块背板由钢板制成,为了避免制动时产生的热量传给制动钳而引起制动液气化和减小制动噪声,可在摩擦衬块与背板之间或在背板后粘一层隔热振垫。由于单位压力和工作温度高等原因,摩擦衬块的磨损较快,因此其厚度较大。据统计,轿车和轻型车的厚度在7.5mm 16mm之间。4.4.9 摩擦材料制动摩擦材料应只有角而稳定的摩擦系数,抗热衰退性能要好,不应在温升到某一数值后摩擦系数突然急剧下降,材料应有好的耐磨性,低的吸水(油、制动液)率,低的压缩率、低的热传导率(要求摩擦衬块么300的加热板上:作用30min后,背板的温度不越过190)和低的热膨胀率,高的抗压、抗打、抗剪切
- 温馨提示:
1: 本站所有资源如无特殊说明,都需要本地电脑安装OFFICE2007和PDF阅读器。图纸软件为CAD,CAXA,PROE,UG,SolidWorks等.压缩文件请下载最新的WinRAR软件解压。
2: 本站的文档不包含任何第三方提供的附件图纸等,如果需要附件,请联系上传者。文件的所有权益归上传用户所有。
3.本站RAR压缩包中若带图纸,网页内容里面会有图纸预览,若没有图纸预览就没有图纸。
4. 未经权益所有人同意不得将文件中的内容挪作商业或盈利用途。
5. 人人文库网仅提供信息存储空间,仅对用户上传内容的表现方式做保护处理,对用户上传分享的文档内容本身不做任何修改或编辑,并不能对任何下载内容负责。
6. 下载文件中如有侵权或不适当内容,请与我们联系,我们立即纠正。
7. 本站不保证下载资源的准确性、安全性和完整性, 同时也不承担用户因使用这些下载资源对自己和他人造成任何形式的伤害或损失。

人人文库网所有资源均是用户自行上传分享,仅供网友学习交流,未经上传用户书面授权,请勿作他用。