资源目录
压缩包内文档预览:
编号:272206
类型:共享资源
大小:1.66MB
格式:RAR
上传时间:2014-04-11
上传人:上***
认证信息
个人认证
高**(实名认证)
江苏
IP属地:江苏
45
积分
- 关 键 词:
-
散热
风扇
支架
注射
设计
图纸
优秀
优良
- 资源描述:
-
散热风扇支架注射模设计
55页-15000字数+说明书+开题报告+中期报告+6张CAD图纸
三维散热风扇支架注射模开模图.dwg
中期报告.doc
动模垫板.dwg
开题报告封皮.doc
推杆固定板.dwg
散热风扇支架.jpg
散热风扇支架塑件图.dwg
散热风扇支架注射模装配图.dwg
散热风扇支架注射模设计开题报告.doc
散热风扇支架注射模设计论文.doc
浇口套.dwg
目 录
摘要I
AbstractII
第1章 绪论1
1.1 模具工业在国民经济中的地位1
1.2 各种模具的分类和占有量2
1.3 我国模具工业的现状3
1.4 世界五大塑料生产国的产能状况4
1.5 我国模具技术的现状及发展趋势7
第2章塑件设计分析9
2.1 塑件模型建立9
2.1.1 模型3D图9
2.1.2 塑件2D图及其技术条件9
2.2 塑件参数设计10
2.2.1 材料选择10
2.2.2 塑件收缩率12
2.2.3 塑件的壁厚12
2.2.4 塑件的拔模斜度13
2.2.5 分型面的设计13
2.2.6 确定型腔数量以及排列方式13
2.3 本章小结14
第3章注塑设备和模架选择15
3.1 注塑设备选择15
3.2 注塑机重要参数校核15
3.2.1 注塑容量校核15
3.2.2 锁模力校核16
3.2.3 开模行程校核17
3.3 模架选择17
3.4 本章小结18
第4章浇注系统设计19
4.1 主流道设计19
4.1.1 浇口套设计19
4.1.2 浇口套的固定形式20
4.2 分流道设计20
4.2.1 分流道的形状20
4.2.2 分流道的布局21
4.2.3 分流道的长度21
4.3 浇口设计22
4.3.1 点浇口的尺寸22
4.3.2 浇口位置的选择22
4.4 冷料穴和钩料脱模装置23
4.5 本章小结23
第5章成型零件设计加工工艺方案制定24
5.1 型腔的设计24
5.2 型芯的设计24
5.2.1 型芯的径向尺寸24
5.2.2 型芯的高度尺寸25
5.3 镶件的设计27
5.4 加工工艺方案制订27
5.4.1 型腔加工工艺方案27
5.4.2 型芯加工工艺方案28
5.5 本章小结28
第6章侧向分型与抽芯机构设计29
6.1 机动侧向分型与抽芯机构29
6.2 斜销侧向分型抽芯机构主要参数29
6.2.1 抽芯距29
6.2.2 斜销的倾角30
6.2.3 抽芯力的计算30
6.2.4 圆形斜导柱直径的确定31
6.2.5 斜导柱的总长度计算32
6.3 本章小结33
第7章脱模机构设计34
7.1 推杆脱模机构34
7.2 推杆尺寸计算及校核35
7.2.1 推杆直径计算35
7.2.2 推杆应力校核35
7.3 推杆脱模机构布局36
7.4 本章小结36
第8章冷却系统设计37
8.1 冷却管道的直径计算37
8.1.1 求塑件在固化时每小时释放的热量37
8.1.2 求冷却水的体积流量38
8.1.3 求冷却水的管道直径39
8.2 冷却管道的孔数计算40
8.2.1 求冷却水在管道内的流速40
8.2.2 求冷却管道孔壁与冷却介质之间的传热系数40
8.2.3 求冷却管道中的传热面积41
8.2.4 求模具上应开设的冷却管道的孔数41
8.3 本章小结42
第9章模具装配图和零件图43
9.1 模具装配图绘制43
9.1.1 模具装配图包含的内容43
9.1.2 模具装配图绘制步骤43
9.2 模具零件图绘制44
9.2.1 模具零件图包含的内容44
9.2.2 模具零件图绘制步骤44
9.3 本章小结45
结论46
致谢47
参考文献48
附录149
附录250
摘要
本论文主要通过对工控机散热风扇支架的设计分析,设计出该塑件的模具。在整个模具设计过程中,涉及到了塑件的结构设计、注塑机和模架的选择及注塑机的一些重要工艺参数的校核,并详细叙述了模具设计中的分型面设计、浇注系统设计、成型零件设计、顶出机构设计和冷却系统设计。
利用塑料成型模拟分析软件Moldflow的MPI模拟其成型过程,制定合理的工艺方案并优化模具结构,Moldflow可提供如下分析:产品结构是否合理 、怎样选择合适的注塑材料 、怎样确定合理的浇口位置 、浇口位置自动优化 、预测熔接痕位置 、模具型腔是否充满 、最终制品的质量如何 、怎样选择合适的注塑机 、缩痕分析,所以这次设计中Moldflow的引入很重要。本论文基于Pro/E CAD系统,通过该系统,用户可以在可视化平台上交互式的设计注塑模具各个部件,不仅可以避免相似零件设计的重复性,大大提高其设计效率和设计质量,缩短产品的开发周期,而且方便了产品后续的有限元分析,同时也符合了现代设计思想的发展要求。
关键词 模具设计;CAD;Pro/E;MoldFlow
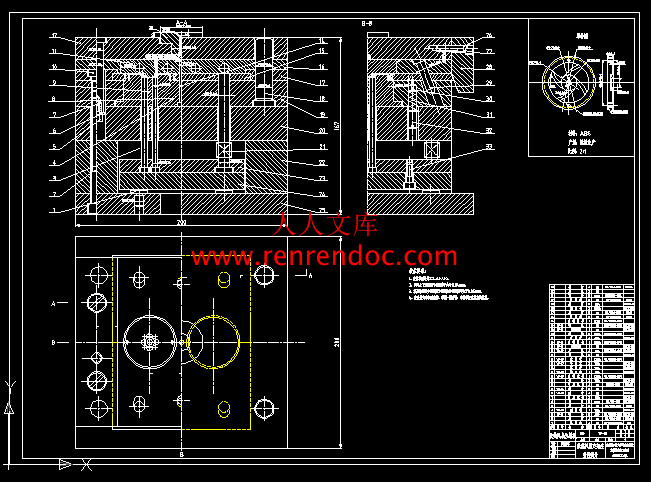

- 内容简介:
-
哈尔滨工业大学华德应用技术学院毕业设计(论文)中期报告 题 目:散热风扇支架注射模设计 系 (部) 材料工程系 专 业 材料成型及控制工程 学 生 赵佳辉 学 号 1089522120 班 号 0895221 指导教师 朱斌海 中期报告日期 2011年11月23日 哈工大华德学院说 明一、中期报告应包括下列主要内容:1论文工作是否按开题报告预定的内容及进度安排进行;2目前已完成的研究工作及结果;3后期拟完成的研究工作及进度安排;4存在的困难与问题;5如期完成全部论文工作的可能性。二、中期报告由指导教师填写意见、签字后,统一交所在院(系)保存,以备检查。指导教师评语: 指导教师签字: 检查日期: 毕业设计(论文)中期报告一、论文工作是否按开题报告预定的内容及进度安排进行 1.1 目前的论文工作已按照开题报告预定的内容及进度进行了安排二、目前已完成的研究工作及成果2.1 塑件模型建立2.1.1 模型3D图模型绘制3D图采用PTC公司的产品Pro/ENGINEER Wildfire 3.0,最终绘制出来的3D结构图2-1所示: 图2-1塑件模型3D图2.1.2 塑件2D图及其技术条件模型2D图绘制采用Autodesk公司的产品AutoCAD2006, 最终绘制出来的2D结构图2-2所示: 图2-2塑件模型2D图1.塑件精度等级及尺寸公差塑件采用的精度等级为5级精度,部分尺寸的公差标注如图2-2所示。2.塑件的表面质量该塑件要求外形美观,色泽鲜艳,外表面没有斑点及熔接痕,粗糙度可取。2.2 塑件参数设计2.2.1 材料选择通常,选择塑件的材料依据是它所处在的工作环境及使用性能的要求,以及原材料厂家提供的材料性能数据。对于常温工作状态下的结构件来说,要考虑的主要是材料的力学性能,如屈服应力,弹性模量,弯曲强度,表面硬度等。该塑件为一般的零件,属于圆盘类,没有特别的要求,根据以上的依据,选择材料ABS为塑料件的材料。ABS塑料 化学名称:丙烯腈-丁二烯-苯乙烯共聚物 英文名称:Acrylonitrile Butadiene Styrene 比重:1.05 成型收缩率:0.40.7 成型温度:200240 干燥条件:8090 2 特点: (1)综合性能较好,冲击强度较高,化学稳定性,电性能良好。(2)与372有机玻璃的熔接性良好,制成双色塑件,且可表面镀铬,喷漆处理。 (3)有高抗冲、高耐热、阻燃、增强、透明等级别。(4)流动性比HIPS差一点,比PMMA、PC等好,柔韧性好。 成型特性: (1)无定形料,流动性中等,吸湿大,必须充分干燥,表面要求光泽的塑件须长时间预热干燥8090,3h。(2)宜取高料温,高模温,但料温过高易分解(分解温度为270)。对精度较高的塑件,模温宜取5060,对高光泽。耐热塑件,模温宜取6080。(3)如需解决夹水纹,需提高材料的流动性,采取高料温、高模温,或者改变入水位等方法。 (4)如成形耐热级或阻燃级材料,生产37天后模具表面会残存塑料分解物,导致模具表面发亮,需对模具及时进行清理,同时模具表面需增加排气位置。ABS树脂是目前产量最大,应用最广泛的聚合物,它将PS,SAN,BS的各种性能有机地统一起来,兼具韧,硬,刚相均衡的优良力学性能。ABS是丙烯腈、丁二烯和苯乙烯的三元共聚物,A代表丙烯腈,B代表丁二烯,S代表苯乙烯。 ABS工程塑料一般是不透明的,外观呈浅象牙色、无毒、无味,兼有韧、硬、刚的特性,燃烧缓慢,火焰呈黄色,有黑烟,燃烧后塑料软化、烧焦,发出特殊的肉桂气味,但无熔融滴落现象。ABS工程塑料具有优良的综合性能,有极好的冲击强度、尺寸稳定性好、电性能、耐磨性、抗化学药品性、染色性,成型加工和机械加工较好。ABS树脂耐水、无机盐、碱和酸类,不溶于大部分醇类和烃类溶剂,而容易溶于醛、酮、酯和某些氯代烃中。 ABS工程塑料的缺点:热变形温度较低,可燃,耐候性较差。用途: 适于制作一般的机械零件,磨耐磨零件,盘体,车配件,日用品,管材及文具等。2.2.2 塑件收缩率根据以上选用的材料为ABS,查相关资料可知,ABS的收缩率为0.0040.007,由公式(2-1)求出ABS平均收缩率: (2-1)式中 塑料的平均收缩率; 塑料的最大收缩率;塑件的最小收缩率。计算如下: 2.2.3 塑件的壁厚 一般说来,塑件的厚度越厚就越能满足产品的强度和刚度的性能要求,但是从塑件的成型过程看来,塑件的壁厚越厚,冷却的时间就越长,整个塑件的成型周期就要延长,提高了生产的成本,降低了生产的效率,同时,塑件的壁厚越厚,收缩率就增大,这样使的得产品的尺寸不稳定性增加,降低了产品的质量。因此产品的厚度必须得适中,根据材料的的特性,查阅相关的资料,查得ABS制品的壁厚通常为1、1.2、1.5、2、2.5、3、6。本次设计中,塑件的壁厚为6。2.2.4 塑件的拔模斜度拔模斜度是为了便于脱模,防止塑件表面在脱模时划伤,擦毛,在设计塑件表面沿脱模方向应具有合理的脱模斜度。塑件的脱模斜度大小跟塑件的性质、收缩率、摩擦因素、塑件的壁厚和几何形状有关。在设计时,可以参考一些资料来确定塑件的脱模斜度,一般以塑件的材料为选择依据,而ABS塑料的脱模斜度为,本设计选择的脱模斜度为。2.2.5 分型面的设计选择分型面是为了便于塑件的脱模和简化模具结构,该塑件因为壁薄故应采用点浇口形式进料,采用点浇口时,为了能取出流道凝料,应使用三板式双分型面模具。2.2.6 确定型腔数量以及排列方式本次模具设计采用的是一模两腔,型腔的分布如图2-3所示:图2-3型腔分布图3.1 注塑设备选择选取注射机型号为,具体参数如表3-1:表3-1注塑机参数理论容量ShotSize (Theoretical)60注塑速率Injection Rate70塑化能力Plasticizing Capacity35注塑压力Injection Pressure180锁模力Clamp Tonnage400移模行程Toggle Stroke250最大模厚Max Mold Height250最小模厚Min Mold Height150喷嘴球半径Spray nozzle10喷嘴口孔径Aperture nozzle33.2 注塑机重要参数校核3.2.1 注塑容量校核注塑机标准规定,以容量计算时,必须使得在一个注塑成型周期内所需的注塑塑料熔体的容量在注塑机额定注塑量的80内,也就是 (3-1)式中 注塑机最大注塑容量(); 成型塑件与浇注系统体积的总和(); 为最大注塑容量的利用系数。计算如下: (3-2) 式中 成型塑件的体积,乘以2是因为本次的模具是一模两腔; 浇注系统中主流道,分流道,浇口,冷料穴的体积和。所以, 注 (3-3)而注塑机的注塑容量为60,所以注塑机的注塑容量符合要求。3.2.2 锁模力校核当高压的塑料熔体充满型腔时,会产生一个沿注塑机轴向的很大的推力,其大小等于制件与浇注系统在份型面上的垂直投影之和乘与型腔内塑料熔体的平均压力。该推力应该小于注塑机额定的锁模力,否则在注塑成型时会因锁模不紧而发生溢边跑料现象。型腔内塑料熔体的推力()可按下式计算 (3-4)式中 型腔内塑料熔体沿注塑机轴向的推力(); 塑料与浇注系统在分型面上的投影面积(); 压力损耗系数,取0.4; 注塑压力。计算如下:=1844.96 =180也就是型腔内的塑料熔体沿注塑机轴向的推力为133,而注塑机的锁模力为400,所以注塑机的锁模力符合要求。3.2.3 开模行程校核模具开模后为了能取出塑胶件,要求有足够的开模距离,本次模具使用的注塑机的开模行程是给定的,不受模具厚度的影响,当模具的厚度变化时,可由其调模装置调整。只要使得注塑机最大开模行程大于模具所需的开模距离就符合注塑的要求。即: (3-5)式中 注塑机最大开模距离(); 模具所需的开模距离()。也就是,所以注塑机的锁模力符合要求。3.3 模架选择根据型腔排列的方式以及初步确定的壁厚,选择模架A4型,系列,其结构以及一些重要尺寸如图3-1、3-2所示: 图3-1 模架尺寸1 图3-2 模架尺寸24.1 主流道设计4.1.1 浇口套设计为了便于浇注凝料从主流道取出,主流道采用的圆锥孔;浇口套与注塑机喷嘴嘴头的接触球面必须吻合。注塑机的喷嘴是球面,其半径SR是固定的,为了浇口套端面的凹球面与注塑机的端凸球面接触良好,一般取半径: (4-1)式中 主流道入口凹坑球面半径(); 喷嘴球半径()。在此次设计中,所以;而浇口套的圆锥孔的小端直径d应该大于喷嘴内孔直径: (4-2)由注塑机的参数可以看到,所以,浇口套的端面凹球深度。浇口套的尺寸如图4-1所示图4-1 浇口套尺寸4.1.2 浇口套的固定形式本次设计中,浇口套与注塑机定位孔采用过盈配合。4.2 分流道设计4.2.1 分流道的形状分流道的截面形状常用的有圆形,梯形,和矩形, 其中圆形截面的分流道效率最高,也就是分流道流过相同的塑料流量,其分流道的内表面积最小。这样可以减少注塑过程中散热面积,即熔料的温度降低最小,同时使得摩擦力变小,减少压力损失。其缺点就是制造起来比较麻烦,因为它必须将分流道分设在模板的两侧,在对合时容易产生错口现象。当分型面为平面时候,常采用圆形截面流到,本次设计中,分型面非平面,采用圆形截面分流道加工困难,故采用效率较高的梯形截面分流道。4.2.2 分流道的布局本次模具设计为一模两腔,分流道的布局对塑料件的成型影响也较大的,由于前面已经将型腔的布局确定,设计分流道的布局既要跟型腔的布局协调,同时还应该注意一些分流道布局的设计要点:分流道和型腔的分布原则是排列紧凑,间距合理,应该采用轴对称或者中心对称,使其平衡,尽量缩小成型区域的总面积。最好使型腔和分流道在分型面上的总投影面积的几何中心和锁紧力的中心重合;在可能的情况下,分流道的长度尽可能的缩短,以减少压力损失,避免模体压力过大的影响成本。在多型腔模具中,各型腔的分流道长度应该尽量相等,以达到注塑时压力传递的平衡。分流道的布局如图4-2,分流道长度短,对称分布。 图4-2 分流道布局4.2.3 分流道的长度根据分流道的布局,大概的可以测量出分流道的长度总长;4.3 浇口设计本次设计采用的浇口为点浇口,其优点是浇口位置能灵活地确定,浇口附近变形小,多型腔时采用点浇口容易平衡浇注系统,对于投影面积大的塑件或易变形的塑件,采用多个点浇口能够取得理想的效果,适用一模多腔的模具。4.3.1 点浇口的尺寸根据经验的数据,一般的点浇口直径常为0.51.8,这里选1;浇口的长度常为0.52,这里选2。4.3.2 浇口位置的选择本次设计浇口位置的选择如图4-3所示: 图4-3 浇口位置示意图4.4 冷料穴和钩料脱模装置采用拉杆式钩料装置:由冷料穴和拉料杆组成,在冷料穴的底部设有一拉料杆,拉料杆固定在型腔板上,一次分型依靠拉料杆抽出主流道凝料。 其基本形状如图4-4所示,采用带球形头的冷料穴,其中冷料穴的直径要比主流道的稍大,主流道末端的半径大约为5,所以冷料穴的直径设为6,此处的拉料杆直径为4。图4-4 拉料杆形状示意图5.1 型腔的设计采用整体式型腔,也就是由整块材料加工而成的型腔。整体式型腔的优点是,强度和刚度相对较高,且不易变形,对塑件的上表面不会产生拼模缝的痕迹,缺点为切削量大,模具成本高,同时给热处理和表面处理带来一定的困难。型腔的外形尺寸为:。 5.2 型芯的设计本次设计塑件中共有三个孔,两个的直孔和一个阶梯孔,故需要两个直型芯和一个阶梯型芯成型。型芯的径向和高度尺寸计算如下: 5.2.1 型芯的径向尺寸型芯径向尺寸计算公式: (5-1)式中 型芯径向基本尺寸();塑件内形尺寸();塑料的平均收缩率;修正系数,取3/4;塑件的公差();型芯制造公差,取/3()。大型芯径向尺寸计算如下:小型芯径向尺寸计算如下: 5.2.2 型芯的高度尺寸型芯高度尺寸计算公式: (5-2)式中 型芯高度基本尺寸();塑件高度基本尺寸();塑料的平均收缩率;修正系数,取2/3;塑件的公差();型芯制造公差,取/3()。阶梯型芯高度尺寸计算如下: 型芯尺寸如图5-1、5-2所示:图5-1 阶梯型芯尺寸 图5-2 直型芯尺寸5.3 镶件的设计镶件位置放在定模板上,其尺寸形状如图5-3所示:图5-3 镶件形状及尺寸5.4 加工工艺方案制订塑料模具的加工方法大体上可以分为切削机床加工、钳加工和特殊加工三大类。切削机床加工是指采用不同的切削机床,如车床、铣床、磨床等进行粗加工或精加工等。钳加工是指采用锉、铲、研等手工措施去除切削机床所预留的加工余量,将模具半成品加工成符合蓝图的要求尺寸,形状以及表面粗糙度的合格零件,并通过组装总装成符合要求的模具。当模具零件使用普通机床或人工的传统的方法很难加工或者耗时很大时,则往往采用特殊加工的方法,如电火花,线切割以及等。5.4.1 型腔加工工艺方案表5-1型腔的加工工艺方案工序内容设备1铣削端铣坯料的六个端面铣床2钻削钻镶件孔钻床3CNC粗加工粗加工成型面CNC4热处理调质5磨削磨上、下端面磨床6CNC精加工精加工成型面CNC7钳工抛光成型面、倒角,攻丝6.1 机动侧向分型与抽芯机构机动侧向分型与抽芯是利用注射机的开模力,通过传动机构改变运动方向,将侧向的活动型芯抽出。机动抽芯机构的结构比较复杂,但抽芯不需要人工操作,抽拔力较大,具有灵活,方便,生产效率高,容易实现全自动操作,无需另外添置设备等优点,在生产中被广泛采用。机动抽芯按结构形式可分为斜销,弹簧,弯销,斜导槽,斜滑块,楔块,齿轮条等多种抽芯形式。本设计采用的是斜销侧向分型抽芯机构。6.2 斜销侧向分型抽芯机构主要参数6.2.1 抽芯距型芯从成型位置抽到不妨碍塑件脱模的位置所移动的距离叫抽芯距,用表示。一般抽芯距等于侧向孔或侧凹深度加上23余量,即: (6-1)式中 抽芯距();侧向孔或侧凹深度()。而所以 6.2.2 斜销的倾角斜销的倾角是决定斜销抽芯机构工作效果的一个重要参数,它不仅决定了开模行程和斜销长度,而且对斜销的受力状况有着重要的影响。决定倾斜角的大小时,应从抽芯距,开模行程和斜销受力几个方面综合考虑。实际生产中,一般取,不宜超过。选。6.2.3 抽芯力的计算抽芯力的计算跟脱模力的计算是一样的,计算的公式为 (6-2)式中 抽芯力();单位面积塑件对型芯的正压力(),一般取p(4.8411.76); 塑件包紧型芯的侧面积(); 塑件与模体钢材的摩擦系数,一般取0.10.3; 脱模斜度。计算得: 6.2.4 圆形斜导柱直径的确定图6-1 导柱直径计算计算公式(字母对应的尺寸如图6-1所示) (6-3)式中 斜导柱直径(); 抽拔力(); 受力点到斜导柱固定板平面的距离(); 抽拔角; 斜导柱钢材许用弯曲应力()碳素钢; (6-4)计算如下:取。6.2.5 斜导柱的总长度计算图6-2 导柱长度计算导柱长度计算公式为(字母对应的尺寸如图6-2所示) (6-5)式中 斜导柱的总长度(); 斜导柱台肩直径(); 斜导柱抽拔角; 斜导柱固定板厚度(); 斜导柱与侧滑块斜孔的配合间隙(); 抽芯距(),实际距离加24。计算如下:取的长度为40。7.1 推杆脱模机构采用圆柱型推杆优点:由于圆柱形状的推杆和推杆孔最容易加工,而且很容易保证其配合精度,易于保证其互换性,并且易于更换,而且它还具有滑动阻力小,不易于卡滞等。推杆结构形式如图7-1(a)所示;推杆的固定形式如图7-1(b)。 (a) (b)图7-1 推杆结构形式7.2 推杆尺寸计算及校核7.2.1 推杆直径计算推杆直径计算公式为: (7-1)式中 圆形推杆直径(); 推杆长度系数, 0.7; 推杆长度(); 推杆数量; 钢材抗拉弹性模量(); 脱模力()。计算如下:取标准值推杆直径。7.2.2 推杆应力校核推杆应力校核公式为: (7-2)式中 推杆应力();脱模力();推杆数量;圆形推杆直径(); 推杆钢材的屈服极限强度()。一般中碳钢;合金中碳钢计算如下:7.3 推杆脱模机构布局推杆的布局如图7-2所示图7-2 推杆的布局8.1冷却系统设计模具的冷却是将注塑成型过程中产生的、并传导给模具的热量尽可能迅速、并最大程度地导出,以使塑件以较快的速度冷却固化。因此,冷却的效果直接决定着塑件的质量和注塑效果。调节模具温度的主要目的是:缩短成型周期;提高塑件质量。模具的冷却主要采用的是循环水冷却方式,而此次设计中采用的冷却方式就是采用的循环水冷却方式。8.2 冷却管道的直径计算已知条件:塑件材料为ABS;塑件的成型周期根据经验方法得壁厚6的制件成型周期为45;成型周期内塑件的质量为=14.51;水的密度为。8.2.1 求塑件在固化时每小时释放的热量塑件的产量计算公式为: (8-1)式中 塑件的产量(); 成型周期内塑件的质量(); 每小时成型次数()。计算如下:查表81得ABS的单位热流量表8-1常用塑料熔体的单位热流量塑料品种塑料品种ABS低密度聚乙烯聚甲醛高密度聚乙烯丙烯酸聚丙烯醋酸纤维素聚碳酸酯聚酰胺聚氯乙烯所以总热流量为: (8-2)式中 总热流量();塑件的产量();单位热流量()。计算如下:8.2.2 求冷却水的体积流量 冷却水的体积流量公式为: (8-3)式中 冷却水的体积流量();总热流量();水的密度(); 冷却介质的比热容(); 模温与冷却介质温度之间的平均温差()。计算如下:8.2.3 求冷却水的管道直径 查表8-2,为了使冷却水处于湍流状态,取d=8mm。表8-2冷却水的稳定湍流速度与流量冷却水道直径最低流速流量81.66101.32121.10150.878.3 冷却管道的孔数计算8.3.1 求冷却水在管道内的流速冷却水在管道内的流速公式为: (8-4)式中 冷却水在管道内的流速();冷却水的体积流量(); 冷却水道直径()。计算如下:8.3.2 求冷却管道孔壁与冷却介质之间的传热系数 查表8-3,取=6.48(水温为时)表8-3不同水温下的值平均水温05101520254.915.305.686.076.456.48由公式: (8-5)式中 冷却管道孔壁与冷却介质之间的传热系数;冷却介质的比热容();水的密度();冷却水在管道内的流速();冷却水道直径()。计算如下:8.3.3 求冷却管道中的传热面积由公式: (8-6)式中 冷却管道中的传热面积();塑件的产量();单位热流量();冷却管道孔壁与冷却介质之间的传热系数;模温与冷却介质温度之间的平均温差()。计算如下:8.3.4 求模具上应开设的冷却管道的孔数由公式: (8-7)式中 冷却管道中的传热面积();圆周率;冷却水道直径();冷却管道长度()。计算如下:所以模具上开设的管道孔数为4。3、 后期拟完成的研究工作及进度安排 1、注射模具的温度调节系统的设计 2、塑料模具部装图的绘制 3、零件图的绘制 凹模嵌板的绘制; 凸模嵌板的绘制; 4、撰写毕业设计论文。4、 存在的困难与问题 无5、 日程安排 11月27日12月11日模具部件装配图的绘制; 12月12日12月20日模具零件图的绘制; 12月21日 1月01日 撰写毕业设计论文与准备答辩; 1月01日 1月08日 毕业答辩;6、 如期完成全部论文工作的可能性根据日程和时间的安排,可以按时完成毕业设计。哈尔滨工业大学华德应用技术学院毕业设计(论文)开题报告 题 目:散热风扇支架注射模设计 系 (部) 材料工程系 专 业 材料成型及控制工程 学 生 赵佳辉 学 号 1089522120 班 号 0895221 指导教师 朱斌海 开题报告日期 2011年10月21日 哈工大华德学院说 明一、开题报告应包括下列主要内容:1课题来源及研究的目的和意义;2国内外在该方向的研究现状及分析;3主要研究内容;4研究方案及进度安排,预期达到的目标;5预计研究过程中可能遇到的困难和问题,以及解决的措施;6主要参考文献。二、对开题报告的要求1开题报告的字数应在1000字以上;2阅读的主要参考文献应在5篇以上,本科学生应有相应的外文资料。本学科的基础和专业课教材一般不应列为参考资料。3参考文献按在开题报告中出现的次序列出;4参考文献书写顺序:序号 作者.文章名.学术刊物名.年,卷(期):引用起止页。三、如学生首次开题报告未通过,需在一周内再进行一次。四、开题报告由指导教师填写意见、签字后,统一交所在院(系)保存,以备检查。指导教师评语: 指导教师签字: 检查日期: 毕业设计(论文)开题报告一、毕业设计(论文)任务书1.题 目:散热风扇支架注射模设计2.工作量:(1) 计算说明部分 编写计算说明书一份,约10000字(2) 图纸部分 完成A0图纸2张,零件图若干(3) 技术条件 制品材料:ABS 生产批量:小批量生产(4) 制品三维图:如图1所示(5) 制品二维图:如图2所示 图1散热风扇支架三维图 图2散热风扇支架二维图 二、选题的目的和意义本课题的研究将涉及一些二维和三维的软件的应用,如Auto CAD,Pro/E等,以及相关软件的应用,这将会使我运用这些软件的能力得到提升。通过本次毕业设计,能全面系统的掌握塑料模设计的一般方法和典型零件的加工工艺的编制。本次学习将对我进一步巩固所学知识及灵活应用所学知识来解决实际问题有着深远的意义。另外,通过本次毕业设计,将使我掌握写论文的一般步骤及方法。同时也提高了我如何快速而有效的查阅相关信息的方法,不仅锻炼了我在遇到困难时冷静分析,独立思考及解决问题的能力,而且培养了我和同学相互讨论,相互学习的习惯。 材料只有通过成型才能成为具有使用价值的各种产品,75%以上的金属制品,95%以上的塑料制品是通过模具来成型的。采用模具生产制件具有效率高,质量好,切削少,节约能源和原材料,成本低等一系列优点,模具成型已成为当代工业当代生产的重要手段,成为多种成型工艺中最具有潜力的发展方向。模具是机械,电子等行业的基础工业,它对国民经济和社会的发展起着越来越大的作用。塑料生产中先进合理的成型工艺,高效的设施,先进的模具是必不可少的重要因素。塑料模具对实现塑料成型工艺要求和塑件使用要求起着十分重要的作用。任何塑件生产和更新换代都是以模具的制造和更新为前提的,由于目前工业和民用塑件的产量猛增,质量要求越来越高,因而导致了塑料模具研究,设计和制造技术的迅猛发展。三、论文综述1.模具工业在国民经济中的地位模具工业是国民经济的基础工业,是国际上公认的关键工业。用模具制造零件效益高,产品质量好,材料消耗低,生产成本低,所以广泛应用于制造业中。模具生产技术水平的高低是衡量一个国家产品制造水平高低的重要标志,它很大程度上决定着产品的质量,效率和新产品的开发能力。随着科技的发展,国内已经认识到了模具在制造业中的重要基础地位,许多模具企业十分重视技术发展,增大了用于模具技术进步的投资。早在1989年3月中国政府颁布的关于当前产业政策要点的决定中,就将模具列为机械工业技术改造的第一位,模具工业既是高新技术产业的一个组成部分,又是高新技术产业的重要领域。模具在机械,电子,轻工,汽车,纺织,航空航天等领域里,日益成为使用最广泛的主要工艺 装备,它承担了这些领域中60%90%的产品的零件,组件和部件的生产加工。模具制造业的重要性主要体现在市场的需求上,而目前国际市场供不应求,因此研究和发展模具技术,提高技术水平,对提高国民经济的发展有特别重要的意义。 2.模具的分类和占有量模具主要类型有:冲模,锻模,塑料模,压铸模,粉末合金模,玻璃模,橡胶模,陶瓷模等。塑料模是塑料成型的工艺装备,塑料模可占模具总数的35%,塑料模主要包括压塑模,挤塑模,注射模,此外还有挤出成型模,泡沫塑料的发泡成型模,低发泡注射成型模,吹塑模等。3.我国模具工业的现状自20世纪80年代以来,我国的经济逐渐起飞,也为模具产业的发展提供了巨大的动力。90年代以后大部分工业发展十分迅速,模具工业总产值由1990年到1994年增长了70亿人民币,2000年增至270亿人民币,今后预计每年仍会以10-15亿的速度快速增长。目前,我国有17000多个模具生产厂点,从业人数五十多亿。除了国有的专业模具厂外,其他所有制形式的模具厂家也都得到了快速发展,其中集体和私营的企业在广东和浙江等省发展的最为迅速。4.我国模具技术的现状及发展趋势中国的塑料模具工业从起步到现在,历经了半个多世纪,有了很大的发展,模具水平有了较大的提高。许多模具企业十分重视技术发展,加大了技术进步的投入力度,并将其作为企业发展的重要动力。大型模具方面已能生产48(约122cm)大屏幕彩电塑壳注射模具,6.5kg大容量洗衣机全套塑料模具以及汽车保险杠和整体仪表等塑料模具,精密塑料模方面,已能生产照相机塑料件模具,多型腔小模数齿轮模具及塑封模具。经过多年的努力,在模具CAD/CAM/CAE技术,模具的电加工和数控加工技术,快速成型与快速制模技术,新型模具材料等方面取得了显著进步,在提高模具质量和缩短模具设计制造周期等方面做出了贡献。从模具设计和制造两方面来看,模具发展趋势归纳为以下几点:1 理论研究不断发展,设计计算日趋成熟;2 塑料模的高效率自动化;3 大型塑料模具;4 高精度塑料模具;5 模具计算机辅助设计(CAD)辅助工程(CAE);6 模具制造新工艺的进展;7 简易制模工艺的研究;8 模具标准化;9 特种塑料成型模具的研制。5. 国外模具工业的发展情况 当今国际市场正在进行新一轮的产业调整,一些模具制造业逐渐向发展中国家转移,中国正在成为世界模具大国。日本模具产能约占全球的40%,居全球第一位每年向国外出口大量模具。现在模具市场竞争日趋激烈,日本模具业在努力降低生产成本。随着模具工业全球化布局的发展,模具行业在美国工业总产值中所占的比重呈现不断下降的趋势,但是美国模具在全球模具的高端产品仍然占据着重要地位。德国技术含量较高的制造业作为立国之本,所以会加强模具技术的研究和开发。四、模具设计内容和设计方案1.主要研究内容利用Pro/E设计软件完成该塑件的三维实体造型设计,在查阅相关设计资料和分析该塑件注射成型工艺性基础上进行模具的总体方案设计及可行性分析。在完成模具参数计算和结构设计的基础上,最终完成该模具的总装配图、开模状态图、及有关的零件图设计以及塑化部件的装配图;最后完成设计计算说明书编写。 2.材料分析 本次设计散热风扇支架选用的材料为ABS,ABS无毒、无味、呈微黄色,成形的塑件有较好的光泽。密度为1.02 g/cm1.05g/cm,收缩率(0.4-0.8)%一般用(0.5)%。ABS有较好的抗冲击强度,且在低温下也不迅速下降。优良好的机械强度、硬度和一定的耐磨性、耐寒性、耐油性、耐水性、化学稳定性及电器性能。水、无机盐、碱、酸类对ABS几乎无影响。ABS有一定的硬度和尺寸稳定性,易于成形加工。经过调色可配成任何颜色。其缺点是耐热性不高,连续工作温度为70左右,热变形温度约为93左右。耐气候性差,在紫外线的作用下易变硬发脆,由于该零件仅起一个固定散热风扇叶片的作用。因此,选用5级精度。3.确定型腔数目 确定型腔的方法有很多,根据锁模力、最大注射量、制品的精度要求、模具成本。根据制品的一般精度和塑件的质量确定本设计为一模两件。4.选择分型面根据散热风扇支架模具结构及成型工艺的角度选择分型面,选择垂直于开模方向的介于定模座板和定模板之间的平面为一个分型面,垂直于开模方向且介于定模板和动模板之间的平面为另一个分型面。 5.选择注射模应从以下几方面考虑:(1)定模机构 定模机构是安装在注射机的固定模板上的部分型腔。由定位浇环,主流道体,定模底板,定模板,凹模组成一体,在注射机上固定不动。 (2)动模机构 动模机构是安装在注射机动模板上的部分型腔。由凸模,动模板,导柱,动模垫板组成一体,在注射机的锁模装置的驱动下往复运动。 (3)浇注系统 浇注系统是将熔融塑料引向闭合模腔的通道。通常由主流道,冷料穴,分流道和浇口等组成,本次设计采用平衡式点浇口浇注系统。 (4)脱模机构 塑件为散热风扇支架塑件,故利用斜导柱式侧向分型于抽芯机构的设计方法。 (5)导向装置 导向装置是用以保证动模和定模闭和时位置准确。它由导柱,导套组成,本次设计采用了复位杆、拉杆等导向装置。 (6)顶出机构 顶出机构是实现制品脱模的装置。常见有顶杆式,顶管式,推板式等,本次设计采用顶杆式顶出机构。 (7)冷却和加热装置 加热是为了满足注射成型工艺对模具温度的要求,冷却为使熔料能在模具内冷却定型。 (8)排气系统 排气系统是为了把型腔内原有的空气以及塑料受热过程中分解的气体排出,而在模具分型面处开设的排气槽。 本设计由于推杆较多,并且采用的是过渡配合,配合选用H8/f7。可以起到排气作用。另外,动模板与定模板之间留有间隙,同样可以起到排气作用,因此没必要开设专用的排气槽。五、毕业设计进度安排 1.第一阶段:开题 10月9日10月21日(2周),10月21日开题报告;2.第二阶段:设计阶段 10月24日12月9日(7周);3.第三阶段:撰写毕业设计论文与准备答辩 12月12日12月23日(2周);4.毕业答辩:12月28日12月30日六、主要参考文献 1、王连明、宋宝玉 机械设计课程设计 哈尔滨工业大学出版社,20052、刘颜召等 Pro/Engineer野火版3.0模具设计与加工 北京电子工业出版社 2007.10 3、肖祥芷、王孝培 中国模具设计大典 哈尔滨工业大学出版社,20034、叶久新、王群 塑料制品成型及模具设计 湖南科学技术出版社,20055、孙玉芹 机械精度设计基础 科学出版社,20046、陈剑鹤 塑料模具设计图册 清华大学出版社,2008.3 7、中国塑料机械信息网 WWW.SLJX.CN 首页,行业咨询,2006.4.198、刘品,李哲 机械设计与检测基础 哈尔滨工业大学出版社,20045哈尔滨工业大学华德应用技术学院毕业设计(论文)摘要 本论文主要通过对工控机散热风扇支架的设计分析,设计出该塑件的模具。在整个模具设计过程中,涉及到了塑件的结构设计、注塑机和模架的选择及注塑机的一些重要工艺参数的校核,并详细叙述了模具设计中的分型面设计、浇注系统设计、成型零件设计、顶出机构设计和冷却系统设计。利用塑料成型模拟分析软件Moldflow的MPI模拟其成型过程,制定合理的工艺方案并优化模具结构,Moldflow可提供如下分析:产品结构是否合理 、怎样选择合适的注塑材料 、怎样确定合理的浇口位置 、浇口位置自动优化 、预测熔接痕位置 、模具型腔是否充满 、最终制品的质量如何 、怎样选择合适的注塑机 、缩痕分析,所以这次设计中Moldflow的引入很重要。本论文基于Pro/E CAD系统,通过该系统,用户可以在可视化平台上交互式的设计注塑模具各个部件,不仅可以避免相似零件设计的重复性,大大提高其设计效率和设计质量,缩短产品的开发周期,而且方便了产品后续的有限元分析,同时也符合了现代设计思想的发展要求。关键词 模具设计;CAD;Pro/E;MoldFlowAbstractThis paper mainly through the plastic parts of the disc design analysis, design of the plastic molds. In the die design process, relate to the structural design of plastic parts, injection molding machines and die-injection molding machines and the choice of a number of important parameters of the verification process, and described in detail the design of the die-design, gating system design , molding parts design, the top agencies to design and cooling system design.In this paper, based on Pro / E CAD system, through the system, users can interactive visualization platform on the injection mold design various components, not only can avoid similar to the repetitive parts design, greatly improving the efficiency of its design and design quality and shorten product development cycle, and facilitate the follow-up product finite element analysis, but also in line with the thinking of the development of modern design requirements.Key words Mold Design;CAD;Pro/E;MoldFlow 目 录摘要IAbstractII第1章 绪论11.1 模具工业在国民经济中的地位11.2 各种模具的分类和占有量21.3 我国模具工业的现状31.4 世界五大塑料生产国的产能状况41.5 我国模具技术的现状及发展趋势7第2章塑件设计分析92.1 塑件模型建立92.1.1 模型3D图92.1.2 塑件2D图及其技术条件92.2 塑件参数设计102.2.1 材料选择102.2.2 塑件收缩率122.2.3 塑件的壁厚122.2.4 塑件的拔模斜度132.2.5 分型面的设计132.2.6 确定型腔数量以及排列方式132.3 本章小结14第3章注塑设备和模架选择153.1 注塑设备选择153.2 注塑机重要参数校核153.2.1 注塑容量校核153.2.2 锁模力校核163.2.3 开模行程校核173.3 模架选择173.4 本章小结18第4章浇注系统设计194.1 主流道设计194.1.1 浇口套设计194.1.2 浇口套的固定形式204.2 分流道设计204.2.1 分流道的形状204.2.2 分流道的布局214.2.3 分流道的长度214.3 浇口设计224.3.1 点浇口的尺寸224.3.2 浇口位置的选择224.4 冷料穴和钩料脱模装置234.5 本章小结23第5章成型零件设计加工工艺方案制定245.1 型腔的设计245.2 型芯的设计245.2.1 型芯的径向尺寸245.2.2 型芯的高度尺寸255.3 镶件的设计275.4 加工工艺方案制订275.4.1 型腔加工工艺方案275.4.2 型芯加工工艺方案285.5 本章小结28第6章侧向分型与抽芯机构设计296.1 机动侧向分型与抽芯机构296.2 斜销侧向分型抽芯机构主要参数296.2.1 抽芯距296.2.2 斜销的倾角306.2.3 抽芯力的计算306.2.4 圆形斜导柱直径的确定316.2.5 斜导柱的总长度计算326.3 本章小结33第7章脱模机构设计347.1 推杆脱模机构347.2 推杆尺寸计算及校核357.2.1 推杆直径计算357.2.2 推杆应力校核357.3 推杆脱模机构布局367.4 本章小结36第8章冷却系统设计378.1 冷却管道的直径计算378.1.1 求塑件在固化时每小时释放的热量378.1.2 求冷却水的体积流量388.1.3 求冷却水的管道直径398.2 冷却管道的孔数计算408.2.1 求冷却水在管道内的流速408.2.2 求冷却管道孔壁与冷却介质之间的传热系数408.2.3 求冷却管道中的传热面积418.2.4 求模具上应开设的冷却管道的孔数418.3 本章小结42第9章模具装配图和零件图439.1 模具装配图绘制439.1.1 模具装配图包含的内容439.1.2 模具装配图绘制步骤439.2 模具零件图绘制449.2.1 模具零件图包含的内容449.2.2 模具零件图绘制步骤449.3 本章小结45结论46致谢47参考文献48附录149附录250IV第1章 绪论1.1 模具工业在国民经济中的地位模具是制造业的一种基本工艺装备,它的作用是控制和限制材料(固态或液态)的流动,使之形成所需要的形体。用模具制造零件以其效率高,产品质量好,材料消耗低,生产成本低而广泛应用于制造业中。 模具工业是国民经济的基础工业,是国际上公认的关键工业。模具生产技术水平的高低是衡量一个国家产品制造水平高低的重要标志,它在很大程度上决定着产品的质量,效益和新产品的开发能力。振兴和发展我国的模具工业,正日益受到人们的关注。早在1989年3月中国政府颁布的关于当前产业政策要点的决定中,将模具列为机械工业技术改造序列的第一位。 模具工业既是高新技术产业的一个组成部分,又是高新技术产业化的重要领域。模具在机械,电子,轻工,汽车,纺织,航空,航天等工业领域里,日益成为使用最广泛的主要工艺装备,它承担了这些工业领域中的6090产品的零件,组件和部件的生产加工。 模具制造的重要性主要体现在市场的需求上,仅以汽车,摩托车行业的模具市场为例。汽车,摩托车行业是模具最大的市场,在工业发达的国家,这一市场占整个模具市场一半左右。汽车工业是我国国民经济五大支柱产业之一,汽车工业重点是发展零部件,经济型轿车和重型汽车,汽车模具作为发展重点,已在汽车工业产业政策中得到了明确。汽车基本车型不断增加,2005年将达到170种。一个型号的汽车所需模具达几千副,价值上亿元。为了适应市场的需求,汽车将不断换型,汽车换型时约有80的模具需要更换。中国摩托车产量位居世界第一,据统计,中国摩托车共有14种排量80多个车型,1000多个型号。单辆摩托车约有零件2000种,共计5000多个,其中一半以上需要模具生产。一个型号的摩托车生产需1000副模具,总价值为1000多万元。其他行业,如电子及通讯,家电,建筑等,也存在巨大的模具市场。 目前世界模具市场供不应求,模具的主要出口国是美国,日本,法国,瑞士等国家。中国模具出口数量极少,但中国模具钳工技术水平高,劳动成本低,只要配备一些先进的数控制模设备,提高模具加工质量,缩短生产周期,沟通外贸渠道,模具出口将会有很大发展。研究和发展模具技术,提高模具技术水平,对于促进国民经济的发展有着特别重要的意义。1.2 各种模具的分类和占有量模具主要类型有:冲模,锻摸,塑料模,压铸模,粉末冶金模,玻璃模,橡胶模,陶瓷模等。除部分冲模以外的的上述各种模具都属于腔型模,因为他们一般都是依靠三维的模具形腔是材料成型。 (1)冲模:冲模是对金属板材进行冲压加工获得合格产品的工具。冲模占模具总数的50以上。按工艺性质的不同,冲模可分为落料模,冲孔模,切口模,切边模,弯曲模,卷边模,拉深模,校平模,翻孔模,翻边模,缩口模,压印模,胀形模。按组合工序不同,冲模分为单工序模,复合模,连续模。 (2)锻模:锻模是金属在热态或冷态下进行体积成型是所用模具的总称。按锻压设备不同,锻模分为锤用锻模,螺旋压力机锻模,热模锻压力锻模,平锻机用锻模,水压机用锻模,高速锤用锻模,摆动碾压机用锻模,辊锻机用锻模,楔横轧机用锻模等。按工艺用途不同,锻模可分为预锻模具,挤压模具,精锻模具,等温模具,超塑性模具等。 (3)塑料模:塑料模是塑料成型的工艺装备。塑料模约占模具总数的35,而且有继续上升的趋势。塑料模主要包括压塑模,挤塑模,注射模,此外还有挤出成型模,泡沫塑料的发泡成型模,低发泡注射成型模,吹塑模等。 (4)压铸模:压铸模是压力铸造工艺装备,压力铸造是使液态金属在高温和高速下充填铸型,在高压下成型和结晶的一种特殊制造方法。压铸模约占模具总数的6。 (5)粉末冶金模:粉末冶金模用于粉末成型,按成型工艺分类粉末冶金模有:压模,精整模,复压模,热压模,粉浆浇注模,松装烧结模等。 模具所涉及的工艺繁多,包括机械设计制造,塑料,橡胶加工,金属材料,铸造(凝固理论),塑性加工,玻璃等诸多学科和行业,是一个多学科的综合,其复杂程度显而易见。1.3 我国模具工业的现状自20世纪80年代以来,我国的经济逐渐起飞,也为模具产业的发展提供了巨大的动力。20世纪90年代以后,大陆的工业发展十分迅速,模具工业的总产值在1990年仅60亿元人民币,1994年增长到130亿元人民币,1999年已达到245亿元人民币,2000年增至260270亿元人民币。今后预计每年仍会以1015的速度快速增长。 目前,我国17000多个模具生产厂点,从业人数五十多万。除了国有的专业模具厂外,其他所有制形式的模具厂家,包括集体企业,合资企业,独资企业和私营企业等,都得到了快速发展。其中,集体和私营的模具企业在广东和浙江等省发展得最为迅速。例如,浙江宁波和黄岩地区,从事模具制造的集体企业和私营企业多达数千家,成为我国国内知名的“模具之乡”和最具发展活力的地区之一。在广东,一些大集团公司和迅速崛起的乡镇企业,为了提高其产品的市场竞争能力,纷纷加入了对模具制造的投入。例如,科龙,美的,康佳和威力等知名集团都建立了自己的模具制造中心。中外合资和外商独资的模具企业则多集中于沿海工业发达地区,现已有几千家。 在模具工业的总产值中,企业自产自用的约占三分之二,作为商品销售的约占三分之一。其中,冲压模具约占50(中国台湾:40),塑料模具约占33(中国台湾:48),压铸模具约占6(中国台湾:5),其他各类模具约占11(中国台湾:7)。 中国台湾模具产业的成长,分为萌芽期(19611981),成长期(19811991),成熟期(19912001)三个阶段。 萌芽期,工业产品生产设备与技术的不断改进。由于纺织,电子,电气,电机和机械业等产品外销表现畅旺,连带使得模具制造,维修业者和周边厂商(如热处理产业等)逐年增加。在此阶段的模具包括:一般民生用品模具,铸造用模具,锻造用模具,木模,玻璃,陶瓷用模具,以及橡胶模具等。 1981年1991年是台湾模具产业发展最为迅速且高度成长的时期。有鉴于模具产业对工业发展的重要性日益彰显,自1982年起,台湾地区就将模具产业纳入“策略性工业适用范围”,大力推动模具工业的发展,以配合相关工业产品的外销策略,全力发展整体经济。随着民生工业,机械五金业,汽机车及家电业发展,冲压模具与塑料模具,逐渐形成台湾模具工业两大主流。从1985年起,模具产业已在推行计算机辅助模具设计和制造等CAD/CAM技术,所以台湾模具业接触CAD/CAM/CAE/CAT技术的时间相当早。 成熟期,在国际化,自由化和国际分工的潮流下,1994年,1998年,由台湾地区政府委托金属中心执行“工业用模具技术研究与发展五年计划”与“工业用模具技术应用与发展计划”,以协助业界突破发展瓶颈,并支持产业升级,朝向开发高附加值与进口依赖高的模具。1997年11月间台湾凭借模具产业的实力,获得世界模具协会(ISTMA)认同获准入会,正式成为世界模具协会会员。整体而言,台湾模具产业在这一阶段的发展,随着机械性能,加工技术,检测能力的提升,以及计算机辅助设计,台湾模具厂商供应对象已由传统的民用家电,五金业和汽机车运输工具业,提升到计算机与电子,通信与光电等精密模具,并发展出汽机车用大型钣金冲压,大型塑料射出及精密锻造等模具。1.4 世界五大塑料生产国的产能状况美国塑料(原料)的产量多年来一直雄居各国之首。早在80年代前期,美国塑料产量就已达之多,1986年增至,占全球总产量8100的28.5,此后美国塑料产量继续呈现稳定增长之势,1988年、1990年、1992年、1994年、1996年和1998年分别增加到、和,占世界总产量的比例从1996年起提高到30以上。2001年美国塑料产量为,其中以聚乙烯为最多,达。其次分别是氯乙烯、聚丙烯、聚苯乙烯对酞酸脂、聚苯乙烯。国内塑料消费量(产量+进口量一出口量),美国也是全球最多的。美国的全部塑料消费量2001年为。美国人均塑料消费量也是很高的,2000年为159,2001年略减为155,居全球第三位。美国现有各种大小塑料企事业单位1万多家,其中职工人数少于50人的占总数的53,50100人的占21,100500人的占23,超过500人的占近4,职工总数近90万人。在美国塑料制品加工业的就职人数达110万,2001年的出货金额为2150亿美元,人均出货金额为195美元。 德国是世界最大的塑料(原料)生产国之一,上世纪90年代初的1991年、1992年和1993年,德国塑料产量都为,1994年增达超过的1998年达近,1999年为近,2000年增至,超过日本为世界第二大塑料生产国,2001年上升为,2002年已过。2001年德国生产的种种塑料原料中,聚乙烯为 (低密度聚乙烯,高密度聚乙烯),氯乙烯,聚丙烯。德国2001年的国内塑料消费量为,其中聚乙烯,聚丙烯氯乙烯。德国人均塑料消费量2001年为160,在世界上仅少于比利时的172,高于美国的155,排在世界第二位。德国塑料制品加工业的职工总计有近30万人,2001年的出货金额为360亿美元,人均126美元。德国塑料制品加工企业中职工少于50人的占44,50100人的占28,100500人的占25,500人以上的占4。 中国塑料工业多年持续高速增长,1991年产量仅为,1995年增为,1998年超过,到2002年已增达约,超过日本而成为世界第三大塑料原料生产国。中国今年塑料制品市场将持续走强,在包装、工程、建材、农用和日用塑料制品等各个领域都将有较大幅度的增长,需求量将超过。其中包装塑料制品今年需求量将超过,工程塑料制品需求量将达左右,建材塑料制品需求量将达以上,农用塑料制品需求量将在左右,日用塑料制品需求量约为左右。 日本在很长的时期内都是仅次于美国的世界第二大塑料生产国。一直到1997年,日本塑料产量曾经连续多年增长,年产量在70年代中期就已达,1987年突破,1991年达约,1992年和1993年因受日本经济下滑的影响,产量略有减少,分别降至和。从1994年起产量再度增长,1994年、1995年和1996年分别回升到、和,1997年的产量又比上年增长3.7,达到,首次超过。但这种增势在1998年受到遏制,产量大幅度减少。1998年,日本塑料产量为,比上年减少了8.7。1999年和2000年日本塑料产量分别回升到和,但仍远未恢复到1997年的水平。2001年和2002年日本塑料产量再度下降至以下的和。2002年日本塑料(原料)产量减为。而中国则增为,日本又退居第三位。 韩国塑料产量增长十分迅速,1986年超过,1990年增达,1992年突破,1994年、1996年和1997年分别上升到、和,1998年产量增至,1999年突破,2001年达,跻身于世界五大塑料生产国之列。韩国塑料原料产品中以聚乙烯居首,2001年产量为 (低密度聚乙烯,高密度聚乙烯),聚丙烯以排在第二位,其次分别是聚酯、氯乙烯、ABSAS树脂、聚苯乙烯。韩国国内塑料消费量2001年,只相当于产量的1/3略高。人均塑料消费量2001年为106,韩国塑料制品加工业的职工总数2001年为3.1万人,出货金额为85亿美元,人均276美元。 塑料产量位居世界前十名的国家和地区还有法国、比利时、中国台湾、加拿大和意大利 (均为2001年产量)。1.5 我国模具技术的现状及发展趋势20世纪80年代开始,发达工业国家的模具工业已从机床工业中分离出来,并发展成为独立的工业部门,其产值已超过机床工业的产值。改革开放以来,我国的模具工业发展也十分迅速。近年来,每年都以15的增长速度快速发展。许多模具企业十分重视技术发展。加大了用于技术进步的投入力度,将技术进步作为企业发展的重要动力。此外,许多科研机构和大专院校也开展了模具技术的研究与开发。模具行业的快速发展是使我国成为世界超级制造大国的重要原因。今后,我国要发展成为世界制造强国,仍将依赖于模具工业的快速发展,成为模具制造强国。 中国塑料模工业从起步到现在,历经了半个多世纪,有了很大发展,模具水平有了较大提高。在大型模具方面已能生产48(约122)大屏幕彩电塑壳注射模具,6.5大容量洗衣机全套塑料模具以及汽车保险杠和整体仪表板等塑料模具,精密塑料模方面,以能生产照相机塑料件模具,多形腔小模数齿轮模具及塑封模具。经过多年的努力,在模具CAD/CAE/CAM技术,模具的电加工和数控加工技术,快速成型与快速制模技术,新型模具材料等方面取得了显著进步;在提高模具质量和缩短模具设计制造周期等方面作出了贡献。 尽管我国模具工业有了长足的进步,部分模具已达到国际先进水平,但无论是数量还是质量仍满足不了国内市场的需要,每年仍需进口10多亿美元的各类大型,精密,复杂模具。与发达国家的模具工业相比,在模具技术上仍有不小的差距。今后,我国模具行业应在以下几方面进行不断的技术创新,以缩小与国际先进水平的距离。 (1)注重开发大型,精密,复杂模具;随着我国轿车,家电等工业的快速发展,成型零件的大型化和精密化要求越来越高,模具也将日趋大型化和精密化。 (2)加强模具标准件的应用;使用模具标准件不但能缩短模具制造周期,降低模具制造成本而且能提高模具的制造质量。因此,模具标准件的应用必将日渐广泛。 (3)推广CAD/CAM/CAE技术;模具CAD/CAM/CAE技术是模具技术发展的一个重要里程碑。实践证明,模具CAD/CAM/CAE技术是模具设计制造的发展方向,可显著地提高模具设计制造水平。 (4)重视快速模具制造技术,缩短模具制造周期。第2章塑件设计分析2.1 塑件模型建立2.1.1 模型3D图模型绘制3D图采用PTC公司的产品Pro/ENGINEER Wildfire 3.0,最终绘制出来的3D结构图2-1所示: 图2-1塑件模型3D图2.1.2 塑件2D图及其技术条件模型2D图绘制采用Autodesk公司的产品AutoCAD2006, 最终绘制出来的2D结构图2-2所示: 图2-2塑件模型2D图1.塑件精度等级及尺寸公差塑件采用的精度等级为5级精度,部分尺寸的公差标注如图2-2所示。2.塑件的表面质量该塑件要求外形美观,色泽鲜艳,外表面没有斑点及熔接痕,粗糙度可取。2.2 塑件参数设计2.2.1 材料选择通常,选择塑件的材料依据是它所处在的工作环境及使用性能的要求,以及原材料厂家提供的材料性能数据。对于常温工作状态下的结构件来说,要考虑的主要是材料的力学性能,如屈服应力,弹性模量,弯曲强度,表面硬度等。该塑件为一般的零件,属于圆盘类,没有特别的要求,根据以上的依据,选择材料ABS为塑料件的材料。ABS塑料 化学名称:丙烯腈-丁二烯-苯乙烯共聚物 英文名称:Acrylonitrile Butadiene Styrene 比重:1.05 成型收缩率:0.40.7 成型温度:200240 干燥条件:8090 2 特点: (1)综合性能较好,冲击强度较高,化学稳定性,电性能良好。(2)与372有机玻璃的熔接性良好,制成双色塑件,且可表面镀铬,喷漆处理。 (3)有高抗冲、高耐热、阻燃、增强、透明等级别。(4)流动性比HIPS差一点,比PMMA、PC等好,柔韧性好。 成型特性: (1)无定形料,流动性中等,吸湿大,必须充分干燥,表面要求光泽的塑件须长时间预热干燥8090,3h。(2)宜取高料温,高模温,但料温过高易分解(分解温度为270)。对精度较高的塑件,模温宜取5060,对高光泽。耐热塑件,模温宜取6080。(3)如需解决夹水纹,需提高材料的流动性,采取高料温、高模温,或者改变入水位等方法。 (4)如成形耐热级或阻燃级材料,生产37天后模具表面会残存塑料分解物,导致模具表面发亮,需对模具及时进行清理,同时模具表面需增加排气位置。ABS树脂是目前产量最大,应用最广泛的聚合物,它将PS,SAN,BS的各种性能有机地统一起来,兼具韧,硬,刚相均衡的优良力学性能。ABS是丙烯腈、丁二烯和苯乙烯的三元共聚物,A代表丙烯腈,B代表丁二烯,S代表苯乙烯。 ABS工程塑料一般是不透明的,外观呈浅象牙色、无毒、无味,兼有韧、硬、刚的特性,燃烧缓慢,火焰呈黄色,有黑烟,燃烧后塑料软化、烧焦,发出特殊的肉桂气味,但无熔融滴落现象。ABS工程塑料具有优良的综合性能,有极好的冲击强度、尺寸稳定性好、电性能、耐磨性、抗化学药品性、染色性,成型加工和机械加工较好。ABS树脂耐水、无机盐、碱和酸类,不溶于大部分醇类和烃类溶剂,而容易溶于醛、酮、酯和某些氯代烃中。 ABS工程塑料的缺点:热变形温度较低,可燃,耐候性较差。用途: 适于制作一般的机械零件,磨耐磨零件,盘体,车配件,日用品,管材及文具等。2.2.2 塑件收缩率根据以上选用的材料为ABS,查相关资料可知,ABS的收缩率为0.0040.007,由公式(2-1)求出ABS平均收缩率: (2-1)式中 塑料的平均收缩率; 塑料的最大收缩率;塑件的最小收缩率。计算如下: 2.2.3 塑件的壁厚 一般说来,塑件的厚度越厚就越能满足产品的强度和刚度的性能要求,但是从塑件的成型过程看来,塑件的壁厚越厚,冷却的时间就越长,整个塑件的成型周期就要延长,提高了生产的成本,降低了生产的效率,同时,塑件的壁厚越厚,收缩率就增大,这样使的得产品的尺寸不稳定性增加,降低了产品的质量。因此产品的厚度必须得适中,根据材料的的特性,查阅相关的资料,查得ABS制品的壁厚通常为1、1.2、1.5、2、2.5、3、6mm。本次设计中,塑件的壁厚为6mm。2.2.4 塑件的拔模斜度拔模斜度是为了便于脱模,防止塑件表面在脱模时划伤,擦毛,在设计塑件表面沿脱模方向应具有合理的脱模斜度。塑件的脱模斜度大小跟塑件的性质、收缩率、摩擦因素、塑件的壁厚和几何形状有关。在设计时,可以参考一些资料来确定塑件的脱模斜度,一般以塑件的材料为选择依据,而ABS塑料的脱模斜度为40 1 20,本设计选择的脱模斜度为。2.2.5 分型面的设计选择分型面是为了便于塑件的脱模和简化模具结构,该塑件因为壁薄故应采用点浇口形式进料,采用点浇口时,为了能取出流道凝料,应使用三板式双分型面模具。2.2.6 确定型腔数量以及排列方式本次模具设计采用的是一模两腔,型腔的分布如图2-3所示:图2-3型腔分布图2.3 本章小结通过绘制塑件的2D,3D图,来直观分析塑件的具体形状和结构,为模具所需要的成型零件的选择奠定基础。第3章注塑设备和模架选择3.1 注塑设备选择选取注射机型号为,具体参数如表3-1:表3-1注塑机参数理论容量ShotSize (Theoretical)60注塑速率Injection Rateg/s70塑化能力Plasticizing Capacityg/s35注塑压力Injection PressureMpa180锁模力Clamp TonnageKN400移模行程Toggle Strokemm250最大模厚Max Mold Heightmm250最小模厚Min Mold Heightmm150喷嘴球半径Spray nozzlemm10喷嘴口孔径Aperture nozzlemm33.2 注塑机重要参数校核3.2.1 注塑容量校核注塑机标准规定,以容量计算时,必须使得在一个注塑成型周期内所需的注塑塑料熔体的容量在注塑机额定注塑量的80内,也就是 (3-1)式中 注塑机最大注塑容量(); 成型塑件与浇注系统体积的总和(); 为最大注塑容量的利用系数。计算如下: (3-2) 式中 成型塑件的体积,乘以2是因为本次的模具是一模两腔; 浇注系统中主流道,分流道,浇口,冷料穴的体积和。所以, 注 (3-3)而注塑机的注塑容量为60,所以注塑机的注塑容量符合要求。3.2.2 锁模力校核当高压的塑料熔体充满型腔时,会产生一个沿注塑机轴向的很大的推力,其大小等于制件与浇注系统在份型面上的垂直投影之和乘与型腔内塑料熔体的平均压力。该推力应该小于注塑机额定的锁模力,否则在注塑成型时会因锁模不紧而发生溢边跑料现象。型腔内塑料熔体的推力()可按下式计算 (3-4)式中 型腔内塑料熔体沿注塑机轴向的推力(); 塑料与浇注系统在分型面上的投影面积(); 压力损耗系数,取0.4; 注塑压力。计算如下:=1844.96 =180 也就是型腔内的塑料熔体沿注塑机轴向的推力为133,而注塑机的锁模力为400,所以注塑机的锁模力符合要求。3.2.3 开模行程校核模具开模后为了能取出塑胶件,要求有足够的开模距离,本次模具使用的注塑机的开模行程是给定的,不受模具厚度的影响,当模具的厚度变化时,可由其调模装置调整。只要使得注塑机最大开模行程大于模具所需的开模距离就符合注塑的要求。即: (3-5) 式中 注塑机最大开模距离(); 模具所需的开模距离()。也就是,所以注塑机的锁模力符合要求。3.3 模架选择根据型腔排列的方式以及初步确定的壁厚,选择模架A4型,系列,其结构以及一些重要尺寸如图3-1、3-2所示: 图3-1 模架尺寸1 图3-2 模架尺寸23.4 本章小结模架尺寸的选择确定模具的整体框架,为模具具体内部设计奠定基础。第4章浇注系统设计4.1 主流道设计4.1.1 浇口套设计为了便于浇注凝料从主流道取出,主流道采用的圆锥孔;浇口套与注塑机喷嘴嘴头的接触球面必须吻合。注塑机的喷嘴是球面,其半径SR是固定的,为了浇口套端面的凹球面与注塑机的端凸球面接触良好,一般取半径: =SR+(12)mm (4-1)式中 主流道入口凹坑球面半径(); 喷嘴球半径()。在此次设计中,所以;而浇口套的圆锥孔的小端直径d应该大于喷嘴内孔直径: d=d +(0.51)mm (4-2)由注塑机的参数可以看到,所以,浇口套的端面凹球深度。浇口套的尺寸如图4-1所示图4-1 浇口套尺寸4.1.2 浇口套的固定形式本次设计中,浇口套与注塑机定位孔采用过盈配合。4.2 分流道设计4.2.1 分流道的形状分流道的截面形状常用的有圆形,梯形,和矩形, 其中圆形截面的分流道效率最高,也就是分流道流过相同的塑料流量,其分流道的内表面积最小。这样可以减少注塑过程中散热面积,即熔料的温度降低最小,同时使得摩擦力变小,减少压力损失。其缺点就是制造起来比较麻烦,因为它必须将分流道分设在模板的两侧,在对合时容易产生错口现象。当分型面为平面时候,常采用圆形截面流到,本次设计中,分型面非平面,采用圆形截面分流道加工困难,故采用效率较高的梯形截面分流道。4.2.2 分流道的布局本次模具设计为一模两腔,分流道的布局对塑料件的成型影响也较大的,由于前面已经将型腔的布局确定,设计分流道的布局既要跟型腔的布局协调,同时还应该注意一些分流道布局的设计要点:分流道和型腔的分布原则是排列紧凑,间距合理,应该采用轴对称或者中心对称,使其平衡,尽量缩小成型区域的总面积。最好使型腔和分流道在分型面上的总投影面积的几何中心和锁紧力的中心重合;在可能的情况下,分流道的长度尽可能的缩短,以减少压力损失,避免模体压力过大的影响成本。在多型腔模具中,各型腔的分流道长度应该尽量相等,以达到注塑时压力传递的平衡。分流道的布局如图4-2,分流道长度短,对称分布。 图4-2 分流道布局4.2.3 分流道的长度根据分流道的布局,大概的可以测量出分流道的长度总长;4.3 浇口设计本次设计采用的浇口为点浇口,其优点是浇口位置能灵活地确定,浇口附近变形小,多型腔时采用点浇口容易平衡浇注系统,对于投影面积大的塑件或易变形的塑件,采用多个点浇口能够取得理想的效果,适用一模多腔的模具。4.3.1 点浇口的尺寸根据经验的数据,一般的点浇口直径常为0.51.8,这里选1;浇口的长度常为0.52,这里选2。4.3.2 浇口位置的选择本次设计浇口位置的选择如图4-3所示: 图4-3 浇口位置示意图4.4 冷料穴和钩料脱模装置采用拉杆式钩料装置:由冷料穴和拉料杆组成,在冷料穴的底部设有一拉料杆,拉料杆固定在型腔板上,一次分型依靠拉料杆抽出主流道凝料。 其基本形状如图4-4所示,采用带球形头的冷料穴,其中冷料穴的直径要比主流道的稍大,主流道末端的半径大约为5,所以冷料穴的直径设为6,此处的拉料杆直径为4。图4-4 拉料杆形状示意图4.5 本章小结浇注系统的设计确定了主流道、分流道、浇口和冷料穴的形状及尺寸,确定了浇注系统的平衡和浇口的位置,决定了模具的类型。 第5章成型零件设计加工工艺方案制定5.1 型腔的设计采用整体式型腔,也就是由整块材料加工而成的型腔。整体式型腔的优点是,强度和刚度相对较高,且不易变形,对塑件的上表面不会产生拼模缝的痕迹,缺点为切削量大,模具成本高,同时给热处理和表面处理带来一定的困难。型腔的外形尺寸为:。 5.2 型芯的设计本次设计塑件中共有三个孔,两个的直孔和一个阶梯孔,故需要两个直型芯和一个阶梯型芯成型。型芯的径向和高度尺寸计算如下: 5.2.1 型芯的径向尺寸型芯径向尺寸计算公式: (5-1)式中 型芯径向基本尺寸();塑件内形尺寸(); 塑料的平均收缩率;修正系数,取3/4;塑件的公差();型芯制造公差,取/3()。大型芯径向尺寸计算如下: 小型芯径向尺寸计算如下: 5.2.2 型芯的高度尺寸型芯高度尺寸计算公式: (5-2)式中 型芯高度基本尺寸();塑件高度基本尺寸();塑料的平均收缩率;修正系数,取2/3;塑件的公差();型芯制造公差,取/3()。阶梯型芯高度尺寸计算如下: 型芯尺寸如图5-1、5-2所示:图5-1 阶梯型芯尺寸 图5-2 直型芯尺寸5.3 镶件的设计镶件位置放在定模板上,其尺寸形状如图5-3所示:图5-3 镶件形状及尺寸5.4 加工工艺方案制订塑料模具的加工方法大体上可以分为切削机床加工、钳加工和特殊加工三大类。切削机床加工是指采用不同的切削机床,如车床、铣床、磨床等进行粗加工或精加工等。钳加工是指采用锉、铲、研等手工措施去除切削机床所预留的加工余量,将模具半成品加工成符合蓝图的要求尺寸,形状以及表面粗糙度的合格零件,并通过组装总装成符合要求的模具。当模具零件使用普通机床或人工的传统的方法很难加工或者耗时很大时,则往往采用特殊加工的方法,如电火花,线切割以及等。5.4.1 型腔加工工艺方案表5-1型腔的加工工艺方案工序内容设备1234567铣削钻削CNC粗加工热处理磨削CNC精加工钳工端铣坯料的六个端面钻镶件孔粗加工成型面调质磨上、下端面精加工成型面抛光成型面、倒角,攻丝铣床钻床CNC磨床CNC5.4.2 型芯加工工艺方案表5-2型芯的加工工艺方案工序内容设备12345678铣削钻削CNC粗加工热处理磨削CNC精加工电火花加工钳工端铣坯料的端面钻孔粗加工成型面调质磨下端面精加工成型面加工镶件孔抛光成型面、倒角,攻丝铣床钻床CNC磨床CNCEDM5.5 本章小结通过对型芯型腔的计算,确定了模具成型零件的具体尺寸及加工方案。 第6章侧向分型与抽芯机构设计6.1 机动侧向分型与抽芯机构机动侧向分型与抽芯是利用注射机的开模力,通过传动机构改变运动方向,将侧向的活动型芯抽出。机动抽芯机构的结构比较复杂,但抽芯不需要人工操作,抽拔力较大,具有灵活,方便,生产效率高,容易实现全自动操作,无需另外添置设备等优点,在生产中被广泛采用。机动抽芯按结构形式可分为斜销,弹簧,弯销,斜导槽,斜滑块,楔块,齿轮条等多种抽芯形式。本设计采用的是斜销侧向分型抽芯机构。6.2 斜销侧向分型抽芯机构主要参数6.2.1 抽芯距型芯从成型位置抽到不妨碍塑件脱模的位置所移动的距离叫抽芯距,用表示。一般抽芯距等于侧向孔或侧凹深度加上23余量,即: =+(23)mm (6-1)式中 抽芯距();侧向孔或侧凹深度()。而所以 6.2.2 斜销的倾角斜销的倾角是决定斜销抽芯机构工作效果的一个重要参数,它不仅决定了开模行程和斜销长度,而且对斜销的受力状况有着重要的影响。决定倾斜角的大小时,应从抽芯距,开模行程和斜销受力几个方面综合考虑。实际生产中,一般取,不宜超过。选。6.2.3 抽芯力的计算抽芯力的计算跟脱模力的计算是一样的,计算的公式为 F=pA(fcos-sin) (6-2)式中 抽芯力();单位面积塑件对型芯的正压力(),一般取p(4.8411.76); 塑件包紧型芯的侧面积(); 塑件与模体钢材的摩擦系数,一般取0.10.3; 脱模斜度。计算得: 6.2.4 圆形斜导柱直径的确定图6-1 导柱直径计算计算公式(字母对应的尺寸如图6-1所示) (6-3)式中 斜导柱直径(); 抽拔力(); 受力点到斜导柱固定板平面的距离(); 抽拔角; 斜导柱钢材许用弯曲应力()碳素钢; (6-4)计算如下:取。6.2.5 斜导柱的总长度计算图6-2 导柱长度计算导柱长度计算公式为(字母对应的尺寸如图6-2所示) (6-5)式中 斜导柱的总长度(); 斜导柱台肩直径(); 斜导柱抽拔角; 斜导柱固定板厚度(); 斜导柱与侧滑块斜孔的配合间隙(); 抽芯距(),实际距离加24mm。计算如下:取的长度为40mm。6.3 本章小结通过对斜销侧向分型机构具体尺寸的设计和计算,确定了在模具中的相对位置和形状。第7章脱模机构设计本设计中的脱模机构采用推杆脱模机构7.1 推杆脱模机构采用圆柱型推杆优点:由于圆柱形状的推杆和推杆孔最容易加工,而且很容易保证其配合精度,易于保证其互换性,并且易于更换,而且它还具有滑动阻力小,不易于卡滞等。推杆结构形式如图7-1(a)所示;推杆的固定形式如图7-1(b)。 (a) (b)图7-1 推杆结构形式7.2 推杆尺寸计算及校核7.2.1 推杆直径计算推杆直径计算公式为: (7-1)式中 圆形推杆直径(); 推杆长度系数, 0.7; 推杆长度(); 推杆数量; 钢材抗拉弹性模量(); 脱模力()。计算如下:取标准值推杆直径。7.2.2 推杆应力校核推杆应力校核公式为: (7-2)式中 推杆应力();脱模力();推杆数量;圆形推杆直径(); 推杆钢材的屈服极限强度()。一般中碳钢;合金中碳钢计算如下:7.3 推杆脱模机构布局推杆的布局如图7-2所示图7-2 推杆的布局7.4 本章小结通过计算,确定了脱模的具体方式和推杆脱模机构的具体尺寸。第8章冷却系统设计模具的冷却是将注塑成型过程中产生的、并传导给模具的热量尽可能迅速、并最大程度地导出,以使塑件以较快的速度冷却固化。因此,冷却的效果直接决定着塑件的质量和注塑效果。调节模具温度的主要目的是:缩短成型周期;提高塑件质量。模具的冷却主要采用的是循环水冷却方式,而此次设计中采用的冷却方式就是采用的循环水冷却方式。8.1 冷却管道的直径计算已知条件:塑件材料为ABS;塑件的成型周期根据经验方法得壁厚6的制件成型周期为45;成型周期内塑件的质量为=14.51;水的密度为。8.1.1 求塑件在固化时每小时释放的热量塑件的产量计算公式为: (8-1)式中 塑件的产量(); 成型周期内塑件的质量(); 每小时成型次数()。计算如下:查表81得ABS的单位热流量表8-1常用塑料熔体的单位热流量塑料品种塑料品种ABS聚甲醛丙烯酸醋酸纤维素聚酰胺低密度聚乙烯高密度聚乙烯聚丙烯聚碳酸酯聚氯乙烯5.9108.1106.9108.1105.9102.7101.6103.610所以总热流量为: (8-2)式中 总热流量();塑件的产量();单位热流量()。计算如下:8.1.2 求冷却水的体积流量 冷却水的体积流量公式为: (8-3)式中 冷却水的体积流量();总热流量();水的密度(); 冷却介质的比热容(); 模温与冷却介质温度之间的平均温差()。计算如下:8.1.3 求冷却水的管道直径 查表8-2,为了使冷却水处于湍流状态,取d=8mm。表8-2冷却水的稳定湍流速度与流量冷却水道直
- 温馨提示:
1: 本站所有资源如无特殊说明,都需要本地电脑安装OFFICE2007和PDF阅读器。图纸软件为CAD,CAXA,PROE,UG,SolidWorks等.压缩文件请下载最新的WinRAR软件解压。
2: 本站的文档不包含任何第三方提供的附件图纸等,如果需要附件,请联系上传者。文件的所有权益归上传用户所有。
3.本站RAR压缩包中若带图纸,网页内容里面会有图纸预览,若没有图纸预览就没有图纸。
4. 未经权益所有人同意不得将文件中的内容挪作商业或盈利用途。
5. 人人文库网仅提供信息存储空间,仅对用户上传内容的表现方式做保护处理,对用户上传分享的文档内容本身不做任何修改或编辑,并不能对任何下载内容负责。
6. 下载文件中如有侵权或不适当内容,请与我们联系,我们立即纠正。
7. 本站不保证下载资源的准确性、安全性和完整性, 同时也不承担用户因使用这些下载资源对自己和他人造成任何形式的伤害或损失。

人人文库网所有资源均是用户自行上传分享,仅供网友学习交流,未经上传用户书面授权,请勿作他用。