数控车床尾座套筒液压装置设计
36页 19000字数+说明书+12张CAD图纸【详情如下】
半圆盘A4.dwg
导向套A2.dwg
底盘A4.dwg
接头A4.dwg
支承盘A3.dwg
数控车床尾座套筒液压装置设计论文.doc
数控车床总装图A0.dwg
活塞杆A3.dwg
液压尾座液压泵站总图A1.dwg
液压缸总装配图A1.dwg
盖板A4.dwg
缸体A2.dwg
缸底A3.dwg
缸筒A2.dwg

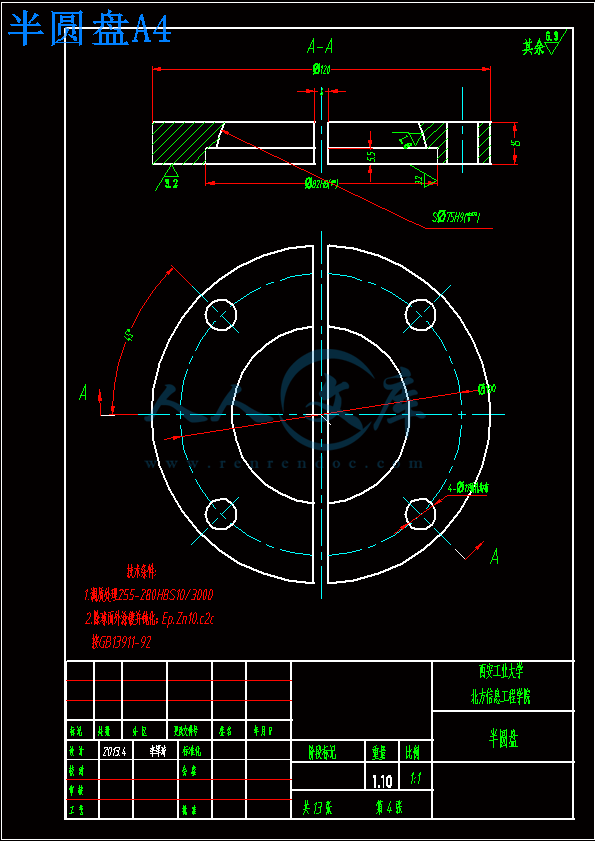
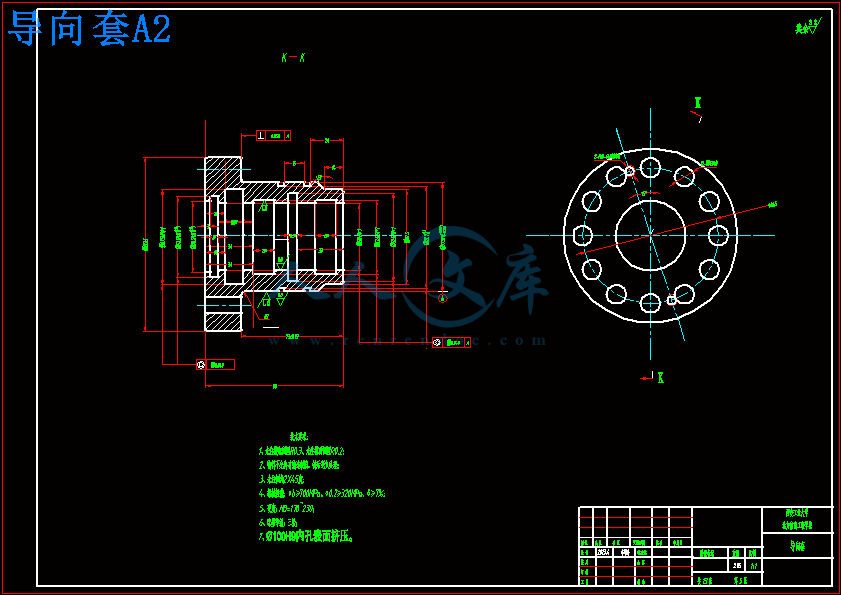
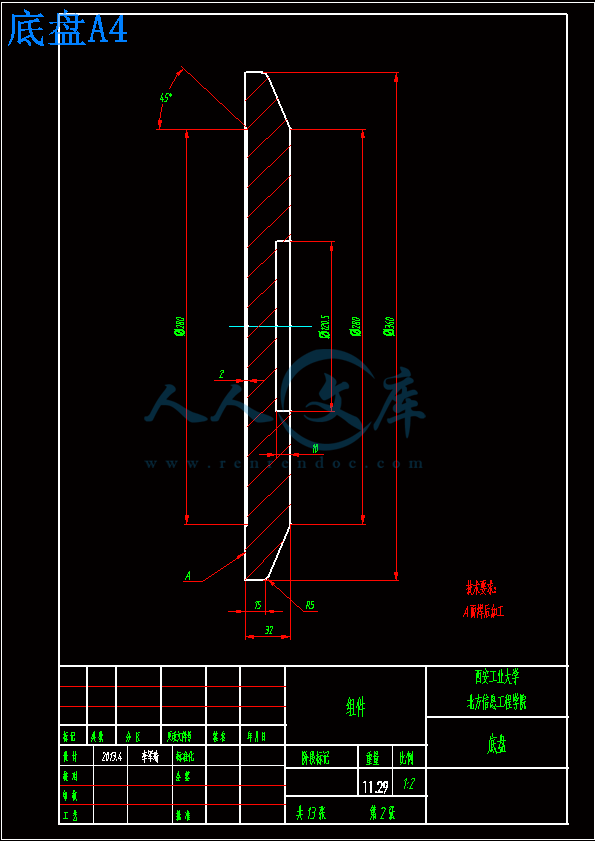

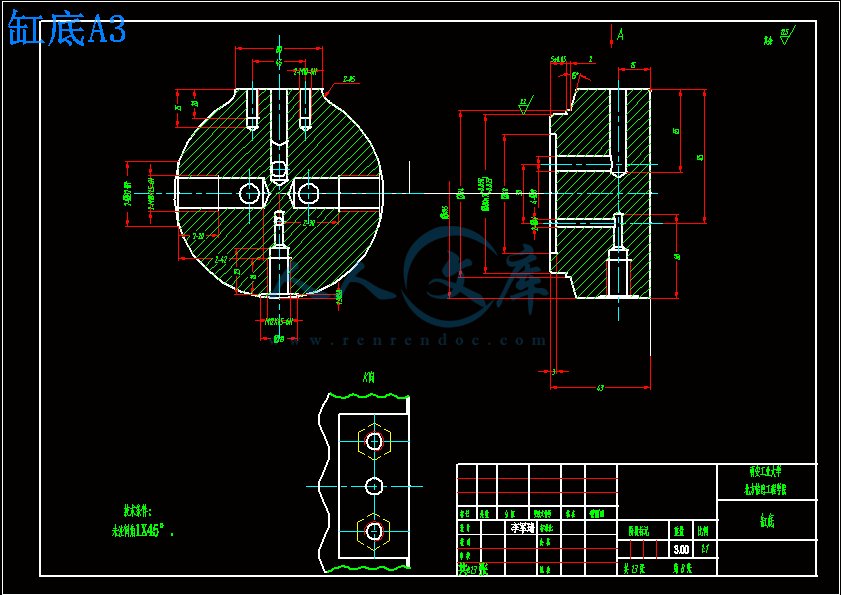





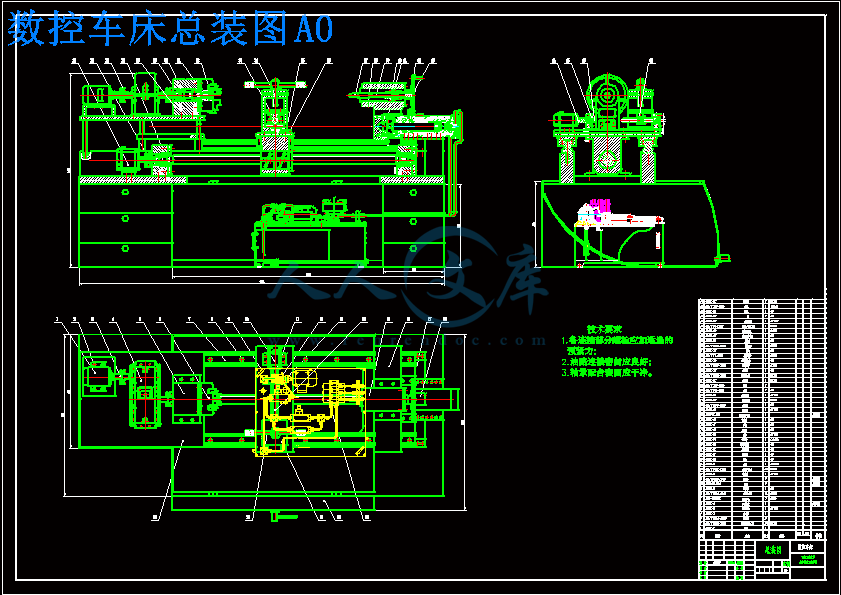


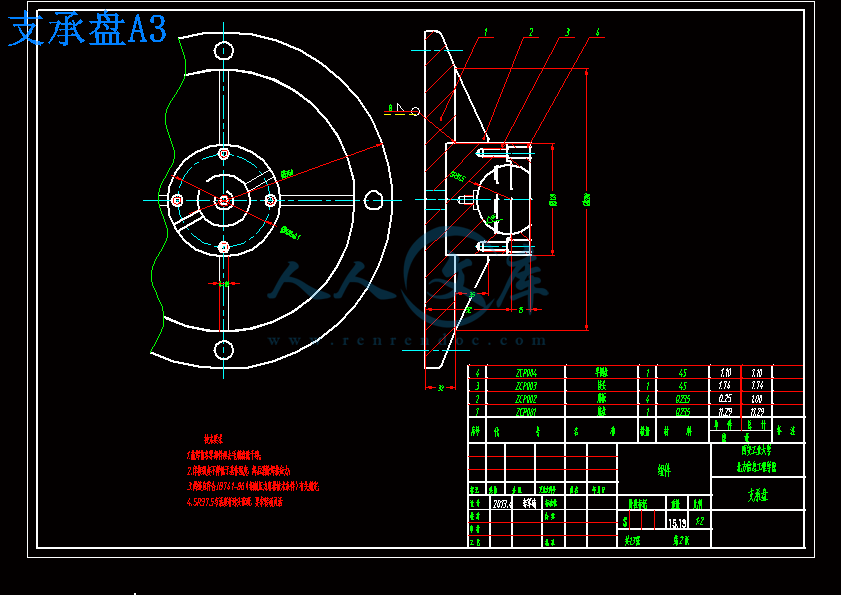
数控车床尾座套筒液压装置设计
摘要
为了完成本课题的设计,在设计之前的准备工作必须做好,首先是搜集和分析资料,主要包括国内外数控机床的发展现状;液压技术和液压传动系统的基本资料;同等机床液压尾座的图纸和资料等。其次是初步确定液压尾座的总体布局,包括配置形式、液压系统的布置及选择液压能源及相应的配套元件等。最后主要是关于尾座的设计计算。
数控机床变档卡紧及尾座顶紧的控制方式基本上是手工控制,在通常的加工过程中,需先用手工控制的方式完成变档和卡紧工作,然后再进行装夹,在装夹完毕后还需要使用手工控制的方式完成尾座的顶紧工作。由此可知,在数控机床的加工作效率效率并不高,而且工人劳动强度大,耗时又耗力,还会增加企业成本。因此,本课题研究所要达到的预期效果是在数控车床加工过程中,当需要使用尾座时,使用本课题所设计的尾座可以提高加工过程的机械化和自动化水平,提高生产效率,降低工人的劳动强度,降低企业成本。
关键词:数控机床;尾座;液压系统;液压缸
The design of CNC machine Tailstock Hydraulic system
Abstract??
To accomplish this design, I collected and analysed the information before the design, including domestic and international development of CNC machine tools; hydraulic system of hydraulic technology and the basic information; equal hydraulic machine Tailstock the drawings and information . Then is tentatively determined the overall layout of hydraulic Tailstock, including the allocation of form, layout and the hydraulic system of hydraulic energy, and select the appropriate matching components, such as. This was followed by the main Tailstock the design and calculation.
CNC machine tools changed file cards bear and Tailstock top tight is basically manual control, in the conventional process, the change required manual card file and clamping a tight and then again after the fixture also need to use a manual Tailstock The top tight. Therefore, in the process of CNC machine tools in efficiency is not high, workers in labor intensity and great. Therefore, the issue of the Institute to achieve the desired results in the CNC lathe processing, when the need to use Tailstock, the use of this issue by the Tailstock design can improve the process of mechanization and automation level, increase production efficiency and reduce Workers in the labor intensity.
Key words:Numerically-controlled machine;Tailstock;Hydraulic system;Hydraulic cylinder inside diameter
目录
1 绪论 1
1.1 研究背景和意义1
1.2 液压传动介绍1
1.3 国内外数控机床的发展现状2
1.3.1 国外数控机床发展现状2
1.3.2 国内数控机床发展现状3
1.4 本文研究对象4
2 液压尾座液压传动总体设计5
2.1 尾座简介5
2.2 回路设计5
2.2.1 液压尾座顶针液压回路6
2.2.2 液压尾座顶针夹紧液压回路7
3 尾座部分的设计9
3.1 液压系统压力9
3.2 顶针油缸的计算9
3.2.1 顶针轴向力9
3.2.2 液压油缸计算10
3.3 液压泵的设计12
3.3.1 液压泵工作压力的确定13
3.3.2 液压泵流量的确定13
3.3.3 电动机功率的确定15
3.4 液压元件的选择16
3.4.1 油管及管接头16
3.4.2 过滤器的选择16
3.4.3 油箱的选择17
3.4.4 油箱容积的确定17
3.5 液压系统的性能验算 18
3.5.1 液压系统压力损失计算18
3.5.2 液压系统发热温升的验算19
4 液压尾座结构设计21
4.1 液压尾座箱体设计21
4.2 尾座顶尖的设计21
4.3 尾座主轴的设计21
4.4 尾座导轨的设计22
4.4 尾座孔系设计23
4.4.1 套筒与尾座体的配合24
4.4.2 套筒与顶尖、尾座活塞轴的配合24
4.4.3 孔和键的设计24
5 尾座精度的设计26
5.1 表面粗糙度的确定26
5.2 尾座与机床形位公差的确定26
5.3 底面及立导向面形位公差的确定26
结 论28
参考文献29
致 谢30
2 液压尾座液压传动总体设计
尾座是车床的重要部件,其作用是固定轴类零件,当加工轴类零件时,除用卡盘外,还需要尾座将其加紧,同时具有辅助支撑和夹紧的功能。本文设计的尾座采用的是整体式结构,整体式结构尾座由尾座体、套筒、芯轴结构、套筒液压测力装置、尾座和套筒移动机构、尾座和套筒夹紧与放松结构及液压装置等组成,其夹紧与松开,靠液压控制,液压控制具有,冲击小,对零件的损害小,抗震性好,能吸收一定震动,能实现高精度的加工。液压系统设计对整个尾座来说,非常重要,因此液压系统的设计十分关键。
2.1 尾座简介
(1)机床采用标准液压尾座,尾座套筒可编程控制,尾座体移动通过销轴由托板带动。根据用户需求也可提供可程控尾座、内置旋转活络顶尖等(特殊配置)。尾座单元安装在床身导轨上,可沿导轨纵向调整其位置。它的功用是用顶尖支承长工件,也可以安装钻头、铰刀等孔加工刀具进行孔加工。
(2)尾座应具有足够的净刚度和较高的刚度-重量比,后者在很大程度上反应了设计的合理性;应具有良好的动态性,这包括较大的动刚度和阻尼,与其它件配合,使整机的各个固有频率不致与激振频率重合而发生共振;应具有良好热变形性,使整机的热变形较小或热变形对加工精度的影响最小;应具有良好的工艺性,以便于制造和装配。3 尾座液压系统设计
前面章节已经设计好液压尾座的控制回路,本章将从计算方面来设计液压缸的,以及液压泵的设计。液压缸的设计主要分为顶针油缸,顶针夹紧油缸。
3.1 液压系统压力
液压缸工作压力主要根据运动循环各阶段中的最大总负载力来确定,此外,还需要考虑以下因素: (1)各类设备的不同特点和使用场合,如表3.1所示。 (2)考虑经济和重量因素,压力选得低,则元件尺寸大,重量重;压力选得高一些,则元件尺寸小,重量轻,但对元件的制造精度,密封性能要求高,如表3.2所示。 所以,液压缸的工作压力的选择有两种方式:一是根据机械类型选;二是根据切削负载选。4 液压尾座结构设计
尾座是卧式车床的重要附件,其主要作用:轴类零件定心,同时具有辅助支撑和夹紧的功能。本文设计的尾座采用的是整体式结构。整体式尾座的组成为:尾座体、套筒、芯轴结构、尾座和套筒移动机构、尾座和套筒夹紧与放松结构及液压装置等组成。整体式尾座,将分体式尾座上、下体合为一个尾座整体,经有限元分析、计算,通过对尾座内部筋板的合理布置,提高了尾座的刚度和固有频率,尾座采用高强度低应力铸铁铸造,经良好的时效处理,热变形小,刚度高、抗震性能好,精度高,精度保持性好动、静刚度好,精度高。在承受最大工件重量和最大额定切削力的情况下芯轴结构选用高精度的进口轴承支承。结构更加简单、优化、合理,整体式尾座将分体式尾座上、下体合为一个尾座整体,取消了分体式尾座联结的定位键和把合螺钉,总零件数和标准件数更少,取消了分体式尾座上、下体的配合加工面,取消了分体式尾座上、下体的装配环节,加工、装配工艺性更好,节约了加工、装配总费用,降低了尾座的总重量和总成本。下面将从尾座座体,尾座主轴,尾座顶针,尾座导轨设计。
4.1液压尾座箱体设计
尾座体的材料采用HT200,铸造加工而成。在尾座体的设计过程中考虑到加工工艺,需要设计出工艺凸台和工艺孔。在铸造设计过程中应注意:尾座体的壁厚要尽量均匀,拐角处要设计成圆角以减少集中应力。将尾座箱体固定在导轨上,这样才能使尾座工作。从尾座上为导轨加润滑油,油杯选择为直径为10,此油杯为压配式压注油杯,此油杯使用比较方面,当润滑主轴时只需将油口对准油杯口即可往里注油,不用拆装尾座即可起到润滑的作用。此尾座壳体的前面有防尘罩,此防尘罩的作用是防止主轴伸出时有杂质粘在上面,也防止杂质渗入影响主轴伸出的速度及稳定性。此键的作用是固定主轴,使其不能左右旋转只能伸缩,在其旁边有一定位螺钉,此作用是将键牢牢固定于壳体,防止键定位不准。 本课题研究的主要目的是设计出卧式数控机床相匹配的液压尾座,使其满足诸如旋转精度等众多要求,以使其达到预想的目的。
为了完成本课题的设计,在设计之前的准备工作必须做好,首先是搜集和分析资料,主要包括国内外数控机床的发展现状;液压技术和液压传动系统的基本资料;同等机床液压尾座的图纸和资料等。其次是初步确定液压尾座的总体布局,包括配置形式、液压系统的布置及选择液压能源及相应的配套元件等。最后主要是关于尾座的设计计算。
数控机床变档卡紧及尾座顶紧的控制方式基本上是手工控制,在通常的加工过程中,需先用手工控制的方式完成变档和卡紧工作,然后再进行装夹,在装夹完毕后还需要使用手工控制的方式完成尾座的顶紧工作。由此可知,在数控机床的加工作效率效率并不高,而且工人劳动强度大,耗时又耗力,还会增加企业成本。因此,本课题研究所要达到的预期效果是在数控车床加工过程中,当需要使用尾座时,使用本课题所设计的尾座可以提高加工过程的机械化和自动化水平,提高生产效率,降低工人的劳动强度,降低企业成本。本次设计是根据实际生产中存在的问题,提出能改善这种状况的可行性方案。
通过这次设计,可以达到以下目的:培养综合运用专业基础知识和专业技能来解决工程实际问题的能力;强化工程实践能力和意识,提高本人综合素质和创新能力;使本人受到从事本专业工程技术和科学研究工作的基本训练,提高工程绘图、计算、数据处理、外文资料文献阅读、使用计算机、使用文献资和手册、文字表达等各方面的能力;培养正确的设计思想和工程经济观点,理论联系实际的工作作风,严肃认真的科学态度以及积极向上的团队合作精神。
参考文献
[1] 濮良贵,纪名刚.机械设计第八版[M].北京:高等教育出版社,2006.12.
[2] 赵大兴.工程制图[M]. 北京:高等教育出版社,2004.7.
[3] 联合编写组.机械设计手册(中册)[M].北京:化学工业出版社,1987.2.
[4] 顾熙棠 金瑞琪,刘瑾.金属切削机床[M].上海:上海科学技术出版社,1993.2.
[5] 机械设计手册编委会. 机械设计手册新版[M]. 北京:机械工业出版社, 2004.8.
[6] 余仲裕. 数控机床维修[M]. 北京:机械工业出版社.2001.2.
[7] 许福玲 陈尧明.液压与气压传动第二版[M].北京:机械工业出版社,2006.1.
[8] 唐保宁.机械设计与制造简明手册[M]. 同济大学出版社,1998.2.
[9] 戴曙. 金属切削机床[M]. 北京:机械工业出版社,1993.5.
[10] 陈婵娟. 数控车床设计[M]. 北京:化学工业出版社,2006.3.
[11] 王爱玲. 现代数控机床[M]. 北京:国防工业出版社,2003.3.
[12] 郭荣第.金属切削原理与刀具[M]. 哈尔滨:哈尔滨工业大学出版社,2007.7.
[13] 许福玲 陈尧明.液压与气压传动[M] .机械工业出版社,2012-01-01.
[14] 卢秉恒.机械制造技术基础[J]. 机械工业出版社 ,2008-06-03.
[15] 田勇 高长银.液压与气压传动技术及应用[M]. 电子工业出版社,2011.7.
[16] The LEE Company Technical Center.LEE Technical Hydraulic Handbook. Westbrook.
Connecticut.1989.
[17] A.L.Hitchcox.Water Hydraulics Continues Steady Growth.Hydraulics &Pneumatics. DEC
1999.3.1.
[18] T.Vidar.From Finite Differences to Finite Elements. A Short History of Numerical Analysis of
Partial Differential Equations.Journal of Computational and Applied Mathematics.2001.
128.1~54.
[19] K.K.Gupta,J.L.Meek.A Brief History of the Beginning of the Finite Element Mathematics.
2001,128.1~54.