LH157QMJ-C左箱体工序卡及第一道机加工夹具设计【说明书+CAD】
收藏
资源目录
压缩包内文档预览:(预览前15页/共51页)
编号:10048996
类型:共享资源
大小:2.87MB
格式:RAR
上传时间:2018-04-23
上传人:柒哥
认证信息
个人认证
杨**(实名认证)
湖南
IP属地:湖南
20
积分
- 关 键 词:
-
lh157qmj
箱体
工序
及第
中举
一道
加工
夹具
设计
说明书
仿单
cad
- 资源描述:
-
【温馨提示】 购买原稿文件请充值后自助下载。
以下预览截图到的都有源文件,图纸是CAD,文档是WORD,下载后即可获得,所见即所得。
预览截图请勿抄袭,原稿文件完整清晰,无水印,可编辑。
有疑问可以咨询QQ:12401814









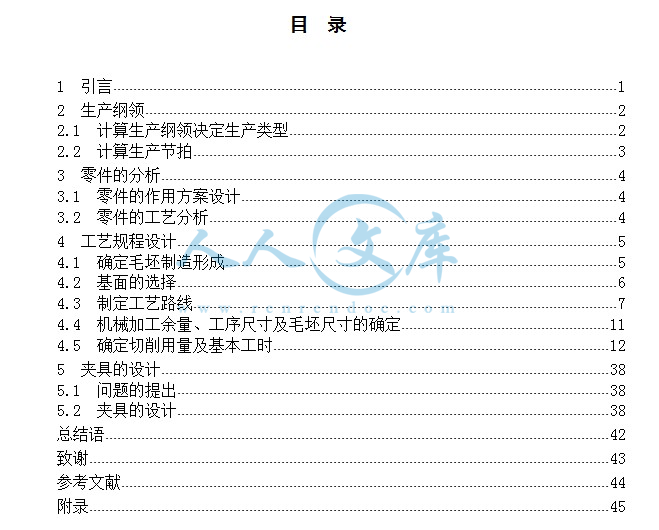


- 内容简介:
-
1引言机械加工工艺和夹具结构设计在加深我们对课程基本理论的理解和加强对解决工程实际问题能力的培养方面发挥着极其重要的作用。选择曲轴箱体的加工工艺和夹具设计能很好的综合考查我们大学四年来所学的机械理论知识。机械加工工艺是实现产品设计,保证产品质量、节约能源、降低成本的重要手段,是企业进行生产准备,计划调度、加工操作、生产安全、技术检测和健全劳动组织的重要依据,也是企业上品种、上质量、上水平,加速产品更新,提高经济效益的技术保证。然而夹具又是制造系统的重要组成部分,不论是传统制造,还是现代制造系统,夹具都是十分重要的。因此,好的夹具设计可以提高产品劳动生产率,保证和提高加工精度,降低生产成本等,还可以扩大机床的使用范围,从而使产品在保证精度的前提下提高效率、降低成本。当今激烈的市场竞争和企业信息化的要求,企业对夹具的设计及制造提出了更高的要求。我们这些即将大学毕业的机械工程及自动化专业的学生,要进行对本专业所学习的知识进行综合的运用和掌握,为此我们要进行毕业设计,要自己动手进行思考问题,为社会主义现代化建设的发展贡献力量,也要从此迈出展现自己价值的第一步。本次设计是根据林海集团生产的要求,设计LH157左箱体工序卡及第一道工序的夹具。所用机床主要是加工中心。本次设计要求是单班制年产2万台;夹具设计须定位准确,夹紧可靠。以及节约劳动力,节约生产成本,提高生产的效率。但由于本人的水平有限,结合生产实际应用设备的能力有限,故没有能够做到很详细的设计,而且还有许多地方有待改进,请老师给以指导和批评1。2生产纲领21计算生产纲领决定生产类型生产纲领是企业在计划期内应当生产的产品产量和进度计划。(计划期常为一年,所以生产纲领也称年产量。)如附图所示的LH157左箱体,江苏林海动力机械集团则该产品年产量为2万台,设备品率A为17机械加工废品率为05,现制定该零件的机械加工工艺流程。技术要求;1铸件尺寸公差按GB64141999CT要求;2未注铸造圆角R23,未注倒角145,未注壁厚3;3铸件技术条件JB270280IIY2要求;4在3040104PA压力下作水压试验1MIN,不得漏水和浸润;5表面喷丸处理;6硬度HB90,试样抗拉强度MPA;270B7压铸件材料为ADC12;8带标记的螺孔及底孔根据配套要求加工。生产纲领N1BAQN200001170523500件/年年产量为23500件/年,现通过计算,生产纲领对工厂的生产过程和生产组织有着决定性的作用,包括各工作点的专业化程度,加工方法,加工工艺设备和工装等。同一种产品,生产纲领不同也会有完全不同的生产过程和专业化程度,即有着完全不同的生产组织类型。根据生产专业化程度的不同,生产组织类型可分为单件生产,成批生产,和大量生产三种,其中成批生产可分为大批生产,中批生产和小批生产,下表1是各种生产组织管理类型的划分,从工艺特点上看单件生产与小批生产相近,大批生产和大量生产相近,因此在生产中一般按单件小批,中批,大批大量生产来划分生产类型,这三种类型有着各自的工艺特点。表1生产组织管理类型的划分零件年生产类型(件/年)生产类型重型机械中型机械轻型机械单件生产520100小批生产510020200100500中批生产1003002005005005000大批生产30010005005000500030000大量生产1000500050000所以综上所述,根据生产类型和生产纲领的关系,可以确定该产品的生产类型为大批量生产2。22计算生产节拍生产节拍22天12个月8小时60单双班90/生产纲领22126090/2000057分钟3零件的分析31零件的作用箱体是各类机器的基础零件,它将机器和部件中的轴、套、齿轮等有关零件连接成一个整体,并使之保持正确的位置,以传递转矩或改变转速来完成规定的运动。因此,箱体的加工质量直接影响机器的性能、精度和寿命3。题目所给定的LH157左箱体是整个机器的重要组成部分,其主要作用是与右箱体配合使用达到应有作用4。32零件的工艺分析零件图中规定了一系列技术要求(查表1428机械制造工艺设计简明手册),即LH157左箱体共有三组加工面,它们之间有一定的要求。现分析如下1以56MM、50MM轴承毛坯孔为定位这组加工表面包括箱体盖面;30MM、220MM的吊耳孔;16MM、18MM、12MM的镗孔;12MM的铣铰销孔;M6底孔5MM、M8底孔67MM、M10125底孔87MM、M1215底105MM;孔口倒角其中主要加工箱体盖面,三个吊耳孔。2以210MM销孔定位这组加工表面包括镗轴承孔58MM、50MM、35MM、42MM;镗油封孔30MM、35MM;铣铰销孔28MM、210MM;M6底孔105MM其中,主要加工变速箱结合面;30MM、35MM的油封孔。3以缸体结合面,210MM销孔为定位这组加工表面包括配合面;M6底孔35MM、M8底孔27MM;镗孔615MM;孔口倒角。其中,主要加工配合面。这三组加工表面之间有一定的要求,主要是1结合面必须位于距离为公差值005MM的两平行平面内;2销孔必须位于直径为公差值0015MM的孔内,该孔位于相对于基准A、B所确定的理想位置上;3保证与右箱体结合面厚度尺寸125005MM、保证与变速箱体结合面厚度尺寸48005MM。由以上分析可知,对于这三组加工表面而言,可以先加工箱体结合面,然后再加工出两销,以确定精基准,最终以结合面和两销孔(即一面两销)为精基准加工出其余需要加工的部分。然后再借助于专用夹具对另外两组进行加工,并保证它们之间的精度要求1。4工艺规程设计对于机器中的某一零件,可以采用多种不同的工艺过程完成。在特定条件下,总存在一种相对而言最为合理的工艺规程,将这工艺规程用工艺文件形式加以规定,由此得到的工艺文件统称工艺规程2。工艺规程是生产准备、生产组织、计划调度的主要依据,是指导工人操作的主要技术文件,也是工厂和车间进行设计或技术改造的重要原始资料。工艺规程的制订须严格按照规定的程序和格式进行,并随技术进步和企业发展,定期修改完善3。1根据机械加工工艺规程进行生产准备(包括技术准备)。在产品投入生产以前,需要做大量的生产准备和技术准备工作,例如,技术关键的分析与研究;刀、夹、量具的设计、制造或采购;设备改装与新设备的购置或定做等。这些工作都必须根据机械加工工艺规程来展开。2机械加工工艺规程是生产计划、调度、工人的操作、质量检查等的依据。3新建或扩建车间(或工段),其原始依据也是机械加工工艺规程。根据机械加工工艺规程确定机床的种类和数量,确定机床的布置和动力配置,确定生产面积的大小和工人的数量等4。41确定毛坯的制造形式铸造性能所涉及的主要是铸件的质量问题,铸件结构设计时,必须充分考虑适应合金的铸造性能。缩孔,缩松,裂纹,冷隔,浇不足、气孔等多种铸造缺陷,造成铸件很高的废品率4。零件材料为ADC12铝合金。考虑到零件材料的综合性能及材料成本和加工成本,保证零件工作的可靠,采用铸造。由于左箱体年产量为2万台,已达到大批生产的水平,而且零件轮廓尺寸不大,再者,考虑到铸造方法生产工艺简单、生产周期短、适合批量生产,故可以采用铸造成型,这从提高生产率、保证加工精度上考虑,也是应该的。为了消除压铸后的残余应力,在压铸完成后的将铸件低温加热过程中使合金产生强化,以消除应力即人工时效1。42基面的选择制订机械加工规程时,定位基准的选择是否合理,将直接影响零件加工表面的尺寸精度和相互位置精度。同时对加工顺序的安排也有重要的影响。定位基准选择不同,工艺过程也将随之而异,基准面选择是工艺规程设计中的重要工作之一。421基准的概念及其分类基准是指确定零件上某些点,线,面位置时所依据的那些点、线、面,或者说是用来确定生产对象上几何要素间的几何关系所依据的那些点、线、面4。按其作用的不同,基准可分为设计基准和工艺基准两大类。设计基准是指零件设计图上用来确定其他点,线,面位置关系所采用的基准。工艺基准是指在加工或装配过程中所使用的基准。工艺基准根据其使用场合的不同,又可分为工序基准,定位基准,测量基准和装配基准四种。1工序基准在工序图上,用来确定本工序所加工表面加工后的尺寸,形状,位置的基准,及工序图上的基准。2定位基准在加工时用作定位点基准。它是工件上与夹具定位元件直接接触的点,线,面。3测量基准在测量零件已加工表面的尺寸和位置时所采用的基准4装配基准装配时用来确定零件或部件在产品中的相对位置所采用的基准。422基准问题的分析分析基准时,必须注意以下几点1基准是制订工艺的依据,必须是客观存在的。当作为基准的是轮廓要素,如平面,圆柱面等时,容易直接接触到,也比较直观。但是有些作为基准的是中心要素,如圆心,球心,对称轴线等时,则无法触及,然而它们却也是客观存在的。2当作为基准的要素无法触及时,通常由某些具体的表面来体现,这些表面称为基面。如轴的定位则可以外圆柱面为定位基面,这类定位基准的选择则转化为恰当地选择定位基面的问题。3作为基准,可以是没有面积的点,线以及面积极小的面。但是工件上代表这种基准的基面总是有一定接触面。4不仅表示尺寸关系的基准问题如上所述,表示位置精度的基准关系也是如此1。423定位基准的选择选择定位基准时应符合两点要求1各加工表面应有足够的加工余量,非加工表面的尺寸,位置符合设计要求;2定位基准应有足够大的接触面积和分布面积,以保证能承受打打切削力,保证定位稳定可靠。定位基准可分为粗基准和精基准。若选择未经加工的表面作为定位基准,这种基准被称为粗基准。若选择已加工的表面作为定位基准,则这种定位基准称为精基准。粗基准考虑的重点是如何保证各加工表面有足够的余量,而精基准考虑的重点是如何减少误差。在选择定位基准时,通常是保证加工精度要求出发的,因而分析定位基准选择的顺序应从精基准到粗基准1。1精基准的选择。选择精基准的目的是使装夹方便正确可靠,以保证加工精度。主要应该考虑基准重合和统一基准的问题。当设计基准与工序基准不重合时,应该进行尺寸换算,这在以后还要专门计算,此处不再重复。按照有关的精基准选择原则(基准重合原则;基准统一原则;可靠方便原则),为了加工精基准面才选择了粗基准面。对于本箱体,我是以56MM、50MM轴承毛坯孔和三搭子定位为粗基准来加工盖面的。先保证精基准的精度,然后在加工出销孔。最终以结合面和两销孔作为精基准。在以后的加工过程中精度就会得到保证并提高。2粗基准的选择。对于刚性差、批量较大、要求精度较高的箱体,一般要粗、精加工分开进行,即在主要平面和各支承孔的粗加工之后再进行主要平面和各支承孔的精加工。这样,可以消除由粗加工所造成的内应力、切削力、切削热、夹紧力对加工精度的影响,并且有利于合理地选用设备等。而箱体零件一般都选择重要孔(如主轴孔)为粗基准,但随着生产类型不同,实现以主轴孔为粗基准的共建装夹方式是不同的。大批生产时,毛坯精度较高,可直接以主轴孔在夹具上定位,采用专用夹具装夹,但对本箱体来说,如果以轴承孔作为基准,则无法合理地加工出所要加工的箱体结合面,按照有关粗基准的选择原则(即当零件有不加工表面时,应以不加工表面作为粗基准;若零件有若干个不加工表面时,则应以与加工表面要求相对位置精度较高的不加工表面作为粗基准),现取以56MM、50MM轴承毛坯孔及三搭子定位并夹紧作为粗基准,从而达到要完成的零件加工4。43制订工艺路线拟订零件的机械加工工艺路线是制订工艺规程的一项重要工作,拟订工艺路线时主要解决的问题有选定各加工表面的加工方法;划分加工阶段;合理安排各工序的先后顺序;确定工序的集中和分散程度。拟订工艺路线的出发点,应当是使零件的几何形状,尺寸精度及位置精度等技术要求能得到合理的保证。在确定生产纲领为大批生产和在加工中心加工的条件下,并尽量使工序集中来提高生产率,除此以外,还应当考虑经济效果,以便使生产成本尽量下降。工艺设计时,主要考虑精度和效率两个方面,一般遵循先面后孔、先基准后其它、先粗后精的原则。加工中心在一次装夹中,尽可能完成所有能够加工表面的加工。对位置精度要求较高的孔系加工,要特别注意安排孔的加工程序,安排不当,就有可能将传动副的反向间隙带入,直接影响位置精度。除此以外,还应当考虑经济效果,以便使生产成本尽量下降。工艺路线一工序I铸造,去除浇口、毛刺、飞边。工序II喷砂。工序III铸检。工序IV加工结合面,镗轴承孔MM,镗油封孔,铣铰0195803M销孔28MM钻105MM。工序V加工变速箱结合面。工序VI镗轴承孔MM、MM;镗油封孔;铣铰销021O5017O420253孔210MM;钻透孔79MM。工序VII以50MM、56MM轴承毛坯孔定位。工序VIII镗吊耳孔、2;镗孔、0213M0210216M、;铣铰销孔210MM;钻孔02718M70145MM、M8、M10125、M12125。工序IX以210MM的销孔定位。工序X钻35MM、27MM;镗615MM。工序XI去刺、清洗、检入库。工艺路线二工序I铸造,去除浇口、毛刺、飞边。工序II喷砂。工序III铸检。工序IV以50MM、56MM轴承毛孔坯定位。工序V镗吊耳孔、2;镗孔、0213M0210216M、;铣铰销孔0271870210MM;钻孔145MM、M8、M10125、M12125。工序VI加工与右箱体结合面。工序VII镗轴承孔MM,镗油封孔,铣铰销孔280195803MMM,钻105MM。工序VIII加工变速箱结合面。工序IX镗轴承孔MM、MM;镗油封孔;铣铰销021O5017O420253M孔210MM;钻透孔79MM。工序X加工与右箱体配合面、210MM的销孔定位的表面;钻35MM、27MM;镗615MM。工序XI去刺、清洗、检入库。工艺方案的比较与分析上述两个工艺方案不同之处在于方案一(工序I)加工箱体结合面后还是以先加工结合面的定位基准作为基准来进行镗轴承孔MM,镗油封孔01958,铣铰销孔28MM,钻105MM孔加工;(工序IX)加工与右箱03M体结合面,210MM的销孔定位的表面所用时间非常短;(工序X)钻孔和镗孔要求精度低而其用时少;而方案二(工序VI)在加工箱体结合面后没有再以原先的定位基准进行加工,而是重新定位加工轴承孔、铣铰销孔,攻丝M6,3、4号孔深25MM,其余八孔深18MM。两方案相比较可以看出;把方案一中的工序I(加工与右箱体结合面,镗轴承孔MM,镗油封孔,0195803M铣铰销孔28MM钻105MM。)分为两道工序较合理,把加工箱体结合面、,镗轴承孔MM,镗油封孔,铣铰销孔28MM钻105MM放0195803M在同一定位基准内加工不能满足基准选择的相关原则、也不能保证相应的精度要求。所以将方案工序IV分别改为两道工序进行加工。具体工艺过程如下以上加工方案大致看来似乎已经改正了以同一基准加工两道工序。但通过仔细考虑零件的技术要求以及可能采取的加工手段之后,就会发现还存在问题,基本上没有改变任何不足之处,主要还表现在方案一工序(IV)和工序(VI)加工结合面可以放在同一道工序当中加工,这样就会可以减少换刀次数,可以节省时间,保证了箱体结合面与变速箱结合面的尺寸。上述两个方案的特点在于方案一适合小批量的生产,方案二是采用铣削方式加工端面,每道工序比较清楚,且符合大批量的加工生产,最主要解决了基准问题,保证了基准重合。因而选用方案二的方式来加工。这样修改后就可以修正由于基准不重合造成的加工误差。因此,最后的加工路线确定如下工序I铸造,去除浇口、毛刺、飞边。工序II喷砂。工序III铸检。工序IV以56MM、50MM轴承毛坯孔定位的,三搭子定位并夹紧选用加工中心VFO。工序V(1)加工盖面(2)镗吊耳孔、20213M021(3)镗孔、加工销孔、轴承孔、060278M027攻丝M6深13MM。(4)铣铰销孔210MM(5)钻孔145MM、M8、M10125、M12125(6)攻丝15M6、M8、M10125、M12125工序VI以210MM销孔和箱体结合面、压紧三塔子定位、选用加工中心VFO工序VII(1)加工与右箱体配合面和变速箱结合面(2)镗轴承孔MM、镗轴承孔、0958021O5017O42(3)镗油封孔、镗油封孔30M03M(4)铣铰销孔28MM、铣铰销孔210MM(5)钻105MM、透孔79,(6)攻丝M6工序VIII以210的销孔定位,钻35MM、27MM;镗615MM。工序IX去刺、清洗、检入库。44机械加工余量、工序尺寸及毛坯尺寸的确定LH157左箱体的材料为ADC12铝合金,硬度HB90,试样抗拉强度270MPA;毛坯重量为12千克。生产类型为大批生产,采用高压浇注毛坯7。B根据上述原始资料及加工工艺,分别确定各加工表面的机械加工余量、工序尺寸及毛坯尺寸如下1箱体结合面参照机械制造工艺设计简明手册表239,箱体的最大基本尺寸330MM1040MM,铸造毛坯时一般采取7级尺寸公差等级和D级加工余量等级进行高压浇注7,所以毛坯的加工余量MM15MM。而箱体结合表面的表面粗糙度要90Z求为RA的最大允许值为16UM,参照机械制造工艺学表112,要求达到精铣加工,箱体结合面的最大加工长度1040MM,加工宽度300MM,所以加工余量MM。因此,只要进行一次精加工就已能满足加工要求6。51Z2MM的轴承孔08O3轴承孔不是盲孔,再加上其精度要求较高,故采用镗削加工。轴承孔尺寸为MM,见图样。轴承孔表面粗糙度要求为的最大允许值为08O35AR16UM,参照机械制造工艺学表111,要求达到精镗加工,且加工精度为IT6IT7级,参照机械制造工艺设计简明手册表238确定轴承孔的加工余量分配粗镗346MM2Z15MM精镗MM2Z04MM08O35A销孔底孔2MM,考虑到其表面粗糙度要求为RA的最大允许值为01563UM,精度要求不是佷高,参照,机械制造工艺学表112,加工精度为IT11IT12级,只要粗加工,一次钻销(此时加工余量MM)就已能满足加工要求。512ZB销孔210MM,其表面粗糙度要求为RA的最大允许值为16UM,参照机械制造工艺学表111,加工精度为IT8IT9级,要求精加工才能达到精度要求,参照机械制造工艺设计简明手册表239确定销孔的加工余量分配钻孔98MM2Z15MM铰孔8MM2Z02MM3的油封孔03M油封孔端面其表面粗糙度要求为RA的最大允许值为63UM,油封孔的表面粗糙度要求为RA的最大允许值为16UM,主要考虑油封孔的精度要求,采用复合刀加工,参照机械制造工艺学表112,加工精度为IT11级,要求达到半精镗加工,参照机械制造工艺设计简明手册表239确定油封孔的加工余量分配镗削296MM2Z15MM精镗2Z04MM03M46MM考虑其表面粗糙度要求为RA的最大允许值为16UM,参照机械制造工艺学表111,加工精度为IT8IT9级,参照机械制造工艺设计简明手册表239确定加工余量分配钻孔58MMMM312Z攻丝6MMMM045确定切削用量及基本工时在一定生产条件下,规定生产一件产品或完成一道工序所消耗的时间称为时间定额。合理的时间定额能促进工人的生产技能和技术熟练程度的不断提高,调动工人的积极性,从而不断促进生产向前发展和不断提高劳动生产率。时间定额是安排生产计划、成本核算的主要依据,在设计新厂时,又是计算设备数量、布置车间、计算工人数量的依据7。工序I铸造,去除浇口、毛刺、飞边。工序II喷砂。工序III铸检。工序IV以56MM、50MM轴承毛坯孔定位,三搭子定位并夹紧,选用加工中心VFO。本工序采用计算法确定切削用量。1加工条件工件材料ADC12铝合金,试样抗拉强度MPA、高压浇注。270B加工要求铣箱体盖面,表面粗糙度要求为RA的最大允许值为16UM。机床加工中心VFO。刀具盘铣刀。刀具材料高速钢(YT15)。2计算切削用量箱体盖面A已知箱盖面毛坯厚度方向的加工余量为MM,但考虑到箱体结合面毛51Z坯长度方向不是规则形状,因此可以把其考虑为长方形的形状考虑,又由于高压浇注的毛坯精度本身就较高,所以只要加工一次就行,MM计。PAB进给量根据切削用量简明手册表35,当要求达到表面粗糙度FRA16UM时,圆柱铣刀每转进给量04MM/R06MM/R,而用于盘铣刀时进给量应F该减小一半,02MM/R03MM/R。F按加工中心VFO说明书(见切削用量简明手册表330)取03MM/RFC计算切削速度按切削用量简明手册表327,切削速度的计算公式为(寿命MIN)60T(4VPUEYXPMVOVKZAFTQDCVV1)其中31VC,250XQ1V40VY3V,。修正系数见切削用量简明手册表128,0VPK即,。1MVK0SVK1KV0RV1PVK所以M/MIN8645031602613402VD确定机床主轴转速R/MIN(447560810WDVN2)按加工中心VFO说明书(见切削用量简明手册表330),与45647R/MIN相近的转速为355R/MIN及510R/MIN。现取R/MIN。如果取R/MIN,则510N480N速度损失太大。所以实际切削速度M/MIN96VE检验机床功率根据切削用量简明手册表323,当硬度HB160,试样抗拉强度560MPA,MM,MM,MM,MM,52PA71PA60D4Z96V近似为KW。3CP根据切削用量简明手册床说明书表330,机床主轴允许的功率为KW57CMP075KW(其中机床效率为075KW)。65故,因此选用的切削用量可以采用。CPM即03MM/R,MM,R/MIN,M/MIN。F51PA10N96VF切削工时,按机械制造工艺设计简明手册表627,(4NFLT213)式中,MM,MM104LM51L32L所以,FNLLTW2136IN504工序V镗吊耳孔、2;镗孔0213M021、;铣铰销孔210MM;钻孔1450216M027870MM、M8、M10125、M12125,以56MM、50MM轴承毛坯孔定位;选用加工中心VFO。本工序采用查表法和计算法确定切削用量。1加工条件工件材料ADC12铝合金,试样抗拉强度MPA、高压浇注。270B加工要求加工镗吊耳孔、2;镗孔、0213M10216M、;铣铰销孔210MM;攻丝M6其中16号孔深17M02787021MM,5、6、13、15号孔深25MM,1号深28MM,712、14、36号孔通,M8、M10125、M12125其深通,粗糙度要求为RA的最大允许值为16UM;机床VFO加工中心。刀具复合刀,中心钻,直钻,铣铰刀。刀具材料高速钢(YT15)。2计算切削用量镗吊耳孔0213MA已知吊耳孔毛坯厚度方向的加工余量为MM,考虑到吊耳孔的形状规51Z则,可以用复合刀加工,尽管高压浇注的毛坯精度本身较高,但在此工序需要经过粗镗精镗加工才能达到RA的最大允许值为16UM的精度要求。所以,粗镗MM单边余量MM一次镗去全部余量,12Z50ZMM50PA精镗MM单边余量5MM一次镗去全部余量,031MM1PB进给量根据机械加工切削数据手册表324,当要求达到表面粗F糙度时,粗镗每转进给量039MM/R,精镗每转进给量015MM/R16ARUMFFC计算切削速度按机械加工切削数据手册表39,粗加工时的切削速度为46M/MIN,精加工时的切削速度为230M/MIN。VVD确定机床主轴转速根据42式,粗镗加工时的机床主轴转速R/MIN10468930WVNDR/MIN2172W精镗加工时的机床主轴转速R/MIN10301984WVNDR/MIN22760W因在加工中心上加工,所以无需考虑机床主轴转速没有这一挡。E切削工时,根据43式,NFLT21式中MM,MM,MM6L51L02L所以,粗镗切削工时12LLTNF6501MIN4893122LLTF7I7精镗切削工时12LLTNF6507MIN9841122LLTF3I所以镗吊耳孔、2总切削工时为01100701802130211TMIN0070030102镗孔、0216M02781M027机床加工中心VFO刀具复合刀。刀具材料高速钢(YT15)A由于用复合刀加工,考虑到毛坯到成品的加工余量为10MM13MM,又因其底面表面粗糙度要求为的最大允许值为63UM,镗孔的表面粗糙度要求为AR的最大允许值为16UM,则用镗刀精镗一次即可。根据相关手册,镗刀加工时ARMM01PB进给量参照机械加工切削数据手册铝合金铸造的进给量要求F001MM039MM,根据加工相关要求取02MM;FFC切削速度参照机械加工切削数据手册表24,镗刀加工时230M/MIN;VD确定主轴速度103207/MIN16WNRD25/IV3103206/IN18WNRD4495/MIV镗切削工时12LLTNF39504MIN72122LLTF4I6123LLTNF3503IN12124LLTFMI49铣铰销孔210MM深8015A根据林海集团LH157左箱体工序过程卡有关资料介绍,在铰孔时,进给量取MM/R,即02MM/R,30M/MIN2FFVB确定主轴速度R/MIN10309521WND根据有关资料介绍,由于选取的机床是加工中心,根据加工中心的相关要求选取R/MIN。所以实际切削速度M/MIN。30VC切削工时计算FNLLT218506MIN92所以,铣铰销孔210MM深8的总切削工时015201INT钻中心孔18A25A进给量根据机械加工切削数据手册,MM/RF180FB切削速度根据机械加工切削数据手册,M/MIN5VC确定主轴速度根据42式,R/MIN36210510WDVN因为选取的机床是加工中心,根据机床相关要求选取R/MIN。所以实际362N切削速度M/MIN。5VD切削工时,根据43式,NFLT21式中MM,MM,MM5L1L02L所以,MMNFLT2118036所以,钻中心孔18A25的总切削工时021836MINT钻145MM的孔其中16号孔深21MM,5、6、13、15号孔深25MM,1号深28MM,712、14、36号孔通;考虑到其表面粗糙度要求为RA的最大允许值为63UM,参照机械制造工艺学表111,其加工精度为IT11IT12级,精度要求不是佷高,参照机械制造工艺设计简明手册表239,一次钻销即可满足要求。此时加工余量MM。512ZA进给量根据机械加工切削数据手册,MM/R0FB切削速度根据机械加工切削数据手册,M/MIN84VC确定主轴速度1084539/MINWVNRD16号孔切削工时;NFLT2102IN53495、6、13、15号孔切削工时所以孔总切削工时FLT213MI012;034TMIN1号孔切削工时;NFLT218503MIN349712、14、36号通孔切削工时所以7FLT21502IN4912、14、36号通孔总切削工时086INT26号孔切削工时NFLT21502M34917号孔切削工时FLT213IN18号孔切削工时NFLT21501I3492攻丝15M6、M8、M10125、M12125本工序采用查表法和计算法确定切削用量。1加工条件工件材料ADC12铝合金,试样抗拉强度MPA、高压浇注。270B加工要求攻丝M101256H深16MM,其表面粗糙度要求为的最大允许值为AR32UM,机床加工中心VFO刀具机丝刀。刀具材料高速钢(YT15)。2计算切削用量A进给量参照机械加工切削数据手册表4129,125MM/R。FFB切削速度根据机械加工切削数据手册表31,25M/MINVC确定主轴速度1025137/MIN6WVNRD210259/MIN8WVRD39/I041063/I根据有关手册,考虑其在攻深孔、盲孔时,或当螺纹的比例较大时,速度宜降低,而根据S4012机床的相关性能,现取、150/MINNR210/INR、3850/MINNR4750/IRD切削工时16号孔切削工时;NFLT218501IN5、6、13、15号孔切削工时所以孔总切削工时125014MILTNF0145MINT1号孔切削工时NFLT215016IN712、14、36号通孔切削工时;所以孔总切削工时NFLT2135014MI01482MINT26号孔切削工时;122502MIN1LTNF17号孔切削工时1233I8LTF18号孔切削工时1245018IN7LTNF工序VI加工结合面。以210销孔和箱体结合面、压紧三塔子定位、选用加工中心VFO1加工条件工件材料ADC12铝合金,试样抗拉强度MPA、高压浇注。270B加工要求铣箱体盖面,表面粗糙度要求为RA的最大允许值为16UM。刀具盘铣刀。刀具材料高速钢(YT15)。2计算切削用量铣与右箱体结合面和变速箱结合面A已知箱体结合面毛坯厚度方向的加工余量为MM,但考虑到箱体结合51Z面毛坯长度方向不是规则形状,因此可以把其考虑为长方形的形状考虑,又由于高压浇注的毛坯精度本身就较高,所以只要加工一次就行,MM计。PAB进给量根据切削用量简明手册表35,当要求达到表面粗糙度FRA16UM时,圆柱铣刀每转进给量04MM/R06MM/R,而用于盘铣刀时进给量应F该减小一半,02MM/R03MM/R。F按加工中心VFO说明书(见切削用量简明手册表330)取03MM/RFC计算切削速度按切削用量简明手册表327,切削速度的计算公式为(寿命MIN)60T(4VPUEYXPMVOVKZAFTQDCVV1)其中31VC,250XQ1V40VY3V,。修正系数见切削用量简明手册表128,0VPK即,。1MVK0SVK1KV0RV1PVK所以M/MIN02104301382556D确定机床主轴转速R/MIN(42)54780WVND按机床说明书(见切削用量简明手册表330),与4578R/MIN相近的立式铣床转速为355R/MIN及550R/MIN。现取R/MIN。如果取R/MIN,则速5N480N度损失太大。所以实际切削速度M/MIN120VE检验机床功率根据切削用量简明手册表323,当硬度HB160,试样抗拉强度560MPA,MM,MM,MM,M/MIN52PA71PA08D4Z120V近似为KW。3CP根据切削用量简明手册加工中心VFO说明书表330,机床主轴允许的功率为KW075KW(其中机床效率为075KW)。57CM65故,因此选用的切削用量可以采用。PC即05MM/R,MM,R/MIN,M/MINF1PA50N120VF切削工时,按机械制造工艺设计简明手册表627,(43)NFLT21式中MM,MM,MM480L51L32L所以,与右箱体配合面切削工时12WLLTNF3045MIN与变速箱结合面切削工时122WLLTNF7305IN54镗轴承孔MM、MM、MM、MM019821O5017O4208O35A已知镗轴承孔毛坯厚度方向的加工余量为MM,考虑到镗轴承孔的形Z状规则,可以用复合刀加工,尽管高压浇注的毛坯精度本身较高,但在此工序需要经过粗镗精镗加工才能达到RA的最大允许值为16UM的精度要求。所以,粗镗MM单边余量MM一次镗去全部余量,12Z50ZMM50PA精镗MM单边余量MM一次镗去全部余量,MM21010PAB进给量根据机械加工切削数据手册表324,当要求达到表面粗F糙度时,粗镗每转进给量039MM/R,精镗每转进给量02MM/R16ARUMFFC计算切削速度按机械加工切削数据手册表39,粗加工时的切削速度为180M/MIN,精加工时的切削速度为350M/MIN。VVD确定机床主轴转速根据42式,粗镗加工时的机床主轴转速101809/MIN5WVNRD246/I0WR3101835/MIN2WVNRD40679/IWR精镗加工时的机床主轴转速103501928/MINWVNRD2/I31035026/IN4WVNRD418/MIE切削工时,根据43式,NFLT21式中MM,MM,MM3L51L02L所以,粗镗切削工时,切削工时12LLTNF36504MIN981228I4LLTF1233507IN69LLTNF124MI7LLTF精镗切削工时,切削工时211365048IN92LTNF2127MILTF2133506IN62LTNF2144I8LTF所以镗MM轴承孔的总切削工时019510480MINT镗MM轴承孔的总切削工时2O12715镗MM轴承孔的总切削工时0742363IT镗MM轴承孔的总切削工时8O35405209N加工、油封孔以销孔和箱体结合面定位;选用加工中心02M03VFO。1加工条件工件材料ADC12铝合金,试样抗拉强度MPA、高压浇注。270B加工要求加工油封孔,其底面表面粗糙度要求为的最大允许值为63UM,AR油封孔的表面粗糙度要求为的最大允许值为16UMAR机床加工中心VFO刀具复合刀。刀具材料高速钢(YT15)。2计算切削用量加工油封孔,并倒角30,宽2MMA由于用复合刀加工,考虑到毛坯到成品的加工余量为10MM13MM,又因其底面表面粗糙度要求为的最大允许值为63UM,油封孔的表面粗糙度要求为AR的最大允许值为16UM,则先用复合刀一次加工出,然后在用镗刀精镗一次即可。AR根据相关手册,用复合刀加工时MM,用镗刀加工时MM01P01PAB进给量参照机械加工切削数据手册铝合金铸造的进给量要求F02MM039MM,根据加工相关要求取02MMFFC切削速度参照机械加工切削数据手册表24,复合刀加工时取95M/MIN,镗刀加工时350M/MINVVD确定主轴速度根据42式,复合刀加工时1095864/MIN3WVNRD根据机床说明书(见机械制造工艺设计简明手册表428),与543R/MIN相近的机床转速为850R/MIN及1200R/MIN。而此工序在加工中心上加工,并且此工步的要求不高,所以速度可适当大一些,现取。如果取,120/INNR850/MINR则速度损失太大。根据44式,所以实际切削速度341208/MIN10WDNV根据42式,镗刀加工时103502784/MINWVRD同理,根据加工中心VFO说明书(见机械制造工艺设计简明手册表428),与32784R/MIN相近的机床转速为3200R/MIN及3250R/MIN。而此工序在加工中心上加工,并且此工步的要求并不是很不高,所以速度可适当大一些,现取。如果取,则速度损失太大。3250/MINNR320/MINR根据43式,所以实际切削速度34507/IN10WDNVE切削工时,根据43式,NFLT21复合刀加工时式中,MM,MM10LM51L02L263INWTNF镗刀加工时式中,MM,MM10LM51L02L112503MIN32LTTNF所以,加工油封孔的总切削工时02531606IT加工油封孔的总切削工时0M20INT铣铰销孔28MM深01502517MA根据林海集团LH157左箱体工序过程卡有关资料介绍,在铰孔时,进给量取MM/R,即02MM/R,30M/MIN39FFVB确定主轴速度根据42式,R/MIN19483010WDVN根据有关资料介绍,由于选取的机床是加工中心,根据加工中心的相关要求选取R/MIN。所以194N实际切削速度M/MIN。30VC切削工时计算根据43式,FNLLT21750MIN942所以,铣铰销孔28MM深总切削工时015025170521MINT钻中心孔10A25A进给量根据机械加工切削数据手册,MM/RF8FB切削速度根据机械加工切削数据手册,M/MIN15VC确定主轴速度根据42式,R/MIN36210510WDVN因为选取的机床是加工中心,根据机床相关要求选取R/MIN。所以实际362N切削速度M/MIN。5VD切削工时,根据43式,NFLT21式中MM,MM,MM5L1L02L所以,MMNFLT2101836所以,钻中心孔18A25的总切削工时021MINT钻105MM,3、4号孔深25MM其余八孔深18MM考虑到其表面粗糙度要求为RA的最大允许值为63UM,参照机械制造工艺学表111,其加工精度为IT11IT12级,精度要求不是佷高,参照机械制造工艺设计简明手册表239,一次钻销即可满足要求。此时加工余量MM。512ZA进给量根据机械加工切削数据手册,MM/R03FB切削速度根据机械加工切削数据手册,M/MIN7VC确定主轴速度1017560/MINWVNRD3、4号孔切削工时NFLT215017MIN63所以3、4号孔切削总工时074IT其余八孔切削工时NFLT2185013MIN6所以其余八孔切削总工时034IT攻丝105MM3、4号孔深22MM其余八孔深10MMA切削速度的计算参照有关手册可知刀具寿面M/MIN,由于高压浇注60T毛坯精度已较高,又因粗牙螺纹,根据切削用量简明手册表118,高速钢刀具加工铝合金时,25M/MIN45M/MIN。根据相关手册,攻丝时速度可适当放小。V所以,现取M/MIN30B确定主轴速度根据42式,10301592/MIN6WVNRD由于仍在加工中心上加工,且攻丝时速度可适当调大些。所以按相关要求选取。则切削速度1650/MINNR1650328/MINWDVC计算切削工时切削工时,根据43式,NFLT21式中MM,MM,MM;,MM,MML51L02L15LM1L02L所以,21106MIN65LTNF212813ILTF所以3、4号孔切削总工时10623INT其余八孔切削总工时384M透孔79MM;本工序采用查表法和计算法确定切削用量。1加工条件工件材料ADC12铝合金,试样抗拉强度MPA、高压浇注。270B加工要求透9MM其表面粗糙度要求为的最大允许值为63UM,AR机床加工中心VFO。刀具直钻。刀具材料高速钢(YT15)。2计算切削用量A进给量参照机械加工切削数据手册表31039MM/RFFB切削速度根据机械加工切削数据手册表31,50M/MINVC确定主轴速度根据42式105017693/MINWVNRD根据有关手册,考虑其深度大于二倍直径,所以要适当降低速度和进给量,又根据11式,则降低就等于降低速度,根据钻床ZX7025性能的有关说明书,与1769NR/MIN相近的机床转速为1760R/MIN及2150R/MIN。现取1760/MINNR根据44式,所以实际切削速度9176048/IN10WDNVD切削工时,根据43式,NFLT2101、08号透孔深34MM,MM,MM51L2L113505MIN769TNF所以01、08号透孔切削总工时102IT09、01、07号透孔深27MM,MM,MM5LL2127043MIN69LTNF所以09、01、07号透孔切削总工时203129MINT02、06号透孔深36MM,MM,MM51LL2133606MIN79LTNF所以02、06号透孔切削总工时352013INT工序VIII加工与右箱体配合面、28的销孔定位的表面,钻35、27;镗615,以销孔和箱体结合面定位;选用加工中心VFO。1加工条件工件材料ADC12铝合金,试样抗拉强度MPA、高压浇注。270B加工要求铣箱体盖面,表面粗糙度要求为RA的最大允许值为16UM。机床加工中心VFO。刀具盘铣刀。刀具材料高速钢(YT15)。2计算切削用量箱体盖面A已知箱盖面毛坯厚度方向的加工余量为MM,但考虑到箱体结合面毛51Z坯长度方向不是规则形状,因此可以把其考虑为长方形的形状考虑,又由于高压浇注的毛坯精度本身就较高,所以只要加工一次就行,MM计。PAB进给量根据切削用量简明手册表35,当要求达到表面粗糙度FRA16UM时,圆柱铣刀每转进给量04MM/R06MM/R,而用于盘铣刀时进给量应F该减小一半,02MM/R03MM/R。F按加工中心VFO说明书(见切削用量简明手册表330)取03MM/RFC计算切削速度按切削用量简明手册表327,切削速度的计算公式为(寿命MIN)60T(4VPUEYXPMVOVKZAFTQDCVV1)其中31VC,250XQ1V40VY3V,。修正系数见切削用量简明手册表128,0VPK即,。1MVK0SVK1KV0RV1PVK所以M/MIN8645031602613402VD确定机床主轴转速R/MIN(447560810WDVN2)按机床说明书(见切削用量简明手册表330),与45647R/MIN相近的立式铣床转速为355R/MIN及510R/MIN。现取R/MIN。如果取R/MIN,则速510N480N度损失太大。所以实际切削速度M/MIN96VE检验机床功率根据切削用量简明手册表323,当硬度HB160,试样抗拉强度560MPA,MM,MM,MM,MM,52PA71PA60D4Z96V近似为KW。3CP根据切削用量简明手册加工中心VFO说明书表330,机床主轴允许的功率为KW075KW(其中机床效率为075KW)。57CM65故,因此选用的切削用量可以采用。PC即03MM/R,MM,R/MIN,M/MIN。F1PA510N96VF切削工时,按机械制造工艺设计简明手册表627,NFLT21式中,MM,MM30LM51L32L所以,2104MIN503LTNF镗615MM的孔A已知吊耳孔毛坯厚度方向的加工余量为MM,考虑到吊耳孔的形状规51Z则,可以用复合刀加工,尽管高压浇注的毛坯精度本身较高,但在此工序需要经过粗镗精镗加工才能达到RA的最大允许值为16UM的精度要求。所以,粗镗MM单边余量MM一次镗去全部余量,12Z50ZMM50PA精镗MM单边余量MM一次镗去全部余量,01MM1PB进给量根据机械加工切削数据手册表324,当要求达到表面粗F糙度时,粗镗每转进给量039MM/R,精镗每转进给量015MM/R16ARUMFFC计算切削速度按机械加工切削数据手册表39,粗加工时的切削速度为95M/MIN,精加工时的切削速度为250M/MIN。VVD确定机床主轴转速根据42式,粗镗加工时的机床主轴转速10
- 温馨提示:
1: 本站所有资源如无特殊说明,都需要本地电脑安装OFFICE2007和PDF阅读器。图纸软件为CAD,CAXA,PROE,UG,SolidWorks等.压缩文件请下载最新的WinRAR软件解压。
2: 本站的文档不包含任何第三方提供的附件图纸等,如果需要附件,请联系上传者。文件的所有权益归上传用户所有。
3.本站RAR压缩包中若带图纸,网页内容里面会有图纸预览,若没有图纸预览就没有图纸。
4. 未经权益所有人同意不得将文件中的内容挪作商业或盈利用途。
5. 人人文库网仅提供信息存储空间,仅对用户上传内容的表现方式做保护处理,对用户上传分享的文档内容本身不做任何修改或编辑,并不能对任何下载内容负责。
6. 下载文件中如有侵权或不适当内容,请与我们联系,我们立即纠正。
7. 本站不保证下载资源的准确性、安全性和完整性, 同时也不承担用户因使用这些下载资源对自己和他人造成任何形式的伤害或损失。

人人文库网所有资源均是用户自行上传分享,仅供网友学习交流,未经上传用户书面授权,请勿作他用。