灯罩塑料模具设计【24张CAD图纸和说明书】
收藏
资源目录
压缩包内文档预览:(预览前20页/共48页)
编号:10105258
类型:共享资源
大小:6.50MB
格式:RAR
上传时间:2018-05-14
上传人:俊****计
认证信息
个人认证
束**(实名认证)
江苏
IP属地:江苏
40
积分
- 关 键 词:
-
灯罩
塑料
模具设计
24
cad
图纸
以及
说明书
仿单
- 资源描述:
-
摘要
本设计分析了灯罩的结构,提出了模具设计的关键点,设计了模具的整体结构。根据塑件分型面的位置,设计了推件板和斜顶杆的推出结构,零件采用了双分型面的点浇口,提高了零件的外面质量。通过对塑件进行工艺的分析及其结构分析,从产品结构工艺性,具体模具结构出发,对模具的浇注系统、模具成型部分的结构、顶出系统、注射机的选择及有关参数的校核都有详细的设计。该模具一模四腔,采用顶针顶出结构。经过生产验证,该模具结构合理,动作可靠。
关键词:灯罩;塑料模具;注射机
The Plastic Mold Design of Lampe Shade
Abstract
This design on the analysis of the structure of lamp shade,and puts forward the mold design key points,designed the overall structure of the mold. According to the plastic pieces of parting surface,designed the push plate and the inclined plunger, the introduction of the structure,part uses the double parting surface point gate, improve the quality of the parts outside of the. Through to the plastic parts for process analysis and structure analysis,from the product structure craft,specific die structure, the mold of gating system,molding part of the structure,the ejection system, selection of injection machine and related parameters of checking all have detailed design. The mold one module and four cavities,adopts the thimble ejection structure. Through production verification,the die structure is reasonable,reliable operation.
Keyword:Lampe shade;Plastic mold;Injection machine
主要符号表
k 安全系数 E 材料弹性模量
Smax 塑料的最大收缩率 q 熔融塑料在模腔内的压力
Smin 塑料的最小收缩率 V塑 塑件体积
P0 注射压力 V注 注射机理论注射量
P公 公称注射压力 F锁 锁模力
Δs 塑件公差 δs 塑件收缩引起的塑件尺寸误差
T 注射机的额定锁模力 LS 塑件尺寸
L凹 型腔尺寸 L凸 型芯尺寸
H塑 塑件內形深度基本尺寸 S 注射机最大行程
d 塑件外径基本尺寸 H 模具闭合尺寸
D 塑件內形基本尺寸 Hmin 模具最小尺寸
h 凸模/型芯高度尺寸 Hmax 模具最大尺寸
δ 模具制造公差 α 倾斜角
A 塑件包紧型芯的侧面积 p 单位面积塑件对型芯的正力
F 塑件的投影面积 n 个数
P 型腔压力 f 摩擦系数
φ 长度系数 Q 总脱模力
目录
1 绪论 1
1.1塑料模具概况 1
1.2 国内外发展状况 1
1.2.1 国内发展状况 1
1.2.2 国外发展状况 2
1.2.3中国与国外先进技术的差距 2
1.3塑料模具发展走势 2
2 塑件成型工艺的可行性分析 3
2.1功能设计 3
2.2塑件分析 3
2.3材料的选择 3
2.3成型工艺分析 5
3 注塑机的选择 6
3.1估算塑件体积 6
3.2浇注系统凝料体积的初步估算 6
3.3根据注射容量初选注塑机 6
3.6注塑机的校核 7
3.6.1最大注射量校核 7
3.6.2注射压力校核 7
3.6.2锁模力校核 7
3.6.3模具厚度校核 7
3.6.4开模行程校核 8
4 浇注系统设计 9
4.1主流道设计 9
4.2冷料井设计 9
4.3分流道设计 10
4.3.1分流道的布置形式 10
4.3.2分流道长度 10
4.3.3分流道截面形状 10
4.3.4分流道的截面尺寸 10
4.4浇口设计 10
5 成型零件设计 12
5.1分型面的设计 12
5.1.1分型面的分类及选择原则 12
5.1.2分型面的确定 12
5.2型腔分布 12
5.3成型零件结构设计 12
5.3.1成型零件具备的性能 12
5.3.2凹模结构设计 13
5.3.3凸模的结构设计 13
5.3.4影响塑件尺寸和精度的因素 13
5.3.5模具成型零件的工作尺寸计算 14
6 导向机构设计 18
6.1 导向机构的作用和设计原则 18
6.1.1 导向机构的作用 18
6.1.2 导向机构的设计原则 18
6.2导柱、导套设计 18
6.2.1导柱的设计 18
6.2.2导套设计 19
7 脱模机构的设计 20
7.1脱模机构的设计原则 20
7.2 顶出机构的确定 20
7.2脱模力的计算 21
7.3简单脱模机构 21
7.3.1顶杆脱模机构的设计要点 21
7.3.2顶杆的形状 22
7.3.3顶杆强度的计算 22
7.4复位装置 23
8 抽芯机构设计 24
8.1 抽芯机构的概述 24
8.2抽芯机构的设计 24
9 温度调节系统设计 25
9.1温度调节系统的作用 25
9.1.1温度调节系统的要求 25
9.1.2温度调节系统对塑件质量的影响 25
9.2冷却系统的机构 25
10 排气系统设计 26
11 塑料模具用钢 27
11.1注塑模材料应具备的要求 27
11.2模具材料选用的一般原则 27
11.3本模具所选钢材及热处理 27
12 模具装配图及工作过程 28
12.1模具装配二维图 28
12.2模具开模状态 29
12.3模具装配图三维爆炸图 30
12.4模具工作过程 31
13 模具可行性和环保分析 32
13.1本模具的特点 32
13.2市场效益及经济效益分析 32
13.3环保分析 32
14 总结 33
致谢 34
参考文献 35
毕业设计(论文)知识产权声明 36
毕业设计(论文)独创性声明 37
1绪论
1.1塑料模具概况
模具是制造业的一种基本装备,作用是控制和限制材料的流动,形成所需要的形体[7]。模具制造零件效率高,质量好,材料消耗低,生产成本低,广泛应用在制造业中。模具工业是高新技术产业的一部分,也是高新技术产业化的重要领域。模具在机械电子,汽车,纺织,航空航天等领域里,成为使用最广泛的主要装备,它承担了这些领域中 60%~90%的产品。
塑料模具是大批量生产塑料制品的现代化专用成型工艺装备的总称[8]。塑料是继陶瓷和金属后的第三大材料,广泛应用于现代工业和日常生活中。
塑料成型就是将各种形态的塑料原料制成所需的制品或胚件的过程。
塑料注塑成型过程是将塑料原料从注塑机的料斗进入加热筒,经塑化后由柱塞或螺杆的推动,在一定压力下通过喷嘴进入模具型腔,经冷却固化后而开模获得制品。


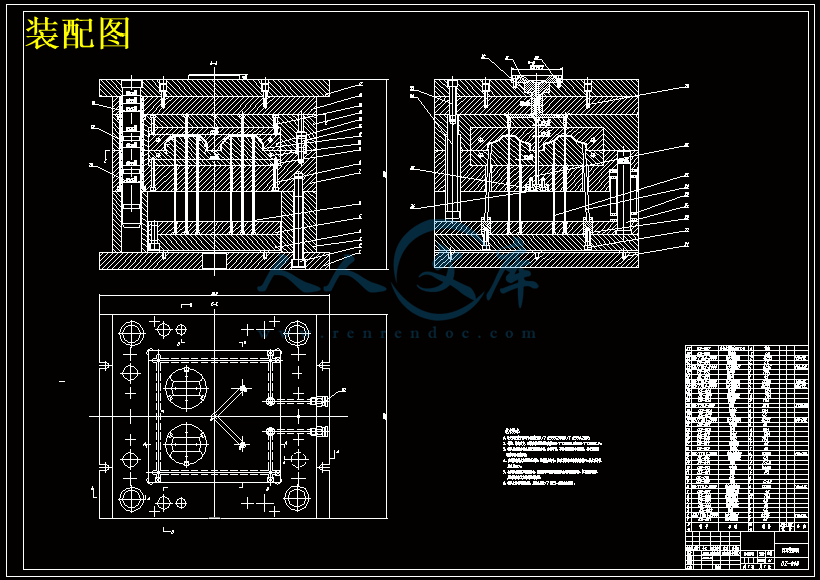
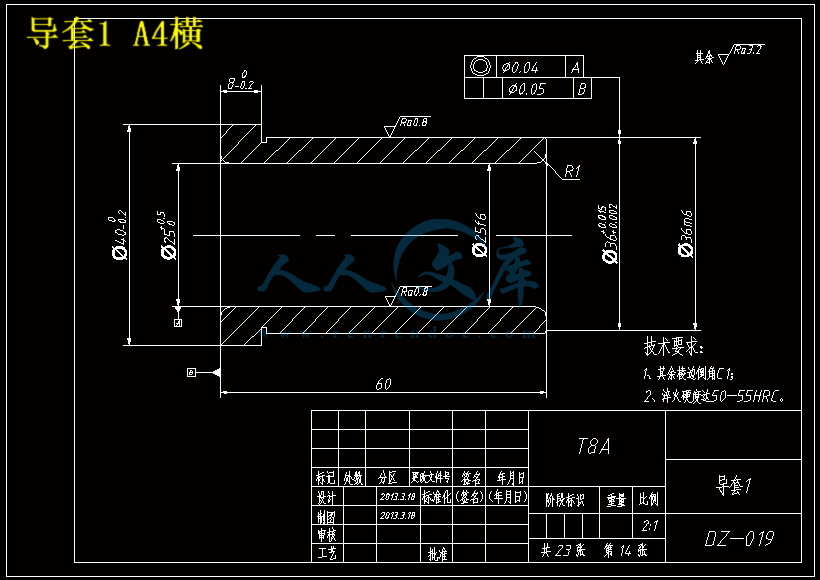



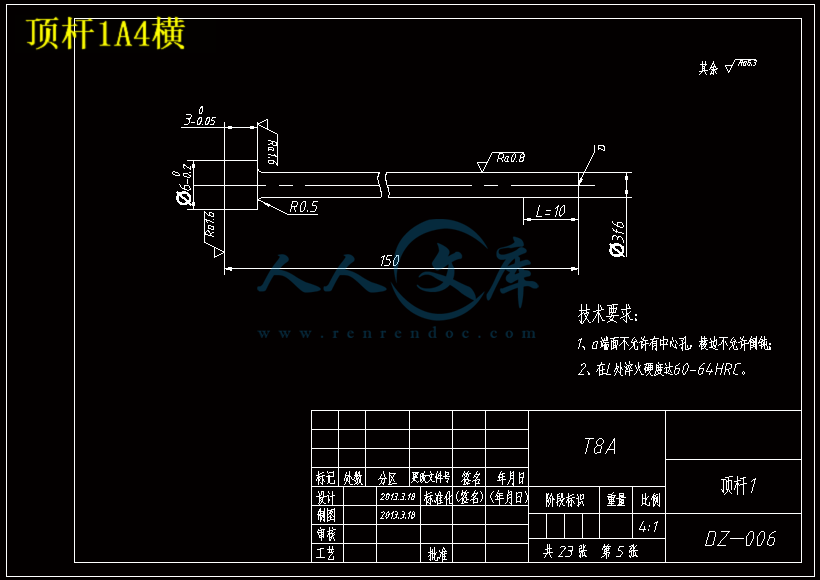













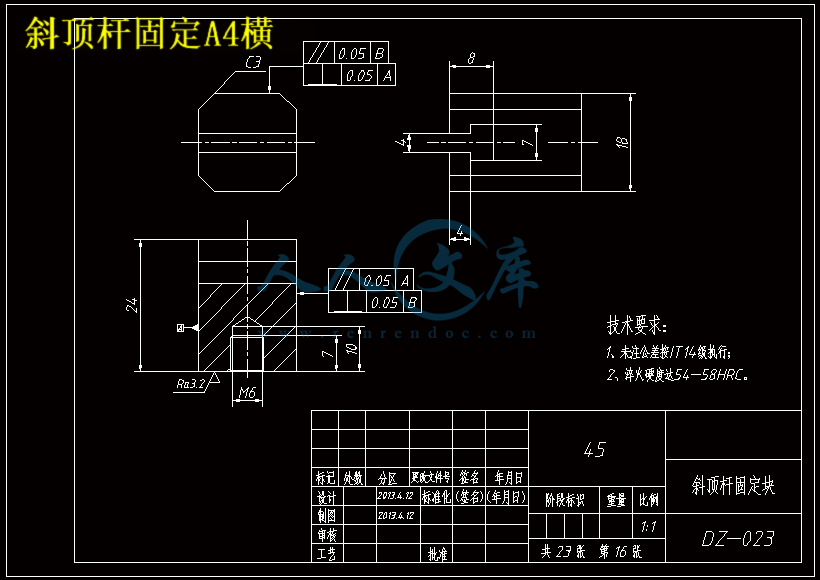
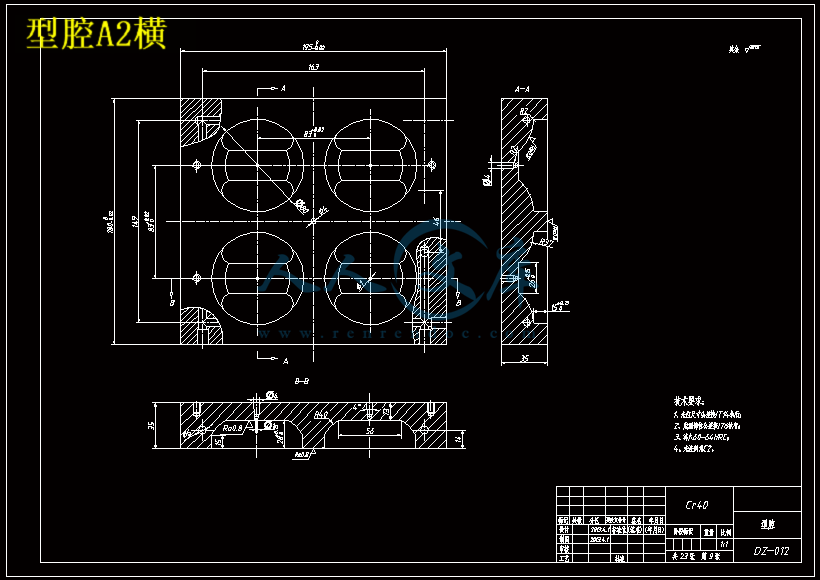
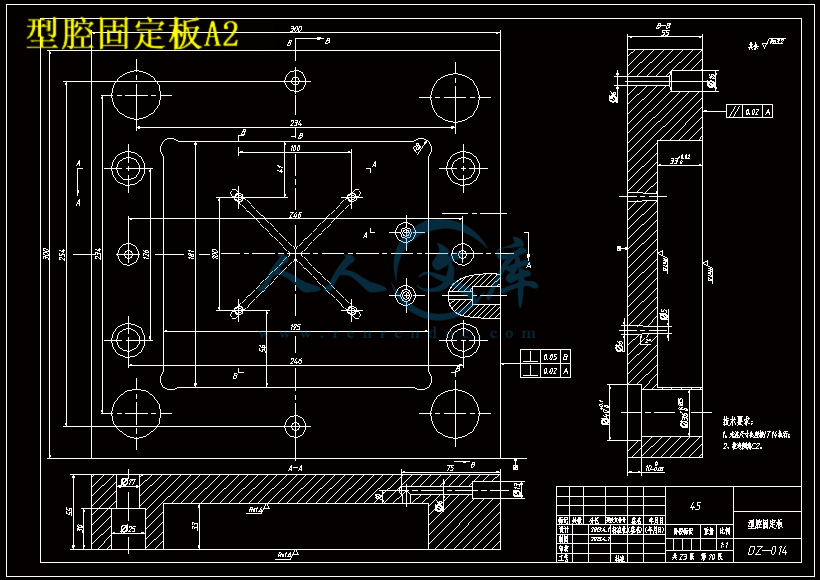



- 内容简介:
-
本科毕业设计(论文)题目灯罩塑料模具设计系别机电信息系专业机械设计制造及自动化班级学生学号指导老师2013年5月I灯罩塑料模具设计摘要本设计分析了灯罩的结构,提出了模具设计的关键点,设计了模具的整体结构。根据塑件分型面的位置,设计了推件板和斜顶杆的推出结构,零件采用了双分型面的点浇口,提高了零件的外面质量。通过对塑件进行工艺的分析及其结构分析,从产品结构工艺性,具体模具结构出发,对模具的浇注系统、模具成型部分的结构、顶出系统、注射机的选择及有关参数的校核都有详细的设计。该模具一模四腔,采用顶针顶出结构。经过生产验证,该模具结构合理,动作可靠。关键词灯罩;塑料模具;注射机IITHEPLASTICMOLDDESIGNOFLAMPESHADEABSTRACTTHISDESIGNONTHEANALYSISOFTHESTRUCTUREOFLAMPSHADE,ANDPUTSFORWARDTHEMOLDDESIGNKEYPOINTS,DESIGNEDTHEOVERALLSTRUCTUREOFTHEMOLDACCORDINGTOTHEPLASTICPIECESOFPARTINGSURFACE,DESIGNEDTHEPUSHPLATEANDTHEINCLINEDPLUNGER,THEINTRODUCTIONOFTHESTRUCTURE,PARTUSESTHEDOUBLEPARTINGSURFACEPOINTGATE,IMPROVETHEQUALITYOFTHEPARTSOUTSIDEOFTHETHROUGHTOTHEPLASTICPARTSFORPROCESSANALYSISANDSTRUCTUREANALYSIS,FROMTHEPRODUCTSTRUCTURECRAFT,SPECIFICDIESTRUCTURE,THEMOLDOFGATINGSYSTEM,MOLDINGPARTOFTHESTRUCTURE,THEEJECTIONSYSTEM,SELECTIONOFINJECTIONMACHINEANDRELATEDPARAMETERSOFCHECKINGALLHAVEDETAILEDDESIGNTHEMOLDONEMODULEANDFOURCAVITIES,ADOPTSTHETHIMBLEEJECTIONSTRUCTURETHROUGHPRODUCTIONVERIFICATION,THEDIESTRUCTUREISREASONABLE,RELIABLEOPERATIONKEYWORDLAMPESHADE;PLASTICMOLD;INJECTIONMACHINEIII主要符号表K安全系数E材料弹性模量SMAX塑料的最大收缩率Q熔融塑料在模腔内的压力SMIN塑料的最小收缩率V塑塑件体积P0注射压力V注注射机理论注射量P公公称注射压力F锁锁模力S塑件公差S塑件收缩引起的塑件尺寸误差T注射机的额定锁模力LS塑件尺寸L凹型腔尺寸L凸型芯尺寸H塑塑件內形深度基本尺寸S注射机最大行程D塑件外径基本尺寸H模具闭合尺寸D塑件內形基本尺寸HMIN模具最小尺寸H凸模/型芯高度尺寸HMAX模具最大尺寸模具制造公差倾斜角A塑件包紧型芯的侧面积P单位面积塑件对型芯的正力F塑件的投影面积N个数P型腔压力F摩擦系数长度系数Q总脱模力IV目录1绪论111塑料模具概况112国内外发展状况1121国内发展状况1122国外发展状况2123中国与国外先进技术的差距213塑料模具发展走势22塑件成型工艺的可行性分析321功能设计322塑件分析323材料的选择323成型工艺分析53注塑机的选择631估算塑件体积632浇注系统凝料体积的初步估算633根据注射容量初选注塑机636注塑机的校核7361最大注射量校核7362注射压力校核7362锁模力校核7363模具厚度校核7364开模行程校核84浇注系统设计941主流道设计942冷料井设计943分流道设计10431分流道的布置形式10432分流道长度10433分流道截面形状10434分流道的截面尺寸1044浇口设计10V5成型零件设计1251分型面的设计12511分型面的分类及选择原则12512分型面的确定1252型腔分布1253成型零件结构设计12531成型零件具备的性能12532凹模结构设计13533凸模的结构设计13534影响塑件尺寸和精度的因素13535模具成型零件的工作尺寸计算146导向机构设计1861导向机构的作用和设计原则18611导向机构的作用18612导向机构的设计原则1862导柱、导套设计18621导柱的设计18622导套设计197脱模机构的设计2071脱模机构的设计原则2072顶出机构的确定2072脱模力的计算2173简单脱模机构21731顶杆脱模机构的设计要点21732顶杆的形状22733顶杆强度的计算2274复位装置238抽芯机构设计2481抽芯机构的概述2482抽芯机构的设计249温度调节系统设计2591温度调节系统的作用25911温度调节系统的要求25912温度调节系统对塑件质量的影响25VI92冷却系统的机构2510排气系统设计2611塑料模具用钢27111注塑模材料应具备的要求27112模具材料选用的一般原则27113本模具所选钢材及热处理2712模具装配图及工作过程28121模具装配二维图28122模具开模状态29123模具装配图三维爆炸图30124模具工作过程3113模具可行性和环保分析32131本模具的特点32132市场效益及经济效益分析32133环保分析3214总结33致谢34参考文献35毕业设计(论文)知识产权声明36毕业设计(论文)独创性声明371绪论11绪论11塑料模具概况模具是制造业的一种基本装备,作用是控制和限制材料的流动,形成所需要的形体7。模具制造零件效率高,质量好,材料消耗低,生产成本低,广泛应用在制造业中。模具工业是高新技术产业的一部分,也是高新技术产业化的重要领域。模具在机械电子,汽车,纺织,航空航天等领域里,成为使用最广泛的主要装备,它承担了这些领域中6090的产品。塑料模具是大批量生产塑料制品的现代化专用成型工艺装备的总称8。塑料是继陶瓷和金属后的第三大材料,广泛应用于现代工业和日常生活中。塑料成型就是将各种形态的塑料原料制成所需的制品或胚件的过程。塑料注塑成型过程是将塑料原料从注塑机的料斗进入加热筒,经塑化后由柱塞或螺杆的推动,在一定压力下通过喷嘴进入模具型腔,经冷却固化后而开模获得制品。塑模传统的设计方法,是依靠设计经验技巧和现有数据,从对塑件的计算到塑模的设计制图,全靠手工。对塑模的制造更需要专业人士付出大量繁杂劳动。所以塑件的质量和数量都远不能满足生产发展的需要。随着计算机广泛应用,塑模设计和制造采用了CAD/CAM系统,大大提高了模具设计制造的效率。12国内外发展状况121国内发展状况20世纪80年代开始,发达国家的模具已从机床中分离出来,并发展成为独立的部门,产值超过机床的产值。改革开放后,我国模具发展非常迅速。近年来,每年增长速度达15。模具企业十分重视技术的发展。加大了技术投入力度,将技术进步作为企业发展的动力。另外,许多科研机构和院校也开展了模具技术的研究与开发。模具行业的快速发展是使我国成为制造大国的重要原因。我国塑料模工业从起步到现在,历经了半个多世纪,有了很大发展,模具水平有了较大提高。经过多年的努力,模具CAD/CAE/CAM技术,模具的电加工技术和数控加工技术、快速成型与快速制模技术、新型材料等方面取得了显著进步;在提高模具质量和缩短模具设计制造周期等方面作出了贡献。毕业设计(论文)2122国外发展状况欧美大多数模具企业的生产技术水平,在国际上是一流的。模具的设计与制造,成为快速制造优质模具的有力保证。CAD/CAE/CAM的广泛应用,显示了信息技术带动和提升模具工业的优越性。目前,国外注射成型发展迅速,精密注射成型计算机技术的广泛应用,及全电动注射剂、两板式注射机、无拉杆注射机、电磁动态化注射机、低压注射成型、高速注射成型、复合注射成型、超级小精密注射成型等技术的研发及应用,提高了国外模具的生产和制造水平9。123中国与国外先进技术的差距尽管我国模具工业有了很大的进步,部分模具达到国际先进水平,但无论是数量还是质量仍无法满足国内市场的需求,每年仍需进口各类大型精密复杂模具。与发达国家模具工业相比,在模具技术上仍有很大的差距。今后,我国模具行业在以下几方面进行技术创新,缩小与国际先进水平的距离。注重开发大型精密复杂模具;提高成型零件的大型化和精密化要求;加强标准件的应用;使用标准件能缩短模具制造周期,降低成本且能提高模具的质量;推广CAD/CAM/CAE技术;模具CAD/CAM/CAE技术是模具发展的一个重要里程碑。实践证明,模具CAD/CAM/CAE技术是模具设计制造的发展方向,可提高模具设计制造水平;缩短模具制造周期。13塑料模具发展走势从市场来看,塑料模具生产企业应重点发展技术含量高的大型精密复杂长寿命模具,大力开发国际市场,发展出口模具。随着塑料特别是工程塑料的高速发展,模具工业的整体发展迅速。主要表现在以下几个方面(1)用户将交货周期放在首位。(2)提高开发能力,将开发工作往前推,到模具用户的产品开发中去,甚至在尚无明确用户对象前进行开发,变被动为主动。(3)模具企业及模具生产正在向信息化迅速发展。(4)随着人类社会的进步,模具必然会向更广泛的领域和更高水平发展。(5)发达国家模具工业正加速向中国转移,其表现方式一迁厂;二投资;三采购。2塑件成型工艺的可行性分析32塑件成型工艺的可行性分析21功能设计功能设计是要求塑件应具有满足使用目的功能,并达到一定的技术指标10。该塑件是日用品,承受外力很小,如冲击载荷,振动,摩擦等;塑件的工作温度是室温,则材料选择时对热变形、脆化、分解温度的要求降低;作为一种日用品,生产批量应该是大批大量生产,这样,就必须考虑生产成本和模具寿命,在材料的选择时要综合各种因素;此外,塑料都会老化,作为一种光学用品,还要考虑到材料的光氧化等问题。22塑件分析塑件如图21所示,它是日常用品,需求量大,外面要求比较高,所以模具浇注系统采用双分型面的点浇口,根据该塑件的结构特点,模具设计采用顶杆顶出机构,也是工厂里比较简单实用,常见的顶出结构。为了使模具与注射机相匹配以提高生产力和经济性、保证塑件精度,并考虑模具设计时应合理确定型腔数目,由于产量比较大,该模具选择一模四腔。23材料的选择通常,选择塑件的材料依据是它所处在的工作环境及使用性能的要求。该塑件对材料的要求必须是透光性好,其次才是成型难易和经济性问题,以下是对几种透光性能较好材料的性能对比,如表21所示16。图21塑件图(A)二维塑件图(B)三维塑件内部结构(C)三维塑件外部结构毕业设计(论文)4表21材料特性材料名称材料特性聚苯乙烯(PS)聚碳酸酯(PC)聚甲基丙烯酸甲酯(PMMA)拉伸强度/MPA5196672弯曲强度/MPA11095113洛氏硬度/(M)11582101氧指数/(OI)181249173热变形温度/85134100维卡软化点/105153120马丁耐热温度/112体积电阻率/CM1017101921101610141015透光度/88928992雾度/30909折射率/159215861492价格/(元/吨)1150123033000410001950020700与机械加工一样要考虑加工工艺问题,模具成型也要考虑材料的注塑特性,在各材料特点都相差无几的情况下,成型特性是选择材料的主要标准,以下是三种材料性能和成型特性比较,如表22所示16。表22材料的性能和成型特性比较塑料品种性能特点成型特点模具设计注意事项使用温度主要用途聚苯乙烯透明性好,电性能好,抗拉强度高,耐磨性好,质脆,抗冲击强度差,化学稳定性教好成型性能好,成型前可不干燥,但注射时应防止溢料,制品易产生内应力,易开裂因流动性好,适宜用点浇口,但因热膨胀大,塑件中不宜有嵌件3080装饰制品,仪表壳,绝缘零件,容器,泡沫塑料,日用品等聚甲基丙烯酸甲酯透光率最好,质轻坚韧,绝缘性好、表面硬度不高,质脆,化学稳定性较好,不耐无机酸等流动性差,易产生流痕,缩孔,易分解,透明性好,成型前要干燥,注射时速度不能太高合理设计浇注系统,便于充型,脱模斜度尽可能大,严格控制料温与模温2135),即该注塑机的开模行程符合要求。由以上对各参数的效核可知该G54S200/400型注塑机符合要求。4浇注系统设计104浇注系统设计浇注系由主流道、分流道、浇口、冷料井组成。41主流道设计主流道通常位于模具的中心,是塑料熔体的入口,其形状为圆锥形,便于熔融塑料的顺利进入,开模时又能使主流道的凝料顺利拔出。热塑性塑料的主流道一般由浇口套构成2。主流道设计如下主流道长度取L45MM;取主流道锥角4;主流道入口直径D注射机喷嘴直径1415MM;主流道出口直径DD2LTAN(/2)5245TAN(4/2)8MM;主流道球面半径SR注射机喷嘴球头半径(12)18220MM;球面配合高度H3MM。故主流道的结构形式如图41。42冷料井设计冷料井的位置正对主浇道的动模上,它的作用是将物料前端的“冷料”收集起来,防止“冷料”进入型腔而影响塑件的质量。开模时冷料井起到将主流道的冷凝料拉出。冷料井有带Z形拉料勾的冷料井;带球头形拉料的冷料井;倒锥形冷料井等4。本方案采用的是倒锥形冷料井。(A)浇口套二维图(B)浇口套三维图图41浇口套毕业设计(论文)1143分流道设计主流道与浇口之间的通道称为分流道。431分流道的布置形式为了尽量减少在流道内的压力损失和尽可能避免熔体温度降低,同事还要考虑减少分流道的容积和压力平衡,因此采用平衡式分流道15。如图42所示。432分流道长度根据四个型腔的结构设计,分流道长度适中,如图42。433分流道截面形状常用的分流道截面形状有圆形、正方形、梯形、U形、半圆形和正六角等15。考虑加工工艺,装配和经济性,本模具采用梯形截面分流道。434分流道的截面尺寸根据塑件的体积、形状、壁厚、所用塑料的工艺性能、注射速率以及浇道的长度等因素来确定1。对于壁厚小于3MM(本塑件厚度为2MM),质量在200G本塑件质量19G一下的塑件可用一下经验公式确定分流道的直径15。(41)1/24065DWL式中D分流道的直径,MM;W流经分流道的塑料量,G;L分流道长度,MM。由于本模具选择梯形截面,所以本模具梯形截面上底宽度D6MM,这也符合加工刀具选择,选择圆角半径R1MM16,由表41知梯形高度H2D/34MM,梯形斜边与竖直方向夹角在510,即可确定下底边宽度为D45MM。分流道截面如图43。图42分流道布置形式图43分流道截面形状毕业设计(论文)1244浇口设计浇口的形式众多,通常都有边缘浇口、圆环浇口、点浇口、潜伏式浇口、护耳浇口、直浇口等16。该塑件表面质量要求较高,采用一模四腔注射,点浇口。位置在塑件的定端中心位置。浇口的结构如图44。图44点浇口的结构形式5成型零件设计135成型零件设计模具闭合时,成型零件构成了塑料制品的型腔,成型零件主要有型腔、型芯、各种成型杆。成型零件承受高温高压冲击和摩擦,在冷却固化中形成塑件的形体、尺寸和表面。在开模和脱模时需克服塑件的包紧力。在上万次的注射周期,成型零件的形状、尺寸精度、表面质量及其稳定性,决定了塑料制品的质量。成型零件结构材料和热处理的选择及加工工艺性,是影响模具工作寿命的主要因素2。51分型面的设计511分型面的分类及选择原则实际的模具结构主要有三种情况(1)型腔在动模一侧;(2)型腔在定模一侧;(3)型腔在动定、模中。分型面的选择关系到塑件的正常成型和脱模。分型面的总体选择原则有以下几条(1)脱出塑件方便;(2)模具结构简单;(3)型腔排气顺利;(4)确保塑件质量;(5)无损塑件外观;(6)合理利用设备。512分型面的确定该模具中分型面设在塑件截面尺寸最大的部位,如图51中AA截面。52型腔分布模具型腔在模板上的排列方式有圆形排列、H形排列、直线排列、对称排列及复合排列等10。该模具有简单的抽芯结构,综合考虑模具设计为一模四腔,零件采用对称排列,有利于节约材料,简化结构。具体排布如图5253成型零件结构设计531成型零件具备的性能由于成型零件质量直接影响到塑件的质量,且与高温高压的塑料熔体接触,图51分型面位置图52型腔分布5成型零件设计14所以必须具备一下性能13毕业设计(论文)15(1)具有足够的强度和刚度,以承受塑料熔体的高温和高压;(2)具有足够的硬度和耐磨性,以承受流料的摩擦和磨损;(3)具有良好的抛光性能和耐腐蚀性能;(4)零件的加工性能好,可淬性良好,热处理变形小;(5)成型部位须有足够的位置精度和尺寸精度。532凹模结构设计凹模用于成型塑件的外表面,又称为型腔。按其结构的不同可分为整体式、整体嵌入式、局部镶嵌式和四壁镶嵌式5种。总体上说,整体是强度、刚度好,但不适于复杂的型腔。镶嵌式采用组合的模具结构,是复杂型腔加工相对容易,可避免采用同一材料,可利用拼接间隙排气,但刚度较差易在塑件表面留下镶嵌块的拼接痕迹,模具结构复杂5。由于该模具结构简单,又属于中小型模具,所以凹模板采用整体式。533凸模的结构设计凸模用于成型塑件的内表面,又称型芯。凸模按结构分为整体式和镶拼组合式两类。由于凸模的加工相对凹模容易,所以大多数的凸模是整体式的,尤其是在小型模具中型芯、模板常做成一体5。凸模板采用整体式。534影响塑件尺寸和精度的因素工作尺寸是成型零部件上直接决定塑件形状的有关尺寸,主要包括凹模、凸模的径向尺寸与高度尺寸等。为了保证塑件质量,模具设计时必须根据塑件的尺寸与精度等级确定相应的成型零部件工作尺寸与精度。其中影响模具尺寸和精度的因素很多,主要包括以下几个方面7(1)成形收缩率在实际工作中,成形收缩率的波动很大,从而引起塑件尺寸的误差很大,塑件尺寸的变化值为式中S为塑件收缩波动而引起的塑件尺寸()(51)误差,MM;SMAX为塑料的最大收缩率,;SMIN为塑料的最小收缩率,;LS为塑件尺寸,MM。一般由收缩率引起的塑件尺寸误差要求控制在塑件尺寸公差的1/3以内。(2)模具成形零件的制造误差实践证明,如果模具的成形零件的制造误差在IT7IT8级之间,成型零件的制造公差占塑件尺寸公差的1/3。(3)零件的磨损模具在使用过程中,由于种种原因会对型腔和型芯造成毕业设计(论文)16磨损,对于中小型塑件,模具的成形零件最大磨损应取塑件公差的1/6,而大型零件,应在1/6之下。(4)模具的配合间隙的误差模具的成形零件由于配合间隙的变化,会引起塑件的尺寸变化。模具的配合间隙误差不应该影响成形零件的尺寸和位置精度。综上所述,在模具型腔与型芯的设计中,应综合考虑各种影响成型零件尺寸的因素,在设计时进行有效的补偿。由于影响因素很不稳定,补偿值应在试模后进行逐步修订。535模具成型零件的工作尺寸计算通常凹模、凸模组成的模腔工作尺寸简化后的计算方法有平均收缩率法和公差带法两种。其中平均收缩率法以平均概念进行计算,从收缩率的定义出发,按塑件收缩率、成形零件制造公差、磨损量都为平均值的计算,公式如以下7(1)凹模(型腔)內形尺寸凹塑(1)343(52)式中L凹型腔內形尺寸,MM;L塑塑件外径基本尺寸,MM;K塑料平均收缩率,此处取05;模具制造公差,按IT9级公差选取而精度要求不高的塑件按(1/31/6)选取,此处选1/3。塑件公差,查表知PS塑件精度等级取3级;查塑料公差表得塑件基本尺寸3MM,020MM;塑件基本尺寸在36MM,024MM;塑件基本尺寸在1014MM,028MM;塑件基本尺寸在1418MM,030MM。塑件基本尺寸在2430MM,050MM;塑件基本尺寸在3040MM,056MM;塑件基本尺寸在8580MM,086MM;所以型腔尺寸如下180(10005)34086086380780290毕业设计(论文)17228(10005)34050050328750170337(10005)34056056336760190型腔深度的尺寸计算式中H凹凸模/型芯高度尺寸,MM;凹塑(1)233(53)H塑为塑件內形深度基本尺寸,MM;、K含义如(52)式中。128(10005)23050050327810170215(10005)23030030314860100型腔二维图三维图如图53。(2)凸模(型芯)外形尺寸计算(A)型腔板二维图主视图(B)型腔板二维左视图(C)型腔板三维图正面(D)型腔板三维图背面图53型腔毕业设计(论文)18凸塑(1)343(54)式中L凸凸模/型芯外形尺寸,MM;L塑塑件內形基本尺寸,MM;、K含义如(51)式中。由于该塑料的收缩率不大为05,故只需在型腔尺寸比较大的考虑其收缩率,在尺寸小的地方不用考虑由收缩率引起的尺寸偏差。所以型芯的尺寸如下176(10005)3408608637703002924(10005)340240243420008213(10005)3402802831330009型芯的二维三维如图54。(A)型芯二维主视图(B)型芯二维左视图(D)型芯三维背面图(C)型芯三维正面图毕业设计(论文)19型芯的深度尺寸计算(55)凹塑(1)233式中H凹凸模/型芯高度尺寸,MM;H塑塑件內形深度基本尺寸,MM,即塑件的实际內形深度尺寸;、K含义如(51)式中。型芯的高度为14(10005)230240243418000821(10005)230200203114000736(10005)2302402436190008抽芯机构斜顶杆二维三维图55。图54型芯图55斜顶杆(A)斜顶杆二维图(B)斜顶杆三维图6导向机构设计206导向机构设计61导向机构的作用和设计原则611导向机构的作用导向机构是保证塑料注射模具的动模与定模合模时正确定位和导向的重要零件,通常采用导柱导向,主要零件包括导柱和导套。具体作用有以下几点15(1)定位作用;(2)导向作用;(3)承载作用;(4)保持运动平稳作用。612导向机构的设计原则主要设计原则(1)导柱(导套)应对称分布在模具分型面的四周,其中心至模具外缘应有足够的距离,以保证模具强度和防止模板发生变形;(2)导柱(导套)的直径应根据模具尺寸选定,并应保证有足够的抗弯强度;(3)导柱固定端的直径和导套的外径应尽量相等,有利于配合加工,并保证了同轴度要求;(4)导柱和导套应有足够的耐磨性;(5)为了便于塑料制品脱模,导柱最好装在定模板上,但有时也要装在定模板上,这就要根据具体情况而定20。62导柱、导套设计导柱导向是指导柱与导套采用间隙配合使导柱在导套内滑动,配合间隙一般采用H7/F6级配合。621导柱的设计导柱的基本结构形式有两种。一种是除安装部分的凸肩外,其余部分直径相同,成为带头导柱GB4169484;另一种是除安装部分的凸肩外,安装的配合部分直径比外伸的工作部分直径大,成为有肩导套GB4169584。为了减小导柱导套的摩擦,有的导柱开设油槽18。本模具采用加油槽的带头导柱,根据GB4169484选用直径为25MM长度为200MM的导柱。其示意图61如下(A)二维图(B)三维图6导向机构设计21图61导柱毕业设计(论文)22622导套设计由于导柱已选定所以由机械设计手册可查的与之相配的导套为。为了使导柱进入导套比较顺利,在导套的前段倒一圆角R。根据导柱选择直径为25MM的导套,其结构如图62和图63图62导套1(A)导套1二维图(B)导套1三维图图63导套2(B)导套2三维图(A)导套2二维图7脱模机构设计237脱模机构的设计在注射成型的每一循环中,塑件必须从模具的型腔及型芯中被脱出,这一完成塑件脱出的机构成为脱模机构18。71脱模机构的设计原则塑件滞留于动模,模具开启后应以使塑件及浇口凝料滞留于带有脱模装置的动模上,以便模具脱模装置在注射机顶杆的驱动下完成脱模动作。保证塑件不变形损坏,这是脱模机构应达到的基本要求。首先要正确分析塑件对型腔或型芯的附着力的大小以及所在的部位,有针对性地选择何时的脱模方法和脱模位置,使顶出中心和脱模阻力中心相重合。型芯由于塑件收缩时对其包紧力最大,因此顶出的作用应该竟可能地靠近型芯,顶出力应该作用于塑件刚度、强度最大的部位,作用面尽可能大一些。影响脱模力大小的因素很多,当材料的收缩率大,塑件壁厚大,模具的型芯形状复杂,脱模斜度小以及型腔(型芯)粗糙度高时,脱模阻力就会增大,反之则小。力求良好的塑件外观,顶出塑件的位置应该尽量设在塑件内部或对外观影响不大的部位,在采用顶杆脱模时尤其要注意这个问题11。72顶出机构的确定顶出机构的功能是在任何正常的情况,顶出机构都能确实可靠的将成型塑件从模板一侧顶出,并在合模时其相关的顶出零件确保不与其它模具零件相干扰的恢复到原来的位置。顶出机构的设计原则开模时应留在动模的一侧;塑件在成型顶出后,一般都有痕迹,但应尽量使顶出残留痕迹不影响塑件的外观,一般顶出机构应设在塑件内表面以及不显眼的位置;顶出装置力求均匀分布,顶出力作用点应在塑件承受顶出力最大的部位,即不易变形或损伤的部位,尽量避免顶出力作用于最薄的位置,防止塑件在顶出过程中的变形和损伤;顶出机构应平稳顺畅,灵活可靠。顶出机构有多种类型,本设计采用顶杆中心顶出。采用段面形状为圆柱形的顶杆,圆柱型顶杆是最常用的一种,由于这个形状的顶杆和顶杆孔最容易加工,且容易保证其配合精度,易于保证其互换性,并易于更换,而且它还具有滑动阻力小,不易卡滞等优点,因此,我们采用圆柱形顶杆顶出。毕业设计(论文)2472脱模力的计算经过注射机的高压注射塑料在模具内冷却定型,此时塑料收缩将型芯包紧,这一包紧力是开模后塑件脱出时所必须克服的,此外还有不通孔带来的大气压力,塑料及型芯的粘附力,摩擦力及机构本身运动时所产生的摩擦阻力。开始脱模时的瞬时阻力最大,称为初始脱模力。脱模力的计算一般总是计算初始脱模力。塑件的脱模力计算公式如下所示。(71)()式中F脱模力,N;P单位面积塑件对型芯的正力,PA,一般取(4481176)MPA;PA塑件包紧型芯的侧面积,M2;F塑件与模体刚才的摩擦系数,一般去0103;F脱模斜度,取536。2231440266531103210106653103(02536536)640873简单脱模机构在所有模具的脱模机构中,简单脱模机构是最常用的一种形式,即在动模一边施加一次顶出力,就可将塑件从模具中脱出的机构,通常包括顶杆脱模机构,顶管脱模机构,推板脱模机构,活动镶件或凹模脱模机构,多元件联合脱模机构和气动脱模机构等。本模具方案采用顶杆脱模机构。731顶杆脱模机构的设计要点(1)顶出的顶出位置应该设在脱模阻力大的部位。(2)顶杆不设置在塑件薄壁处,一面塑件变形破损。(3)顶杆直径不宜过小,有足够的刚度。(4)顶杆与型芯或型腔板顶杆孔的配合一般为H8/H7或H7/H7,配合间隙可参考塑料不溢料间隙值。(5)顶杆材料多用45钢或T8、T10等碳素工具钢制造,采用头部局部淬火,淬火硬度在50HRC以上,局部淬火长度为15倍推出行程与配合长度之和,表面粗糙度在RA16M。(6)在一般情况下顶杆已基本作为模具标准出现,但是在特殊情况下,需要对顶杆作出进一步的加工。毕业设计(论文)25732顶杆的形状顶杆的形状多种多样,最常见的是截面为圆形的圆形顶杆。其尺寸可参照GB416911984。本模具采用顶杆为截面为圆形的圆形顶杆如图71,特殊顶杆如图72。733顶杆强度的计算(1)圆形推杆直径D的计算公式如下。式中6422314(72)圆D形推杆直径,CM;推杆长度系数07;推杆长度,CM;L推杆数量;N推杆材料的弹性模量,N/CM2,钢;E710E总脱模力,N;Q计算得(640721352203143211076408)143(2)推杆应力校核4273式中推杆应力,N/CM2;推杆钢材的屈服极限强度,N/CM2;一般中碳钢N/CM2;32000合金结构钢N/CM2;420004640820314324535(A)顶杆1二维图(B)顶杆1三维图图71顶杆1图72顶杆2(A)顶杆2二维图(B)顶杆2三维图毕业设计(论文)26即推杆满足要求。74复位装置脱模机构将塑件脱模后,在进行下一次成型前,除推板脱模机构以外,必须先行回到初始位置,尤其是有侧向分型的模具,顶杆与侧向抽出型芯之间会相互干扰,这就更要求顶出机构必须在闭模前回到初始状态。常用的复位形式有复位杆复位,顶出杆兼复位杆复位,弹簧复位。本模具采用复位杆复位,复位杆的工作端面顶在定模的固定板上,由于定模固定板没有热处理,为防止在模具工作中复位杆将定模固定板顶出凹坑,一般在固定板上镶入淬火垫块,复位杆的另一工作面与固定顶杆的顶出固定板相连,在模具闭模时,由复位杆推动顶杆固定板,带动顶杆回程。复位杆结构形式如图73所示。(A)复位杆二维图(B)复位杆三维图图73复位杆8抽芯机构设计278抽芯机构设计81抽芯机构的概述当塑件具有与开模方向不同的内侧孔、外侧孔或侧凹穴时,除少数情况可以强制脱模外,一般都必须将成型侧孔或侧凹穴的零件做成可动的机构,在塑件脱模前,先将其抽出,然后再从型腔中和型芯上脱出塑件。完成侧向活动型芯抽出和复位的机构就叫侧向抽芯机构。此类模具脱出塑件的运动有两种情况一是开模时优先完成侧向分型或抽芯,然后推出塑件;二是侧向抽芯分型与塑件的推出同时进行。侧向分型与抽芯机构按其动力来源分为手动、机动、气动或液压三类。其中机动侧向分型抽芯是指开模时,依靠注塑机的开模动力,通过侧向抽芯机构改变运动方向,将活动零件抽出。机动抽芯具有操作方便、生产效率高、便于实现自动化生产的优点,虽然模具结构复杂,但仍在生产中广为采用22。82抽芯机构的设计注射成型带有侧凹或者侧孔的塑料制品是,模具必须带有侧向分型或者侧抽芯机构,以便在脱模之前先抽掉侧向成型零件,否则无法脱模。侧抽芯分为内侧抽芯和外侧抽芯15。当塑件的侧凹较浅,抽芯距不大,且抽芯力也不大,本模具采用斜滑杆机构进行侧向分型与抽芯。斜滑杆侧向分型与抽芯的特点是利用推出机构的推力推动斜滑杆固定块斜向运动,在塑件被推出脱模的同时由斜滑杆完成侧向分型与抽芯动作。由于该塑件有内侧凹孔,故该塑件必须有内侧抽芯机构。结构如图81所示。抽芯机构的简单运动过程模具在分模时型腔6与动模分开,动模继续运动,直到顶出机构顶到推板1,推板1与T型滑槽2和顶杆8,9连接,推动斜顶杆3和顶杆8,9,斜顶杆3和顶杆8,9推出塑件7,而斜顶杆3为内侧抽芯,此内侧抽芯与塑件推出同时进行。图81内侧抽芯1推杆固定板2T型滑槽3斜导杆4型芯固定板5型芯6型腔7塑件8和9顶杆9温度调节系统设计289温度调节系统设计塑料注射模温度调节能力,直接影响到塑件的质量,也决定着生产效率的高低,塑件在型腔内的冷却力求做到均匀、快速,以减少塑件的内应力,使塑件的生产做到优质高效率。91温度调节系统的作用温度调节系统在模具中的作用非常重要的,尤其对厚壁塑件和平整度有要求的大型薄壁塑件来讲更为重要。911温度调节系统的要求质量优良的塑件应满足一下六方面的要求,即收缩率小,变形小,尺寸稳定,冲击强度高,耐应力开裂性好和表面粗糙度低。912温度调节系统对塑件质量的影响塑料熔体注入型腔后,释放大量热量。不同的塑料,需要模腔维持在某一适应温度。模温对塑件质量的影响主要表现在如下六个方面(1)改善成形性;(2)成型收缩率;(3)塑件变形;(4)尺寸稳定性;(5)力学性能;(6)外观质量。92冷却系统的机构冷却水道形式大体分为,沟道式冷却、管道式冷却和导热杆式冷却。本模具采用的是沟道式冷却;冷却水道的连通方式有串联和并联两种;型腔的冷却;本模具采用的是沿型腔边缘设置若干并联或串联的循环水路。由于该塑件体积比较小,所以水道采用直水道直径为6MM,其分布如下图(B)冷却管道分布主视图9温度调节系统设计29(A)冷却管道分布俯视图(C)冷却管道分布左视图图91冷却管道分布10排气系统设计3010排气系统设计该塑件采用点浇口进料,熔体经塑件上方向下流动,充满型腔,每个型芯上有四个顶杆和三个抽芯杆,其配合间隙可作为气体排出方式,不会产生憋气现象。同时产生的气体会沿着分型面之间的间隙向外排出。11塑料模具用钢3111塑料模具用钢由于难加工成型材料的不断出现以及产品零件形状的日益复杂化和锻压生产的高速化,对模具耐磨性、耐热性、强度与韧性等使用性能的要求也随之提高。因此,按照模具的性能要求与生产过程,正确选用模具材料,并施以适当的热处理,以充分发挥其最大潜力9。111注塑模材料应具备的要求塑模材料必须具备以下条件(1)机械加工性能良好;(2)耐磨性和韧性等机械性能良好;(3)加工和时效处理的变形微小;(4)难化学侵蚀和难腐蚀性能良好;(5)较好的淬火性能和热处理变形极小;6)焊接修补性能良好;(7)不易产生电加工硬化层。112模具材料选用的一般原则选用模具材料的一般原则是1满足模具使用性能要求;2具有良好的工艺性能;3适当考虑经济性。113本模具所选钢材及热处理我国模具用钢一般采用工具钢,如T8A、T10A、CRWMN、CR12MOV钢等,这些钢由于切削加工性一般较差,难以制造成复杂型腔的模具,而且一旦热处理变形超差即难以修复使用。因此,近年来模具制造业采用退火或正火状态的45钢及预硬刚做塑料模具用钢2。塑料膜型腔模具用于较高温度状态下,一般要求具有耐热性、一定的机械强度、耐磨性、耐腐蚀性、镜面加工性。塑料膜对强韧性方面的要求不高,但要求较高的耐蚀性。本模具所用钢材及热处理如下表111所示。表111本模具所用钢材及热处理零件名称主要性能要求材料热处理浇口套、定位环耐磨性T8A淬火低温回火导柱、导套表面耐磨,心部有一定韧性T8A渗碳淬火低温回火顶杆、拉料杆头部耐磨,杆部有一定强度45局部淬火低温回火11塑料模具用钢32固定模板、垫板一般强度45正火型芯、型腔高精度、高抛光性、高寿命40CR淬火12模具工作过程3312模具装配图及工作过程121模具装配二维图如图121。图121模具装配图1动模固定板2内六角螺钉13垫块4推杆支撑板5推杆固定板63顶杆17型芯固定板8内六角螺钉29型芯10水路11塑件12开闭器13型腔14型腔固定板15内六角螺钉316推料板17定模座板18导套219导套120导柱21支撑钉22内六角螺钉423滑块24复位杆25弹簧26斜顶杆273顶杆228拉料杆29内六角螺钉530内六角螺钉631定位环32浇口套33内六角螺钉734定位拉杆35内六角螺钉836固定块37冷却水管接头GZ1/4毕业设计(论文)34122模具开模状态模具开模状态如图122。123模具装配图三维爆炸图模具装配爆炸图如图123。图122模具开模状态(A)第一次开模(B)第二次开模(C)第三次顶出塑件毕业设计(论文)35图123三维爆炸图毕业设计(论文)36124模具工作过程将模具装在G54S200/400型号的注塑机中,注射机成型时,注射机的合模系统带动动模(1)前行,在导套(18、19)导柱(20)的作用下与定模(17)靠拢合并形成闭合。喷嘴通过定位环(3)将注塑机喷嘴固定,喷嘴与浇口套(32)配合,将注塑机中的熔融状态的聚苯乙烯(PS)通过浇口套(32)将PS注入浇注系统(包括分流道和点浇口)中,最后流入型芯(9)和型腔(12)中,注满后,经过保压补缩、冷却(通过水嘴(36)将冷却水注入型芯(9)和型腔(12)中冷却管道(10)定型固化为塑件制品,最后塑件包覆在型芯(9)上,浇注系统(浇口套(32)和分流道和点浇口)中剩余的塑料中的塑料完全固化后,然后通过注射机上的合模系统带动动模固定板(1),而动模固定板通过内六角螺钉(2)、(8)连接垫块(3)型芯固定板(7),然后带动动模机构运动。动模机构通过导套1(18)、2(19)和导柱(20)定位、定位拉杆(35)和开闭器(15)进行第一次分型如图112(A)。动模继续运动,型腔固定板(14)和型腔(12)通过内六角螺栓连接,并通过定位拉杆(35)将型腔固定板(14)和型腔(12)拉开,即第二次分型如图112(B)。动模继续运动,注射机顶杆通过动模固定板(1)中顶杆孔进入推动推杆支撑板(4)和推杆固定板(5),推动顶杆滑块(23)和顶杆(6和27)将塑件(11)顶出,同时进行内侧抽芯并推动复位杆(24)压缩弹簧(25)还有通过拉料杆(28)将浇口套(32)和分流道点浇口中凝料推出,如图112(C),然后手取出塑件。最后通过复位杆(24)和弹簧(25)将顶出机构复位,准备一次模具的制作。13模具可行性分析3713模具可行性和环保分析131本模具的特点(1)本模具结构合理、紧凑,符合客户的生产要求;(2)模具的设计不仅解决了一些形状复杂的零件无法加工成型的问题,还使得生产实现自动化,提高了生产效率,降低了生产成本,在精度方面也有一定的提高。132市场效益及经济效益分析首先,该产品的市场需求量很大,有着广阔的市场前景;其次,采用注塑成型不仅可以实现自动化生产,提高生产效率,节约劳动力,降低成本。综上所述,该设计方案是一个可行的经济合理。133环保分析在生产过程中产生的废品和浇口套分流道中的凝料,可以回收利用,可以成为下次制作的原料,这样不仅环保而且减少浪费。14总结3814总结本文主要针对灯罩,对其进行塑料模具设计。本文介绍了注射模具国内外的发现状况及发展趋势,介绍了注射成型原理和工艺过程;根据塑件要求选择合适的注塑机,进而选择合适的浇注系统与冷却系统;通过计算,对导向机构、脱模机构和侧向分形与抽芯机构进行设计。该模具的凹模采用整体式型腔,结构简单、合理,改善了模具加工的工艺性,降低了模具的生产成本。型芯采用斜滑块导滑内侧抽芯机构,解决了塑件内壁三向凹口的成型问题,保证了模具运动平稳可靠。采用双分型面设计,分散了脱模力,使塑件能顺利脱模,并有利于提高塑件的成型质量。该模具总体结构设计合理,型芯采用组合式,降低了模具的制造成本。成型的壳体塑件质量合格稳定,使塑件质量符合设计和使用要求。通过本次毕业设计让我学会了运用所学知识解决实际问题的能力,让我掌握了塑料模具设计的基本程序和方法,巩固、深化和扩展了我对所学的专业课程和专业知识,实例了我
- 温馨提示:
1: 本站所有资源如无特殊说明,都需要本地电脑安装OFFICE2007和PDF阅读器。图纸软件为CAD,CAXA,PROE,UG,SolidWorks等.压缩文件请下载最新的WinRAR软件解压。
2: 本站的文档不包含任何第三方提供的附件图纸等,如果需要附件,请联系上传者。文件的所有权益归上传用户所有。
3.本站RAR压缩包中若带图纸,网页内容里面会有图纸预览,若没有图纸预览就没有图纸。
4. 未经权益所有人同意不得将文件中的内容挪作商业或盈利用途。
5. 人人文库网仅提供信息存储空间,仅对用户上传内容的表现方式做保护处理,对用户上传分享的文档内容本身不做任何修改或编辑,并不能对任何下载内容负责。
6. 下载文件中如有侵权或不适当内容,请与我们联系,我们立即纠正。
7. 本站不保证下载资源的准确性、安全性和完整性, 同时也不承担用户因使用这些下载资源对自己和他人造成任何形式的伤害或损失。

人人文库网所有资源均是用户自行上传分享,仅供网友学习交流,未经上传用户书面授权,请勿作他用。