绕线筒手柄注塑模具设计【5张CAD图纸和说明书】
收藏
资源目录
压缩包内文档预览:(预览前20页/共36页)
编号:10111048
类型:共享资源
大小:1.62MB
格式:RAR
上传时间:2018-05-19
上传人:俊****计
认证信息
个人认证
束**(实名认证)
江苏
IP属地:江苏
40
积分
- 关 键 词:
-
绕线筒
手柄
注塑
模具设计
cad
图纸
以及
说明书
仿单
- 资源描述:
-
目 录
前言 1
1 塑件成型工艺分析 3
1.1 塑件分析 3
1.2 塑件材料的成型特性与工艺参数 4
2 拟定模具结构形式 7
2.1 分型面的设计 7
2.2 型腔的设计 8
3 注塑机型号选择与确定 10
3.1 所需注射量的计算 10
3.2 注射机型号的选定 11
3.3 型腔数量及注射机有关工艺参数的校核 12
3.4 注射机安装部分相关尺寸的校核 14
3.5开模行程的校核 14
3.6 模架尺寸与注射机拉杆内间距校核 15
4 浇注系统的设计 16
4.1 浇注系统设计的原则 16
4.2 主流道的设计 16
4.3 冷料穴的设计 18
4.4 分流道的设计 19
4.5 浇口的设计 22
4.6 浇注系统的平衡 23
4.7 浇注系统凝料体积计算 23
4.8 浇注系统各截面流过熔体的体积计算 24
4.9 普通浇注系统截面尺寸的校核 24
5 成型零件的设计 26
5.1 成型零件的要求及选材 26
5.2 成型零件的结构设计 26
5.3 成型零件尺寸的计算 26
5.4 型腔刚度的校核 30
6 模架的确定和标准件的选用 32
6.1 模架的选用 32
6.2 模板尺寸的确定 33
7 合模导向机构的设计 35
7.1 导柱的设计 35
7.2导套的设计 36
8 脱模机构的设计 38
8.1 脱模机构的分类及设计原则 38
8.2 脱模力的计算与校核 39
8.3 推杆的设计 40
8.4 脱模机构的复位元件 41
8.5 侧向分型与抽芯机构的设计 41
9 排气系统和温度调节系统的设计 45
9.1 排气系统的设计 45
9.2 冷却系统的设计 45
10 典型零件制造工艺 47
10.1定模仁型腔部分的制造工艺 47
10.2动模座板的数控程序设计 48
11 模具材料的选择 51
12 模具的工作过程 52
13 设计总结 53
14 参考文献 54
1 塑件成型工艺分析
1.1 塑件分析
1.1.1塑件模型
以下是塑件立体与平面图:
图1-1 塑件三维立体图
图1-2 塑件平面图
1.1.2 塑料 ABS(丙烯腈-丁二烯-苯乙烯共聚物)
1.1.3 塑料件质量 46.92g
1.1.4 塑料件体积 44.69
1.1.5 色调 不透明(黑色)
1.1.6 生产纲领 大批量生产
1.1.7 工艺结构分析
(1)结构分析
塑件结构复杂程度一般,表面质量要求也较高。塑件外观质量要求高,外表面不允许出现划伤、气泡、缩孔、熔接痕等缺陷, 综合考虑其浇注时的难易程度和成型特征等因素,浇口最好在另一侧的表面用侧浇口来进行浇注,以保证其表面的成型质量。整体来看该塑件成型简单,但在脱模时包紧力较大,应有一定的脱模斜度,用推杆推出即可。
(2)精度等级

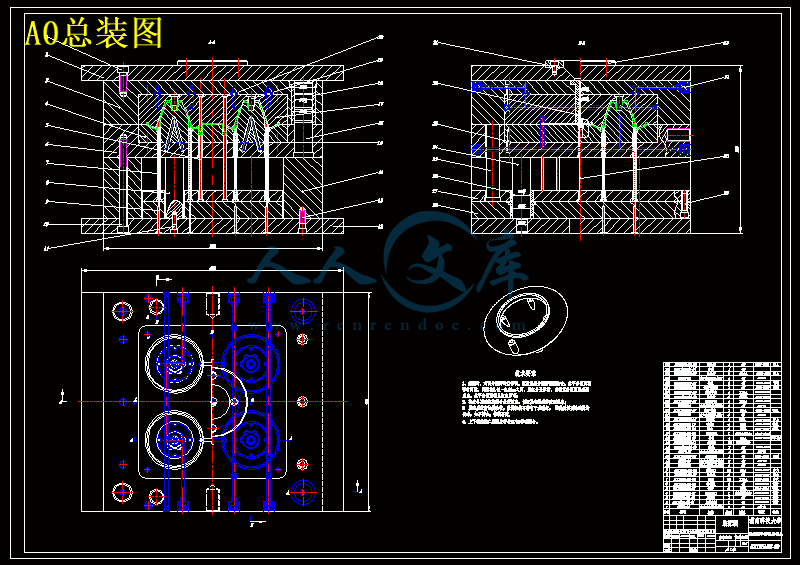

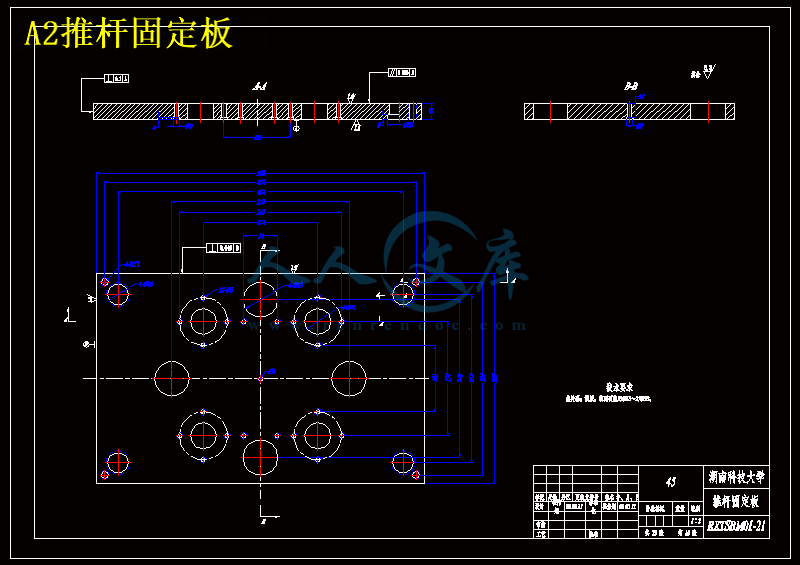

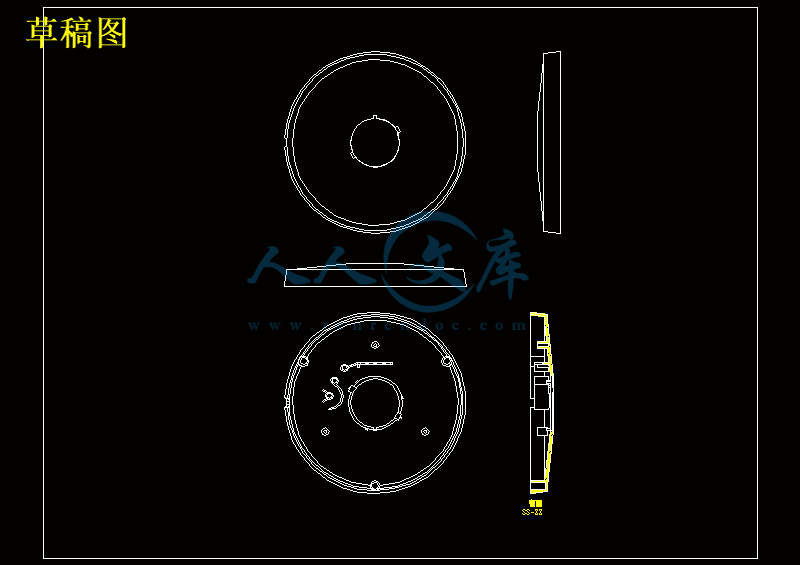
- 内容简介:
-
目 录前言 .11 塑件成型工艺分析 .31.1 塑件分析 .31.2 塑件材料的成型特性与工艺参数 .42 拟定模具结构形式 .72.1 分型面的设计 .72.2 型腔的设计 .83 注塑机型号选择与确定 .103.1 所需注射量的计算 .103.2 注射机型号的选定 .113.3 型腔数量及注射机有关工艺参数的校核 .123.4 注射机安装部分相关尺寸的校核 .143.5 开模行程的校核 .143.6 模架尺寸与注射机拉杆内间距校核 .154 浇注系统的设计 .164.1 浇注系统设计的原则 .164.2 主流道的设计 .164.3 冷料穴的设计 .184.4 分流道的设计 .194.5 浇口的设计 .224.6 浇注系统的平衡 .234.7 浇注系统凝料体积计算 .234.8 浇注系统各截面流过熔体的体积计算 .244.9 普通浇注系统截面尺寸的校核 .245 成型零件的设计 .265.1 成型零件的要求及选材 .265.2 成型零件的结构设计 .265.3 成型零件尺寸的计算 .265.4 型腔刚度的校核 .306 模架的确定和标准件的选用 .326.1 模架的选用 .326.2 模板尺寸的确定 .337 合模导向机构的设计 .357.1 导柱的设计 .357.2 导套的设计 .368 脱模机构的设计 .388.1 脱模机构的分类及设计原则 .388.2 脱模力的计算与校核 .398.3 推杆的设计 .408.4 脱模机构的复位元件 .418.5 侧向分型与抽芯机构的设计 .419 排气系统和温度调节系统的设计 .459.1 排气系统的设计 .459.2 冷却系统的设计 .4510 典型零件制造工艺 .4710.1 定模仁型腔部分的制造工艺 .4710.2 动模座板的数控程序设计 .4811 模具材料的选择 .5112 模具的工作过程 .5213 设计总结 .5314 参考文献 .5411 塑件成型工艺分析1.1 塑件分析1.1.1 塑件模型以下是塑件立体与平面图:图 1-1 塑件三维立体图2图 1-2 塑件平面图1.1.2 塑料 ABS(丙烯腈丁二烯苯乙烯共聚物)1.1.3 塑料件质量 46.92g1.1.4 塑料件体积 44.69 3cm1.1.5 色调 不透明(黑色)1.1.6 生产纲领 大批量生产1.1.7 工艺结构分析(1)结构分析塑件结构复杂程度一般,表面质量要求也较高。塑件外观质量要求高,外表面不允许出现划伤、气泡、缩孔、熔接痕等缺陷, 综合考虑其浇注时的难易程度和成型特征等因素,浇口最好在另一侧的表面用侧浇口来进行浇注,以保证其表面的成型质量。整体来看该塑件成型简单,但在脱模时包紧力较大,应有一定的脱模斜度,用推杆推出即可。(2)精度等级选用的精度公差等级按照国家标准为一般精度MT3级。(3)脱模斜度该塑件的壁厚约为2.26mm,从表查得该ABS塑件的脱模斜度, 型腔为35130, 型芯3040。脱模斜度取决于塑件的形状、壁厚、摩擦系数的大小及塑料的收缩率。形状愈复杂或成型孔较多时取较大的脱模斜度;制品高度愈高、孔愈深则取较小的脱模斜度;内孔包住型芯,应取较大的斜度。因此, 本次设计的脱模斜度型腔取1, 型芯取 40。一般情况下,脱模斜度不包括在塑件的公差范围内,否则应在图样上加以注明。当要求开模后塑件留在型腔内时,塑件内表面的脱模斜度应不大于塑件外表面的脱模斜度。1.2 塑件材料的成型特性与工艺参数1.2.1 塑料 ABS 成型特性(1)名称ABS(丙烯腈丁二烯苯乙烯共聚物) ,热塑性塑料。综合性能好,冲击强度、力学强度较高,尺寸稳定,耐化学性,电气性能良好;易于成型和机械加工,其表面可镀铬,适合制作一般机械零件、减摩零件、传动零件盒结构零件。(2)ABS 主要性能ABS,燃烧性慢,屈服强度、拉伸强度3850Mpa ,伸长率不大,热变形温度6075C,计算收缩率为0.4-0.7%。具体如下表:3表1-1 ABS的物理、热性能指标性能 单位 数值密度 3/cmg1.021.08比体积 0.860.98吸水率(24h) % 0.20.4收缩率(%) % 0.40.7熔点(或粘流温度) 130160热变形温度线膨胀系数 C/105 8310368表1-2 ABS的力学、电气性能指标性能 单位 数值抗拉、屈服强度 MPa 50拉伸弹性模量 MPa 1.4 310抗弯强度 MPa 80冲击韧度 kJ/m2 11(有缺口)布氏硬度 HB 9.7R121体积电阻率介电常数( 10 HZ)6m 6.9 1602.42.65(3)成型特性a 无定型塑料。其品种很多,各品种的机电性能及成型特性也各有差异,应按品种来确定成型方法及成型条件。b 吸湿性强。含水量应小于0.3%(质量) ,必须充分干燥,要求表面光泽的塑件应要求长时间预热干燥。c 流动性中等。溢边料0.04mm左右。d 模具设计时要注意浇注系统,选择好进料口位置、形式。推出力过大或机械加工时塑件表面呈现白色痕迹1.2.2 塑料ABS的成型工艺参数4(1)注射成形机类型:螺杆式,螺杆转数为30r/min。 (2)料筒温度():后段150170中段165180前段180200(3)喷嘴温度():170180。(4)模具温度():5080。(5)注射压力(MPa):60100。(6)成型时间(s):30(注射时间取1.6,冷却时间20.4,辅助时间8) 。 1.2.3 注射成型过程(1) 成型前的准备。对 ABS的色泽、粒度和均匀度等进行检验,由于ABS吸水性较大,成型前应 进行充分的干燥(2)注射过程。塑件在注射机料筒内经过加热、塑化达到流动状态后,由模具的浇注系统进入模具型腔成型,其过程可分为充模、压实、保压、倒流和冷却五个阶段。(3)塑件的后处理。处理的介质为空气和水,处理温度为 6075,处理时间为1620s2 拟定模具结构形式2.1 分型面的设计2.1.1 分型面的设计原则分型面即打开模具取出塑件或取出浇注系统凝料的面,在塑件设计阶段,就应考虑成型时分型面的形状和位置,否则无法用模具成型。在模具设计阶段,应首先确定分型面的位置,然后才选择模具的结构。分型面设计是否合理,对塑件质量、工艺操作难易程度和模具的设计制造有很大的影响。分型面的设计原则为:(1)便于塑件脱模;a 在开模时尽量使塑件留在动模内b 应有利于侧面分型和抽芯c 应合理安排塑件在型腔中的方位(2)考虑和保证塑件的外观不遭损坏;(3)尽力保证塑件尺寸的精度要求(如同心度等) ;(4)有利于排气;(5)尽量使模具加工方便;(6)有利于嵌件的安装;(7)有利于预防飞边和溢料的的产生;5(8)有利于模具结构的简化。该塑件在进行塑件设计时已充分考虑了上述原则,同时从塑件图样可看出该塑件一端顶部有一个圆形孔,且对应着底部有许多个凸起端,因此在分型时需要在型芯上安置多个镶块进行分型。2.1.2 分型面选择方案(1)分型面选择方案:单分型面注射模单分型面注射模又称两板式模具。它是注射模中最简单又最常见的一种结构形式。这种模具可根据需要设计成单型腔,也可以设计成多型腔。构成型腔的一部分在动模,另一部分在定模。主流道设在定模一侧,分流道设在分型面上。开模后由于拉料杆的拉料作用以及塑件应收缩包紧在型芯上,塑件连同浇注系统凝料一同留在动模一侧,动模一侧设置的推出机构推出塑件和浇注系统凝料。一般对于塑件外观质量要求不高,尺寸精度要求一般的小型塑件,可采用此结构。(2)分型面选择方案:双分型面注射模双分型面又称三板式注射模。与单分型面注射模相比,在动模与定模之间增加了一个可移动的浇口板(又称中间板) ,塑件和浇注系统凝料从两个不同的分型面取出。双分型面的种类较多,常见的有以下几种:a 定距板式双分型面注射模b 定距拉式双分型面注射模c 定距导柱式双分型面注射模d 拉钩式双分型面注射模e 摆钩式双分型面注射模f 尼龙拉钩式双分型面注射模双分型面对于塑件外观质量要求比较高,尺寸精度要求一般的小型塑件,可采用以上各种双分型面结构。综上分析,本设计拟定采用单分型面注射模。2.1.3 分型面的确定对于此塑料件,外观质量要求一般,并为防止在塑件外表面出现飞边而影响外观质量,其分型面形式与位置如图所示: 分 型 面图 2-1 分型面的形式与位置62.2 型腔的设计2.2.1 型腔数目的拟定为了使模具与注射机的生产能力相匹配,提高生产效率和经济性,并保证塑件精度,模具设计时应确定型腔数目,常用的方法有四种:(1)根据经济性确定型腔数目;(2)根据注射机的额定锁模力确定型腔数目;(3)根据注射机的最大注射量确定型腔数目;(4)根据制品精度确定型腔数目。型腔数目的确定一般可以根据经济性、注射机的额定锁模力、注射机的最大注射量、制品的精度等。一般来说,大中型塑件和精度要求高的小型塑件优先采用一模一腔的结构,但对于精度要求不高的小型塑件(没有配合精度要求) ,形状简单,又是大批量生产时,若采用多型腔模具可提供独特的优越条件,使生产效率大为提高。该塑件精度要求不高,生产批量大批量生产,从模具加工成本,制品生产时的成本考虑,故拟定为一模两腔。一般来说,精度要求高的小型塑件和中大型塑件优先采用一模一腔的结构,对于精度要求不太高的小型塑件,是大批量生产时,若采用多型腔模具可提供独特的优越条件,使生产效率大为提高。由此可见,该注塑机正好匹配所对应的型腔数目,所以可确定其型腔数量为2个。2.2.2 型腔的布置型腔的布置和浇口的开设部位应力求对称,以防模具承受偏载而产生溢料。为此,本模具一模两腔的布置方式如下图:图2-2 型腔的布局3 注塑机型号选择与确定注射模是安装在注射机上使用的工艺装备,因此设计注射模时应该详细了解注射机的技术规范,才能设计出符合规范的模具。注射机规格的确定主要是根据塑件的大小及型腔的数目和排列方式。在确定模具结构形式及初步7估算外型尺寸的前提下,设计人员应对模具所需的注射量、注射力锁模力、注射压力、拉杆间距、最大和最小模具厚度、推出形式、推出位置、推出行程、开模距离等进行计算。同时设计人员还必须对提供的注射机进行校核。3.1 所需注射量的计算3.1.1 塑件质量、体积的计算对于该设计,用户提供了塑件图样,据此建立塑件模型并对此塑件分析得:塑件体积 V144690 mm 3=44.69cm3,塑件质量 =46.92gm3.1.2 浇注系统凝料的初步计算、确定由于该模具采用一模两腔,按塑件体积的 0.2 倍计,所以浇注系统的凝料体积为:17.88cm369.42.02.1V则:该模具一次注射所需塑料 ABS:体积 107.26cm3210质量 112.61gVm3.1.3 塑件和流道凝料(包括浇口)在分型面上的投影面积及所需锁模力 221 6.351809.1462.09.461mAn KNPFm35)(2型式中 A-塑件及流道凝料在分型面上的投影面积;-单个塑件在分型面上的投影面积;1A-流道凝料(包括浇口)在分型面上的投影面积;2-模具所需的锁模力/N;mF-塑料熔体对型腔的平均压力/Mpa:由于该塑件材料为 ABS 且壁厚均匀,属于容易成型P型的塑件,故查表可取 =35 Mpa。型3.2 注射机型号的选定一般注射机都有高速、低速两种特性(或称高压时间,低压时间)并可调节选用。1000 以下2cm的中、小型注射机,其注射时间常为 4s,大型注射机注射时间在 12s 以内,注射速度一般为857m/min,常用低速注射。选用低速注射的注射机时,模具设计应注意防止产生冷接缝,型腔充填不足。选用高速注射的或用大注射量、大锁模力的注射机注射大面积、小重量的塑件时,模具设计应防止融料内充入空气、排气不良、融接不良、塑件内应力增大、塑料易分解、嵌件型芯受冲击力大及易发生飞边等弊病。根据上面计算得到的 m 和 值来选择一种注射机,注射机的最大注射量(额定注射量 G)和额F定锁模力 F 应满足 gG48.1325.06式中 -注射系数,无定型塑料取 0.85,结晶型塑料
- 温馨提示:
1: 本站所有资源如无特殊说明,都需要本地电脑安装OFFICE2007和PDF阅读器。图纸软件为CAD,CAXA,PROE,UG,SolidWorks等.压缩文件请下载最新的WinRAR软件解压。
2: 本站的文档不包含任何第三方提供的附件图纸等,如果需要附件,请联系上传者。文件的所有权益归上传用户所有。
3.本站RAR压缩包中若带图纸,网页内容里面会有图纸预览,若没有图纸预览就没有图纸。
4. 未经权益所有人同意不得将文件中的内容挪作商业或盈利用途。
5. 人人文库网仅提供信息存储空间,仅对用户上传内容的表现方式做保护处理,对用户上传分享的文档内容本身不做任何修改或编辑,并不能对任何下载内容负责。
6. 下载文件中如有侵权或不适当内容,请与我们联系,我们立即纠正。
7. 本站不保证下载资源的准确性、安全性和完整性, 同时也不承担用户因使用这些下载资源对自己和他人造成任何形式的伤害或损失。

人人文库网所有资源均是用户自行上传分享,仅供网友学习交流,未经上传用户书面授权,请勿作他用。