摘 要
近几年好多国家都在发展机械行业,与机械相关的各个行业都越来越重视CAD/CAM技术,如今CAD/CAM技术已发展成为一项比较成熟的共性技术,我国家电工业的高速发展对模具工业,尤其是塑料模具提出了越来越高的要求,国内塑料模具市场以注塑模具需求量最大,其中发展重点为工程塑料模具。同时还因为塑料制品及模具的3D设计与成型过程中3D分析正在塑料模具工业中发挥越来越重要的作用。
在本次毕业设计中,通过运用三维实体造型高端软件UG NX对“温控器垫块”外形进行3D造型,同时也设计了其塑料注塑模的3D模型。在正确分析塑件工艺特点和ABS的性能的基础上,介绍了对凸模,凹模,浇注系统,脱模机构,顶也机构的设计,选择标准零件,设计非标件的设计过程。由于模具生产的塑料制品具有高精度、高复杂程度、高一致性、高生产率和低消耗等特点,涉及模具结构、强度、寿命计算及熔融塑料在模具中流动预测等复杂的工程运算问题;CAD、UG NX等不同的软件可分别用于模具的设计、制造和产品质量进行分析。塑料注射成型所用的模具称为注射模成型模具,该模具特点是模具先由注射机合模机构闭和紧密,然后由注射机注射装置将高温高压的塑料熔体注入模腔内,经冷却或固化成型后,在侧向分型的作用下开模取出塑件。还根据所设计的模具尺寸选择安装了相应的模架,最终生成了直观的结构设计图;此外还利用CAD绘制了模具装配图以及各种成型零件图。
关键词:温控器;注塑模;CAD/CAM;ABS塑料;3D
Abstract
A lot of countries in the development of machinery industry in recent years, every industry pay more and more attention to related to mechanical CAD/CAM technology, CAD/CAM technology has now developed into a relatively mature technology, with the rapid development of our country home a ABS liance industry of mold industry, puts forward higher and higher requirements, especially plastic mould, in 2004, as a proportion of the plastic mold in the mold industry has risen to 30%, according to experts predict that in the next few years, China plastic mould industry will continue to maintain an annual growth rate of more than 10% of the high speed of development. Domestic demand in injection mold plastic mold market is the largest, the key for engineering plastic mold development. Also because of the plastic products and mould Three-Dimensional design and molding process of Three-Dimensional analysis is the plastic mold industry plays a more and more important role.
In this graduation design, the high-end software UG NX three-dimensional entity model is used to shape of "t type mounting bracket" Three-Dimensional modeling, and design the Three-Dimensional model of the plastic injection mold.On the basis of the correct analysis of the characteristics and ABS plastic parts process performance, the introduction of the punch,die,casting system, stripping agencies,top agency also design, selection of standard parts,the design of non-standard parts of the design process.Due to mold plastic products with high precision,high complexity,high consistency,high productivity and low consumption, etc,involve mold structure, strength,life span,and the molten plastic in the mold flow projections and other complex engineering computing problems; CAD,different software may be designed such UG NX molds are used,the manufacturing and product quality analysis.Plastic injection molding mold used for injection molding is called a mold injection machine is characterized first by a mold clamping mechanism and tightly closed, and then the injection machine injection device of the high temperature and pressure of the plastic melt into the mold cavity, cooling or after curing,in the role of the lateral parting remove mold plastic parts.Also according to the design of the mould size choose to install the corresponding mold frame, the resulting intuitive structure design; In addition to use CAD draw the mold assembly drawing as well as a variety of molding part drawing.
Key words:Thermostat;plastics mold;CAD/CAM;ABS plastic;Three-Dimensional
目 录
引言 1
1 注塑模设计的相关理论概述 3
1.1 注塑成型的相关概念 3
1.1.1 注塑成型的基本概念 3
1.1.2 注塑成型的特点 3
1.1.3 注塑成型的工艺过程 3
1.2 注塑模的定义 4
1.3 注塑模的分类 4
1.4 注塑模设计流程及关键环节 6
1.5 注塑模设计软件——UG简介 7
1.6 注塑模主要加工方法简介 9
2 温控器垫块注塑模设计 10
2.1 温控器垫块相关参数计算 10
2.2 温控器垫块成型工艺要求 10
2.2.1 塑件工艺性分析 10
2.2.2 塑件材料的基本特性 11
2.2.3 ABS的性能指标 11
2.2.4 塑件材料成型性能 11
2.2.5 尺寸精度分析 11
2.2.6 表面质量分析 11
2.2.7 模塑设备的选择 12
2.3 注射模的结构设计 13
2.3.1 分型面的选择 13
2.3.2 确定型腔的排列方式 13
2.3.3 浇注系统的设计 14
2.3.4 浇注系统的平衡 16
2.3.5 推件机构的设计 16
2.4 模架的选择 17
2.5 型腔工作尺寸的计算 17
2.6 型芯工作尺寸的计算 19
2.7 模具的其他相关计算 20
2.8 冷却装置的设计 20
2.8.1 冷却时间的计算 21
2.8.2 冷却水管直径 21
2.8.3 冷却水道的结构 21
2.9 开模行程的校核 22
2.10 注射机的校核 22
2.11 模具外形尺寸校核 22
2.12 注射模的安装与调试 23
3 温控器垫块注塑模的仿真实现 24
3.1 模具开发流程 24
3.2 产品建模 24
3.3 温控器注塑模装配仿真 25
4 温控器垫块注塑模型腔加工工艺及流程 28
5 机械加工工艺卡 30
6 结论 31
致 谢 32
参考文献 33
引言
模具是基础工业的生产设备,模具技术就是生产技术。作为发展和振兴我国大力推手的模具行业,日益受到人们的关注和重视。模具工业的一个组成部分是属于高新技术产业,重要组成部分是装备工业。在每一个国家的模具一直享有“工业(百业)之母”,“重点行业”,“不可估量的电力行业”,“产业发展的全部秘密”,“效益放大器”等一系列的声誉。模具行业的现状是很重要的,而且在国民经济工业机械,石化,汽车,电子,建筑的五大支柱,需要相应的模具行业。在推行资源节约型社会的当今时代,塑料工业的强大也要求注塑模具的发展紧随其后,所以相关研究也逐步深入并实现实践。注塑模具的研究包含着产品材料、模具设计、模具制造,国内外研究学者投入的心血都转化成海量的文献,对注塑模具的发展有着承前启后的作用。
中国已成为承接工业发达国家模具业转移的良好目的地,随着国际交往的日益增多和外资在中国模具行业的投入日渐增加,中国压铸模具已与世界有着千丝万缕的联系。据相关专业人士分析,接下来的十年,中国的模具行业技术发展的主要方向如下:
(1)模具结构越来越大、复杂、精密、预期寿命增加
由于成型部件越来越大,高效率的生产要求的一模多腔的模具(如塑料模具已达到几百模腔),使模具体积越来越大,随着元件的小型化和不断发展,模具结构(例如进模工作位数增加,提高精度)的改善,精密模具增加了从5微米到2?3微米,在将来需要一些模具的精度容差为1μm或更小,这将促进超精密加工的发展。[1]








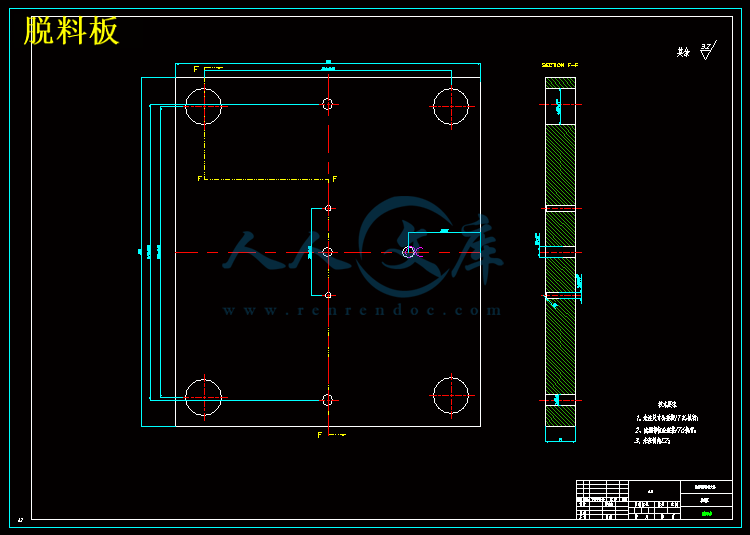

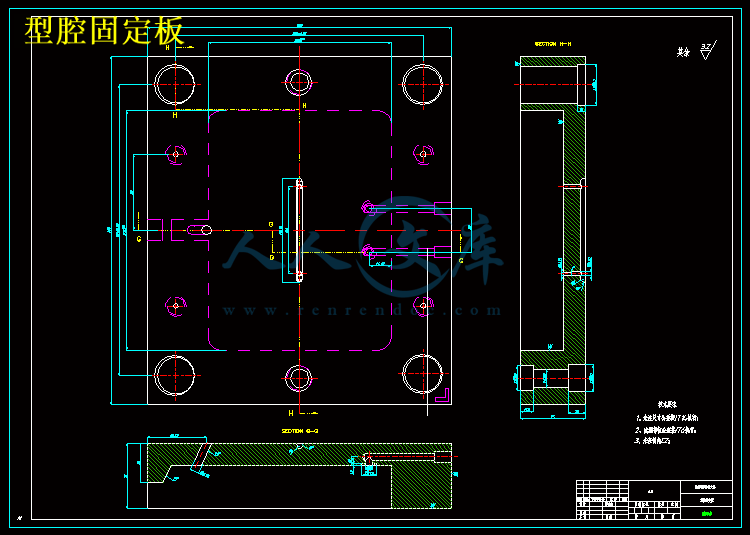
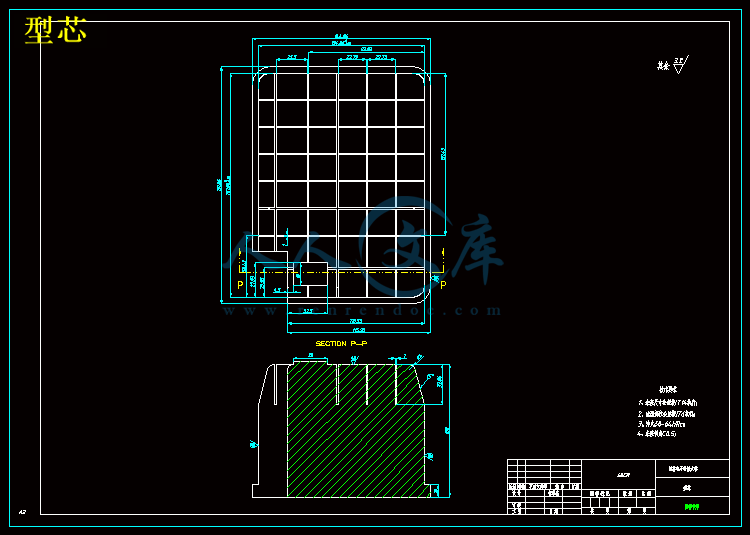
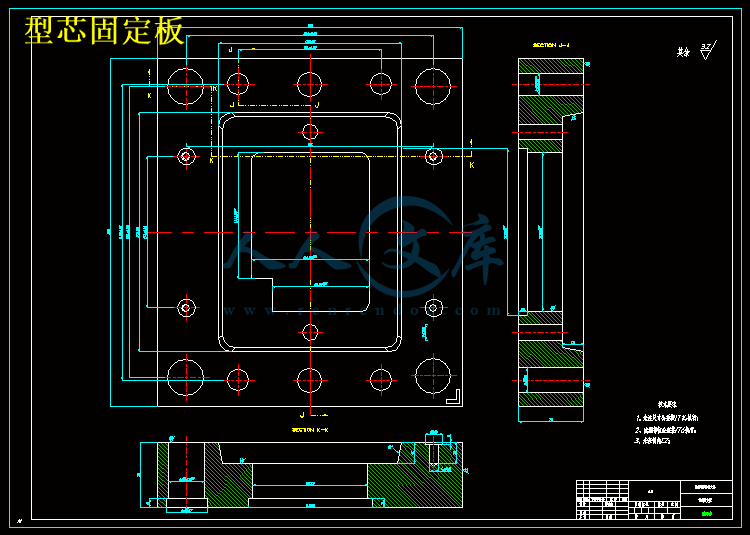
