序言
机械制造工艺课程设计是在我们完成了全部基础课、技术基础课、大部分专业课以及参加了生产实习之后进行的。这是我们在进行毕业设计之前对所学各课程的一次深入的综合性的复习,也是一次理论联系实际的训练,因此,它在我们四年的大学生活中占有重要的地位。
通过本次课程设计,应该得到下述各方面的锻炼:
1 能熟练运用机械制造工艺设计中的基本理论以及在生产实习中学到的实践知识,正确地解决一个零件在加工中的定位、夹紧以及工艺路线安排、工艺尺寸确定等问题,保证零件的加工质量。
2 提高结构设计的能力。通过设计夹具的训练,应当获得根据被加工零件的加工要求,设计出高效、省力、经济合理而且能保证加工质量的夹具的能力。
3 学会使用手册及图表资料。掌握与本设计有关的各种资料的名称、出处、能够做到熟练运用。
目 录
?
?
一、设计任务………………………………………………………………3
?
二、计算生产纲领、确定生产类型………………………………………3
?
三、零件的分析……………………………………………………………3
?
四、确定毛坯的制造方法、初步确定毛坯形状…………………………4
?
五、工艺规程设计………………………………………………………….5
?
1、定位基准的选择………………………………………………………...5
?
2、工件表面加工方法的选择………………………………………………5
?
3、制定工艺路线…………………………………………………………...6
?
4、确定加工余量、工序尺寸及毛坯尺寸,设计、绘制毛坯图…………..6
?
5、确定切削用量、基本工时(机动时间) ………………………………...7
?
六、夹具设计……………………………………………………………… 8
?
1、设计要求………………………………………………………..……….8
?
2、夹具设计的有关计算……………………………………………………8
?
3、夹具结构设计及操作简要说明………………………………. ……….8
4、夹具操作简要说明………………………………. …………………….9
七、总结…………………………………………………………………….10
八、参考文献……………………………………………………………….11
?
《一》零件作用及设计任务:
该换挡叉应用在汽车变速箱的换挡机构中。叉头以Φ15.8孔套在变速叉轴上,并以螺钉经M10孔与叉联结,叉脚夹在双联变换齿轮的槽中。当需要变速时,操纵变速杆,变速操纵机构就通过叉头的槽带动换挡叉与变速叉轴一起在变速箱中滑移,叉脚拨动双联变速齿轮在花键轴上滑动改变档位,从而改变汽车的行驶速度。
《二》计算生产纲领、确定生产类型:
变速换挡叉年产量5000,设其备品率为3%,机械加工废品率为0.5%,则该零件的年生产纲领为:N=Qn(1+3% )×(1+0.5% )=5000×1(1+3%)×(1+0.5%)=5176(件/年)。
换挡叉重量3kg,查1-3属于轻型零件,由表1-4知,该换挡叉生产类型为大量生产。
《三》换挡叉技术要求
加工表面 尺寸及偏差(mm) 公差及精度等级 表面粗糙度Ra 形位公差(mm)
叉脚两端面 5.90 -0.15 IT12 6.3
叉口两内侧面 5.1+0.1 0 IT12 6.3
Φ15.8内孔 15.8+0.043 +0.016 IT8 3.2
M10螺纹孔 M10×1 IT7
叉头凸台两端面 9.650 -0.25 IT12 6.3
叉头平台外表面 IT13 6.3
叉头平台凸面 11 IT13 12.5
叉头下表面 IT13 12.5
该变速器换挡叉结构简单,属于典型得叉杆类零件。为实现换挡、变速得功能,其叉轴孔和变速叉轴有配合要求,因此加工精度要求高。叉脚两端面在工作中需承受冲击载荷,为增强耐磨性,采用局部淬火,硬度为180HBS左右,为保证换挡叉换挡时叉脚受力均匀,要求叉脚两端面与孔Φ15.8垂直度要求为0.15mm。换挡叉用螺钉定位,螺纹孔为M10。
综上所述,该零件得各项技术要求制订较合理,符合在变速箱中得功用。
《四》审查换挡叉得工艺性
分析零件图可知,该换挡叉叉脚两端面厚度薄于连接的表面,但减少了加工面积,使用淬火处理提供局部的接触硬度。叉脚两端面面积相对较大,可防止加工过程中钻头钻偏,保证孔的加工精度及孔叉脚两端面的垂直度。其它表面加工精度较低,,通过铣削、钻床的粗加工就可达到加工要求;而主要工作表面虽然加工精度相对较高,但也可以在正常得生产条件下,采用较经济得方法保质保量地加工出来。可见该零件工艺性好。
《五》确定毛坯:
1.选择毛坯
由于该换挡叉在工作过程中承受冲击载荷,为增强强度和冲击韧度,获得纤维组织,毛坯选用锻模制作毛坯。拔模斜度为5°。
2.确定毛坯的尺寸公差和机械加工余量
公差等级
由换挡叉的功用和技术要求,确定该零件的的公差等级为普通级。
锻件重量
已知机械加工后换挡叉的重量为3kg,由此可初步估计机械加工前锻件毛坯的重量为3.5kg。
3.锻件形状复杂系数
对换挡叉零件图分析计算,可大概确定锻件外轮廓包容体的长度、宽度和高度,即l= 136mm,b= 76mm,h= 72mm,由公式2-3、2-5可计算出该换挡叉锻件的形状复杂系数
S=mt/mN=3.5/(136×76×72×7.8×10-6 kg/mm3 )=3.5/5.8=0.6
故属于S 2级。
4.锻件材质系数
由于该换挡叉材料为35钢,是碳的质量分数少于0.65%的碳素钢,故该锻件的材质系数属M 1级。
5.锻件分模线形状
根据该换挡叉的形位特点,以对称平分面为分模面,属平直分模线。
6.零件表面粗糙度
由零件图可知,该换挡叉各加工表面粗糙度Ra均大于等于3.2um。
由上查表可知锻件毛坯的尺寸公差及机械加工余量:
锻件重量/kg 包容体重量/kg 形状复杂系数 材质系数 公差等级
6 3.5 S 2 M 1 普通级
项目/mm 机械加工余量/mm 尺寸公差/mm 备注
厚度5.9 1.8+1.4 -0.4 表2-11
2.0~2.5 表2-13
宽度51 2.5+1.7 -0.8 表2-10
2.0~2.5 表2-13
宽度14.2 2.2+1.5 -0.8 表2-10
2.0~2.5 表2-13
孔径Φ15.8 2.2+1.5 -0.7 表2-10
2.0 表2-14
中心距 ±0.5 表2-12
《六》拟定工艺路线
1.定位基准选择
精基准选择:
根据该零件的技术要求和装配要求,选择叉头轴孔和叉脚右端面作为精基准,零件上很多表面可用它们作基准。轴孔Φ15.8是设计基准,与用作精基准保证被加工表面的垂直度要求。该零件刚性差,夹紧力作用在叉脚右端面上。
粗基准选择:
作为粗基准的表面应平整,没有飞边、毛刺或其他表面缺欠。选择轴孔Φ15.8的外圆和叉脚左端面作粗基准保证孔的壁厚均匀。采用叉脚左端面作粗基准加工左端面,可为后续工序准备好精基准。
2.表面加工方法确定
根据换挡叉零件图各加工表面的尺寸精度和表面粗糙度,确定加工件各表面的加工方法:
加工表面 尺寸精度等级 表面粗糙度Ra 加工方案 备注
叉脚两端面 IT12 6.3 粗铣-半粗铣 表1-8
叉口内侧面 IT12 6.3 同上 表1-8
Φ15.8孔 IT8 3.2 钻-扩-铰 表1-8
M10 钻-攻螺纹 表1-10
叉头凸台两端面 IT12 6.3 粗铣 表1-8
叉头凸台外表面 IT13 12.5 粗铣 表1-8
叉头凸台槽 IT12 12.5 粗铣 表1-7
3.加工阶段的划分
该零件加工质量要求一般,可将加工分为粗加工,半精加工和精加工。
粗加工时,先将精基准准备好,使后续工序都可采用精基准定位加工,保证精度要求,然后粗铣叉脚左端面,叉口内侧面,叉头凸台两端面,叉头凸台外表面,凸台槽和M10螺纹底孔。半精加工,完成叉脚两端面,叉口内侧面,攻螺纹,扩Φ15.8孔。精加工时,铰孔Φ158。
4.工序的集中与分散
该零件生产类型为大批生产,可采用万能型机床配以专用工、夹具,以提高生产率,而且运用工序集中原则使工序的装夹次数少,不但可缩短辅助时间,而且由于在一次装夹中加工了许多表面,有利于保证各加工表面间相对位置精度要求。
5. 工艺路线
(1)机械加工工序
先加工精基准——叉头轴孔和叉脚右端面。
先粗加工,后精加工。
先加工主要表面——叉脚右端面,叉头轴孔Φ15.8,叉头凸台槽。后加工叉口内侧面,叉头凸台两端面,攻螺纹。
先加工叉脚右端面,再加工叉头轴孔Φ15.8。
(2)热处理工序
锻模成形后,切边,进行调质,硬度185HBS。叉脚两端面在粗加工完后进行局部高频淬火,提高其耐磨性和在工作中承受冲击载荷的能力。
(3)辅助工序
粗加工叉脚两端面和热处理后,安排教直工序:半精加工后,安排去毛刺和中间检验工序;精加工后,安排去毛刺、清洗和终检工序。
综上所述,该换挡叉工序安排顺序:正火——基准加工——主要表面粗加工、一些余量大的表面粗加工及次要表面粗加工——热处理——主要表面半精加工——主要表面精加工。
《七》加工余量、工序尺寸和公差的确定
本工序为钻M10的螺纹底孔Φ8.4,孔深少于5mm,位置精度一般,可采用一次走刀加工。钻孔:Φ8.4±15mm。
《八》切削用量、时间定额的计算
工序:钻螺纹底孔
(1)背吃刀量确定 a p=4.2mm。
(2)进给量确定 由表5-1得 f=0.20mm/r.
(3)钻削速度的计算 由表5-21 得 v=24m/min。由公式n=1000v/πd得钻头转速n=909.9r/min。由表4-9得,选用立式钻床Z525,主轴转速n=960r/min。
则切削速度v=nπd/1000=25.3m/min。
时间定额计算:
由表5-41得钻孔的基本时间公式:t j=L/fn=(l+l 1+l 2)/fn.。
l=5.2;l 1=Φcotκ r/2+(1~2)=8.4cot(118/2)/2+(1~2)=3.5~4.5;l 2=1~4。
所以 t j=0.06min=3.6s。
辅助时间: t f=(0.15~0.2)t j=0.65s。
其它时间: t b+t x=6%×(t j+ t f)=0.26s。
单件时间计算:t=3.6+0.65+0.26=4.51s。
专用钻床夹具设计
《一》夹具设计任务
已知工件材料为35钢,毛坯为模锻件,所用机床为Z525型立式钻床,大批生产规模。试为该工序设计一钻床夹具。
《二》确定夹具的结构方案
(1)确定定位元件
选用一面两销,心轴和工件孔配合,限制四个自由度。削边销与叉脚内侧面接触,限制一个自由度。偏向轮与工件槽夹紧定位,限制一个自由度,实现工件正确定位。对于工序尺寸3.1±0.1,定位误差△ dw=0.1。该定位方案可行。
(2)确定导向装置
本工序要求对加工孔进行钻一个工步的加工,生产类型为大批生产,选用可换钻套作为刀具的导向元件。
(3)确定夹紧机构
针对大批生产,选用偏向轮夹紧机构。
(4) 夹紧力计算


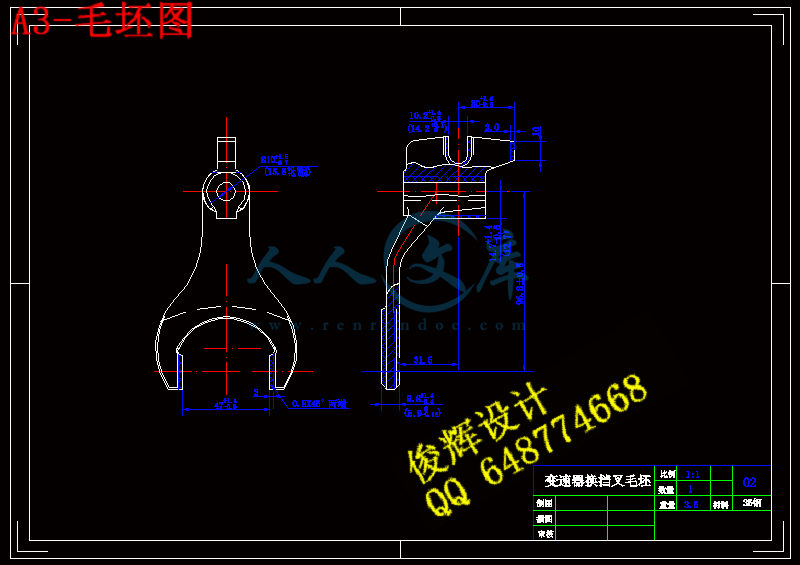

