摘 要
在这几周时间里,我们进行了机械制造加工工艺设计及夹具设计。机械设计制造基础课程设计是在学完了机械制造基础课(含机床夹具设计)和大部分专业课(材料力学、机械原理等),并在进行了生产实习的基础上进行的一个教学过程。这次设计使我们能综合运用机械制造工艺学中的一些基本理论,并结合生产实习中学到的一些实践知识,独立地分析和解决工艺上的问题。初步具备了设计一个中等复杂程度零件(气门摇杆轴支座)的工艺规程的能力和运用夹具设计的基本原理和方法,制订夹具设计方案,完成夹具结构设计的能力,也是熟悉和运用相关手册,图表等技术资料及编写技术文件技能的一次难得的实践机会,为今后的毕业设计及未来从事的工作奠定良好的基础。
由于所掌握的知识不全面且能力所限,经验不足,设计中还有许多不足之处,希望各位老师多加指导
关键词:气门摇杆 夹具
目 录
摘 要 I
第1章 零件的工艺分析 1
1.1零件的功能、结构及生产类型的确定 1
1.1.1零件的作用 1
1.1.2 零件的工艺分析 1
1.1.3 零件的生产类型 2
第2章 毛坯的选择 3
2.1确定毛坯的类型、制造方法和尺寸及其公差 3
2.2毛坯的技术要求 3
第3章 基准的选择 4
3.1粗基准的选择 4
3.2精基准的选择 4
第4章 制订工艺路线 5
4.1确定各加工面的加工方法 5
4.2拟定加工工艺路线 6
4.2.1工艺路线方案1 6
4.2.2工艺路线方案2 7
4.3工艺方案的比较与分析 7
第5章 工序设计 9
5.1工序12 的尺寸链计算 9
5.2机械加工余量、工艺尺寸及毛坯尺寸的确定 11
5.3切削余量及基本工时的确定 11
5.3.1 机械加工余量确定 11
5.3.2确定切削用量及基本工 12
第6章 铣端面夹具设计 16
6.1确定设计方案 16
6.2定位原理图: 17
6.3定位误差分析 17
6.4夹紧力计算 18
设计心得 20
参考文献 21
附录 22
第1章 零件的工艺分析
1.1零件的功能、结构及生产类型的确定
1.1.1零件的作用
气门摇杆轴支座是柴油机一个主要零件。是柴油机摇杆座的结合部孔装摇杆轴,轴上两端各装一进气门摇杆,摇杆座通过两个孔用螺杆与汽缸盖相连,轴向槽用于锁紧摇杆轴,使之不转动。其零件图如下图:
图1.1 摇杆轴支座
1.1.2 零件的工艺分析
由图1.1得知,其材料为。该材料具有较高的强度,耐磨性,耐热性及减振性,适用于承受较大应力,要求耐磨的零件。 该零件上主要加工面为上端面,下端面,左右端面,孔和以及轴向槽的加工孔的尺寸精度以及下端面的平面度与左右两端面孔的尺寸精度,直接影响到进气孔与排气门的传动精度及密封,孔的尺寸精度,以上下两端面的平行度。因此,需要先以下端面为粗基准加工上端面,再以上端面为粗基准加工下端面,再把下端面作为精基准,最后加工孔时以下端面为定位基准,以保证孔轴相对下端面的位置精度。
1.1.3 零件的生产类型
依照设计题目可知:该零件的生产纲领为件/年,查表可知生产类型是大批量生产。
第2章 毛坯的选择
2.1确定毛坯的类型、制造方法和尺寸及其公差
毛坯的铸造方法选用砂型机器造型。此外,为消除残余应力,铸造后安排人工时效处理。由<<机械加工工艺手册>>2—12可知该种铸造公差等级为,级。
2.2毛坯的技术要求
(1) 铸件必须经过时效处理;
(2) 铸件不得有气孔、砂眼等铸造缺陷。
第3章 基准的选择
基准的选择是工艺规程设计中的重要工作之一。基准面的选择是否真确与合理关系到零件的加工质量,以及生产效率的高低。如果选择不当,在加工过程中出现很多问题,更可能造成零件的大批报废使生产无法进行。
3.1粗基准的选择
选择零件的重要面和重要孔做基准。在保证各加工面均有加工余量的前提下,使重要孔或面的加工余量尽量均匀,此外,还要保证定位夹紧的可靠性,装夹的方便性,减少辅助时间,所以粗基准为上端面。
3.2精基准的选择
气门摇杆轴支座的下端面既是装配基准又是设计基准,用它作为精基准,能使加工遵循基准重合的原则。孔及左右两端面都采用底面做基准,这使得工艺路线又遵循“基准统一”的原则,下端面的面积比较大,定位比较稳定,夹紧方案也比较简单,可靠,操作方便。
第4章 制订工艺路线
4.1确定各加工面的加工方法
上下端面:粗铣—精铣
左右端面:粗铣—精铣
端面:粗铣—精铣
孔:钻孔
孔:钻孔—粗镗—精镗
轴向槽—精铣
因左右两端面均对孔有较高的位置要求,故它们的加工宜采用工序集中原则,减少装次数,提高加工精度。根据先面后孔原则,将上端面下端面的粗铣放在前面,左右端面上孔放后面加工。
4.2拟定加工工艺路线
制订工艺路线的出发点,应当是使零件的几何尺寸形状,尺寸精度位置精度等技术要求能得到合理的保证。
4.2.1工艺路线方案1
加工路线方案
工序号 工序内容
铸造
时效
涂漆
车上端面
铣下端面
钻两通孔
铣左右端面
钻通孔
镗孔
轴向槽
铣检验
入库
4.2.2工艺路线方案2
以V形块定位的加工路线方案
工序号 工序内容
铸造
时效
涂漆
粗铣上下端面
精铣上下端面
钻两通孔
钻两通孔的螺纹
粗铣左右端面
精铣左右端面
钻孔
镗孔
铣轴向槽
清洗
入库
4.3工艺方案的比较与分析
上述两个方案遵循了工艺路线拟订的一般原则,但某些工序还有一些问题还值得进一步讨论。
车上端面,因工件和夹具的尺寸较大,在卧式车床上加工时,它们惯性力较大,平衡困难;又由上端面不是连续的圆环面,车削中出现断续切削容易引起工艺系统的震动,故应当选择铣削加工。
因为在零件图纸中要求左右端面的跳动度为,所以需要同时铣削左右端面,保证两端的平行度。
工序应在工序25前完成,使上端面在加工后有较多的时间进行自然时效,减少受力变形和受热变形对通孔加工精度的影响。综上所述选择方案二。
最后确定的工件加工工序如下:
序号 工序内容 定位基准
铸造
时效
涂漆
粗铣下端面 上端面(3)+左右端(3)
粗铣上端面 下端面(3)+左右端(3)
粗铣左右端面 下端面(3)+ 外圆柱面
钻两通孔 下端面(3)+ 外圆柱面
精铣下端面 上端面(3)+左右端(3)
精铣上端面 下端面(3)+左右端(3)
精铣左右端面 下端面(3)+ 外圆柱面
钻通孔 下端面(3)+ 两通孔(3)
镗孔到 下端面(3)+ 两通孔(3)
粗-精铣轴向槽 下端面(3)+ 外圆柱面
入库
第5章 工序设计
5.1工序12 的尺寸链计算
加工过程为:
1)铣右端面
2)钻通孔,保证工序尺寸
3)粗镗,保证工序尺寸
4)精镗,保证工序尺寸,达到零件设计尺寸D 的要求,
5)倒角
如图,可找出工艺尺寸链
求解工序尺寸及公差的顺序如下:
(1)从图知,=
(2)从图知,,其中 是精镗的余量,,则 ,由于工序尺寸p2 是在粗镗中保证的,查参考资料(5)中表
知,粗镗工序的经济加工精度等级为,因此确定该工艺尺寸公差为,
其公差值为,故;
(3)从图所示的尺寸链知, 其中 为粗镗的余量,,,查参考资料(5)中表 知,确定钻削工序的经济加工精度
等级为,其公差值为故。
为验证确定的工序尺寸及公差是否合理,还需对加工余量进行校核。
(1)余量的校核,在图b 所示的尺寸链里Z2是封闭环,故
(2)余量的校核,在图a 所示的尺寸链中Z1是封闭环,故
余量校核结果表明,所确定的工序尺寸公差是合理的。
将工序尺寸按“入体原则”表示:,
,
。
5.2机械加工余量、工艺尺寸及毛坯尺寸的确定
因工件的生产类型为成批生产,毛的铸造方法选用砂型机器造型。根据<<机械加工工艺手册>>表确定各表面的加工余量如下表所示:
表 各表面加工余量
加工表面 基本尺寸 加工余量等级 加工余量数值 说明
上端面 单侧加工
下端面 单侧加工
左端面 单侧加工
右端面 单侧加工
5.3切削余量及基本工时的确定
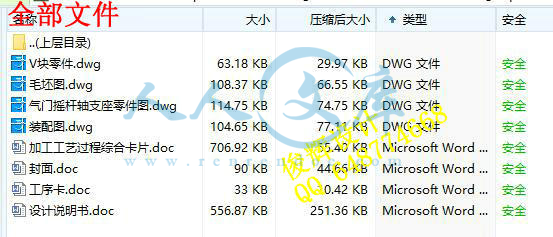



