摘 要
在机械制造的机械加工,检验,装配,焊接和热处理等冷热工艺过程中,使用着大量的夹具,用以安装加工对象,使之占有正确的位置,以保证零件和工件的质量。
本次设计主要是进行填料箱盖零件的专用夹具的设计,是对我们以往所学知识的总结和对我们所掌握知识的一次扩展。本文主要从工艺规程的指定与夹具的设计两方面出发。根据零件本身的特点,生产类型以及零件在具体工作时的作用选择工艺规程和夹具。在工艺规程方面:确定生产类型,综合考虑其准确度高,生产效率高,消耗经济少等方面,选择一个最优方案;在夹具设计方面,因为是盖体类零件,加工孔,选择钻床加工,考虑诸多因素拟订最优方案,最终完成本次设计。
Abstract
While the machining, checkout, assemblage, jointing and heat treatment in manufacture, masses of clamps have been made use of to fix the manufacturing objects in order to guarantee the quality of accessories and work pieces.
In this engineering, the main aim is to engineer the special clamp of the cover part of the stuffing box, which can summarize the knowledge we have learned and extend the knowledge we have known. This article sets out from two parts: the setting down of the technical schedule and the engineering of the clamp. The technical schedule and the clamp are chose depended on the character of the part itself, the types of manufacturing and the function while working. While ascertaining the technical schedule, choose the optimal case after taking the high precision, the high productivity and the low cost in economy into consideration. While engineering the clamp, by the reason of the type of the part, machining the aperture in size , and choosing the drill press for machining, consider all the conditions above and draft the optimal project, and then finish the engineer.
目录
1 零件的分析 1
1.1 零件的作用 1
1.2 零件的工艺分析 1
2 机械加工工艺规程设计 1
2.1 毛坯的制造形式 1
2.2 基准面的选择 1
2.2.1 粗基准的选择 2
2.2.2 精基准的选择 2
2.3 制订工艺路线 2
2.4 机械加工余量、工序尺寸及毛坯尺寸的确定 3
2.5 确定切削用量 4
2.5.1 工序Ⅰ:车削端面、外圆 4
2.5.2 工序Ⅱ:粗车外圆以及槽和倒角 5
2.5.3工序Ⅲ 钻扩及孔。Z3025摇臂钻床 7
2.5.4 工序Ⅳ 钻深孔深24 8
2.5.5 工序Ⅴ:精车的外圆及与相接的端面 10
2.5.6工序Ⅵ:精、粗、细镗孔 12
2.5.7 工序Ⅶ:铣孔底面 13
2.5.8 工序Ⅷ:磨孔底面 13
2.5.9工序Ⅸ: 镗孔底沟槽 14
2.5.10 工序Ⅹ: 研磨孔底面 14
3指定工序的专用机床夹具设计 14
3.1 问题的指出 14
3.2 夹具设计 14
3.2.1 定位基准的选择 14
3.2.2 切削力及夹紧力的计算 14
3.3 定位误差的分析 16
3.4 夹具设计及操作的简要说明 16
4.方案综合评价与结论 16
5. 本次课程设计体会与展望 16
参考资料 17
1 零件的分析
1.1 零件的作用
题目所给定的零件是填料箱盖,其主要作用是保证对箱体起密封作用,使箱体在工作时不致让油液渗漏。
1.2 零件的工艺分析
填料箱盖的零件图中规定了一系列技术要求:
1.以轴为中心的加工表面。
包括:尺寸为的轴,表面粗糙度为, 尺寸为的轴与相接的肩面, 尺寸为与同轴度为的面。尺寸为与同轴度为的孔。
2.以孔为中心的加工表面.
尺寸为与垂直度为的孔底面,表面粗糙度为,须研磨。
3. 以孔为中心均匀分布的孔,,,孔深及。
4.其它未注表面的粗糙度要求为,粗加工可满足要求
2 机械加工工艺规程设计
2.1 毛坯的制造形式
零件材料为,考虑到零件材料的综合性能及材料成本和加工成本,保证零件工作的可靠,采用铸造。生产类型:中批或大批大量生产。
2.2 基准面的选择
基面的选择是工艺规程设计中的重要工作之一。也是保证加工精度的关键。
2.2.1 粗基准的选择
对于一般轴类零件而言,以外圆作为粗基准是完全合理的。按照有关的粗基准选择原则(保证某重要表面的加工余量均匀时,选该表面为粗基准。若工件每个表面都要求加工,为了保证各表面都有足够的余量,应选择加工余量最小的表面为粗基准。)
2.2.2 精基准的选择
按照有关的精基准选择原则(基准重合原则;基准统一原则;可靠方便原则),对于本零件,有中心孔,可以以中心孔作为统一的基准,但是随着孔的加工,大端的中心孔消失,必须重新建立外圆的加工基面,一般有如下三种方法:
1.当中心孔直径较小时,可以直接在孔口倒出宽度不大于的锥面来代替中心孔。若孔径较大,就用小端孔口和大端外圆作为定位基面,来保证定位精度。
2.采用锥堵或锥套心轴。
3.精加工外圆亦可用该外圆本身来定位,即安装工件时,以支承轴颈本身找正。
2.3 制订工艺路线
工艺路线确定如下:
工序Ⅰ 车削左右两端面。
工序Ⅱ 粗车外圆及倒角。
工序Ⅲ 钻孔、扩,扩孔。
工序Ⅳ 钻孔,,孔深24的孔及攻螺纹。
工序Ⅴ 精车外圆及与相接的端面.
工序Ⅵ 粗、精、细镗孔。
工序Ⅶ 铣孔底面。
工序Ⅷ 磨孔底面。
工序Ⅸ 镗孔底面沟槽。
工序Ⅹ 研磨孔底面。
工序Ⅺ 终检。
以上工艺过程详见机械加工工艺过程卡片。
2.4 机械加工余量、工序尺寸及毛坯尺寸的确定
“填料箱盖”零件材料为钢,硬度为,毛坯质量约为,生产类型为中批生产,采用机器造型铸造毛坯。
根据上述材料及加工工艺,分别确定各加工表面的机械加工余量、工序尺寸及毛坯尺寸如下:
1外圆表面考虑到尺寸较多且相差不大,为简化铸造毛坯的外形,现直接按零件结构取为的阶梯轴式结构,除以外,其它尺寸外圆表面粗糙度值为,只要粗车就可满足加工要求。
2外圆表面沿轴线长度方向的加工余量及公差。查《机械制造工艺设计简明手册》(以下简称《工艺手册》表2.2-1,铸件轮廓尺寸(长度方向>100~160mm,故长度方向偏差为.长度方向的余量查表2.2-4,其余量值规定为.现取。
3毛坯为实心。两内孔精度要求自由尺寸精度要求,为6.3,钻孔再扩孔即可满足要求。
4内孔)。要求以外圆面定位,铸出毛坯孔。
5 孔底面加工。
按照《工艺手册》表2.3-21及2.3-23
研磨余量 取
磨削余量 取
铣削余量
6).底面沟槽.采用镗削,经过底面研磨后镗可保证其精度。
7) 孔及孔、孔。均为自由尺寸精度要求。
2.5 确定切削用量
2.5.1 工序Ⅰ:车削端面、外圆
本工序采用计算法确定切削用量
加工条件:工件材料:,铸造。
加工要求:粗车、端面及
外圆,表面粗糙度值为。
机床:C620—1卧式车床。
刀具:刀片材料为,刀杆尺寸为,,计算切削用量:
1)粗车两端面
确定端面最大加工余量:已知毛坯长度方向单边余量为,则毛坯长度方向的最大加工余量为,分两次加工,计。长度加工方向取级,取。确定进给量:根据《切削用量简明手册》(第三版)表1.4,当刀杆, 时,以及工件直径为时。
按C620—1车床说明书(见《切削手册》表1.30)取计算切削速度: 按《切削手册》表1.27,切削速度的
计算公式为:
,,,。修正系数见《切削手册》表1.28,即
, , , ,
所以
确定机床主轴转速
按机床说明书(见《工艺手册》表4.2—8)与相近的机床转速
选取。实际切削速度
2) 粗车端面
确定机床主轴转速:
转速选取。实际切削速度
2.5.2 工序Ⅱ:粗车外圆以及槽和倒角
1)切削深度:先车至以及车至。
进给量: 见《切削手册》表1.4





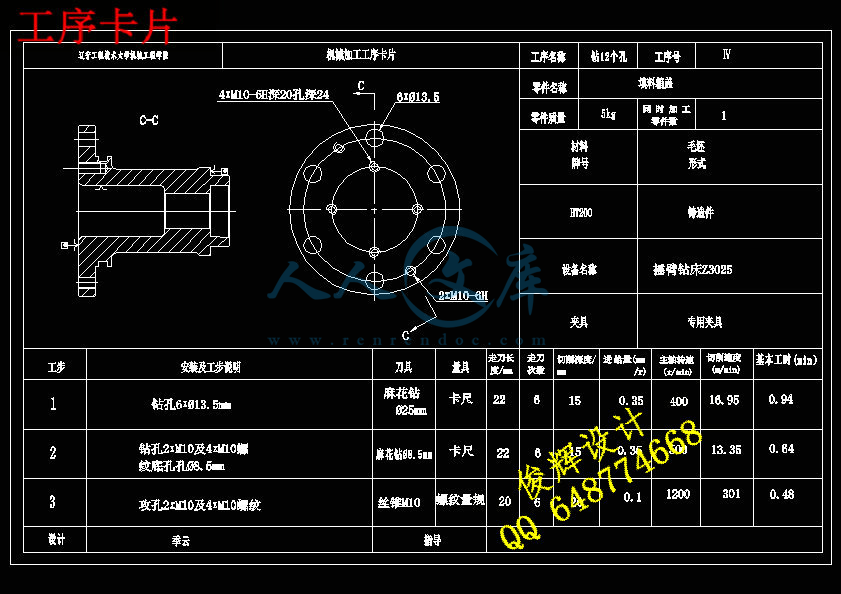