小连杆加工工艺及钻2-φ7.94孔夹具设计【4张CAD图纸、工艺卡片和说明书】
收藏
资源目录
压缩包内文档预览:
编号:1148468
类型:共享资源
大小:509.71KB
格式:ZIP
上传时间:2017-04-11
上传人:俊****计
认证信息
个人认证
束**(实名认证)
江苏
IP属地:江苏
15
积分
- 关 键 词:
-
连杆
加工
工艺
夹具
设计
cad
图纸
卡片
以及
说明书
仿单
- 资源描述:
-
目 录
摘 要……………………………………………………………………………I
Abstract …………………………………………………………………………II
绪论 …………………………………………………………………………… 1
第1章 零件工艺的分析………………………………………………………2
1.1 零件的分析……………………………………………………………2
1.1.1 零件作用的分析 …………………………………………… 2
1.1.2 零件的工艺性分析……………………………………………2
1.2 工艺规程设计…………………………………………………………2
1.2.1 确定毛坯的制造形式…………………………………………2
第2章 拟定零件加工的工艺路线…………………………………………… 3
2.1 定位基准的选择………………………………………………………3
2.1.1精基准的选择…………………………………………………3
2.1.2粗基准的选择…………………………………………………3
2.2 加工路线的拟定……………………………………………3
第3章 机械加工余量及工序尺寸的确定…………………………………… 6
3.1 选择刀具…………………………………………………………… 6
3.2 选择量具………………………………………………………………6
3.3 确定工序尺寸及加工余量………………………………………… 6
第4章 专用夹具的设计………………………………………………………9
4.1 斜钻孔专用夹具…………………………………………………… 9
4.2 钻铰两个φ7.94孔专用夹具…………………………………………9
总 结…………………………………………………………………………… 10
致 谢…………………………………………………………………………… 11
参考文献 ……………………………………………………………………… 12
绪 论
机械制造业是一个古老而永远充满生命力的行业,“机械制造工艺”和“机床夹具设计”毕业设计是机械类专业学生的重要实践性环节之一。这次设计是我们在学习完了大学的全部基础和专业课程之后进行的。这是我们在走入社会,走上工作岗位之前对所学的课程的一次深入的综合性的复习,是一次理论联系实际的训练,也是我们大学的全部所学的考察。
就个人而言,我希望通过这次毕业设计对自己将来从事的工作进行一次适应性的训练,从中锻炼自己处理生产工艺问题的能力,掌握机械加工工艺规程设计和机床夹具设计的方法,从而进一步巩固有关的理论知识,提高独立工作的能力,为将来从事专业技术工作打好基础。当然,无法期望通过一次毕业设计就成为合格的工程师,但起码可以籍此领略机械设计专业的大概,为今后参加工作打好基础。
由于能力有限,设计尚有许多不足之处,请各位评申老师给予指正。
第1章:零件工艺的分析
1.1零件的分析
1.1.1 零件作用的分析
题目所给的零件典型零件的一种——连杆。连杆在机械运动中起着传递动力和连接运动的重要作用。其在各类机械中都有着广泛的应用,如:车辆的转向连接处、起重机的推杆等等,而且他还可以承受一定的拉力,具有良好的平均载荷的能力。连杆的截面积很小 但是,却可以传递很大的力,且加工简单,因此,在传递动力的场合大多选用连杆机构。
1.1.2 零件的工艺性分析
连杆结构总共有两类加工表面。现分述如下:
(1)两连接头处的平面,,即图中尺寸8和尺寸14两个厚度以及期间的距离11-0.150 都是在加工两端面的过程中要考虑到的。其中尺寸线都出自小端的一边可以将该面作为端面加工的基准从而对与其相联系的相关尺寸进行控制及验收。
(2) 两个主要受力面即两个∮7.94+0.0160的孔,两个孔是本零件的关键尺寸,和其位置尺寸39.5±0.1需首要保证的。以它们为基准加工其他部分才能保证本件的正确性。再就是三个润滑孔Ф1、∮2.5、∮3.7和M3.5×0.35-6H。
由以上分析知道:对于这两组加工面而言,可以先半精加工其中两个∮7.94+0.0160的面,找到该零件的精基准,然后借助于专用的夹具加工另一组表面,和打润滑孔,从而保证它们之间的位置精度要求。
1.2 工艺规程设计
1.2.1 确定毛坯的制造形式
零件材料为HT200,零件为连杆用来承受一定的拉压力并且受变换的载荷,再者考虑其生产纲领为大批大量,而且它的内外形状亦非太复杂,而且外型尺寸不大。故选用金属型浇注成型,其大体形状铸出,这对节约成本,保证质量也是有利的。
第2章:拟定零件加工的工艺路线
2.1 定位基准的选择
定位基准有粗基准和精基准只分,通常先确定精基准,然后确定粗基准。
2.1.1精基准的选择
精基准的选择应重保证零件的加工精度,特别是加工表面的相互位置精度来考虑,同时也要考虑到装夹方便,夹具结构方便。选择精基准应遵循下列原则:
①“基准重合”原则 即应尽可能选用设计基准作为精基准。这样可以避免由于基准不重合而引起的误差。
②“基准统一”原则 即应尽可能选择加工工件的多个表面时都能使用的一组定位基准作为精基准。这样就便于保证各加工表面的相互位置精度,避免基准变换说产生的误差,并能简化夹具的设计制造。
③“互为基准”原则 当两个表面相互位置精度以及他们自身的尺寸与形状精度都要求很高时,可以采取互为基准的原则,反复多次进行加工。
④“自为基准”原则 有些精加工或光整加工工序要求加工余量小而均匀,再加工时就应尽量选择加工表面本身作为精基准,而该表面与其他表面之间的位置精度则有先行工序保证。
2.1.2粗基准的选择
粗基准的选择主要影响不加工表面与加工表面的相互位置精度,以及加工表面的余量分配。选择粗基准时必须注意以下几个问题:
① 如果必须首先保证工件上加工表面与不加工表面之间的位置精度要求,应以不加工表面作为粗基准。如果工件上由很多不需加工的表面,则应以其中与加工表面的位置精度要求较高的表面作为粗基准。
② 必须首先保证工件上的某种要表面的加工余量均匀,则应选择该表面作为粗基准。
③ 选作粗基准的表面应尽量平整光洁,不应有飞边、浇口、冒口等缺陷。
④ 粗基准一般只能使用一次。
2.2 加工路线的拟定
拟定机械加工工序,要依照“先粗后精”“先主后次”,“先面后孔”加工连杆零件的原则。必要的热处理、检验等辅助工序安排在各加工阶段之间。
加工阶段的划分
(1) 粗基准的选择 按有关原则(当零件有不加工表面时,应该以不加工表面做粗基准,若零件有若干不加工表面时,则应该以与加工表面要求相对位置精度要求较高的不加工表面为粗基准),现取宽度为8处的一端为粗基准定位。
(2) 精基准的选择 按照有关的精基准选择原则(基准重合原则;基准统一原则;可靠方便原则)由基准重合原则取宽度为8的∮7.94+0.0160的中心线为精基准定位。
工艺规程的设计:
本零件的加工有内孔、端面、外圆以及螺纹材料为HT200,针对本零件现对各个加工面选择如下的加工方法:
1、∮7.94+0.0160 mm的内孔面,经查∮7.94H7上偏差+0.015下偏差0与本要求差0.001,对于一般的机械传动可以忽略这点误差,将其表面粗糙度定为1.6,这在一般的配合面中也足够使用,针对这种小孔径,无法用车、镗的方法实现,故此处可选择先钻孔然后在精铰的方法;
2、两头的四个端面 端面加工一般的选择是铣削或者车刨削,这里本零件的加工端面非常的小,铣削或者刨削加工端面的优点难以发挥,故本处选用车削的方法,因其两面必定与其他表面接触、配合,所以定其表面粗糙度值为6.3,以满足一般表面的相互作用;
3、外圆止口∮10台阶 对于外回转表面我们选择的加工方法一般是车削。本工位尺寸输未注公差,可选择粗车,表面粗糙度值取12.5。
4、∮1、∮2.5、∮3.7等孔 考虑这些孔的作用是润滑孔其位置和尺寸精度的要求并不高,可用钻床一次钻出,表面粗糙度值取12.5。
5、螺纹孔M3.5×0.5-6H 螺纹很小且深度也很小,可以考虑手工攻丝。
制定工艺路线:
由于大批大量的生产,故采用专用的夹具及尽量使工序集中来提高生产率,以降低成本。
(1)工艺路线方案一
工序 1 粗车大头端和小头端4个端面;
工序 2 钻内孔Ф7.94;
工序 3 精车大头端和小头端4个端面,车外圆Ф10;
工序 4 钻Ф2.5、Ф3.7孔;钻Ф1孔;
工序 5 铰内孔Ф7.94及倒角;
工序 6 攻M3.5×0.5-6H;
工序 7 去毛刺,终检。
(2)工艺路线方案二
工序 1 划线,找孔Ф7.94中心;
工序 2 钻内孔Ф7.94;
工序 3 车外圆Ф10及其端面;
工序 4 精车大头端和小头端4个端面;
工序 5 划润滑孔线;
工序 6 钻Ф2.5、Ф3.7孔;钻Ф1孔,;
工序 7 打M 3.5×0.5孔并攻丝;
工序 8 铰内孔Ф7.94及倒角;
工序 9 去毛刺,终检。
以上加工方案大致看来还是合理的,但通过相互比较来看,方案一:虽然,首先保证了两个关键孔的垂直度但是却无法确定基准空的中心位置,从而得在另一工序中才能加工确定四个端面和外圆止口的尺寸;方案二:先确定了两个关键孔的位置,接着精加工其位置精度,也可以保证他的垂直度,同时也更满足设计基准和工艺基准统一的原则。为了更好的保证加工精度和节约成本,现选用第二套工艺方案加工该零件。
第3章:机械加工余量及工序尺寸的确定
3.1 选择刀具
本零件粗加工孔的时候可以使用硬质合金麻花钻;
粗车外圆的时候使用硬质合金外圆车刀
粗车及精车端面和止口端面的时候使用硬质合金端面车刀
攻M3.5×0.5螺纹的时候使用手用丝锥。
3.2 选择量具
本零件属于成批生产,一般采用通用的量具。选择量具的方法有两种:一、按计量器具的不确定度选择;二、按计量器具的测量方法极限误差选择;选择时采用其中的一种方法即可。
在测定两端面的距离值和其相对位置时,可选用游标卡尺,因为其相对位置尺寸110-0.15,可选用分度值为0.02mm的卡尺,同时,该卡尺还可以测量Ф10外圆的自由公差和尺寸值39.5±0.1的距离值。
测量内孔的时候,因为Ф7.94的孔经过了钻,铰两道工序,所以在粗加工时可以使用内径百分尺测量,分度值为0.02mm,铰孔后可以选用合适孔径的圆柱塞规。
3.3 确定工序尺寸及加工余量
确定工序尺寸的一般方法是:由加工表面的最后工序往前推算,最后工序的尺寸按零件图样的要求标注,当无基准转换时,同一表面多次加工的工序尺寸只与工序(或工步)的加工余量有关。当基准不重合的时候,工序尺寸应该由工艺尺寸链来解出。
孔Ф7.94的工序尺寸 钻Ф7.5±0.05,铰孔至∮7.94+0.0160 mm
端面尺寸 小端 毛坯厚度11加工至8
大端 毛坯厚度17加工至14
本零件的外圆表面需要加工的很少,故其两头四个端面的加工余量定为单边1.5;内孔划线后钻出。
确定切削用量以及基本工时
工序2 根据划线确定的位置钻孔Ф7.94至Ф7.5
(1) 加工条件:HT200铸件
加工要求:钻
机床:Z 512台式钻床
刀具: 硬质合金锥柄麻花钻(GB10946-89)


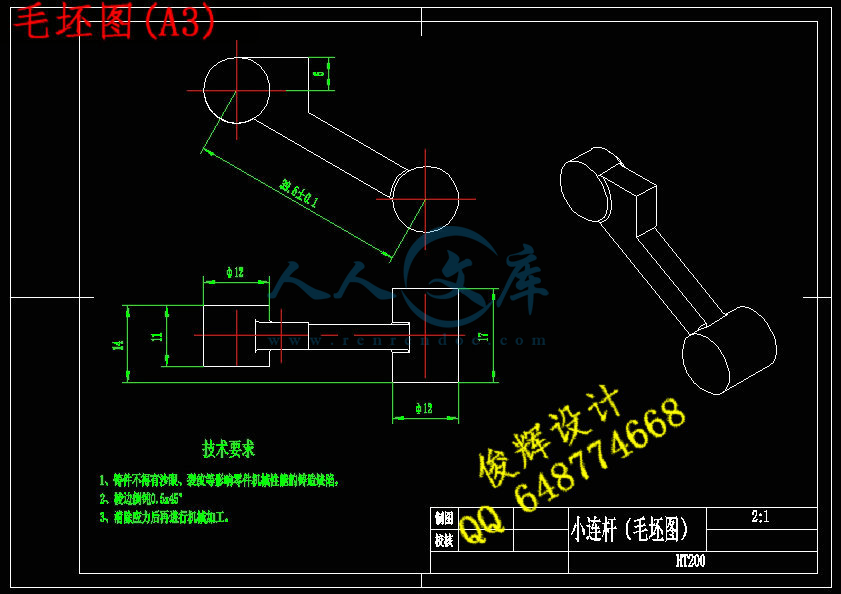


- 内容简介:
-
1 机械加工工序卡片 工厂 机械加工工序卡片 产品型号 零件图号 共 页 产品名称 零件名称 小连杆 第 页 材料牌号 坯种类 铸件 毛坯外形尺寸 每毛坯件数 每台件 数 备注 (工序图) 111714 1 2 1 2车 间 工 序 号 工 序 名 称 材料牌号 1 划线 坯种类 毛坯外形尺寸 每坯件数 每台件数 铸件 设备名称 设备型号 设备编号 同时加工件数 夹具编号 夹具名称 冷却液 3 9 0 . 16工序工时 准终 单件 工步号 工步内容 工艺装备 主轴转速 /( r/ 切削速度 /(m/进给量 /(mm/r) 切削深度 /给次数 工时定额 机动 辅助 1 编制 (日期 ) 审核 (日期 ) 会签 (日期 标记 处记 更改文件号 签字 日期 标记 处记 更改文件号 签字 日期 2 机械加工工序卡片 工厂 机械加工工序卡片 产品型号 零件图号 共 页 产品名称 零件名称 小连杆 第 页 材料牌号 坯种类 铸件 毛坯外形尺寸 每毛坯件数 每台件 数 备注 (工序图)6 7 . 5 7 间 工 序 号 工 序 名 称 材料牌号 2 钻孔 坯种类 毛坯外形尺寸 每坯件数 每台件数 铸件 设备名称 设备型号 设备编号 同时加工件数 夹具编号 00 夹具名称 夹具(二) 冷却液 工序工时 准终 单件 工步号 工步内容 工艺装备 主轴转速 /( r/ 切削速度 /(m/进给量 /(mm/r) 切削深度 /给次数 工时定额 机动 辅助 1 钻小 头孔 512 台式钻床 760 1 编制 (日期 ) 审核 (日期 ) 会签 (日期 标记 处记 更改文件号 签字 日期 标记 处记 更改文件号 签字 日期 3 机械加工工序卡片 工厂 机械加工工序卡片 产品型号 零件图号 共 页 产品名称 零件名称 小连杆 第 页 材料牌号 坯种类 铸件 毛坯外形尺寸 每毛坯件数 每台件 数 备注 (工序图)6 1412 1 0 1 28 1 01 26 . 36 . 36 . 33 . 23 . 26 . 36 . 36 . 863 9. 50 间 工 序 号 工 序 名 称 材料牌号 2 钻孔 坯种类 毛坯外形尺寸 每坯件数 每台件数 铸件 设备名称 设备型号 设备编号 同时加工件数 夹具编号 00 夹具名称 夹具(二) 冷却液 工序工时 准终 单件 工步号 工步内容 工艺装备 主轴转速 /( r/ 切削速度 /(m/进给量 /(mm/r) 切削深度 /给次数 工时定额 机动 辅助 1 2 车端面 车外圆 000 2 编制 (日期 ) 审核 (日期 ) 会签 (日期 标记 处记 更改文件号 签字 日期 标记 处记 更改文件号 签字 日期 4 机械加工工序卡片 工厂 机械加工工序卡片 产品型号 零件图号 共 页 产品名称 零件名称 小连杆 第 页 材料牌号 坯种类 铸件 毛坯外形尺寸 每毛坯件数 每台件 数 备注 (工序图)2 . 50 . 7 3 . 5车 间 工 序 号 工 序 名 称 材料牌号 4 钻孔 坯种类 毛坯外形尺寸 每坯件数 每台件数 铸件 设备名称 设备型号 设备编号 同时加工件数 夹具编号 00 夹具名称 夹具( 一 ) 冷却液 工序工时 准终 单件 工步号 工步内容 工艺装备 主轴转速 /( r/ 切削速度 /(m/进给量 /(mm/r) 切削深度 /给次数 工时定额 机动 辅助 1 2 钻 Z 512 台式钻床 760 760 3 编制 (日期 ) 审核 (日期 ) 会签 (日期 标记 处记 更改文件号 签字 日期 标记 处记 更改文件号 签字 日期 5 机械加工工序卡片 工厂 机械加工工序卡片 产品型号 零件图号 共 页 产品名称 零件名称 小连杆 第 页 材料牌号 坯种类 铸件 毛坯外形尺寸 每毛坯件数 每台件 数 备注 (工序图)2. 53 9. 50 间 工 序 号 工 序 名 称 材料牌号 4 钻孔 坯种类 毛坯外形尺寸 每坯件数 每台件数 铸件 设备名称 设备型号 设备编号 同时加工件数 夹具编号 00 夹具名称 夹具(一) 冷却液 工序工时 准终 单件 工步号 工步内容 工艺装备 主轴转速 /( r/ 切削速度 /(m/进给量 /(mm/r) 切削深度 /给次数 工时定额 机动 辅助 1 2 钻 1 Z 512 台式钻床 760 1 编制 (日期 ) 审核 (日期 ) 会签 (日期 标记 处记 更改文件号 签字 日期 标记 处记 更改文件号 签字 日期 6 机械加工工序卡片 工厂 机械加工工序卡片 产品型号 零件图号 共 页 产品名称 零件名称 小连杆 第 页 材料牌号 坯种类 铸件 毛坯外形尺寸 每毛坯件数 每台件 数 备注 (工序图)0 . 5 4 5 0 . 5 4 5 0 0 4 . 9 4 H 7 (+ 0 . 0 1 50 ) . 9 4 H 7 (+ 0 . 0 1 50 )0 . 5 4 5 0 . 0 0 4 0 1 2 5 4 5 车 间 工 序 号 工 序 名 称 材料牌号 5 钻孔 坯种类 毛坯外形尺寸 每坯件数 每台件数 铸件 设备名称 设备型号 设备编号 同时加工件数 夹具编号 00 夹具名称 夹具(一) 冷却液 工序工时 准终 单件 工步号 工步内容 工艺装备 主轴转速 /( r/ 切削速度 /
- 温馨提示:
1: 本站所有资源如无特殊说明,都需要本地电脑安装OFFICE2007和PDF阅读器。图纸软件为CAD,CAXA,PROE,UG,SolidWorks等.压缩文件请下载最新的WinRAR软件解压。
2: 本站的文档不包含任何第三方提供的附件图纸等,如果需要附件,请联系上传者。文件的所有权益归上传用户所有。
3.本站RAR压缩包中若带图纸,网页内容里面会有图纸预览,若没有图纸预览就没有图纸。
4. 未经权益所有人同意不得将文件中的内容挪作商业或盈利用途。
5. 人人文库网仅提供信息存储空间,仅对用户上传内容的表现方式做保护处理,对用户上传分享的文档内容本身不做任何修改或编辑,并不能对任何下载内容负责。
6. 下载文件中如有侵权或不适当内容,请与我们联系,我们立即纠正。
7. 本站不保证下载资源的准确性、安全性和完整性, 同时也不承担用户因使用这些下载资源对自己和他人造成任何形式的伤害或损失。

人人文库网所有资源均是用户自行上传分享,仅供网友学习交流,未经上传用户书面授权,请勿作他用。