目 录
一、设计任务……………………………………………………3二、计算生产纲领、确定生产类型………………………………5
三、零件的分析………………………………………………5
3.1、零件的作用…………………………………………………5
3.2、零件的工艺分析……………………………………………5四、确定毛坯的制造方法、初步确定毛坯形状………………7五、工艺规程设计……………………………………………8
5.1、定位基准的选择……………………………………………8
5.2、工件表面加工方法的选择……………………………………8
5.3、制定工艺路线………………………………………………9
5.4、确定加工余量、工序尺寸及公差……………………………9
5.5、选择机床及对应夹具、量具、刃具…………………………12
5.6、确定切削用量、基本工时(机动时间)…………………14 六、夹具设计…………………………………………………31
6.1、设计要求…………………………………………………31
6.2、夹具设计的有关计算………………………………………31
6.3、夹具结构设计及操作简要说明……………………………32
参考文献……………………………………………………34
致谢…………………………………………………………34
二、计算生产纲领、确定生产类型
生产纲领:年产 10 万件成批生产
三、零件的分析
3.1零件作用
对工作零件起支承、定位的作用
3.2零件的工艺分析
零件图如下:
支承块阶梯孔、60mm表面、50mm表面是重要加工表面。根据零件的尺寸、形位要求,60mm表面有平行度要求,50mm表面对阶梯孔37的中心线有垂直度要求。零件材料:支承块的工作性能要求选择45号钢,45号钢为优质碳素结构钢,硬度不高,易切削加工,但要进行热处理。调制处理后45号钢零件具有良好的机械性能,广泛应用于各种重要的结构零件,特别是一些在交变荷载下工作的连杆、螺栓、齿轮、及轴类等。但表面硬度低,不耐磨。可用调制+表面淬火提高零件表面硬度。
零件的尺寸及技术要求列于下表中
粗糙面度 尺寸精度 尺寸公差 形位公差
阶梯孔 1.6 IT7 与上表面有垂直度要求0.02
阶梯孔阶梯端面 3.2
左右表面AB 1.6 IT8 AB表面有对称度要求0.02
上下表面CD 3.2
外圆 3.2
螺纹底孔3-M5深12 6.3
螺纹底孔M16X1.5 6.3
四、确定毛坯的制造方法、初步确定毛坯形状
4.1选择毛坯的制造方式
根据生产纲领的要求,本零件是中批、大批大量生产,还有零件的材料要求(45号钢)及加工表面与非加工表面的技术要求,我们选择毛坯的制造方式为锻造。根据《机械制造工艺设计简明手册》(机械工业出版出版社、哈尔滨工业大学李益民主编) 零件材料为45钢,采用模锻,精度可达到IT11-15,因此毛坯的加工余量一般。
4.2毛坯尺寸确定
(1)锻件质量
(2)锻件的形状复杂系数
所以为。
(3)分模线形状:平直对称
(4)锻件的材质系数:45号钢含碳量0.42~0.5%,所以材质系数为级。
根据上述数据参照《模锻件机械加工余量与公差标准》(JB3834-1985)执行。锻件的公差范围为普通级。查表的尺寸及公差如下:
阶梯孔 ,左右表面AB ,外圆 43 ,上下表面CD 53,GH面98,EF面偏离零件设计面1.5mm。
4.3绘制毛坯图
毛坯图如下:
五、工艺规程设计
5.1定位基准的选择
(1) 精基准的选择:根据该零件的技术要求,选择37的孔为精基准。零件上的很多表面都可以用它们作为基准进行加工,即遵循了“基准统一原则”。为了保证50mm表面与其中心线垂直和保证60mm表面和零件的对称面平行,须先将37的孔加工出来,再用它定位满足其他尺寸要求。
(2)粗基准的选择:作为粗基准的表面应平整,没有飞边、毛刺或其他表面缺陷。对于本零件而言,选择50mm表面作为粗基准。该表面毛坯质量好,余量均匀。
5.2工件表面加工方法的选择
阶梯孔加工方法:粗镗、半精镗、精镗
50mm面CD:粗铣、精铣
60mm面AB:粗铣、半精铣、精铣
直径40mm外圆表面:粗车、精车
95mm面GH:粗铣
EF面:粗铣
螺纹孔M16X1.5:钻孔、攻螺纹
螺纹孔3-M5:钻孔、攻螺纹
半圆孔4-R3:插齿
5.3制定加工工艺路线
加工工艺方案分析:遵循“先基准后其他”原则,应先加工37的孔。按照“先粗后精”的原则,先安排粗加工工艺,后安排精加工工艺。遵循“先主后次”的原则,先加工主要表面直径37的孔级台阶孔端面,50mm表面,60mm表面,40mm外圆;后加工次要表面M16X1.5螺纹孔和3个M5深12的螺纹孔。遵循“先面后孔”原则,先加工支承块四个表面、外圆表面,在加工3个孔。由于生产类型为成批生产,故采用通用机床配专用夹具,并尽量使工序集中来提高生产率。除此之外,还应降低成本。因此确定加工路线如下:
工序10: 粗铣上下面CD
工序20: 粗镗、半精镗、精镗Φ37阶梯孔。粗镗至尺寸Φ31和Φ、半精镗至尺寸Φ、 精镗至尺寸Φ
工序30: 精铣上下面CD
工序40:粗车、精车Φ40外圆并倒角
工序50: 精车Φ37阶梯孔的阶梯端面
工序60: 粗铣、半精铣、精铣左右面AB;
工序70:粗铣G、H面
工序80:粗铣E、F面
工序90: 钻螺纹孔、攻螺纹;
工序100:钻螺纹孔、攻螺纹;
工序110: 插齿
工序120:清洗、检验入库
5.4确定加工余量、工序尺寸及公差
5.4.1支承块阶梯孔工序尺寸及公差计算
阶梯孔孔径Φ,表面粗糙度为1.6,加工方案为粗镗、半精镗、精镗, 阶梯孔端面表面粗糙度为3.2而且有尺寸要求,加工方案为精车,下面求解各道工序尺寸及公差。
(1)用查表法确定各道工序的加工余量及毛坯总余量如下(见课程设计手册表)
精镗加工余量=0.5mm
半精镗加工余量=2mm
粗镗加工余量=4.5mm
毛坯总余量=各工序余量之和=(0.5+2+4.5)mm=7mm
精车加工余量=0.2mm
(2)计算各工序尺寸的基本尺寸
精镗后孔径应达到图样规定尺寸,因此磨削工序尺寸即图样上的尺寸=mm(设计尺寸)。其他各道工序基本尺寸依次为
半精镗=(37-0.5)mm=36.5mm
粗镗=(36.5-2)mm=34.5mm
毛坯=(34.5-4.5)mm=30mm
(3)确定各道工序尺寸的公差及其偏差。
工序尺寸的公差按各加工方法所能达到的经济精度确定,查阅相关“机械制造技术基础”教材中各种加工方法的经济加工精度表或参阅机械制造技术基础课程设计图2-9进行选择。
精镗前半精镗取IT10级,查表得=0.10mm(机械制造技术基础课程设计表3-4)
粗镗取IT12级,查表得=0.25mm(机械制造技术基础课程设计表3-4)
毛坯公差取自毛坯图,这里查阅《机械零件工艺性手册》(GB/T 6414-1999),取=0.7mm。
(4)工序尺寸偏差按“入体原则”标注
精镗:mm
半精镗:mm
粗镗:mm
毛坯孔:mm
为了清楚起见,把上述结果汇于表5-1中。
表5-1 孔的工序尺寸及公差的计算 mm
工序名称 工序间双边余量 工序达到的公差 工序尺寸及公差
精镗 0.5 IT7 (H7)
半精镗 2 IT10
粗镗 3.5 IT12
毛坯孔 - mm
镗孔深度40-0.2=39.8mm
5.4.2上下面C、D的工序尺寸及公差计算
上下面C、D经过了粗铣和精铣,用查表法确定各道工序的加工余量
计算各工序尺寸的基本尺寸。
粗铣(单边)余量 =1.0mm 表面粗糙度6.3
精铣(单边)余量=0.5mm 表面粗糙度3.2
5.4.3外圆表面的工序尺寸及公差计算
外圆表面经过了粗车、精车两道工步
用查表法确定各道工序的加工余量及毛坯总余量如下
粗车加工余量=2.8mm(见课程设计手册表)
精车加工余量=0.2mm(见课程设计手册表)
毛坯总余量=各工序余量之和=(2.8+0.2)mm=3mm
5.4.4左右面AB的加工余量的确定
用查表法确定各道工序的加工余量及毛坯总余量
工序尺寸的公差按各加工方法所能达到的经济精度确定,查阅相关“机械制造技术基础”教材中各种加工方法的经济加工精度表或参阅机械制造技术基础课程设计图2-9进行选择。
精铣前半精铣取IT11级,查表得=0.22mm(机械制造技术基础课程设计表)
粗镗取IT12级,查表得=0.35mm(机械制造技术基础课程设计表)
为了清楚起见,把上述结果汇于表中。
AB表面的工序尺寸及公差的计算 mm
工序名称 工序间双边余量 工序达到的公差 工序尺寸及公差
精铣 0.5 IT8
半铣镗 1 IT11
粗铣 1.5 IT12
毛坯孔 - mm
5.4.5.由于G、H、E、F表面只要粗铣就可以达到加工要求所以它们工序的加工余量均为1.5。
5.5选择机床及对应夹具、量具、刃具
5.5.1选择机床


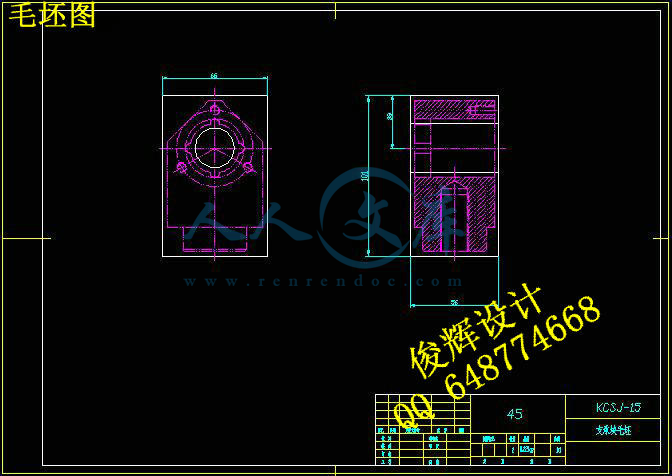



