CNC齿轮测量中心三维测头模块及测试软件设计.doc
CNC齿轮测量中心三维测头模块及测试软件设计【11张CAD图纸和说明书】
收藏
资源目录
压缩包内文档预览:(预览前20页/共44页)
编号:1624748
类型:共享资源
大小:766KB
格式:ZIP
上传时间:2017-08-27
上传人:俊****计
认证信息
个人认证
束**(实名认证)
江苏
IP属地:江苏
40
积分
- 关 键 词:
-
cnc
齿轮
测量
丈量
中心
三维
模块
测试
软件设计
11
十一
cad
图纸
以及
说明书
仿单
- 资源描述:
-
目录
摘要 1
Abstract 2
主要符号表 1
1 绪论 1
1.1引言 1
1.2研究意义 1
1.3国内外发展状况 1
1.4本文的主要任务 3
2 齿轮测量原理与总体方案设计 4
2.1齿轮齿形测量的方法与误差分析 4
2.1.1齿形误差的定义 4
2.1.2齿形误差测量方法 4
2.1.3齿形测量范围的确定 4
2.1.4齿形误差评定与分析 6
2.2齿轮齿向测量的方法与误差分析 8
2.2.1齿向误差的定义 8
2.2.2齿向误差测量方法 8
2.2.3齿向误差评定与分析 8
2.3 总体方案设计 10
3 板卡操作 11
3.1接口方案 11
3.2 HY6040板卡介绍及操作 11
3.3 HY6110板卡介绍及操作 11
3.4 CA220-PCI 12
3.4.1 CA220-PCI简介 12
3.4.2 CA220-PCI操作过程 12
4 EFRS-401MZ齿轮测量机软件设计 14
4.1开发软件简介 14
4.2用户需求 14
4.3软件的界面设计 15
4.3.1界面应具备的功能元素 15
4.3.2具体界面设计 16
4.4总体程序流程图 20
4.5分功能模块的实现 22
4.5.1齿形测量程序流程设计 22
4.5.2数据处理程序流程设计 23
4.5.3数据采样流程及部分程序代码 25
4.5.4按键扫描流程图设计 26
5 伺服机械子系统设计及校核 29
5.1原理方案设计 29
5.2结构方案设计 29
5.2.1结构布局 29
5.2.2驱动装置 29
5.2.3传动系统 30
5.2.4滚动导轨 30
5.3伺服机械子系统设计计算 30
5.3.1伺服电机的选择 30
5.3.2设计并校核齿轮 31
5.3.3同步带传动设计 33
5.3.4导轨设计 35
5.3.5各支承件的设计 35
5.4强度校核 36
5.4.1伺服电机校核 36
5.4.2轴承校核 37
6 结论 38
7 致谢 39
参考文献 40
主要符号表
n 转速 F 集中载荷,力
V 线速度 M 弯矩,力矩
传动效率 计算拉压应力
P 功率 E 材料的弹性模量
i 传动比 L、l 长度
T 转矩 齿形系数
Z 齿轮齿数 J 转动惯量
m 模数 应力校正系数
d 直径 K 载荷系数
KV 动载荷系数 B 宽度
a 中心距 ZE 弹性影响系数
KA 使用系数 ZP 接触系数
Vs 相对滑动速度 N 应力循环次数
载荷分布不均系数 KHN 寿命系数
1 绪论
1.1引言
齿轮传动是广泛应用于机器和仪表中的一种重要形式。它用来传递位移、速度和动力。随着我国汽车摩托车制造业的迅速发展,汽摩齿轮制造业也得到了空前快速的发展。尽快成为汽摩齿轮的全球制造与供应基地,是我国齿轮制造业的总体发展战略,并已经成为我国众多齿轮制造商的共识。航空航天工业的崛起、造船业的兴盛、机械装备制造业的复苏以及IT行业的快速发展,都对齿轮制造业提出了更高的要求,也提供了前所未有的机遇。无论是国有企业、股份公司还是民营企业,齿轮制造商在扩大齿轮产量、品种的同时,更加注重提高齿轮制造质量。为此,最近几年来在引进技术、购置设备、更新工艺、加强信息化管理等技术改造和技术升级方面进行了大量的投入;强化并提高齿轮制造全过程的测量与监控技术水平获得了空前的重视,并成为确保齿轮质量的一个关键。开发具有自主知识产权的齿轮测量技术和仪器,满足我国齿轮制造质量检测的迫切需要,提高国产齿轮仪器在国内市场的占有率,是我国齿轮测量仪器制造业当前所面临的一项重要而紧迫的任务。
1.2研究意义
目前,我国齿轮行业测试仪器和设备十分缺少,有不少齿轮生产企业竟然没有一台齿轮量仪;有些国有大中型企业所使用的齿轮量仪,还是国外六七十年代的产品,已远远满足不了技术发展的要求。造成这种现象的主要原因是:a. 前几年齿轮制造业的发展以量为主,对质的要求尚不迫切,但今后,能否保证齿轮产品的质量,是否拥有与产品等级相适应的齿轮量仪,将成为企业能否生存的关键;b.信息沟通不够,技术交流偏少是造成我国齿轮生产企业仪器装备落后的另外一个原因。许多齿轮生产企业对国内齿轮量仪的发展了解不够,对齿轮量仪的性能了解不够,制约着齿轮量仪进入齿轮生产企业。事实上,这几年在齿轮制造业迅猛发展的同时,我国齿轮量仪制造水平也经历了跨越式发展,特别是2000年以来,以3903系列为代表的CNC齿轮测量中心投放市场,标志着我国齿轮量仪的制造水平达到了当今国际先进水平,基本上可以满足齿轮行业对测量仪器的需求。
1.3国内外发展状况[1]
1923年,德国Zeiss公司在世界上首次研究成功一种被称为“Tooth surface Tester”的仪器,实际上是机械展成式万能渐开线检查仪。1965年,英国的
R.Munro博士研制成功光栅式单啮仪,标志着高精度测量齿轮动态性能成为可能。
1970年,美国Fellow公司在芝加哥博览会展出Microlog50,标志着数控齿轮测量中心开始投入使用,这是齿轮测量技术发展的转折点。70年代以前,机械展成式测量技术已经发展成熟,并在生产实践中经受了考验。经过30多年的完善和推广,齿轮整体误差测量方法在我国已发展成为传统元件的运动几何测量法,其基本思想是将被测对象作为一个刚性的功能元件或传动元件与另一标准元件作啮合运动,通过测量啮合运动误差来反求被测量的误差。
最近几年一些新的齿轮测量仪器也在不断的涌现,在新的齿轮精度国家标准中,齿轮精度的检测项目有齿距偏差、齿廓偏差、螺旋线偏差、切向综合偏差、径向综合偏差、径向跳动等项目。这里主要介绍以下几种最为先进的齿轮测量仪:a. CNC齿轮测量中心3903/3906
3903/3906型CNC齿轮测量中心是哈量集团精密量仪公司开发出的新产品,具有测量功能强、精度高、速度快等特点,达到了当代国际先进水平.该中心可满足用户对齿轮精度的全面检测,工艺间检测、刀具检测等需求。可完成齿轮的齿距、齿廓 、螺旋线、径跳、切向综合(单截面整体误差)等项目的检测,可测量的工件有齿轮、齿轮刀具(滚刀、插齿刀、剃齿刀等)、蜗轮、蜗杆、弧齿锥齿轮等。由于其工作原理上不需要标准齿轮、标准蜗杆等标准件和机械展成机构,测量运动由计算机数控系统来完成,因此可以根据用户的要求,开发出各种特殊软件。整个操作界面汉字提示,操作简单,对操作人员的要求不高
b. PFSU系列齿轮测量机640/1200/1600[2]
该系列测量机是引进德国克林贝格公司技术生产的,主要用于对大齿轮的测量。目前哈量集团精密量仪公司已经完成了该测量机控制系统国产化改造.将过时的控制电路、记录器等全部淘汰,采用新的工业控制计算机和可编程控制器,改造后的PFSU系列齿轮测量机不仅保留了仪器原有的全部功能,而且使仪器的功能和性能都有很大提升。齿轮的测量项目有齿廓、螺旋线、齿距、径跳等,还可以测量齿轮刀具(滚刀、插齿刀、剃齿刀等)、蜗杆及工件表面粗糙度、工件锥度、圆度等形位误差。针对国内已有PFSU系列测量机的用户,公司可提供升级改造服务。
c. 3004B、3006B、3008B系列万能齿轮测量机
该系列齿轮测量机是哈量集团具有自主知识产权的智能化齿轮量仪,在工作原理和仪器功能上接近CNC齿轮测量中心.测量中不需要标准齿轮、标准蜗杆,即可测量齿轮、齿轮刀具等工件的多项误差,在测量效率要求不很高的情况下,可广泛用于工厂计量室和车间检测站,进行精密测量。
d. 3100系列双面啮合检查仪
主要检测齿轮的径向综合误差,可广泛用于除汽车、摩托车行业4级以下精度齿轮的分选检测,工作效率高,精度稳定。
e. 3200、3300系列齿形、齿向检查仪
该系列测量仪是机械展成式测量机.根据测量要求的不同,有多种不同的机械结构,主要完成对齿轮齿形、齿向等单项误差测量,仪器结构简单、效率高、精度稳定,可广泛用于生产车间使用。





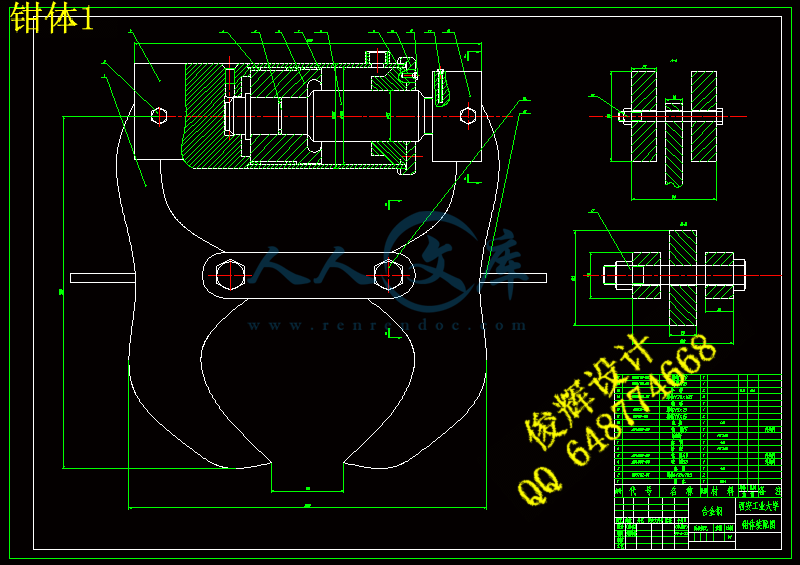

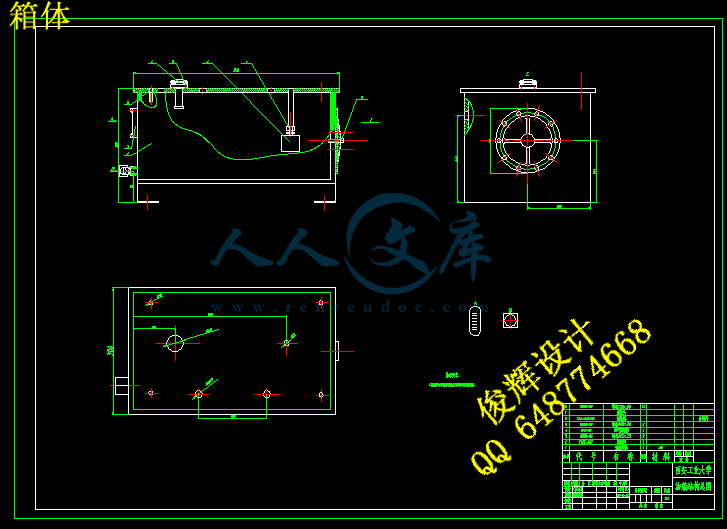




- 内容简介:
-
1 目录 摘要 . 1 . 2 主要符号表 . 1 1 绪论 . 1 . 1 . 1 . 1 . 3 2 齿轮测量原理与总体方案设计 . 4 . 4 . 4 . 4 . 4 . 6 . 8 . 8 . 8 . 8 体方案设计 . 10 3 板卡操作 . 11 . 11 . 11 . 12 . 12 . 12 2 . 12 4 . 14 . 14 . 14 . 15 . 15 . 16 . 20 . 22 . 22 . 23 . 25 . 26 5 伺服机械子系统设计及校核 . 29 . 29 . 29 . 29 . 29 . 30 . 30 . 30 . 30 . 31 . 33 . 35 . 35 . 36 机校核 . 36 . 37 3 6 结论 . 38 7 致谢 . 错误 !未定义书签。 参考文献 . 40 1 主要符号表 n 转速 F 集中载荷,力 V 线速度 M 弯矩,力矩 传动效率 计算拉压应力 P 功率 E 材料的弹性模量 i 传动比 L、 l 长度 T 转矩 Z 齿轮齿数 J 转动惯量 m 模数 d 直径 K 载荷系数 动载荷系数 B 宽度 a 中心距 弹性影响系数 使用系数 接触系数 相对滑动速度 N 应力循环次数 k 载荷分布不均系数 寿命系数 1 绪论 1 1 绪论 齿轮传动是广泛应用于机器和仪表中的 一种重要形式。它用来传递位移、速度和动力。 随着我国汽车摩托车制造业的迅速发展,汽摩齿轮制造业也得到了空前快速的发展。尽快成为汽摩齿轮的全球制造与供应基地,是我国齿轮制造业的总体发展战略,并已经成为我国众多齿轮制造商的共识。航空航天工业的崛起、造船业的兴盛、机械装备制造业的复苏以及 业的快速发展,都对齿轮制造业提出了更高的要求,也提供了前所未有的机遇。无论是国有企业、股份公司还是民营企业,齿轮制造商在扩大齿轮产量、品种的同时,更加注重提高齿轮制造质量。为此,最近几年来在引进技术、购置设备、更新工艺、加强信 息化管理等技术改造和技术升级方面进行了大量的投入;强化并提高齿轮制造全过程的测量与监控技术水平获得了空前的重视,并成为确保齿轮质量的一个关键。开发具有自主知识产权的齿轮测量技术和仪器,满足我国齿轮制造质量检测的迫切需要,提高国产齿轮仪器在国内市场的占有率,是我国齿轮测量仪器制造业当前所面临的一项重要而紧迫的任务。 目前,我国齿轮行业测试仪器和设备十分缺少, 有不少齿轮生产企业竟然没有一台齿轮量仪;有些国有大中型企业所使用的齿轮量仪,还是国外六七十年代的产品,已远远满足不了技术发展的要求。造成这 种现象的主要原因是: a. 前几年齿轮制造业的发展以量为主,对质的要求尚不迫切,但今后,能否保证齿轮产品的质量,是否拥有与产品等级相适应的齿轮量仪,将成为企业能否生存的关键; 术交流偏少是造成我国齿轮生产企业仪器装备落后的另外一个原因。许多齿轮生产企业对国内齿轮量仪的发展了解不够,对齿轮量仪的性能了解不够,制约着齿轮量仪进入齿轮生产企业。事实上,这几年在齿轮制造业迅猛发展的同时,我国齿轮量仪制造水平也经历了跨越式发展,特别是 2000年以来,以 3903 系列为代表的 轮测量中心投放市场,标 志着我国齿轮量仪的制造水平达到了当今国际先进水平,基本上可以满足齿轮行业对测量仪器的需求。 1 1923年,德国 仪器,实际上是机械展成式万能渐开线检查仪。 1965年,英国的 2 士研制成功光栅式单啮仪,标志着高精度测量齿轮动态性能成为可能。 1970年,美国 志着数控齿轮测量中心开始投入使用,这是齿轮测量技术发展的转折点 。 70 年代以前,机械展成式测量技术已经发展成熟,并在生产实践中经受了考验。经过 30 多年的完善和推广,齿轮整体误差测量方法在我国已发展成为传统 元件 的运动几何测量法,其基本思想是将被测对象作为一个刚性的功能元件或传动元件与另一标准元件作啮合运动,通过测量啮合运动误差来反求被测量的误差。 最近几年一些新的齿轮测量仪器也在不断的涌现,在新的齿轮精 度国家标准中,齿轮精度的检测项目有齿距偏差、齿廓偏差、螺旋线偏差、切向综合偏差、径向综合偏差、径向跳动等项目。这里主要介绍以下几种最为先进的齿轮测量仪:a. 轮测量中心 3903/3906 3903/3906型 有测量功能强、精度高、速度快等特点,达到了当代国际先进水平该中心可满足用户对齿轮精度的全面检测,工艺间检测、刀具检测等需求。可完成齿轮的齿距、齿廓 、螺旋线、径跳、切向综合(单截面整体误差)等项目的检测,可测量的工件有齿轮、齿轮刀具( 滚刀、插齿刀、剃齿刀等)、蜗轮、蜗杆、弧齿锥齿轮等。由于其工作原理上不需要标准齿轮、标准蜗杆等标准件和机械展成机构,测量运动由计算机数控系统来完成,因此可以根据用户的要求,开发出各种特殊软件。整个操作界面汉字提示,操作简单,对操作人员的要求不高 b. 列齿轮测量机 640/1200/16002 该系列测量机是引进德国克林贝格公司技术生产的,主要用于对大齿轮的测量。目前哈量集团精密量仪公司已经完成了该测量机控制系统国产化改造将过时的控制电路、记录器等全部淘汰,采用新的工业控制计算机和可编程控制 器,改造后的 列齿轮测量机不仅保留了仪器原有的全部功能,而且使仪器的功能和性能都有很大提升。齿轮的测量项目有齿廓、螺旋线、齿距、径跳等,还可以测量齿轮刀具(滚刀、插齿刀、剃齿刀等)、蜗杆及工件表面粗糙度、工件锥度、圆度等形位误差。针对国内已有 列测量机的用户,公司可提供升级改造服务。 c. 3004B、 3006B、 3008B 系列万能齿轮测量机 该系列齿轮测量机是哈量集团具有自主知识产权的智能化齿轮量仪,在工作原理和仪器功能上接近 量中不需要标准齿轮、标准蜗杆,即可测量 齿轮、齿轮刀具等工件的多项误差,在测量效率要求不很高的情况下,可广泛用于工厂计量室和车间检测站,进行精密测量。 d. 3100 系列双面啮合检查仪 主要检测齿轮的径向综合误差,可广泛用于除汽车、摩托车行业 4级以下精度齿轮的分选检测,工作效率高,精度稳定 。 e. 3200、 3300 系列齿形、齿向检查仪 该系列测量仪是机械展成式测量机根据测量要求的不同,有多种不同的机 3 械结构,主要完成对齿轮齿形、齿向等单项误差测量,仪器结构简单、效率高、精度稳定,可广泛用于生产车间使用。 文的主要任务 本文分析了 齿轮误差测量的发展状况和特点,针对国内外出现的各种测量仪器的局限和不足,提出改进齿轮测量软件测 量齿轮的方法,并设计完成一种新型的、 人机界面友好的,自动化程度较高的齿轮测量软件。 a. 首先通过对齿轮齿形和齿向测量原理 以 及 齿轮测量机机械部分运动机理的理解,完成总体方案设计; b. 依据齿形、齿向测量原理建立齿形、齿向误差测量算法,并完成齿形误差软件的程序流程; c. 针对测量中出现特性 和整个界面的易于操作性和美观性,利用言来实现齿形测量系统软件的设计; d. 最后对所编写 的测量软件进行模拟 调试,并进一步肯定了整个测量系统的合理性和实用性。 2 齿轮测量原理与总体方案设计 4 2 齿轮测量原理与总体方案设计 形误差的定义 3 根据标准 J 形误差的定义是:在端截面上,齿形工作部分内(齿顶倒棱部分除外)包容实际齿形的两条最近的设计齿形间的法向距离。由定义可知,在齿形误差测量中应测出实际齿形相对于设计齿形之误差 ,设计齿形是指以渐开线理论齿形为基础,考虑弹性变形和误差对噪声的影响而加以修正的齿形 ,在成对齿轮副中,可以设计为两个齿轮都作齿顶 修缘,也可以设计为一个齿轮(常是小齿轮)作齿顶修缘,齿根过切或设计为凸齿形,另一个相配的齿轮不作修正 ,修正量是很小的,仅有( m,或从 20m。因 此,齿形误差测量还是以实际齿形与理论渐开线进行比较作为基础。 形误差测量方法 a. 坐标法 将被测齿形上若干点的实际坐标与相应的计算坐标进行比较从而计算出齿形误差的方法称为齿形误差坐标测量法。以坐标法测量齿形误差,既可以在以坐标为测量原理所构成的专用齿形误差测量仪上进行,也可以在坐标测量机或测量显微镜上测量。 b. 标准轨迹法 将被测齿形与仪器复现的理论渐开线轨迹进行比较从而求出齿形误差的方法称为齿形误差的标准轨迹测量法。由于电子和计算机技术的发展,出现了用电子和机械共同组成的系统来复线理论渐开线轨迹,这种系统可以进行数控( 也可以由计算机进行数控( 称这种方法为电子展成法。电子展成法正在发展中。 c. 标准曲线法 这种方法是使被测齿形与标准渐开线齿形曲线直接进行比较,从而测出齿形误差,(标准渐开线齿形曲线应具有一定的准确度)。这种方法可用于车间条件下的生产测量,也可用于高准确度的实验室测量。 本文采用 标准轨迹法进行齿形与齿向的测量。 形测量范围的确定 4 a. 确定起测圆的方法 (1)当被测齿轮 2相啮合时,被测齿轮 实际部分是齿顶圆与工作圆之间的一段渐开线齿形。所谓工作圆是指通过相啮合的齿轮 ,其半径为 如 5 图 , 222rb ( 22a s i n 1 2 2li a r a r b ( 其中 1 2 / c o s a rb rb a t ( ( 2 ( 1 2 ) / 1 2 )i n v a t t g a t X t X t Z Z i n v a t ( 2 2 * 2 *r a r h a m n X n m n n m n ( 式中 数 ; n 高度变位时 n =0,角度变位时 n 0。 / c o ( ( 1 2 )t X t X t y t ( c o s( 1 2 / 2 ) 1c o s t z z ( 式中 t (2)由于在测量单位个齿轮时,常常不知与其啮合的齿轮的参数,为使测量的齿形工作部分稍大于齿形有效部分,可以按照被测齿轮与标准齿条啮合时的有效工作部分来计算其工作圆。此时工作圆是指通过齿条的齿顶线与啮合线的交点 半径为 如图 示。 图 轮渐开线 6 222Ra r ( 22 *s i nh a m n X n m nl i r r b ( (3)为了简化计算,可以按进入圆来确定起测点。进入圆是指其半径 分度圆半径相差 C=(xs)圆 如图 示 下式计算 : mn*z/2) ( C=hn* ( 当齿数少时按基圆确定:当齿数 Z 33 时; Z 16时, 为只在基圆外才有渐开线,当齿数少时,应该以基圆作为起测圆。 以上三种计算结果相比较 ,起测圆按进入 圆计算时 ,齿形上被测范围为最大 ,这将对切齿条件要求严格 应当选以免对加工条件要求过严 b. 起测和终测展开角和展开长度的计算 5 由于齿形测量是按照展成角度或展开长度进行的,实际的测量范围是以展成角或展成长度来表示的。 如图 示 起测点 A 所对应的展开角与展开长度称为起测展开角 A 与起测展开长度 所对应的为终测展开角 B,终测展开长度 A= ( LA= ( 1co s A ( : B= ( LB=a 1co s a ( 形误差评定与分析 a. 齿形误差的评定 用齿形误差曲线图表示齿形误差。曲线图的横坐标表示展开角度或展开长度 L,纵坐标表示个测量点 的齿形误差 展开长度的误差 见图 果被测齿形与理论渐开线没有差别,在记录图上记录为平行于横坐标的直线。 7 在确定了齿形测量范围( A、 B)之后,在此范围内作两条平行线分别与齿形误差曲线的上下两个最高点相切,平行线间的纵坐标格数乘以误差放大比即可得到齿形误差 了反映齿轮偏心等因素的影响,测量均布的四个齿面的齿形误差,以期最大值作为该齿轮的齿形误差,用来评定该齿轮的齿形质量是否合于要求。 b. 齿形误差的分析 对方程式 L= (2)全微分并 取增量形式,可得 L= ( 或 L= ( 展开长度的变化就是齿形误差,有上式可以看出,基圆半径的变化 b 或压力角的变化都是影响齿形误差的因素,其主要的工艺原因是刀具的齿形角有误差。由于齿形角误差在一般情况下可以认为是定值, 所以, 果没有其他的 误差因素,仅有由于齿形角误差所造成的压力角误差,齿形误差的记录曲线是一条与横坐标有一定夹角的倾斜直线。 由以上分析可知,齿形误差由两部分组成: 由压力角误差(或基圆半径误差 b)引起的渐开线齿形的倾斜误差 以齿形误差曲线的中线 由机床传动链误差引起的渐开线齿形的形状误差 中线 方向左两条能包容齿形误差曲线的平行线,它们之间沿着横坐标的距离即为 c. 确定中线 为了求出 先要确定中线 (1)根据最小二乘法原理求出齿形误差曲线的拟合直线即为中线。表征直线方程的参数为直线的斜率 ,计算拟合直线的斜率 K 的方法为 :在测得的曲线上取一系列点的坐标值 ( 1, ,( 2, ( i, 斜率计算式为 : 22n ( 式中 、 L 分别为i及平均值; n: 测量点的总数。 这种方法的精度高,但计算较为复杂,一般为手工计算所不用,当测量系统由计算机控制和进行数据处理时常常用这种方法 ,这时可由测出的各个坐标值直图 形误差分析 8 接进行计算。 (2)对于一般精度的测量,常常用目估作图法确定中线。即在所得的齿形误差曲线图上画一条直线,使在测量范围内,直线两边的齿形误差曲线与直线间所包容的面积相等,这条直线就是中线 这种方法精度不高,但简单易性。而且目估的方向,对于一个熟练的测量者来说也不会偏离最小二乘法所确定中线的 2 度的范围,这是测量精度所允许的。 d. 基圆半径误差 式 (前一项可以知道 ,当仅有基圆半径误差 ,齿形误差曲线是一条与横坐标有夹角的直线 ,由计算法求出中 线的斜率即为基圆半径误差 : ( 由作圆法确定中线后可以在曲线上直接量出倾斜误差 时由下式计算基圆半径误差 : ( 式中 单位为 m; 单位为 单位 m. 向误差的定义 在分度圆柱面(允许在齿高中部测量)上,齿宽工作部分范围内(端部倒角部分除外)包容实际齿向线的两条最近的设计齿向线之间的端面距离。 向误差测量方法 (1). 标准轨迹法 测量仪器形成标准的螺旋运动与被测齿轮的螺旋线进行比较测量,齿向误差直接由测量装置指示出来。形成标准的螺旋线轨迹的装置可以是机械式的、光学机械式的,也可以是电子展成式的。 (2). 坐标测量法 螺旋线是一条空间曲线,可按照螺旋线形成原理分别测量齿 轮转角和测头齿轮方向的位置,然后与相应的理论值进行比较,计算出齿轮向的误差;或者按照空间直角坐标沿螺旋线逐点测量其三个坐标值,然后计算出齿向误差。 向误差评定与分析 齿向误差在一般情况下是由两部分组成的,即齿向线的位置误差和形状 ,如 9 下图 向线的位置误差也就是螺旋线角误差的线值,用 定 要求不十分精确的情况下也可以用作图法使中线两边曲线多包围的面积相等来确定中线的位置。包容实际齿向误差曲线且与中线平行的两条直线之间的距离(仍为 齿轮端面距离,在 为形状误差,用 齿向误差分为位置误差和形状误差将有助于分析齿向的加工误差。 由 为 b (将此式微分并取增量形式,且( = =( b) (式中 b 图 图 齿面的齿向线位置误差 向齿体内的误差为负值),其螺旋角误差方向相反,主要是由于加工时刀具沿着工件轴线方向进给时,刀具的运动方向与工件轴线方向不平行所引起的,其不平行度由左、右齿面的齿向线位置误差的平均值来确定的,即: =( + ) /2 (图 齿面的齿向线位置误差 左、右齿面螺旋角误差方向相同的情况。这主要是由于刀具轴向进给方向相对于工件轴线倾斜所造成 的,其倾斜度按左、右齿面齿向线位置误差的绝对值之平均值来确定,即: = + ( 工件的安装误差也会造成工件轴线相对于刀具轴向进给方向倾斜,而且二者相对的倾斜度是工件转角的函数,这就导致一个齿轮上各个齿的齿向误差数值不同。 图 向误差评定法 10 图 向误差曲线 由于机床 传动链的传动比不准确也会 造成 此在分析工艺误差的时候要结合具体加工条件进行分析。 当左、右齿面的齿向误差曲线较大, 的值也相 差较大,则是兼有几种工艺误差因数的综合作用,可先找出主要工艺误差因数,再按照任一齿面的 齿向误差的形状误差 f f 是由于切齿加工中刀具相对于工件轴线移动的导轨的直线度误差及轴向进给丝杠的轴向窜动等因数所引起。 体方案设计 本设计采用标准轨迹法进行齿轮齿形齿向的误差测量,将被测齿轮的实际齿形与仪器复现的理论渐开线进行比较从而得出误差的测量方法,运动的合成经参数设置完成后计算机自动进行计算,控制控制系统发出指令脉冲,驱动执行机构完成相应的运动,硬件数据采集系统从安装在滑架上的测头采集数据,送入计算机进行计算,得出误差结果,转化为图形和数字量形式的结果输出。 根据系统的特点,对软件的编写拟采用可视化编程语言 +为该语言执行速度快,人机界面友好,具有较高的操作系统访问权。齿形测量程序设计时主要完成齿形测量中的数据采样和结果的处理,并根据测量算法得到齿廓总偏差、齿廓斜率偏差、齿廓形状偏差和齿廓误差曲线,通过对齿形误差测量方法的分析并结合机械部分运动机理,齿形误差测量的理论方方法采样坐标法;齿向测量程序设 计时主要完成齿向测量中的数据采样和结果的处理,并根据测量算法得到齿向总偏差 向斜率偏差 向形状偏差 过对齿形误差测量方法的分析并结合机械部分运动机理,齿向误差测量的理论方方法采样标准轨迹法。最后所有的误差结果以文字和图形的方式显示在屏幕上,而且用户的所由参数以对话框的形式由用户通过键盘输入。3 板卡操作 11 3 板卡操作 6 综合考虑此设计,计算机 需 要完成如下任务 :测量者按下操作面板的按键时,计算机要能对其识别并发出指令,驱 动系统动作 完成测量 , 为此,测量系统需要 一个 开关量输入设备; 算机 只能对数字量进行处理,而数据 采集 系统采集到 的信号 为电压模拟信号,因此在计算机与数据采集系统之间需要一块 A/D 转换卡, 本设计中 采用北京华远自动化公司的 转化卡 、 110数字量输入卡,光栅数据采集卡选用 中前两个板卡为 设计中采用 件,它 允许 序实时直接访问 的 i/o 端口而无须使用 或其他工具。 持 5/98 和 000/并且 非常容易使用 , 在 000/, 动程序可以动态地加载和卸载,不需要做任何设置工作。 是 令的替代品。 可以获得 口的基地址。 而 基于 线的采集卡, 线系统要求有一个 制卡,它必须安装在一个 槽内。根 据实现方式, 制器可以与一次交换 32 位或 64 位数据,它允许智能助适配器利用一种总线主控技术与 行地执行任务。 卡介绍及操作 7 ,它有三种不同的触发方式:软件触发、定时触发和外部触发。 本设计采用软件触发,主要操作步骤如下: (1). 对“ ”口进行读操作,清除 A/免引起系统误操作。 (2). 对“ ”口进行写操作,选择模拟输入通道和程控增益。 (3). 对“ ”口进行写操作,关闭定时触发、外触发。 (4). 对“ ”口进行写操作,触发 A/ (5). 从“ ”口进行读操作,读取板状态字,检测 A/是否为“ 1”。 (6). 当 A/D 转换完成位为“ 1”后,延时大约 25 s。 (7). 从“ ”和“ ”口读取转换结果。 软件在查询方式下,用户编程自行决定在检测到 A/读取 A/应部分程序代码如下 _,0); /读基地址 +2位,是否启动 A/_); /读 A/位 _)&0 /读 A/位 N=( +1 取 计算每个采样点误差和 求所有偏差的和除以 对 点根据最小二乘法确定中线 距 由 y b 及实际采样点处的偏差求形状偏差和斜率偏差 返回计算结果及测量 值 返 回 图 据处理程序流程图 25 据采样流程及部分程序代码 采样函数 程序代码如下 12: y=0; i=0; /采样 _,0); /写控制字触发 A/D 转换 初始化 读基地址控制变量 读基地址 +3 的数据 送给 给 6040基地址 +2 写控制程序 读基地址 +4的数据 送给 8)送给 &0? 00/1000/4096 00/1000/4096 00/1000/4096 00/1000/4096 返回 样函数流程图 26 y=_ /读基地址 (y&0; /检测 A/); /读 A/位 )&0|(8); /得到采样数据送入 ; 00;/辨率 4000v 000/4096; /数据运算 键扫描流程图设计 初始化 i=0 i 读 6110值 赋 i+ i=8 o 01 2*) i4? 27 由于整个测量软件要根据输入按键的状态决定什么时候开始测量,具体测量什么项目什么时候测量结束,开始测量时要控制电机带动运动部件按要求轨迹运动,结束时还要控制电机停止运动。所以按钮检测与控制程序就显的很重要,在按钮检测与控制程序中主要完成按键的读取。 按钮检测与控制 程序代码如下: ) 1; /检测按键 _); /6110 i=0;i4;i+) 0(2*i) i; if(0|1|2|3)/测量项目 齿形右 2齿向上 3齿向下 i=8;i10;i+) /8 9停止 02*i) 00/1000/4096 00/1000/4096 00/1000/4096 i 图 键扫描流程图 i10? i 结束 28 0(2*i) i; if( ; 5 伺服机械子系统设计及校核 29 5 伺服机械子系统设计及校核 原理方案设计 13 图 工作原理:计算机通过计算测量者输入的数据得到一系列运动信息,传递给数控装置发出运动的指令脉冲,再经过传动导向装置使测头工作台与被测齿轮合成理论的渐开线运动,测头检测到的信息即为误差信息,数据采集系统把采集到的数据送给计算机,经过运算得出误差结果。 结构布局 14。 动装置 驱动系统:它是使 机械结构运动的装置,伺服驱动装置是带有力或力矩或速度或位置反馈并可自动调节的驱动装置。要求主要在以下几方面:高精度、快速响应、无超调、调速范围宽、稳定性要好、快速的应变能力和较长时间的过载能力。 综合选择,取电机类型为交流伺服电机。被测齿轮 计算机 数控驱动装置 传动、导向装置 测量装置 结果输出 30 动系统 由于此测量机 r/常工作时转速极低,且测量系统为较高精度的测量,因此采用两级转速,考虑到整个测量机的安装位置,第一级选锥齿轮传动,传动效率高,有很大的经济效益,结构紧凑,工作可靠,寿命长,传动比稳定;第二 级选择同步带传动,它可保持恒定的传动比,传动精度较高,工作平稳,效率高,达 98%,噪音小,不需要润滑。 动导轨 15 导轨是精密机械中用来保证各运动部件相对精度的一个重要部件。滚动导轨具有以下优点:运动灵敏度高,没有爬行现象;定位精度高;牵引力小,移动灵活;主要由导轨、滑块以及滚珠组成。 服机械子系统设计计算 伺服电机的选择 (1). 选择滚珠丝杠 已知正常工作状态时丝杠的转速约为 5r/丝杠的预计寿命为 15000h,由 610150006 0 5, (得出 L= 先初选丝杠的导程为 5mm/r, 335 5 1 02 2 2 1 0 1 0aF m a N ( 3 , (因此 3 31 0 4 . 5 1 6 . 5 L N 因为受力不大,优先选取丝杠的导程为 5mm/r, 由因为需要安装带轮、轴承等零件,故丝杠轴径取为 25预紧方式为双螺母垫片式。 根据表 5择丝杠的型号为 相关参数为: 丝杠中径 25本导程 5mm/r ,钢珠直径为 杠外径为 列。 (2). 由于测量机 且 31 在测量过程中丝杠的测量速度很慢,为 5r/对电机要求为额定转速低、响应速度快,本设计选取上海赢双电机有限公司生产的型号为 交流电机, 相关参数如下: 电压: 200v; 额定转速: 200r/ 最高转速: 500r/ 额定转矩: 安装尺寸: 0 16 30 计并校核齿轮 (1). 总传动比分配 16 由于伺服电机转速为 200r/终丝杠转速为 5r/总传动比i=n/v= =40,设计传动系统为两级减速,第一级采用直齿锥齿轮传动,第二级采用同步带传动减速。分配的传动比为 , 0/6 (2).
- 温馨提示:
1: 本站所有资源如无特殊说明,都需要本地电脑安装OFFICE2007和PDF阅读器。图纸软件为CAD,CAXA,PROE,UG,SolidWorks等.压缩文件请下载最新的WinRAR软件解压。
2: 本站的文档不包含任何第三方提供的附件图纸等,如果需要附件,请联系上传者。文件的所有权益归上传用户所有。
3.本站RAR压缩包中若带图纸,网页内容里面会有图纸预览,若没有图纸预览就没有图纸。
4. 未经权益所有人同意不得将文件中的内容挪作商业或盈利用途。
5. 人人文库网仅提供信息存储空间,仅对用户上传内容的表现方式做保护处理,对用户上传分享的文档内容本身不做任何修改或编辑,并不能对任何下载内容负责。
6. 下载文件中如有侵权或不适当内容,请与我们联系,我们立即纠正。
7. 本站不保证下载资源的准确性、安全性和完整性, 同时也不承担用户因使用这些下载资源对自己和他人造成任何形式的伤害或损失。

人人文库网所有资源均是用户自行上传分享,仅供网友学习交流,未经上传用户书面授权,请勿作他用。
2:不支持迅雷下载,请使用浏览器下载
3:不支持QQ浏览器下载,请用其他浏览器
4:下载后的文档和图纸-无水印
5:文档经过压缩,下载后原文更清晰
|