摘 要
圆筒混合机是烧结厂主要设备之一。一次混合机主要作用是将物料混匀及湿润,二次混合机主要是对物料进行制粒,使物料满足成分均匀、水分适中、透气良好的要求。混合料的进料由皮带机和漏斗两种形式,将料送入圆筒混合机的进料端,通过筒体的旋转,物料在筒体内呈螺旋状运动,在运动的过程中使混合料形成“滚落”状,从而完成物料的混合、湿润、制粒、混匀,通过圆筒混合机排料端的溜槽排到皮带输送机上。
阐述了混和、制粒时物料的运动过程,对圆筒混合机内物料运动的几种状态进行分析。描述了影响圆筒混合机混匀、制粒的因素。分析了圆筒混合机筒体各部分的力学性能,提供了相应的受力的计算方法。然后阐述了圆筒混合机传动装置的受力分析和计算方法,主要是对轴的安全性能的校核,保证传动的可靠性。
关键词 圆筒混合机;传动;受力分析;校核
Abstract
Drum blender is one of the most important equipments in modern iron and steel corporation. The primary role of the first mixer is mixing materials and humid. The Mixer of second major is used to proceed granulation. Uniform material to meet constituents, moderate water, good ventilation requirements. Mixture of feed material from the belt and a funnel in two forms, Will be expected into the cylinder-feed mixer Through the revolving cylinder Materials in the cylinder show a spiral movement movement in the process of mixture formation is tumble accusation .Thus completing the mixed materials、 humid、 granulation and blending, Through mixing drum nesting end of the chute into the conveyor belt.
The mixing and rolling process of material is explored. Several characteristics of material motion in drum blender are carefully analysis. Influence factors on material mixing and balling is described. Analysis of the mixing drum cylinder parts of the mechanical properties. To provide the corresponding force method of calculation. Then the mixing of the Transmission stress analysis and calculation method are explored the main to the axis is checking at the safety performance, Ensure the reliability of transmission.
Keywords Drum blender; transmission; stress analysis; check
目录
摘要…………………………………………...……………………I
Abstract.............................................................................................II
第一章 绪论...................................................................................1
1.1 引言 ....................................................................................1
1.2 圆筒混合机的发展.......................................................................1
1.2.1圆筒混合机概述........................................................................3
1.2.2 圆筒混合机的工作原理.................................................................3
1.2.3 一次混合机..................................................................................3
1.3 圆筒混合机的结构.......................................................................4
1.3.1 入料装置.....................................................................................4
1.3.2 筒体部分.....................................................................................4
1.3.3 传动装置.....................................................................................5
1.3.4 支撑装置.....................................................................................5
1.3.5 给料装置.....................................................................................5
1.4 圆筒混合机的工艺布置...............................................................5
1.4.1支撑形式.....................................................................................6
1.4.2传动形式.....................................................................................6
1.5 影响物料混合及造球的因素.......................................................6
1.5.1原料性质的影响...........................................................................6
1.5.2加水润湿方法..............................................................................6
1.5.3混合、制粒效果..........................................................................7
1.5.4混合制粒时间..............................................................................7
1.5.5混合机的安装倾角及充填率.........................................................7
1.5.6添加物........................................................................................8
1.6 作用及意义...................................................................................8
第二章 圆筒混合机电机功率计算..............................................9
2.1 混合机传动总功率的分析...........................................................9
2.2 圆筒混合机内物料运动过程分析..............................................10
2.2.1物料转动所消耗功率的计算.........................................................10
2.2.2一次混合机的最佳参数选择.........................................................12
2.2.3二次混合机的最佳参数选择.........................................................12
2.3 计算物料重心上移所消耗的功率..............................................13
2.3.1计算物料滚动时内摩擦所消耗的功率...........................................15
2.3.2计算转动物料所消耗的功率........................................................15
2.4 计算克服支承系统的摩擦所消耗的功率..................................15
2.4.1计算托轮上所消耗的功率............................................................16
2.4.2计算挡轮上所消耗的功率............................................................17
2.4.3计算支承系统所消耗的总功率.....................................................17
2.5 计算总功率..................................................................................17
2.5.1圆筒混合机的电机功率计算.........................................................18
2.6 本章小结......................................................................................19
第三章 传动装置的总体设计...........................................................21
3.1 分析传动装置的工作情况..........................................................21
3.1.1传动装置示意图..........................................................................21
3.1.2传动形式....................................................................................21
3.2 根据传动装置的组成和特点确定传动方案..............................21
3.2.1圆柱齿轮减速器传动布置形式.......................................................22
3.3 初步确定减速器结构和零部件类型..........................................23
3.3.1确定传动装置的总传动比和分配各级传动比................................23
3.3.2计算传动装置的运动和动力参数..................................................24
3.3.3减速器的选择.............................................................................24
3.3.4减速器的校核.............................................................................25
3.3.5圆柱齿轮减速器箱体设计注意事项..............................................26
3.4 联轴器的选择.............................................................................26
3.4.1联轴器的附加力矩的计算............................................................26
3.4.2类型选择的条件..........................................................................27
3.4.3与电机轴相连的联轴器型号选择..................................................27
3.4.4与减速器输出轴相连的联轴器型号选择........................................27
3.5 传动齿轮和齿圈的设计.............................................................28
3.5.1 选定齿轮类型、精度等级、材料及齿数......................................28
3.5.2 按齿面接触强度设计..................................................................28
3.5.3 按齿根弯曲强度设计..................................................................30
3.5.4 几何尺寸计算............................................................................32
3.6 轴的结构设计.............................................................................32
3.6.1 轴结构设计的一般原则.............................................................32
3.6.2 初步确定轴的形状及外形尺寸...................................................33
3.6.3 初步选择滚动轴承....................................................................34
3.6.4 确定轴上圆角和倒角尺寸..........................................................35
3.6.5 求轴上的载荷...........................................................................35
3.6.6 按弯扭合成应力校核轴的强度...................................................39
3.6.7 精确校核轴的疲劳强度..............................................................39
3.7 本章小结....................................................................................42
第四章 设备的使用和维护..............................................................43
4.1 设备的使用................................................................................43
4.2 设备的维护................................................................................43
第五章 结束语.................................................................................44
参考文献..............................................................................................45
第一章 绪论
1.1 引言
混合设备是一种量大面广、品种繁多的机械产品,在化工、冶金、医药、造纸、化妆品、涂饰材料、食品、饲料及废水处理等行业都得到了广泛的应用,尤其是在化工行业使用最多。混合过程是一个使体系内物料的不均一度不断下降的过程。混合机械可分为两大类,即回转式混合机械和非回转式混合机械[1]。固体混合是指把两种或两种以上不同的固体粉体或粒料在干燥状态或有少量液体存在下,在外力下混匀,使不均匀度不断降低的一个随机过程。
在世界各国烧结厂的烧结原料作业中,不论一次混合还是二次混合均选用圆筒混合机。经过长期实践和改进,随着烧结机向大型化方向发展,与之相配套的圆筒混合机的规格也相应的增大,结构也有了很大发展,新型圆筒混合机就是这一发展的产物。
由于人们设计混合工艺和计算混料的能力仍有限,目前的设计主要依赖于经验,在整体结构上没有多大的变化。随着粉体混合过程数值模拟技术的发展,有助于人们对混合机理的认识。掌握先进的混合技术,开发和生产高效的混合设备对于国民经济有重大意义。
1.2 圆筒混合机的发展
目前, 世界烧结工业的发展趋向大型化和自动化。由于圆筒混合机运行可靠、产量高, 能够适应烧结设备向大型化发展的需要, 所以世界上大型烧结厂几乎无一例外的采用圆筒混合机作为一、二次混合设备。
一次混合机、二次混合机、烧结机和冷却机被称为烧结厂的四大主机。1985 年宝钢一期烧结设备全套引进, 1991 年宝钢二期虽然通过与日本合作制造四大主机等设备, 使国产化率提高到84%, 但混合机的国产化率仅达到 34%。其主要
原因是国内制造大型圆筒混合机筒体的技术尚不成熟。
我国混合机设备的发展是和烧结工业的发展同步的, 经历了从简单到逐步完善、从小型到大型化的发展历程。70 年代未, 我国已自行设计制造多种不同规格的圆筒混合机, 最大直径达3m,长度达12m, 并形成了系列产品, 满足了烧结机发展的需要。进入 80 年代, 尤其是宝钢引进的450m2 烧结机建成投产后, 有力地促进了我国烧结工业的发展, 圆筒混合机设计制造水平也有了新的提高, 自行解决了264m2 、300m 2以及435m2烧结机配套的大型圆筒混合机的设计制造技术。国内自行设计制造的圆筒混合机规格见表 1。
表 1 国内自行设计制造的圆筒混合机规格
国内虽然积累了多年制造圆筒混合机的经验, 但制造的混合机规格小, 与大型混合机相比技术要求低。滚圈与筒体的联接方式多为螺栓联接或滚圈套入筒体加垫片调整后焊接; 滚圈为铸钢件; 小型混合机筒体整体入炉热处理容易; 筒体精度可以用加工来保证。
目前在大型圆筒混合机制造的难点有如下几个方面:
(1) 规格大。二次混合机筒体单件重量为210t, 内径 5.1m, 长度 24.5m, 滚圈净重 42.5t, 规格为。
(2) 精度高。设计要求筒体滚圈和法兰的径向圆跳动用通光度检验不大于20mm;筒体法兰的径向圆跳动不大于20mm;端面圆跳动为0.3mm;齿圈架与齿圈的结合面对筒体公共轴线的垂直度为0.5mm。
(3)锻造焊接难。整体锻造滚圈在一般的万吨水压机上直接锻造也十分困难。目前, 国内拥有万吨水压机的厂家为上海重型机器厂、第二重型机器厂和第一重型机器厂。用上重厂和二重厂的万吨水压机生产需用体外锻造法, 并要相当的改
造费用; 在一重生产也要采取一定的措施。滚圈与筒体直接焊接, 筒体焊缝需退火, 且应保证筒体的同轴度和形位公差。大齿圈加工周期长、工艺复杂。
另外, 筒体和滚圈陆地运输也十分困难。
经过十多年的徘徊, 我国终于实现了大型圆筒混合机的自行设计、自行制造。武钢435m2烧结机配套圆筒混合机的设计制造成功, 使我国大型圆筒混合机的国产化率提高到了 94. 6%, 并使我国大型混合设备的制造加工水平取得了突破性进展。
1.2.1圆筒混合机概述
混合机是烧结厂主要设备之一,混合设备设置在配料设备与烧结机之间,为烧结机提供混匀、适合烧结的原料。根据原料性质不同,烧结厂的混合作业分为一次混合机和二次混合机,一次混合机主要作用是将物料混匀及湿润,二次混合机主要是对物料进行制粒,使物料满足成分均匀、水分适中、透气良好的要求。当烧结原料是以富矿粉为主时,粒度已满足烧结要求,混合作业主要目的是把混合料混匀和加水润湿,放置一次混合机即可。当烧结机含铁原料以细磨精矿为主时,由于粒度较细,导致混合料的透气性差,为改善透气性,必须在混合过程加强制粒,所以需采用二次混合。也有的在工艺流程中设置了滚煤机,称作为三次混合机。
1.2.2圆筒混合机的工作原理
烧结机用的各种原料组成的混合料由给料漏斗送入一次混合机内。混合机的筒体倾斜安装 ,传动装置中的电动机转动时 ,经舌簧联轴器、减速器、齿轮联轴器、小齿轮、大齿圈从而使筒体旋转。物料在筒体内因摩擦力的作用 ,使其随着筒体旋转方向向上运行 ,当提升到一定高度后由于物料自重作用又下来。并沿倾斜筒体的轴向朝低端移动。物料是在随筒壁反复提升和落下的过程中使物料中的各种成份和水分等混合均匀。物料经多次提升和抛落 ,形成一个螺旋状运动轨迹。向前推进至卸料端将物料排除出 ,整个一次混合过程完成。
1.2.3一次混合机
主要目的与作用是将物料混匀并湿润。
混合料的进料由皮带机和漏斗两种形式,将料送入圆筒混合机的进料端,通过筒体的旋转,物料在筒体内呈螺旋状运动,在运动的过程中使混合料形成“滚落”状,从而完成物料的混合、湿润、制粒、混匀后通过圆筒混合机排料端的溜槽排到皮带输送机上。传动形式主要分齿式传动和胶轮传动两种形式,按工艺需要而定。齿式传动一般适用于Φ3.2m以上规格圆筒混合机,胶轮传动一般适用于Φ3.2m以下规格圆筒混合机。但不能一概而论,也有Φ3m采用齿式传动,Φ3.2m采用胶轮传动的。
1.3圆筒混合机的结构
圆筒混合机由筒体、给(排)料端支承托轴、传动装置、喷水装置、排料端漏斗、给(排)料托辊罩、齿轮罩、检修平台等组成。
筒体支承在支承托辊上,由主电机通过硬齿面减速机及筒体上的大、小齿轮带动筒体旋转。为了便于检修和调整,在减速机主电机的对侧设有微动装置以使筒体能缓慢转动,并按要求准确定位。一次混合机和二次混合机除筒体内构造和洒水装置设置不同外,其余结构形式完全相同。组合型圆筒混合机的筒体更长一些,筒内前后段结构不同,前段采用一次筒内结构,后段采用二次筒内结构,其余部分和分离型的一、二次混合机并无差异。圆筒混合机示意图如图1-1所示。
1.筒体装置 2.托圈 3.洒水装置 4.传动装置
图1-1圆筒混合机示意图
1.3.1入料装置
1)料溜子入料;2)皮带机入料。
1.3.2筒体部分
筒体由滚圈和钢板制成的圆筒对焊而成 ,滚圈为整体锻造 ,滚圈为筒体的一部分。这种结构制造易 ,安装简单 ,筒体刚度大 ,避免滚圈与筒体之间在运转时产生滑动现象 ,滚圈寿命长。其断面采用实心矩形 ,形状简单 ,便于制造 ,但对滚筒精度要求很高 ,它直接影响设备的安装和运转要求。设计的高要求必须在制造中采取先进的工艺措施来实现 ,特别是为保证滚筒各段的同心度要求在组焊前各段在接头处设“定中心块 ”的方法定中心 ,调整好同心度后用螺栓联接固定后再进行焊接 ,这样保证滚圈 ,齿圈同心度要求 ,使端摆 ,径跳达到最小范围。大齿圈为铸钢分两半制造 ,用 4个螺栓联接成一体 ,再由 20个铰制配合螺栓和 16个普通螺栓与筒体上的固定架联接 ,安装时根据筒体上设置的专用基准进行调整。筒体内铺有耐磨橡胶衬板,在入口的1.5m段安装与混合机轴线成15°倾角的导料橡胶板 ,作为混合料向排料端移动导向装置 ,使给料端不堆料和散料 ,其余部分的橡胶衬板及压条与筒体轴线平行。橡胶衬板的安装必须在现场进行 ,严格按设计圆周等分先在筒体内焊好螺柱 ,将各衬板及压条就位后再拧紧螺母 ,这样安装能使各块衬板间予紧力相等。能有效地缓解冲击震动,降低噪音,保护筒体,为提高造粒效果,筒体内采用锥形逆流复合导流。轮带与筒体采用加铁焊接连接型式,加强筒体刚性又便于安装检修。
1.3.3传动装置
减速机采用硬齿面减速机,满足传动要求,减少事故维修量,电动机采用YR、 JR、YTS等。(左装右旋)左装右旋开式齿活动,大齿圈与筒体采用刚性螺栓把合结构,结构简化,传动平稳,又易于安装检修。
出料装置:采用出料与筒体偏心形式,有利于出料,又起到使出料寿命大大提高的效果。
1.3.4支撑装置
设有两挡支撑,采用强力型,二挡统一,有利于制造更换。
1.3.5给料装置
入料槽采用铸石衬板,提高导料槽的耐磨性,为确保下料通畅,导料槽下安装脉 冲震打器,为检修方便设有焊接平台。
1.4圆筒混合机的工艺布置
对于中小型烧结厂通常是把一次混合机配置在地坪上,而把二次混合机配置在烧结厂房顶层 上,这样避免了混合机制粒后混合料由长距离输送可能引起的小球破损以及湿度、温度波动等问题影响烧结厂的产量和质量。 对于大型烧结厂圆筒混合机,因转动质量和接触压力很大,不宜采用上述型式混合,最好把一、二次混合机都设置在地坪上。
1.4.1支撑形式:
圆筒混合机支撑形式对于金属托辊都设置两组,分别设置在轴向和径向,对称布置。对于大型圆筒混合机都以轮胎来代替金属托辊的橡胶轮胎传动,其设置一般都是大于两组或四组,支撑沿轴向、径向对称布置,这种对称布置是沿用了金属托辊而设计的。这种设计还应进行深入的探讨。
1.4.2传动形式
由于圆筒混合机这种设备很庞大。电机、减速机传动系统都设计在筒体一侧的下部,对金属托辊设计两组,一侧为主动,另外一侧为被动,筒体在传统设计时朝着传动侧转动,由于筒内物料的运动偏离筒体中心,使得筒体传动侧受到的力较大,其摩擦阻力矩和弹性变形阻力矩较大,因此筒体转动时需要克服的摩擦阻力矩和弹性变形阻力矩也较大,使得筒体振动,电机电流增大,使减速机磨损胶合。因此有必要对传动形式进行优化。

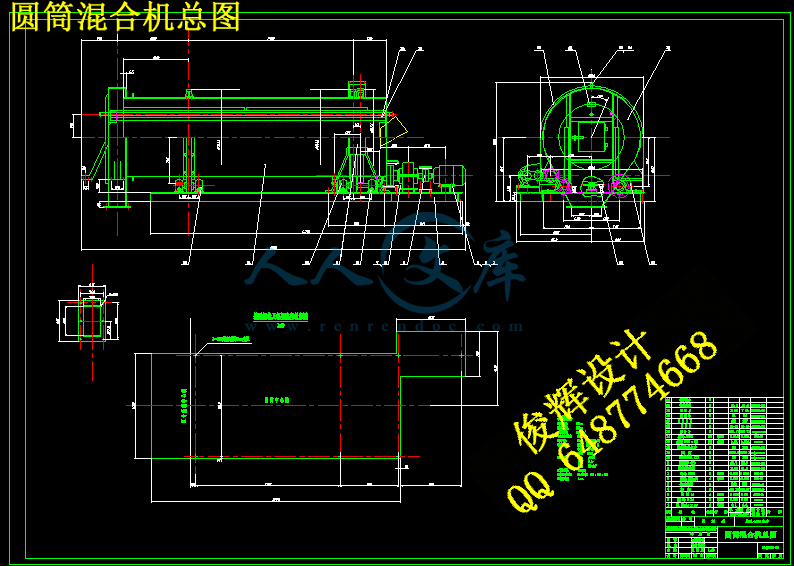


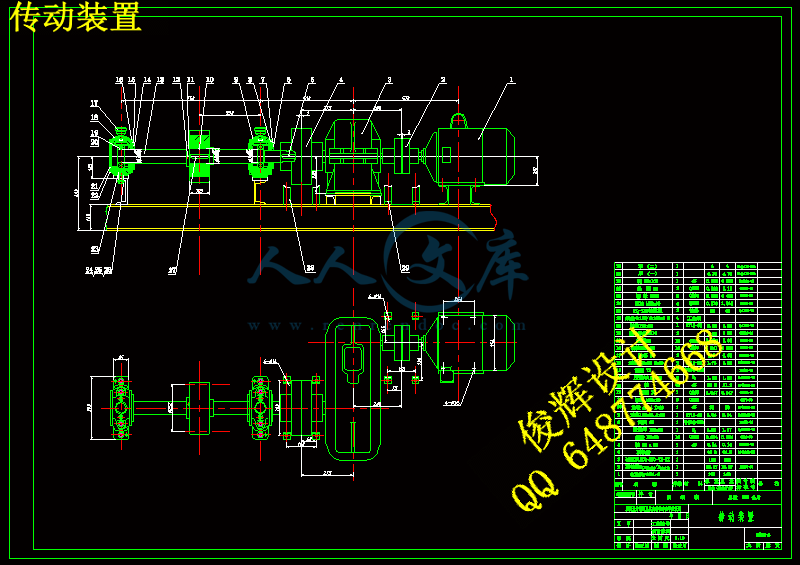




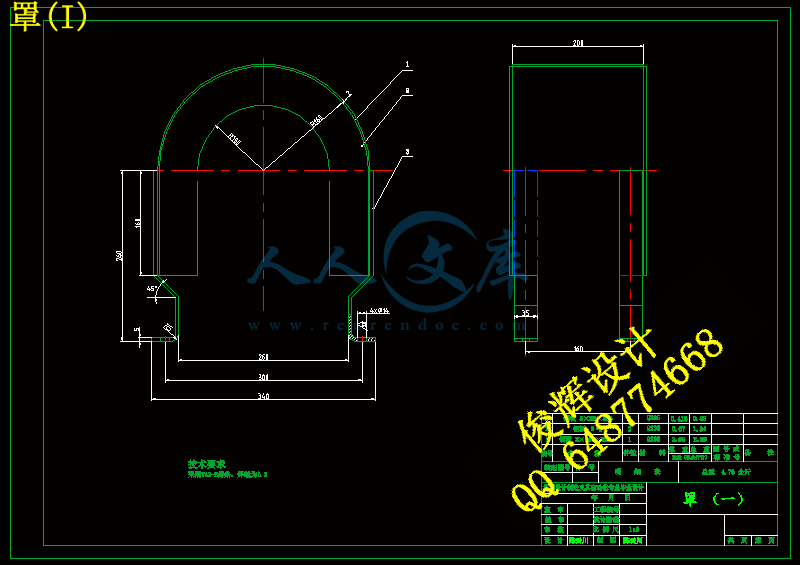
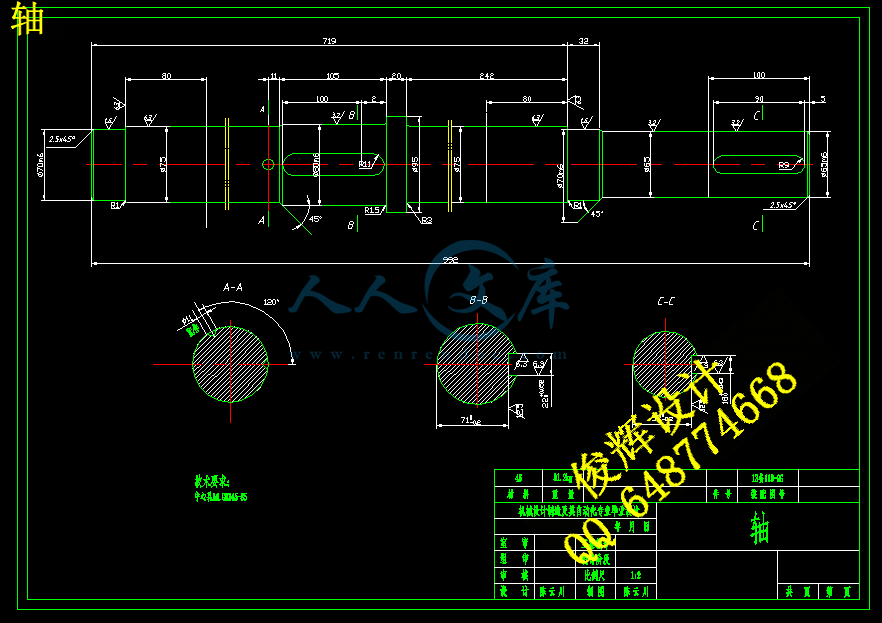