人人文库网 > 图纸下载 > 毕业设计 > 山东滨州裕华化工厂有限公司年产8万吨甲基丙烯酸甲酯项目【设计说明书+可行性报告+设备设计选型计算书+CAD图】
山东滨州裕华化工厂有限公司年产8万吨甲基丙烯酸甲酯项目设备设计选型计算书.docx
山东滨州裕华化工厂有限公司年产8万吨甲基丙烯酸甲酯项目【设计说明书+可行性报告+设备设计选型计算书+CAD图】
收藏
资源目录
压缩包内文档预览:
编号:17898794
类型:共享资源
大小:27.63MB
格式:RAR
上传时间:2019-04-19
上传人:hon****an
认证信息
个人认证
丁**(实名认证)
江苏
IP属地:江苏
20
积分
- 关 键 词:
-
设计说明书+可行性报告+设备设计选型计算书+CAD图
山东滨州裕华化工厂有限公司
化工有限公司
- 资源描述:
-
1.1概述
本项目是为山东省滨州市裕华化工厂新建一座8万吨/年的甲基丙烯酸甲酯生产装置。厂区选址于山东省滨州市化工园区内,此地依河傍海,交通便利,并且有较多的石油化工厂,资源丰富,是政府发展经济的重点地区。
1.2设计依据和准则
1.2.1设计依据
(1)2018年“东华科技-陕鼓杯”第十二届全国大学生化工设计竞赛设计任务书》;
(2)《化工工厂初步设计说明书内容和深度规定》(HG/T20688-2000);
(3)《中华人民共和国环境保护法》和《中华人民共和国劳动安全法》等相关的国家法律、法规;
(4)《石化和化学工业“十三五”发展规划》;
(5)中国石油和化学工业协会文件中石化协产发(2012)115号“关于印发《化工投资项目可行性研究报告编制方法》(2012修订版)、《化工投资项目申请报告编制办法》和《化工投资项目资金申请报告编制办法》(2012修订版)的通知”;
(6)山东省滨州市滨北工业园区有关供水、供电、项目征用土地意见和建设项目环境保护意见的批文及资料。
1.2.2设计准则
(1)认真贯彻落实可持续发展战略和国家基本建设的有关政策、法规,合理安排建设周期,严格控制工程建设项目的生产规模和建设投资;
(2)严格遵循现行消防、安全、卫生、劳动保护等有关规定、规范,保障生产安全顺利进行和操作人员的安全;
(3)选用成熟可靠的先进技术,以提高生产效率,降低能耗和生产承办,减少污染,保证装置运行和产品质量的稳定性,增强产品的竞争力;
(4)坚持安全生产与环境保护并重,设计中选用清洁生产工艺,在生产过程中减少“三废”排放,执行国家和地区的有关环保政策,对生产中的“三废”进行处理,并达到国家和地区规定的排放标准;
(5)贯彻工厂规模大型化、布置一体化、生产装置露天化、公用工程社会化、引进技术与创新相结合的项目建设方针。
(6)坚持体现“社会经济效益、环保效益和企业经济效益并重”的原则,按照国民经济和社会发展的长远规划,行业、地区的发展规划,在项目调查、选择中对项目进行详细全面的论证。
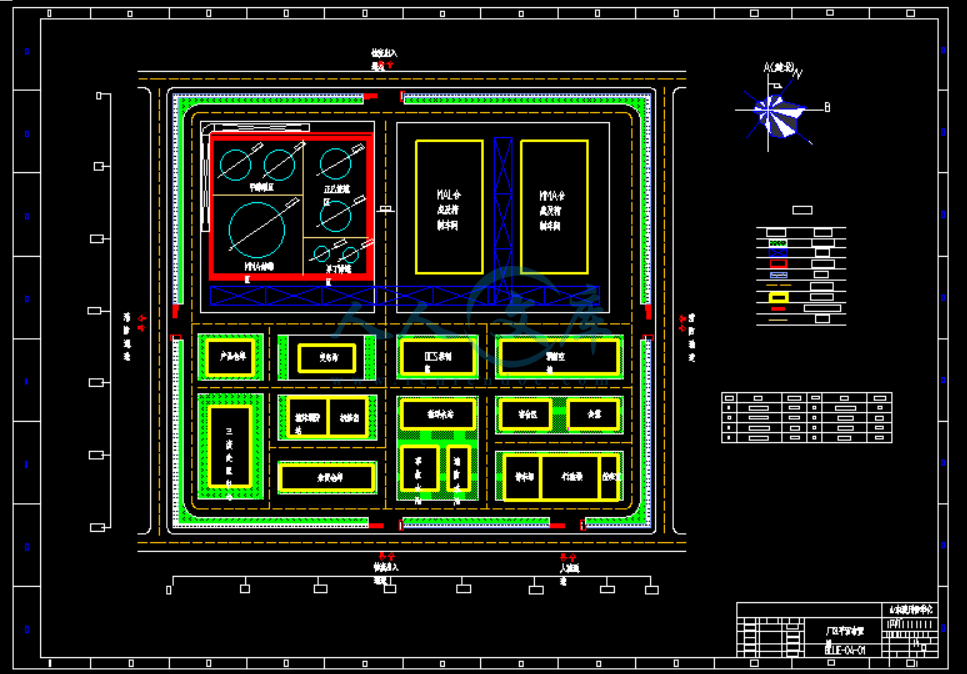
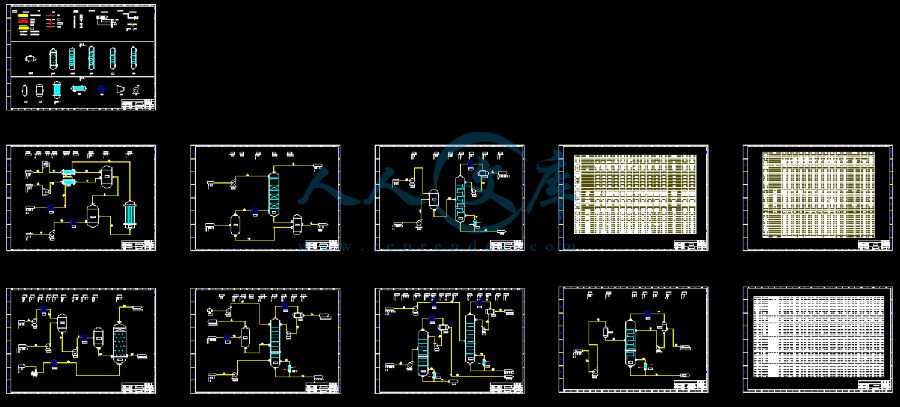

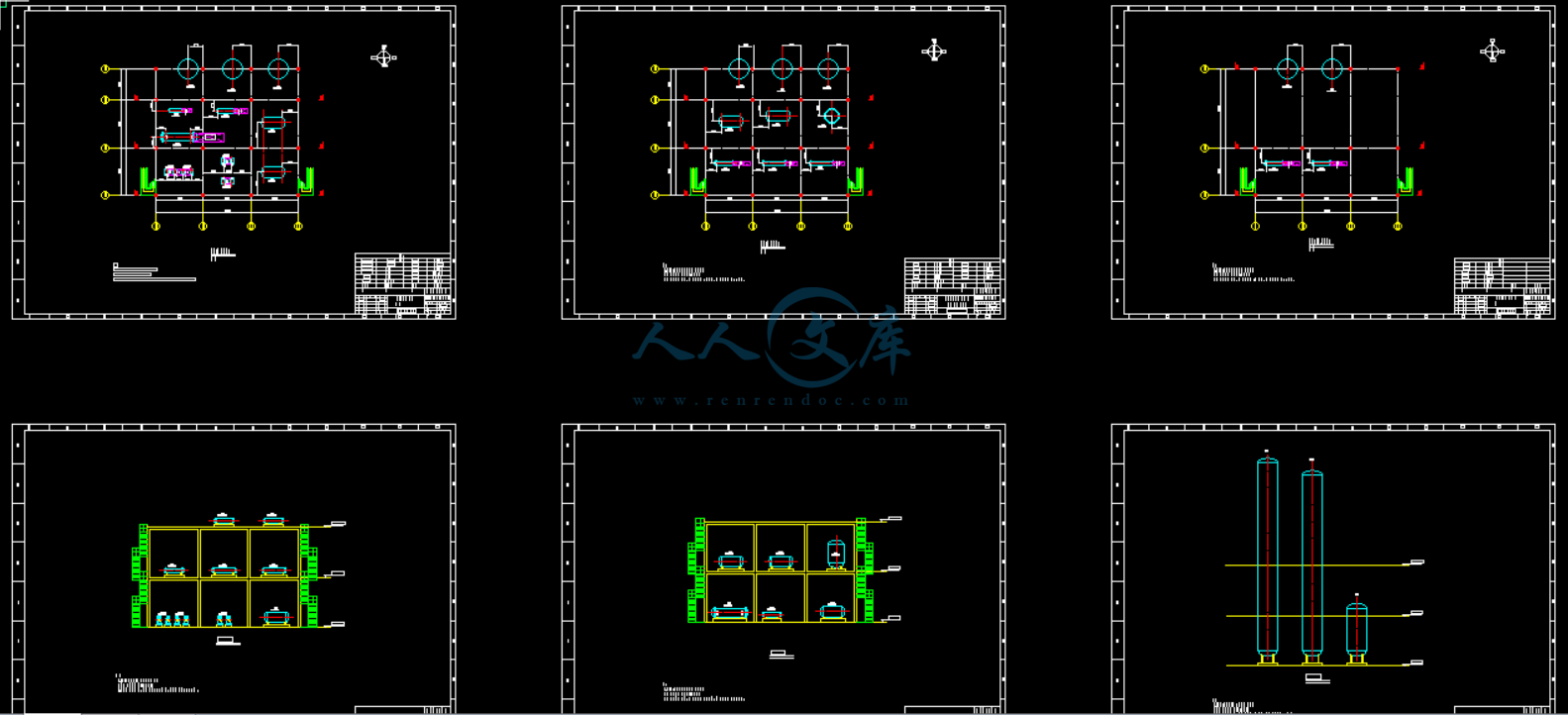
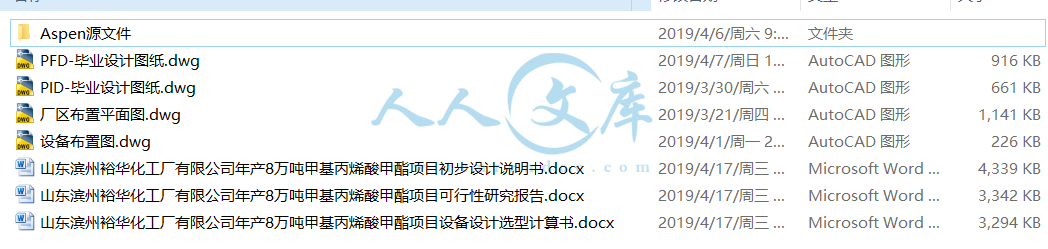
- 内容简介:
-
山东滨州裕华化工有限公司年产8万吨甲基丙烯酸甲酯项目 设备设计计算书山东滨州裕华化工厂有限公司年产8万吨甲基丙烯酸甲酯项目设备设计选型计算书 第一章 总述1.1 过程设备的选型目的化工设备的工艺设计与选型是在物料衡算和热量衡算的基础上进行的,其目的是决定工艺设备的类型、规格、主要尺寸和数量,为车间布置设计、施工图设计及非工艺设计项目提供足够的设计数据。1.2 过程设备的基本要求过程设备基本的要求是满足工艺要求的同时,满足安全性与经济性。对于工艺上所要求的温度、压力、液位、流量等都需要过程设备来实现。在满足工艺要求的同时,过程设备也必须保证有足够的强度,不会在操作过程中遭到破坏。经济性包括经济的制造过程,经济的安装、使用与维护,以及设备的长期安全运行。在满足工艺要求的前提下,为了确保安全与经济,过程设备应满足以下基本要求。首先,结构合理,安全可靠。过程设备所有部件都必须具有足够的强度、刚度和稳定性,可靠的密封性和一定的耐久性。其次,设备必须具有先进的技术经济指标,技术经济指标是衡量过程设备优劣的重要参数。再次,运转性能好,操作简单,运转方便;最后,还要具有优良的环境性能。上述要求很难全部满足,设计选用时应针对具体问题具体分析,满足主要要求,兼顾次要要求。1.2.1设计原则及依据(1)锅炉和压力容器用钢板GB 713-2008;(2)奥氏体不锈钢焊接钢管选用规定HG/T 20537.1-1992;(3)化工装置用奥氏体不锈钢大口径焊接钢管技术要求HG/T 20537.4-1992;(4)工艺系统工程设计技术规定HG/T 20570.9-1995;(5)钢制化工容器设计基础规定HG/T 20580-2011;(6)钢制化工容器材料选用规定HG/T 20581-2011;(7)钢制化工容器强度计算规定HG/T 20582-2011; (8)钢制化工容器制造技术要求HG/T 20584-2011;(9)化工设备基础设计规定HG/T 20643-2012;(10)承压设备无损检测(合订本)JB/T 4730.16-2005;(11)石油化工塔型设备基础设计规范SH/T 3030-2009;(12)管壳式换热器GB 151-1999;(13)石油、重化学和天然气工业用离心泵GB/T 3215-2007;(14)离心泵效率GB/T 13007-2011;(15)双锥回转真空干燥机HG/T 3682-2000;(16)石油化工泵用过滤器选用、检验及验收SH/T 3411-1999;(17)化工管道过滤器HG-T 21637-1991;(18)厢式压滤机和板框压滤机JB/T4333-2005;(19)结晶器JB/T 20068-200;(20)工艺系统工程设计技术规定气-液分离器设计HG/T 20570.8-95;(21)烟道式余热锅炉通用技术条件JB/T 6503-1992;(22)过滤机型号编制方法GB/T 7780-2005;1.3 过程设备的类别化工设备从从工艺设计的角度可分为两类,一类称定型设备或标准设备,这是由一些加工厂成批成系列生产的设备,通俗地说,就是可以买到的现成的设备,如泵、反应釜、换热器、大型储罐等。另一类称非定型设备或非标准设备,是指规格和材料都是不定型的,是根据工艺要求、通过工艺计算及设备专业设计人员设计的特殊设备,可由有资质的厂家制造,如反应器、塔器等。1.4 过程设备设计与选型原则1.4.1合理性即设备必须满足工艺需求,与工艺流程、生产规模、工艺条件及工艺控制水平相适应,在设备的许可范围内,能够最大限度地保证工艺的合理和优化并运转可靠。1.4. 2 可靠性和先进性工艺设备的型式、牌号多种多样,实现某一化工单元过程,可能有多种设备,要求设备运行可靠。在可靠的基础上考虑先进性,便于连续化和自动化生产,转化率、收率、效率要尽可能达到高的先进水平,在运转的过程中,波动范围小,保证运行质量可靠,操作上方便易行,有一定的弹性,维修容易,备件易于加工等。1.4.3 安全性设备的选型和工艺设计要求安全可靠、操作稳定、无事故隐患,对工艺和建筑、地基、厂房等无苛刻要求,工人在操作时劳动强度小,尽量避免高温高压高空作业,尽量不用有毒有害的设备附件、附材,创造良好的工作环境和无污染。1.4. 4 经济性设备的选择力求做到技术上先进,经济上合理。1.5 设计与选型的主要内容1.5.1 确定单元操作所需的设备类型这项工作应与工艺流程设计结合进行。1.5.2 确定设备的材质根据工艺操作条件(温度、压力、介质性质)和工艺要求确定符合要求的设备材质。1.5.3 确定设备的设计参数设备的设计参数是由工艺流程设计、物料衡算、热量衡算、设备的工艺计算多项工作得到的。对塔设备,需要确定进出口物料的流量、组成、温度、压力、塔径与塔的材质、填料类型与填料高度或塔板类型与塔板数等,对于精馏塔还要确定塔顶冷凝器和塔底再沸器的热负荷、换热流体的种类等;对换热器,则需要知道热负荷、换热面积、冷热流体的种类及流量。1.5.4 确定标准设备的型号或牌号及数量对已有标准图纸的设备,确定标准图的图号和型号。对非标设备,向化工设备专业设计人员提出设计条件和设备草图,明确设备的型式、材质、基本设计参数、管口、维修安装要求、支承要求及其他要求(如防爆口、人孔、手孔、卸料口、液面计接口等)。1.5.5 编制工艺设备一览表在初步设计阶段,根据设备工艺设计的结果,编制工艺设备一览表,可按非定型工艺设备和定型工艺设备两类编制。初步设计阶段的工艺设备一览表作为设计说明书的组成部分提供给有关部门进行设计审查。第二章 反应器设计2.1概述化学反应过程和反应器是化工生产流程的中心环节,反应器的设计往往占有重要的地位。由于反应器单元内部涉及很多复杂的过程,如:热量的传递,温度的变化,反应速率的不稳定,这都将影响产品的产量和质量。所以反应器一直以来都是化工设计的一个难题。化学反应器是将反应物通过化学反应转化为产物的装置,是化工生产及相关工业生产的关键设备。由于化学反应种类繁多,机理各异,因此,为了适应不同反应的需要,化学反应器的类型和结构也必然差异很大。反应器的性能优良与否,不仅直接影响化学反应本身,而且影响原料的预处理和产物的分离,因而,反应器设计过程中需要考虑的工艺和工程因素应该是多方面的,一个适合反应体系的反应器可大大提高目标产物的转化率且能保证稳定的操作环境。反应器的设计主要包括:(1)反应器选型;(2)确定合适的工艺条件;(3)确定实现这些工艺条件所需的技术措施;(4)确定反应器的结构尺寸;(5)确定必要的控制手段。2.2 反应器类型反应器按结构大致可分为管式、釜式、塔式、固定床和流化床等。表2.1 部分反应器特性型式适用的反应优缺点管式气相;液相返混小,所需反应器容积较小,比传热面大;但对慢速反应,管要很长,压降大釜式液相;液-液相;液-固相适用性大,操作弹性大,连续操作时温度、浓度容易控制,产品质量均一,但高转化率时,反应容积大固定床气-固(催化或非催化)相返混小,高转化率时催化剂用量少,催化剂不易磨损;传热控温不易,催化剂装卸麻烦流化床气-固(催化或非催化)相;特别是催化剂失活很快的反应传热好,温度均匀,易控制,催化剂有效系数大;粒子输送容易,但磨耗大;床内返混大,对高转化率不利,操作条件限制较大反应器的形式是由反应过程的基本特征决定的。本反应流程中,第一个反应的原料(氧气,异丁烷,水)以气相进入反应器,在高温下反应,故属于气固相反应过程。第二个反应的原料(MAL,甲醇,氧气)以液相与气相进入反应器,在负压下进行反应,故属于气液固三相反应过程。2.3固定床反应器固定床反应器又称填充床反应器,催化剂颗粒装填在反应器中,呈静止状态,是化工生产中最重要的气固反应器之一。常用的固定床反应器下部设有多孔板,板上放置固体催化剂颗粒。流体自反应器顶部通入,流经催化剂床层后自反应器底部引出。催化剂颗粒保持静止状态,故称之为固定床反应器。2.3.1 固定床反应器的操作原则1.为防止流体带出,流体一般由上向下通过床层;2.为保证床层适宜的温度条件,床内布置各种换热元件;3.为防止流动压降过大,催化剂粒径不能过小,为减少内扩散的影响,粒径不能过大。适宜粒径为2-6mm。4.为防止近壁出现沟流,催化剂的粒径应小于管径的8倍,一般范围2.3.2 固定床反应器的优点返混小固定床反应器的催化剂床层内反应流股的流动接近于平推流,与其他反应器相比几乎不存在返混,故可以有效地避免过度反应和反应不足,保证了反应产品收率,提高反应速率,完成同样的生产能力时所需的催化剂用量和反应器容积都较小。催化剂机械损耗小固定床反应器中催化剂排列致密,形成固定床层,催化剂颗粒之间不存在相对移动,使催化剂颗粒间的机械能损失达到最小化。便于控制固定床反应器中的催化剂以固定床层的形式固定在反应器中,因此可以严格控制反应原料的停留时间,特别有利于提高反应的选择性与转化率。2.3.3 固定床反应器的缺点传热差,容易飞温固定床反应器中,催化剂颗粒紧密堆砌,以固定床层的形式装填在反应器中,传热形式以热传导为主,导致反应器床层传热效果较差,对于强放热反应,如果不能及时移走反应产生的大量反应热,就会很难控制反应的热点,从而导致飞温,产生严重后果。催化剂更换困难固定床反应器的催化剂床层由固定圈固定,两端使用瓷球填充,更换催化剂的时候必须停产,将反应器卸下,更换麻烦,并影响生产,不适用于容易失活的催化剂。工业中常用的固定床反应器有两种形式:绝热式反应器和换热式反应器。对于强放热反应系统,如果系统产生的热量不能及时排放掉,势必导致反应系统温度升高。当反应系统温度超过某限度时,对于转化率、选择性、催化剂活性和寿命等带来不良影响。因此,强放热反应系统温度控制是固定床反应器设计和安全操作的主要问题之一。与绝热式固定床反应器相比,列管式固定床反应器能够对外换热,便于控制反应温度,使反应达到较高的转化率,因而适应性较强,应用比较广泛。2.3.4 列管式固定床反应器的特点1.当反应热不太大或单程转化率不太高时,催化床层温度易控制,整个催化床层内温度分布均匀。另一方面,由于传热面积与床层体积比大,传热迅速,床层同平面温差小,有利于延长催化剂使用寿命。2.能准确、灵敏地控制反应温度,催化剂床层的温度可通过调节汽包蒸汽压力来控制。3.以较高能位回收反应放出的热量,热量利用合理。4.设备紧凑,开停车方便。5.合成反应过程中副反应少,杂质含量少,产品质量高。该类反应器的不足之处是对管壳结构机械设计要求高,设备复杂,制作困难,对材料及制造方面的要求较高。列管换热式固定床反应器,虽然可以通过管壁与壳程的换热介质换热但是由于热量的生成速率与移走速率之间存在差异,使得反应温度沿轴向存在分布。在一定条件下,此分布对诸如反应器入口反应物的浓度、气速、冷却温度等操作参数均十分敏感,操作条件的微小变化,将引走反应系统温度的较大变化,反应热迅速增加,如果产生的热量不能及时移走将导致反应系统温度跳跃式的增加,使反应系统失去控制,即造成飞温问题。为了增大单位床层体积所具有的传热面积,一般列管式固定床反应器有成千上万根列管并联联结。各列管的操作参数和床层的温度、浓度分布接近。因此只要根据反应条件计算出一根列管的床层温度与浓度分布,确定其所须床层高度和催化剂装填量,就可求得整个反应器所须催化剂量,并且确定其合适的操作参数,核算传热介质的流量,避免反应飞温现象的发生。2.4流化床反应器流化床反应器,又称沸腾床反应器。反应器中气相原料以一定速度通过催化剂颗粒层,使颗粒处于悬浮状态,并进行气固相反应。流态化技术在工业上最早应用于化学反应过程。到20世纪40年代,催化裂化(FCC)实现工业化后,流化床反应器在工业上的应用得到了迅速发展,目前已广泛应用在催化裂化、费托合成等工业流程中,成为炼油、能源、医药、生物工程和环境保护等众多工业过程系统中的重要反应装置。流化床反应器具有以下优点:(1)传热效果好流化床反应器中,流化的催化剂颗粒在床层内做着强烈的循环运动,保证了气-固、固-固和料-壁之间的有效接触和混合,使它们之间有着较高的传热速率。同时反应器中这种混合效应可以使反应器内温度均匀,避免发生“热点”和“飞温”现象。所以流化床反应器十分适合强放热和热敏感的流程。可实现同体物料连续进出流化床呈现拟流体流动特性,使固体颗粒能够方便地加入和移出反应器。在催化剂失活的时候,可以顺利的移出失活催化剂、加入再生催化剂,可使催化剂在反应器与再生器之间实现循环,在生产的同时执行反应和再生操作。此外,这种流动特性也可以通过固体颗粒携走大量的反应热。(2)压降低与同定床相比,同样颗粒的粒度和表观流化气速相同时,催化剂颗粒在悬浮状态下的压降耍低很多。流化床反应器存在以下缺点:(3)返混严重流化床反应器中颗粒的流动更接近全混流,气体又容易发生“旁路”现象,所以与固定床反应器相比,其中反映物的转化率比较低,对催化剂的选择性也有影响,容易有反应物由于停留时间过长或过短而导致过度反应和反应不充分的现象。对催化剂颗粒要求严格为了达到催化剂颗粒的悬浮状态,对制作流化床反应器的催化剂颗粒的粒度和粒度分布都有一定的耍求。一般来说,粒径小于3X104m或大于3X103m的颗粒都由于无法流化而无法采用。(4)易造成催化剂损失流化床反应器中,催化剂颗粒之间互相接触碰撞,会对催化剂造成机械损失,加速催化剂老化失活。在生产中,还会有部分催化剂随着气相反应产物流出反应器,造成催化剂损失,同时还会对下游的分离工艺造成影响,增加分离设备投资。2.5 MAL氧化反应器的设计2.5.1 反应方程式主反应: 副反应: 2.5.2动力学方程根据文献所述,动力学方程为:两边同时取对数,即:且有:式中:A:指前因子 E为活化能,cal/(gmol)r为反应生成MAL的反应速率,lb mol/(ft3sec)cIB为异丁烯的气相浓度,lb mol/ft3;k为异丁烯转化率的一级速率常数,sec-1;R为通用气体常数,cal/(gmol)T为反应温度,K;2.5.3催化剂本反应选择Mo-Bi系复合氧化物为催化剂。其催化剂物性参数见下表。表2.2催化剂物性参数项目数值项目数值颗粒密度Dp=5.5 mm比表面Sp=4.61g2/g堆积密度b=0.60g/ml孔体积Vv=0.121ml/g视密度b=0.95g/ml空隙率=0.6314异丁烯催化氧化机理见下图:图2.1 异丁烯氧化机理2.5.4反应器类型的选择本工艺可以选用连续反应器,在连续反应器中主要有流化床、鼓泡流化床、固定床。流化床虽然可以增加两相间的接触面积,传热面积以及具有传质速率快等特点,但是由于催化剂颗粒的剧烈运动,造成固体颗粒与流体的严重返混,导致反应物浓度下降,转化率下降,催化剂颗粒的剧烈运动也造成了催化剂破碎率增大,增加了催化剂的损耗。同时催化剂还会与器壁发生剧烈碰撞,易造成设备与管道的腐蚀,增大设备损耗。固定床中催化剂颗粒固定不动,返混少,反应物的平均浓度高,反应速率较快,可以克服上述流化床的缺点。除此之外,固定床层内的流体流动接近平推流,有利于实现较高的转化率与选择性;可用较少量的催化剂和较小的反应器容积获得较大的生产能力;结构简单、催化剂机械磨损小,适合于贵金属催化剂;反应器的操作方便、操作弹性较大。基于异丁烯/氧气合成甲基丙烯醛反应过程中热效应很大,而适宜的反应温度为300-400,反应选择列管式固定床反应器进行模拟计算,管内装填固体颗粒催化剂,管外走换热介质。2.5.5反应器物料信息(1)反应器进出口物料表2.3反应器进出物流信息表反应器进口反应器出口温度380380压力MPa0.150.15气相分率11摩尔流量kmol/h2228.142232.25质量流量kg/h66477.766477.7体积流量m2/h80686.280822.2Mass Flows kg/hrIB75000O213175.98339.56N243393.343393.3CO028.456CO20588.287H202408.465010.93MAL09117.17Mole Flows kmol/hrIB133.6720O2411.764260.621N21549.021549.02CO01.01591CO2013.3672H20133.69278.149MAL0130.076(2)反应压力的确定目前已经工业化或者半工业化的制取甲基丙烯醛的资源化使用工艺中,均是在微正压或者正压下反应。本工艺选择0.15MPa。(3)反应温度的确定异丁烯制甲基丙烯醛反应是放热反应,低温有利于提高反应的平衡转化率。但是反应要求气相反应,且过低的温度降低反应速度,参考相关文献对异丁烯制甲基丙烯醛的研究,催化剂的反应温度为300-400,同时在380时,异丁烯的转化率和甲基丙烯醛的选择性最为合适,所以选择380作为异丁烯制甲基丙烯醛的反应温度。(4)反应条件进料温度为380,反应温度为380,反应压力为0.15MPa。反应器为列管式固定床反应器。根据本工艺实际换热介质,2取2000kJ/(m2hK)。催化剂床层空隙率B为0.6314。反应进口流量V0=80686.2m3/h。在380,0.15Mpa下反应混合物有关物性数据如下:热导率=0.0355701J/msK 粘度=2.358210-5Pas密度 =1.03089kg/m3 比热容Cp=35.571J/(molk)异丁烯转化率97.31% 甲基丙烯醛的选择性92.34%。2.6反应器结构设计2.6.1催化剂填充量根据反应器空时(2800)计算催化剂填充量:VR,=VONSVVON=80686.2*273273+380*150101.325=49937.10即有: VR,=VONSV=49937.102800=17.83m3式中:VR 催化剂的填充量,m3VON 原料气体体积(标准)流量,m3/hSV 体积空时,h-12.6.2反应器管长度的设计:取空床速度为1.5m/s,则床层截面积为:AR=VON/u0=80686.2/1.5/3600=14.94m2则催化剂床层高度为:HR=VR/AR=17.83/14.94=1.193m因为催化剂床层孔隙率为0.6314,则反应器管长为:L=(1+0.6314)HR=1.6314*1.193=1.9474m取整为2m2.6.3管束尺寸和反应管的排列选取工业上所用的 35 2.5的列管,则单管催化剂体积为:V1=1/4dl=1/4*3.14*(35-5)*10-32*8=5.6549*10-3m3则管数为:n=VR/V1 =17.83/5.6549*10-3=3153取整,则管数为3153根。每个反应器列管采用正三角形排列,反应器列管的布置与普通换热器有很大不同。首先,管数中央水循环受阻,传热恶化,温度分布不均,故此区域不布管;其次反应管的排管按30划分为12个区间,整个管板由30区间阵列而成。取中央不布管区域直径为200mm。图2.2反应器列管分布图按三角形排列,取管心距为t=1.25d0=1.25*0.03=0.0375m则单管所占的面积为s=3/2*t2=1.2178*10-3m2则反应器的直径为D=3153*1.2178*0.001+0.007850.785=2.214m则取直径为2400mm反应床层压降式中,P 压力,PaH 床层高度,mf修正摩擦系数;流体密度,kg/m3uo 空塔气速,m/sdp催化剂颗粒的当量直径,mB层床空隙率。 流体的绝对粘度,pa.sl层床高度;b系数,采用Ergun提出的数值,a=1.75,b=150根据前面计算可知,u0=1.5m/s,B=0.6314,=1.03089kg/m3= 2.358210-5Pas,dp=5.5 mm,H=1.93m带入数值进行计算可得, 即:0.9028kPa压降小于入口压力的10%,符合常理。2.7机械强度的计算2.7.1设计的选材考虑到使用温度、需用应力、价格、供货情况及材料的焊接性能等,在设计中选取:壳体、列管、管板、封头、法兰、支座、折流板材料为Q345R。2.7.2板厚的计算根据流体进出口温度,选择流体的设计温度为380.设计压力为:P=1.1Pw=1.1*0.15=0.165由于本操作是在高温下进行,所选材料为耐高温材料Q345R焊接方式:选为双面焊对接接头,100%无损探伤,焊接系数为1根据GE0105654压力容器用钢板和GB3531低温压力容器用低合金钢板规定可知,对应C1=1,腐蚀裕量C2=2mm,焊接方式选用双面焊接。材料的许用压力t=185MPa则厚度按下式计算:计算厚度=Di2t-=0.165*24002*185*1-0.165=1.070mm设计厚度:c=+C2=1.07+2=3.07mm名义厚度:n=+C1+C2+=1.07+1+2+=15mm 2.7.3气压试验所谓气压试验,就是以气体作为工作介质,在容器内施加比它的设计压力还要高的试验压力,以检查容器在试验压力下是否有渗漏、明显的塑性变形以及其他缺陷。Q345R的屈服压力t=185MPa,x=205MPa气压试验:PT=P+0.1=0.15+0.1=0.25MPaPT=1.15P=1.15*0.15=0.1725MPa两者之间取较大值,所以取PT=0.25MPa气压试验强度校核满足公式:t=PTDi+e2e=0.25*2400+152*185=1.004MPa0.8*205=164MPa所以气压试验满足强度要求。取反应器筒体直径2430mm,厚度为15mm,内径为2400mm。2.8壳程设计2.8.1壳程直径:每个反应器管数为3153根,每个管采用错列正三角形排列。采用焊接法,则管心距为:横过管束中心线的管数为:nc=1.1*n=1.1*3153=61.7662壳体内径为:D=tnc-1+2e其中e为管束中心线最外层管的中心至壳体内壁的距离,一般情况下取e=11.5d0本工艺取e=d0=0.03m则壳体内径为:D=0.0375*62-1+2*0.03=2.3475m所以壳体内径为D=2.4m2.8.2外壳壁厚:由于反应器为内压容器,其厚壁的计算公式为:S0=pD2t-p+C1+C2式中,S0壳体厚度,mmP操作时可能的最大压力,内压容器取P=(11.1)PW,Pa;t材料在操作温度范围内的许用应力,Pa;焊接系数,单面焊取0.65,双面焊取0.85;C2腐蚀裕量,根据材料和介质的腐蚀性质在18mm之间选择;D为壳体内径,mm。由于本操作在温度为380,压强在0.15MPa下进行操作,选用材料为Q345R,根据GB 6654压力容器用钢板和GB 3531低温压力容器用低合金钢板规定,腐蚀裕量C2=2mm,焊接方式选用双面焊接。操作时可能的最大压力为P=1.1PW=0.151.1=0.165MPa,Q345R的许用压力t =185MPa,焊接系数=1,带入计算得:S0=Pd2t-p+C=0.165*24002*185*1-0.11+2=3.07mm根据=3.07查表得负偏差C1=0.3mm,S0=+C1=3.07mm+0.3mm=3.307mm圆整后取S0=4mm。经校核后,取15mm所以反应器外径:D0=2400+2*15=2430mm2.8.3反应器筒体长度列管长度:由工艺计算中可知,列管长度为3200mm。筒体顶部空间:根据压力容器手册, Ha=1m;筒体底部空间:根据压力容器手册, Hb=1m;由以上可得:反应器筒体长度 H=L+Ha+Hb=3200+1000+1000=5200mm=5.2m2.9管板、管箱、反应列管的连接结构设计2.9.1连接结构壳体与管板的壳体与管板的连接形式,分为两类:一是不可拆式,如固定式管板换热器管板与壳体是用焊接连接;一是可拆式,管板本身与壳体不直接焊接,而通过壳体上法兰和管箱法兰夹持固定。本工艺根据反应器的结构需要选择可拆式的连接方式。管箱与管板的连接结构管箱与管板的连接结构形式较多,随着压力的大小、温度的高低以及物料性质、耐腐蚀情况不同,连接处的密封要求,法兰形式也不同。本工艺所用的固定式管板与管箱的连接结构较简单,采用螺栓法兰结构连接,考虑的管程介质的密封求以及加工制造方便性,法兰之间采用平面密封形式。反应管与管板的连接结构本工艺考虑到反应器的密封性能要求较高且管板要承受管束振动及疲劳载荷的作用,因此采用胀焊结合的连接结构,先进行强度焊后加贴胀。强度焊是保证列管与管板连接的密封性能及抗拉脱强度,贴胀是消除列管与管孔之间缝隙的轻度胀接。管板法兰及管板的结构设计根据反应器的初步结构确定,本工艺采用固定式管板兼做法兰。管箱法兰与管板法兰通过螺栓连接。2.9.2附件设计裙座支座采用裙座,选用圆筒形裙式支座,材质为16MnR,裙座与壳体的连接采用对接式焊接,裙座筒体外径为1800mm,厚度为36mm,地脚螺栓的结构选择外螺栓作结构形式,螺栓规格为M806,个数为30个。因为反应器筒体大、高,需要在裙座内部设置梯子。裙座上开1个人孔方便检查,选择公称直径为450mm的人孔(根据HG 21515-95)。为减少腐蚀以及在运行中可能有气体溢出,需要在裙座上部设置排气管,根据反应器直径,设置排气管规格2004,数量1个,排气管中心距裙座顶端距离H2=500mm。设置保温圈以免引起不均匀热膨胀。一般筒体的保温延伸到与塔釜封头的连接焊缝4倍保温层厚度的距离为止。考虑到裙座的防火问题,在裙座内外侧均敷设防火层,防火材料为石棉水泥层(容积密度约为1900kg/m3),厚度为50mm。第三章 塔设备设计3.1 概述塔器是气液 、液液间进行传热、传质分离的主要设备,在化工、制药、和轻工业中,应用十分广泛,塔器甚至成为化工装置的一种标志。在气体吸收、液体精馏(蒸馏)、萃取、吸附、增湿、离子交换等过程更离不开塔器,对于某些工艺来说,塔器甚至成为关键设备。作为主要用于传质过程的塔设备,首先必须使气液两相充分接触,以获得较高的传质效率;同时还应保证塔设备的经济性。3.2设计要求(1)分离效率高达到一定分离程度所需塔的高度。(2)生产能力大单位塔截面积处理量大。(3)操作弹性大。对一定的塔器,操作时气液流量的变化会影响分离效率。若将分离效率最高时的气液负荷作为最佳负荷点,可把分离效率比最高效率下降15%的最大负荷与最小负荷之比称为操作弹性,易于稳定操作。(4)气体阻力小可使气体的输送功率消耗小。对真空精馏来说,降低塔器对气流的阻力可减小塔顶、塔底间的压差,降低塔底操作的压强,从而可降低塔底溶液泡点,降低对塔釜加热剂的要求,还可防止塔底物料的分解。(5)结构简单,设备取材面广便于加工制造与维修,价格低廉,适用面广。(6)塔压降小。对于真空塔或者要求塔压降低的塔来说,压降小的意义更为明显。但值得注意的是,通常选择塔型未必能满足所有的原则,应抓住主要矛盾,最大限度满足工艺要求。3.3 塔设备选型设计依据(1)化工设备设计全书塔设备;(2)固定式压力容器GB 150-2011;(3)设备及管道保温设计导则GB 8175-1987;(4)压力容器封头GB/T 25198-2010;(5)塔器设计技术规定HG 20652-1998;(6)钢制化工容器结构设计规定HG/T 20583-2011;(7)工艺系统工程设计技术规范HG/T 20570-1995;(8)塔顶吊柱HG/T 21639-2005;(9)不锈钢人、手孔HG 21594-21604;(10)钢制人孔和手孔的类型与技术条件HG/T 21514-2005;(11)钢制塔式容器JB/T 4710-2005;(12)补强圈JB/T 4736-2002;(13)钢制压力容器用封头JB/T 4746-2002;3.4塔设备简介塔设备的分类可以从不同的角度进行。例如:按操作压力分为加压塔、常压塔和减压塔;按单元操作分为精馏塔、吸收塔、解吸塔、萃取塔、反应塔和干燥塔;按形成相际接触界面的方式分为具有固定相界面的塔和流动过程中形成相界面的塔;也有按塔釜形式分类的,但是长期以来最常用的分类是按塔的内件结构分为板式塔和填料塔。3.4.1板式塔与填料塔填料塔以填料作为气液接触元件,气液两相在填料层中逆向连续接触。它具有结构简单、压力降小、易于用耐腐蚀非金属材料制造等优点,对于气体吸收、真空蒸馏以及处理腐蚀性流体的操作,颇为适用。当塔径增大时,引起气液分布不均、接触不良等,造成效率下降,即称为放大效应。同时,填料塔还有重量大、造价高、清理维修麻烦、填料损耗大等缺点,以致使填料塔在很长时期以来不及板式塔使用广泛。但是随着新型高效填料的出现,流体分布技术的改进,填料塔的效率有所提高,放大效应也在逐步得以解决。板式塔是分级式接触型气液传质设备,种类繁多。板式塔为逐级接触式气液传质设备。在一个圆筒形的壳体内装有若干层按一定间距放置的水平塔板,塔板上开有很多筛孔,每层塔板靠塔壁处设有降液管。气液两相在塔板内进行逐级接触,两相的组成沿塔高呈阶梯式变化。板式塔的空塔气速很高,因而生产能力较大,塔板效率稳定,造价低,检修、清理方便。根据目前国内外实际使用的情况,主要的塔型是泡罩塔、筛板塔、浮阀塔、舌形塔、浮动喷射塔等。板式塔和填料塔的区别如下表3.1所示:表3.1板式塔和填料塔的比较项目填料塔板式塔散堆填料规整填料空塔气速稍小大比散堆填料大压降小更小一般比填料塔大塔效率小塔效率高高,对大塔径无放大效应较稳定,效率较高液气比液体喷淋有要求范围大适应范围大持液量较小较小较大材质可用非金属耐腐蚀材料适应各类材料金属材料造价小塔较低较板式塔高大直径塔较低安装检修较困难适中较容易3.4.2塔设备选择类型选择时需要考虑多方面的因素,如物料性质、操作条件、塔设备的性能,以及塔的制造、安装、运转和维修等。对于真空精馏和常压精馏,通常填料塔塔效率优于板式塔,应优先考虑选用填料塔,其原因在于填料充分利用了塔内空间,提供的传质面积很大,使得汽液两相能够充分接触传质。而对于加压精馏,若没有特殊情况,一般不采用填料塔。这是因为填料塔的投资大,耐波动能力差。同样,吸收过程也分为液膜控制、气膜控制和介于两者之间的共同控制吸收三种类型。气膜控制的吸收与真空精馏相似,应优先考虑选用高效规整填料塔;液膜控制的吸收与加压精馏相似,往往选用板式塔或汽液湍动大、持液量高的散装填料塔;介于两者之间的,宜采用比表面积大、持液量高、液相湍动大的填料塔,一般多采用散装填料塔。具体来讲,应着重考虑以下几个方面:与物性有关的因素易起泡的物系,如处理量不大时,以选用填料塔为宜。因为填料能使泡沫破裂,在板式塔中则易引起液泛。具有腐蚀性的介质,可选用填料塔。如必须用板式塔,宜选用结构简单、造价便宜的筛板塔盘、穿流式塔盘或舌形塔盘,以便及时更换。具有热敏性的物料须减压操作,以防过热引起分解或聚合,故应选用压力降较小的塔型。粘性较大的物系,可以选用大尺寸填料。板式塔的传质效率太差。含有悬浮物的物料,应选择液流通道大的塔型,以板式塔为宜。操作过程中有热效应的系统,用板式塔为宜。(2)与操作条件有关的因素若气相传质阻力大,宜采用填料塔。大的液体负荷,可选用填料塔。液气比波动的适应性,板式塔优于填料塔。操作弹性,板式塔较填料塔大,其中以浮阀塔最大,泡罩塔次之。(3)其他因素对于多数情况,塔径大于800mm时,宜用板式塔,小于800mm时,则可用填料塔。但也有例外,鲍尔环及某些新型填料在大塔中的使用效果可优于板式塔。一般填料塔比板式塔重。大塔以板式塔造价较廉。填料塔用于吸收和解吸过程,可以达到很好的传质效果,它具有通量大、阻力小、传质效率高等性能。因此实际过程中,吸收、解吸和气体洗涤过程绝大多数都使用填料塔。(4)本厂的实际情况在各个工段中,既含有甲醇、环氧丙烷等腐蚀性小的物系,又含有双氧水等腐蚀性较大的物系,因此在塔型选择时应分别考虑。无固体悬浮物。常压、减压、加压操作均存在。塔径一般较大,个别为小尺寸。从成本出发,优先考虑板式塔,但在一些吸附过程中,同时使用填料塔。目前生产能力较大的塔,多采用板式塔,比较经济合理。而新型高效填料(例如金属丝网波纹填料),能显著降低塔高,其放大效应并不明显,只要有合宜的结构,在较大直径的塔内仍具有较高的效率,自然也是经济合理的。表3.2 各种板式塔的优缺点及用途塔盘类型结构优点缺点应用范围泡罩塔圆形泡罩复杂弹性好无泄漏费用高板间距大压力降比较大用于具有特定要求的场合S型泡罩塔板稍简单简化了泡罩的型式,因此性能相似费用高板间距大压力降比较大用于具有特定要求的场合浮阀塔条形浮阀简单操作弹性较好;塔板效率较高;处理能力较大没有特别的缺点适用于加压及常压下的气液传质过程重盘式浮阀有简单的和稍复杂的T型浮阀简单穿流型筛板简单正常负荷下的效率高;费用最低;压力降小稳定操作范围窄;要么扩大孔径,否则易堵物料;容易发生液体泄漏适于处理量变动少且不析出固体物的系统(溢流式)波纹筛板简单比筛板压力降稍高,但具有同样的优点;气液分布好栅板简单处理能力大;压力降小;费用便宜适用于粗蒸馏3.4.3塔盘比较表3.3各种塔盘的比较塔盘型式蒸汽量液量效率操作弹性压力降价格可靠性泡罩良优良超差良优筛板优优优良优超良浮阀优优优优良优优穿流式优超差差优超可浮阀塔盘在蒸汽负荷、操作弹性、效率和价格等方面都比泡罩塔盘优越;筛板塔盘造价低、压力降小,除操作弹性较差外,其他性能接近于浮阀塔盘。3.5精馏塔设计以下为塔设计实例。3.5.1 T0102脱水塔T0102脱水塔内进行的是经过水洗的MAL水溶液与甲醇的共沸精馏,所得醇醛共沸物从塔顶出料进入下一个反应工段。首先获得Aspen Plus V9.0工艺模拟的塔T0102的流股数据。如下表表3.4 T0102的流股数据MEOH-AT2FT2DT2W相态LiquidLiquidLiquidLiquid温度C64.2058.1659.2399.65压力MPa0.10.10.10.1摩尔密度kmol/cum23.2340.1714.9650.99质量密度kg/cum744.44904.17787.11918.67摩尔流量kmol/hr100.001520.80238.031382.76IBkmol/hr0.000.000.000.00MALkmol/hr0.00130.08130.080.00CO2kmol/hr0.002.402.400.00COkmol/hr0.000.000.000.00H2Okmol/hr0.001388.325.551382.76MEOHkmol/hr100.000.00100.000.00O2kmol/hr0.000.000.000.00N2kmol/hr0.000.000.000.00摩尔分率IB0.000.000.000.00MAL0.000.090.550.00CO20.000.000.010.00CO0.000.000.000.00H2O0.000.910.021.00MEOH1.000.000.420.00O20.000.000.000.00N20.000.000.000.00质量流量kg/hr3204.2234233.9312527.2524910.89IBkg/hr0.000.000.000.00MALkg/hr0.009117.179117.170.00CO2kg/hr0.00105.82105.820.00COkg/hr0.000.000.000.00H2Okg/hr0.0025010.93100.0424910.89MEOHkg/hr3204.220.003204.210.00O2kg/hr0.000.000.000.00N2kg/hr0.000.000.000.00质量分率IB0.000.000.000.00MAL0.000.270.730.00CO20.000.000.010.00CO0.000.000.000.00H2O0.000.730.011.00MEOH1.000.000.260.00O20.000.000.000.00N20.000.000.000.00体积流量l/hr4304.1737862.4715915.5627116.46新建塔内件设计:全塔25块理论板,设定塔径3000mm,选用筛板塔,双溢流,板间距0.6096m。塔底液体停留时间5min。图3.1 T0102塔内件基础参数设置对塔板结构进行详细设计图3.2 T0102塔板详细结构参数对设计好的塔内件进行负荷性能计算与水力学校核。校核结果如图图3.3 全塔水力学校核结果图水力学数据如表塔板%液泛率干板压降侧壁降液管停留时间中心降液管停留时间kPasecsec2.0069.150.584.254.253.0068.690.584.284.284.0068.110.574.314.315.0067.410.564.354.356.0066.560.544.404.407.0065.670.534.464.468.0064.620.514.554.559.0063.230.484.694.6910.0061.310.454.914.9111.0058.480.405.315.3112.0053.860.346.296.2913.0049.650.263.693.6914.0044.330.194.254.2515.0043.030.184.494.4916.0042.810.184.564.5617.0042.770.184.584.5818.0042.760.184.594.5919.0042.750.184.594.5920.0042.750.184.594.5921.0042.750.184.594.5922.0042.750.184.594.5923.0042.750.184.594.5924.0042.750.184.594.59进行塔机械结构计算(1)实际塔板数在Aspen Plus中由塔设备的工艺计算得到的理论塔板数为25块,取塔板效率为0.80,则由:式中:NT实际板数;N理论板数。即全塔实际板数为32块,在第17块板进料。(2)塔高的计算1.筒体的高度为了方便清洗、检查、维修,应在塔上开设人孔,拟在塔筒体每7块塔板开设一个人孔(DN500),共开设4个人孔。普通塔板板间距HT为610mm,开设人孔的塔板板间距HT为800 mm。因此可求得塔板段的塔高Hb为:为了满足塔顶空间高度的作用是安装塔板和开人孔的需要,也使气体中的液体自由沉降,减少塔顶出口气中的液滴夹带,空间高度一般取1.001.50m,此处取Hd=1.50m;塔底空间高度具有贮存槽的作用,塔底釜液最好能在塔底有1015min的储量,以保证塔底料液不至排完。对于塔底产量较大的塔,塔底容量可取小些,取25min的储量。此处Hw取1.50m。综上,塔的筒体高度H1为:2.封头的高度封头的选型根据GB/T25198-2010 压力容器封头选型。该塔内径为3000 mm,选用DN=3000的EHA型标准椭圆封头,总深度H2=790 mm。3.裙座的高度裙座的型式分为圆柱形和圆锥形两种。裙座高度是指从塔底封头切线到基础环之间的高度。此处选用DN=2600 mm的圆柱形裙座,裙座高度由塔底封头切线至出料管中心线的高度U和出料管中心线至基础环的高度V两部分组成。则裙座高度H3:综上,全塔的总高度H为:H=H1+H2+H3=23280+790+4250=28320mm3.5.1 T0204甲醇回收塔T0204甲醇回收塔内进行的是甲醇水溶液的分离,所得甲醇从塔顶出料回收利用。首先获得Aspen Plus V9.0工艺模拟的塔T0204的流股数据。如下表表3.5 T0204的流股数据S22S20S23相态LiquidLiquidLiquid温度C20.0063.7599.48压力MPa0.100.100.10摩尔密度kmol/cum44.0622.9150.18质量密度kg/cum924.41743.59917.67摩尔流量kmol/hr1529.58290.621238.56MALkmol/hr0.480.480.00MAAkmol/hr4.970.004.97H2Okmol/hr1234.040.061233.99MEOHkmol/hr288.10288.100.00NHEXkmol/hr1.991.990.00摩尔分率MAL3.11E-041.64E-031.99E-26MAA3.25E-038.76E-244.01E-03H2O8.07E-011.96E-049.96E-01MEOH1.88E-019.91E-019.41E-09NHEX1.30E-036.84E-033.06E-69质量流量kg/hr32095.389437.0222658.35MALkg/hr33.3833.380.00MAAkg/hr427.720.00427.72H2Okg/hr22231.661.0322230.63MEOHkg/hr9231.289231.280.00NHEXkg/hr171.34171.340.00质量分率MAL0.000.000.00MAA0.010.000.02H2O0.690.000.98MEOH0.290.980.00NHEX0.010.020.00体积流量l/hr34721.5812692.0224691.17新建塔内件设计。全塔30块理论板,设定塔径3000mm,选用筛板塔,双溢流,板间距0.6096m。塔底液体停留时间1min。图3.1 T0204塔内件基础参数设置对塔板结构进行详细设计图3.2 T0204塔板详细结构参数对设计好的塔内件进行负荷性能计算与水力学校核。校核结果如图图3.3 全塔水力学校核结果图水力学数据如表塔板%液泛率干板压降侧壁降液管停留时间中心降液管停留时间MPasecsec2.0069.520.005.185.183.0069.520.005.185.184.0069.590.005.175.175.0069.690.005.165.166.0069.830.005.145.147.0069.970.005.125.128.0070.070.005.105.109.0069.950.005.105.1010.0069.350.005.155.1511.0067.750.005.305.3012.0064.390.005.745.7413.0058.390.006.896.8914.0052.840.008.608.6015.0059.610.004.134.1316.0059.270.004.214.2117.0059.320.004.234.2318.0059.360.004.244.2419.0059.370.004.244.2420.0059.380.004.244.2421.0059.370.004.244.2422.0059.360.004.244.2423.0059.340.004.244.2424.0059.290.004.254.2525.0059.200.004.254.2526.0059.030.004.264.2627.0058.750.004.284.2828.0058.340.004.314.3129.0057.860.004.344.34进行塔机械结构计算(1)实际塔板数在Aspen Plus中由塔设备的工艺计算得到的理论塔板数为25块,取塔板效率为0.80,则由:式中:NT实际板数;N理论板数。即全塔实际板数为37块,在第19块板进料。(2)塔高的计算1.筒体的高度为了方便清洗、检查、维修,应在塔上开设人孔,拟在塔筒体每7块塔板开设一个人孔(DN500),共开设5个人孔。普通塔板板间距HT为610mm,开设人孔的塔板板间距HT为800 mm。因此可求得塔板段的塔高Hb为:为了满足塔顶空间高度的作用是安装塔板和开人孔的需要,也使气体中的液体自由沉降,减少塔顶出口气中的液滴夹带,空间高度一般取1.001.50m,此处取Hd=1.50m;塔底空间高度具有贮存槽的作用,塔底釜液最好能在塔底有1015min的储量,以保证塔底料液不至排完。对于塔底产量较大的塔,塔底容量可取小些,取25min的储量。此处Hw取1.50m。综上,塔的筒体高度H1为:2.封头的高度封头的选型根据GB/T25198-2010 压力容器封头选型。该塔内径为3000 mm,选用DN=3000的EHA型标准椭圆封头,总深度H2=790 mm。3.裙座的高度裙座的型式分为圆柱形和圆锥形两种。裙座高度是指从塔底封头切线到基础环之间的高度。此处选用DN=2600 mm的圆柱形裙座,裙座高度由塔底封头切线至出料管中心线的高度U和出料管中心线至基础环的高度V两部分组成。则裙座高度H3:综上,全塔的总高度H为:m第四章 换热器设计4.1概述在不同温度的流体间传递热能的装置称为热交换器,简称换热器。在换热器中至少要有两种温度不同的流体,一种流体温度高,放热;另一种流体温度低,吸热。在工程实践中有时也会有两种以上流体参加换热的换热器,但其基本原理与前一致。各种类型的换热器作为工艺过程必不可少的设备,广泛用于石油化工、医药、动力、冶金、交通、制冷、轻工等部门。随着工业的迅速发展,能源消耗量不断增加,能源紧张已成为一个世界性问题。为缓和能源紧张的状况,世界各国竞相采取节能措施,大力发展节能技术,已成为当前工业生产和人民生活中一个重要课题。换热器在节能技术改造中具有很重要的作用,表现在两方面:一是在生产工艺流程中使用着大量的换热器,提高这些换热器效率,显然可以减少能源的消耗;另一方面,用换热器来回收工业余热,可以显著地提高设备的热效率。4.2换热器选型设计依据(1)化工设备设计全书换热器2003-5;(2)石油化工设备选型手册换热器2009-1;(3)化工工艺设计手册(第四版)2009-6;(4)固定式压力容器安全技术监察规程TSG R0004-2009;(5)压力容器GB 150-2011;(6)热交换器GB/T 151-2014;(7)化工配管用无缝及焊接钢管尺寸选用系列HG 20553-93;(8)石油化工企业钢管尺寸系列SH/T 3405-2012;4.3换热器类型4.3.1按工艺功能分类1.冷却器:冷却工艺物流的设备;2.加热器:加热工艺物流的设备;3.再沸器:用于蒸发蒸馏塔底物料的设备;4.冷凝器:蒸馏塔顶物流的冷凝或者反应器冷凝循环回流的设备;5.蒸发器:专门用于蒸发溶液中水分或者溶剂的设备;6.过热器:对饱和蒸汽再加热升温的设备;7.废热锅炉:由于工艺的高温物流或者废气中回收其热量而产生蒸汽的备;4.3.2按传热方式和结构分类1.间壁式换热器2.直接接触传递热量式换热器结构分类如表4.1所列:表4.1 换热器的结构分类换热器型式换热器特点管式管壳式固定管板式刚性结构:用于管壳温差较小的情况(一般50C),管间不能清洗带膨胀节:有一定的温度补偿能力,壳程只能承受较低压力浮头式管内外均能承受高压,可用于高温高压场合U型管式管内外均能承受高压,管内清洗及检修困难填料函式外填料函:管间容易漏泄,不宜处理易挥发、易爆易燃及压力较高的介质内填料函:密封性能差,只能用于压差较小的场合套管式釜式壳体上都有个蒸发空间,用于蒸汽与液相分离双套管式结构比较复杂,主要用于高温高压场合,或固定床反应器中套管式能逆流操作,用于传热面较小的冷却器、冷凝器或预热器螺旋浸没式用于管内流体的冷却、冷凝,或者管外流体的加热盘管式喷淋式只用于管内流体的冷却或冷凝板式板式拆洗方便,传热面能调整,主要用于粘性较大的液体间换热螺旋板可进行严格的逆流操作,有自洁作用,可回收低温热能伞板式伞形传热板结构紧凑,拆洗方便,通道较小,易堵,要求流体干净板壳式板束类似于管束,可抽出清洗检修,压力不能太高管壳式换热器的优缺点对比表如下表4.2所列:表4.2 管壳式换热器优缺点对比种类优点缺点浮头式换热器管束可以抽出,方便清洗;介质温度不受限制;可在高温高压下工作,一般温度450,压力6.4MPa可用于结垢比较严重的场合;可用于管程易腐蚀场合。小浮头易发生内漏;金属材料耗量大,成本高20%;结构复杂固定管板式换热器传热面积比浮头式换热器大20%30%;旁路漏流较小;锻件使用较少,成本低20%以上;没有内漏。壳体和管子壁温差一般宜小于等于50,大于50时应在壳体上设置膨胀节;管板与管头之间易产生温差应力而损坏;壳程无法机械清洗;管子腐蚀后造成连同壳体报废、壳体部件寿命决定于管子寿命,故设备寿命相对较低;不适用于壳程易结垢场合;U形管式换热器管束可抽出来机械清洗;壳体与管壁不受温差限制;可在高温、高压下工作,一般适用于温度500,压力10MPa;可用于壳程结构结垢比较严重的场合;可用于管程易腐蚀场合。在管子的U形处冲蚀,应控制管内流速;管程不适用于结垢较重的场合;单管程换热器不适用;不适用于内导流筒,故死区较大。4.4换热器设计原则4.4.1 换热器类型(1)固定管板式换热器当冷热流体温差不大时,可采用固定管板式换热器,即两块管板和壳体是连在一起的。特点是结构简单、制造成本低,但由于壳程不易清洗或检修,壳程必须走洁净且不易结垢的流体。当两流体温差较大时,可采用具有膨胀节的壳体。但是不宜用于两流体温差过大(一般要70)和壳程压力过高(可通过改变材料、壳体厚度、封头与管板的设计来增加其可承受压力)的场合。(2)U形管式换热器这种换热器壳程易于清洗,但清洗管子困难,损坏管子难以调换,且管板的有效利用率低。(3)浮头式换热器两端管板只有一端与壳体以法兰实行固定连接,称为固定端。另一端管板不与壳体连接而可相对滑动,称为浮头端。因此,管束的热膨胀不受壳体的约束,检修和清洗时只要将整个管束抽出即可。适用于冷热流体温差较大,壳程介质腐蚀性强、易结垢的情况。本工艺通过Aspen Exchanger Design and Rating V9对换热器进行设计,选用的换热器均为间壁式换热器,主要采用固定管板式换热器。4.4.2 工艺条件的选择(1)设计裕量根据相关标准查阅,换热器如果是两相的,设计裕量取510%,如果设计裕量为负值,则此设计不能用,则选取设计裕量在10%左右,考虑到圆整参数的影响,最多不超过20%。对于工艺物流间的换热,留有3050%的裕量。(2)温度限制高温端的温差不应小于20,低温端的温差不应小于5。当在两工艺物流之间进行换热时,低温端的温差不应小于20。在冷却或者冷凝工艺物流时,冷却剂的入口温度应高于工艺物流中易结冻组分的冰点,一般高5。在对反应物进行冷却时,为了控制反应,应维持反应物流和冷却剂之间。当冷凝带有惰性气体的工艺物料时,冷却剂的出口温度应低于工艺物料的露点,一般低5。换热器的设计温度应高于最大使用温度,一般高15。(3)压力降增加工艺物流流速,可增加传热系数,使换热器结构紧凑,但增加流速将关系到换热器的压力降,使磨蚀和振动破坏加剧等。压力降使动力学消耗加剧,因此通常有一个允许的压力降范围,最大允许的压力降范围一般限制如表4.3所列。表4.3换热器压力降允许范围工艺物流的压力状况允许压力降P/kPa工艺气体真空3.5常压3.414低压1525高压3570工艺流体70170(4)流速水和相类似的液体流速一般取1-2.5m/s;气体和蒸汽的流速可在8-30m/s的范围内选取。一般流体流速选取如表4.4所列。表4.4 换热器流速范围表流体类型管型流速(m/s)管程壳程液体直管0.5-30.2-1.5盘管0.3-0.8气体直管5-302-15盘管3-10(5)物流的安排为了节省保温层和减少壳体厚度,高温物流一般走管层,但如果有时为了节省保温层和减少壳体厚度或为了物料的冷却,也可使高温的物料走壳程。较高压力的物流应走管程。黏度较大的物流应走壳程,在壳程可以得到较高的传热系数。腐蚀性较强的物流应走管程。对压力降有特定要求的工艺物流应走管程,因管程的传热系数和压降计算误差小。较脏和易结垢的物流应走管程,以便清洗和控制结垢。若必须走壳程,则应采用正方形管子排列,并采用可拆式(浮头式、填料函式、U形管式)换热器。流量较小的物流应走壳程,易使物流形成湍流状态,从而增加传热系数。传热膜系数较小的物流(如气体)应走壳程,易于提高传热膜系数。(6)换热管管径越小换热器越紧凑、越便宜。但是,管径越小换热器的压降越大,为了满足允许的压力降,一般推荐选用19mm的管子。对于易结垢的物料,为方便清洗,采用外径为25mm的管子。对于有气、液两相的工艺物流,一般选用较大的管径,例如再沸器、锅炉,多采用32mm的管径。直接火加热时多采用76mm的管径。无相变换热时,管子较长,传热系数增加。在相同传热面时,采用长管管程数少,压力降小,而且每平方米传热面的比价也低。但是,管子过长给制造带来困难,因此,一般选用的管长为46m。对于大面积、或无相变的换热器可以选用89m的管长。管子在管板上的配布主要是正方形配布和三角形配布两种形式。三角形的配布有利于壳程物流的湍流。正方形配布有利于壳程清洗。为了弥补各自的缺点,产生了转过一定角度的正方形配布和留有清理通道的三角形配布两种形式。三角形配布一般是等边三角形的,有时为了工艺的需要可以采用不等边的三角形配布。不常用的还有同心圆式配布,一般用于小直径的换热器。管心距是两相邻管子中心的距离。管心距小、设备紧凑,但将引起管板增厚、清洁不便、壳程压降增大,一般选用范围为1.251.5d(d为管外径)。换热管规格和排列形式如表4.5所列。表4.5换热管规格和排列形式外径壁厚/(mmmm)排列形式管心距/mm碳钢、低合金钢不锈钢252.5252正三角形3219219225管程数有1、2管程或4管程。管程数增加,管内流速增加、给热系数也增加。但管内流速要受到管程压力降等限制,在工业上常用的管内流速如下:水和相类似的液体流速一般取12.5m/s;对大冷凝器的冷却水流速可增加到3m/s;气体和蒸汽的流速可在830m/s的范围内选取。所需的换热面积大,采用多个换热器并联,而不采用串联,避免压力降过高,影响传热系数。换热器型号表示方法:本法来自于GB151,适用于卧式和立式换热器。示例说明:型号:AES500-1.6-54-6/25-4 其中:A表示前端管箱形式为平盖管箱E表示壳体形式为单进单出冷凝器壳体S表示后端结构型式为浮头式500表示公称直径为500mm1.6表示公称压力 1.6MPa54表示公称换热面积为 54m26表示公称长度为6m25表示换热管外径为 25mm4表示管程数为4I表示管束为I级,采用较高级冷拔钢管这个型号代表平盖管箱,公称直径500mm,管程和壳程设计压力均为1.6MPa,公称换热面积54m,碳素钢较高级冷拔换热管外径25mm,管长6m,4管程,单壳程的浮头式换热器。(6)密封条数按照换热器设计建议,每五排管设置一对密封条。4.5选型范例4.5.1 工艺参数确定(1)流股参数确定利用Aspen Plus V9.0对换热器进行模拟计算,可得到该换热器的流股信息为表2-7所示:表4.6 E0402流股信息一览流股名称压力/MPa温度/质量流量/kg/s气相分率介质管程入口0.1547.9518.470氧化反应原料混合气管程出口0.15358.3118.470氧化反应原料混合气壳程入口0.12380.0018.470氧化反应产物混合气壳程出口0.1274.6018.470氧化反应产物混合气(2)设计温度该换热器的壳程工作温度为47.95-358.31,管程工作温度为74.6-380,进出口温度差大于5,符合本项目最经济温差。设计温度以工作温度为依据,一般为工作温度+(15-30)。这里取壳程设计温度为390,管程设计温度为410。(3)设计压力该换热器的操作压力为壳程0.12MPa,管程0.15MPa。换热器的设计压力为设计温度下的最大工作压力,一般为正常工作压力的1.1倍。这里取壳程设计压力为0.13Pa,管程设计压力为0.17MPa。EDR中换热器的压降设置为自动默认值,也可自己设置压降,出口绝压小于0.1MPa(真空条件)时,压降不大于进口压强的40%,出口绝压大于0.1MPa时,压降不大于进口压强的20%。(4) 传热系数传热系数基于传热膜系数、固壁热阻和垢层热阻计算得到。其中传热膜系数和固壁热阻为EDR自动默认值。该换热器壳程介质为以空气为主的氧化反应原料混合气,根据化工工艺设计手册(第四版)的污垢热阻经验系数,如表2-1所示。表4.7 常见流体的污垢热阻此处取壳程介质的污垢系数为0.000344m2K/W。管程介质为以空气为主的氧化反应产物混合气,同样查得手册上的污垢系数为0.000344m2K/W。(5) 流体通道选择该换热器的作用是原料气与产物气的互相换热。由于工艺物料为被冷却物质,为了加快冷却速度,使其走壳程,一方面能与管程的原料气换热,另一方面壳程外的空气也能与之换热转移走部分热量。同时较低压力气体走管程可以降低壳层厚度。4.5.2 EDR数据输入用aspenV9将简捷计算模型转换为严格模型,将流股信息等数据导入EDR,并得出一系列模拟设计。图4.8 EDR数据输入4.5.3 换热器结构参数确定(1) 换热器形式选择经过对流股换热的工艺要求,该换热器选择工业上最常见的管壳式换热器,并选择其
- 温馨提示:
1: 本站所有资源如无特殊说明,都需要本地电脑安装OFFICE2007和PDF阅读器。图纸软件为CAD,CAXA,PROE,UG,SolidWorks等.压缩文件请下载最新的WinRAR软件解压。
2: 本站的文档不包含任何第三方提供的附件图纸等,如果需要附件,请联系上传者。文件的所有权益归上传用户所有。
3.本站RAR压缩包中若带图纸,网页内容里面会有图纸预览,若没有图纸预览就没有图纸。
4. 未经权益所有人同意不得将文件中的内容挪作商业或盈利用途。
5. 人人文库网仅提供信息存储空间,仅对用户上传内容的表现方式做保护处理,对用户上传分享的文档内容本身不做任何修改或编辑,并不能对任何下载内容负责。
6. 下载文件中如有侵权或不适当内容,请与我们联系,我们立即纠正。
7. 本站不保证下载资源的准确性、安全性和完整性, 同时也不承担用户因使用这些下载资源对自己和他人造成任何形式的伤害或损失。

人人文库网所有资源均是用户自行上传分享,仅供网友学习交流,未经上传用户书面授权,请勿作他用。
2:不支持迅雷下载,请使用浏览器下载
3:不支持QQ浏览器下载,请用其他浏览器
4:下载后的文档和图纸-无水印
5:文档经过压缩,下载后原文更清晰
|