QY20汽车起动机传动系统设计--设计说明书.docx
QY20汽车起动机传动系统设计【含CAD图纸、说明书】
收藏
资源目录
压缩包内文档预览:(预览前20页/共87页)
编号:21076924
类型:共享资源
大小:3.70MB
格式:ZIP
上传时间:2019-07-21
上传人:机****料
认证信息
个人认证
高**(实名认证)
河南
IP属地:河南
50
积分
- 关 键 词:
-
含CAD图纸、说明书
QY20
汽车
起动机
传动系统
设计
CAD
图纸
说明书
- 资源描述:
-
















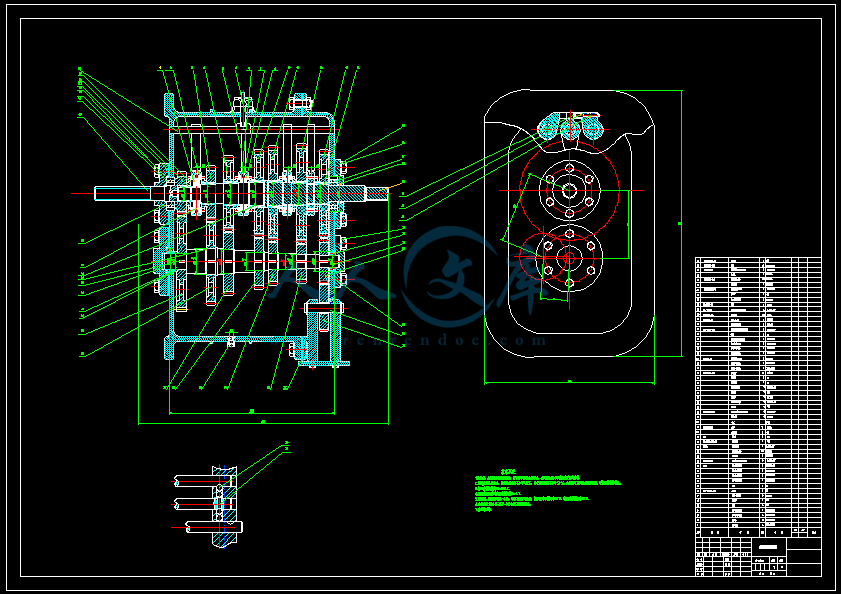










- 内容简介:
-
本科毕业设计UNDERGRADUATE DESIGN 设计题目: QY20汽车起动机传动系统设计 姓 名: 专 业: 年 级 、 学 号: 指 导 教 师: 设计(论文)原创性声明本人郑重声明:所呈交的毕业设计(论文),是在导师的指导下,独立进行研究所取得的成果,所有数据、图片资料真实可靠。除文中已经注明引用的内容外,本设计(论文)的研究成果不包含他人享有著作权的内容。对本设计(论文)所涉及的研究工作做出贡献的个人和集体,均已在设计(论文)中以明确的方式标明。本设计(论文)的知识产权归属培养单位。本人签名: 年 月 日设计(论文)版权使用授权书本设计“ QY20汽车起动机传动系统设计 ”是本人在校期间所完成学业的组成部分,是在江苏师范大学科文学院教师的指导下完成的,因此,本人特授权江苏师范大学科文学院可将本毕业论文的全部或部分内容编入有关书籍、数据库保存,可采用复制、印刷、网页制作等方式将论文文本和经过编辑、批注等处理的论文文本提供给读者查阅、参考,可向有关学术部门和国家有关部门或机构呈送复印件和电子文档。本毕业论文无论做何种处理,必须尊重本人的著作权,署明本人姓名。 作者签名: 指导教师签名: 年 月 日 年 月 日 QY20汽车起动机传动系统设计摘 要汽车起重机驱动系统是整个汽车的核心。汽车变速器及离合器装置是汽车的传动系统中最重要的部件,主要作用体现在汽车行驶的过程当中。驱动桥支承着重载汽车的满载负重和地面给车轮的反作用力、一个框架和一个用于垂直悬挂体以及横向和纵向的力和力矩,还受冲击载荷的作用。因此,一个良好的驱动系统对于起重机性能来说是有绝对的提高。驱动系统中变速器及离合器,驱动桥及差速器装置中关键部件的设计与计算是设计的重难点,主要包括的方面有以下几个方面:分析方面、方案确定方面、计算和校核等。其中结构的分析是对零部件的设计与计算,从机械式变速器的中心矩的计算、各档的齿轮需求参数的计算、传动比的计算还有以及输入输出轴的设计来实现结构分析,实现零部件的设计。在校核计算方面,是通过前面的齿轮装置的设计和轴装置的设计机构等来进行零部件的校核的。关键词:驱动系统;起重机;变速器;离合器;驱动桥;差速器; Design of transmission system for QY20 automobile starter AbstractThe driving system of truck crane is the core of the whole vehicle. Automotive transmission and clutch device are the most important parts in the transmission system of automobiles, and their main functions are reflected in the process of driving. The driving axle supports the full load of the heavy-duty vehicle and the reaction force of the ground to the wheel, a frame and a force and moment for the vertical suspension body, as well as the lateral and longitudinal forces and moments, and is also subjected to impact loads. Therefore, a good driving system for crane performance is an absolute improvement. The design and calculation of key components of transmission and clutch, drive axle and differential device in drive system are the key and difficult points in design. They mainly include the following aspects: analysis, scheme determination, calculation and verification. The structural analysis is the design and calculation of components, from the calculation of the central moment of mechanical transmission, the calculation of gear demand parameters of each gear, the calculation of transmission ratio and the design of input and output shafts to achieve structural analysis, to achieve the design of components. In the checking calculation, parts are checked through the design of the front gear device and the design mechanism of the shaft device.Key words: drive system; crane; transmission; clutch; drive axle; differential;目 录摘 要4Abstract5第1章 绪 论61.1 引言61.2 汽车传动系统的发展历程61.3 研究的目的、依据和意义61.4 研究的方法及技术路线71.4.1研究方法71.4.2研究技术路线7第2章 变速器的主要结构设计82.1 档位数82.2 变速器各档传动比的确定82.3 中心距A的确定82.4 外形尺寸92.5 齿轮参数92.5.1 模数92.5.2 压力角102.5.3 螺旋角102.5.4 齿宽b10第3章 变速器齿轮的设计计算与校核113.1 齿轮的设计与计算113.1.1 各挡齿轮齿数的分配113.1.2 齿轮材料的选择原则213.1.3 计算各轴的转矩213.2 轮齿的校核223.2.1 轮齿的损坏原因及形式223.2.2 轮齿弯曲强度计算22第4章 变速器轴的设计计算与校核254.1 轴的设计计算254.1.1 轴的工艺要求254.1.2 轴的结构264.1.3 初选轴的直径264.1.4 轴的强度计算264.2 轴承的选择及校核304.2.1 输入轴的轴承选择与校核304.2.2 输出轴轴承校核32第5章 离合器的总体设计335.1离合器设计要求335.2 离合器工作原理345.3 离合器结构选择345.3.1 摩擦片的选择345.3.2 压紧弹簧布置形式的选择345.3.2 压盘的驱动方式355.3.3 分离杠杆与轴承355.3.4 离合器的散热355.3.5 从动盘总成355.4 离合器主要零件的设计365.4.1 从动盘365.4.2 摩擦片365.4.3 膜片弹簧365.4.4 压盘36第6章 离合器的主要零部件设计计算366.1 摩擦片主要参数的选择366.2 膜片弹簧主要参数的选择386.3 减振弹簧的设计396.4 分离轴承的寿命计算39第7章 主减速器设计407.1 主减速器的结构型式407.1.1 主减速器的齿轮类型407.1.2 主减速器的减速型式407.1.3 主、从动齿轮的支承型式407.2 确定主减速器的主要参数417.2.1 主减速比的确定417.2.2 主减速器齿轮的分析417.2.3 主减速器齿轮参数计算437.2.4 主减速器螺旋锥齿轮的强度校核477.2.5 齿轮加工工艺选择507.2.6 主减速器锥齿轮的轴承校核51第8章 差速器的结构设计568.1 差速器的工作原理568.2 差速器的结构确定578.3 差速器的结构参数计算588.3.1 差速器齿轮的基本参数的选择588.3.2 差速器齿轮的几何尺寸计算608.3.3 差速器齿轮的强度计算62第9章 传动轴的结构设计639.1 传动轴万向节联轴器的功用和组成639.2 万向节的设计计算64总 结66致 谢66参考文献67第1章 绪 论1.1 引言随着社会的发展,科技的进步,步入21世纪的人们对于精神生活与物质生活的需求越来越高,随之而来的汽车车型也在飞速发展,动力匹配方式在不断的提高。然而如何合理地选择这些部件及有关参数,使匹配达到最优,在满足人们需求的情况加提升动力性及越野性能是所有汽车行业在考虑的问题。在相同变速器条件下,更好地满足实用性要求和最大地增加动力性,也一直是研究者们追求的目标,也是本论文研究的主要目的。近年来,汽车的迅猛发展带动着重型汽车的发展,汽车的驱动系统的需求量也呈现出上升趋势,从而形成一个完整的生产链。就重载汽车而言,其所需要传递的转矩比一般商用车大很多,从而达到运输更多的货物的要求,故选取的发动机功率较大,意味着其传动系统必须能承受和传递该转矩。因此,在选择好发动机后,采用性能良好的驱动系统成了重型载货汽车安装的必要过程。1.2 汽车传动系统的发展历程汽车的传动系统从汽车的一出现便开始了一点点的进步与发展,从最初的链条传动,到带传动,到现在的齿轮传动都经过了大量的试验与实际的论证,可以说每一个类型的发展都在表明这时代的进步。而传动系统在之前的定义中主要包括变速器,驱动桥,轮胎,传动轴等,动力传动系尾端的驱动桥,让发动机的转矩经由主减速器、差速器、半轴等传递到驱动车轮,实现减速增扭;由圆锥齿轮使该转矩的传递方向得以改变;由差速器实现两边车轮的差速作用,使内、外侧车轮以不等的速度转动;由桥壳壳体与车轮共同完成承载及递传力矩的效果。1.3 研究的目的、依据和意义汽车行业的发展,主要是向着多元化和工业化的方向发展,其中驱动系统的设计和生产在汽车中具有非常重要的位置。目前汽车对车速和燃油量的要求方面很高,所以驱动系统的使用对性能将会有十分重要的影响。设计中所采用的基本参数如下:1.4 研究的方法及技术路线1.4.1研究方法(1)通过查阅相关资料,掌握汽车起重机驱动系统的主要参数。(2)充分考虑已有汽车起重机驱动系统的优缺点来确定汽车起重机驱动系统的总体设计方案,对现有装置的不足进行分析。(3)对设计的汽车起重机驱动系统进行修改和优化,最终设计出能满足要求的汽车起重机驱动系统。1.4.2研究技术路线(1)根据题目和原始数据查看相关资料,了解当今国内外汽车起重机驱动系统的发展现状及发展前景,撰写文献综述和开题报告。(2)根据产品功能和技术要求提出多种设计方案,对各种方案进行综合评价,从中选择较好的方案,再对所选择的方案做进一步的修改或优化,最终确定总体设计方案。(3)具体设计汽车起重机驱动系统的驱动装置、工作装置等。 (4)对所设计的机械结构中的重要零件进行校核计算,如齿轮、轴、轴承等,保证设计的合理性和可行性。;(5)绘制零件图、装配图,完成要求的图纸量;(6)整理各项设计资料,撰写论文。不少,也将会使操纵机构变得十分复杂,这对于驾驶员来说增加了不小的负第2章 变速器的主要结构设计2.1 档位数如果要提高汽车的动力性同时降低燃油的经济性的话,那么增加换挡数是一个十分直接有效的方法,它可以是传动比扩大范围,一般的变速器有320个档位数。可是增加换挡数的话对于变速器的结构要求就会变得十分的复杂,需要的常啮合齿轮装置也会变的非常多,而且外形尺寸也将会增加不少,也将会使操纵机构变得十分复杂,这对于驾驶员来说增加了不小的负担,所以也并不是换挡数越多就一定会越好,考虑到多种因素在设计中的汽车变速器拟采用六个档位的变速器。2.2 变速器各档传动比的确定结合参考车型的基本参数,各档传动比结果如下:传动比符号数值一档7.04二档4.10三档2.48四档1.56五档1.00六档0.74倒档R6.262.3 中心距A的确定考虑到中心距对于变速器的重要性,所以在中心间距A的确定上十分谨慎,因为这对变速器的轮廓尺寸和质量大小都有十分重要的影响,而且还会影响与轮齿的接触强度。所以为了能够满足设计的要求,初选中心距 : =195.02mm(2-1)圆整取值为195 mm式中: A-变速器中心距 KA-中心距系数,取9.5 Temax-发动机的最大转矩,1280Nm i1-变速器一档传动比,取7.04 T-变速器传动效率,取0.96 一般轿车变速器的中心距在65-80mm范围内变化,而起重机的变速器中心距在80-200mm范围内变化。由上面算得的数据可知,所初选的中心距符合要求。2.4 外形尺寸根据之前变速器的换挡数和齿轮结构,以及中心间距等因素,综合考虑在不影响结构外观等多种状况的条件下,变速器的横向外形尺寸,可根据齿轮直径及倒档中间(过度)齿轮和换档机构的布置初步确定。参考下列数据选用:四档 (2.2-2.7)A 五档 (2.7-3.0)A 六档 (3.2-3.5)A当变速器选用常啮合齿轮对数和同步器时,中心距系数K应取给出范围的上限。为了检测方便,中心距A最好取为整数。由于是六档机械式变速器,所以其轴向尺寸为:(3.2-3.5)A,一般取3.48A ,即680mm。2.5 齿轮参数2.5.1 模数如果想要选择比较的小的模数来满足使用设计的要求,那么需要在先确定中心距的前提下才可以,这样考虑设计的齿轮才能保证系统的平稳运行,降低运转过程中的噪声。若想要设计的变速各方面都达到最优,需要从工艺设计方面和齿轮强度两个方面入手,首先就是挡齿轮的模数在选择使用时要相同;强度要保持一致。本次设计拟采用渐开线形式的齿轮。这样有利于换挡等操作,其具体可通过表3-1和3-2所示知道:表3-1汽车变速器齿轮法向模数车型类型单位模数单位乘用车的发动机1.0V1.6L2.252.75mm1.6V2.5L2.753.00mm起重机的长度6.0L14m3.504.50mmL14.0m4.506.00mm表3-2汽车变速器常用齿轮模数系列齿轮模数/mm一系列1.001.251.502.002.503.004.005.006.00二系列1.752.252.753.253.503.754.505.50由于是起重机驱动系统,故变速器用齿轮模数可取 4mm。啮合套和同步器的接合齿多数采用渐开线齿形。由于工艺上的原因,同一变速器中的接合齿模数相同。由于是大型起重机,故取3 mm。2.5.2 压力角标准压力角可通过在机械设计手册中相关规定查找,所以汽车手动变速器设计中拟采用的压力角度是20,而变速器中的结合同步器的齿压力角度是3016。2.5.3 螺旋角综合考虑齿轮的重合度、以及运转过程中的噪声,还有要考虑齿轮轻度的增强,所以在设计时要把这些全部囊括在内,因为齿轮的螺旋角对于轮齿的应用强度影响巨大。所以为了减轻轴承的负荷和提高系统设计的使用寿命,本次设计拟采用的螺旋角度是202.5.4 齿宽b考虑到齿轮寿命收到齿宽b的影响,所以在设计时应尽量缩小轮齿的宽度,但也要考虑其强度,所以设计的齿轮的宽度可以根据以上齿轮的模数来进行设定,具体计算见下表:类型名称计算依据为齿宽系数取值直齿4.58.0斜齿6.08.5所以综合考虑拟采用接合齿的宽度是2mm。第3章 变速器齿轮的设计计算与校核3.1 齿轮的设计与计算3.1.1 各挡齿轮齿数的分配一挡齿轮采用的是斜齿轮传动,取其模数4,压力的角度,螺旋角度=20,则这可计算知道一档的传动比值。 (3.1) 根据斜齿齿数和,可以计算出齿数、, (3.2) 因此可以知道的值是11, 的值是81。考虑到安全性和稳定性需要对中心距和螺旋角度修正处理,具体可根据公式计算: (3.3) (3.4)可以通过计算知道修正的螺旋角度。未变位中心距可以通过小表知道:名称计算公式结果单位分度圆直径46.873mm345.158mm未变位中心距196.016mm 但是实际使用时中心距发生了改变,所以为了还能够满足要求,中心距对一挡的齿轮副需要进行变位处理,首先具体计算端面啮合角和啮合角 :tan=tan/cos (3.5)cos= (3.6)带入数值计算可知 ,。有以上计算出的数值可以求的变位系数和和当量齿数与: (3.7) 此外取值 ,可以进一步计算出一挡齿轮副的齿顶高和、齿根高和、齿顶圆直径和、齿根圆直径和以及齿全高h: 式中: 、 式中: 在设计时采用斜齿轮作为二挡的齿轮,取模数数值4,压力的角度,螺旋的角度,因此可以计算出二挡的传动比数值和齿数之和: 同时取 , ,这样可以计算出修正的螺旋角度的值: 通过函数转化求出其值 根据上面的数据还可以计算出二挡的齿轮变位系数相关参数理论中心距、端面压力角、端面啮合角、当量齿数和与变位系数之和: =72.003mm tan=tan/cos 此外取值 =-0.02,可以进一步计算出二挡的齿轮的参数分度圆直径和、齿顶高和、齿根高和、齿顶圆直径和、齿根圆直径和以及齿全高h: 式中: , 式中: =85.722mm 在设计时采用斜齿轮作为三挡的齿轮,取模数数值4,压力的角度,螺旋的角度,因此可以计算出三挡的传动比数值和齿数之和: =2.48 =同时取,这样可以计算出三挡的齿轮变位系数参数理论中心距、端面压力角、端面啮合角、变位系数之和、当量齿数和、分度圆直径和、齿顶圆直径和、齿根圆直径和以及齿全高h: tan=tan/cos 此外取值,可知: 式中: , 式中: 在设计时采用斜齿轮作为四挡的齿轮,取模数数值4,压力的角度,螺旋的角度,因此可以计算出四挡的传动比数值和齿数之和: 同时取 ,则可以计算出修正的螺旋角度的数值: 由三角函数计算可以知道修正的数值这样可以计算出四挡的齿轮变位系数参数理论中心距、端面压力角、端面啮合角、变位系数之和、当量齿数和、分度圆直径和、齿顶圆直径和、齿根圆直径和以及齿全高h: tan=tan/cos 此外取值 可知: 式中: , 式中: 在设计时采用斜齿轮作为五挡的齿轮,取模数数值4,压力的角度,螺旋的角度,因此可以计算出四挡的传动比数值和齿数之和: =1 =同时取 ,这样可以计算出五挡的齿轮变位系数参数理论中心距、端面压力角、端面啮合角、变位系数之和、当量齿数和、分度圆直径和、齿顶圆直径和、齿根圆直径和以及齿全高h: tan=tan/cos 此外取值 可知: 式中: , 式中: 在设计时采用斜齿轮作为六挡的齿轮,取模数数值4,压力的角度,螺旋的角度,因此可以计算出四挡的传动比数值和齿数之和: =0.74 =同时取 ,这样可以计算出五挡的齿轮变位系数参数理论中心距、端面压力角、端面啮合角、变位系数之和、当量齿数和、分度圆直径和、齿顶圆直径和、齿根圆直径和以及齿全高h: tan=tan/cos 此外取值 可知: 式中: , 式中: 根据理论计算可以知道倒挡齿轮的模数,压力角度时,取和的值等于23后,可计算出输入轴和倒挡轴的距离:一般情况下,倒档传动比与一档传动比较为接近,在本设计中倒档传动比igr取6.26。中间轴上倒档传动齿轮的齿数比一档主动齿轮Z12略小,取15。而通常情况下,倒档轴齿轮取Z15 2123,此处取23。 可计算出Z13=38。因本设计倒档齿轮业也是斜齿轮,故可得出中间轴与倒档轴的中心距:而倒档轴与第二轴的中心距计算如下:中间轴式变速器的第二轴和中间轴中部 d0.45A0.45130=58.5mm且da13=d+2ha。 (3-8)式中:ha-齿顶高 ha=(fo+)m -变位系数。选非变位齿轮,则取=0fo-齿顶高系数,取值为1.00 3.1.2 齿轮材料的选择原则1、工作条件的要求 设计时主要考虑的方面有齿轮强度的要求、传动装置耐磨性的要求、材料选择要求、结构尺寸外形的要求,特别时对于工作性能中稳定度、安全性,这几个方面要求全部满足,这样才能保证设计出的变速器使用寿命长、安全有稳定。2、合理选择材料配对 在设计变速器的所有部件中,对于材料的使用要严格的把控,因为一点出现质量问题将会造成十分大的安全隐患和经济上的损失,所以说合理选择材料的配对对于汽车变速器的设计至关重要,特别是在啮合齿轮的选择材料要求抗胶合性能要强,同时两齿轮在选用时往往用不同型号的材料设计19。3、考虑加工工艺及热处理工艺在设计变速箱的齿轮时拟采用时低碳钢,其具体的工艺路线如下:3.1.3 计算各轴的转矩由于设计使用的发动机的最大扭矩是,而且齿轮传动的有效效率,离合器传动的有效效率,轴承传动的有效效率。因此可通过下表知道各个挡的最大扭矩:名称计算公式计算结果单位输入轴=1216Nm输出轴一挡8132.608Nm输出轴二挡4736.32Nm输出轴三挡2864.896Nm输出轴四挡1802.112Nm输出轴五挡1155.2Nm输出轴六挡854.848Nm倒挡1908.59Nm3.2 轮齿的校核3.2.1 轮齿的损坏原因及形式汽车经过长时间的工作,导致轮齿失效的原因主要有因为材料或者受力过大引起的折断、工作时间长了齿面的磨损、塑性变形等因素20。具体的解决方案需要考虑到以上导致齿轮失效的因素,对于每个元件要进行将加工,多余材料要选用合乎规格标注的材质,不然潜在的安全隐患什么可怕,不仅会带来财产的损失,还有可能对驾驶员带来生命的危险,所以马虎不得。3.2.2 轮齿弯曲强度计算1、齿轮弯曲的计算首先要从倒档直齿轮的弯曲应力计算: 式中符号代表的含义件表名称符号单位备注弯曲应力MPa-理论载荷N.mm-应力集中系数-摩擦力系数-主动齿轮取,从动齿轮取齿宽mm-模数-齿宽系数-倒档取7.5齿形系数-公式计算的齿形系数图见图4-1所示。 由计算和设计手册能够知道,如果载荷达到理论计算值时,倒挡轴位置的齿轮弯曲应力应该在400MPa850之间20。 设倒挡位置的齿轮的弯曲应力分别为 ,:,, 2.斜齿轮的弯曲应力的计算 式中各个符号含义与取值见下表名称符号单位备注理论载荷Nmm-法向模数mm-齿数-斜齿轮螺旋角度-应力集中系数-齿形系数-可按当量齿数在图4-1查得;齿宽系数-取7.5重合度影响系数=2.0由计算和设计手册能够知道,只有许用应力在180MPa350MPa范围内才可以满足常啮合齿轮的需求。(1)一挡齿轮弯曲应力 、的计算 , (2)二挡齿轮的弯曲应力 、的计算 , (3)三挡齿轮的弯曲应力 、的计算 , (4)四挡齿轮的弯曲应力 、的计算 , (5)五挡齿轮的弯曲应力 、的计算 , (6)六挡齿轮的弯曲应力 、的计算 ,第4章 变速器轴的设计计算与校核4.1 轴的设计计算4.1.1 轴的工艺要求现在设计变速器的材料主要是采用碳钢和合金作为轴的材料。这两种材料对比发现碳钢的生产成本要比合金钢的生产制造成本低很多,并且碳钢在抗疲劳强度上也表现的十分优秀,在热处理方式上也比较简单,所以本设计拟采用轴的材质的作为轴工艺的材料,同时为了避免倒挡轴的磨损失效,在加工时需要在轴的表面进行精加工处理操作。此外为了保护滑动齿轮能够工作在十分优越的性能,因此在输入轴和输出轴均采用渗碳、氰化等方式进行热处理。4.1.2 轴的结构轴的结构主要从以下几个方面考虑:一是从工艺方面进行考虑,需要加工方便;二是从使用的方面进行考虑,需要满足强度的使用和承受载荷的能力。根据对比分析设计采用齿轮轴作为轴的生产设计的方式。 4.1.3 初选轴的直径在变速器中由于传动轴主要的强度设计只需按照扭转强度进行计算,因此输入轴的轴颈 =43.43149.945mm (4.1) K为经验系数,K=4.04.64.1.4 轴的强度计算 (4.2) (4.3) (4.4) 以上公式中的符号含义见下表:名称符号单位备注齿轮承受的径向力N齿轮承受的圆周力N弹性模量MPa=2.1105MPa惯性矩mm4对于实心轴,轴的直径mm齿轮上的作用力距支座的距离、mm两支座间的距离mm根据式(4.2)和式(4.3)可以计算出轴的全挠度。 (4.5)根据垂直面上的mm使用范围和在水平面内的mm使用范围,再结合齿轮平面转角的使用范围可以计算出一档的基本参数圆周力和、径向力和、轴向力和。 , , ,, 知道数值, ,可以计算出 = 输出轴的刚度计算: =因为一挡的时挠度影响整个系统的安全,所以需要对输入轴强度的校核计算。 1)竖直平面分析得 =2)水平平面分析得= 由第三强度定理计算得: 如图4-2所示即为输入轴的强度分析数据。图4-2输入轴强度分析图 因为一挡的时挠度影响整个系统的安全,所以需要对输出轴强度校核。 1)竖直平面分析 得 图5-3输出轴强度分析 = 2)水平平面分析 得 由第三强度定理计算得: 如图4-3所示即为输出轴的强度分析数据。图4-3输出轴强度分析图4.2 轴承的选择及校核4.2.1 输入轴的轴承选择与校核由机械设计手册可以知道一些据汽车变速器得要求,结合轴承工作得条件需求,还有轴颈直径初选,基本确定输入轴的轴承得型号为NUP204,查找资料可以知道其原型号为92204,此外通过查表可以知道代号NUP204轴承得参数: , ,。由以上数据能够知道轴承的计算预寿命长度为: 因为轴承得使用寿命对于汽车的使用寿命影响巨大,所以为了保险起见需要对其进行校核计算:)、水平平面分析+=得, )、内部力分析,由查手册知 )、轴向力分析 因此轴的左侧易放松,右侧易被压紧。)、当量动载荷的计算 故在轴承的左侧,在轴承的右侧 可计算出左侧的径向当量动载荷值 轴承寿命的校核 ,式中寿命系数用表示,球状的轴承=3;滚子轴承=10/3。 , 可计算出左侧的径向当量动载荷值 ,由左侧和右侧的使用寿命核算分析,分析可知一挡输入轴合格。4.2.2 输出轴轴承校核由以上分析知输出轴的型号,通过查机械设计手册知道输出轴的代号为GB283-87,圆柱型的滚子轴承 , ,。由以上数据能够知道轴承的计算预寿命长度为 轴承寿命的校核)、水平平面分析+=得2,。)、内部分析,取 )、轴向力分析 故轴承的右侧将会被放松,轴承的左侧将会被压紧)、当量动载荷的计算 故轴承的左侧,轴承的右侧.可计算出左侧的径向当量动载荷值 轴承寿命的校核 ,式中寿命系数用表示,球状的轴承=3;滚子轴承=10/3; 左侧: , 可计算出右侧的径向当量动载荷值 右侧: ,由左侧和右侧的使用寿命核算分析,分析可知输出轴合格。第5章 离合器的总体设计5.1离合器设计要求根据以上离合器的主要功能,结合离合器的使用状态,在离合器设计过程中主要有如下几点要求:(1)离合器的设计过程中要保证发动机输出的最大扭矩()小于离合器的摩擦力矩();(2)离合器传递扭矩时要保证扭矩可以缓慢增加,保证车辆可以平稳起步;(3)分离轴承的设计应保证接触迅速,分离彻底;(4)设计中要考虑减震的设置,降低整车的噪音及NVH性能;(5)由于离合器一直在分离结合,因此在设计中要考虑到分离结合时的散热性能,便于散热;(6)操纵机构要简单可靠,同时便于驾驶员的驾驶;(7)摩擦片的设计要保证其耐久性与吸热性。5.2 离合器工作原理如图所示,本设计的离合器为膜片弹簧离合器,主要由一般从动部分、压紧机构、主动部分、操纵机构等组成。离合器在驾驶员松开踏板时,离合器处于接合状态,发动机输出的扭矩通过发动机的飞轮2借助离合器中压盘的力的作用,从而传给从动盘3,从动盘通过花键与变速器相连,从而将力传递给变速器。当驾驶员踩下踏板时,离合器处于分离状态,拉索通过分离轴承8,将力传递给压盘,而外端与压盘连接,在此状态下从动盘3两面的压力消失,从而摩擦力消失,离合器处于分离状态。当松开踏板,受回位弹簧的影响,又恢复至原状态,处于结合状态,由将力传递至变速器。1-轴承 2-飞轮 3-从动盘 4-压盘 5-离合器盖螺栓 6-离合器盖 7-膜片弹簧 8-分离轴承 9-轴 离合器总成5.3 离合器结构选择5.3.1 摩擦片的选择 本设计中由于车辆发动机与变速器之间输出的扭矩大,同时为了使设计结构简单,便于后期维修,提高工作效率,降低设计成本。本设计中的离合器摩擦片结构为单片摩擦片,在两边分别分布一片。这样既能满足使用要求,又能降低设计成本。因此设计摩擦片数为2。5.3.2 压紧弹簧布置形式的选择根据离合器压紧结构的分类,一般情况下可分为周布弹簧式、中央弹簧式、膜片弹簧式等几种。本设计中基于膜片弹簧的优点,初步选用压紧形式为膜片弹簧结构。膜片弹簧的主要优点如下9:(1)膜片弹簧可以将压紧弹簧功能与分离杠杆功能结合到了一起,是离合器的结构简单,整体尺寸减小;(2)由于膜片弹簧的受力面积大,因此其性能较稳定;(3)由于膜片弹簧为环形结构,因此受力均匀;(5)通风散热要比其他结构要好;(6)减少零部件的使用,可以降低制造成本。同时由于近几年来由于材料性能的不断提高,我国对于刚才的生产工艺和加工方法也在飞速发展,膜片弹簧的制造技术已经成熟。因此,本设计的离合器选用膜片弹簧式离合器。5.3.2 压盘的驱动方式在膜片弹簧离合器中,扭矩从离合器盖传递到压盘的方法有三种9: 通过结构的不同驱动方式也不尽相同,主要有凸台窗孔、径向传动驱动、径向传动片驱动等几种。结合各种驱动方式的特点,同时结合整车性能,本设计选用的为径向传动驱动的方式。径向传动片驱动方式主要是通过特制而成的传动片,在工作中可以将压盘与离合器盖结合在一起,主要在力的传递过程中可以保证力的传递连续且不间断,同时可以增强离合器则整体结构。5.3.3 分离杠杆与轴承在本设计中膜片弹簧承即时弹性元件又是分离杠杆,由于其结构的不同因此在设计中主要对膜片弹簧进行设计;对于分离轴承主要是起到与变速器的分离与结合过程,其结构也多种多样,在本设计中选用的轴承为油封轴承,这样由于其使用的强度较高,而且对于润滑较重要,因此选用油封轴承。5.3.4 离合器的散热对于离合器而言,由于离合器相对于车辆的发动机输出轴与变速器输入轴一直处于高速旋转状态,在高档过程中其相对旋转转速更高。而总所周知相对运动会产生摩擦,而摩擦就会产热。离合器就是不断处于摩擦接触状态,因此对于离合器的设计中散热的设计尤为重要。对于离合器如果通风散热性不好,则会导致摩擦片高温,从而使摩擦片烧蚀,导致离合器性能下降,影响车辆性能及安全。本设计的膜片离合器为周布通风结构,由于其承担分离杠杆的作用,因此对于通风散热性有很好的性能,可以提高离合器的使用寿命。 5.3.5 从动盘总成在本设计的离合器结构中从动盘是一个由摩擦片,从动片,减震器和从动盘穀等零部件组成的结构总成。其工作性能直接影响到整车的使用性能,因此其设计过程中主要考虑到如下要求:(1)为减小冲击,转动惯量要小;(2)为使离合器能平顺便于起步要具有轴向弹性,;(3)为避免传动系的共振要装扭转减振器,;5.4 离合器主要零件的设计5.4.1 从动盘从动盘的结构主要有摩擦片,从动片,扭转减震器和从动盘穀等结合而成,因此在制造加工时由于结构的特殊性,主要靠铆钉铆接而成。对于摩擦面的平面度要求平面不平度误差0.2mm,材料主要使用45号钢冲压处理而成。5.4.2 摩擦片摩擦片在性能上要满足如下要求:(1)耐热性能好,结构简单;(2)具有足够的机械强度和耐磨性;(3)有利于接合平顺;(4)不会发生粘着现象,在汽车长期停放时,。5.4.3 膜片弹簧膜片弹簧是离合器中最重要的一部分,在材质选着上也有严格要求,本设计中的材料选用60SiMnA,而对于表面的处理也有一定的要求,主要采用调制后喷丸处理,表面采用堵路处理。5.4.4 压盘压盘为HT150铸造后机加而成的,主要对于高度及耐久性能有一定的要求,同时由于处于运动状态,因此对于粗糙度的要求为1.6-3.2之间。第6章 离合器的主要零部件设计计算6.1 摩擦片主要参数的选择(1) 摩擦片外径的确定根据汽车设计中摩擦片的参数设计,摩擦片的外径可有式: 为直径系数,取值见下表 取 直径系数的取值范围车型直径系数乘用车14.6长度为36.2m的起重机16.018.5(单片离合器)13.515.0(双片离合器)得D=572.43mm。摩擦片的尺寸已系列化和标准化,根据汽车摩擦片设计手册取整后为575mm(2) 摩擦系数及片数的确定摩擦片的摩擦因数取决于摩擦片所用的材料及基工作温度、单位压力和滑磨速度等因素,本设计中取=0.2;摩擦面数Z为离合器从动盘数的两倍,决定于离合器所需传递转矩的大小及其结构尺寸。本题目设计的为单片离合器,因此Z=2。离合器间隙t是指离合器处于正常接合状态、分离套筒被回位弹簧拉到后极限位置时,为保证摩擦片正常磨损过程中离合器仍能完全接合,在分离轴承和分离杠杆内端之间留有的间隙。该间隙t一般为34mm。本设计中取t=4mm。摩擦材料的摩擦因数的取值范围摩擦材料摩擦因数石棉基材料模压0.200.25编织0.250.35粉末冶金材料铜基0.250.35铁基0.300.50金属陶瓷材料0.4(3)摩擦片内径d的确定根据前面计算可知摩擦片外径D=575mm摩擦片的内、外径比应在0.530.70范围内,即 计算可得d=385.25mm,本设计取d=385mm(3) 减震器弹簧位置直径的确定为了保证扭转减振器的安装,摩擦片内径d必须大于减振器振器弹簧位置直径约50mm,即mm计算可,本设计取(5) 摩擦面积转矩的确定为反映离合器传递的转矩并保护过载的能力,单位摩擦面积传递的转矩应小于其许用值,即 式中,为单位摩擦面积传递的转矩(N.m/mm2),按下表本设计为计算可得满足要求。单位摩擦面积传递转矩的许用值离合器规格028030035040 (6)为降低离合器滑磨时的热负荷,防止摩擦片损伤,对于不同车型,单位压力的最大范围为0.111.50MPa,即MPaMPaMPa6.2 膜片弹簧主要参数的选择(1)的确定此值对膜片弹簧的弹性特性影响极大,为保证离合器压紧力变化不大和操纵方便,汽车离合器用膜片弹簧的H/h通常在1.52范围内选取。常用的膜片弹簧板厚为24mm,本设计 ,h=4mm ,则H=8mm 。(2) R/r选择汽车离合器膜片弹簧根据结构布置和压紧力的要求,R/r常在1.21.3 的范围内取值。本设计中取,摩擦片的平均半径mm, 取mm则mm 则。(3)圆锥底角 汽车膜片弹簧在自由状态时,圆锥底角一般在范围内,本设计中 得在之间,合格。分离指数常取为18,大尺寸膜片弹簧有取24的,对于小尺寸膜片弹簧,也有取12的,本设计所取分离指数为18。(4)公差与精度离合器盖的膜片弹簧支承处,应具有较强的刚度和较高的尺寸精度,压力盘高度(从承压点到摩擦面的距离)公差要求要小,支承环和支承铆钉安装尺寸精度要高。6.3 减振弹簧的设计(1)减振弹簧的安装位置,结合mm,得取165mm,则。 (2)减振弹簧尺寸根据机械原理与设计(机械工业出版社)采用65Mn弹簧钢丝, 设弹簧丝直径mm,MPa,MPa。根据下表选择旋绕比旋绕比的荐用范围d/mmC确定旋绕比,曲度系数6.4 分离轴承的寿命计算 根据离合器的基本参数,本设计选取的分离轴承的参数如下表:分离轴承参数表型号Crn7014C48.2KN1.234500r/min则由下式:,得:h,满足使用要求。第7章 主减速器设计7.1 主减速器的结构型式凭借其齿轮型式、减速型式与主、从动齿轮的安置型式的差异,确定主减速器的构造型式。7.1.1 主减速器的齿轮类型螺旋锥齿轮、双曲面齿轮、圆柱齿轮与蜗轮蜗杆等为主减速器中各种各样的齿轮型式,其工作的特点和效率各有闪光点。螺旋锥齿轮传动的主、从动锥齿轮轴线一般交于一点,且夹角为90。因为轮齿端面有重叠,从而使2对或以上轮齿一起啮合,以使弧齿锥齿轮能承受更大的负载。除此之外,轮齿不是在其总长度上一起啮合,却是慢慢地从齿的一头持续且平滑地转向另外一头.因此,其工作平顺稳定,震动和噪声也小,并且其效率能达到。所以,采取螺旋锥齿轮传动的方案就此次设计而言更为符合。7.1.2 主减速器的减速型式质量达16t2的中后桥驱动的重卡,要求采取贯通桥,且其主传动比5.565,故采取双级减速型式。按照两齿轮间啮合方式的差异,贯通桥第一级传动分成圆柱齿轮锥齿轮式与锥齿轮圆柱齿轮式。后者布局空间太大,尤其是主动锥齿轮加工工艺性差,而从动锥齿轮必须采取悬臂式支承方式,支承刚度不够。然而前者有助于贯通式安置,具备降低转速的作用,构造紧密,且布局空间减小,对降低整车质心高度有极大帮助,从而提高了汽车的通过性。由于本设计中第一级圆柱齿轮副只用于贯通,故取其传动比为1。7.1.3 主、从动齿轮的支承型式主动锥齿轮的支承方式:悬臂式和骑马式。悬臂式安置方式虽然简单,但是支承刚度差,只用在传递转矩较小的主减速器上,故不切合此次设计要求。而骑马式安置方式得锥齿轮两头的轴上都有轴承,如许可以提高支承刚度,使轴承负载减小,优化了齿轮的啮合状况。2t以上的装载量汽车主减速器主动齿轮全部采取骑马式安置方式。本设计所研究的总质量16t2的重卡,因此,选用骑马式支承方式。如图21所示图2-1 主动锥齿轮跨置(骑马)式支承形式从动锥齿轮的支承形式也选用骑马式。如图22所示图2-2 从动锥齿轮支承形式7.2 确定主减速器的主要参数7.2.1 主减速比的确定主减速器比的取值,就主减速器的构造型式、轮廓尺寸以及重量大小而言尤为重要。 =0.377 (2-1)式中:车轮的滚动半径,0.47m; 最大功率时发动机转速,2400r/min; 汽车最高速度,76km/h; 变速器最高挡传动比,在此取1。7.2.2 主减速器齿轮的分析凭借发动机的最大转矩和一挡传动比,计算从动锥齿轮的转矩 (22)凭借驱动轮打滑扭矩,计算从动锥齿轮的转矩 (23)式中:因为突然接离合器出现的动载指数,至于液力自动变速器,;至于手动高性能的赛车机械变速器,K=3;至于性能指数的汽车,取K=1;至于的汽车,取K=2或者根据经验选取。性能系数: = (24)0.195G/16,取 =0; G汽车总重量,320000N; 发动机最大转矩,1070; 从发动机到所计算的主减速器从动齿轮之间传动系中的一挡传动比 (即); 传动系统的传动效率,取=0.9; 汽车在满负载的前提下,单个驱动桥对地面施加的最大负载, 320000/2=160000N; 附着指数,取0.85; r车轮的滚动半径,0.47m; 由主减速器从动锥齿轮至驱动车轮间的传动效率,取0.9; 传动比1。=T=T=(,T)=33250依据汽车日常行驶平均(当量)转矩来计算从动锥齿轮的转矩 (25)式中: 路面滚动阻力指数,就载货汽车而言取,故取其为0.018; 汽车正常行驶时的平均上坡能力指数,就载货汽车而言取,故取其为0.07; 汽车的性能系数,在此取0; ,见式247.2.3 主减速器齿轮参数计算选择主动锥齿轮与从动锥齿轮的齿数和及其计算在选取主、从动锥齿轮的齿数和时,我们要考虑以下几方面:a要获取良好的齿面重合度和符合其弯曲强度要求的轮齿,必须大于或等于;b以防磨合不匀称,和之间不能有共同的约数;c为了使齿轮啮合平顺稳定,降低其工作噪声,使其具有较高的疲劳强度,就货车而言,大于或等于6;d为了获得良好的离地间隙,当主传动比较大时,主动锥齿轮齿数尽可能往小取;e至于主传动比,和应该确定好各自合适的齿数。依照以上并凭据汽车车桥设计中表3-12,选择=9和=50。且+=9+50=5940。确定从动锥齿轮分度圆直径和端面模数及其计算主减速器螺旋锥齿轮从动锥齿轮的分度圆直径,可依照这个齿轮的计算转矩,按经验公式算出: (26)式中:从动锥齿轮的节圆直径,mm; 直径系数,取=1316; 。 (1316)=(418514)mm,初选500mm;按照公式算出初选模数: (27) ,校核: (28)式中:m齿轮大端的端面模数,mm; 模数系数,取=0.30.4; 。 m=(0.30.4)=(9.712.9)因此m=10,符合条件。确定双级主减速器圆柱齿轮重要尺寸及其计算(圆柱齿轮副中心距A,齿宽b)(10.5111.92) (29)(0.380.41)A (210)(10.5111.92)=(338383)mm,取350mm(0.380.41)350=(133143.5)mm,取140mm表2-1 螺旋锥齿轮的几何尺寸计算及结果序号项目计算公式计算结果(1)主动锥齿轮齿数9(2)从动锥齿轮齿数50(3)端面模数m10(4)(从)齿面宽;77.5(5)齿工作高16.50(6)齿全高18.65(7)法向压力角223022.5(8)轴交角90(9)节圆直径;90;500(10)节锥角;10.2;79.8(11)节锥距254.1(12)周节31.416(13)齿顶高;12.70;3.80(14)齿根高;5.95;14.85(15)径向间隙2.15(16)齿根角;1.3;3.4(17)面锥角;13.6;81.1(18)根锥角;8.9;76.4(19)外圆直径;115;501.3(20)节锥极点到齿轮外边轮廓的直线长度;247.8;41.3(21)理论弧齿厚;23.136;8.28(22)齿侧间隙B0.3(23)螺旋角35(24)螺旋方向主动锥齿轮左旋,从动锥齿轮右旋(25)驱动齿轮小齿轮(26)螺旋方向从齿轮反面看过去,主动锥齿轮是顺时针旋转方向,而从动锥齿轮是相反方向、参考汽车车桥设计表3-16、3177.2.4 主减速器螺旋锥齿轮的强度校核齿轮的损坏形式及寿命齿轮的损坏形式最多的有:齿轮轮齿折断、齿轮齿面粘结、齿轮齿面磨损和齿轮齿面点蚀及剥落等。汽车驱动桥锥齿轮所承受的载荷为交互变化的,其基本的破坏方式为疲劳,具体往往是在齿轮齿根的疲劳折断与因齿轮齿面点蚀而造成的剥落。在其运行寿命超过的前提下,往复次数已经大过材料的疲劳次数。所以,驱动桥中各齿轮的许用的最大弯曲应力必须小于或等于。 表2-2 汽车驱动桥齿轮的许用应力数值 N/m计算负载主减速器齿轮的许用弯曲应力主减速器齿轮的许用接触应力差速器齿轮的许用弯曲应力7002800980210.91750210.9单位齿长上的圆周力在主减速器中,锥齿轮齿面耐久性,往往利用齿轮上的单位齿长所受到的圆周力p粗略计算 (211)式中:P齿轮所受到的的圆周力,依据发动机的最大转矩和最大附着力矩这两种负载情况演算; F从动齿轮的齿面宽;69.75mma凭借发动机的最大转矩,计算p: (212)式中:变速器传动比,往往选择一挡或者直接挡,在这里取一挡传动比,即; =1070; ; b凭借驱动桥打滑的转矩,计算p (213)式中:汽车在满负载的前提下,单个驱动桥对地面施加的最大负载, 300000/2=160000N; 轮胎的附着指数,取0.85; 车轮的滚动半径,0.47m; 查表,凭借变速器一挡传动比,计算p时:。而在目前的汽车设计中,因为材料品质和加工工艺等制造的优化,可再增大20%25%。因此,=1786N/mm。故,从而主减速器锥齿轮的齿面耐久性达到设计标准。校核轮齿的弯曲强度在主减速器结构中,锥齿轮齿根的弯曲应力是 (214)=33250;式中:所计算齿轮的计算转矩; 过载系数,取1; 尺寸系数,1.6,=0.8; 取1; 质量系数,取1; b,d所设计的齿轮齿面的宽度和大端的节圆直径; 所设计的齿轮轮齿弯曲应力综合指数,由图23可以查得=0.31。图23 计算弯矩综合指数J根据表22,主从动锥齿轮的=700MPa。因此,轮齿弯曲强度满足要求。校核齿轮的齿面接触强度在主减速器结构中,螺旋锥齿轮轮齿的齿面接触应力是 (215)式中:钢对钢齿轮的综合弹性指数:取; 至于制造准确的齿轮齿面品质指数,取1.0; ,b见式214; 齿轮齿面接触强度的综合指数,由图24可以查到=0.137,因此,该螺旋锥齿轮的齿面接触强度达到设计的标准。图24 计算齿轮齿面接触强度的综合指数7.2.5 齿轮加工工艺选择汽车驱动桥中主减速器的使命是极为重要,其工作环境也是极其恶劣的。它与传动系统中的其他齿轮比较,主减速器锥齿轮具有负载大、变化频繁、冲击载荷较大,而且作用的时间较长的特点,让它们的工作环境变得更加严酷。所以,在传动系统中,主减速器锥齿轮的材质选择及加工工艺(热处理)须符合以下内容:I弯曲疲劳强度和表面接触疲劳强度都须较高,齿面硬度也要较高,从而保障其工作耐久性,从而达到适应其工作条件的要求;II轮齿的芯部须有良好的韧性用来承受住冲击负载的作用,以防其在冲击负载的作用下,齿轮轮齿根部出现折断的症状;III钢材铸造性能、切削性能、毛坯成形方式和热处理性能应该满足设计要求,制造和加工工艺良好,热处理变形要小或者变形规律方便节制。从而提升产品品质、收缩生产时间、降低生产资本和提高正品率;IV选择齿轮材料的合金元素,也须符合我国目前状况。为了节省镍、铬等元素,选择采取锰、钒、钼、钛、硼、硅等合金元素。汽车主减速器采用的螺旋锥齿轮与差速器采用的普通行星齿轮,在我国而言,近年来均是由渗碳合金钢铸造而成。在主减速器中,锥齿轮的合金钢主要为、,在差速器中,锥齿轮的合金主要为、等。为了减少镍、铬元素损耗的目的,目前我国设计出的新原料有和。因此,本设计采用新型材料。渗碳合金钢的好处体现在其外表硬度高(因为其表面含碳量高,往往在之间)、抗压性和耐久性也满足设计要求。除此外,芯部含碳量较低,从而韧性好、耐冲击性好。所以,这种材质可以达到齿轮正常工作的设计要求。另外,钢自己的含碳量也较低,所以它们的铸造性能和加工工艺性均优良。要提高齿轮啮合条件,不让它们在工作初期就呈现出早期磨损、擦伤、胶合或者咬死的症状,锥齿轮要在其热处理和精加工之后再进行磷化处理(厚度大致是),也可以在其表面镀铜、镀锡。为了降低齿轮之间的摩擦指数,可对其渗硫处理,改善其润滑环境,提高其耐久性,从而防止齿面擦伤、咬合和胶合症状的发生。为了提高齿轮工作的寿命,再对其外表面作喷丸处理。7.2.6 主减速器锥齿轮的轴承校核为了确定主减速器锥齿轮轴承上的负载,第一步要分析锥齿轮在啮合过程中的齿面作用力。施加于螺旋锥齿轮齿面上的力图25 主减速器主动锥齿轮受力分析图2-5所示为螺旋锥齿轮主动小齿轮的受力简图。该主动锥齿轮的轮齿旋转方向为左旋,往齿轮反面看过去,主动锥齿轮是顺时针旋转方向。齿面法向力作用在齿面宽中央位置A处。可分为3个力:a沿齿轮切线方向的圆周力F;b沿齿轮轴线方向的轴向力A;c垂直于齿轮轴线的径向力R。a齿面宽中央位置的圆周力 (216)式中:施加于这个齿轮上的转矩,也就是施加于主减速器中主动锥齿轮的等效转矩; 这个齿轮的齿面宽中央位置的节圆直径对于圆锥齿轮 (217) (218)就螺旋锥齿轮副而言,施加于主动锥齿轮与从动锥齿轮上的圆周力大小一致,方向相反。b施加于齿轮轴上的轴向力与径向力 (219) (220) (221) (222)所以,施加于齿轮轴上的轴向力和径向力就得以演算出来 (223) (224)式2-162-24参考汽车底盘设计计算出主减速器轴承的负载在锥齿轮齿面上所受的圆周力、轴向力和径向力通过演算得出的前提下,凭借主减速器齿轮轴承的安置尺寸和型式(骑马式),能演算出主减速器轴承负载。图26 主减速器轴承的安置尺寸 (225) (226)i对于轴承A,根据上式已知,F=39.4KN,A=30.7KN,R=14.7KN,a=120mm ,b=70mm,c=50mm,轴承A的径向力轴承A轴向力为0锥齿轮轴承型号的选定就轴承A而言,其仅受径向负载,故当量负载该轴承应该具有的基本额定动负载 (227)式中:载荷系数,取1.5; 温度系数,取1; 寿命系数,因为选取的是滚子轴承,所以; 轴承的预期寿命,取4000h; n轴承的计算转速 ; ;初步选择的圆柱滚子轴承2413。校核圆柱滚子轴承2413的使用寿命 (228)大修里程假设为100000km, (229),满足要求。ii就轴承B而言,于此不是一个轴承,却是两个轴承(即一对)。此时,要计算成对安装的轴承组的等效负载,径向动负载指数X和轴向动负载指数Y值按两列轴承选用,由机械设计中表187可查得X=1.0,Y=1.8,故。由于采用的是成对圆锥滚子轴承 (230)由式227首选的一对圆锥滚子轴承32317。由式228,校核,满足要求。就从动齿轮的轴承、而言,其径向力的计算,由式223、224可得。已知F=39.4KN,A=14.7KN,R=30.7KN,a=450,b=180,c=270。iii对于轴承C径向力轴向力A=14.7KN,由机械设计中表187可查得X=1.0,Y=1.8,故。由式227首选的一对圆锥滚子轴承32312。由式228,校核。,满足要求。iv对于轴承D轴向力为0。 由式227首选的一对圆锥滚子轴承32310。由式228,校核。,满足要求。此小节计算内容和公式依据汽车车桥设计、机械设计指导、汽车底盘设计和汽车设计关于主减器的相关计算而来 QY20汽车起动机传动系统设计第8章 差速器的结构设计在驾驶汽车正常运行时,车轮相对于地面来说,一般作滚动和滑动运动。滑动又可以分成滑移和滑转这两种状态。为了顺应这几种状态,在左、右驱动车轮之间均装有差速器。因为左、右轮胎内气压的差异、轮胎表面损坏的程度不一及左、右车轮负载的不统一,使左、右车轮的滚动半径不统一;左、右两轮与路面状况接触的不统一,从而导致行使阻力不一致。假设驱动桥(中后桥)的左、右车轮由一根整体轴刚性联接,则两车轮的角速度必须是一致的,这时不管汽车是在弯道上运动,还是在直线上运动,都将会造成车轮在地表上的滑移或者滑转。此时,不仅会加重轮胎损坏、传动零件的损伤和能量的浪费,还会让转向变得繁重,操控稳定性和行驶通过性变差。为了消除由于左右车轮的不协调而带来的弊端,必须将驱动两侧车轮的整体轴断开(即半轴),并且在汽车左右车轮间装有轮间差速器,以满足汽车正常行驶的要求。差速器作为一个差速传动装置,用于在左、右半轴之间分别配以不同的转矩,从而保障两半轴以不一定相等的角速度旋转,从而确保在不同运动状况下的左右驱动车轮的功率传输,以防轮胎与地面间发生滑移或滑转的不良症状。根据差速器的结构型式的差异,可将其分为蜗轮式、齿轮式、牙嵌自由轮式与凸轮式等。目前,在汽车中使用最为普遍的是对称锥行星齿轮的差速器。8.1 差速器的工作原理图81 差速器工作(差速)原理图差速器中各个元件的运动关系可用图31来表达。对称式锥齿轮差速器究其根本为行星齿轮装置。差速器壳3与主减速器从动锥齿轮6牢固联接,行星齿轮轴5与差速器壳3牢固联接在一起,因此便构成行星架,且其为主动架。假定其角速度为;半轴与半轴为从动件,假定它们的角速度为和。行星齿轮与两半轴齿轮的啮合于A、B两处位置。行星齿轮的中央位置处是C点。因此,A、B、C三个位置到差速器转动轴线的最小直线长度都是r。在行星齿轮4只跟着行星架围绕差速器转动轴线旋转的前提下即公转,位于相同半径r上的A、B、C三个位置的圆周速度均一致,为。这时,差速器并无差速效果,半轴和半轴的角速度与差速器壳3的角速度相等,即。当行星齿轮4除了绕差速器转动轴线公转之外,还围绕自己的轴5以角速度旋转时即自转,啮合点A的圆周速度为,啮合点B的圆周速度为。于是,便得到了两半轴齿轮节圆半径一致的普通对称式行星锥齿轮差速器的运动特征方程:;将其用转速表示为。于是,可以下定半轴和半轴的转速和为差速器壳转速的两倍,却和行星齿轮的转速无关的结论。所以,在汽车转弯行驶或者在其他导致两侧车轮转速不一致的状态下,均可凭借差速器行星齿轮的自转原理,从而使汽车两侧车轮在地面上以不同的转速做纯滚动运动。8.2 差速器的结构确定在驱动桥(中后桥)中选择差速器构造型式时,第一步应该先从所涉及汽车类型(重载汽车)及其使用前提下出发,所选取的差速器型式是否符合该重卡在指定条件下的行驶性能标准。图82 差速器结构形式框图差速器的构造型式多样,它的基本结构形式如图8-2所示。就重载汽车而言,行驶于公路之上,因为地面较为平坦,从而每个驱动车轮与地面的附着系数几乎一致,且附着良好。所以,本设计采取构造简易、运行平顺、铸造便利、各方面性能可靠的对称式圆锥行星齿轮作为差速器的一部分。8.3 差速器的结构参数计算8.3.1 差速器齿轮的基本参数的选择行星齿轮数目n行星齿轮的数量n往往凭借承载状态来选取。普通轿车往往装上两个行星齿轮,而载货汽车和越野汽车基本上装上四个行星齿轮。因此,本节差速器设计选取四个齿轮作为行星齿轮。行星齿轮的球面半径行星齿轮的球面半径呈现的是差速器锥齿轮节锥距的多少和所能承受载荷的大小,能凭借经验公式进行计算 (31)式中:行星齿轮的球面半径指数,在此取2.7;行星齿轮的节锥距为(0.980.99) (32)(0.980.99)83.6=83mm选定行星齿轮齿数与半轴齿轮齿数要取较大的齿轮模数以使其具有足够大的强度,我们一般让行星齿轮的齿数尽可能的少,但往往是多于或者等于10。半轴齿轮的齿数确定为,除此之外,绝大部分汽车中后桥的差速器行星齿轮的齿数和半轴齿轮比例维持在之内。 差速器中的每个行星齿轮和左、右两半轴齿轮均是啮合的,所以,在选择差速器行星齿轮和半轴齿轮的齿数时,我们还要想到它们是怎样进行装配的。于所有对称式圆锥行星齿轮差速器中,行星齿轮数量n一定可以整除两半轴齿轮齿数之和,从而使行星齿轮可匀称地布局在半轴齿轮轴线周围,使其负载布局匀称,不然,差速器会因为其载荷布局不均而安装失败。因此,符合的差速器行星齿轮的安装前提是: (33)式中:、分别是左、右两半轴齿轮齿数,因为本设计选取的是对称式圆锥行星齿轮作为差速器的一部分,所以=; n行星齿轮数目,n=4; I任意整数取=10;=18; 满足以上要求。选定行星齿轮与半轴齿轮的节锥角、和模数m (34) (35)由3-4,3-5得=29.1;=60.9锥齿轮大端端面模数m (36)取m=8,则;。压力角近年来,差速器在汽车上基本上采取压力角为的行星齿轮,齿高指数为0.8的齿形。故取。行星齿轮轴的直径和其安装深度L (37) (37)式中:差速器传递的扭矩,33250; 支承面的许用挤压应力,去69MPa; l行星齿轮的支承面中心位置至圆锥极点的最短直线长度。;即l=57.6mmL=1.143.6=48.0mm8.3.2 差速器齿轮的几何尺寸计算表31为汽车差速器的锥齿轮几何参数运算过程及结果。表中切向修正系数参考汽车车桥设计图47,在此取=-0.050。表31 汽车差速器直齿锥齿轮的几何参数计算用表序号项目计算公式计算结果(1)行星齿轮齿数10(2)半轴齿轮齿数(1.52.0)18(3)模数8(4)齿面宽b=(0.250.3);25mm(5)工作齿高12.8mm(6)全齿高14.355mm(7)压力角22.5(8)轴交角90(9)节圆直径80mm;144mm(10)节锥角;29.1;60.9(11)节锥距82.2mm(12)周节t=3.1416m25.1328mm(13)齿顶高;8.4mm;4.4mm(14)齿根高;5.9mm;9.9mm(15)径向间隙1.555mm(16)齿根角 ;5.8;3.1(17)面锥角;32.2;66.7(18)根锥角;23.3;57.8(19)外圆直径94.7mm;148.3mm(20)节锥极点到齿轮外缘的最短直线长度;67.9mm;36.2mm(21)理论弧齿厚;14.6mm;10.5mm(22)齿侧间隙B0.250mm(23)弦齿厚;10.4mm;10.4mm(24)弦齿高;9.0mm;4.5mm8.3.3 差速器齿轮的强度计算差速器的行星齿轮和半轴齿轮尽管总是啮合的,然而它们并不是总是相对转动的,只有当左、右两边车轮速度不一致时才会有相对转动的现象。然而,于汽车正常行驶过程中,该种状况往往不是很多。因此,这些齿轮齿面的接触疲劳破坏一般不会发生,主要是齿轮弯曲强度的破坏。这里我们只考虑弯曲强度计算。轮齿的弯曲应力为 (38)式中:T半轴齿轮计算转矩,=0.633250=19950; n行星齿轮数,n=4; 、半轴齿轮的齿面宽度及大端节圆直径,25mm、144mm; 尺寸系数,1.6,=0.75; 取1; 质量系数,取1; J综合系数,如图33,取J=0.260综上,差速器行星锥齿轮达到弯曲强度校核的计算标准。图33 弯曲计算综合系数J第9章 传动轴的结构设计9.1 传动轴万向节联轴器的功用和组成万向节联轴器通常是用来联接两轴(在此主要联接中桥和后桥)并在其间传递运动和转矩的。其能减小振动与降低冲击,往往用来防止被联接工作件承受太大的负载。万向节联轴器联接两轴时,只要机器在运转,两轴就不会分离,所以,万向节联接是极其可靠的。除了这些作用,它还能进行位置补偿作用,用于补偿因为制造及装配的误差、负载后的变形、轴承的磨损、旋转部件的不均衡及温度的升降而导致两轴轴线存在一定程度的相对位移和偏斜的影响。万向节的设计应符合下列要求:使所联接的两轴交角及相对位置在安全范围内变动,而且能有效地传递动力和转矩。使所联接的两轴尽可能转速相对变动较小的运动。因为万向节交角而导致的附加负载、振动和噪声要符合其许用范围。传动效率高,运行寿命长,构造简单,制造便利,维修容易。本设计选择使用普通十字轴式万向节。十字轴式万向节基本上是由主动叉、从动叉、十字轴、滚针轴承及其轴向定位件和橡胶密封件等构成。9.2 万向节的设计计算a依据发动机的最大转矩和一档传动比,计算万向传动轴的计算负载: (61)b依据驱动轮打滑,计算万向传动轴的计算负载: (62)c依据日常平均使用转矩,计算万向传动轴的计算负载:由式25,得上述式子中,取所以作用在十字轴轴颈中央的力是 (63)式中:r合力F作用线到十字轴中心的最短直线长度,取60mm; 主、从动叉轴的最大交角,在此取18 (64) (65)式中:十字轴轴颈直径,取30mm; 十字轴油道口部直径,在此取9mm; s合力F作用点到轴颈根部的直线长度,取15mm为弯曲应力的许用值,为250350MPa;为切应力的许用值,为80120MPa,所以该十字轴符合强度要求计算。要使十字滚针轴承中的滚针不被压破,它的直径一般大于或等于,在此取。此外,尺寸不能相差太大,否则会加剧载荷在滚针间的分配下的不均匀性,所以将其限制于之内。滚针轴承径向间隙太大时,承受载荷的滚针数目减少,将会造成滚针卡住;间隙过小时,将会造成其因受热而卡住,所以需要将径向间隙限制于之内。为了提高滚针承载能力,又不会因为滚针过长而导致应力集中,滚针长度应小于轴颈长度,在此取其长度为。滚针工作长度因此,十字轴滚针轴承的接触应力计算为 (66) (67)式中:每个滚针在合力F作用下所承受的最大负载; i、Z滚针列数、每列滚针数,在此取3和18在滚针和十字轴轴颈表面硬度不低于的前提下,许用应力,所以,此滚针符合接触应力要求。h=120mm查汽车设计表43得k=0.208。万向节叉和十字轴构成一个连接支承,由于合力
- 温馨提示:
1: 本站所有资源如无特殊说明,都需要本地电脑安装OFFICE2007和PDF阅读器。图纸软件为CAD,CAXA,PROE,UG,SolidWorks等.压缩文件请下载最新的WinRAR软件解压。
2: 本站的文档不包含任何第三方提供的附件图纸等,如果需要附件,请联系上传者。文件的所有权益归上传用户所有。
3.本站RAR压缩包中若带图纸,网页内容里面会有图纸预览,若没有图纸预览就没有图纸。
4. 未经权益所有人同意不得将文件中的内容挪作商业或盈利用途。
5. 人人文库网仅提供信息存储空间,仅对用户上传内容的表现方式做保护处理,对用户上传分享的文档内容本身不做任何修改或编辑,并不能对任何下载内容负责。
6. 下载文件中如有侵权或不适当内容,请与我们联系,我们立即纠正。
7. 本站不保证下载资源的准确性、安全性和完整性, 同时也不承担用户因使用这些下载资源对自己和他人造成任何形式的伤害或损失。

人人文库网所有资源均是用户自行上传分享,仅供网友学习交流,未经上传用户书面授权,请勿作他用。
2:不支持迅雷下载,请使用浏览器下载
3:不支持QQ浏览器下载,请用其他浏览器
4:下载后的文档和图纸-无水印
5:文档经过压缩,下载后原文更清晰
|