【温馨提示】 购买原稿文件请充值后自助下载。
[全部文件] 那张截图中的文件为本资料所有内容,下载后即可获得。
预览截图请勿抄袭,原稿文件完整清晰,无水印,可编辑。
有疑问可以咨询QQ:414951605或1304139763
目 录
1 绪论1
1.1 课题的研究背景1
1.2国内外桥式起重机发展概况1
1.3 本论文的主要内容2
2. 桥式起介绍4
2.1 桥式起重机的特点和分类4
2.1.1通用桥式起重机4
2.1.2专用桥式起重机5
2.1.3电动葫芦型桥式起重机6
2.2桥式起重机的组成和特点7
2.2.1桥式起重机小车7
3.总体方案设计8
3.1引言8
3.2起重机设计的总体方案8
3.2.1方案一:选择箱形双梁桥式起重机8
3.2.2方案二:选择通用吊钩桥式起重机9
3.3方案的确定10
3.4 小结10
4起升机构的设计及计算11
4.1 引言11
4.2 吊钩电动起升机构的布置方案11
4.3 主起升机构的计算14
4.3.1 钢丝绳直径的选取14
4.3.2 滑轮与卷筒的计算15
4.3.3 选择电动机17
4.3.4 减速器的选择18
4.3.5选择制动器19
4.3.6选择联轴器21
4.4 副起升机构的计算22
4.4.1 钢丝绳直径的选取22
4.4.2 滑轮、卷筒的计算23
4.4.3 电动机的选择24
4.4.4 减速器的选择25
4.4.5 选择制动器26
4.4.6 联轴器的选择28
4.5 小结29
5 结论30
5.1全文总结30
5.2展望30
参 考 文 献32
致 谢33
1 绪论
1.1 课题的研究背景
当今中国工业经济处于高速发展时期,建筑工业化和工业现代化的进程中起重机的使用是不可缺少的。
从古代,人们为了建造大型建筑就发明了原始的起重设备,到了今天,起重机设计制造已经成为一个专门的产业。起重设备的应用给人们带来了很大的便利,小到仓库里的叉车,大到航天中心的吊装火箭的起重机械,建筑工地上随处可见的塔式起重机,港口码头的大型龙门吊,起重机的身影无处不在。
正是由于起重机使用的普遍性,起重机设计制造具有很强的应用性。据数据显示,仅工程起重机一项,全球的年销售额就有75亿美元,但是这些大多是由欧美企业垄断。
近些年来,伴随着我国固定资产投资的飞速增长、基础设施建设和大型项目的不断上马,使得我国工程机械行业获得了空前的发展,也受到了人们越来越多的关注。我国的起重机制造商与欧美的竞争对手相比在技术上还存在着差距,在产业链条,产品结构方面也存在着一定的劣势,但这并非遥不可及。更主要的是,我国在这一领域从未放弃过自主研发,而且已经具备了相当大的产业规模,创造了几个蜚声全球的知名品牌。
起重机属于典型的机械产品,根据其使用环境的不同,起重机的设计又具有不同特性,作为毕业设计的选题不仅可以检验自己的机械专业能力还可以考察创新创造能力。
1.2国内外桥式起重机发展概况
起重机械是用来对物料进行起重、运输、装卸或安装等作业的机械设备。它在国民经济各部门都有广泛的应用,起着减轻体力劳动、节省人力、提高劳动生产率和促进生产过程机械化的作用。起重机械在现代化生产过程中决不是可有可无的辅助工具,而是合理组织生产的必不可少的生产设备。
通用桥式起重机是使用最为广泛的桥架型起重机。目前,国产通用桥式起重机系列尚未采用参数化设计系统,既不能将设计人员从大量繁琐的重复劳动中解放出来,也不能发挥出CAD/CAM的有事。为了发挥设计人员的创造性减少设计、计算、制图、制表所需的时间,缩短设计周期,新产品,新材料,新工艺的研究,会使得起重机的整机布置更趋优化,部件更加紧凑耐用;起重机的控制和安全保护装置大为改善,保证了操作的安全性和可靠性。
我国的起重机械制造行业起步较晚,原有的基础比较薄弱,与工业先进型国家相比,差距不小。但是,经过见过60年来的不断发展,目前的差距明显缩小,已经建立起自己的子终极研究部门、生产厂和专业人才培养的高等学校,并能够批量生产各种累心轨道起重机械,不仅满足了国内市场需求,部分也打入了国际市场。
目前世界上最大的履带起重机起重量3000t,最大的桥式起重机起生日一1200t,集装箱岸连装卸桥小车的最大运行速度已达350m/min,堆垛起重机级最大运行速度240m/min,垃圾处理用起重机的起升速度达100m/min。实现了 重点产品大型化,高速化和专用化 德国、英国、法国、美国和日本的著名起重机公司采用起重机模块化设计,并取得了显著的效益。德国德马格公司的标准起重机系列改用模块化设计后,比单件设计的设计费用下降12%,生产成本下降45%,经济效益十分可观。 起重机的更新和发展,在很大程度上取决于电气传动与控制的改进。将机械技术和电子技术相结合,将先进的计算机技术、微电子技术、电力电子技术、光缆技术、液压技术、模糊控制技术应用到机械的驱动和控制系统,实现起重机的自动化和智能化。 例如德国采用激光装置查找起吊物的重心位置,在取物装置上装有超声波传感器引导取物装置自动抓取货物。吊具自动防摇系统能在运行速度200m/min,加速度0.5m/s2情况下很快使起吊物摇摆振幅减至几个毫米。起重机可通过磁场变换器或激光达到高精度定位。在起重机单机自动化的基础上,通过计算机把各种起重运输机械组成一个物料搬运集成系统,通过中央控制室的控制,与生产设备有机结合,与生产系统协调配合。这类起重机自动化程度高,具有信息处理功能,可将传感器检测出来的各种信息实施存储、运算、逻辑判断、变换等处理加工,进而向执行机构发出控制指令。日本东芝浜川崎工厂用全自动桥式起重机组成的物料输送系统来搬运柔性加工线上的夹具和工件,为机床运送毛坯或将加工好的零件送到下一工序或仓库。
目前各行业中使用的桥式起重机数不胜数,普遍采用小型PLC控制和调压调速,基本上没有智能化产品。中小型桥式起重机大多应用16/3.2T,50/10T以及32/16T等类型,在冶金工业的大型起重机,各大钢铁公司基本上采用200t~480t起重机,而中小企业绝大多数采用趋于淘汰边缘的75t~160t起重机,这些起重机的更新换代和现代化改造项目,形成了巨大的市场需求,也是科研人员进一步研发的动力和机会。
1.3 本论文的主要内容
桥式起重机主要由金属结构、机械部分(机构)和电气设备三大部分组成。金属结构部分的设计主要是指桥架的结构设计,比较复杂,而电气设备是用来控制起重机的运转,在本次设计中没有对它们进行设计计算,机械部分(机构)主要包括起升机构和运行机构等,这是本设计的重点。本论文的主要设计内容如下:
根据已知的数据参数和起重机的工作等级,首先确定此次设计的总体方案,根据所确定的方案,进行设计计算。
起升机构用来实现货物的升降,是任何起重机不可缺少的部分,是起重机中最重要与基本的机构。50/10t桥式起重机,有主、副两套起升装置,首先应确定好两套装置的合理布置方案,两套装置的原理相类似,只是额定起重量不同,布置方案确定好后,就可以开始进行计算了。起升机构主要由驱动装置、卷绕系统、取物装置与制动装置等组成。完成了对其组成部分的数据计算后,利用AutoCAD把它们装配在一起,可以直观的检查设计是否合理,提前发现问题。
2. 桥式起介绍
2.1 桥式起重机的特点和分类
1、桥式起重机的特点:
取物装置悬挂在可沿桥架运行的起重小车或运行式葫芦上的起重机,称为“桥架型起重机”。
桥架两端通过运行装置直接支撑在高架轨道上的桥架型起重机,称为“桥式起重机”。
桥式起重机一般由装有大车运行机构的桥架、装有起升机构和小车运行机构的起重小车、电气设备、司机室等几个大部分组成。外形像一个两端支撑在平行的两条架空轨道上平移运行的单跨平板桥。起升机构用来垂直升降物品,起重小车用来带着载荷作横向运动;桥架和大车运行机构用来将起重小车和物品作纵向移动,以达到在跨度内和规定高度内组成三维空间里作搬运和装卸货物用。
桥式起重机是使用最广泛、拥有量最大的一种轨道运行式起重机,其额定起重量从几吨到几百吨。最基本的形式是通用吊钩桥式起重机,其他形式的桥式起重机基本上都是在通用吊钩桥式的基础上派生发展出来的。
2、桥式起重机的分类
(1)通用桥式起重机 (2)专用桥式起重机 (3)电动葫芦型桥式起重机
2.1.1通用桥式起重机
通用桥式起重机是指在一般环境中工作的普通用途的桥式起重机(见标准GB/T14405-93)。以下类型的起重机都属于通用桥式起重机。
①通用吊钩桥式起重机
通用吊钩桥式起重机由金属结构、大车运行机构、小车运行机构、起升机构、电器及控制系统及司机室组成。取物装置为吊钩。额定起重量为10T以下的多为1个起升机构;16T以上的则多为主、副两个起升机构。这类起重机能大多种作业环境中装卸和搬运物料及设备。
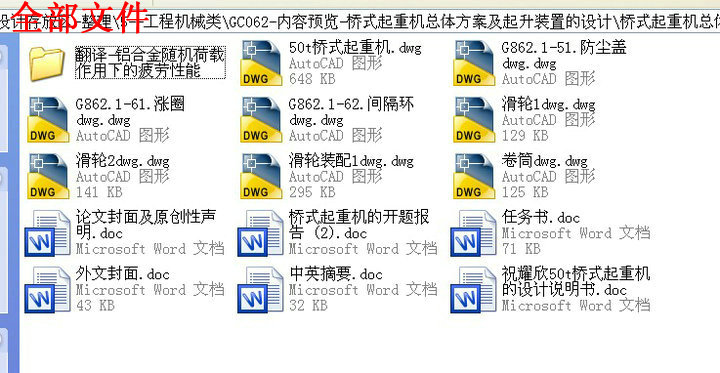
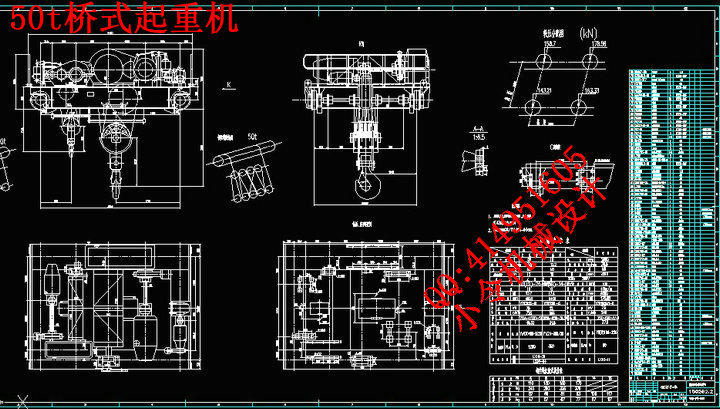
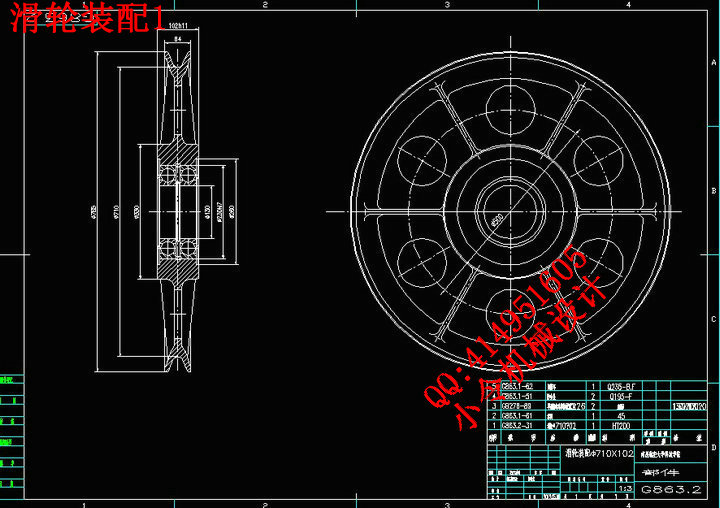
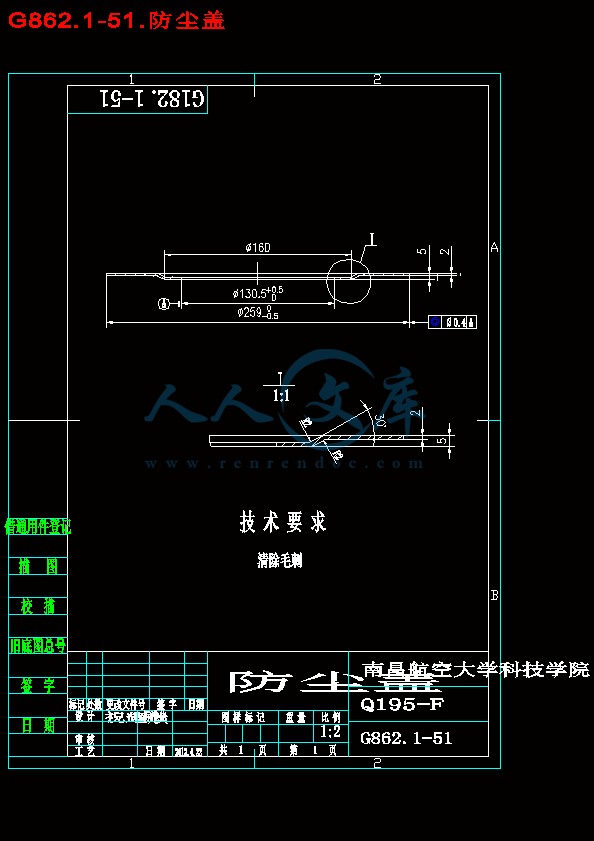


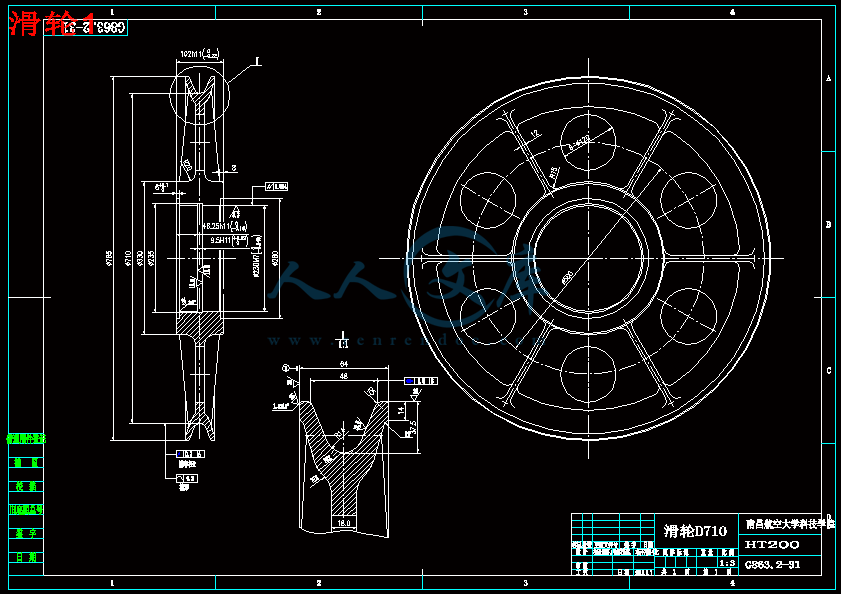
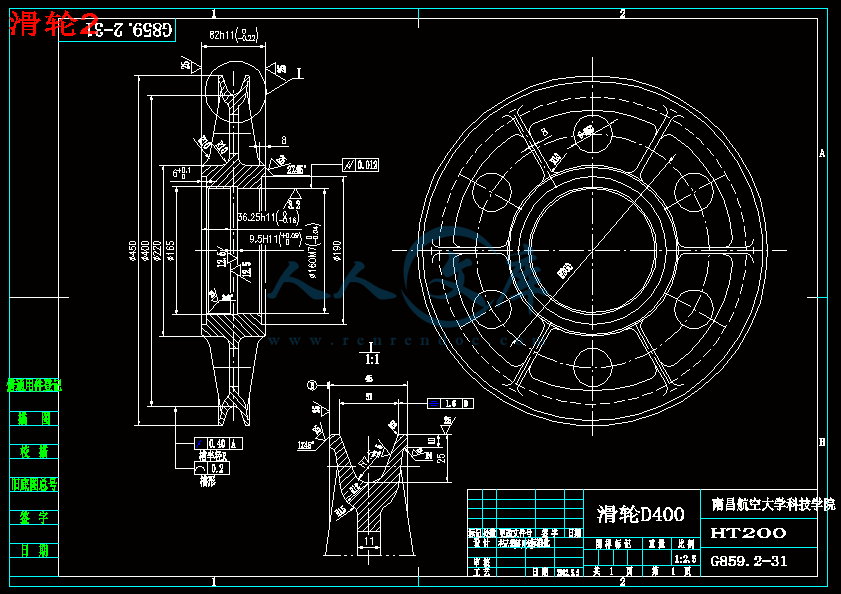
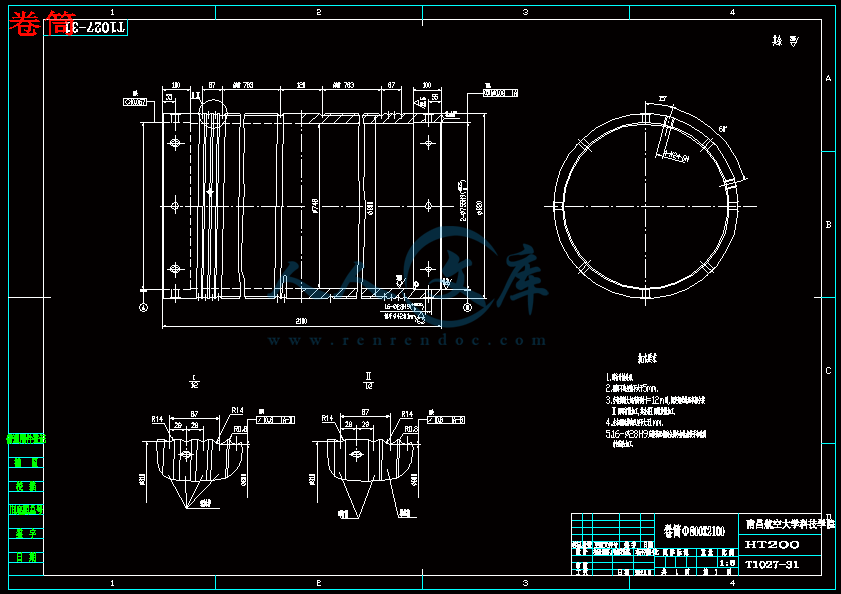