柴油机汽缸体两端面铣削专机设计
50页 18000字数+说明书+任务书+开题报告+10张CAD图纸【详情如下】
3机床联系尺寸图A0.dwg
4主轴箱A0.dwg
5夹具装配图A0.dwg
6支承板结构尺寸图A3.dwg
7螺杆结构尺寸图A3.dwg
8支撑轴结构尺寸图A3.dwg
9压板结构尺寸图A2.dwg
任务书.doc
柴油机汽缸体两端面铣削专机设计开题报告.doc
柴油机汽缸体两端面铣削专机设计说明书.doc
计划周记进度检查表.xls
10导向板结构尺寸图A3.dwg
1零件加工工序图A1.dwg
2加工示意图A1.dwg
摘 要
本课题是柴油机汽缸体两端面铣削专机设计,主要是完成机床夹具设计、组合机床总体设计、组合机床主轴箱设计。根据柴油机汽缸体的结构特点、加工部位、尺寸精度、表面粗糙度及生产率等要求,确定该机床为卧式组合机床;考虑工件尺寸精度,表面粗糙度,切削的排除生产率等因素,选用硬质合金不重磨式面铣刀;根据工件的尺寸、特点及其材料选择切削用量;然后,再经过切削用量来确定组合机床的通用部件;最后进行组合机床的总体设计。由于是铣削柴油机汽缸体的两端面,则夹具的设计可以采用“一面两销”定位,手动夹紧,一次装夹加工汽缸体两端面,保证加工精度,提高生产率;根据工作将受到切削力来计算夹紧力;再根据夹紧力来选择确定夹紧装置的专用部件。
在设计之中,尽量使用通用件,减少制造成本,增加经济效益。通过本次设计可以达到的效果是:所设计的夹具及主轴箱能满足所需的质量要求,使用时安全可靠,拆装方便,易于维修。
关键词:组合机床;汽缸体;铣刀;夹具
目 录
摘 要III
AbstractIV
目 录V
1 绪论1
1.1 课题来源1
1.2 国内外的发展状况1
1.3 指导思想和设计要求2
2 总体方案论证3
2.1 被加工零件分析3
2.2 工艺方案的制定3
2.3 加工设备方案选择3
2.4 确定机床总体布局4
3 切削用量的选择及计算5
3.1 切削刀具的选择5
3.2 切削用量的选择5
3.3 切削力、切削转矩、切削功率的确定5
4 组合机床总体设计8
4.1 被加工零件工序图8
4.2 加工示意图9
4.3 机床联系尺寸图10
4.3.1 动力部件的选择10
4.3.2 滑台及相配底座的选择11
4.3.3 确定机床的装料高度H11
4.4 机床生产率计算卡11
4.4.1 理想生产率Q11
4.4.2 实际生产率Q112
4.4.3 机床负荷率?负13
4.4.4 编写机床生产率计算卡14
5 主轴箱设计15
5.1 主轴及传动轴结构设计15
5.2 主轴箱传动计算16
5.2.1 传动比分配16
5.2.2 传动系统设计及齿轮的排布17
5.3 主轴箱的润滑及油泵轴的确定18
5.4 轴的计算及主轴校核18
5.5 齿轮的校核20
5.6 轴承的选择与校核21
6 夹具设计24
6.1 定位误差分析计算24
6.2 夹紧装置设计25
6.3 夹紧力的计算25
6.4 夹具零部件的设计27
6.4.1 夹具体的设计27
6.4.2 支座的设计28
6.4.3 支承板的设计28
6.4.4 螺杆的设计29
6.4.5 支承轴的设计30
6.4.6 压板的设计30
6.4.7 导向板的设计31
7 液压系统设计32
7.1 负载分析32
7.2 负载图和速度图的绘制32
7.3 液压缸主要参数的确定32
7.4 拟定液压系统原理图35
7.4.1 液压系统的工作要求的确定35
7.4.2 拟定液压系统图35
7.5 计算和选择液压元件37
7.5.1 确定液压泵的最高工作压力37
7.5.2 确定液压泵流量38
7.5.3 选择液压泵规格38
7.5.4 计算油泵需要的电机功率38
7.6 阀类元件的选择38
7.7 油管的确定39
7.8 确定其它辅助装置39
7.9 发热及油箱容量计算39
8 结论与展望40
8.1 结论40
8.2 展望40
致 谢41
参考文献42
2 总体方案论证
设计的机床要满足加工要求、保证加工精度;尽可能选用通用件、以降低成本.因此根据上述要求和柴油机气缸体的加工特点来确定设计方案.
2.1 被加工零件分析
被加工零件:柴油机气缸体
材料:HT250
硬度:187—255HBS
年产量:7万件
加工部位:两端面
加工要求:汽缸体两端面粗糙度被加工到6.3m ,两端面尺寸至582±0.3mm
2.2 工艺方案的制定
工艺方案的拟订是组合机床设计的关键一步.组合机床的总体设计要注重工件及其加工的工艺分析,只有制定出先进合理的工艺方案,才能设计出先进合理的组合机床.根据指定的加工要求,提出若干个工艺方案,择其佳者.工艺方案确定了,组合机床的结构、性能、运动、传动、布局等一系列问题也就解决了.所以,工艺方案设计是组合机床设计的重要环节.而且工艺方案在很大程度上决定了组合机床的结构配置和使用性能.因此,必须认真分析被加工零件图纸,深入了解被加工零件的结构特点、加工部位、尺寸精度、表面粗糙度和技术要求及生产率要求等一些因素.
拟定组合机床工艺方案的一般步骤如下:
1.分析、研究加工要求和现场工艺,在制订组合机床工艺方案时,首先要分析、研究被加工零件,如被加工零件的用途及其结构特点、加工部位及其精度、表面粗糙度、技术要求及生产纲领;其次深入现场调查分析零件的加工工艺方法、定位夹紧方式、所采用的设备、刀具及切用量、生产率情况等.
2.定位基准和夹压部位的选择组合机床一般为工序集中的多刀加工,不但切削负荷大,而且工件受力方面变化.因此,正确选择定位基准和夹压部位是保证加工精度的重要条件.
本道工序主要是加工毛坯,因此,还要对毛坯基准选择考虑有关工序加工余量的均匀性.定位夹压部位的选择应在有足够的夹紧力下工件产生的变形最小,并且夹具易于设置导向和能过刀具.
本道工序:粗铣柴油机气缸体两端面.
2.3 加工设备方案选择
在机械制造业中,金属切削机床占机械设备总台数的50%~70%,它负担的工作量约占一半左右,其中有30%~50%的工作量是由组合机床来完成的,同时,机械加工方法是机电产品及零部件生产的主要方法,且机械加工质量又是提高整个产品质量的关键.因此,组合机床的开发、设计,是机械制造行业一项非常重要的工作.组合机床是根据工件加工需要,以大量通用部件为基础,配以少量专用部件组成的一种高效专用机床,具有如下特点:
1.生产率高;
2.加工精度稳定;
3.研制周期快,便于设计、制造和使用、维护;
4.自动化程度高,劳动强度低;
5.配置灵活,可按工件或工序要求灵活组成机床自动线,易于改装,产品或工艺变化时,通用部件还可以重复利用;
6.使用稳定,结构紧凑,机床费用低.
由于此次被加工的零件已定型,生产批量又较大,加工要求也较高,因此必须采用组合机床来进行生产,同时,又是针对双面加工.因此,采用组合机床来进行加工是较适宜、理想的生产方案.

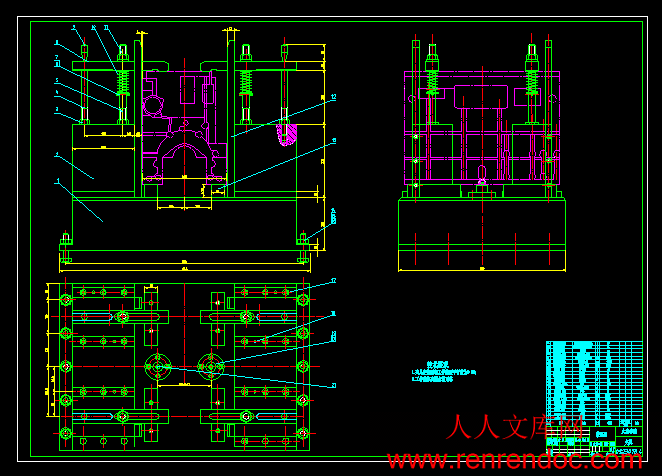
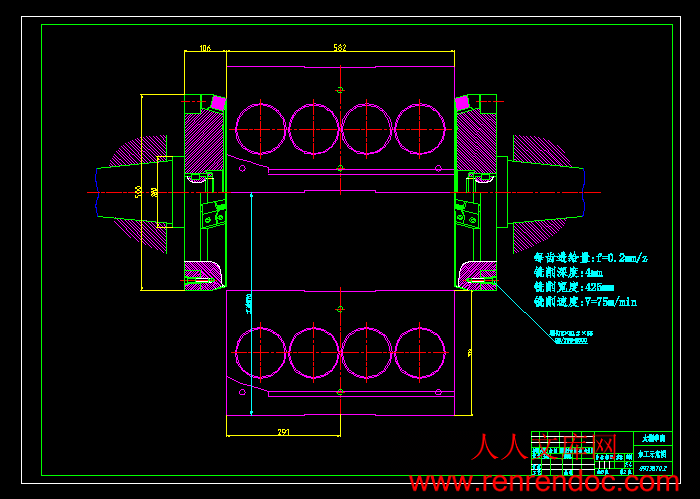

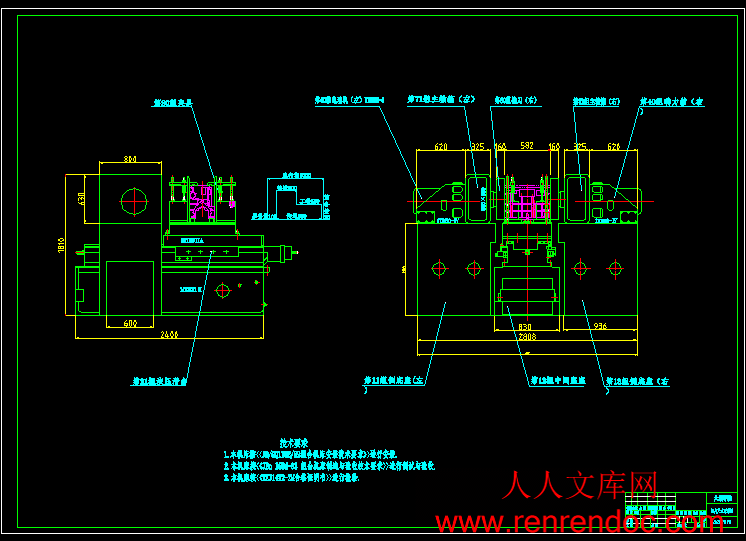