车梁加工用翻转台的设计
38页-11000字数+说明书+开题报告+任务书+6张CAD图纸
任务书.doc
减速器零件图-轴.dwg
原创性申明.doc
封面.doc
开题封面.doc
摘要.doc
目录.doc
车梁加工用翻转台总装图.dwg
车梁加工用翻转台的设计开题报告.doc
车梁加工用翻转台的设计论文.doc
轴承座.dwg
轴承端盖.dwg
输出轴.dwg
链条.dwg
目录
一. 引言
1.选题的依据及意义……………………………………………………(1)
2. 国内外研究概况及发展趋势………………………………………(1)
3.研究内容……………………………………………………………… (2)
二. 总体设计方案和安装使用说明
2.1设计目的…………………………………………………………………(2)
2.2方案的选择和主要参数…………………………………………………(2)
2.3 翻转台设计………………………………………………………………(3)
2.3.1 车梁重心位置的确定………………………………………………(3)
2.3.2 主要尺寸参数的确定………………………………………………(4)
2.4 车梁的装夹结构…………………………… ………… …………… (6)
2.5 翻转台的安装精度………………………………………………………(6)
三. 传动部分的设计计算
3.1 自锁电机功率和转速……………………… …………………………(7)
3.2 各轴转速和功率………………………………………………………(7)
3.3 圆柱齿轮的设计………………………………………………………(9)
3.3.1选择齿轮材料及许用接触应力计算…………………………………(9)
3.3.2按齿面接触疲劳强度设计……………………………………………(9)
3.3.3按轮齿弯曲疲劳强度校核…………………………………………(10)
3.3.4计算齿轮传动的中心矩a……………………………………………(11)
3.4 链传动设计……………………………………………………………(11)
3.5 输入轴的设计计算…………………………………… ………………(13)
3.5.1 输入轴的选材及轴径设计………………………… ………………(13)
3.5.2 轴的结构设计……………………………………… ………………(14)
3.5.3 对输入轴进行校核………………………………… ………………(14)
3.6 输出轴的设计计算……………………………………………………(16)
3.6.1输出轴的选材及轴径设计……………………………………………(16)
3.6.2 轴的结构设计………………………………………………………(16)
3.6.3输出轴的校核………………………………………………………(17)
3.6.4 轴承的选择…………………………………………………………(19)
3.6.5 键的选择……………………………………………………………(20)
3.6.6 减速器箱体尺寸确定………………………… …………………(21)
3.7蜗轮蜗杆的设计计算………………………………… …………… (22)
3.7.1选择材料………………………………………………… …………(22)
3.7.2蜗轮的许用应力……………………………………………………(23)
3.7.3蜗杆与蜗轮的主要参数与几何尺寸………………………………(23)
3.7.4蜗杆轴的设计计算…………………………………………………(24)
3.7.5蜗杆轴的疲劳强度和扭矩强度校核…………………… …………(24)
3.7.6 蜗轮轴的设计计算…………………………………………………(27)
3.7.7减速器箱体尺寸确定………………………………… ……………(30)
3.7.8求作用在蜗轮上的力………………………………… ……………(31)
四、设计总结……………………………………………… ………………(32)
参考文献………………………………………………………… ……………(34)
致谢………………………………………………………………………………(35)
摘要:重型卡车在建筑、矿场等的需求量很大,重型卡车的生产效率决定了市场经济效益。车梁对于车架而言是最基本的基础,决定了车身的安全性能。针对国内车梁加工采用单摇臂钻床靠模加工,加工效率低下,加工精度低,搬运不方便。经过分析单摇臂钻床靠模加工的缺点,对纵梁钻孔翻转系统的设计进行了改进,通过大梁台箱装置的翻转,只需一次安装和定位,减少了车梁的翻转装卸次数,从而减少了反复装卸和定位所引起的定位和加工误差。不仅提高了加工效率,而且增加了厂家的经济效率。
关键词:纵梁钻孔 装置 系统设计
设计目的
机械加工过程中都会使用到夹具来固定工件使之占有正确的位置,以便加工和检测。但是当工件太大而不方便调节位置,不能保证精度,而又有进行旋转加工时,夹具不能满足加工要求。以前,车梁在加工过程中需要使用行车进行多次翻转和定位,才能完成车梁的上各基础孔的钻孔、镗削。效率低,精度低。所以进行车梁加工翻转台的设计,翻转台的必须达到以下的要求:
车梁可绕纵向轴线作正反360。慢转,任何角度均可停止并自锁,使各部面的钻孔都可以转成水平位置作平施工。
车梁上各基础孔的堆焊、镗削均能方便进行,不受翻转台的挡碍。
位置定心滚动。
2.2方案的选择和主要参数:
根据车梁形状和研制要求,曾提出两种方案。它们都由首端和尾端两部分组成。首基本相同,都是用来驱使车梁旋转的动力。由自锁电机、联轴器、链轮、涡轮蜗杆减速器带动主轴低速旋转,固定在主轴一端的转臂与车梁保险杠联接,带其转动。为使不同车型的重心都能调到旋转线上,转臂上设有可调偏心的夹紧装置。两个方案的区别在于尾端结构不同:方案一,翻转台的尾端是由一件直径2.8m 的滚圈和四件滚轮组成,滚圈在滚轮上可作原位置定心滚动。不同型号车梁的尾部都可插入这个滚圈中.夹紧后随圈一齐滚动。用两个平台将首尾端升高,让过旋转的车梁。方案二.翻转台尾端是由一根尾轴和支撑架组成。尾轴是车梁在尾部的旋转中心,它和不同型号车梁的联接.分别有专用钢架完成。比较上述两个方案,从不同车型装夹的适应性、车梁装夹时稳定性和修理时人员的安全程度看,前一个方案较好。虽造价偏高,制造难度偏大,考虑到日后长时间修理工作的方便可靠.我们决定采用第一个方案。
II、毕 业设计(论文)使用的原始资料(数据)及设计技术要求:
本课题旨在设计用于给卡车大梁加工的翻转台的传动系统。此翻转台主要针对长10m
左右,宽2m-2.5m的大型纵梁式卡车车梁。车梁在钻孔过程中需要用起重机吊翻几次进行
各个面的钻孔,工效低,钻孔精度不易保证,所以提出研制车梁翻转台来改变这种状况。
要求技术参数:输入功率7.5kW,旋转速度0.5r/min,最大扭矩58800Nm,车梁可绕纵向
轴线正反360o慢转,任何角度均可停止并自锁。需要设计内容如下:
(1) 翻转台方案设计;(2)传动部份的设计计算;(3)各主要零件的强度计算;
(4)总装图设计;(5)主要零件设计。
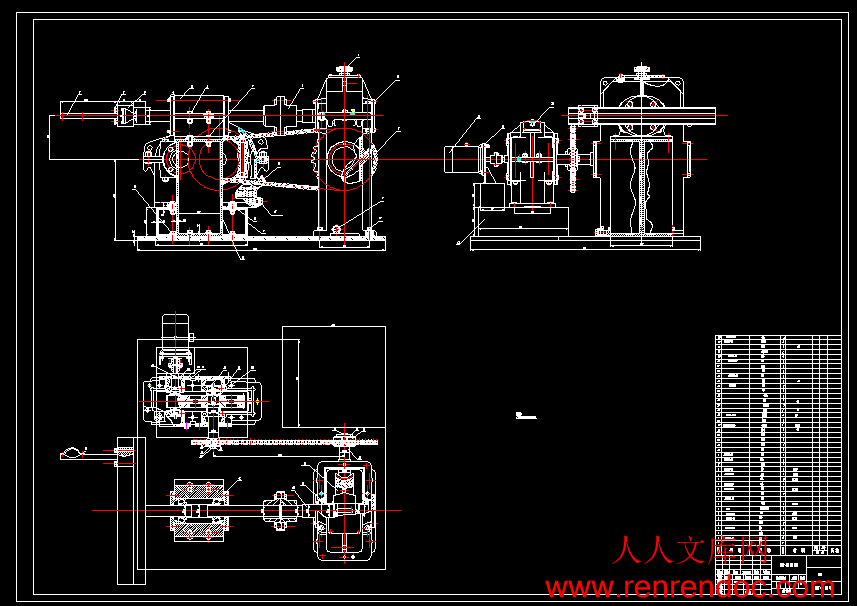