漫步者R211TⅡ低音炮音响外形设计及前面板零件注射模设计
46页 20000字数+说明书+任务书+答辩稿PPT+4张CAD图纸+PROE三维
PROE三维.rar
任务书.doc
前面板.dwg
前面板凸模.dwg
前面板凹模.dwg
扉页.doc
漫步者R211TⅡ低音炮音响外形设计及前面板注射模设计答辩稿PPT.ppt
漫步者R211TⅡ低音炮音响外形设计及前面板零件注射模设计说明书.doc
装配图.dwg
目录
摘要I
AbstractII
第一章 绪论1
1.1我国模具工业及塑料模的发展现状1
1.2 中国模具工业的产业特点2
1.3 模具工业及塑料模技术今后在我国的发展方向3
1.4 Pro/engineer 2001简介5
1.5 注射模简介及pro/engineer 2001在注射模设计过程中的应用6
第二章 低音炮前面板模型设计7
2.1 音炮前面板结构分析7
2.1.1 自顶向下设计简介7
2.1.2 音炮前面板分析8
2. 2塑件的选料及其性能8
2.3音炮前面板注射成型工艺过程9
2.4音炮前面板模型设计过程10
2.4.1 初步造型,切除各预留孔11
2.4.2实体的生成及总体优化设计13
第三章 注射机选择与校核15
3. 1 注射机规格选择15
3. 2 注射机的校核15
3.2.1 注射机注射容量校核15
3.2.2 注射机锁模力校核16
3.2.3 注射机注射压力校核16
3.2.4 注射机模具厚度校核16
3.2.5 注射机最大开模行程校核17
第四章 成型零件的设计18
4. 1 确定分型面18
4. 2 浇注系统形式与浇口设计18
4.2.1 主、分流道设计18
4.2.2 浇口及冷料穴设计20
4.3 凹、凸模成型零件的设计21
4.3.1 建立分型面22
4.3.2 制作浇注系统23
4.3.3 生成成型零件以及浇注件23
4.4 冷却系统设计24
4.4.1 凹模冷却系统设计24
4.4.2 凸模冷却系统设计25
第五章 模架的选择及设计26
5. 1 推出系统设计26
5. 2 确定模架27
5. 3 模架各装配零件设计27
5.3.1 导向零件设计27
5.3.2 浇注系统零件设计29
5.3.3 推出机构零件设计30
5.3.4 定位和支撑零件设计31
5.3.5 其他零件设计31
第六章 模具的装配与调试33
6. 1 模具的装配33
6. 2 模具的调试36
结束语41
参考文献42
文献综述43
摘要
在这次毕业设计中,在进行了简单的市场分析和现有产品的了解后,通过运用三维实体造型软件Pro/Engineer 2001对音炮前面板进行了3D造型,主要完成工作有音炮装配体各个零件的设计,装配体上各零件的细化设计,同时还生成了前面板的塑料注射模具的成型零件,并且设计了浇注系统、冷却系统、模具模架等零件,最后进行了整个模具的装配,生成爆炸图。此外,还就塑件的缺陷及其消除措施进行了简单的探讨。
设计过程中,重点突出了造型设计,成型零件设计,模架设计三个重要工作,在其中造型分模中遇到一定的困难,但是通过努力最终得以解决。
这次设计是对塑件及模具CAD/CAM的一次大胆尝试,相信对实际生产会有一定的指导意义。
关键词:注射模具 热塑性塑料 注射机 低音炮 ABS Pro/Engineer
第二章 低音炮前面板模型设计
2.1 音炮前面板结构分析
2.1.1 自顶向下设计简介
随着计算机技术日新月异的发展,CIMS、并行工程概念的相继产生,以及动态导航技术和参数设计的综合运用,为产品设计从概念设计到零、部件详细设计以及产品的并行设计提供了坚实的基础。为了设计出符合人们设计常规的、面向并行工程的新型CAD系统,我们提出了在装配层次上进行产品建模,用产品装配模型改进现有的CAD系统。自顶向下“Top-down”的设计过程,设计是从产品功能要求出发,选用一系列的零件去实现产品的功能;先设计出初步方案及其结构草图,建立约束驱动的产品模型;通过设计计算,确定每个设计参数,然后进行零件的详细设计,通过几何约束求解将零件装配成产品;对设计方案分析之后,返回修改不满意之处,直到的得到满足功能要求的产品。这种设计过程能充分利用计算机的优良性能,最大限度地发挥设计人员的设计潜力,最大限度地减少设计实施阶段不必要的重复工作,使企业的人力、物力等资源得到充分的利用,有利于提高设计效率,减少新产品的设计研究时间,使企业在市场竞争中占据有利的位置。目前一些流行的CAD系统软件都声称支持Top-down设计。
音炮前面板总体来说结构比较简单,为了使用方便预留各种按钮的靠炮孔,即电源指示灯和音盆。现在前面板的一般都采用各种流线型设计,增强美观效果特别是现在人们欣赏水平的提高,各种个性化、迷你型音响音炮大量出现,造型各异。它们大部分是仍是立式结构,配已木质结构的主体现代而不俗套。内部变化并不影响前面板设计。我在设计时也采用了传统的结构方式,前面板上预置了各种按钮和电源指示灯的靠炮孔。
首先确定以下参数:
1.尺寸精度 塑件的尺寸精度主要取决于塑料收缩率的波动和模具制造误差。由于我们要设计的零件的工作环境对精度要求不高,仅要求外表光滑漂亮,加之选用的塑料ABS推荐精度等级为3、4、5级,因此,塑件的精度等级选用4级已完全满足要求。
2.脱模斜度 脱模斜度大小与塑件的形状、壁厚及收缩率有关。ABS常用的脱模斜度见表2-1。由于脱模过程中最难的地方在于型腔,因此我们把把型腔脱模斜度放大,取1°,型芯的脱模斜度为40′,其余所有需要脱模斜度的地方均取40′。
3.壁厚和圆角 塑件壁厚力求各处均匀,以免产生不均匀收缩等成形缺陷。塑件转角处一般采用圆角过渡,其半径为塑件壁厚的1/3以上,最小不宜小于0.5mm。我们采用的壁厚为2mm,转角处的半径见附录《零件工作图》,即01号图纸。
4.支撑面和加强肋 塑件的支承面应充分保证其稳定性,一般不以塑件的整个底面作为支承面,而将底面设计成凹凸形,或在凹入面增设加强筋。塑件上的加强筋除了能增加刚性和强度外,还能改善塑料熔体的流动性,避免气泡、缩孔和凹陷等成形缺陷。加强筋的形式和尺寸见附录《零件工作图》,即01号图纸。
5.孔 虽然严格意义上讲塑件上的通孔和盲孔通常用单独型芯或分段型芯来成形,对于易弯曲变形的型芯,须附设支承住。但是本次设计中,考虑到生产成本的尽量缩小,以及我们需要的孔在工艺上要求不高,我们采用分型面直接成形法。
2. 2塑件的选料及其性能
机箱前盖一般采用热塑性塑料ABS。
热塑性塑料是在特定的温度的范围内能反复加热软化和冷却硬化的塑料。ABS是acrylonitritle-butadiene-styrene copolymer 的缩写,中文名是丙烯腈-丁二烯-苯乙烯共聚物。ABS的性能可以根据要求通过改变各单体的含量比例进行调整。当丙烯腈增加时,塑料的耐热、耐蚀性和表面硬度可改善;丁二烯可提高弹性和韧性;苯乙烯可改善电性能和成形能力。近年来ABS塑料在汽车上的应用发展很快,如作档泥板、扶手、热空气调节导管,以及小轿车车身等。阻燃级的ABS树脂则用于电子计算机的壳体,控制台、电信、光盘音响设备、彩电的机壳等。
成型性能:
无定性料,流动性中等,吸湿大,必须充分干燥,表面要求光泽的塑件须长时间预热干燥。
宜取高料温、高模温,但料温过高易分解(分解温度为≥250℃)。对精度较高的塑件,模温宜取50~ 60℃,对光泽、耐热塑件,模温宜取60~ 80℃。
综合性能较好,冲击强度较高,化学稳定性、电性能良好。与372有机玻璃的熔接性良好,制成双色塑件,且可表面镀铬。
ABS的主要技术指标见表2-2。

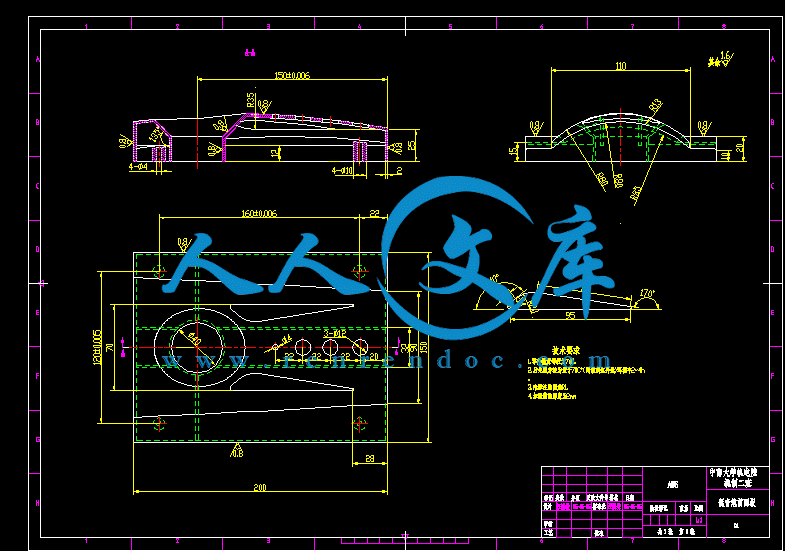
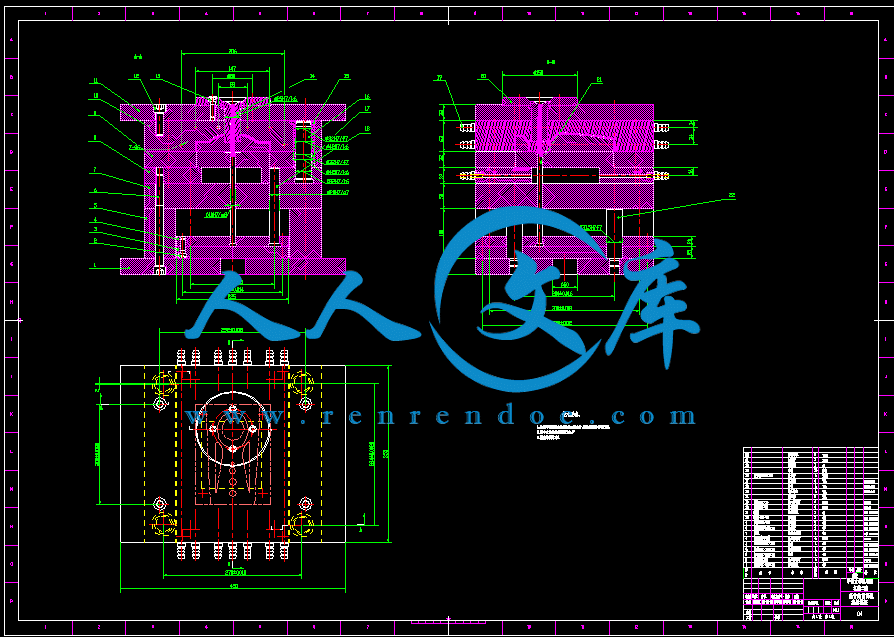