玩具汽车壳模具设计及型腔仿真加工
32页 13000字数+说明书+开题报告+任务书+实习报告+21张CAD图纸
A0装配图.dwg
A2动模垫板.dwg
A2动模板.dwg
A2推杆固定板.dwg
A3制品测绘图.dwg
A3型腔.dwg
A3型芯.dwg
A3定模固定板.dwg
A3定模板.dwg
A3推板.dwg
A4动模固定板.dwg
A4复位杆.dwg
A4定位环.dwg
A4导套.dwg
A4导柱.dwg
A4弹簧.dwg
A4推杆1.dwg
A4推杆2.dwg
A4支架.dwg
A4止位环.dwg
A4浇口衬套.dwg
PROE三维造型.rar
中英文摘要.doc
任务书.doc
实习报告.doc
模具三维图集.doc
模具零件加工工序卡片集
模具零件加工工艺卡片
玩具汽车壳模具设计及型腔仿真加工开题报告.doc
玩具汽车壳模具设计及型腔仿真加工说明书.doc
说明书封面.doc
说明书目录.doc
课题申报表.doc
目 录
1前言…………………………………………………………………………………1
2 总体方案论证………………………………………………………………………3
3具体设计说明……………………………………………………………………4
3.1塑件三维造型……………………………………………………………………4
3.1.1塑件测绘………………………………………………………………………4
3.1.2塑件造型………………………………………………………………………4
3.2模具设计计算……………………………………………………………………5
3.2.1塑件材料性能分析……………………………………………………………5
3.2.2型腔数的确定…………………………………………………………………5
3.2.3型腔壁厚计算…………………………………………………………………6
3.3分型面设计………………………………………………………………………7
3.4浇注系统设计……………………………………………………………………8
3.4.1浇口位置选择…………………………………………………………………8
3.4.2 浇注系统平衡…………………………………………………………………9
3.4.3浇注系统设计计算……………………………………………………………9
3.5冷却系统设计…………………………………………………………………11
3.5.1设计计算…………………………………………………………………11
3.5.2冷却流道结构设计…………………………………………………………12
3.6顶出系统设计…………………………………………………………………13
3.7模架设计………………………………………………………………………15
3.8模流分析………………………………………………………………………16
3.9型腔加工仿真…………………………………………………………………22
3.9.1加工零件工艺审查…………………………………………………………22
3.9.2 毛坯的选择…………………………………………………………………22
3.9.3 基准选择……………………………………………………………………22
3.9.4 Master CAM 9.0仿真加工…………………………………………………22
4结论………………………………………………………………………………25
参考文献……………………………………………………………………………26
致谢…………………………………………………………………………………27
附录…………………………………………………………………………………28
玩具汽车壳模具设计及型腔仿真加工
摘要:本设计是对玩具汽车的模具设计及其零件的加工仿真。设计过程采用Pro/E Wildfire 2.0进行三维造型、分型面设计和模流分析,使用EMX 4.1模块进行模具整体设计,使用Master cam 9.0进行模具型腔仿真加工。
本模具依据厂方给定的注塑机型号和经济性确定型腔为一模四腔;考虑模具中的成型位置及精度等诸多种因素的影响,选取分型面在塑件的底面;为使塑件能够快速均匀冷却,冷却流道布置为环绕式;为使镶块结构不发生泄漏,使用负压冷却水系统;采用平衡式分流道、侧浇口,使型腔同时得到均匀的充填和成型;顶出机构是制品的脱模装置,依据塑件结构采用12根顶杆;由于塑件是薄壁结构可能出现注塑不完整,通过模流分析验证注塑流体可以充满型腔,符合设计要求。根据设计参数,使用EMX对模具整体设计。分析型腔的加工工艺,在Master cam 9.0中完成刀具路径设定,确定数控加工代码,通过仿真加工确定是否满足加工要求。
通过使用模具设计应用软件,使模具设计效率大大提高,完全符合设计要求。
关键词:模具设计;加工仿真;注塑模具;CAM技术
本课题的设计目的是对玩具汽车壳的三维造型及优化、塑料注射模具设计、模具型加工仿真及数控编程。其中:a. 制品的尺寸精度要求:长度方向小于0.50,厚度方向小于0.10; b. 制品材料:ABS;c. 制品表面粗糙度:不低于实物表面;d. 制品生产批量:5万;e. 制品其他要求:符合设计规范。在进行零件的三维造型之前,首先对塑件进行测绘,绘制塑件二维工程图,然后根据工程图进行塑件的三维造型,再进行型腔的设计主要是分型面的设计,接着就是把分型后的型腔装配组件调入EMX4.1进行整个模架的设计,最后进行仿真加工及数控编程。
首先是对塑件进行测绘。由于该塑件大都为曲面实际测量有一定困难所以采用多次取断面进行测量的方法。测绘好后使用Pro/E Wildfire4.0进行三维造型。主要采用拉伸、除料、抽壳等步骤造型。在三维造型之后可以通过Pro/E Wildfire4.0下的“塑料顾问”进行模流分析,通过计算可以验证塑料胶体能不能完全填充满型腔。而后使用Pro/E Wildfire4.0下的EMX4.1模块进行整个模架设计。根据工厂现有设备的注射量、锁模力等方面进行考虑,还有塑件的精度等级确定采用一模四腔。要确保塑件及浇注系统所需的注射量不超过注射机最大容量的80%。接着对各个系统进行设计,首先是浇注系统。浇注系统分为主流道、分流道、浇口、冷料穴等。主流道的中心线与注射机喷嘴的中心线在同一条直线上。由于主流道与高温高压的熔融塑料接触所以外面要加个浇口套。浇口套要进行淬火处理,这样可以延长模具的使用寿命。分流道的半径与塑料种类和所需熔融塑料的体积有关,本模具设计取6mm。主流道与分流道采用圆角过渡,这样可以减小料流转向过渡时的阻力。分流道的布置要均匀处理,确保熔融塑料由主流道到各分流道的距离相等。分流道表面不必很光,可以使熔融塑料的冷却皮层固定,有利于保温。分流道与浇口采用圆弧过渡,有利于熔料的流动及填充。浇口主要有两个作用,一是起控制作用,二是压力撤销后封锁型腔,不产生倒流。在整个模架设计中所有的模架零部件都在EMX中根据自己计算的数据进行选取,所有零部件的三维造型都会在设计完成够自动生成,对以后的二维工程图的绘制提供依据。模具设计完成后,进行型腔的加工工艺分析,在确定加工工艺步骤后,在Master CAM 9.0 中进行刀具路径设定完成仿真加工,而后输出数控程序。

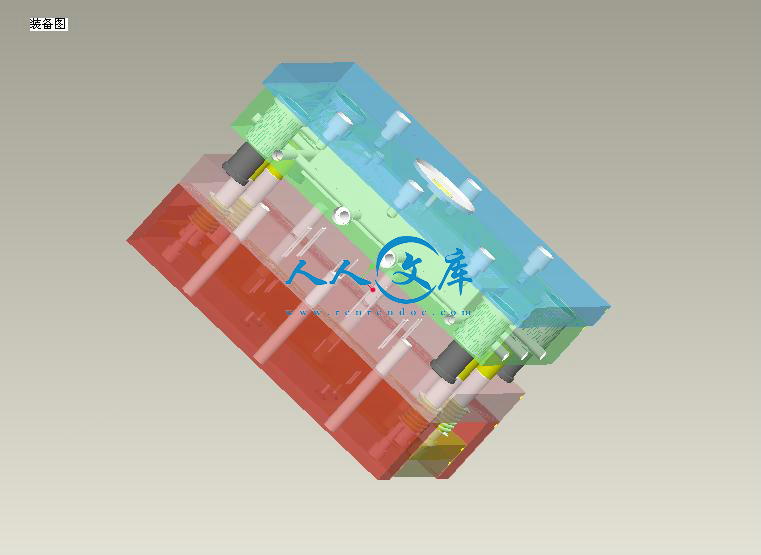
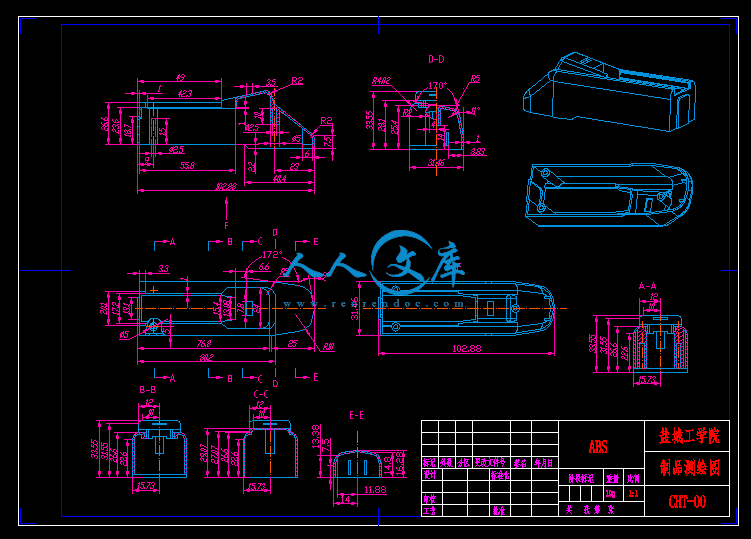