基于UG Moldwizard的注塑模设计和数控加工设计
35页 14500字数+说明书+8张CAD图纸+UG三维图 全套
UG三维图 全套.rar
基于UG Moldwizard的注塑模设计和数控加工设计论文.doc
定位圈.dwg
导套.dwg
导柱.dwg
弹簧.dwg
拉料杆.dwg
推板.dwg
数控加工.rar
草图.dwg
装配图.dwg
目 录
摘 要i
Abstractii
第一章 引言1
1.1 塑料模具现状1
1.2 塑料模具的发展趋势1
第二章 注塑设备及原理3
2.1 注塑机3
2.1.1 注塑机的基本功能3
2.1.2 注塑机结构3
2.2 注塑成型工作原理4
2.2.1 模具生产原理4
第三章 塑件工艺分析5
3.1 塑件的原材料分析5
3.2 塑件结构、尺寸精度及表面质量分析6
3.2.1 结构分析6
3.2.2 尺寸精度分析6
3.2.3 表面质量分析7
3.3 塑件的体积和质量7
第四章 电池板模具设计8
4.1 分型面位置确定8
4.1.1 分型面选取原则8
4.2 型腔数量确定11
4.3 注塑机型号确定12
4.3.1模具所需塑料熔体注射量12
4.3.2 锁模力13
4.3.3 选择注射机型号13
4.4 浇注系统设计14
4.4.1 主流道14
4.4.2 分流道15
4.4.3 浇口设计16
4.5 模架选取17
4.6 侧向分型抽芯机构设计18
4.6.1 侧向分型抽芯机构的分类18
4.6.2 抽拔距19
4.6.3 斜销侧向分型抽芯机构的组成19
4.6.4 斜销长度和最小开模行程计算20
4.7 脱模机构设计21
4.8 模具爆炸图22
第五章 型芯、型腔数控加工24
5.1 数控机床简介24
5.1.1 数控机床特点24
5.2 数控在模具制造业中的应用25
5.2.1 模具制造加工的特点25
5.2.2 模具制造技术的发展趋势25
5.3 型腔数控加工25
5.3.1 型腔分析25
5.3.2 粗加工26
5.3.3 精加工26
5.4 型腔加工程序26
5.5 型芯数控加工27
5.5.1电火花加工27
第六章 总结与展望29
参 考 文 献30
致谢31
摘 要
注塑模具是目前所有塑料模具中使用最广泛的模具之一,能够形成复杂、高精度的塑料制品。本文主要研究了基于UG Moldwizard模块的注塑模设计问题,以及UG加工模块对型芯、型腔的数控加工。由此初步掌握模具设计的方法、过程,为将来走向工作岗位进行科技开发工作和撰写科研论文打下基础。论文首先简单回顾了注塑模的现状及发展趋势,然后以电池板的注塑模具设计为主要内容,详细介绍了注塑模具设计的一般流程,通过对模具所需塑料熔体注射量及模具锁模力的计算,初步选定注射机,同时对模具的分型面进行选择、型腔布局进行设计;其次进行模架的选取、浇注系统的设计以及对抽芯机构进行设计。最后得到模具的三维立体图,并由此导出模具的二维装配图。本论文为UG软件及其外挂程序在注塑模具设计中的应用提供了参考。
关键词:型芯,型腔,浇注系统,抽芯机构,数控加工
2.1.1 注塑机的基本功能
(1)加热塑料,使其达到熔化状态;
(2)对熔融塑料施加高压,使其射出而充满模具型腔。
2.1.2 注塑机结构
注塑机包括注射装置、合模装置、液压系统和电气控制系统等部分。
(1)注射装置:注塑机的主要部分。它的主要作用是使塑料均匀地塑化成熔融状态,并以足够的压力和速度将熔料注射入模具中。
(2)合模装置:它是保证成型模具紧密的闭合和实现开启关闭模动作,以及取出制品的部件。
(3)液压系统和电气控制系统:它是保证注塑机按工艺过程预定的要求(如压力、速度、温度、时间等)和动作程序准确有效的进行工作。
2.2 注塑成型工作原理
注塑成型的基本要求是塑化、注射和成型。塑化是实现和保证成型制品质量的前提,而为满足成型的要求,注射必须保证有足够的压力和速度。同时,由于注射压力很高,相应地在模腔中产生很高的压力,因此必须有足够大的合模力。由此可见,注射装置和合模装置是注塑机的关键部件。注塑成型是一个循环的过程,每一周期主要包括:定量加料——熔融塑化——施压注射——充模冷却——启模取件。取出塑件后又再闭模,进行下一个循环。
注塑机的工作原理:与打针用的注射器相似,它是借助螺杆(或柱塞)的推力,将已塑化好的熔融状态(即粘流态)的塑料注射入闭合好的模腔内,经固化定型后取得制品的工艺过程[3]。
2.2.1 模具生产原理
由凸模和凹模围成型腔,在型腔中填充热融的塑料原料,在一定压力下冷却成型后形成产品。 其过程如图2.2 。
第三章 塑件工艺分析
3.1 塑件的原材料分析
本塑件的几何形状如图3.1所示。塑件的材料采用ABS,属热塑性塑料。ABS树脂是丙烯腈(Acrylonitrile)、聚丁二烯(Butadience)和苯乙烯(Styrene)三种单体共聚而成的,其中丙烯腈(A)使之有较高的硬度,表面光泽;聚丁烯(B)能增加韧性;苯乙烯(S)则使加工性良好,在热塑性树脂中。ABS无毒、无味、显微黄色,成型的塑件有较好的光泽,有极好的抗冲击强度,且在低温下也不迅速下降。ABS最便宜而且容易成型,所以是最经济的材料,且具有良好的综合性能,应用领域很广泛。ABS的主要性能指标如表3.1所示。
图3.1 塑件几何外形
从使用性能上看,该塑件具有高强度,良好的耐水、耐油性,其介电性能与温度和频率无关,是优良的绝缘材料;
从成型性能上看,ABS在升温时粘度增高,所以成型压力较高,ABS吸湿强、成型加工前应进行干燥处理。另外,在成型时应采用较高的成型温度和注射压力,以提高熔料的流动性,减小收缩率。
查资料,ABS的脱模斜度推荐值为:
型腔脱模斜度:40′~1°20′,型芯脱模斜度:35′~1°
表3.1 ABS的主要性能指标
项目/单位 值
密度(Kg.dm-3)1.13~1.14
收缩率%0.3~0.8
熔点℃130~160
热变形温度45N/cm65~98
弯曲强度Mpa80
拉伸强度MPa35~49
拉伸弹性模量GPa1.8
弯曲弹性模量Gpa1.4
压缩强度Mpa18~39
缺口冲击强度kJ/㎡11~20
硬度HRR62~86
3.2 塑件结构、尺寸精度及表面质量分析
3.2.1 结构分析
从零件图上分析,该零件上部为圆帽,最大直径为12mm;下部为两个卡勾,其最大厚度为1.4mm,最小厚度为0.8mm,该零件结构还算比较简单,但在模具设计时,其下部的两个卡勾会影响到正常的脱模,因此得考虑侧向分型与抽芯。
由于塑件成型时冷却过程中产生收缩,使其紧箍在凸模或型芯上,为了便于脱模,防止因脱模力过大而拉坏塑件或使其表面受损,与脱模方向平行的塑件内,外表面都应具有合理的斜度.以下是ABS的脱模斜度推荐值:
型芯 型腔
35′~1° 40′~1.20°
3.2.2 尺寸精度分析
该零件各个尺寸均未注明公差,为提高经济效益,则按未注明公差尺寸来处理,查表3.2得ABS材料的适用未注公差等级为MT5级,对应的模具相关零件的尺寸加工也容易保证。
3.2.3 表面质量分析
该零件的表面质量除要求没有缺陷、毛刺外,没有特别的表面质量要求,因此表面要求易于实现。
综上分析,可以看出,注塑时在工艺参数控制的较好的情况下,零件的成型要求可以得到保证。
表3.2 常用材料模塑件公差等级的选用(GB/T14486)
材料代号模塑材料公差等级
标注公差尺寸未注公差尺寸
高精度一般精度
ABS丙烯腈—丁二烯—苯乙烯共聚物MT2MT3MT5
AS丙烯腈—苯乙烯共聚物MT2MT3MT5
CA醋酸纤维素塑料MT3MT4MT6
3.3 塑件的体积和质量
(1)体积:通过UG软件的“测量体”分析塑件,得到塑件的体积为V=281.9718mm3
(2)质量:材料ABS的密度取=1.14g/ cm3,根据公式4.1得单个塑件的质量为0.32g
(3.1)


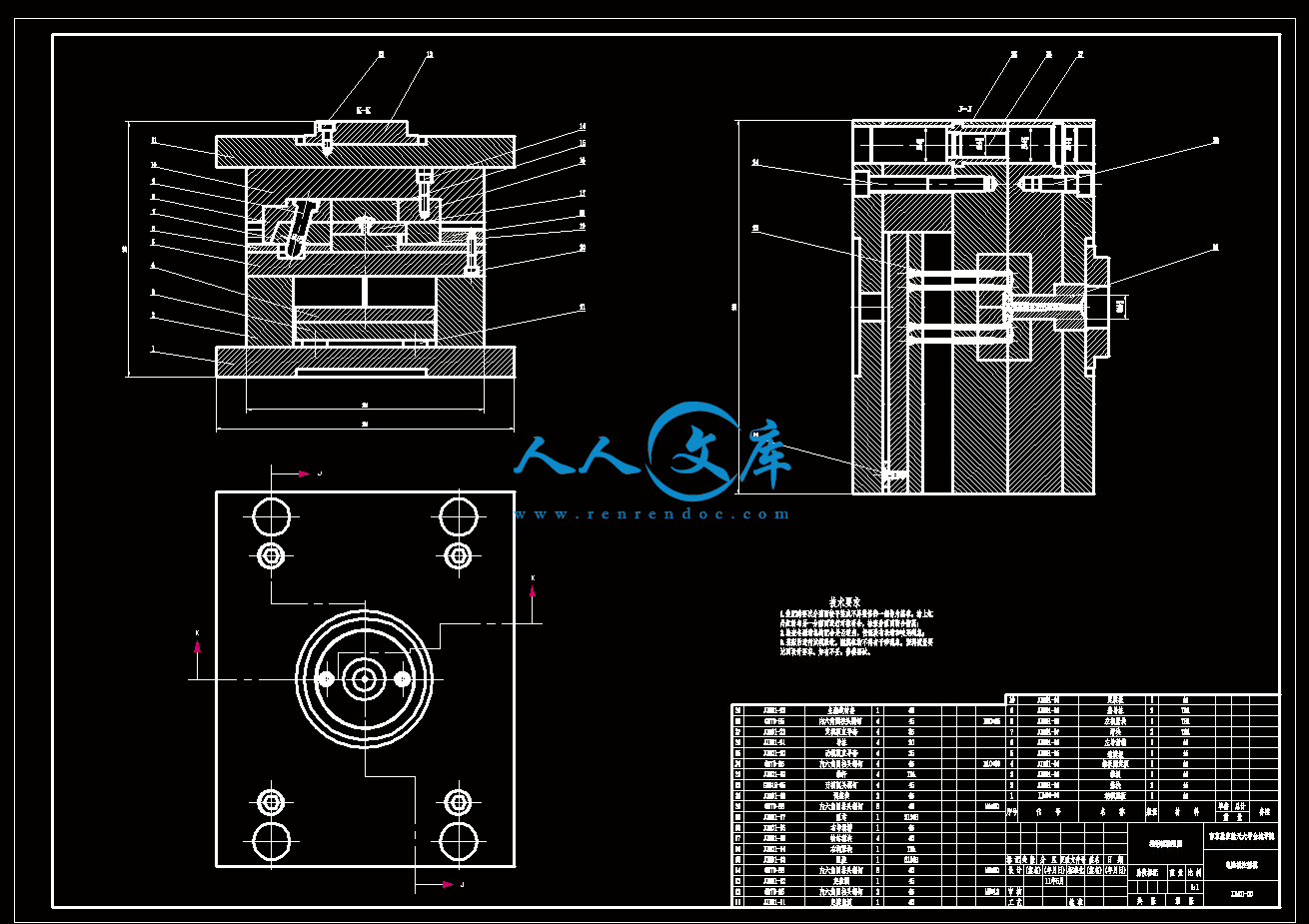
