FSAE赛车双横臂式前悬架设计
83页 23000字数+说明书+任务书+开题报告+ADAMS文件+4张CAD图纸
ADAMS
FSAE赛车双横臂式前悬架装配图.dwg
FSAE赛车双横臂式前悬架设计开题报告.doc
FSAE赛车双横臂式前悬架设计说明书.doc
PROE
上横臂.dwg
下横臂.dwg
任务书.doc
封面.doc
摘要.doc
目录.doc
立柱.dwg
答辩相关材料.doc
过程管理封皮.doc
题目审定表.doc
目 录
摘 要Ⅰ
AbstractⅡ
第1章 绪 论1
1.1 FSAE概述1
1.1.1 背景..1
1.1.2 发展与现状2
1.1.3 国内情况2
1.2 研究内容和方法3
第2章 独立双横臂悬架结构分析4
2.1 悬架的组成与分类4
2.1.1 悬架组成4
2.1.2 悬架分类4
2.2 独立双横臂悬架6
2.3 本章小结8
第3章 独立双横臂悬架设计9
3.1 设计主要依据参数9
3.1.1 影响平顺性参数9
3.1.2簧载质量与非簧载质量10
3.2 螺旋弹簧设计10
3.2.1 螺旋弹簧类型的选择10
3.2.2 弹簧相关计算11
3.3 减振器设计15
3.3.1 减震器形式的选择15
3.3.2相对阻尼系数15
3.3.3 减振器阻尼系数的确定15
3.3.4最大卸荷力的确定16
3.3.5减振器尺寸的确定16
3.4 导向机构的设计17
3.4.1 侧倾中心及横向平面内上、下横臂的布置方案17
3.4.2 纵向平面内上、下横臂的布置方案17
3.4.3 水平面内上、下横臂的布置方案18
3.4.4 上、下横臂长度的确定18
3.5 横向稳定杆设计19
3.5.1稳定杆直径计算19
3.5.2稳定杆校核20
3.6缓冲块20
3.7有限元分析21
3.8 本章小结30
第4章 基于ADAMS/View的悬架优化分析31
4.1 仿真软件ADAMS的介绍31
4.1.1 ADAMS的简介31
4.1.2 ADAMS软件的优点32
4.2悬架建模关键点的确定33
4.3在ADAMS/View中创建悬架模型35
4.3.1建模35
4.3.2 定制界面38
4.4测试悬架模型41
4.4.1 添加驱动41
4.4.2 测量数据41
4.4.3对仿真结果进行分析49
4.5悬架参数化50
4.5.1创建设计变量50
4.5.2设计点参数化51
4.5.3实体参数化54
4.6 设计参数的研究分析56
4.6.1 参数化分析方法56
4.6.2 设计研究56
4.6.3优化方案60
4.6.4优化结果62
4.6.5优化结果的评价62
4.7本章小结62
第5章 悬架实体建模63
5.1悬架各零件的建模63
5.1.1主销的建模63
5.1.2减震器的创建68
5.1.3上横臂的创建68
5.1.4下横臂的创建69
5.1.5关节轴承的创建69
5.2悬架的装配70
5.2.1 各件的装配70
5.2.2 悬架的总装72
5.3本章小结74
结 论75
参考文献76
致 谢78
附 录79
本设计结合悬架设计知识,详细分析了悬架结构,对双横臂独立悬架进行了设计计算。在此基础上,应用虚拟样机技术,在ADAMS/View中对双横臂独立悬架进行合理简化并建模,并对模型进行了参数化,定制界面,即改变初始参数就能快速生成不同的悬架模型,提高了仿真分析以及优化设计的效率,使平台具有开放性。分析研究了所需优化的变量(前轮外倾角、车轮侧滑量)及其函数表达式。进行了悬架动力学仿真分析,研究悬架各性能参数在车轮跳动过程中的变化趋势,并指出需要改进的地方。分析每个设计变量的变化对样机性能的影响,提出优化设计的方案。再次进行仿真,对比分析了优化前后的仿真结果,并评价了优化方案。优化后悬架的性能明显提高,验证了优化方案的可行性,并完成虚拟设计及试验。最后运用Pro/E软件对双横臂独立悬架进行实体的建立。
本设计研究的目的和意义为在赛车制造前进行设计和试验仿真,并且提出改进意见,可以发现并更正设计缺陷,完善设计方案,提高设计质量和效率。
关键词:双横臂;独立悬架;虚拟样机技术;优化;ADAMS
ABSTRACT
On the basis of the Suspension design, this paper calculated a detailed requirements for double wishbone independent suspension structure, I simplified and built a model of double wishbone independent suspension system in ADAMS/View, made the model parameters, then the model was open, and prepared the necessary measuring function. I discussed the performance of the front wheel alignment parameters in a front wheel vehicle positioning. The model was a virtual front suspension test platform. This thesis analyzed the change trend of the suspension performance parameters in the process of flopping the wheel. The impacts of its changes in the trend of design variables are also analyzed, make an optimized design of the program, with the comparative analysis to verify the feasibility of the optimization program before and after the optimization, the suspension’s key data was generated, the virtual design and test were finished. Finally I used Pro/E for double wishbone independent suspension a modeling.
The design for the purpose and significance of the study in car manufacturing design and test before simulation, and puts forward Suggestions of improvement can be found and corrected design flaw, perfecting the design scheme, and improve the design quality and efficiency.
Keywords: Double Wishbone; Independent suspension; Virtual Prototyping Technology; Optimize; ADAMS
2.1、悬架组成和分类
悬架是现代汽车上重要总成之一,他把车架(或车身)与车轴(或车轮)弹性的连接起来。其主要任务是传递作用在车轮很车架(或车身)之间的一切力和力矩;缓和路面传给车架(或车身)的冲击载荷,衰减由此引起的承载系统的振动,保证汽车的行驶平顺行;保证车轮在路面不平和载荷变化时有理想的运动特征,保证汽车的操作稳定性,是汽车获得高速行驶能力。悬架主要由弹性元件,导向装置与减振器等元件组成。
2.1.1、悬架组成
现代汽车的悬架尽管各有不同的结构型式,但一般都是由弹性元件、减振器和导向机构三部分组成。导向机构在轻型汽车中,也是连接车架(或车身)与车桥(或车轮)的结构,除了传递作用力外,还能够使车架(或车身)随车轮按照一定的轨迹运动。这三部分分别起缓冲,减振和力的传递作用。轿车上来讲,弹性元件多采用螺旋弹簧,它只承受垂直载荷,缓和不平路面对车体的冲击,具有占用空间小,质量小,无需润滑的优点,但是没有减振作用。减振器在车架(或车身)与车桥(或车轮)之间作弹性联系,起到承受冲击的作用。采用减振器是为了吸收振动,使汽车车身振动迅速衰弱(振幅迅速减小),使车身达到稳定状态。减振器指液力减振器,是为了加速衰减车身的振动,它是悬架机构中最精密和复杂的机械件。传力装置是指车架的上下摆臂等叉形刚架、转向节等元件,用来传递纵向力,侧向力及力矩,并保证车轮相对于车架(或车身)有确定的相对运动规律。
2.1.2、悬架的分类
根据导向机构的结构特点,汽车悬架可分为非独立悬架和独立悬架
(1)非独立悬架
非独立悬架的左右车轮装在一根整体的刚性轴或非断开式驱动桥的桥壳上,
非独立悬架的优点:结构简单,制造、维修方便,经济性好;工作可靠,使用寿命长;车轮跳动时,车距、前束不变,因而轮胎磨损小;转向是,车身侧倾后轮的外倾角不变,传递侧向力的能力不降低;侧倾中心位置较低,有利于减小转向是车身的侧倾角。缺点:由于车桥与车轮一起跳动,因而需要较大的空间,影响发动机或行李箱的布置;用于驱动桥时,会使得非悬挂质量较大,不利于汽车的行驶平顺性及轮胎的接地性能;当两侧车轮跳动高度不一致时,这跟车桥会倾斜,是左右车轮直接相互影响;在不平路面直线行驶时,由于左右车轮跳动不一致而导致的轴转向会降低直线行驶的稳定性;由于驱动桥时,驱动桥的输入转矩会引起左右车轮负荷转移。非独立悬架广泛应用于载货汽车以及大客车的前后悬架,一些全轮驱动的多用途也采用非独立悬架作为前后悬架。
(2)独立悬架
汽车的每个车轮单独通过一套悬挂安装于车身或者车桥上,车桥采用断开式,中间一段固定于车架或车身上;此种悬挂两边车轮受冲击时互不影响,而且由于非悬挂质量较轻,缓冲与减震能力很强,乘坐舒适,各项指标都优于非独立式悬挂,但该悬挂结构复杂,而且还会使驱动桥、转向系统变得复杂起来。采用此种悬挂的轿车、客车以及载人车辆,可明显提高乘坐的舒适性,并且在高速行驶时提高汽车的行驶稳定性。而越野车辆、军用车辆和矿山车辆,在坏路或无路的情况下,可保证全部车轮与地面的接触,提高汽车的行驶稳定性和附着性,发挥汽车的行驶速度。
与非独立悬架相比,独立悬架具有如下优点:(1)非悬架质量小,悬架所受到并传给车身的冲击载荷小,有利于提高汽车的行驶平顺性及轮胎的接地性能;(2)左右车轮的跳动没有直接的相互影响,可以减少车身的倾斜和振动;(3)占用横向空间小,便于发动机的布置,可以降低发动机的安装位置,从而降低汽车的质心位置,有利于提高汽车的行驶稳定性;(4)易于实现驱动轮的转向[4]。
独立悬架的结构分有横臂式(图2.1a)、纵臂式(图2.1b)、烛式(图2.1c)、麦弗逊式(图2.1d)等多种,其中横臂式又可分为单横臂式和双横臂式[4]。
图2.1 独立悬架的结构
2.2、独立双横臂悬架
双横臂式独立悬架根据上下横臂的长度相等于不相等又可分为等长双横臂式和不等长双横臂式。等长双横臂式悬架在其车轮作上、下跳动时,可以保持主销倾角不变,但轮距却有较大的变化,会使轮胎磨损严重,故已很少使用,多为不等长双横臂式悬架所取代。不等长双横臂悬架在其车轮上、下跳动时,只要适当地选择上、下横臂的长度并合理布置,即可使车轮定位参数的变化量限定在允许的范围内。这种不大的轮距改变,不应引起车轮沿路面的侧滑,而为轮胎的弹性变形所补偿。因此不等长双横臂式独立悬架能保证汽车有良好的行驶稳定行,已为中、高级轿车的前悬架所广泛采用。
当上下横臂长度之比为时车轮平面倾角应不大于。图2.2为不等长双横臂前独立悬架的两种典型结构图[4]。
第3章 独立双横臂悬架设计
3.1、设计主要依据参数
本次设计主要是第一届中国大学生方程式汽车大赛的相关参数来设计的,其具体参数如表3.1。
表3-1 设计相关参数
名称数值单位
车长2900mm
车宽1500mm
车高1200mm
轴距1680mm
前轮距1300mm
后轮距1280mm
离地间隙40mm
前后载荷比46:54
整车整备质量280Kg
总质量360Kg
3.1.2、影响平顺性的参数
前后载荷比46:54
汽车的偏频的计算公式如下:
(3.1)
其中g为重力加速度其值取g=9.8 ,、为前悬架刚度,、为前后悬架的簧载质量[4]。
由于赛车比较注重速度,对舒适性要求不要,所以偏频n=2Hz
(1)静挠度计算
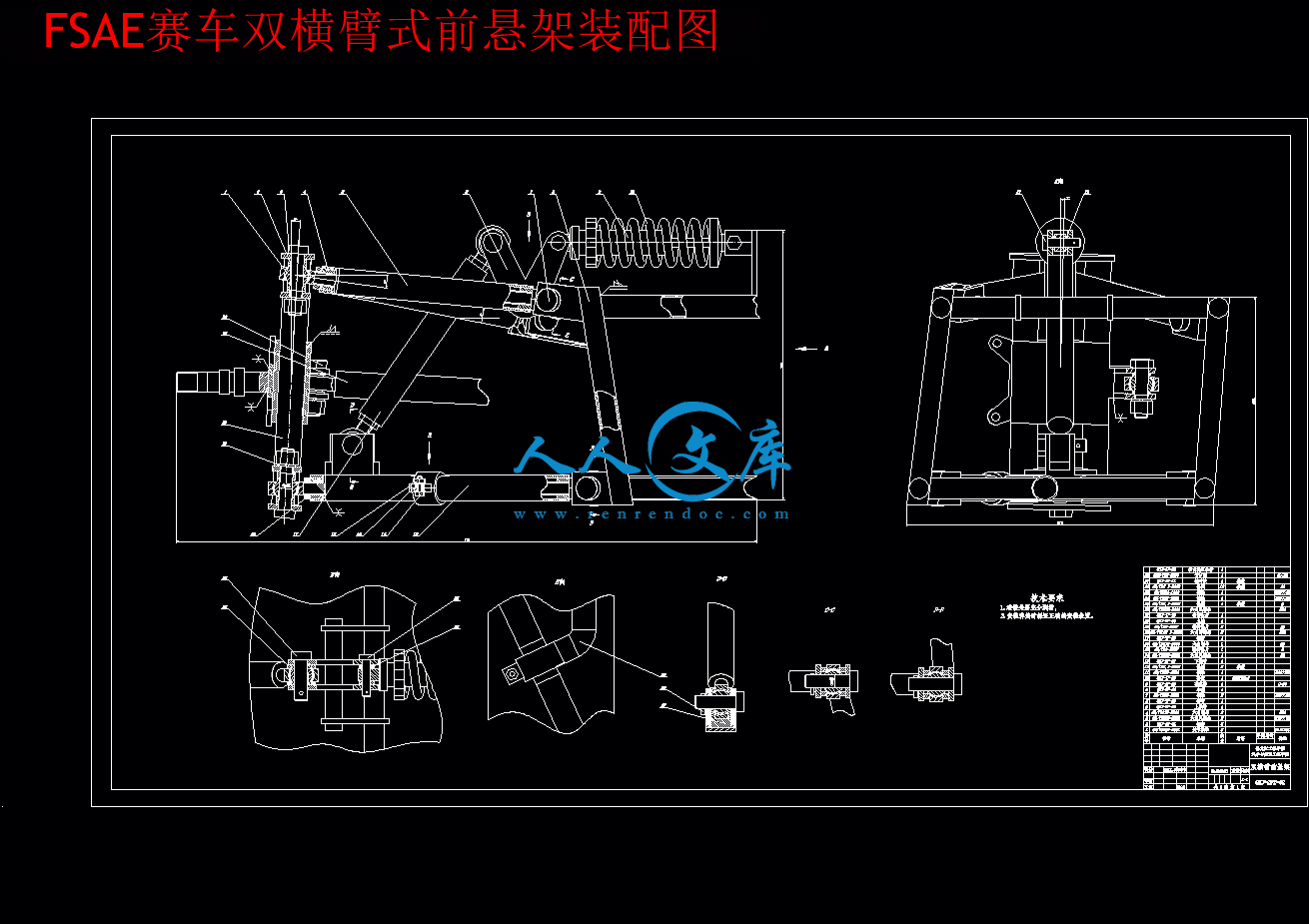
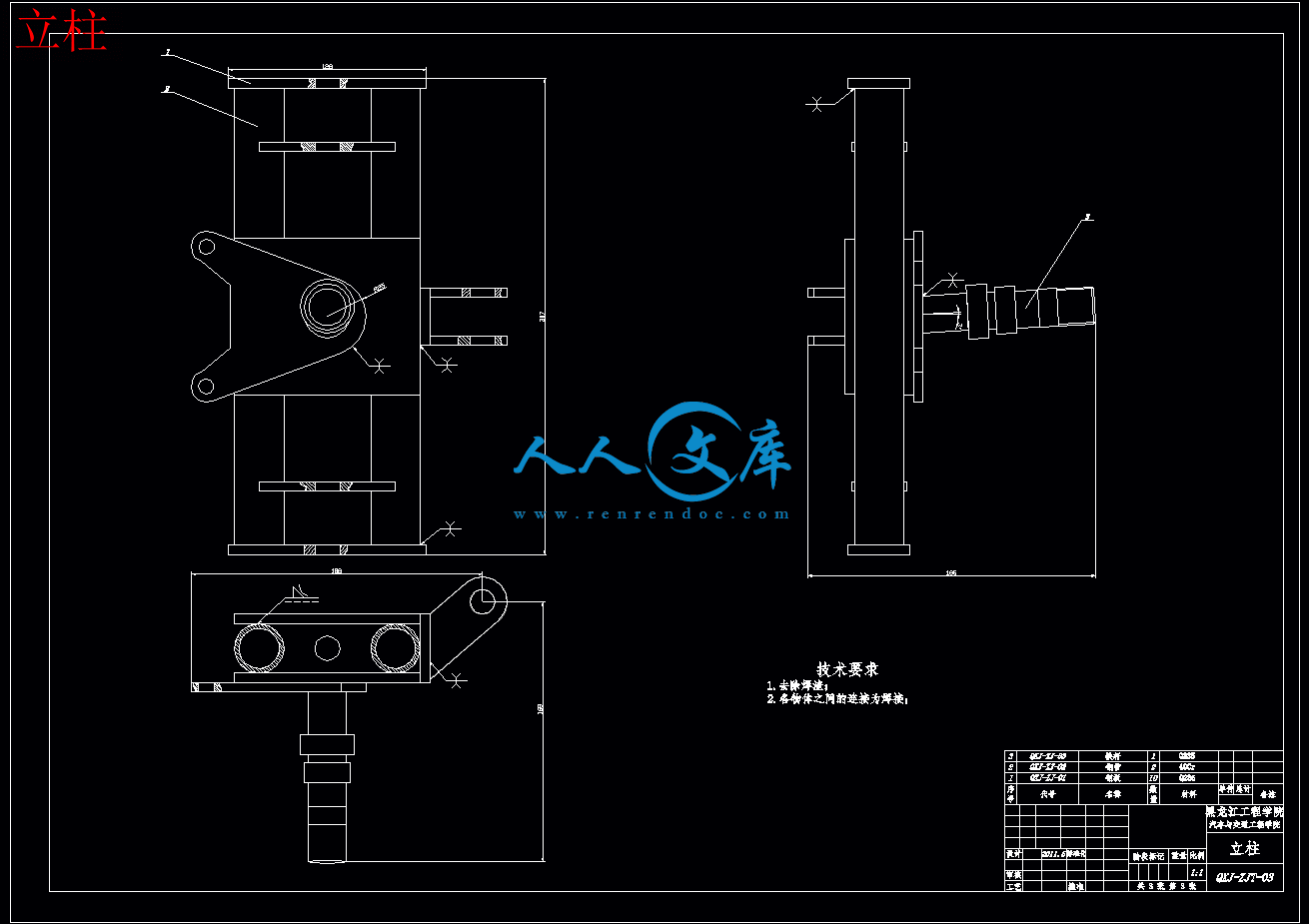
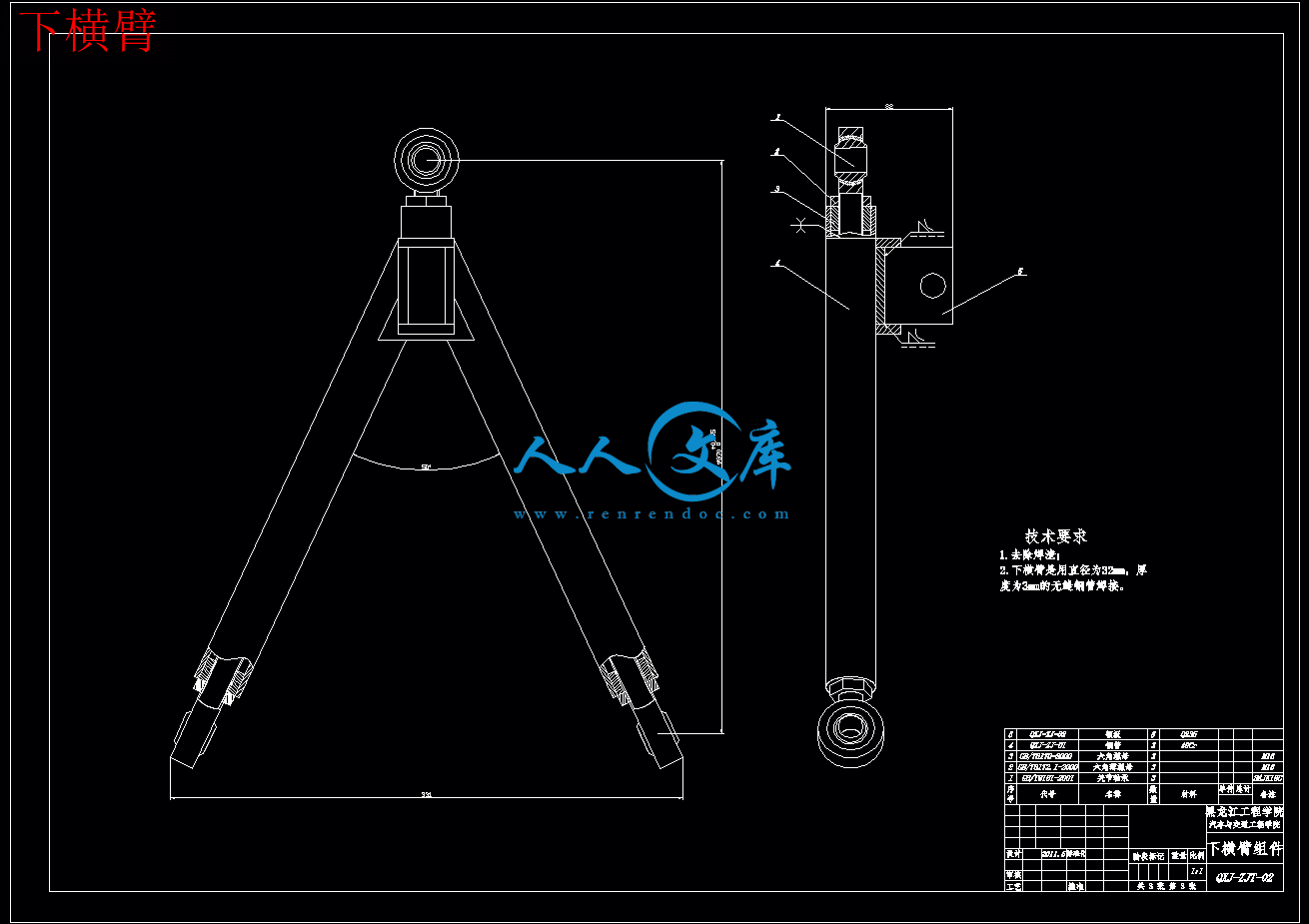