RL7050H0总布置设计
54页 26000字数+说明书+任务书+开题报告+外文翻译+5张CAD图纸【详情如下】
RL7050H0总布置4张.dwg
RL7050H0总布置设计开题报告.doc
RL7050H0总布置设计说明书.doc
RL7050H0车架装配图.dwg
任务书.doc
外文翻译--基本概念的悬架和框架设计.doc
封皮.doc
开题报告封皮.doc
题目审定表.doc
摘 要
RL7050H0总布置设计是在中国大学生方程式汽车大赛的基础上进行的。首先通过充分准备和综合分析,选择一个合理的整车方案,并经过一定的程序将其定下来。方案确定后,进行准确布置和计算,并为各总成下一步开展的工作打好基础、准备条件、提出要求并与各专业组协同完成全部的设计,共同实现整车的总目标。
汽车总布置设计参考同类车型有关数据作为借鉴,重新选定各总成部件,重新布置。提出汽车的长、宽、高、轴距等控制尺寸,轴荷的分布范围以及动力总成、散热器、前后悬架、传动轴与车轮等轮廓尺寸和位置,初步确定新车型的设计硬点。从而保证所设计的汽车不仅在预定的使用条件下具有良好的使用性能、重量轻、寿命长、结构简单、使用方便、效率高、经济性好,制造简单,便于维修。总布置设计在整车开发过程中起到非常重要的作用。
关键词:总布置设计;方程式赛车;总成匹配;车型;控制尺寸
ABSTRACT
RL7050H0 Layout Design Formula cars in the Chinese university students on the basis of competition. First, through the full preparation and comprehensive analysis of vehicle to select a reasonable solution, and after certain procedures to be laid down. Plan was finalized, the exact layout and calculation, and the next step for the assembly to lay the foundation work in preparation for the conditions, request and coordination with the professional group to complete all of the design together to achieve the overall objective of the vehicle.
General layout of car design reference data as a reference on similar models, re-selected parts of the assembly, re-arranged. Proposed vehicle length, width, height, wheelbase and other control dimensions, axle load distribution range and power train, radiator, front and rear suspension, drive shafts and wheels outline size and location of initial hard to determine the design of new models point. Designed to ensure the car is not only the intended conditions of use with good performance, light weight, long life, simple structure, onvenient operation, high efficiency, good economy, manufacturing is simple and easy maintenance. Layout design in the vehicle development process play a very important role.
Key words:The layout design;Formula car;Assembly matching;Models;Control dimensions
目 录
摘要I
AbstractII
第1章 绪论1
1.1 FSAE方程式研究现状1
1.2 FSAE方程式目的、依据和意义2
第2章 总布置设计准备及整车型式选择4
2.1 总布置设计的准备4
2.1.1 市场调研4
2.1.2 样车分析5
2.1.3 制定设计目标6
2.2 整车型式的选择6
2.2.1 发动机的种类和布置型式6
2.2.2 驾驶室的型式8
2.2.3 轮胎的选型10
2.2.4 转向机构型式的选择11
2.2.5 制动器型式的选择13
2.2.6 悬架布置形式16
2.2.7 差速器型式的选择18
2.3 本章小结20
第3章 新车型主要目标参数的初步确定21
3.1 几个主要“目标参数”的确定21
3.2 发动机最大功率及其转速21
3.3 发动机最大扭矩及其转速22
3.4 传动系速比的选择22
3.4.1 最小传动比的选择23
3.4.2 最大传动比的选择24
3.4.3 变速器档位数的选择25
3.5 本章小结25
第4章 尺寸参数与质量参数的初步确定26
4.1 轿车的级别与载荷确定26
4.2 轿车主要参数的确定26
4.2.1 驾驶员单元26
4.2.2 整车外形尺寸的确定29
4.3 本章小结30
第5章 各总成的匹配及总布置图绘制31
5.1 各相关总成的匹配31
5.1.1 车身总布置设计31
5.1.2 发动机总布置设计31
5.1.3 转向节、车轮总成与前制动器总成的布置设计31
5.2 整车总布置图绘制32
5.2.1 整车布置的基准线32
5.2.2 总布置图绘制的基本原则33
5.3 本章小结33
第6章 主要总成的布置及其硬点概述34
6.1 各总成的布置34
6.1.1 发动机及传动系的布置34
6.1.2 驾驶室及悬架的布置35
6.1.3 车架总成外形及转向系的布置36
6.1.4 制动系及进、排气系统的布置36
6.2主要总成硬点概述37
6.2.1 整车设计基准37
6.2.2 总体设计方案及主要硬点37
6.3 本章小结41
第7章 运动校核42
7.1 轮胎运动校核42
7.2 转向传动装置与悬架共同工作校核42
7.3 制动力匹配校核42
7.3.1 制动力匹配基本理论公式42
7.3.2 RL7050H0赛车制动力匹配校核43
7.4 本章小结45
结论46
参考文献47
致谢49
第3章 新车型主要目标参数的初步确定
3.1 几个主要“目标参数”的确定
2010年第一届中国FSAE大赛中,部分车队赛参数:
北京理工大学参赛赛车,最高车速可达135km/h,整车整备质量 208Kg;
哈尔滨工业大学参赛赛车,最高车速可达160km/h,整车整备质量 265Kg。
根据以上参数初步选定RL7050H0最高车速为140km/h,整车整备质量210Kg。
一、设计(论文)目的、意义
设计的小型汽车为一种乘用车,亦可易于比赛和娱乐休闲。
本课题的选择充分考虑了研究课题对汽车车辆工程专业学生学习和工作的指导作用,对本课题的研究能够使学生了解专用汽车改装设计方法,通过本课题的研究学生可以完成理论课程的实践总结,获得一定的工程设计工作方法。
二、设计(论文)内容、技术要求(研究方法)
进行一种微型乘用车的总体设计;面向单件生产;
设计内容包括:整车总体参数的确定,总体方案的选择与分析,主要总成的计算选择和步骤,运动校核分析,整车性能的分析。
要求:
(1) 技术指标满足“FSAE”要求;
(2) 不进行总成部件的详细设计;
(3) 未详述指标和要求按“汽车设计”。
1.1 FSAE方程式研究现状
近年来,汽车技术突飞猛进,方程式赛车也逐步被大多数人所了解,Formula SAE,是由各国SAE,即汽车工程师协会举办的面向在读或毕业7个月以内的本科生或研究生举办的一项学生方程式赛车比赛,要求在一年的时间内制造出一辆在加速、刹车、操控性方面有优异的表现并且足够稳定耐久,能够成功完成规则中列举的所有项目业余休闲赛车。自1981年创办以来,FSAE已发展成为每年由7个国家(美国、英国、澳大利亚、日本、意大利、德国及巴西)举办的9场赛事所组成,并有数百支来自全球顶级高校的车队参与的青年工程师盛会。
SAE方程式(Formula SAE)系列赛源于1978年。第一次比赛于1979年在美国波斯顿举行,13支队伍中有11支完赛。当时的规则是制作一台5马力的木制赛车。SAE方程式(Formula SAE)系列赛将挑战本科生、研究生团队构思、设计与制造小型具有越野性能的方程式赛车的能力。为给车队最大的设计弹性和自我表达创意和想象力的空间,在整车设计方面将会限制很少。赛前车队通常用8至12个月组的时间设计、建造、测试和准备赛车。在与来自世界各地的大学代表队的比较中,赛事给了车队证明和展示其创造力和工程技术能力的机会。
2009年中国国产汽车产销分别为1379.10万辆和1364.48万辆,首次成为世界汽车产销第一大国。汽车从中国人眼中的奢侈品到代步工具,到跃居世界汽车产销量第一的头把交椅,中国只用了短短十年时间。回顾十年来中国汽车工业的突飞猛进,一浪高过一浪的市场消费力,驱使中国一跃成为全球最大的汽车消费大国,而非真正意义上的汽车产业强国。中国汽车工业一直是在借鉴和应用,国外汽车一百多年来成熟的技术和制造工艺一路走来,而缺乏自主创新研发新技术的能力和人才培育。
中国大学生方程式汽车大赛(以下简称"FSAE")是中国汽车工程学会及其合作会员单位,在学习和总结美、日、德等国家相关经验的基础上,结合中国国情,精心打造的一项全新赛事。我国从2006年起开始组建FSAE车队。湖南大学、上海交通大学、厦门理工大学与同济大学自2007年至2009年共参加了在美国和日本举办的4场FSAE赛事,获得了多个单项奖及新秀奖。为搭建国内优秀汽车人才的选拔平台,培养和提高汽车专业学生的综合素质,2010年第一届中国FSAE由中国汽车工程学会、中国二十所大学汽车院系、国内领先的汽车传媒集团——易车(BITAUTO)联合发起举办。中国FSAE秉持“中国创造擎动未来”的远大理想,立足于中国汽车工程教育和汽车产业的现实基础,吸收借鉴其他国家FSAE赛事的成功经验,打造一个新型的培养中国未来汽车产业领导者和工程师的交流盛会,并成为与国际青年汽车工程师交流的平台。中国FSAE致力于为国内优秀汽车人才的培养和选拔搭建公共平台,FSAE要求各参赛队按照赛事规则和赛车制造标准,自行设计和制造方程式类型的小型单人座休闲赛车,并携该车参加全部或部分赛事环节。比赛过程中,参赛队不仅要阐述设计理念,还要由评审裁判对该车进行若干项性能测试项目,通过全方位考核,提高学生们的设计、制造、成本控制、商业营销、沟通与协调等五方面的综合能力,全面提升汽车专业学生的综合素质,为中国汽车产业的发展进行长期的人才积蓄,促进中国汽车工业从“制造大国”向“产业强国”的战略方向迈进。
1.2 FSAE方程式目的、依据和意义
汽车总布置设计是新车型开发的第一道工序,而新车型总体方案的确定是总布置设计的第一步。首先通过充分准备和综合分析,选择一个合理的整车方案,并经过一定的程序将其定下来。方案确定后,进行准确布置和计算,并为各总成下一步开展的工作打好基础、准备条件、提出要求并与各专业组协同完成全部的设计,共同实现整车的总目标。一种新车型的投产,除产品开发过程外,还要做大量的生产准备工作,如投入资金设备厂房、人员及制定一整套相关工艺等。这些都是为了保证整车能够稳定的大量的投入生产,并确保其整车性能和质量能被客户接受,所以整车总体方案和全部设计内容,也直接决定着工厂的投入。因此,总布置工作——方案选择、布置、和计算,都是非常重要的,而且是不可缺少的。做好整车设计工作,必须做好以下两点:第一、要能准确地分析市场形势、了解客户的心理状态、车辆使用特点,熟悉工厂的生产条件,以便真正确定出合理的整车方案;第二、要有独立工作的能力。因为方案确定后,实现该方案的所有布置、计算及整车的开发工作,基本上是由一个人来完成,所以要求设计者工作不应该有任何失误,否则会造成反工和浪费,甚至失掉抢占市场的机会。因此要求设计者必须具有严谨、认真、细致、负责的精神,在整个开发过程中能协调和解决各方面问题和矛盾,使设计产品质量达到设计要求。总布置工作虽然以完成全部图纸及技术文件资料来标志着阶段性的结束,但还应该进行整车装配图的校核工作,即利用已完成的全部图纸或三维数模进行全面的细致的整车装置的图面及运动校核,及时发现问题、解决问题,使设计中存在的问题消除在试制和试装第2章 总布置设计准备及整车型式选择
2.1 总布置设计的准备
2.1.1 市场调研
市场调研是制定商品规划的前提和基础,企业为了获取对外部环境的认识,需要设置专门机构,不断地进行认真、细致和规范的市场调查和预测。
调研工作可以分为市场普查和专项调查。
市场普查:可参与每年进行的市场情况调查,包括国内外制造厂家的产品开发生产销售国家政策地方规定、社会车辆运转情况统计、营运费用、管理维修、车辆性能、可靠性、寿命及备件供应等,从而掌握国内外市场情况、变化规律、发展趋势、用户的使用和需求状况,及时发现市场需求和预测未来。
专项调查:参加为开发某车型而专门进行的市场调查,明确调查目标,细化调研提纲,对整车总成性能参数必须有初步的设想后,再对使用者和使用现场逐项进行的了解、找出差异,特别重点调研有关技术难点——性能要求、结构处理、特殊用途或要求等。
调研的方法主要是通过听问看和测试手段,达到预期目的,通过研究思考达到完善和创新,形成一个比较完整的方案。
中国FSAE赛车总体设计要求:
1.赛车构造
赛车必须是裸露式车轮和敞开式驾驶舱(方程式车型),以及四个车轮不能在一条直线上。
2.车身
从车的前端到主防滚架或者防火墙的这段空间里,除了驾驶舱必须的开口,车体上不允许有其他的开口。允许在前悬架处有微小的开口。
3.轴距
赛车必须有至少1525mm(60英寸)的轴距。轴距是指在车轮指向正前方时同一侧两车轮与地面的接触点之间的距离。
4.轮距
赛车较小的轮距(前轮或后轮)必须不小于较大轮距的75%。
5.可视性
检查表格上所有的条目必须在不使用工具,比如内窥镜或是镜子的情况下清楚地呈现给技术检察官看。呈示时可以拆卸车身外板或提供可拆卸的可见套件。 汽车常用的轮胎有普通斜交胎和普通子午线胎。普通斜交胎的胎体帘线层较多,胎侧厚,使用中不易刺破,侧向刚度大,但是缓冲性能差。而子午线胎的帘布层呈子午线排列,是帘布线的强度得到充分的利用,缓冲层也较多,加强了胎冠,所以提高了轮胎的缓冲性能、附着性能和使用寿命,滚动阻力比普通斜交胎要小,因而提高了整车的经济性。但是制造成本较高,由于胎侧较薄,侧向刚度小,太侧易被刺破。但是其优点较明显,相对斜交轮胎,子午线轮胎具备以下特点 : 良好的操纵稳定性能、安全的转弯性能 、良好的耐磨性能、生热少、滚动阻力低,节省燃油费用、牵引能力强,打滑少、高速行驶时的乘车舒适感好。
2010中国FSAE攒足轮胎相关参数见表2.1,赛事规定赛车可装备如下两套轮胎:
表2. 1 2010中国FSAE赞助轮胎的相关参数
规格180/530R13轮胎接地面宽(mm?inch)185?7.3
标准轮辋内距8.0轮胎半径(mm)244
轮胎胎面宽(mm?inch)223?8.8轮胎周长1626
轮胎外径(mm?inch)533?21.0轮辋内距7.5-8.5
干胎——在检查时安装在赛车上的轮胎定义为干胎。干胎尺寸任意,型号任意。他们可以是光头胎,也可是有纹的
雨胎——雨胎可以是如下规定的任何型号和尺寸的有花纹和沟槽的样式:
(1)花纹和沟槽的图案必须是由轮胎厂商塑造成型的,任何被刻制的花纹沟槽必须有文件证明它是符合比赛的相关规定的。
(2)沟槽最浅为2.4mm(3/32英寸)。
2.2.4 转向机构型式的选择
1.齿轮齿条式转向器
中小型轿车以及前轴轴荷小于1.2t的客车、货车,多采用该种型式,如图2.5所示。齿轮齿条式转向器的传动副为齿轮与齿条。转向轴带动小齿轮旋转时,齿条便做直线运动。有时,靠齿条来直接带动横拉杆,就可使转向轮转向。通常均布置在前轮轴线之后。转向传动副的主动件是一斜齿圆柱小齿轮,它和装在外壳中的从动件——齿条相啮合,外壳固定在车身或车架上。齿条利用两个球接头直接和两根分开的左、右横拉杆相联。横拉杆再经球接头与梯形臂相接。齿轮齿条式转向器是依靠齿条背部靠近主动小齿轮处装置的可调节压力的弹簧来消除齿轮齿条传动副的齿间间隙的。为了转向轻便,主动小齿轮的直径应尽量小。通常,这类转向器的齿轮模数多在2~3mm范围内,压力角为20。,主动小齿轮有5~8个齿,螺旋角为9°~15°。根据小齿轮螺旋角和齿条倾斜角的大小和方向的不同,可以构成不同的传动方案。
齿轮齿条式液压助力转向器,是相对于机械转向器而言的,其增加了转向油泵、转向油壶、转向油管、转向阀、转向油缸等部件,以期达到改善驾驶员手感,增加转向助力的目的的转向装置。
齿轮齿条式转向器结构简单、紧凑;布置方便;制造容易,成本低廉;壳体采用铝合金或镁合金压铸而成,转向器的质量较小;转向灵敏,传动效率高达90%;齿轮与齿条间因磨损出现间隙以后,利用装在齿条背部、靠近主动小齿轮处的压紧力可以调节的弹簧,能自动消除齿间间隙,能提高转向系统的刚度,防治工作时产生冲击和噪声;占用体积小,便于布置,制造容易。但转向传动比较小,(一般不大于15),且齿条沿其长度方向磨损不均匀;逆效率高(60% ~70%),不易控制。
6.2.1 整车设计基准
整车绝对坐标系采用右手坐标系,它是总布置设计和详细设计中的基准线。绝对坐标系的定义如下:高度方向,上正下负;宽度方向,取汽车的纵向对称中心线为 Y 零线,左负右正;长度方向,取通过汽车前轮中心的垂线为 X 零线,前负后正。
6.2.2 总体设计方案及主要硬点
1.整车总体技术硬点
以整车方案为指导,总体技术硬点如表6.1所示:
表6.1 总体技术硬点
基本形式裸露式车轮和敞开式驾驶舱(方程式车型)
驱动形式动力总成后置后轮驱动
外形尺寸长mm2968
宽mm1468
高mm1497
轴距mm1940
轮距前轮距mm1245
后轮距mm1180
前悬mm742.6
后悬mm285.4
质量参数整车整备质量Kg210
乘载质量Kg75
空载前后轴荷Kg前轴荷89.04(42.4%)后轴荷120.96(57.6%)
满载前后轴荷Kg前轴荷130.39(45.8%)后轴荷154.61(54.2%)
通过性数据接近角(满载)(°)20
离去角(满载)(°)88
最小离地间隙mm109
最小转弯半径m4.425
2.动力传动系统设计硬点
动力总成参数如表6.2所示:
表6.2 动力总成参数
基本型式横置中置后驱发动机排量(L)0.493
发动机CF188发动机最大功率(kw/rpm)24/6500
变速器CVT发动机最大扭矩(N.m/rpm)31.16/5500
动力传动系统主要布置硬点如表6.3所示:
表6.3 动力传动系统主要布置硬点
动力总成BHC点坐标X:1377.3;Y:0;Z:190.0
发动机缸体对称中心面Y:65,平行于Y平面
差速器中心点坐标X:1959.6;Y:88.2;Z:106.1
发动机悬置中心点坐标前X:1212.9;Y:49.0;Z:494.9
后X:1553.8;Y:56.0;Z:356.9
左X:1345.3;Y:65.0;Z:50.0
右X:1601.8;Y:65.0;Z:37.0
发动机输出轴中心左传动轴X:1377.3;Y:-54.0;Z:19.0.0
右传动轴X:1377.3;Y:196.0;Z:190.0
后左半轴理论长度mm667.5
后右半轴理论长度mm491.2
油底壳最小离地间隙mm146.5
3.底盘系统布置方案及主要硬点
(1)悬架车轮系统
悬架车轮系统的主要布置硬点如表6.4所示:
表6.4 悬架车轮系统的主要布置硬点
前悬架上支点X:428.0;Y:±194.2;
Z:530.0前轮总前束0.2o±30′
后悬架上支点X:1632.5;Y:±171.4;
±Z:563.0主销内倾12.6o±30′
轮胎类型子午线轮胎主销后倾2.5o±30′
轮胎规格180/530R13后轮外倾-0.6o±30′
轮辋规格13×8J后轮总前束0.2o±30′
前轮外倾-0.8o±30′
前后悬架车轮系统:均采用空间多连杆、圆柱螺旋弹簧,双向作用筒式减振器结构,独立悬架。前车轮为非驱动轮,后车轮为驱动轮。
(2)转向系统
转向系统主要布置硬点如表6.5所示:
表6.5 转向系统主要布置硬点
转向器断开点X:170.3;Y:-157.4;Z:213.1
转向传动装置方向盘外径260mm
内外转角36.4°/26°
传动比44.6
转向管柱上下角度65o/68o/60o
方向管柱传动轴长度302.5mm
转向器行程140±1mm(厂家值)
管柱上顶点X:534.3;Y:0;Z:514.8
(3)制动系统
行车制动系统采用液压助力结构。前后制动器均为强制通风式盘式制动器。制动管路为 X 型双回路布置。
驻车制动系统为拉索式手动结构,操纵手柄放置在座椅的右侧。
制动系统主要布置硬点如表6.6所示:
表6.6 制动系统主要布置硬点
制动总泵安装面中心X:-200.0;Y:72.5;Z:170.0
前后轮缸数量2,2
前后轮缸直径(mm)57.15
前后制动半径(mm)92.5
制动踏板比5
驻车制动转动中心X:754.4;Y:239.7;Z:239.8
驻车制动手柄最大角度45°
6.3 本章小结
本章主要是对总布置中的各总成部件,如发动机、传动系、悬架、转向系、制动系等进行详细的布置,以保证新车型运转平稳,不影响使用性能的发挥。简述了各总成的布置和各附件的硬点,主要包括确定车身、底盘与零部件相互关系的基准点、线、面及控制结构,为整车的详细设计提供依据和指导。
参考文献
[1]勾治践,鲍明全.基于ADAMS/VIEW的双横臂式独立悬架机构运动学分析[J].机械设计与制造,2007, (8) _3 .
[2]刘江南,韩旭,陈羽等.双横臂式前独立悬架的改进遗传算法优化[J].中国机械工程, 2007, 18 (22) _4 .
[3]陈俊.基于双横臂独立悬架对轿车转向机构优化设计[D].合肥工业大学, 2007.
[4]勾治践,鲍明全.基于ADAMS/VIEW的双横臂式独立悬架转向梯形机构断开点位置的仿真分析[J].机械设计,2007, 24 (3) _3 .
[5]鲁春艳.基于UG的齿轮齿条式转向器的虚拟设计与分析[J].苏州市职业大学学报, 2009, 20 (1) _4 .
[6]张帮琴.齿轮齿条式机械转向器异响优化设计[J].汽车零部件,2009, (9) _3 .
[7]刘冰.齿轮齿条转向器的建模及分析[J].上海工程技术大学学报,2006, 20 (1) _4 .
[8]周祥基.汽车转向传动机构的类型分析与优化设计[D].东南大学,2005.
[9]阳鹏.齿轮齿条式转向器综合试验台测控系统的设计与开发[J].装备制造技术, 2009, (8) _3 .
[10]张松青,赵晓运.齿轮齿条传动机构参数的优化研究[J].煤矿机械,2007, 28 (12) _3 .
[11]方家.某矿用越野车总体设计[D].南京理工大学,2009.
[12]聂创业.基于多体整车模型的驾驶室悬置隔振系统优化设计平台开发[D].武汉理工大学,2007.
[13]曾志强.小型轮式甘蔗收获机总体研究及车架的设计分析[D].广西大学,2007.
[14]苏信杰.混合动力城市客车总体设计与控制策略的研究[D].合肥工业大学,2009.
[15]李乐.四轮独立驱动电动车控制系统的设计[D].武汉理工大学,2010.
[16]吴亚祥.野马混合动力电动汽车总体结构与控制系统方案研究[D].四川大学, 2006.
[17]杨晓明,潘双夏,邱清盈等.面向整车性能的盘式制动器协同仿真[J].农业机械学报,2007, 38 (2) _4 .
[18]韩智慧.某商用车驾驶室空气悬置及整车性能分析[D].西南交通大学,2010.
[19]高传宝,宋艳冗,李英等.GT-Power模型分析在整车排气噪声性能方面的应用[J].汽车技术,2009, (12) _3 .
[20]陈晓新.基于刚柔耦合的整车动力学建模与悬架隔振性能分析[D].合肥工业大学,2010.
[21]柳杨.悬架的KC特性对整车操纵稳定性影响的初步研究[J].机械设计与制造, 2010, (9) .
[22]钱德猛,程立望,朱凌云等.一种商务车的整车噪声性能试验分析[J].现代制造工程,2007,(4) _4 .
[23]郭伟.汽车前悬架的优化设计及整车稳态转向特性的研究[D].西南交通大学,2008.
[24]赵海宾.汽车整车性能测试分析系统的研究与开发[D].河北工业大学,2007.
[25]江沿.轿车后悬架运动学与整车操稳性仿真[D].南京信息工程大学,2010.
[26]许文娟.汽车制动性测试分析系统的研究[D].河北工业大学,2008.
[27]陈宗好.汽车动力传动系分析、优化匹配的研究及软件开发[D].合肥工业大学,2006.
[28]方英武,张永芳,张广鹏等.车架结构动力学特性边界元法解析[J].交通运输工程学报, 2005, 5 (4) _4 .
[29]徐晓娜.微型客车车身有限元分析及车架结构优化[D].南京航空航天大学,2009.
[30]石磊.某特种车辆一体化复合车架结构分析研究[D].南京理工大学,2008.
[31]胡爱华,李左龙,黄彦等.特种越野车底盘车架结构基本力学性能仿真计算[A].中国宇航学会发射工程与地面设备专业委员会学术会议论文集[C]. 2003 .
[32]朱喆.越野汽车双横臂式悬架系统平顺性计算及优化[J].沈阳理工大学学报,2007, 26 (5) _4 .
[33]成大先.机械设计手册[M].北京:化学工业出版社,2004.
[34]Chieh Chen.Lateral Control of Commercial Heavy Vehicles.Vehicle System Dynamics.2002.3.
[35]Richard Swift.Flexible Body Contact for Modeling Squeal in Braking Systems.MDI North American IJsers Conference.2002.

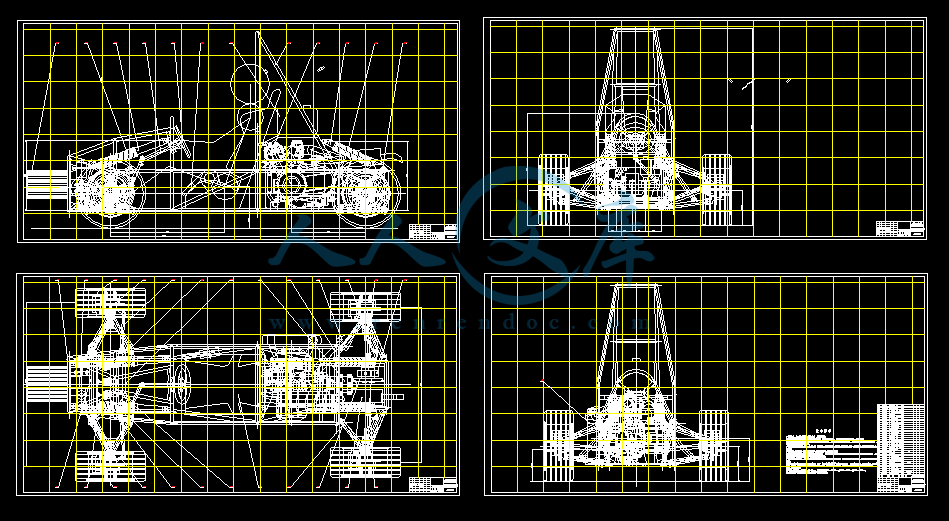