【温馨提示】 购买原稿文件请充值后自助下载。
[全部文件] 那张截图中的文件为本资料所有内容,下载后即可获得。
预览截图请勿抄袭,原稿文件完整清晰,无水印,可编辑。
有疑问可以咨询QQ:414951605或1304139763
第1章 绪论1
1.1 选题背景,研究目的及意义1
1.2 国内外研究现状1
1.2.1 大梁校正仪的发展历史1
1.2.2 国内外研究状况及结果2
1.3 研究内容及研究方法2
1.3.1 研究内容2
1.3.2 研究方法3
第2章 校正仪的整体结构设计4
2.1 简述框架式汽车大梁校正仪工作原理4
2.2 举升机构主要结构确定4
2.2.1 举升机构整体结构形式及基本组成4
2.2.2 举升机构各零部件安装位置及润滑5
2.3 举升平台及定位夹具主要结构确定5
2.3.1 举升平台整体结构形式及基本组成5
2.3.2 定位夹具整体结构形式及基本组成6
2.4 拉塔的主要结构确定6
2.4.1 拉塔横梁处整体结构形式及基本组成6
2.4.2 拉塔柱的结构形式及基本组成7
2.5 其它附件7
2.6 确定框架式大梁校正仪各结构尺寸及材料7
2.6.1 建立待修汽车基本参数模型8
2.6.2 校正仪底部结构部分主要尺寸及材料的确定8
2.6.3 校正仪中间结构部分尺寸及材料的确定8
2.6.4 校正仪上部平台结构尺寸及材料的确定9
2.6.5 定位夹具的尺寸及材料的确定11
2.6.6 拉塔组件的尺寸及材料的确定12
2.6.7 方凳及斜坡板凳的尺寸确定13
2.7 设备各部件质量的估算及设计举升质量13
2.7.1 估算拉塔组件的质量14
2.7.2 估算平台上设备的质量14
2.7.3 估算平台中部的质量14
2.7.4 估算底板处的质量15
2.7.5 实际设计举升质量15
2.8 本章小结15
第3章 校正仪的力学分析及校核16
3.1 双铰接剪刀式举升机构的力学模型16
3.1.1 举升机构力学模型建立与分析16
3.1.2 举升机构主要关系参数的确定17
3.2 液压机构力的分析与计算17
3.2.1 确定载荷与液压缸推力的关系17
3.2.2 计算液压缸的推力18
3.3 举升机构的力学分析与计算19
3.3.1 举升机最低状态时,各臂受力情况19
3.3.2 举升机举升到最高位置时,各臂受力情况20
3.4 定位夹具及拉塔的力学分析与计算22
3.4.1 定位夹具的受力分析22
3.4.2 拉塔的受力分析22
3.5 主要零部件的强度校核23
3.5.1 举升臂AOB的强度校核23
3.5.2 举升臂COD的强度校核25
3.5.3 液压缸上端支承轴的强度校核27
3.5.4 连接举升臂销轴的强度校核27
3.5.5 平台内横梁的强度校核28
3.5.6 定位夹具的强度校核29
3.5.7 定位夹具支撑横梁的强度校核30
3.5.8 拉塔的强度校核31
3.5.9 拉塔处液压缸支撑销轴的强度校核32
3.6 本章小结33
第4章 校正仪液压系统的选择与计算34
4.1 液压系统的选择34
4.1.1液压系统的介绍34
4.1.2液压系统的选型34
4.2 液压系统的计算35
4.2.1 举升处液压缸行程的计算35
4.2.2 举升处液压系统工作压力的计算36
4.2.3 关于拉塔处液压系统的相关选择36
4.3 本章小结36
第5章 校正仪三维建模与整机装配37
5.1 CATIA软件简介37
5.2 利用CATIA进行三维建模38
5.2.1 底坐板的建立38
5.2.2 举升臂AOB的建立39
5.2.3 液压缸支承轴的建立39
5.2.4 上平台的建立40
5.2.5 夹具的建立40
5.2.6 拉塔柱的建立42
5.3 整机装配42
5.3.1 CATIA装配功能概述43
5.3.2 装配的CATIA零件图43
5.3.3 CATIA整机装配图及爆炸图48
5.4 本章小结50
第6章 校正仪主要零部件有限元分析51
6.1 ANSYS有限元分析软件介绍51
6.2 ANSYS与CATIA接口的建立51
6.3利用ANSYS对主要零部件进行分析52
6.3.1定位夹具卡钳的有限元分析52
6.3.2液压缸支撑轴的有限元分析56
6.3.3举升臂的有限元分析59
6.3.4拉塔柱的有限元分析62
6.4 本章小结65
结论66
参考文献67
致谢68
附录A69
附录B72
附录C73
附录D74
绪 论
选择背景、研究目的及意义
随着汽车市场的不断发展与壮大,与之相协调的汽车维修行业也迅速发展起来。目前在汽车事故中对大梁及钣金的修复十分常见。而随着对售后服务的要求的不断提升,也为了更好的发展企业,各维修厂家已经开始了激烈的服务竞争。汽车大梁校正仪是在因交通事故碰撞所致车身损坏,以及大梁变形等的技术数据恢复中重要的维修设备。在以往的事故后维修时,很多企业选择了更换零部件,但是这样往往会增加客户的损失及保险公司的负担。汽车大梁校正仪的出现避免了高额的更换费用,这样既减少了顾客的损失,也可促进制造设备企业市场的发展。利用大梁校正仪专业设备方可保证对汽车大梁的维修的质量水平。然而对于在维修中为了保证汽车安全的定位,方便的使用,高维修水平等众多关键要素,必须设计质量及安全可靠的设备。因此,为了满足维修企业对占地空间的要求及保证维修质量。对框架式汽车大梁校正仪进行深入研发将对我国在这一领域发展有实质性的意义。本课题基于计算机仿真平台,应用CAD/CAE领域比较领先的设计软件AutoCAD进行二维草图绘制,使用了当前先进的三维设计软件CATIA进行三维建模及整机装配,在产品投入生产之前运用ANSYS软件进行质量分析,可及时发现并更改设计中的缺陷,完善设计方案,减少产品开发周期,提高研发的质量和效率,为此设备的生产实际提供一些有价值的理论支持。
1.2 国内外研究现状
1.2.1 大梁校正仪的发展历史
汽车大梁校正仪的发展已经有了将近30年的历史。它的出现主要是基于剪式汽车举升机的框架的改装。由于举升机历史较长,技术较成熟,所以在80年代期间,美国及欧洲就率先通过对剪式举升机的改造而研发出框架式大梁校正仪。九十年代欧洲通过出口到中国市场逐渐把它的产品推向亚洲地区。90年代中期,在我国山东地区逐渐出现了很多此类设备制造企业,目前在国内市场发展史已经是标新立异。经过几十年的发展,剪式举升机及一些定位夹具已经更新了很多代,框架式汽车大梁校正仪至今也经历了许多变化与改进。目前欧美已经将其产品出口至全世界,我国山东地区少数企业也已经打破传统局面,将设备出口至芬兰等北欧国家。而框架式大梁校正仪使用方便,占地空间较小,也受到很多实力雄厚的特约维修站的欢迎。
1.2.2 国内外研究状况及成果
框架式汽车大梁校正仪目前是市场上主流的产品之一。欧洲及美国目前在这方面的技术处于领先地位,并且不断的主导市场的发展方向。所以市面上此产品主要由欧洲及美国设计制造,他们已经在精确恢复技术方面取得了很大成就。在这其中美式大梁校正仪凭借价格优势及外观而市场占有率较高,但随着维修质量要求的提高,夹具设备的不断升级,欧式凭借其功能的强大,操作灵活及占地面积小等优势逐渐在市场上走俏。但由于进口设备的高价格及售后服务不方便等因素,仍然只是少数大型维修企业及汽车4S店会购置进口设备。90年代末,在我国山东地区出现了一些制造汽车大梁校正仪的中小型企业。由于起步较晚,所以目前多数企业是借鉴国外的先进技术。随着时间的推移,目前市场上自主的品牌已经逐渐成熟起来,并且在不断地扩大销售网络于全国,基本在各大省会城市均有销售代理,且价格范围较广,多数在3-6万元左右。但质量水平,技术创新性等方面与进口品牌还有一定的差距,而且产品类型主要以平台式为主。但是自主品牌却已经出口至欧洲及非洲。由此可见目前中国汽车维修设备市场对框架式汽车大梁校正仪的需求将会不断上升。目前框架式汽车大梁校正仪主要有以下功能特点:(1)能实现单拉臂可多角度拉伸,同时能对事故车进行360°遥控拉伸;(2)定位系统是模块式,能具有高通用性;(3)定位夹具高度可调,能方便上下车辆的准确定位;(4)配备举升平台和上车导板,移动支架,电脑底盘测量系统等附属件。随着市场的发展,提高汽车大梁校正仪的高水平技术与整体制造水平是在市场上获得良好口碑的关键要素。
1.3 研究内容及研究方法
1.3.1 研究内容
(1)分析框架式汽车大梁校正仪的结构形式及工作原理,根据以下参数:最大举升高度1060mm,工作台长度 2300mm,工作台高度230-1060mm,工作台宽度950mm,降到最低点为230mm,拉塔工作范围360度,液压系统最大工作压力16Mpa,气源压力要求0.8Mpa, 拉塔牵引最大拉力70KN,完成方案设计及质量校核计算。利用AutoCAD完成校正仪的二维总体结构设计,然后CATIA建立三维模型,在将关键零部件模型通过专用模型数据转换接口导入ANSYS软件进行有限元分析,获得校正仪在载荷工况作用下的应力、应变及变形状,然后用CATIA整机虚拟装配。
(2)拟解决的主要问题
1)框架式汽车大梁校正仪总体方案设计;
2)利用AutoCAD完成大梁校正仪二维结构设计;
3)利用CATIA完成大梁校正仪的三维建模;
4)利用ANSYS软件对关键零部件进行有限元分析;
5) CATIA虚拟装配。

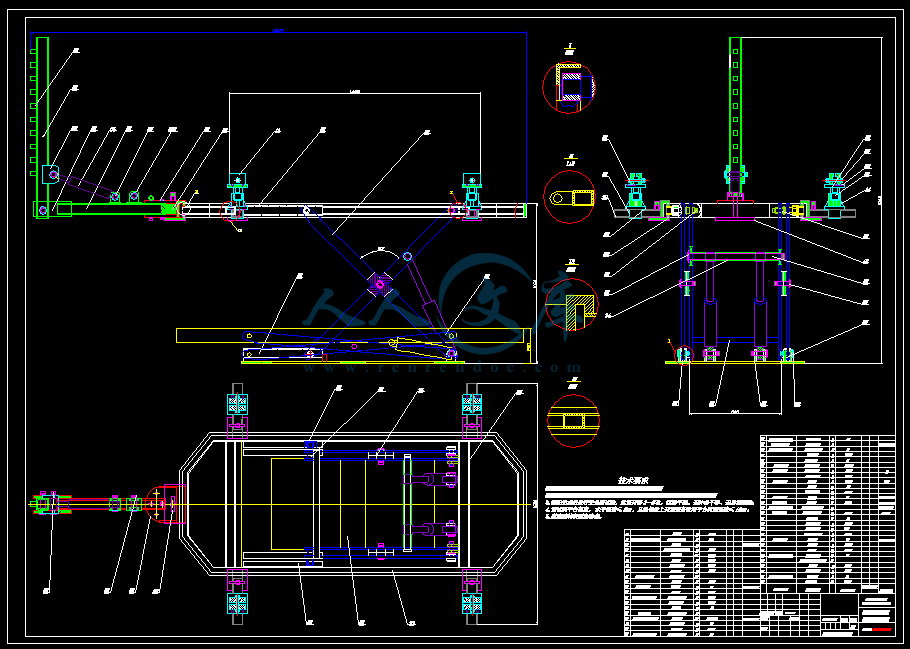







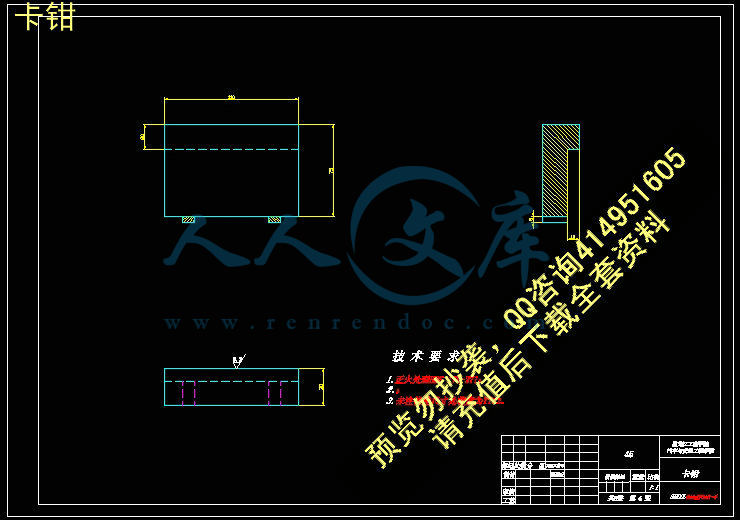


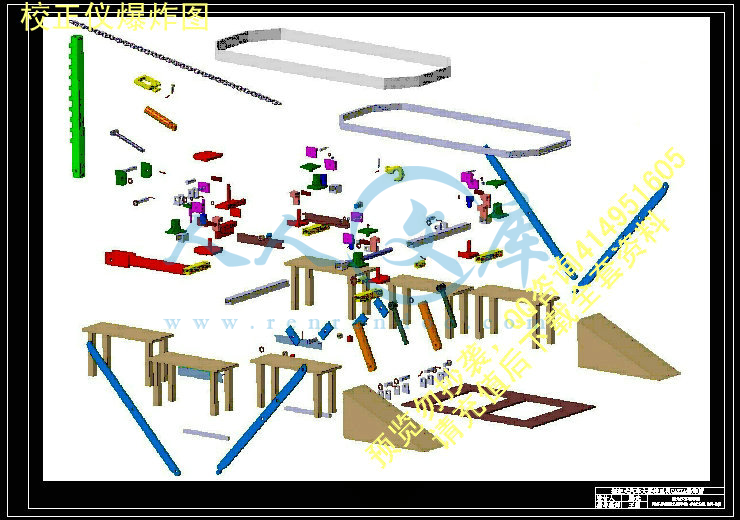