【温馨提示】 购买原稿文件请充值后自助下载。
[全部文件] 那张截图中的文件为本资料所有内容,下载后即可获得。
预览截图请勿抄袭,原稿文件完整清晰,无水印,可编辑。
有疑问可以咨询QQ:414951605或1304139763
目 录
摘要Ⅰ
AbstractⅡ
第1章 绪论1
1.1课题研究的目的意义1
1.2课题的国内外研究现状1
1.3设计的主要内容与技术路线2
第2章 万向传动装置结构方案确定4
2.1设计已知参数4
2.2万向传动的运动和受力分析4
2.2.1单十字轴万向节传动4
2.2.2双十字轴万向节传动6
2.2.3多十字轴万向节传动7
2.3结构方案的确定7
2.3.1万向节与传动轴的结构型式7
2.3.2传动轴管、伸缩花键及中间支承结构方案分析8
2.3.3万向节类型分析10
2.4本章小结14
第3章 万向传动装置设计15
3.1万向节传动的计算载荷15
3.1.1按发动机最大转矩和一档传动比来计算15
3.1.2按驱动轮打滑来计算15
3.2 万向传动轴的计算载荷16
3.2.1初选十字轴万向节尺寸16
3.2.2十字轴万向节设计与校核18
3.3 滚针轴承设计19
3.3.1滚针轴承初选尺寸19
3.3.2滚针轴承的接触应力19
3.4 万向节叉设计和校核20
3.5 传动轴的设计计算21
3.5.1传动轴的临界转速22
3.5.2传动轴长度和内外径确定23
3.5.3传动轴的校核23
3.6 花键轴的设计计算24
3.6.1花键轴初选尺寸24
3.6.2花键轴的校核25
3.7 中间支承的结构分析和设计25
3.8 本章小结28
第4章 万向传动装置的有限元静力学分析29
4.1 基于Pro/ENGINEER软件的三维建模29
4.1.1 Pro/ENGINEER软件简介29
4.1.2利用Pro/E进行三维建模30
4.2基于ANSYS的有限元模型生成31
4.2.1 ANSYS有限元分析软件的简介31
4.2.2 Pro/E与ANSYS接口的创建33
4.2.3基于ANSYS的有限元模型生成35
4.3万向传动装置静载和约束的施加与结果分析36
4.3.1十字轴有限元受力分析36
4.3.2万向节有限元受力分析39
4.3.3中间传动轴有限元受力分析44
4.4本章小结47
第5章 万向传动装置的有限元优化设计48
5.1优化设计概述48
5.2基于有限元的十字轴优化设计49
5.2.1十字轴数学模型建立49
5.2.2十字轴优化结果分析50
5.3万向节叉的结构优化52
5.3.1万向节叉的数学模型建立52
5.3.2万向节叉的优化结果分析53
5.4传动轴管的优化56
5.4.1传动轴管的数学模型建立56
5.4.2传动轴管优化结果分析56
5.5万向传动装置优化后尺寸的确定58
5.6进行整机装配与校核58
5.6.1 Pro/E实体建模后的整体装配图58
5.6.2干涉检查60
5.7本章小结61
结论62
参考文献63
致谢64
附录65
附录A 外文文献原文65
附录B 外文文献中文翻译69
摘 要
万向传动装置是汽车传动系中的重要总成,它直接与变速器和驱动桥相联系,用来实现对传动系的动力传递。课题研究对象是后轮驱动广泛应用的十字轴式万向传动装置,主要零件包括传动轴、万向节、支撑装置等,这些关键零部件的设计对整个万向传动装置性能具有很大的影响。
本文主要是对汽车的十字轴式万向传动装置进行设计。根据车辆使用条件和车辆参数,按照传动系统的设计步骤和要求,主要进行了以下工作:选择相关设计参数主要为:十字轴、万向节、传动轴、中间支承的参数确定,并进行了总成设计主要为:十字轴的设计,万向节的设计、传动轴的设计以及中间支承的设计等。并通过有限元ANSYS软件对设计万向传动装置进行结构分析,根据分析结果对万向传动装置进行改进优化设计并得出合理的设计方案。在传动轴的设计中采用有限元技术研究这些关键零部件的静力学特性,对其结构进行优化设计,可以大大缩短万向传动装置总成开发周期、降低开发费用,提高设计质量,保证其设计的精确性。
关键词:万向传动装置;十字轴;万向节;传动轴;有限元分析;优化设计
ABSTRACT
Universal transmission is important in automobile transmission assembly, which directly linked to transmission and drive axle, used to achieve the transfer of the power transmission system. Research object is widely used in rear-wheel drive transmission cross shaft universal, the main parts including drive shafts, universal joints, support devices, the design of these key components for the universal transmission has a great influence on the performance .
This article mainly is carries on the design to the automobile cross shaft type rotary transmission device. According to vehicles exploitation conditions and vehicles parameter, according to transmission system design procedure and request, Mainly has carried on following work: Mainly has carried on following work choice correlation design variable mainly is: Cross axle, universal joint, drive shaft, middle supporting parameter determination, and has carried on the unit design mainly is: Cross axle design, universal joint design, drive shaft design as well as middle supporting design and so on. And to designs the rotary transmission device through the finite element ANSYS software to carry on the structure analysis, Carries on the improvement design according to the analysis result to the rotary transmission device to obtain the reasonable design proposal. The propeller shaft of the design used in technical research on these crucial component element of statics. in its structural design and optimize can greatly shorten the automobile universal transmission device always into the development cycle and reduce the development costs and improve the quality of design to ensure the accuracy of its design.
Key word: Universal Transmission Device; Cross Axle; Universal Joint; Drive Shaft; Finite Element Analysis; Optimization Design
第1章 绪 论
1.1 课题研究的目的意义
万向传动装置是汽车传动系中的重要总成,它直接与变速器和驱动桥相联系,用来实现对传动系的动力传递。课题研究对象是后轮驱动广泛应用的十字轴式万向传动装置,主要零件包括传动轴、万向节、支撑装置等,这些关键零部件的设计对整个万向传动装置性能具有很大的影响。万向节传动应适应所联两轴的夹角及相对位置在一定范围内的不断变化且能可靠而稳定地传递动力,保证所联两轴能等速旋转,且由于万向节夹角而产生的附加载荷、振动及噪声应在允许范围内,在使用车速范围内不应产生共振现象。此外,万向节传动还要求传动效率高,使用寿命长,结构简单,制造方便,维修容易。传统的分析方法,一般都是首先通过轴传递的最大转矩,计算出轴的最小直径;然后通过计算作用在轴上的载荷、不同断面上的转矩、轴向力和弯矩,利用解析法或图解法确定轴不同位置的支反力,最后利用传统的计算公式进行强度校核,确定安全系数。如果安全系数小于许用安全系数,还要进行疲劳强度计算。此过程计算繁杂,反复性强,而且可靠性差,很可能因为计算误差,造成由于传动轴强度不够而引发的轴裂、轴断事故。因此,研究一种新的准确、快捷的强度分析方法迫在眉睫。ANSYS软件作为一种广泛应用CAE软件,应用有限元法对结构进行静力学、动力学、热力学和电磁学等多种分析。通过ANSYS软件的应用,可以大大缩短轴类零件的设计周期,从而减少设计成本,并有利于多种型号产品的开发。
1.2 课题的国内研究现状
万向传动装置最早出现于1352年,在Strasbourg大教堂时钟机构中的万向节传动轴。1663年Robert Hook万向节诞生,后来被人们叫做虎克万向节,也就是十字轴万向节。紧接着在1683年研制出的双联式虎克万向节,消除了单个虎克万向节传递的不等速性,并于1901用于汽车转向轮。在上世纪初,虎克万向节和传动轴,以及后来的等速万向节和传动轴在机械工程和汽车工业的发展中起到了极其重要的作用。现在,根据在扭转方向上是否有明显的弹性,万向节可分为刚性万向节和挠性万向节。刚性万向节是靠零件的铰链式传递动力,又分为不等速万向节、准等速万向节和等速万向节;挠性万向节是靠弹性零件传递动力的,具有缓冲减震作用[1]。
现在汽车万向传动装置一般是由万向节、传动轴和中间支撑组成。主要用于工作过程中相对位置不断改变的两根轴间传递转矩和旋转运动。伸缩套能自动调节变速器与驱动桥之间距离的变化。万向节是保证变速器输出轴与驱动桥输入轴两轴线夹角的变化,并实现两轴的等角速传动。一般万向节由十字轴、十字轴承、凸缘叉及轴向定位件和橡胶密封件等组成。
在1950年后,传动轴的产量达到数以万计。1984年主要由于汽车工业的增长,生产了三千五百万套虎克万向节传动轴,一亿二千万套等速万向节传动轴,一亿三枢轴式万向节传动轴。在国内,近年来随着我国汽车业的高速发展,带动我国汽车传动轴需求持续大幅增长。2007年中国汽车传动轴的需求已经突破992万根,产值达到45亿。2008年汽车销量达到938万两,而作为汽车零部件的汽车传动轴需求量也接近1900万套,产值达到50亿元。倒2010年我国汽车传动轴总销售额达到87亿之多,因次国内也出现一批传动轴制造的厂家。但产品的性能与国外相比仍有相当大的差距,具体表现在两个方面:绝大多数轿车厂家对等速万向节产品没有制定出相应的技术规范,而国外公司对驱动轴和传动轴的技术规定达67款之多,其中严格规定驱动半轴总成和传动轴总成的振动频率,目的是避免和发动机、轮胎以及其他传动系部件发生共振,从而更加全面合理地设计汽车底盘;零件供应商,易随意组合中心固定型等速万向节和伸缩型等速万向节,从而造成总成的失衡,使汽车产生异常振动,出现异响[2]。对于创立自主知识产权的汽车厂家来说,造出一流汽车仍有很长的路要走。
1.3 汽车万向传动装置设计主要内容与设计思路
课题研究对象是后轮驱动广泛应用的十字轴式万向传动装置,主要零件包括传动轴、万向节、支撑装置等,这些关键零部件的设计对整个万向传动装置性能具有很大的影响。采用有限元技术研究这些关键零部件的静力学特性,对其结构进行优化设计,是非常重要和必须的。在此基础上,再进行万向传动装置设计不但可以获得最佳的万向传动装置基本参数,还可以大大缩短万向传动装置总成开发周期、降低开发费用,提高设计质量,保证其设计的精确性。
1. 设计的主要内容
本设计选择万向传动轴的优化,设计基本要求如下:
(1)保证所连接的两轴的夹角及相对位置在一定范围内变化时,能可靠而稳定的传递动力;
(2)保证所连接的两轴尽可能等速运转;
(3)使用有限元分析软件ANSYS对万向传动装置的设计零部件进行静态分析,完成万向传动装置主要部件的优化设计从而解决工艺合理、成本低、可靠性高的设计要求;
(4)在CAE分析的基础上完成设计图纸。
2. 设计的基本技术路线
设计的技术路线如图1.1所示。
第2章 万向传动装置结构方案确定
2.1 设计已知参数
本设计的已知参数如表2.1所示
表2.1 设计基本参数
发动机转矩Temax430N••m/1500r/min
变速器一挡传动比i16.515
整车总质量8495Kg
驱动桥满载载荷5500Kg
主减速器传动比i04.875
轮胎规格8.25R16
万向传动装置最左与最右两万向节中心之间的距离L2186m
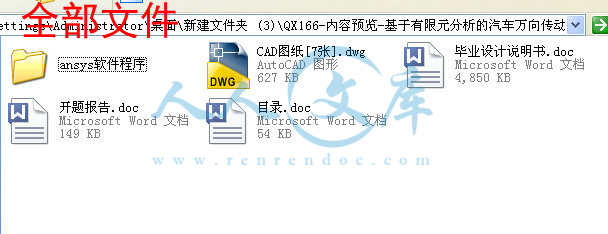
![CAD图纸[7张].jpg](/ueditor/net/upload/2014-06-11/41455cbf-13de-411f-901f-491f7134f45e.jpg)

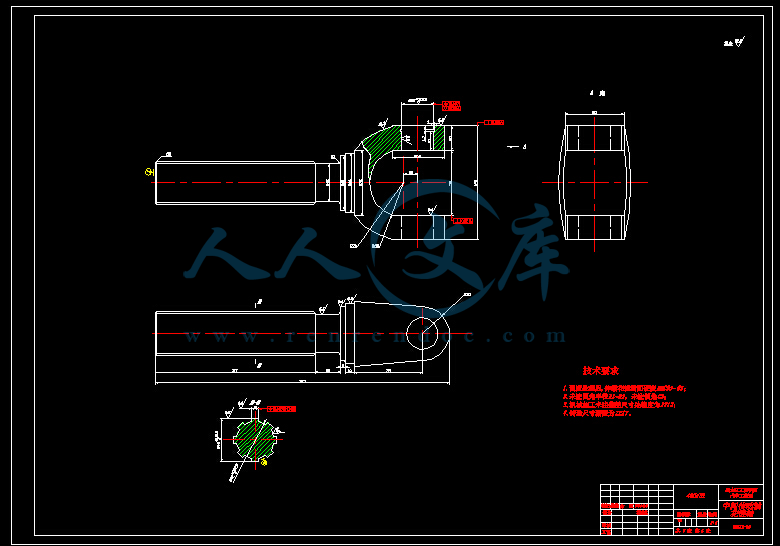
