缠绕式双卷筒提升机设计
59页 18000字数+说明书+外文翻译+开题报告+8张CAD图纸
A0总装图.dwg
A1主轴装配图.dwg
A1油缸.dwg
A1滚筒.dwg
A1盘式制动器.dwg
A2制动器筒体.dwg
A2离合器.dwg
A3制动器体.dwg
中期检查表.doc
外文翻译--ALSiC颗粒金属基复合材料的加工 中文版.doc
外文翻译--ALSiC颗粒金属基复合材料的加工 英文版.pdf
毕业实习报告.doc
缠绕式双卷筒提升机设计开题报告.doc
缠绕式双卷筒提升机设计论文.doc
摘 要
单绳缠绕式矿井提升机的工作原理:钢丝绳的一端用钢丝绳夹持固定在卷筒幅板上,另一端经卷筒的缠绕后,通过井架天轮悬挂提升容器。这样,利用主轴旋转方式的不同,将钢丝绳缠绕上或放松,以完成提升或下降容器的工作。
主轴装置是单绳缠绕式矿井提升机的主要工作机构,它的作用是: ①缠绕提升机钢丝绳;②承受各种正常载荷(包括固定载荷和工作载荷);③承受各种积极情况所造成的非常载荷。在非常载荷作用下,主轴装置部分不应有残余变形。单绳缠绕式矿井提升机的主轴装置是其核心部件,要求我们应认真设计,精心制造,这对于确保矿井提升机安全可靠运行,预防和杜绝故障及事故的发生,也具有十分重要的意义。
本设计根据生产实际和预选的数据,以提升机的配套设备为核心,经过科学的计算和分析,设计、选择了一套矿井提升机的传动系统设备,并采用了光电测速传感器作为深度指示系统的数据采集装置,实现了从机械控制到数电控制的转变,同时为提升机控制系统的技术改造奠定了基础。
关键词:提升机,主轴,制动器,光电测速传感器
ABSTRACT
What the principle of the single rope twines mine pit elevator is that: One end of the steel wire rope is fixed to Winding by the steel wire rope nip, another end after twined hangs and promotes the vessel by derrick wheel. In this way, we make use of the differences of the revolve way to twine or relax the steel wire rope so that to complete the vessel to step up or drop down.
Main axle is the core part of the mine elevator. Its functions are: ① the steel wire rope of twines the type mine pit elevator ; ② endure a kind of normal load( including fixed load and work load ); ③ endure the kinds of unusual load which is result from positive situation. Under the unusual load function, the part of the main axle equipment should not remain remaining distortion. It required us to be careful designing and manufacture when designing and manufacturing. Only in this way, we can prevent the occurrence of failures or accidents .Obviously, the possesses is very significance.
This design is on the basis of the data which are chosen by advance and actually, take the elevator supplementary equipment as the core, after the analysis and computation in science, has designed and chosen a set of the transmission system of the mine pits elevators, and used the electrical-light sensor as the equipment of the indicating system which to measure the amount of the depth of the tank. It enforced the change from the mechanically control to the numerical control, at the same time, has laid the foundation for improve the control system of the elevator.
KEY WORDS: elevator, main axle, brake, electrical-light measurement velocity sensor
目 录
1 前 言1
1.1提升机的用途和发展概况1
1.2提升机的结构和用途2
2 课题设计简介5
2.1设计课题5
2.2设计步骤5
2.3设计思路5
3 JK—3提升机 (E系列)主轴装置的原始资料6
3.1本产品的型号、名称6
3.2本产品的性能指标和设计参数6
4 JK—3提升机(E系列)的选择和设计7
4.1 JK—3矿井提升机的工作原理和主要结构7
4.1.1主轴7
4.1.2卷筒7
4.1.3主轴承8
4.1.4盘形制动器装置9
4.1.5深度指示系统9
4.1.6减速器10
4.1.7联轴器10
4.2主轴装置的设计依据11
4.2.1钢丝绳11
4.2.2卷筒宽度11
4.2.3钢丝绳最大静张力11
4.2.4钢丝绳最大静张力差△F12
4.2.5最大提升速度Vmax12
4.2.6电动机功率PN12
4.3主轴的选择13
4.4主轴的设计13
5 主要通用部件的选型计算15
5.1盘形制动器15
5.2减速器15
5.3齿轮联轴器16
5.4弹性棒销联轴器16
6 主轴的校核17
6.1主轴强度校核17
6.1.1工况一:提升开始, 。18
6.1.2工况二:提升终了, ,。21
6.2主轴挠度校核26
6.2.1工况一:提升开始27
6.2.2工况二:提升终了27
7 轴承寿命计算29
7.1左轴承29
7.2右轴承30
8 螺栓联接的计算和校核31
8.1螺栓选用型号31
8.2高强度螺栓平面摩擦联接校核31
8.3受扭转力矩铰制孔螺栓强度计算31
9 机器的安装调试和维护33
9.1机器的安装要求33
9.1.1主轴装置33
9.1.2卷筒34
9.1.3盘形制动器34
9.1.4电动机34
9.1.5减速器35
9.2机器的调整35
9.2.1产品空运转试验要求35
9.2.2机器的负荷试车36
9.2.3机器的加载试车36
9.3机器的维护和保养37
9.3.1机器的维护和安全使用37
9.3.4制动器的保养37
9.4机器故障的排除38
结 论40
致 谢41
参考文献42
附录① 单绳缠绕式提升机设计规范(摘录)44
附录② 光电测速传感器52
2 课题设计简介
2.1设计课题
我所设计的课题题目是:缠绕式双卷筒提升机,以提升机(系列)为例,主要是主轴装置的设计。
提升机(系列)主轴装置设计的主要技术指标:
1.卷筒直径;
2.最大提升速度不大于;
3.矿井深度设定为。
2.2设计步骤
第一步:根据类似主轴结构选定主轴并进行优化设计;
第二步:依据所设计的主轴选用通用部件;
第三步:对主轴及通用部件进行校核计算;
第四步:确定主轴装置的安装、使用和维护的方法。
本产品的性能指标和设计参数
卷筒直径
最大提升速度
矿井深度
容器自重
载重量
2.3设计思路
在总的设计过程当中,尽量选用通用部件,尽量采用成熟的结构和标准部件以及提升机通用部件,提高标准化、系列化、通用化的程度;积极、慎重地采用和推广新结构、新材料、新工艺,做到技术先进,结构、工艺经济合理;在结构上尽可能考虑最大限度地缩短安装调试时间,做到以最少的代价带来最大的经济效益;在设计过程中,我以可靠性、安全性、经济性、方便性为原则,认真、求实、虚心求教、改革创新为信念,完成每一项任务
提升机是矿山大型固定设备之一,是联系井下与地面的主要运输工具,在矿山生产建设中起着重要的作用。矿井提升机主要用于煤矿、金属矿和非金属矿中提升煤炭、矿石和矸石、升降人员、下放材料、工具和设备。
矿井提升机与压气、通风和排水设备组成矿井四大固定设备,是一套复杂的机械——电气排组。所以合理的选用矿井提升机具有很大的意义。
矿井提升机的工作特点是在一定的距离内,以较高的速度往复运行。为保证提升工作高效率和安全可靠,矿井提升机应具有良好的控制设备和完善的保护装置。矿井提升机在工作中一旦发生机械和电器故障,就会严重地影响到矿井的生产,甚至造成人身伤亡。
熟悉矿井提升机的性能、结构和动作原理,提高安装质量,合理使用设备,加强设备维护,对于确保提升工作高效率和安全可靠,防止和杜绝故障及事故的发生,具有重大意义。
矿井提升机已有很长的发展历史。早在八百多年以前,我国古代劳动人民就发明了轱辘,用手摇骨碌从地下提升煤炭和矿石,以后发展成畜力绞车。十九世纪,由于电力的发展,电力拖动的提升机逐渐代替蒸汽提升机。近几十年来,矿井提升机有了更大的发展,出现了多绳摩擦式提升机以及先进的拖动和控制系统。目前,国外的矿井提升机正向体积小、重量轻和自动化的方向发展,以适应深井和大量的需要。
解放以前,我国根本不能制造大型矿井提升机。解放以后,我国建立了矿井提升机的制造工厂,并已由仿制和改进国外产品发展到能自行设计和制造。目前,我国已能成批生产近代化的大型矿井提升机。
1958年,我国设计并试制成功第一台DJ2*4多绳摩擦式提升机,为我国矿井提升机的制造和使用开辟了一个新的领域。目前,我国已能成批生产JKM型多绳摩擦式提升机,并正在逐渐形成多绳摩擦式提升机的新系列。
1.2提升机的结构和用途
每台提升机都由若干部分组成:主轴、缠绕机构、轴承和主制动器。这些便是基本部分。缠绕机构有好几种,最常用的结构是单圆柱形滚筒及双圆柱形滚筒。对于单圆柱形滚筒,两根钢丝绳功用一个滚筒缠绕面;第一根钢丝绳自滚筒松开而相应地漏出的滚筒面由另一根钢丝绳缠上。对于双圆柱形滚筒,没根钢丝绳都缠绕在特有的滚筒上,即在任何时刻钢丝绳都只是缠在两支滚筒总缠绕面的一半上。在这种情形下,一个滚筒结实地固定在主轴上,另一个则活套在主轴上,借助于离合器与主轴相连,以便在必须时可使二滚筒作相对转动。滚筒相对转动的可能行使得提升设备的操作变得容易,因为可以容易地调节由于钢丝绳弹性变形而逐渐伸长的长度。此外,还可以补偿由于对钢丝绳做周期性的试验而截下的长度。依次,在每个滚筒的表面除了等于提升高度的钢丝绳长度外尚需附加30米长的钢丝绳,这样才有可能当滚筒作相对转动以使一根钢丝绳的铅垂长度增加时并不使另一根钢丝绳缩短。当有双滚筒提升机时还可能更换操作水平。当上容器停在井口车场时而下容器移至新的位置。这在一个提升水平但有个承受台时也是需要的,例如翻转式罐笼当提升重物及提人时容器的终端位置是不同的。当用单滚筒或滚筒的离合器不作用时,除原定水平外,如要服务于另一水平或承受台则仅能用一个提升容器;第二个容器不过起着平衡锤的作用,此时,提升生产率骤然减少一半。
提升机的第二个重要部分为把电动机的转动传到安置有缠绕机构的主轴上的减速器。减速器结构因其类型、用途不同而异。但无论何种类型的减速器,其基本结构都是由轴系部件、箱体及附件三大部分组成。轴系部件包括传动件、轴和轴承组合,轴承组合包括轴承、轴承盖、密封装置以及调整垫片等。减速器箱体上用以支持和固定轴系零件,保证传动件的啮合精度、良好润滑及密封的重要零件。箱体质量约占减速器总质量的50/%。因此,在箱体结构对减速器的工作性能、加工工艺、材料消耗、质量及成本等有很大影响,设计时必须全面考虑。为了使减速器具备较完善的性能,如注油、排油、通气、吊运、检查油面高度、检查传动件啮合情况、保证加工精度和装拆方便等,在减速器箱体上常需设置某些装置或零件,将这些装置和零件及箱体上相应的局部结构统称为减速器附属装置或简称为附件。它们包括:视孔与视孔盖、通气器、游标、放游螺塞、定位销、启盖螺钉、吊运装置、油杯等。
制动器为提升机设备第三个重要部分。制动器直接作用于制动轮或制动盘上产生制动力矩的部分按结构分为盘式和块式闸等;第四部分是传动机构,是控制并调节制动力矩的部分。按传动能源分为油压、压气或弹簧等;第五部分为深度指示器及与其相连的控制保护装置,其用途为给司机指出提升容器在井筒中的位置;第六部分为操作台,电动机及制动器的操纵手把均匀集中在这里,有时也有离合器操纵手把;提升机最后一部分为油压及压气设备前者为每一机器所必备的;并且在油压制动传动时,它需作为机器润滑,同时也作为制动装置。当用压气制动时,油压设备所起的作用仅限于机器的润滑,而此时需要附加压气设备,而在油压制动时却不需要附加压气设备。
这次毕业设计过程的认真思考、反思,我总结出此次设计过程的得与失:
1.面对主轴装置的设计,我开始设计自己的方案,由于没有经验,走了很多弯路。经过指导老师的提醒,我才认识到研究以往设计资料的重要性,然后根据相似结构设计主轴,最终取得了成功。
2.在接下来的设计过程中,我吸取了开始的教训,按照《矿井提升机械》上的要求进行设计和选型,然后对其进行校核,确定其是否满足裁量的强度刚度要求和设计任务书的要求,不满足要求,再重新设计主轴进行校核,直到设计出合适的主轴为止。
3.主轴与固定卷筒支轮的连接采用无键连接,因为我们选择的主轴的安装方式为热装,这样比键连接更安全;卷筒的安装方式为对半结构,这样一方面便于安装,另一方面运输方便;卷筒与固定支轮的连接采用高强度螺栓连接,装拆方便。这些都是在借鉴以往设计成果的基础上决定的方案。
4.其次,在设计中没有考虑到整个装置的润滑,比如轴承的润滑、制动器的润滑;液压站也没有涉及,这是本设计的一个缺憾。
5.在设计中,我在深度指示系统上使用光电测速传感器接收、传递信号,使提升机的整体结构更加紧凑,占地面积大大减少,同时提高了可编程控制器的使用价值,优化了提升机电控系统的结构和功能。
通过这次设计,我认识到一名设计人员在设计过程中要具有求实、严谨、负责的态度,要有积极创新的精神,这是我在这次毕业设计中的所感和所得。
参考文献
[1] 曾志新主编.机械制造技术基础.武汉:武汉理工大学出版社,2004.4
[2] 甘水立主编.几何量公差与检测.上海:上海科学技术出版社,2004.7
[3] 文九巴主编.机械工程材料.北京:机械工业出版社,2002.7
[4] 彭文生等主编.机械设计.北京:高等教育出版社,2002.8
[5] 朱冬梅、胥北澜主编.画法几何及机械制图.北京:高等教育出版社,2000.12
[6] 陈康宁主编.机械工程控制基础.西安:西安交通大学出版社,2004.6
[7] 丁玉兰编著.人机工程学(第三版).北京:北京理工大学出版社,2005.7
[8] 邓文英主编.金属工艺学(上册).北京:高等教育出版社,2003
[9] 邓文英主编.金属工艺学(下册).北京:高等教育出版社,2003
[10] 范钦珊主编.工程力学.北京:清华大学出版社,2005.8
[11] 单辉祖编著.材料力学(Ⅰ).北京:高等教育出版社,1999
[12] 单辉祖编著.材料力学(Ⅱ).北京:高等教育出版社,1999
[13] 邹惠君主编.机械原理.北京:高等教育出版社,1999
[14] 任嘉卉主编.公差与配合手册.北京:机械工业出版社,2000.4
[15] 吴宗泽主编.机械设计实用手册.北京:化学工业出版社,2003.6
[16] 梁德本、叶玉驹主编.机械制图手册.北京:机械工业出版社,2002.2
[17] 赵丁选主编.光机电一体化设计使用手册(上册).北京:化学工业出版社,2003.4
[18] 赵丁选主编.光机电一体化设计使用手册(下册).北京:化学工业出版社,2003.4
[19] 李仪钰主编.矿山机械(提升运输机械部分).北京:冶金工业出版社,1980.7
[20] 矿研究院编.矿井提升机培训教材之二(电控部分).洛阳矿山机械工程设计研究院自动化研究所
[21] 矿研究院编.矿井提升机培训教材之一(机械部分).洛阳矿山机械工程设计研究院提升机械研究所
[22] 许福玲,陈尧明主编.液压与气压传动.北京:机械工业出版社,2004.7
[23] 矿山提升设备.北京:煤炭工业出版社,1980.9
[24] 机械工业洛阳轴承研究所编.全国滚动轴承产品样本. 1995
[25]2002-12-6 冶金矿山设计参考资料(上册).冶金工业出版社.1974
[26] 冶金矿山设计参考资料(下册).冶金工业出版社.1974
[27] JK—2矿井提升机(E系列)使用说明书.1991.5
[28] 贾现召,曹艳玲.HHS-900/1500液压卸荷站的使用与维护.煤矿机械.2004
[29] 张步斌.一种新型矿井提升机.中国专利技术.2004-04-01
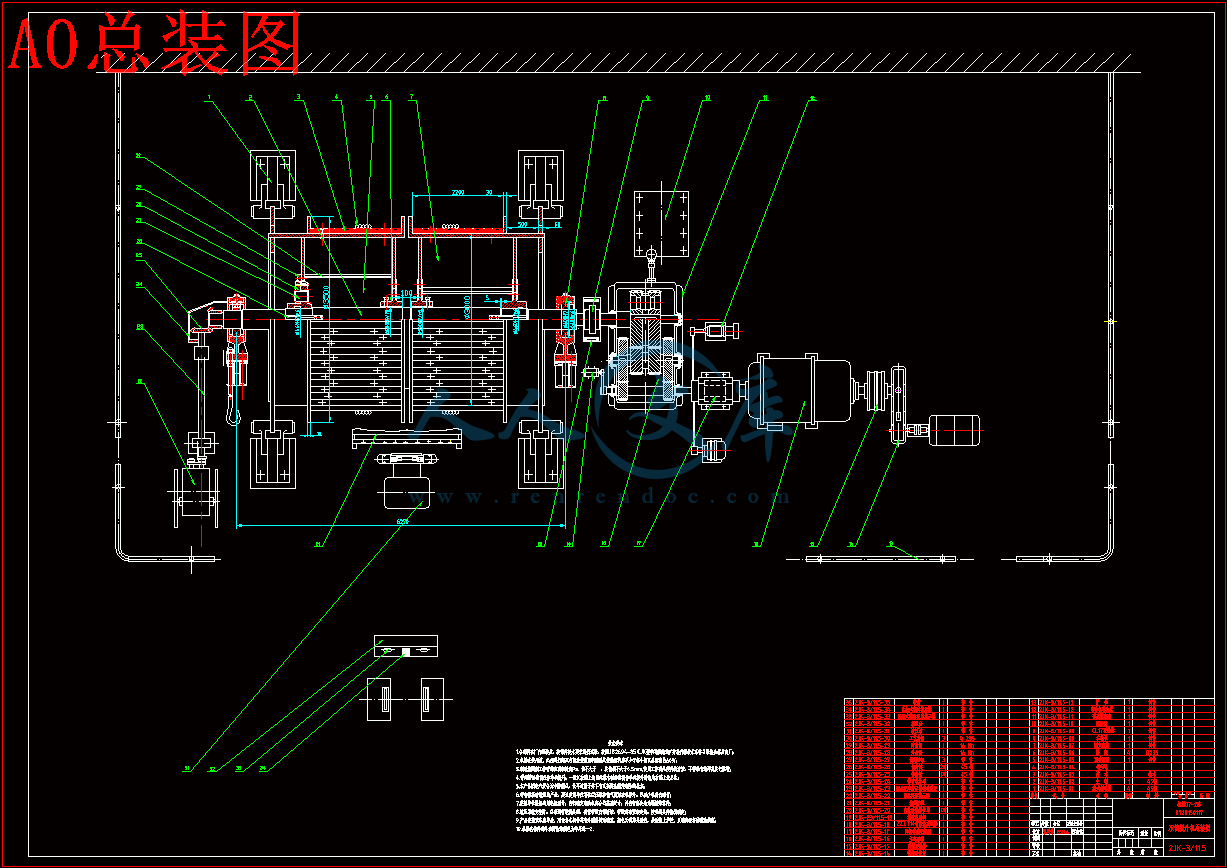
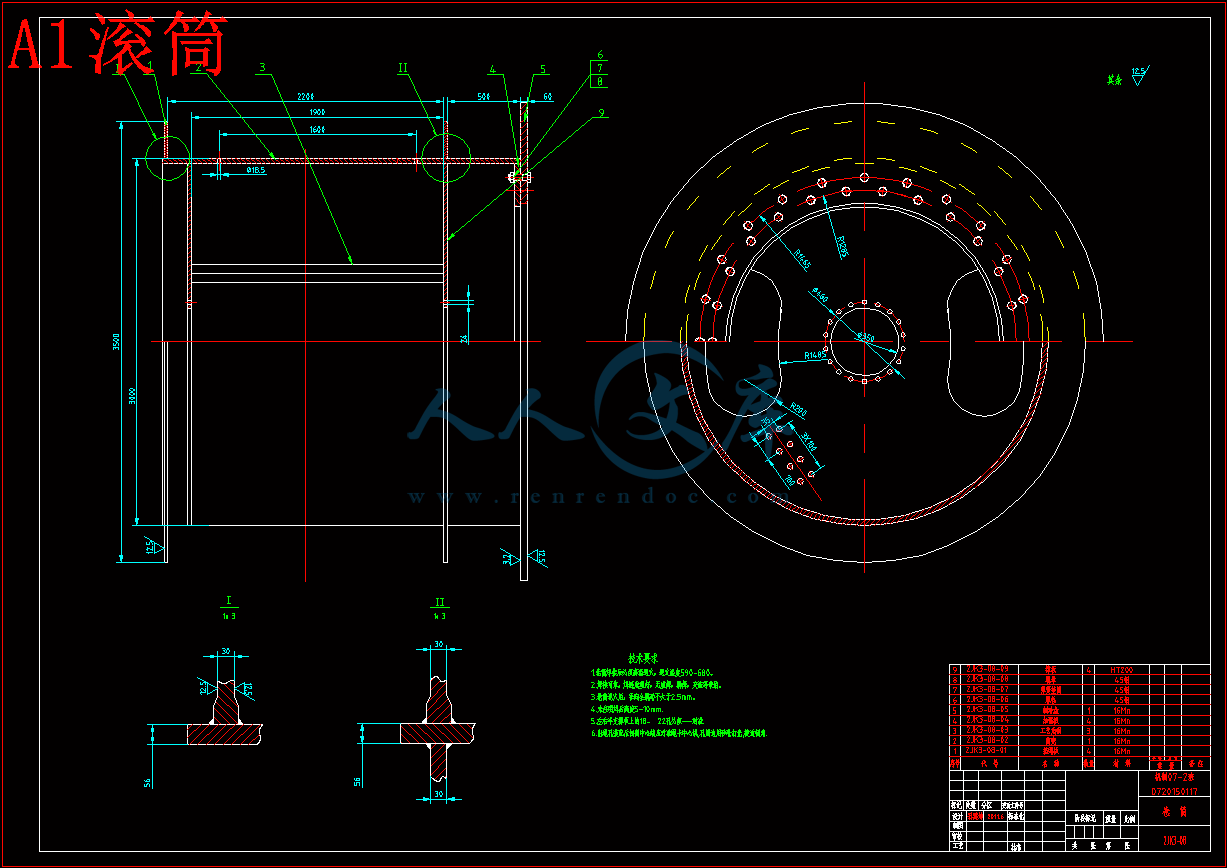
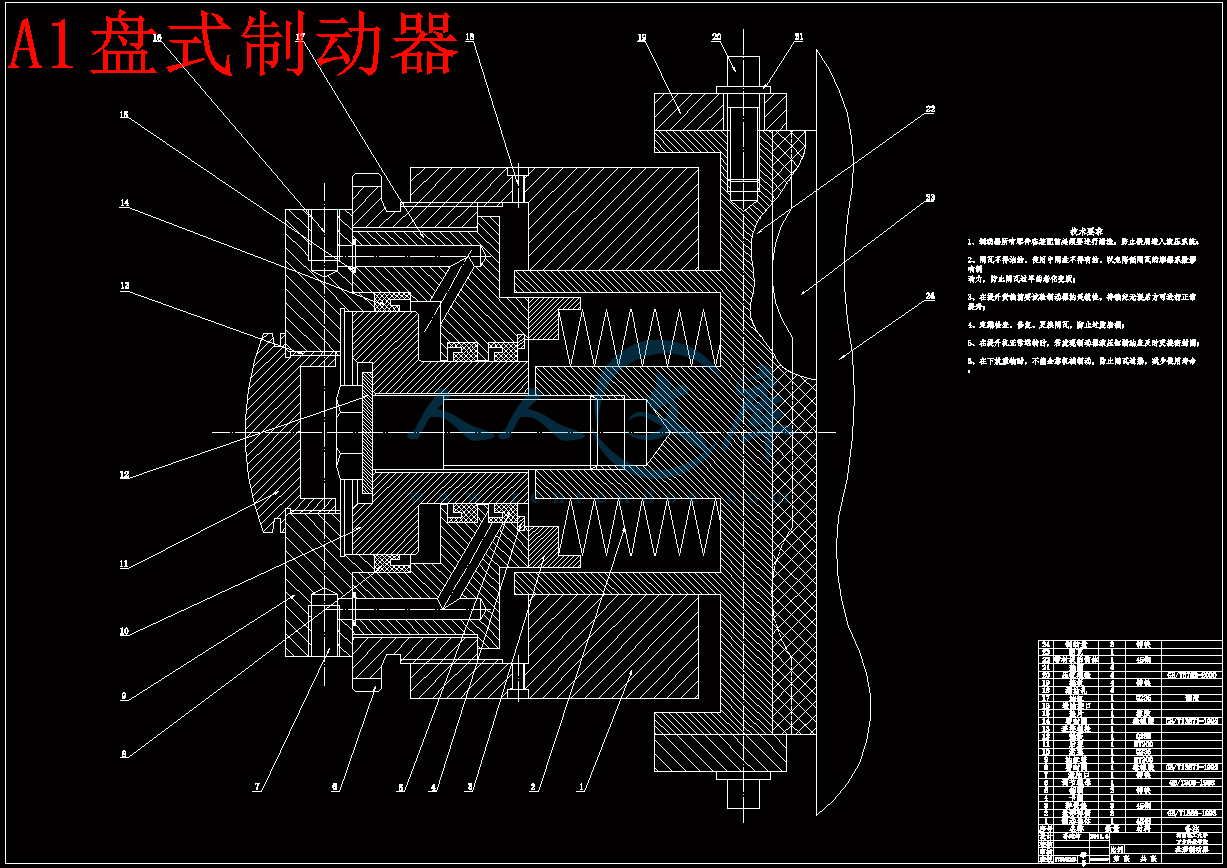
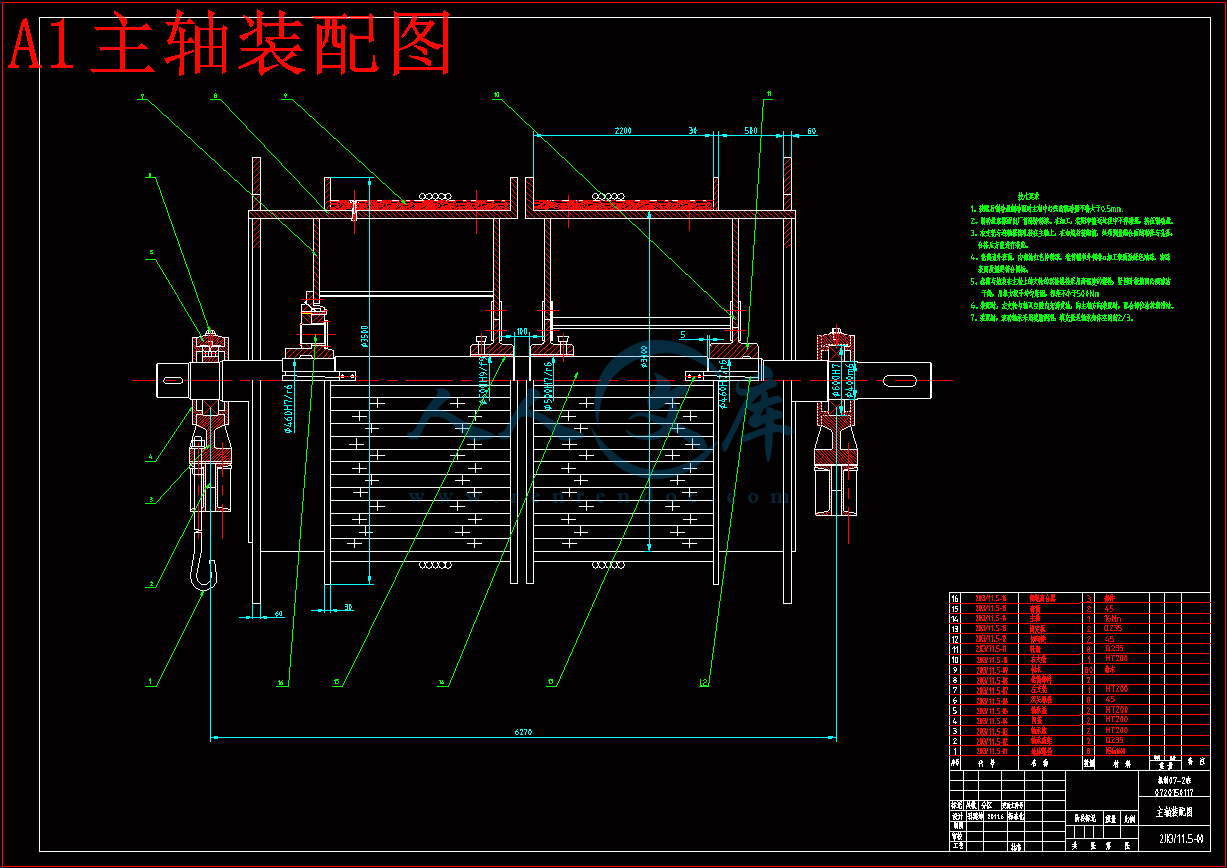
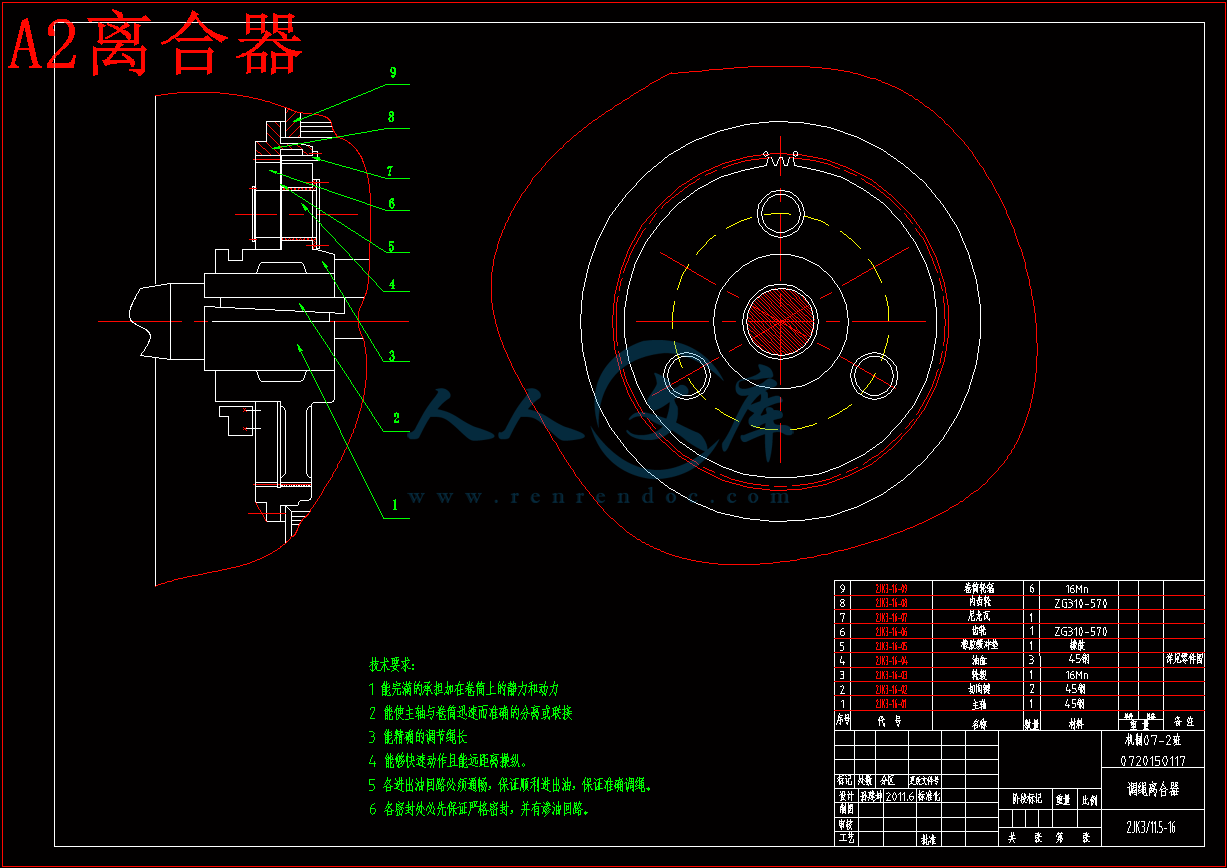
