超声珩磨机床的设计
57页 21000字数+说明书+外文翻译+开题报告+8张CAD图纸
中期报告.doc
主轴A2.dwg
外文翻译--一种研究光学玻璃机械加工的实验.doc
套筒A3.dwg
总装图A0.dwg
油石A3.dwg
珩磨头A1.dwg
胀锥A2.dwg
螺母套筒A2.dwg
装配图A0.dwg
超声珩磨机床的设计开题报告.doc
超声珩磨机床的设计论文.doc
摘 要
超声加工广泛应用于磨削加工,已经成为新一代精密加工发展方向之一。本文主要是从珩磨应用这一角度来作一个具体介绍。
从介绍超声加工原理和特点与珩磨的特点、原理以及应用入手,本设计引出超声珩磨加工,介绍其原理应用并详细阐述超声波振动珩磨头的基本结构及设计要点。在以上基础上,针对设计目标分别对超声波振动珩磨的各个组件进行结构和理论设计与分析并校核。珩磨是一种固结磨粒压力进给切削的精整加工方法,不仅能切除较大的加工余量而且能有效的提高工件的尺寸精度和形状精度、降低工件表面的粗糙度。珩磨主要加工内孔,在一定条件下也可以加工外圆、平面、球面、齿面。珩磨轨迹是交叉网纹,珩磨加工变质层很小能提高工件的使用寿命,因为珩磨油石磨粒受两个方向的磨削阻力所以它有自锐作用。珩磨与主轴一般采用浮动连接,符合光整加工的的浮动加工原理。为了改善珩磨加工的使用性能可采用分粗、精珩磨的平顶珩磨。目前珩磨正向改善珩磨油石组合安装的方向发展,以便实现一次加工就能实现粗珩和精珩两到工序。
关键词:超声加工 珩磨 浮动连接
Abstract
Ultrasonic processing is widely applied in the process of rubing, already becoming a new generation of developing direction of accuratelly processing. This study mainly uses this angle about how to practice honing operation to make a concrete introduction.
From introducing the characteristics and principle of ultrasonic processing and the use of honing, it is drawing ultrasonic honing processing , recommending its principle use and explaining ultrasonic vibration basic structure of the head of honing and the main point in detail. On the basis of the summary above , this study will give a design of structural and theoretical of each package of ultrasonic vibration honing separately to the designed object,and of course analyse and check it. It is a kind of solid knot that honing whet is to process the method when a pressure enter to slice, not only can it cut off bigger process but the amount of remaining and size accuracy and shape accuracy of the ability valid exaltation work piece, lower rough degree of a surface of work.The honing whets to mainly process inside the bore, can also process the outside circle, flat surface, surface of sphere under the condition of certain.The honing whet is to cross the net surface, the honing whets is to process to change the layer very small and it can raise the service life of the work piece, because the honing whets of the oil stone is to pare the resistance so it has the function of cutting .The honing whets is to adopt the conjunction with principal axis generally, matching the light processed float.Whet to process ,for the sake of the improvement of the function , can adopt the an accurate honing.Currently the honing whet just the direction development that whet the oil stone combination to press to pack toward the improvement honing , in order to carry out to process once and then can carry out the thick honing and the accurate honing to arrive the work preface.
Keyword: Processing ultrasonically Honing Floating connector
目 录
前 言1
1 绪论3
1.1珩磨加工特点及应用范围3
1.1.1珩磨加工3
1.1.2珩磨加工特点4
1.1.3珩磨工艺应用范围5
1.2珩磨加工的工作原理5
1.2.1珩磨加工的原理5
1.2.2珩磨运动过程6
1.2.3珩磨的切削过程7
2珩磨头的设计10
2.1珩磨头设计因素及要求10
2.1.1珩磨头设计时应考虑的因素10
2.1.2对珩磨头结构的基本要求10
2.2珩磨头的结构形式12
2.2.1通用珩磨头14
2.2.2小孔珩磨头15
2.2.3大孔珩磨头20
2.2.4平项珩磨头20
2.2.5特殊珩磨头21
2.3珩磨油石23
2.3.1珩磨油石的性能24
2.3.2珩磨油石的规格及数量28
2.3.3珩磨油石的连接方式30
2.4常见的珩磨缺陷和解决措施31
2.4.1圆度误差超差31
2.4.2孔的直线度误差超差31
2.4.3孔的尺寸超差32
2.4.4珩磨表面粗糙度达不到工艺要求32
2.4.5珩磨表面刮伤32
3超声珩磨34
3.1 珩磨加工34
3.1.1 珩磨加工特点34
3.1.2珩磨工艺应用范围34
3.2 超声珩磨工作原理及加工特点35
3.2.1 超声珩磨工作原理35
3.2.2超声珩磨加工特点37
3.3换能器的选用38
3.3.1换能器工作原理38
3.3.2换能器的分类39
3.3.3换能器的选择41
4 浮动连接装置与回复装置43
4.1动连接浮装置43
4.2 回复装置45
结束语48
致 谢50
参考文献51
珩磨是一种低速磨削法,常用于内孔表面的光整、精加工。珩磨油石装在特制的珩磨头上,由珩磨机主轴带动珩磨头作旋转和往复与动,并通过其中胀缩机构使油石伸出,向孔壁施加压力以作进给运动,实现珩磨加工。为提高珩磨质量,珩磨头与主轴一般都采用浮动连接,或用刚性连接而配用浮动夹具,以减少珩磨机主轴回转中心与被加工孔的同轴度误差对珩磨质量的影响。
珩磨头在每一往复行程内的转数为一非整数,因而它在每一行程的其实位置都与上次错开一个角度,这就使油石上的每颗磨粒在加工表面上的切削轨迹不致重复,从而形成均匀交叉珩磨网纹。
由于油石具有一定长度,油石的切削轨迹与前一转在轴向上有一段重复,所以保证了前后切削轨迹衔接得比较平滑。当珩磨头在孔中往复运动时,油石就像桥板一样搭在加工表面突出的高点上,在珩磨压力的作用下,将高点削去。同时加工表面上的高点也冲击着钝了的磨粒,使之破碎或脱落,而重新露出锋锐的磨粒。所以珩磨过程也就是油石与加工面不断相互磨削与修整,使原来刀痕与残余应力变形层被磨去、孔形误差得以校正,油石也相应地被磨损。当二者由点接触转为面接触湖,单位面积上的珩磨压力相应降低,切削边薄,油石开始被堵塞钝化,切削作用逐渐下降而消失,加工表面的粗糙度也逐渐降低,珩磨过程转为抛光过程,达到要求尺寸,最后油石退回。
1.1.2珩磨加工特点
(1)表面质量特性好 珩磨可以获得较低的表面粗糙度,一般可达Ra0.8~0.2μm,甚至可低于Ra0.025μm,同时珩磨表面上有均匀的交叉网纹有利于贮油润滑。实现平顶珩磨,可使有相对运动的摩擦副获得较理想的表面质量。
(2)加工精度高 现代珩磨技术不仅可以获得较高的尺寸精度,而且还能修正孔在珩磨加工中出现的轻微形状误差,如圆度、圆柱度和表面波纹等。珩磨小孔时,圆度与圆柱度可达0.5μm,轴线直线度可小于1μm,珩磨中等孔径,圆柱度可达5μm,圆柱度不超过10μm,珩磨短孔时,若用刚性连接珩磨头与平面浮动夹具,还可适当提高短孔轴线与端面的垂直度。间断孔珩磨可提高同轴度。
(3)珩磨效率高 可以使用多条油石或超硬磨料油石,也可提高珩磨头的往复速度一增大网纹交叉角,能较快地去除珩磨余量与孔形误差。也可应用强力珩磨工艺,一有效地提高珩磨效率。珩磨工件干净,在冷却液的冲洗下,很少积存赃物。珩磨加工一些圆周有孔或内槽的液压系统偶件时,可以保持这些孔与工件孔壁形成锐边,以保证偶件的液压性能。
(4)珩磨工艺较经济 薄壁孔和刚性不足的工件,或较硬的工件表面,用珩磨进行光整加工不需复杂的设备与工装,操作方便。磨料选择适当,工具设计合理,切削速度合理的情况下,珩磨的经济效果较研磨好(主要反映在加工效率、加工精度和表面质量上),且加工稳定,因而零组件的成品率高。并且,珩磨加工可节省研磨加工所必须的辅助材料,如清洗用的汽油、棉花等。采用超硬磨料做珩磨油石,经济效果更好。
1.1.3珩磨工艺应用范围
大量应用于各种形状的孔的光整或精加工,孔径从Ф1~1200mm,长度可达12000mm。国内珩磨机工作范围:Ф5~250mm,孔长3000mm。
可用语外圆、球面及内外环形曲面加工,如镀铬活塞环、挺杆球面与球轴承的内外圈等。
用于汽车、拖拉机与轴承制造业中的大量生产,也适用于各类机械制造中的批量生产。如珩磨缸套、缸孔、连杆孔、油泵油嘴与液阀体孔、轴套、摇臂和齿轮孔等。
适用于金属材料与非金属材料的加工,如铸铁、淬火与未淬火钢、硬铝、青铜、黄铜、硬铬与硬质合金、玻璃、陶瓷、晶体与烧结材料等。
1.2珩磨加工的工作原理
1.2.1珩磨加工的原理
珩磨是利用安装在珩磨头圆周上的若干砂条(油石),由张开机构将砂条沿径向张开,使其压向工件的孔壁;与此同时,使珩磨头(或工件)作旋转运动和直线往复运动。对孔进行低速磨削和摩擦抛光(见图1)。旋转及往复运动的结果是,油石上的磨粒在孔的表面上的切削轨迹呈交叉面又不重复的网纹,如图1(c)所示,因面获得表面粗糙度较小的加工表面。径向加压运动是油石的进给运动,加压压力愈大.进给量就愈大。
图1-l珩磨原理
(a)珩磨原理; (b)珩磨机; (c)一根油石在积行程中切削轨迹的展开
l,2,3,4—形成纹痕的顺序;5—工件;6一油石;7—油缸;8一链条;
?一网纹交叉角(切削角)
1.2.2珩磨运动过程
立式珩磨时,珩磨头由机床主轴带动相对工件作旋转和直线往复运动,同时油石对被加工表面作径向进给运动。前两种运动构成珩磨的主运动,井使油石形成螺旋运动,因此,油石上大量的磨粒就在加工表面上刻划下螺旋形交叉网纹的珩磨条纹。图2是单个油石在孔中完成一个双行程运动后所刻划的条痕展开示意图。图中为孔长:d。为孔的周长;日为网纹交叉角。I,Ⅱ,Ⅲ是油石在一个双行程中转折时顺次的位置。为避免每条油石的运动轨迹重复。即不让油石上的磨粒仍在原先刻出的条痕上刻划,应使油石在一个双行程终了时的位置Ⅲ,相对其行程的初始位置I,在圆周方向上有一个附加的偏移量s。
△和△为油石距孔两端的越程量,它是保证孔的正确形状和使油石磨损的主要因素。越程量偏小,容易使两端孔径变小,形成鼓形误差。越程量过大,将使两端孔径变大,形成喇叭形误差。当越程量取0.3~0.5倍的油石长度时.一般两端孔径不致产生较大的误差。
1.2.3珩磨的切削过程
深孔加工技术在珩磨的切削过程中,油石的表面状态、油石压力被加工表面二者的变化情况及相互关系,因采用的扩张进给方式的不同而不同。
1.定压进给的珩磨过程
定压进给中,进给机构以恒定压力压向孔壁,珩磨过程可根据油石表面的变化状态分为三个阶段:
(1)脱落切削阶段:加工初始阶段,由于孔表面粗糙,油石与孔壁的实际接触面积小,接触压力大,工件孔粗糙表面的凸起部分很快被磨去,而油石面因接触压力过大,加上切屑对油石粘接剂的磨耗使磨粒和粘接剂问的结合强度下降,因而有的磨粒在切削力作用下自行脱落,油石面即露出新的磨粒,即为油石的自锐。
(2)破碎切削阶段:随着珩磨的进行,孔表面越来越光滑,接触面积也逐渐增大,单位面积接触压力下降,切削效率降低,同时切下的切屑既少又细。这些切屑对油石粘接剂的磨耗也很小,因此,油石面的磨粒脱落很少。油石主要不是靠新磨粒切削,面是由磨粒尖顶切削,因而磨粒尖顶的负荷很大,磨粒易于破裂、崩碎而形成新的切削刃。
(3)堵塞切削阶段:此时油石与件表面的接触面积很大,极细的切屑堆积于油石孔壁之间不易排除,造成油石面气孔的堵塞。因此油石的切削能力极低,油石表面也变得很光滑,此时油石的磨削相当于施光。但当油石堵塞严重而产生黏结性堵塞时,油石完全失去切削能力并严重发热,加工精度与表面粗糙度均可受到破坏。因此,当油石进入堵塞切削时,要尽快结束珩磨。
参考文献
[1] 李伯民,赵波主编.现代磨削技术.北京:机械工业出版社,2003.1
[2]高兴军,赵恒华.高速超高速磨削加工技术的发展及现状.辽宁石油化工大
学学报,2004,24(4):43-46
[3]赵恒华,冯宝富,高贯斌等超高速磨削技术在机械制造领域中的应用.东北大学学报(自然科学版),2003,24(6):564-568
[4]张云电著.现代珩磨技术.北京:科学出版社,2007
[5]机械工程手册,第九卷.机械制造工艺(三).机械工业出版社.1982.5
[6]邹峰,于爱兵,王长昌.金属基金刚石砂轮修整技术的研究进展,精密制造与自动化,2003(2):12-14
[7]周曙光,关佳亮,郭东明等.ELID镜面磨削技术一综述,制造技术与机床,
2001(2):38-40
[8]龚庆寿,宁立伟,黄菊生等ELID精密镜面磨削技术及其应用研究.湖南工程学院学报,2003,13(3):45-47
[9]张春河,袁哲俊,张飞虎等.在线电解修整(ELID)超精密镜面磨削的影响
因素初探,金刚石与磨料磨具工程,1996.93(3):21-23
[10]朱波,袁哲俊,张飞虎等.ELID超稍密磨削钢结硬质合金及其表面质量分析.中国机械工程,2000,11(8):866-868
[11]关佳亮,袁哲俊,张飞虎等.ELID精密镜面磨削用新磨削液的研制.哈尔滨工业大学学报,1998,30(5):69-71
[12」关佳亮,袁哲俊,张飞虎.ELID精密镜面内孔磨削技术的应用.制造技术与机床,1998(1):25-26
[13]张飞虎,朱波,亲殿荣等.ELID磨削硬脆材料精密和超精密加工的新技术宇航材料工艺,1999(1):51-55
[14」张飞虎,张春河,欧海涛等.在线电解修整镜面磨削中砂轮耐用度的研究.哈尔滨工业大学学报,1999,31(6):9-11
[15〕关佳亮,郭东明,袁哲俊.ELID镜面磨削砂轮氧化膜生成机理.中国机械工程,1999,10(6):630-632
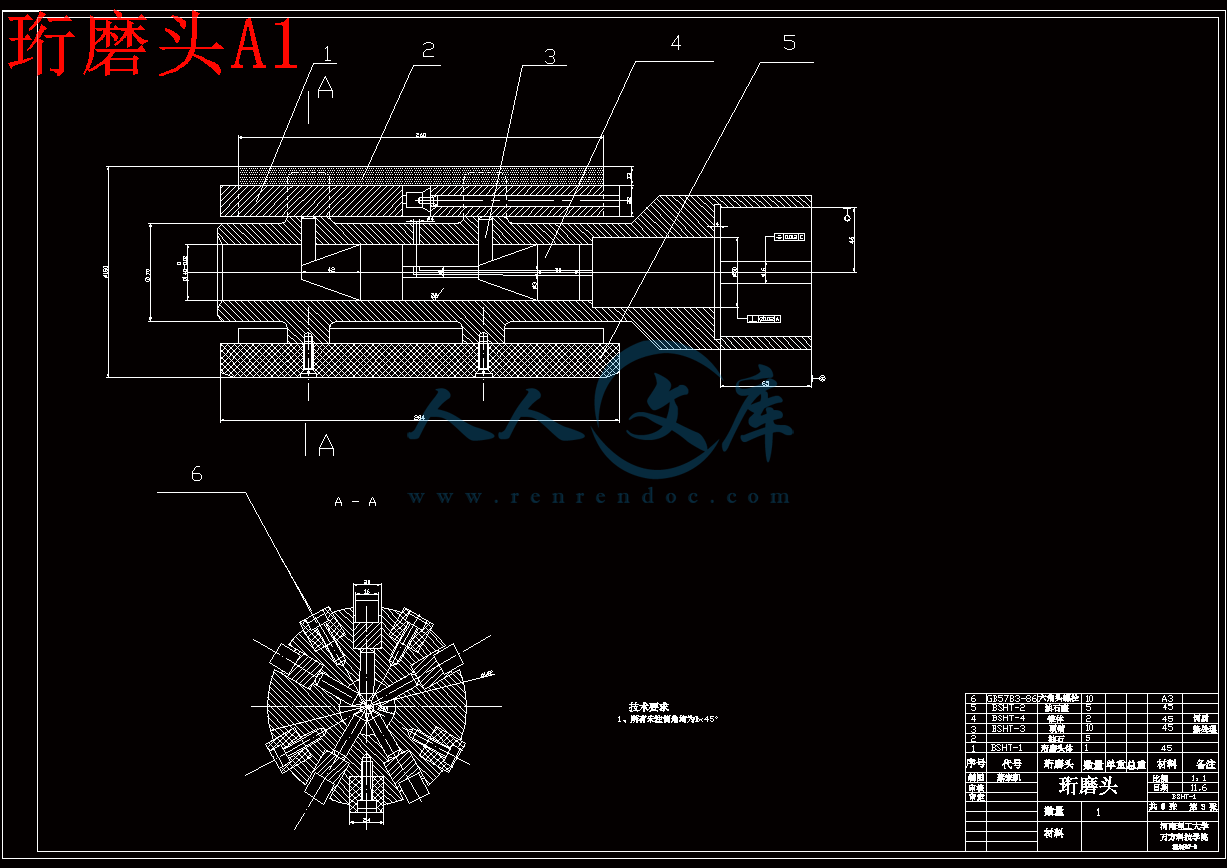
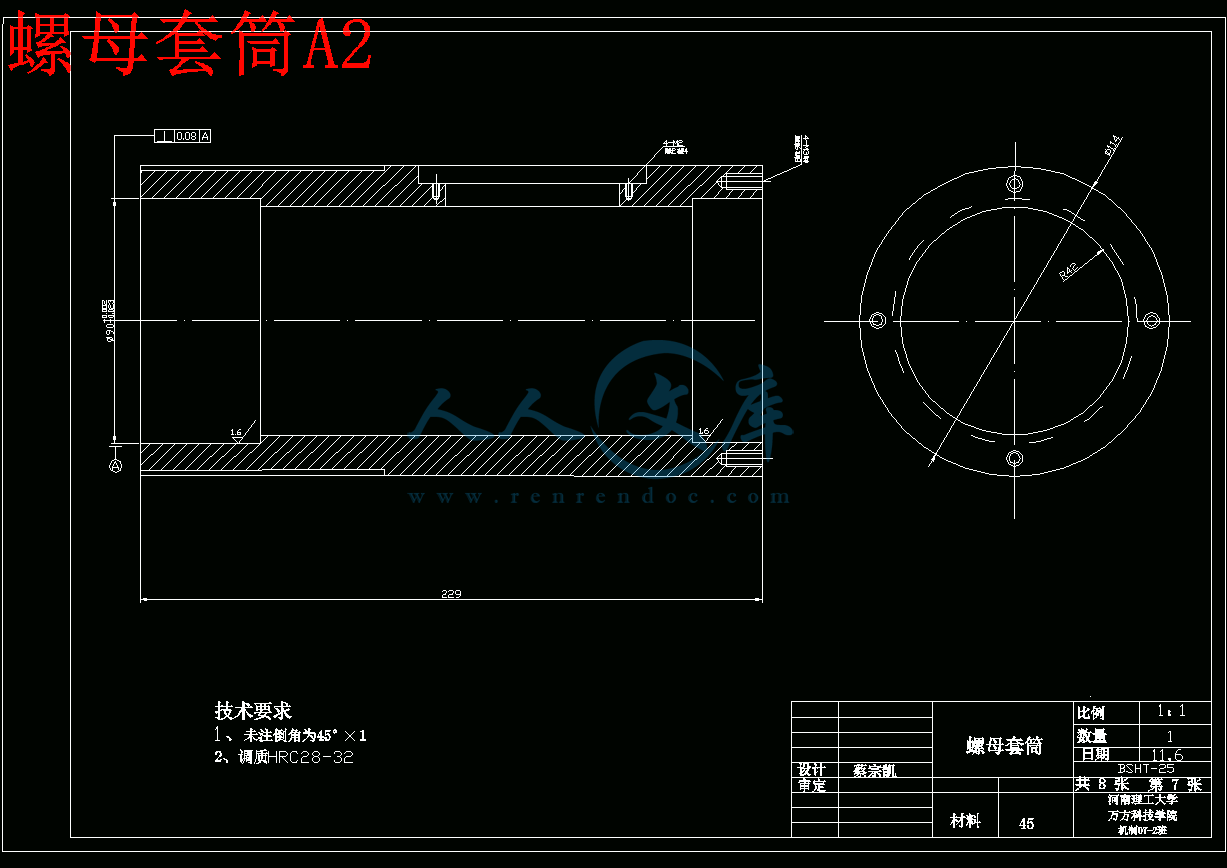
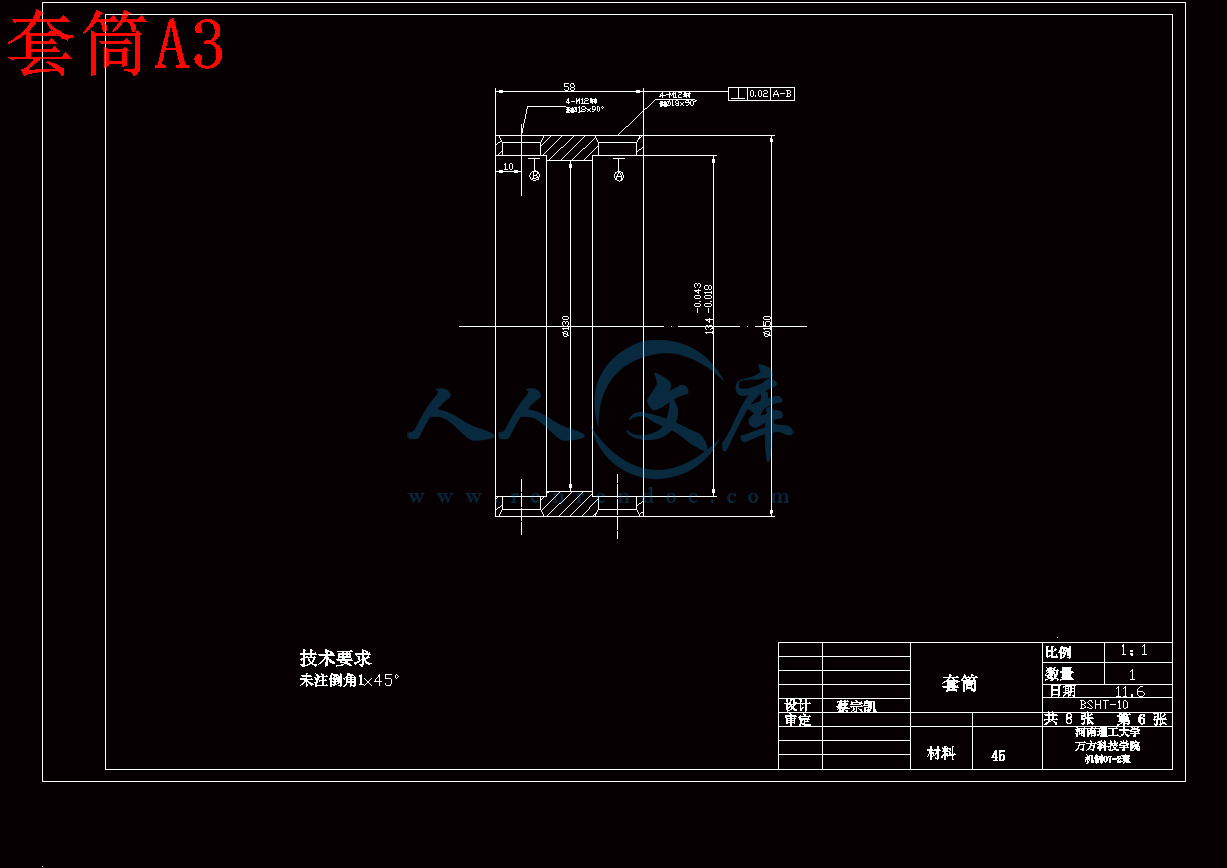
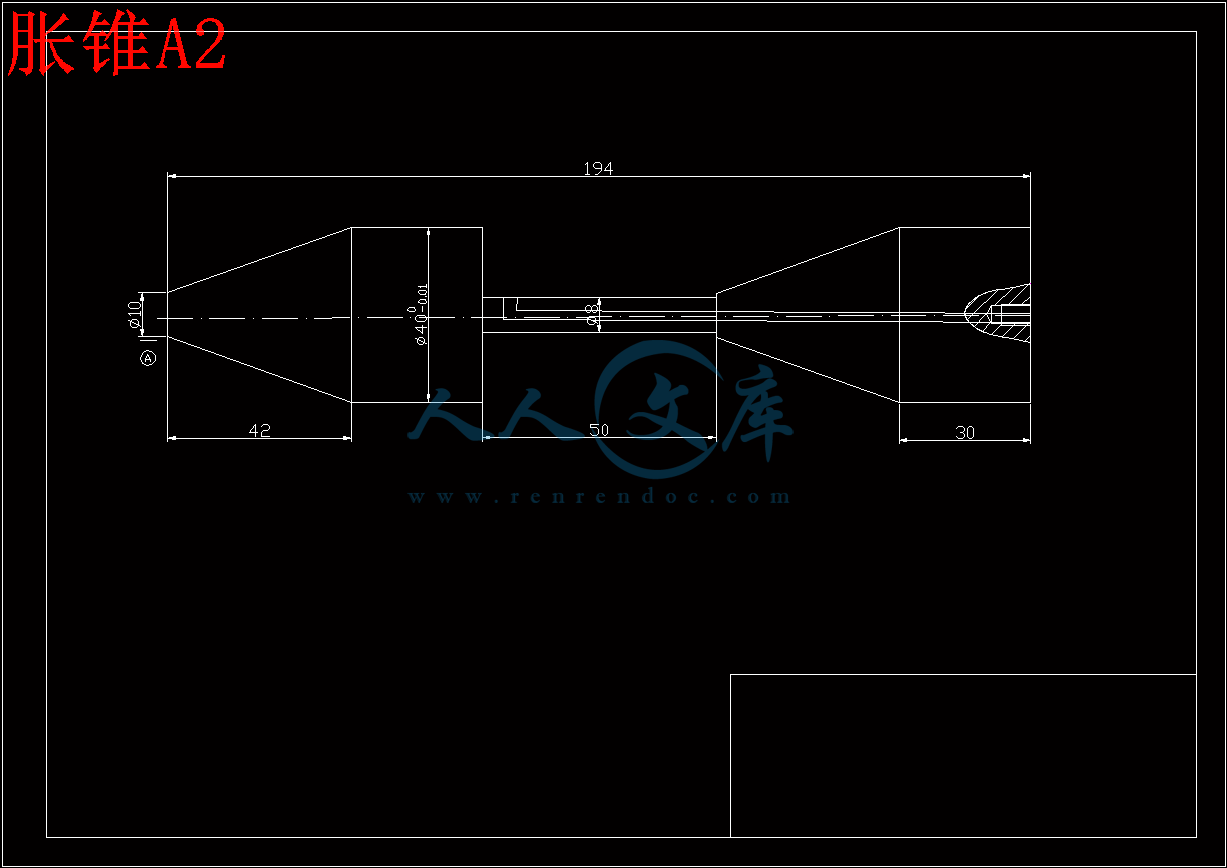
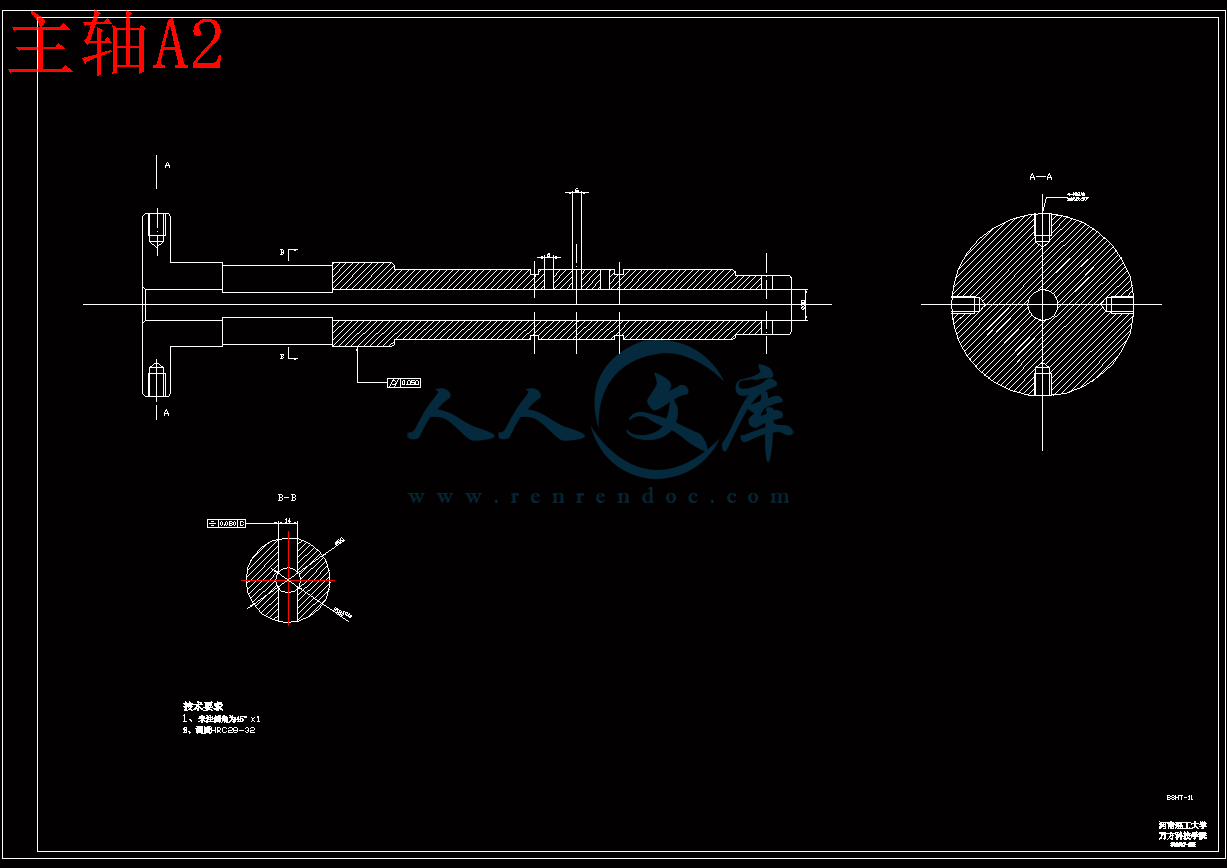
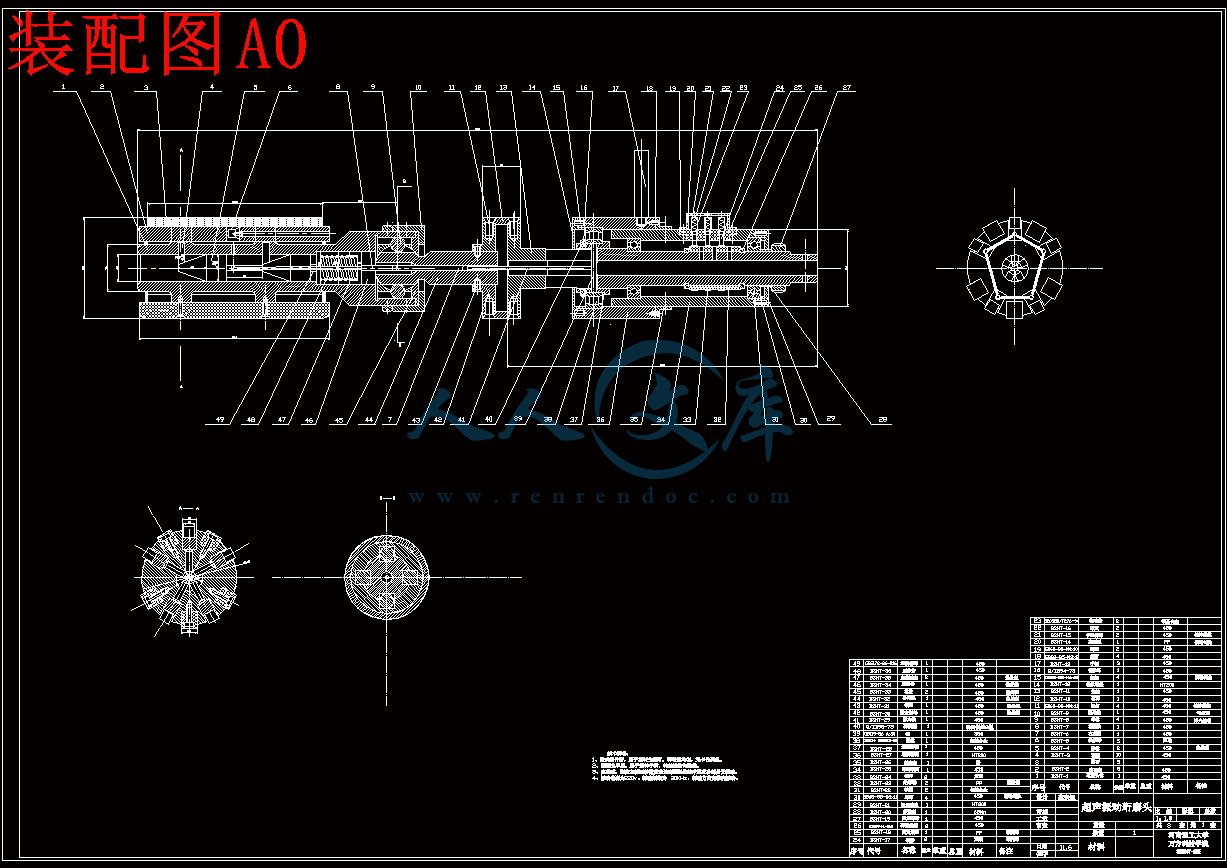
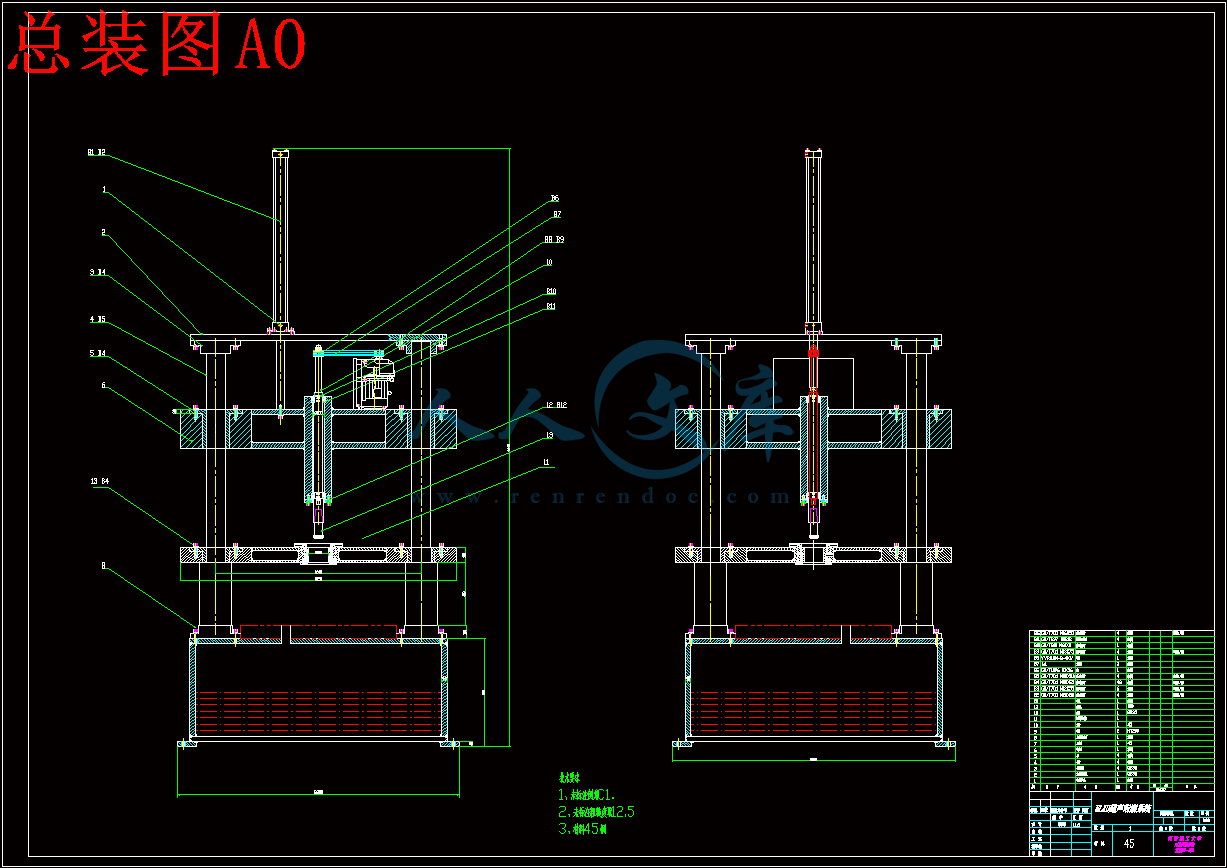