豆干片自动上装系统总体设计
68页 27000字数+说明书+外文翻译+开题报告+4张CAD图纸
中期报告.docx
双通道振动盘装配图A0.dwg
外文翻译--电梯传动轴的事故分析 中文版.doc
外文翻译--电梯传动轴的事故分析 英文版.pdf
弹簧片A3.dwg
振动盘底座.dwg
料斗A2.dwg
豆干片自动上装系统总体设计开题报告.doc
豆干片自动上装系统总体设计论文.doc
摘 要
豆干片自动上装排序系统,是个既熟悉又陌生的机械系统,随着豆类食品越来越受到人们的青睐,豆干片的生产工艺的发展完善是不可或缺的部分。在现在国内为市场,还没有豆干片自动上装排序系统机械出现,豆干片的生产厂家要在豆干片的包装过程中花费大量的劳动力,因此,为了改善豆干片的生产工序,提高食品加工的机械化,增加劳动效率,同时保障生产过程中食品的卫生,我们选择了此课题作为本科毕业设计题目。
本次设计的豆干片自动上装排序系统主要包括两大部分:豆干片的自动排序和豆干片的自动落料填装。为实现此目的主要设计使用了两种主要机械装置:振动盘和气缸。通过对豆干片生产现状的了解,通过指导老师对本次设计的背景的介绍和设计目的及要求的说明讲解,通过查找翻阅有关书籍和网上查找相关信息和在指导老师的指导下,完成了本次设计各个部分的设计。
关键词:豆干片 自动上装 振动盘 气缸
The bean curd pieces automatic sorting system is a both familiar and strange mechanical system. With the bean food is getting more and more favors of all ages, the production process have been an integral part of development and improvement. In the domestic market now, there is no automatically upload mechanical sorting systems, in order to improve the production processes and the mechanization of food processing and to increase the labor efficiency and guarantee the hygiene of food, we’ve chosen this topic as a graduate design project.
The design mainly consists of two parts: the bean curd pieces automatic sorting and its automatic blanking. For this purpose, two main mechanisms are used: vibration plate and cylinder. Through understanding the production status and the background of this design and referring to the online information, I’ve completed the design under the guidance of instructor
Key words: bean curd pieces; vibration plate; cylinder; automatic upload
目 录
前 言1
1 总体方案的制定2
1.1 设计目的和意义2
1.2 总体方案的确定3
2振动盘的设计5
2.2 振动盘的原理7
2.2.1 振动盘的原理分析7
2.3 振动盘的定向方法12
2.4单通道振动盘料斗的设计13
2.4.1 振动盘料斗设计13
2.4.2振动器设计16
2.5 双通道震动盘的设计20
2.5.1振动器设计22
2.7振动盘涂层27
2.8振动盘技术参数28
2.8 振动盘的调整步骤与要点29
3 滑道设计31
4 气动传动设计33
4.1 气压传动的系统分析33
4.1.1气压传动的组成及工作原理33
4.2.1 气缸的性能40
4.2.2缓冲装置44
4.2.3 连接与密封44
4.2.4 气缸筒与气缸盖的设计44
活塞与活塞杆46
气动装置的密封49
5.1 机架的概念及分类56
5.1.1 机架的概念56
5.1.2 机架按外形分类56
5.1.3 机架按制造方法和材料分类56
5.1.4 机架按力学模型分类56
5.2 机架设计的准则57
5.2.1 工况要求57
5.2.2刚度要求57
5.2.3强度要求57
5.2.4稳定性要求58
5.2.5美观58
5.2.6其他58
5.3 机架设计的一般要求58
5.4 机架的设计步骤59
5.5 机架结构选择的一般原则59
5.6 机架的设计与计算60
5.7 机架设计的技术要求61
致 谢62
参考文献64
目前,食品安全是大家特别关注的一个问题,随着社会发展人们对食品营养,卫生,安全要求越来越严格。而人们在追求优质营养的时候很容易选择豆干,营养丰富,含有大量蛋白质、脂肪、碳水化合物,还含有钙、磷、铁等多种人体所需的矿物质。豆腐干在制作过程中会添加
食盐、茴香、花椒、大料、干姜等调料,既香又鲜,久吃不厌,被誉为“素火腿”。社会需求很大然而豆干的加工还是人工的,存在着很大的食品安全隐患,并且生产效率比较低。尤其在豆干片加工企业需要花费大量的人力劳动从而完成排序部分。所以说,本次豆干片自动上装系统设计,不管是对食品加工工业的发展还是对企业社会的利益增长都是具有重要价值和意义的。
所以我们选择做豆干片自动上装系统总体设计,这次设计符合我们专业的培训目标,可以体现综合训练的要求,而且,本次设计题目符合现代社会食品加工工业的发展要求,是具有重大的现实价值。
本次设计也是对我能力的一种考试,是检查自我是否是合格的本科毕业生的一次考核。道路是曲折的,前途是光明的。梅花香自苦寒来,宝剑锋从磨砺出。
由于我国机械自动化,或者说是食品机械自动化还远远落后于发达国家,缺少成功的经验,同样,豆干片是我们的传统特色美食,国内外没有过自动上装的成功经验,所以我们在设计过程中没有成功案例可循,首次进行设计,由于实际生存知识的欠缺和设计经验的缺乏。还有许多地方不足和错误,希望老师指出指导!1.1 设计目的和意义
豆干有抗氧化的功效。所含的植物雌激素能保护血管内皮细胞,使其不被氧化破坏。如果经常食用就可以有效地减少血管系统被氧化破坏。另外这些雌激素还能有效地预防骨质疏松、乳腺癌和前列腺癌的发生,是更年期的保护神。丰富的大豆卵磷脂有益于神经、血管、大脑的发育生长。比起吃动物性食品或鸡蛋来补养、健脑,豆干都有极大的优势,因为豆干在健脑的同时,所含的豆固醇还抑制了胆固醇的摄入。大豆蛋白可以显著降低血浆胆固醇、甘油三酯和低密度脂蛋白,同时不影响血浆高密度脂蛋白。所以大豆蛋白恰到好处地起到了降低血脂的作用,保护了血管细胞,有助干预防心血管疾病。所以在这个人们越来越追求食品营养安全的大氛围下,豆干越来越受亲睐。
然而,豆干的生产包装却依然是人工排序上料。这影响了企业的生产,也威胁着这一行业的食品安全。所以做这个课题也是很迫切的任务。
2振动盘的设计
2.1 振动盘的发展过程振动盘的发展过程
国内振动机械新技术
a、预防长距离振动输送机产生弹性弯曲的新技术
b、保持振动盘振动稳定的新技术
c、消除构件焊接内应力的新技术
d、防止螺钉和螺帽松动的新技术
e、防止筛孔堵塞的技术
f、提高筛面耐磨性的技术
g、二次隔振减小传给基础振动的技术
h、减少振动机起动通过共振振幅的技术
国内振动盘新产品
1) 激振器偏转式大型冷矿振动筛
2) 惯性共振式概率筛
3) 20-40米长的平衡加隔振动的大长度振动输送机
4) 新型振动压路机
5) 大宽度新型摊铺机
6) 750吨振动沉拔桩机
7) 实现振动同步传动的自同步振动给料机
8) 双激振器自同步振动破碎机
国内振动盘发展展望
A,大力加强研究振动盘理论与技术的研究, 一方面深入开展振动盘的基础理论与工作机理的研究, 如加强非线性振动机的理论, 振动的稳定性等, 另一方面加强实际技术的应用等,如筛面耐磨性和延长筛机寿命研究等
B,应该大力开展振动盘实际应用的研究与开发工作, 扩大振动技术的应用领域与范围, 将振动盘广泛应用于各个领域和各种工艺过程.
C,特别要加强振动盘技术与信息技术, 即多煤体技术,集成电路技术,光导纤维技术,网络技术和人工智能技术的结合, 使振动盘的理论与技术成为一种以智力为依托的高新技术. 振动盘是振动式料斗的工作原理不同于机械传动的料斗,它借助于电磁力产生微小的振动,依靠惯性力和摩擦力的综合作用驱使豆腐干向前运动,并在运动中自动定向。
这种料斗装置的主要优点:
(1)送料和定向过程中没有机械的搅拌、撞击、和强烈的摩擦作用,因而工作稳定。对于柔软富有弹性的豆干用这种料斗是很合适的,因此我们采用振动盘作为筛选排序装置。
(2)结构简单,易于维护,比较耐用。
(3)通用性强。对于豆干形状的变化,我们只要稍作调整,就仍然可以使用。
振动盘在使用中的缺点和局限性:
(1)工作中有噪声,特别当豆干较大或结构参数设计得不合理时噪声尤大,以致扰乱周围工作环境。因此必须合理地设计和调整,使之减小和避免噪声,同时,振动盘对于尺寸和重量较大的豆干不甚合适。
(2)必须保持料斗中洁净的工作环境,当有豆干碎渣时,必须给予清理,否则将影响送料速度和工作效果。
参考文献
[1] (美)杰佛里-布斯罗伊德《装配自动化与产品设计》,2009.3
[2] 肖旭霖.《食品机械与设备》.科学出版社,2006.1
[3] 华中工学院机械制造教研室.《机床自动化及自动线》.机械工业出版社,1981.3
[4] 洪钟德,《简明设计机械手册》.同济大学出版社,2002.5
[5] 梁珣,《Auto CAD2007绘图与辅助教程》.清华大学出版社,2007.2
[6] 武良臣 《互换性和测试技术》.北京邮电大学出版社,2009.8
[7] 马桃林 《包装技术》.武汉测绘科技大学出版社,1999.6
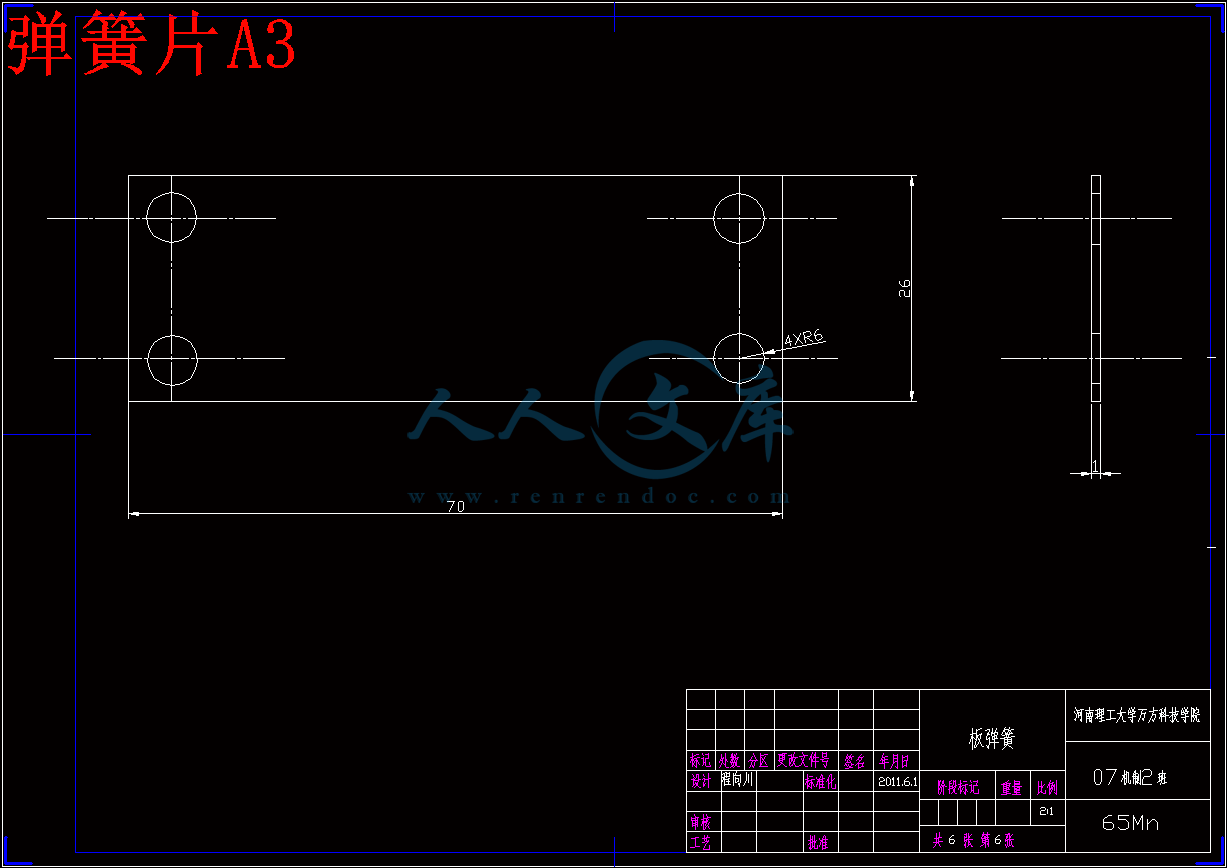

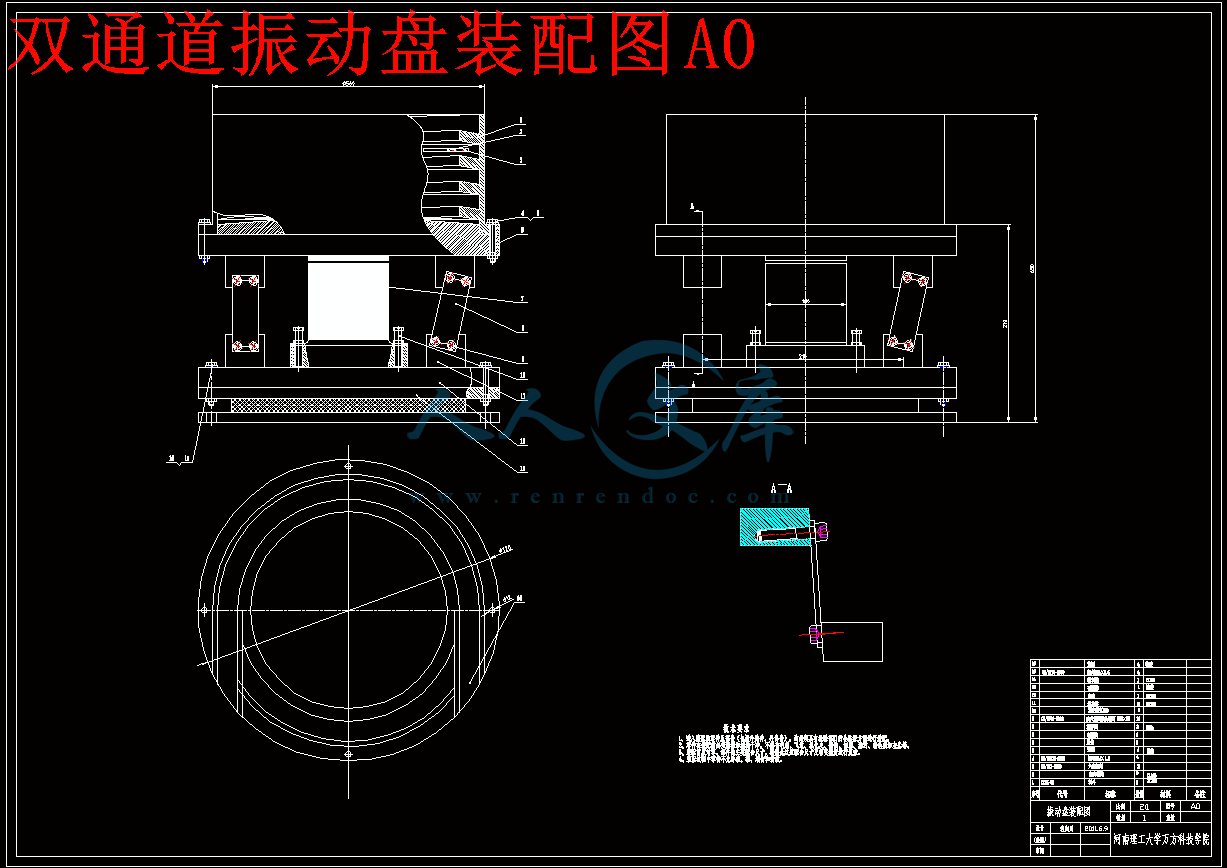
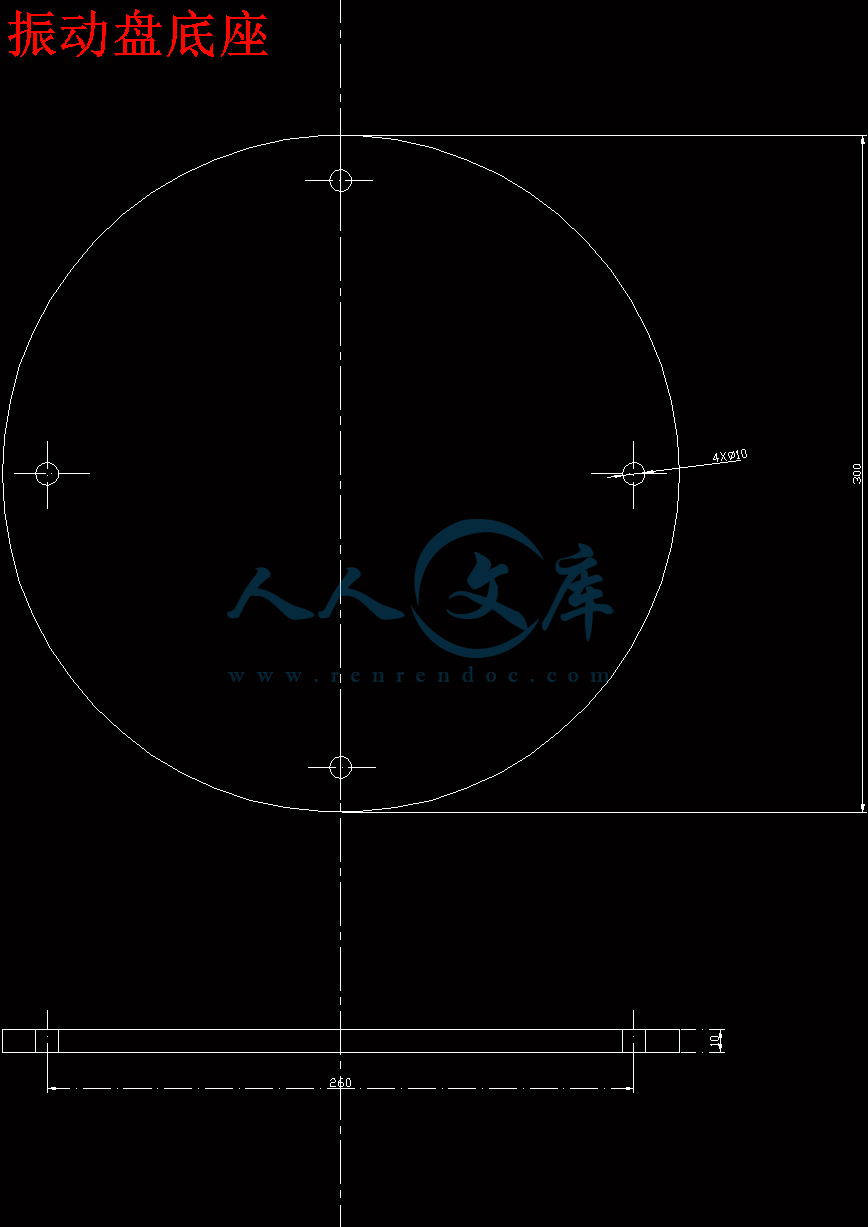