车床尾座体工艺规程制订及工装设计【镗孔Ф75H6】
29页 11000字数+说明书+任务书+开题报告+外文翻译+3张CAD图纸【详情如下】
任务书.doc
外文翻译--基本加工工序和切削技术.doc
夹具底板A0.dwg
夹具总装图A0.dwg
封皮.doc
封面及封底.doc
尾座体零件图A1.dwg
工序卡.doc
工艺过程卡.doc
评语.doc
车床尾座体工艺规程制订及工装设计开题报告.doc
车床尾座体工艺规程制订及工装设计论文.doc
零件图.JPG
车床尾座体工艺规程制订及工装设计
摘要
尾座体是车床上的重要的部件之一,是车床上用以支撑轴类零件车削加工和实施钻孔的主要车床附件。本文针对某类给定的尾座体进行了加工工艺与工装的设计,完成了以下工作:
概述了尾座体的技术和现状发展;
对尾座体进行了工艺分析,并提出了两种方案进行比较;
编制了尾座体的工艺规程,完成了其工序卡的设计;
针对工艺中的某重要工序,设计完成了一套镗孔夹具,包括定位元件,夹紧机构、对刀块、夹具体的设计并分析了定位误差。
关键词 设计;工装;工艺;尾座体
Lather tail the craft work of the body pack a design
Abstract
stalk spare parts, the car pares to process the main lather enclosure that drills a hole with implementation.This text aims at a certain the tail body giving certainly carried on to process the design that craft and work pack and completed once work:
1.All said a tail the technique and present condition development of the body;
2.Carried on craft analysis to the tail body, and put forward two kinds of projects to carry on a comparison;
3.Drew up a tail body of craft regulations, completed the design of its work preface card;
4.Aim at a craft in of some important work preface, designed to complete a set of Xian slot tongs, including fixed position component, clipped tight organization, to the knife piece, clip a concrete design and analyzed a fixed position error margin.
Keywords design; clamping; craft; tailstock
目录
摘要I
AbstractII
第1章 绪论1
1.1 课题来源1
1.2 课题背景及发展趋势1
1.3 夹具的基本结构及夹具设计的内容1
1.4 本章小结2
第2章 尾座体加工工艺规程设计3
2.1 零件的分析3
2.1.1 零件的作用3
2.1.2 零件的工艺分析3
2.2 加工的主要问题和工艺过程设计所应采取的相应措施4
2.2.1 确定毛坯的制造形式4
2.2.2 基面的选择4
2.2.3 确定工艺路线4
2.2.4 机械加工余量、工序尺寸及毛坯尺寸的确定5
2.2.5 确定主要工序工程中的切削用量7
2.3 本章小结17
第3章 专用夹具设计18
3.1 镗Ф75H6孔夹具设计18
3.1.1 定位基准的选择18
3.1.2 夹紧力的计算18
3.1.3 夹紧元件及动力装置确定19
3.1.4 镗套、镗模板及夹具体设计19
3.1.5 夹具精度及定位误差分析20
3.1.6 夹具设计及操作的简要说明20
3.2 本章小结22
结论23
致谢24
参考文献25
附录27
课题来源
本课题来源于指导教师所给众多题目之一。
课题背景及发展趋势
加工工艺及夹具毕业设计是对所学专业知识的一次巩固,是在进行社会实践之前对所学各课程的一次深入的综合性的总复习,也是理论联系实际的训练。
机床夹具已成为机械加工中的重要装备。机床夹具的设计和使用是促进生产发展的重要工艺措施之一。随着我国机械工业生产的不断发展,机床夹具的改进和创造已成为广大机械工人和技术人员在技术革新中的一项重要任务。
材料、结构、工艺是产品设计的物质技术基础,一方面,技术制约着设计;另一方面,技术也推动着设计。从设计美学的观点看,技术不仅仅是物质基础还具有其本身的“功能”作用,只要善于应用材料的特性,予以相应的结构形式和适当的加工工艺,就能够创造出实用,美观,经济的产品,即在产品中发挥技术潜在的“功能”。
技术是产品形态发展的先导,新材料,新工艺的出现,必然给产品带来新的结构,新的形态和新的造型风格。材料,加工工艺,结构,产品形象有机地联系在一起的,某个环节的变革,便会引起整个机体的变化。
工业的迅速发展,对产品的品种和生产率提出了愈来愈高的要求,使多品种,对中小批生产作为机械生产的主流,为了适应机械生产的这种发展趋势,必然对机床夹具提出更高的要求。
夹具的基本结构及夹具设计的内容
根据夹具设计的基本原理,选择合理的夹紧与定位方案,最有效的满足镗床夹具的设计 要求当工件的加工精度要求较高时,应采用具有固定夹具的单工位组合机床;加工精度较低时,可采用具有移动夹具的多工位组合机床。此外,还要考虑到不同布置形式的机床所能达到的加工精度。例如,对于同轴度要求较高的各孔,应采用从同一面对工件进行加工的机床布置形式。
按在夹具中的作用,地位结构特点,组成夹具的元件可以划分为以下几类:
1.定位元件及定位装置;
2.夹紧元件及定位装置(或者称夹紧机构);
3.夹具体;
4.对刀-引导元件及装置(包括刀具导向元件,对刀装置及靠模装置等);
5.动力装置;
6.分度,对定装置;
7.其它的元件及装置(包括夹具各部分相互连接用的以及夹具与机床相连接用的紧固螺钉,销钉,键和各种手柄等);
每个夹具不一定所有的各类元件都具备,如手动夹具就没有动力装置,一般的车床夹具不一定有刀具导向元件及分度装置。反之,按照加工等方面的要求,有些夹具上还需要设有其它装置及机构,例如在有的自动化夹具中必须有上下料装置。
专用夹具的设计主要是对以下几项内容进行设计:
1.定位装置的设计;
2.夹紧装置的设计;
3.对刀-引导装置的设计;
4.夹具体的设计;
5.其他元件及装置的设计。
本章小结
通过本章陈述了尾座体加工的发展趋势以及所研究课题的主要内容,使以后的设计有了明确的针对性。
本论文以车床尾座为模板,根据零件的特性,通过分析计算,确定加工 基准。需在多种方案中选择最优的加工工艺路线,并根据计算所得的余量选择合理的机床进行加工。最后在所有的工序中选择一道工序,做镗床夹具设计。
零件的作用
题目所给的零件是机床尾座体,Φ75H6的孔与顶尖研配,底面与工作台相连,通过Φ20mm孔用螺栓将“尾座体”紧固在工作台上。主要作用是固定顶尖。圆柱体形的部分有一个Φ75H6孔,并且有一个Φ25孔,顶尖穿过Φ75H6孔,将螺钉拧紧,这样就将顶尖固定。
零件的工艺分析
“尾座体”共有三组加工表面,其中两组有位置度要求。
1.以A为基准的加工表面。这一组表面包括110x390的上平面,两侧表面,Φ75mm孔,Φ25×5的沉头孔,Φ35H9孔以及Φ42H7孔。
2.以B为基准的加工表面。这一组表面包括Ra=3.2μm的前端面, Ra=1.6μm的后端面,底平面60x20与32x3的槽,Φ20H7和Φ22的孔。
3.以C为基准的加工表面。这一组表面包括Φ25H7孔。
加工表面有位置度要求,如下:
底面平面度要求为0.04;Φ75H6孔圆度公差为0.004,轴线与底面平行度为0.05;后端面与Φ75H6轴线垂直度为0.04;Φ25H7孔与Φ42H7同轴度公差为0.02;底面60x20槽壁与孔Φ75H6轴线垂直度要求0.1;Φ75H6的孔需精加工、研配。
加工的主要问题和工艺过程设计所应采取的相应措施
确定毛坯的制造形式
零件的材料HT200。由于尾座体年产量一般为几千件,达到大批生产的水平,而且零件的轮廓尺寸较大,铸造表面质量的要求高,故可采用铸造质量稳定的,适合大批生产的金属模铸造。便于铸造和加工工艺过程,而且还可以提高生产率。
基面的选择
1.粗基准的选择 对于本零件而言,按照互为基准的选择原则,选择本零件的下表面作为加工的粗基准,可用装夹对肩台进行加紧,利用底面定位块支承和底面作为主要定位基准,以限制z、xz、y、xy、yz五个自由度达到定位目的。
2.精基准的选择 主要考虑到基准重合的问题,和便于装夹,采用已加工结束的上、下平面作为精基准。
确定工艺路线
表2.1工艺路线方案一
工序1粗,精镗φ75H6孔
工序2加工φ42H7孔,φ25H7孔
工序3粗,精铣上平面、侧平面
工序4粗,精铣底平面
工序5加工上平面φ25H7孔
工序6镗φ35H9侧面孔
工序7加工底平面各孔,槽
工序8去除锐边毛刺
工序9检验
表2.2工艺路线方案二
工序1粗,精铣底平面
工序2粗,精铣上平面、侧平面
工序3粗,精镗φ75H6孔
工序4加工φ42H7孔,φ25H7孔
工序5镗φ35H9侧面孔
工序6加工上平面φ25H7孔
工序7加工底平面各孔,槽
工序8去除锐边毛刺
工序9检验
工艺路线的比较与分析:
第二条工艺路线不同于第一条是将“镗孔工序放在除前后端面外的各面加工结束后再进行加工。其它的先后顺序均没变化。通过分析发现这样的变动提高了生产效率。而且对于零的尺寸精度和位置精度都有太大程度的帮助,并且符合先面后孔的加工原则。采用基准重合的原则,先加工底平面,然后以底平面为精基准再加工其它平面上的各孔与平面,这样便保证了Φ75H6和Φ42H7孔的轴线,同时满足了以两轴轴线为基准加工的要求。符合先加工面再钻孔的原则。若选第一条工艺路线, 加工不便于装夹,并且毛坯的端面与轴的轴线是否垂直决定了钻出来的孔的轴线与轴的轴线是非平行这个问题。所以发现第一条工艺路线并不可行。选取第二条工艺方案,先镗上、下平面,各孔,然后以这些已加工的孔为精基准,加工其它各孔,槽的形位公差要求。
从提高效率和保证精度这两个前提下,发现第二个方案比较合理。所以我决定以第二个方案进行生产。具体的工艺过程见工艺卡片所示。
机械加工余量、工序尺寸及毛坯尺寸的确定
尾座体的材料是HT200,生产类型为大批生产。由于毛坯采用金属模铸造, 毛坯尺寸的确定如下:
由于毛坯及以后各道工序或工步的加工都有加工公差,因此所规定的加工余量其实只是名义上的加工余量,实际上加工余量有最大加工余量及最小加工余量之分。
由于本设计规定零件为大批量生产,应该采用调整法加工,因此计算最大与最小余量时应按调整法加工方式予以确定。这里就不讲述如何铸造成毛坯的过程了,只分析从毛坯加工成成品零件的过程如下:
1.加工尾座体的底平面,底平面粗糙度要求为Ra=1.6μm,平面度要求为0.04,根据参考文献[8]表4-35和表4-37考虑3mm,粗加工2mm,精加工1mm到金属模铸造的质量和表面的粗糙度要求。最后刮研底面,保证平面度0.04。加工上平面和侧面时,用铣削的方法加工上平面和两侧面。由于上平面和两侧面的加工表面粗糙度未标注,所以按照粗糙度要求为Ra=6.3μm来加工,根据参考文献[8]表4-35和表4-37考虑2mm,粗铣加工2mm到金属模铸造的质量和表面的粗糙度要求。
2.加工前后端面时,用铣削加工方法加工。考虑到加工方便,按照粗糙度都是Ra=1.6μm加工,根据参考文献[8]表4-35和表4-37考虑可用镗刀一次加工2mm到金属模铸造的质量和表面的粗糙度要求。因为后端面要求与基准B垂直度为0.04,所以等Φ75H6孔加工之后,再刮研保证垂直度。
3.镗直径Φ75H6孔时,由于粗糙度要求Ra=0.8μm,因此考虑加工余量2.5mm。可一次粗加工2mm,一次精加工0.5mm就可达到要求。并且要保证从前端面开始的340mm锥度在0.04以内。
4.加工Φ42H7孔,内壁粗糙度要求Ra=1.6μm,根据参考文献[8]表4-23考虑加工余量2.5mm。可一次钻削加工余量2mm,一次精镗0.5mm就可达到要求。以Φ42H7孔加工Φ25H7孔同轴度0.02,余量与Φ42H7孔相同。同时粗铣Φ42H7孔两个端面和Φ25H7孔的两个端面,保证各自长度值。
5.加工Φ35H9孔,轴线距前端面为80mm,内壁粗糙度为Ra=3.2μm,根据参考文献[8]表4-23考虑加工余量2mm。可一次粗镗1.5mm,一次精镗0.5mm就可达到要求。
6.加工上平面Φ25H7孔,先加工Φ25H7孔,内壁粗糙度要求Ra=1.6μm,根据参考文献[8]表4-23考虑加工余量1.5mm。可一次钻削加工余量1mm,一次铰孔0.5mm就可达到要求。然后锪粗糙度为Ra=6.3μm的Φ45的沉孔。
7.加工底平面上的孔、槽,
先分析孔的加工:
Φ20H7孔内壁粗糙度Ra=1.6μm,根据参考文献[8]表4-23考虑加工余量1.5mm。可一次钻削加工余量1mm,一次铰孔0.5mm可达到要求
Φ22孔及上面Φ45沉头孔粗糙度为Ra=6.3μm,一次粗加工即可完成,只需留1mm余量,需要考虑的是如何安排加工顺序,使用可调刀径的钻头,先钻削Φ22的孔,然后将刀径调大回拉,锪钻出沉头孔,最后调小刀径退刀即可。
如前所说,在设计夹具时,应提高劳动生产率。切削力较大,为了夹紧工件,要求夹具的精度高,而这样的话将使整个夹具过于麻烦, 因此,应首先设法降低切削力,措施有二:一是提高毛坯的制造精度,使最大切削深度降低,以降低最大切削力;二是选择一种比较理想的压板压紧机构,由于自锁性比较好,故容易夹紧。因此,本夹具总的感觉还比较紧凑。对专用夹具的设计,可以了解机床夹具在切削加工中的作用,可靠地保证工件的加工精度,提高加工效率,减轻劳动强度,充分发挥和扩大机床的给以性能。本夹具设计可以反应夹具设计时应注意的问题,如定位精度、夹紧方式、夹具结构的刚度和强度、结构工艺性等问题。 目前车床尾座的生产周期相对较长,车床尾座采用铸造,不能达到其使用要求,必须经过许多步的在加工,才能满足其使用要求,在其加工过程中采用许多道工序。该课题就是为了优化加工工艺,提高加工生产效率,降低生产成本。该课题将在不降低车床尾座的使用性能的前提下采用机械加工的优化设计来达到预期目。其中本人对于对生产加工中的各个工序所需用时进行了计算,主要通过工厂请教加工工人,利用其丰富的加工经验从而使本课题更具实际的可运行性,并寻求指导老师的帮助,使得本次设计可以投入到实际的生产加工当中。
本文对车床的机械结构进行了分析和说明,具体包含进给机构和主轴系统等核心部分的介绍。在对车床尾座的分析设计中,文章针对尾座体进行了结构设计,并进行了工艺规程文件的编制。对以后车床尾座设计计算方面的工作提供了参考,具有一定的实用价值。
在整个设计过程中,我本着实事求是的原则,抱着科学、严谨的态度,主要按照课本的步骤,到图书馆查阅资料,在网上搜索一些相关的资料和相关产品信息,进工厂请教工人师傅,在学校征求指导老师的建议,最终完成了此次毕业设计。
参考文献
刘德荣.组合夹具结构简图的初步探讨,组合夹具,1982,15~32
孙已德.机床夹具图册.机械工业出版社,1984:20~23
贵州工学院机械制造工艺教研室.机床夹具结构图册.贵州任命出版社,1983:32~50
刘友才.机床夹具设计.机械工业出版社,1992:27~39
孟少龙.机械加工工艺手册第1卷.机械工业出版社,1991:3~10
金属机械加工工艺人员手册修订组.金属机械加工工艺人员手册.上海科学技术出版社,1979:5~25
李洪.机械加工工艺手册.机械工业出版社,1990:21~124
马贤智.机械加工余量与公差手册.中国标准出版社,1994:34~78
上海金属切削技术协会.金属切削手册.上海科学技术出版社,1984:7~23
周永强.高等学校毕业设计指导.中国建材工业出版社,2002:40~143
薛源顺.机床夹具设计(第二版) .机械工业出版社,2003:9~17
余光国,马俊,张兴发等.机床夹具设计.重庆大学出版社,1995:5~40
东北重型机械学院,洛阳农业机械学院,长春汽车厂工人大学.机床夹具设计手册.上海科学技术出版社,1980:32~46
李庆寿.机械制造工艺装备设计适用手册.宁夏人民出版社,1991:29~45
廖念钊,莫雨松,李硕根.互换性与技术测量.中国计量出版社,2000:9~19
哈尔滨工业大学,哈尔滨市教育局.专用机床夹具设计与制造.黑农江人民出版社,1979:32~42
乐兑谦.金属切削刀具.机械工业出版社,2005:4~17
哈尔滨工业大学.机床夹具设计手册.上海科学技术出版社,1983:10~69
Chernor.Machine Tools N,1984:3~18
John Louis Feirer.Machine Tool Metalworking.Glencoe/McGraw-Hill School Pub Co,1973:15~30
Manfred Weck.Handbook of Machine Tools: Automation and controls.Translated by H. Bibring.Wiley Heyden publication,1984 :12~66
Sors l.fatigue design of machine components.Oxford:pergramon press,1971:1~55

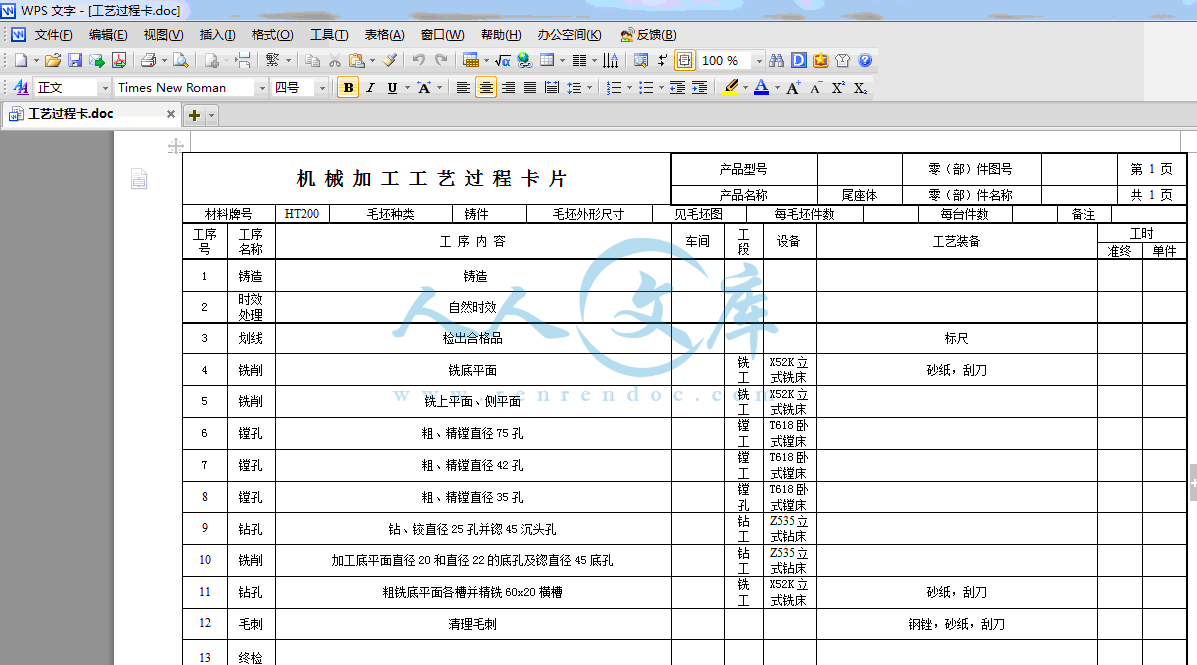
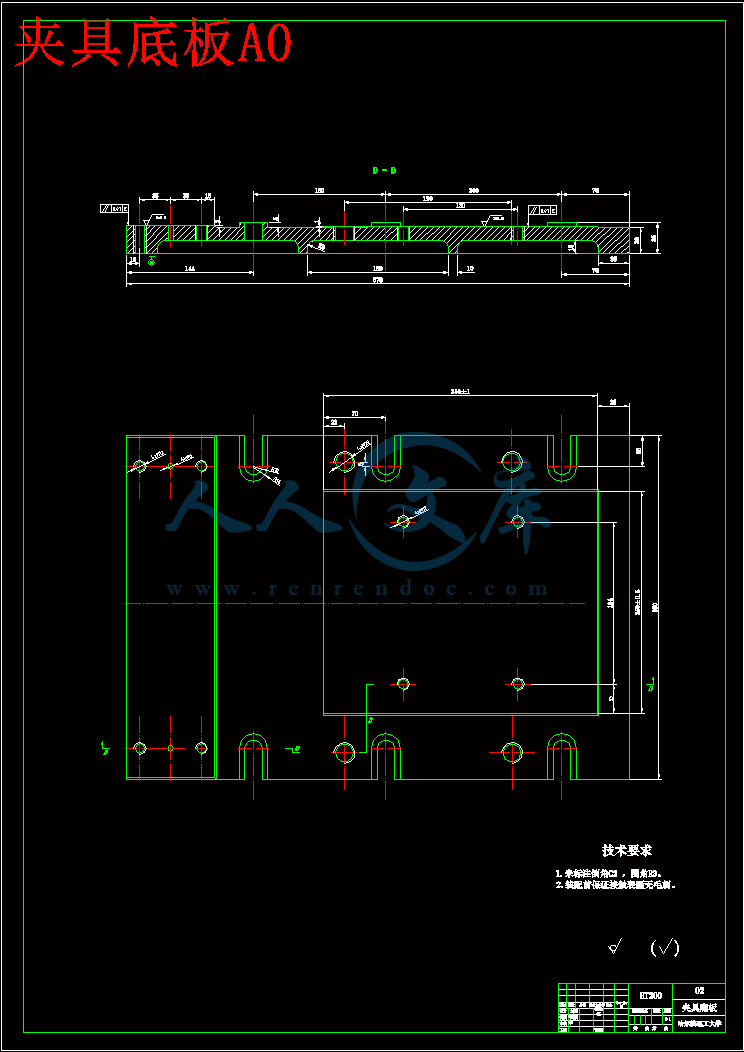
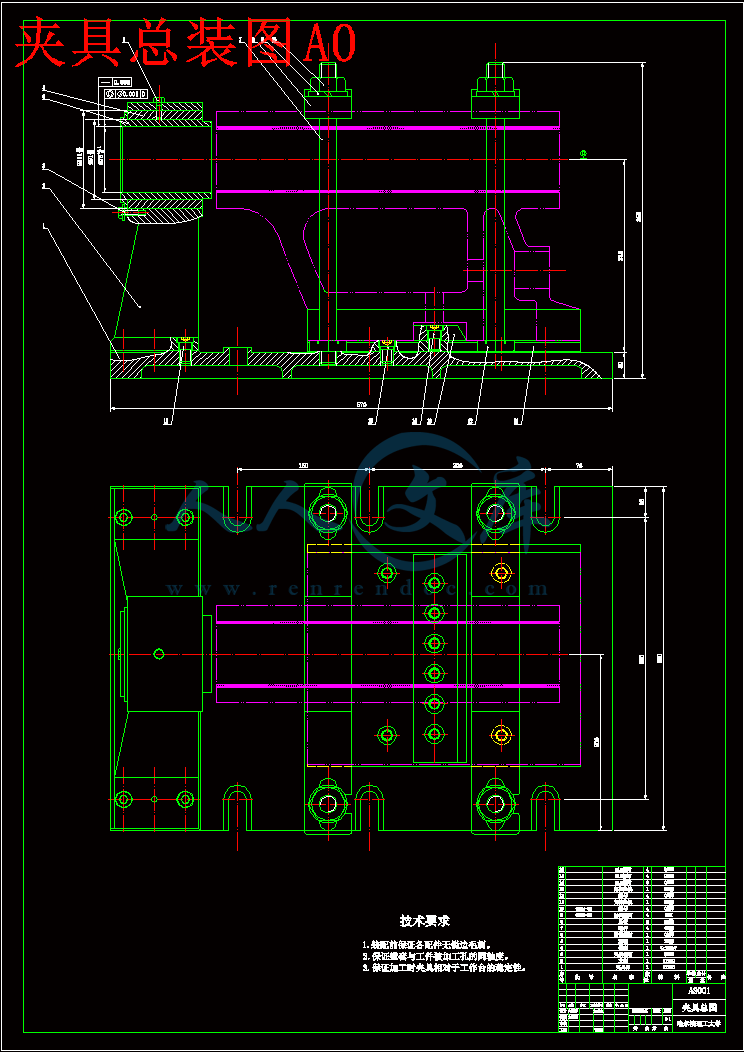
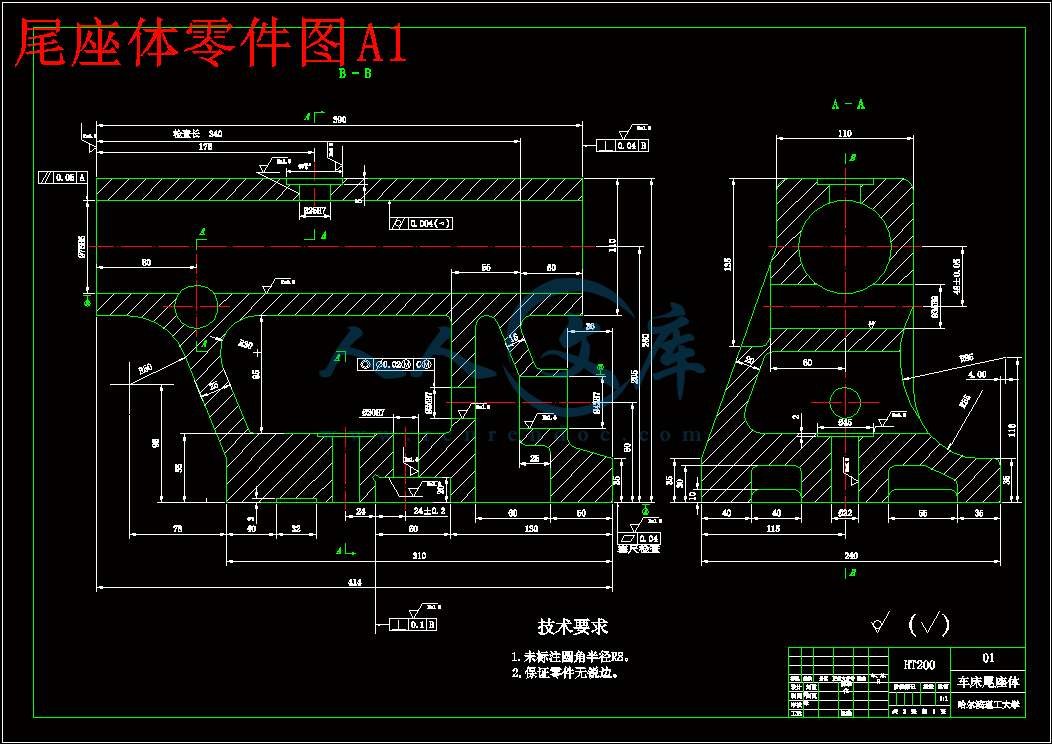